Impossible objects 3d printer
Impossible Objects unveils new CBAM-2 3D printer, partnership with BASF, and $4.1 million funding
0Shares
Composite-based additive manufacturing (CBAM) developer Impossible Objects has made a series of announcements at RAPID + TCT 2019, including $4.1 million in funding, a collaboration with BASF, and a new 3D printer: the CBAM-2.
The release of the CBAM-2 3D printer builds upon the company’s previous CBAM offering in the Model One, with greater print sizes and efficiency. Impossible Objects’ collaboration with BASF centers around the support of the chemical giant’s Ultrasint PA6-carbon fiber powder for use with the Model One and CBAM-2 3D printers. Both the partnership with BASF and its new CBAM-2 3D printer, which has a planned release for Q3 2019, aim to extend the industrial applications of Impossible Objects’ patented CBAM process.
Regarding funding, Impossible Objects raised $4.1 million in a round led by tech equity specialist OCA Ventures, in order to meet demand for its products. The new round brings its total funding at Impossible Objects to more than $13 million. Previously in 2017, the company had raised $6.4 million in series A funding, once more led by OCA Ventures.
“It’s been exciting to see how our customers are putting our approach to work to create high-performance parts for everything from aircraft and cars to lightweight athletic gear,” commented Impossible Objects Founder and Chairman Bob Swartz.
The CBAM-2 3D printer. Image via Impossible Objects.“We’re continuing to bring machines, materials and expertise to the market to transform the entire manufacturing process, from prototyping through to high-volume production.”
Impossible Objects’ innovative CBAM process
The unveiling of the CBAM-2 3D printer at RAPID + TCT represents the first demonstration of the new system. Designed to deliver complex parts on an industrial scale, the CBAM-2 is said to be capable of producing at high volume with claims of 10 times faster than ‘conventional 3D printing’ using the CBAM process.
Furthermore, the CBAM-2 supports the 3D printing of high-strength composites, enabled by CBAM technology. Also equipped on the Model One 3D printer, Impossible Objects’ CBAM technology creates composite material prints by fusing together high-performance thermoplastics like PEEK and Nylon with long-fiber carbon and fiberglass sheets. This results in the production of parts with reportedly better strength to weight ratios than 3D printed metal, as well as better chemical resistance and temperature performance compared to standard 3D printing methods.
Updates on the CBAM-2 from the Model One includes support for larger parts, with 3D printed sheets now reaching up to 12 inches x 12 inches in size. Furthermore, the CBAM-2 also features three added cameras for increased precision and quality control in the 3D print, as well as automatic powder filling and bulk ink cartridges for streamlined maintenance.
A complex 3D printed part using the CBAM process. Image via Impossible Objects.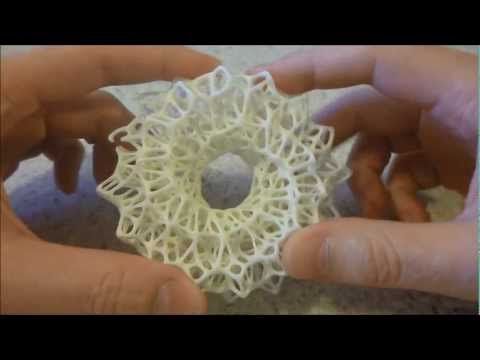
3D printing carbon fiber-PA6 composite parts for the first time
Working with BASF, Impossible Objects has also enabled an “industry-first” in the 3D printing of carbon fiber-PA6 composite parts, using the Model One and CBAM-2 systems. BASF’s PA6 powder expands upon Impossible Objects’ current roster of supported materials for CBAM technology, with the aim of creating “an unmatched range of material choices and capabilities.”
The benefits of carbon fiber-PA6 composites lie in its offering of high strength and temperature performance that surpasses PA12, while costing less. PA6 composite parts produced using Impossible Objects’ CBAM process are said to be up to four times stronger than conventional Fused Deposition Modeling (FDM) parts and twice as strong as Multi Jet Fusion (MJF) parts made with PA12.
“Our collaboration with Impossible Objects opens up new possibilities for customers, especially in the automotive and industrial sectors where we’re seeing strong demand for PA6,” added Kara Noack, regional business director for BASF 3D Printing Solutions.
“This partnership is in line with our philosophy of open innovation and support for open platforms. We’re encouraged by how Impossible Objects is using PA6 and are excited to work together to advance the state of additive manufacturing.”
This is not the only BASF collaboration announced at RAPID + TCT this year, with Paxis, an Illinois-based OEM, collaborating with the chemical company to study advanced applications of Paxis’ Wave Applied Voxel (WAV) 3D printing platform.
Success with CBAM for Impossible Objects
The Model One, Impossible Objects’ previous model, was initially unveiled at RAPID 2017, where it won the Innovation Award for the system at the event. The CBAM process was described as an “innovative solution that could provide significant value to its customers and to the industry as a whole,” according to Chris Williams, Associate Professor of Mechanical Engineering at Virginia Tech and one of the award judges.
Its novel capabilities has led to a variety of high profile acquisitions of the 3D printer. U.S. based global manufacturing company Jabil was the first customer of the Model One, and since then, Impossible Objects has also provided Model One 3D printers to the the U.S Air Force, as well as the Ford Motor Company, which adopted two systems for research and development. Now, with the unveiling of the CBAM-2, Impossible Objects is looking to continue bringing its patented technology to the market with the aim of revolutionizing the manufacturing industry.
You can now cast your vote for the third annual 3D Printing Industry Awards. Help decide this year’s winners now.
Make sure to keep up to date on all the news from RAPID + TCT by Subscribing to the 3D Printing Industry newsletter, following us on Twitter and liking us on Facebook.
Looking for a career in additive manufacturing? Visit 3D Printing Jobs for a selection of roles in the industry.
Featured image shows the CBAM-2 3D printer. Image via Impossible Objects.
Tags basf Bob Swartz CBAM CBAM-2 composite-based additive manufacturing Impossible Objects Kara Noack Model One OCA Ventures PA-6 RAPID + TCT 2019 Ultrasint PA6-carbon fiber
Anas Essop
Anas Essop is an English and Film graduate, who loves writing about the advancement of technology.
Impossible Objects and Owens Corning Join Forces to Develop Stronger, Cheaper 3D Printing Materials
3D printing news News Impossible Objects and Owens Corning Join Forces to Develop Stronger, Cheaper 3D Printing Materials
Published on May 26, 2021 by Amelia H.
Earlier this week, Impossible Objects announced that it would be joining a development agreement with Owens Corning targeted at developing new materials for Impossible Objects’ revolutionary composite-based additive manufacturing (CBAM) process. While Impossible Objects is both a 3D printers and materials company, though a global leader, Owens Corning focuses on the manufacture of building and industrial materials alone. Together the companies will create specialized materials tailor-made for composite-based additive manufacturing. They also hope to be able to achieve the production of stronger parts at costs lower than other 3D printing processes.
These new materials will include fiberglass composites. Fiberglass composite materials demonstrate impressive advantages for 3D printed parts, such as considerably greater strength-to-weight ratios compared to aluminum, lower costs, superior high-temperature performance and greater chemical resistance. Of these advantages low material cost is particularly important, especially in the context of broadening the adoption of additive manufacturing technologies. This is because materials used in 3D printing can often be more expensive than those used by traditional manufacturing methods by a factor of eight on a per-weight basis. It is also of note that the CBAM also allows for the combination of parts, and thus results in lower assembly costs.
Speed is also an important factor when it comes to the benefits offered by 3D printing technology and is one of the main advantages offered by Impossible Objects’ proprietary CBAM technology. Impossible Objects’ proprietary CBAM technology is capable of producing parts up to ten times faster than conventional fused deposition modeling (FDM) 3D printing. “Our CBAM process is a revolution in 3D printing, with faster speeds, better material properties and wider material selection,” Robert Swartz, chairman and founder of Impossible Objects explains. “This collaboration with Owens Corning will allow us to quickly experiment with and refine new materials to significantly lower cost and bring unprecedented options for additive manufacturing.” The CBAM process is compatible with a wide variety of materials including carbon fiber and fiberglass paired with PEEK, PA 6, PA 12, elastomerics and most other thermoplastics. Moreover, Impossible Objects machines are able to combine high-performance polymers like Nylon and PEEK with carbon fiber and fiberglass nonwoven materials. This means that they are able to print parts which are stronger, lighter, and have better dimensional accuracy as well as better temperature performance than what’s possible with conventional 3D printing methods.
By combining Impossible Objects’ CBAM process and Owens Corning’s fully integrated glass nonwoven manufacturing capabilities, the pair will be able to amplify the CBAM process to an industrial scale, and thus also allow the process to compete with other high-volume manufacturing methods like injection molding. Also, thanks to the elimination of long lead-times and tooling costs involved in injection molding, the CBAM process can eliminate the while enabling mass customization of parts. According to Dr. Chris Skinner, Vice President of Strategic Marketing, Composites, Owens Corning. “We have found the Impossible Objects technology and know-how potentially transformative for the conversion of some applications to composites. Because we believe it can be successful and deliver value to the market and our customers, we’ve entered into a joint agreement to support the development further.” Together, Owens Corning and Impossible Objects are aiding 3D printing technologies in revolutionizing the world in the same ways that computers and the Internet have revolutionized the way we live.
You can find out more on the Impossible Objects website HERE. What do you think about this partnership between Impossible Objects and Owens Corning ? Let us know in a comment below or on our Facebook, Twitter and LinkedIn pages! Sign up for our free weekly Newsletter here, the latest 3D printing news straight to your inbox!
$100 3D printer, "impossible objects" and Stratasys 3D printing trusses
News
In this episode, we'll talk about Kodama's new budget $100 3D printer, Impossible Objects' extraordinary high-performance 3D printing technology with reinforced polymer composites, and showcase 3D printing truss demonstrators from one of the largest 3D printer manufacturers, Stratasys Corporation. . nine0003
$100 3D printer
Kodama, founded by ex-Apple employee Michael Hasmann, is getting ready to take orders for the sub-$100 Obsidian desktop 3D printer. Last fall, Kodama ran a wildly successful crowdfunding campaign to support the $250 Trinius MFP in its base configuration, raising over $1. 5 million. The next offer is already in a household 3D printer at an even lower price. nine0003
The attractive design is designed to print objects up to 120x120x120 mm in size with a layer thickness of 50 to 350 microns at speeds up to 70 mm/s. In the basic version, the printer is designed for novice users, and therefore professional car designers were involved in creating the most understandable and convenient interface. The "professional" version will get Android compatibility and remote monitoring capability. Display, heated table and wireless interface will be optional, as upgrades. The start of the crowdfunding campaign is scheduled for June this year, and the developers promise to deliver the printer to the earliest customers for only $49.. You can follow the project at this link.
Impossible Objects
Impossible Objects is conducting closed beta testing of a CBAM (Composite-based Additive Manufacturing) hybrid plant designed to create composite polymer parts reinforced with carbon fiber, Kevlar, silk and other materials. The closest analogue, oddly enough, is the 3D printing technology with LOM paper from the Irish company Mcor. nine0003
The process begins with a selective application of adhesive to the reinforcing sheets at 600 DPI, after which the pattern is powdered with a powdered plastic binder. The sheets are connected to each other by thermal pressing, and excess material is removed by mechanical and chemical processing.
The technology allows you to easily combine various thermoplastics (including PEEK) and reinforcing fibers, demonstrating high productivity - at least 735 cu. centimeters per hour. The thickness of the layer depends on the sheet materials used and, as a rule, varies between 40-50 microns. The size of the construction area reaches 300x400x100 mm, although the maximum size along the Z axis is easily scaled to the required levels. nine0003
Stratasys 3D Printing Trusses
Stratasys showcased its vision for 3D printing trusses called "Continuous Build". The modular system is highly scalable and highly automated, including the removal of ready-made models and the transfer of current tasks to available cells in the event of a failure in one of the printers. The system is not yet available for sale, and demonstrators are being tested by OEM In'Tech Industries, advanced industrial design and manufacturing studio FATHOM, and the Savannah College of Art and Design. nine0003
In addition, the company announced its intention to sell 3D printers from startup Desktop Metal side by side with its own range. Recall that Desktop Metal has developed an “office” system for 3D printing of metal and alloy products, and Stratasys was one of the investors. Whether the startup will move under the corporate wing is not yet discussed.
Do you have interesting news? Share your developments with us, and we will tell the whole world about them! We are waiting for your ideas at news@3Dtoday. ru. nine0047
Follow the author
Follow
Don't want
6
A new 3D printing method allows you to create impossible glass shapes
November 26, 2019, 20:36 2500
ETH engineers have developed a new 3D printing method that creates incredibly complex porous glass shapes. Until now, the creation of such glass forms was technically impossible. All because of the complexity of the manufacturing process. nine0003
Only a handful of researchers around the world are developing glass 3D printing technology. One of the proposed methods involves traditional layer-by-layer printing. But this technology is very complex and requires working with extremely high temperatures and heat-resistant electronics. An alternative method involves the use of powdered ceramic particles that are shaped at room temperature and then sintered to form glass. This method is not so difficult to implement, but it is also not ideal. Both layer-by-layer and powder printing do not allow the creation of complex glass objects with very fine details or a porous internal structure. But this becomes possible thanks to a new technology developed in ETH. nine0003
The new method is based on stereolithography, one of the first 3D printing technologies developed back in the 1980s. The innovation lies in the material used. ETH engineers have developed a special resin that contains plastic and organic molecules that hold particles of the future glass. The researchers shared the results of their work in the latest issue of the journal Natural Materials.
Initially, the resin is processed using conventional stereolithography. That is, the resin container is exposed to ultraviolet rays. Where the rays hit the resin, it hardens. The plastic monomers “stick together” to form a rigid labyrinth-like polymer structure.