Gmu 3d printing
Mason Innovation Exchange
Welcome to the MIX
The MIX, located at Horizon Hall at George Mason University, hosts workshops, competitions, and accelerator programs. It is a Makerspace, Incubator, and Media Lab.
Monday through Friday: 10 am to 8 pm
The MIX will be closing on December 9th for Winter Break, and will reopen when classes resume January 23rd.
Explore Student & Faculty Projects
-
3D Printer - Prototype
Our 3D Printer created these cases to help track bats and other wildlife. We printed cases for a Biology Research Project to protect electronic listening devices that needed waterproof enclosures.
Read more
-
Utilize Virtual Reality
VR can be used to virtually travel to far away places, create all new environments, or learn in an immersive experience.
Book VR Time
-
Laser Cutter - 3D Art Project
Laser Cutting and engraving can be used to cut precise shapes and to engrave a variety of materials. Consider using it for artistic purposes or to create structural elements, chassis, boxes, etc.
Get Help with a Project
-
Soldering Project
We offer tools to work on electronics projects, from Arduino and Raspberry Pi microcontrollers, to electronics parts, soldering irons and other tools.
Register for Class
Space to Create & Innovate
Thank you for making the MIX an amazing space to create, innovate, and collaborate this year.
Get Involved
Create
Access to tools for hands-on prototyping, designing, experimenting, and creating.
Makerspace
Innovate
Mentors guide Mason innovators and entrepreneurs from ideation to customer discovery to company launch.
Incubator
Collaborate
A space for the Mason community interested in multidisciplinary sharing and creation of knowledge.
Media Lab
Space for Collaboration on Research & Projects
Space to Create Video, Audio, and VR Projects
Space for Speakers & Events
Space to Prototype & Build
Get started making your idea a reality.
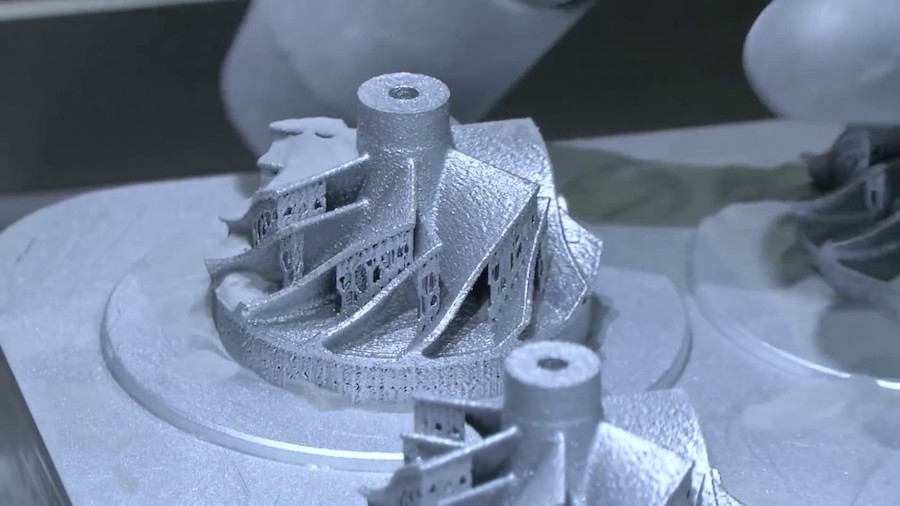
Contact Us
Services 2 — Mason Innovation Exchange
Explore Our Workshops and Events
Be in the MIX
-
Space to Collaborate
Hold events, hackathons, and more at the MIX.
Reserve a Spot
-
See Our Training Schedule
Workshop Schedule for Fall 2022 is now available to download
Download PDF
-
Master Classes
For advanced workshops, contact us.
Contact Us
Explore Upcoming Workshops & Events
Register for Training Classes Below
Explore Our Recent Workshops
Engineering & Wiring
Drone Workshop
LED Theater Project
Reach out to the MIX to see how you can incorporate the MIX into your class.
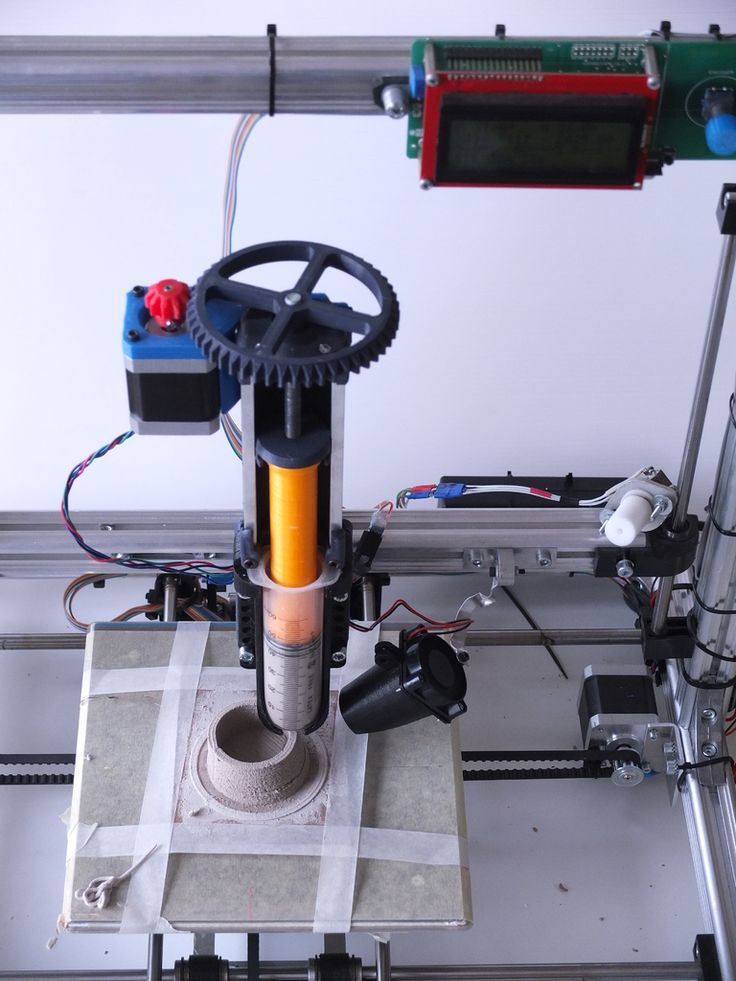
Orientation workshops for basic use and safety training of equipment, tools, and software offered at the MIX. Receive training on 3D Modeling and Printing, Textiles and Sewing, 2D Design for Laser Cutter and CNC, Video Editing, and VR.
Have questions? Email us at [email protected].
PDF Workshop Schedule
Contact The MIX for Your Next Event
Contact Us
3D printing of respirators and protective masks on Zortrax
printersThere are 5 areas of application of 3D printing in medicine: teaching students, making surgical instruments, pharmaceutical experiments, creating organs and biological tissues, building durable prostheses and anatomical models for preparing for operations.
3D printing laboratory at the Department of Pediatric Cardiology and Congenital Heart Diseases of the Gdansk Medical University of the State Medical University (Poland), is currently operating at full capacity. Scientists are busy releasing much-needed personal protective equipment such as face shields and respirators. In the current crisis, additive manufacturing has demonstrated its main advantage - the ability to quickly create prototypes and make new designs.
Quick prototyping
Protective masks and respirators are devices that are constantly on the face, so the comfort of products is as important as functionality. Moreover, there are many things that are simply difficult to predict at the digital design stage, so the rapid prototyping capability that Zortrax 3D printers provide is highly valued by medical device designers.
The GMU team of scientists can quickly produce several different designs and put them through real tests to show how new designs work and which ideas don't work. There are several factors that should be considered when determining the ergonomics of a design:
- how quickly the object can be made;
- how many auxiliary structures are needed for successful printing;
- what post-processing is required.
Standard surgical masks are designed to protect others from the wearer, not the other way around. Respirators are more complex devices that come with a case and filter. And they are made in order to protect the owner from infection. The SARS-COV-2 virus is only 120 m long. For staff working with patients with COVID-19or persons suspected of being infected, the filter must meet the requirements of HEPA E11 (or higher) in order for the respirator to meet established standards. Since there is a huge shortage of masks worldwide, manufacturers are using E12 class HEPA filters as an alternative.
It is important that such personal protective equipment should allow the person to breathe freely even during periods of intense physical exertion. When masks allow too little air to pass through, users will feel comfortable at rest, but will not be able to function properly when exercising.
This is why rapid prototyping has become so important. You can quickly print several different designs on Zortrax machines, install filters, and hand them over to testers for real-life testing. So you can immediately determine which design suits best.
Rapid production
Before the pandemic, the laboratory of the Polish Medical University had Zortrax M200, M200 Plus printers, as well as Inventure and Inkspire models. The team recently received a Zortrax M300 printer for 3D printing of respirators as part of the brand's assistance to those affected by COVID-19. Volunteer students quickly mastered the equipment and independently optimized the design and printing parameters.
Scientists can now maintain ongoing production on the M200 while testing new respirator prototypes. With advanced hardware, impressive daily throughputs can be achieved. The unit is designed to print 20 face shields every day. Taking into account the previously available equipment, the total production capacity has increased to 44 pieces of PPE per day. This efficiency is made possible by a relatively simple product design.
The Inventure 3D Printer used to print respirators exclusively in dual extrusion mode. This meant that 2 strands of melted plastic were used: one for the model and the other for the soluble support structures. The applied technology increases the accuracy of construction and facilitates the removal of supports, but increases the time of work. The single extrusion mode, recently implemented in all Zortrax Inventure 3D printers, has played a key role in improving productivity. The devices are optimized to use as few supports as possible, which greatly improves performance because no time is wasted switching between support threads.
The results of printing respirators on the printer were first evaluated by staff working in the departments of pediatric cardiology and congenital heart defects, pediatrics, hematology and oncology, the clinical cardiology center, and the angiographic laboratory of the hospital at GUM. The demand for personal protective equipment is huge, and the 3D printed equipment made at the medical university is now used in many hospitals in the country. The printed face shields have been praised by users for both design and functionality.
After that, a team of scientists took up the creation of components to maintain the sterility of ear thermometers. Here, medical 3D printing has once again solved a problem that doctors face all too often during a pandemic. The equipment consists of a polymer ring and a sheet of foil that are bonded together and used to prevent direct contact of the thermometer with the patient's body. There are currently no such components available for sale. 3D printers print the rings, and volunteers apply foil to them by hand.
report about construction 3D printing in Russia
News
a developer and manufacturer of construction 3D printers based in Yaroslavl and successfully operating in the Russian and foreign markets. The narrator is the head of the enterprise Alexander Maslov.
In already completed projects, AMT-Spetsavia printed houses both on top of the foundation and in blocks in workshop conditions. In the video, Alexander clarifies this point, which is related, among other things, to weather conditions.
“If we print a prefab in the shop, then [the process] does not depend on weather conditions in any way. Both winter and summer are about the same temperature, which is good. When you print on a foundation (which everyone loves because it eliminates the assembly step, which is quite a lot of time and money), then of course the weather conditions come into play. The construction season is usually from spring to autumn. It's hard to print in very hot weather because the long, thin concrete walls start to crack. To do this, various additives are introduced into the concrete or the printing is transferred to a more convenient night time. Comfortable temperatures are from spring to autumn, from about 5°C to 25°C. Of course, precipitation and strong winds have a very strong influence - the structure still has windage, and there is a slight shift in the printed layers. Light rain is not a hindrance, in heavy rain the wet concrete will erode, so you need to keep an eye on the weather. As a rule, an hour and a half before the approach of a thunderstorm, we stop printing, wash the equipment and wait. There is another option to close it with some kind of canopy or a greenhouse, but it’s actually easier to miss two hours of printing than to fence the roof, ”said Alexander.
A 100 square meter 3D printed box takes thirty to thirty five hours to build. Fixed formwork is printed, which can be poured with foam compounds after one or several days, depending on the brand of concrete.
Alexander did not dare to give an exact figure, since the pace of work for each team is different, but in general, a small house can be built in about a month, including pouring the foundation and curing, 3D printing of formwork, inserting windows, doors, and so on.
According to Alexander, about forty companies are currently operating in the global market for 3D construction printing — some are engaged in the development and production of equipment, some directly in construction, some combine them. According to Alexander, AMT-Spetsavia accounts for 70% of the world production of construction 3D printers, with half of them going to Russian customers. In six years, the company has sold two hundred and forty pieces of equipment to sixteen countries.
AMT-Spetsavia produces portal 3D printers of two main types - workshop systems and larger options for outdoor work. The former are used in 3D printing of small architectural forms and building blocks, while the latter are installed on construction sites and print formwork directly on top of foundations.
The working area of such large-scale systems varies from one hundred and twenty square meters with the possibility of erecting two-story structures up to four hundred and twenty square meters. The latter can theoretically build buildings up to twenty-six stories high, although in practice such grandiose projects have not yet been implemented.
Details in the report of the channel "Low-Rise Country":