Fizik 3d printed
Best 3D-printed saddle: A Fizik vs Specialized head-to-head
Image 1 of 3
Where the Specialized features CLIP technology (Continuous Liquid Interface Production) the Fizik saddles use Digital Light Synthesis (DLS) - both methods are essentially the same (Image credit: Aaron Borrill)Unlike the other two saddles that feature a more traditional black colour, the Fizik Antares Versus Evo 00 Adaptive uses a colourless, off-white 3D-printed lattice (Image credit: Aaron Borrill)A close up of the various 3D-printed textures (Image credit: Aaron Borrill)The 3D-printing concept is a hugely popular phenomenon in the cycling world at present with everything from helmets and gloves through to components and even bikes utilising this new technology - all in the quest for the perfect fit. We've already covered both the 3D-printed Fizik Antares Versus Evo 00 Adaptive and Specialized S-Works Power with Mirror saddles in detail and came away thoroughly impressed by what both options offer cyclists as far as the best road bike saddles go. However, the same question keeps coming up: which of the two is the better option? Well, to complicate matters even further, we've also included the newest addition to Fizik's Adaptive range - the all-black Antares Versus Evo R3 - and pitted all three options against each other to establish which saddle truly is the best 3D-printed saddle currently on the market.
Image 1 of 7
The 00 Adaptive saddle's unidirectional carbon fibre makes for a refined appearance (Image credit: Aaron Borrill)The Versus Evo R3 Adaptive has eschewed a carbon-fibre monocoque in favour of a plastic platform (Image credit: Aaron Borrill)The Mirror's platform is constructed from TeXtreme fibres (Image credit: Aaron Borrill)The 00 Adaptive's detailing is exquisite with various textures, shapes and surfaces on offer (Image credit: Aaron Borrill)The Versus Evo R incorporates a brace of diffuser-style vents at the rear (Image credit: Aaron Borrill)The Mirror's sheath supplies a superb blend of grip - ideal for when things get wet and damp (Image credit: Aaron Borrill)Apart from the white 'S' logo nestled under the lattice webbing on the back of the saddle, there are no other visual markings that allude to its maker (Image credit: Aaron Borrill)Fizik unveiled the Antares Versus Evo 00 Adaptive saddle at Eurobike in 2019 amid much fanfare. Sporting a peculiar-yet-striking milky-lime-green colourway, it turned many heads, but some argued the 'colourless' lattice lacked visual impact. While polarising in appearance, it still managed to conjure a sense of curiosity and intrigue - particularly here at Cyclingnews. The 00 however, fails to effectively complement the majority of contemporary bicycle colourways, not to mention has a propensity for showing up dirt, mud and grime. Closer examination, however, reveals a raft of incredible stylistic touches that can easily be overlooked. For instance, the saddle is as much about texture and form as it is function. The level of detailing is exquisite, and the way the various textures, shapes and surfaces work together is truly impressive - carbon fibre is used liberally throughout its construction while the maker's name and model type is subliminally fashioned into the centre channel that separates the 3D-printed cushion.
Save for the stealthy-looking black facade the Fizik Antares Versus Evo R3 Adaptive is virtually identical to the 00 model pictured here, retaining the same shape, central channel and zonal cushioning. The disparities only materialise once you turn it over and examine the platform and rail configuration in detail. Here you'll notice the Versus Evo R3 Adaptive has eschewed a carbon-fibre monocoque in favour of a plastic platform so the look and feel is a little different, as are the rail mouldings which are filled with hollow Kium rails. Other notable details include a brace of diffuser-style vents at the rear, an aesthetic touch of course.
- Fizik Antares Versus Evo 00 Adaptive saddle review
Specialized's S-Works Power with Mirror saddle represents the complete antithesis of Fizik's Adaptive range and, while it utilises a black-on-black colour palette to maximum effect, it hasn't been designed as an out-and-out performance saddle. As a result, there's a greater surface area of padding on offer and the snub-nose design lends itself more towards comfort. Despite the white 'S' logo nestled under the lattice webbing on the back of the saddle, there are no other visual markings that allude to its maker - a nice touch for those who ride rival brands. Visually, the Mirror shares its design blueprint with the Power and Power Arc models - a proven recipe when it comes to sit-bone support and pressure dissipation. It's only under intense scrutiny that the differences between its stablemates come to the fore and that's because Specialized has treated the Mirror with an outer sheath to give the illusion of a traditional perch. In fact, of the three saddles gathered here, the Mirror takes on the most resolute - read traditional - appearance as a package; the sheath, 3D-matrix, carbon rail and undercarriage infrastructure are just superb.
- Specialized S-Works Power with Mirror saddle full review
Image 1 of 5
At 153g, the 00 Adaptive is the lightest perch here (Image credit: Aaron Borrill)At 215g the Versus Evo R3 ditches the lavish carbon-fibre garnishing for plastic and metal (Image credit: Aaron Borrill)Specialized's S-Works Power with Mirror saddle tips the scales at 190g (Image credit: Aaron Borrill)Save for the stealthy-looking black facade the Fizik Antares Versus Evo R3 Adaptive is virtually identical to the 00 model (Image credit: Aaron Borrill)The Versus Evo R3's plastic rail mouldings are filled with hollow Kium rails.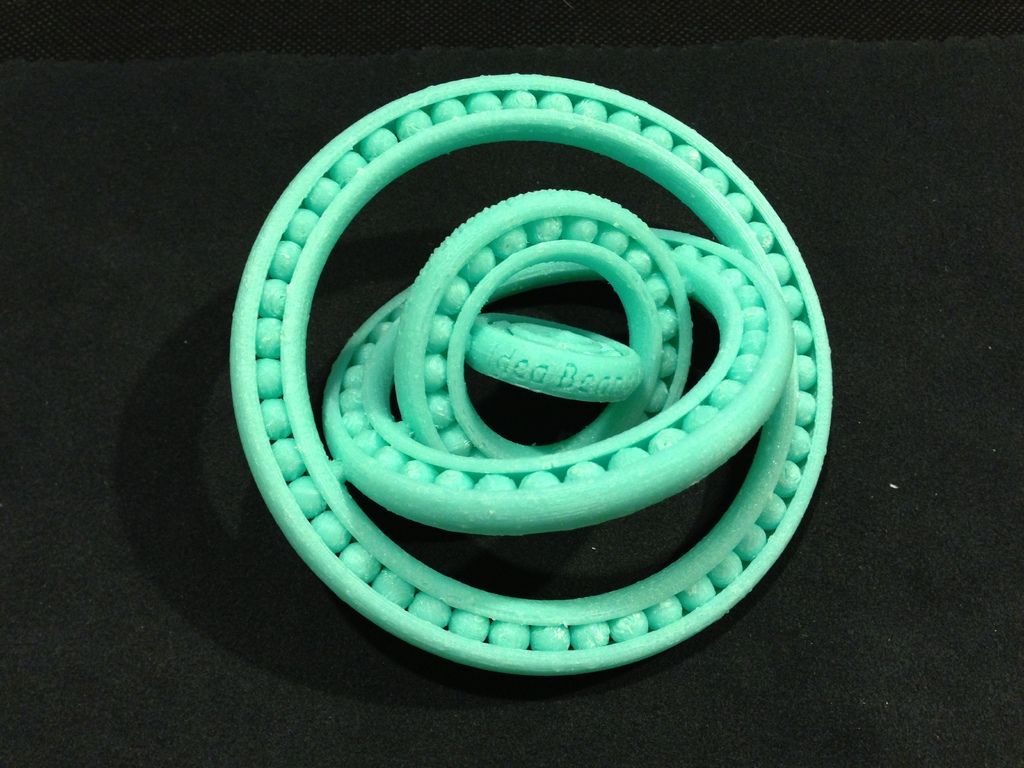
Specifications
On paper, the Specialized Mirror runs neck-and-neck with the 00 Adaptive. They both feature carbon-fibre monocoques and rails and weigh less than 200 grams each - a respective 190g and 153g to be exact. The carbon fibre used in the manufacture of these two saddles, however, is quite different: the Mirror uses TeXtreme fibres while the Antares 00 Adaptive makes do with a unidirectional composite, a far more attractive and refined recipe in my opinion.
While the Versus Evo R3 is the heaviest perch here at 215g and ditches the lavish carbon-fibre garnishing for plastic and metal, its 3D-printed lattice is manufactured using the same principles as its lighter compatriots. In fact, all three saddles are manufactured by the same company - Carbon, a 3D printing specialist based out of California. This method uses Digital Light Synthesis (DLS), a photochemical process that balances light and oxygen to 3D print the lattice structure before curing in a forced-circulation oven.
- Best road seatposts : Lightweight, compliance-boosting seatposts for your road bike
- Best bar tape : Grippy, comfortable and durable handlebar tape to protect your palms
- Best road handlebars : How to choose the best handlebars for your bike
- Best road bike pedals : Our pick of the best performance road bike pedals
Both Fizik and Specialized have poured years of research into these saddles and claim similar levels of tunability when it comes to tailoring the density, dampening and elasticity of the lattice polymer, the results of which far surpass anything achievable from a foam equivalent. All three options are comfortable saddles but its the 00 Adaptive and Specialized Mirror that stand out as far as specification and materials are concerned.
Image 1 of 4
A closer look at the undercarriages of each saddle (Image credit: Aaron Borrill)Cheaper Versus Evo R3 Adaptive vs Versus Evo 00 Adaptive (Image credit: Aaron Borrill)The Specialized Power Mirror saddle and its TeXtreme carbon-fibre weaves (Image credit: Aaron Borrill)Like the 00 Adaptive, the rail configuration is more refined and integrated than the Versus Evo R3 (Image credit: Aaron Borrill)Comfort and performance
It's appreciably difficult to critique a saddle, as attributes such as comfort and performance are subjective. I for one am a fervent proponent of the longer, flatter-style road bike saddle and the Fizik Arione has long been my go-to perch of choice. However, after spending a lengthy spell testing the trio of 3D-printed saddles gathered here, it's clear that Fizik and Specialized have aimed their products at opposite ends of the performance spectrum.
For starters, the Mirror saddle with its snub-nose design and broader 143mm width is the far more comfortable option of the three. I spent a good portion time with it fixed atop the new Specialized S-Works Diverge and found it offered good all-round support and cushioning. It's by no means a racy proposition - instead, it's aimed squarely at providing comfort and support on longer rides yet can still quite easily double up as a racing option depending on whether it's compatible with your ischial tuberosities. While it doesn't quite suit my narrow sit-bones, shifting to the front provided the aggressive position I enjoy - helped along by the 3D cushion's low-speed, softer compression around the nose. I did, however, experience some numbness during the latter part of a 120km ride but again, this could be down to my sit-bone structure. The outer sheath I mentioned earlier supplies a superb blend of grip - ideal for when things get wet and damp - and it's easier to keep clean as a result.
As far as out-and-out race saddles go the Antares Adaptive range offers some of the better options around. As mentioned in my standalone review, the Adaptive saddle does well to balance comfort and performance - the 00 is supremely light but offers the same zonal cushioning as its heavier Evo R3 sibling so there's nothing separating the two in that regard. That said, the differences come by way of pliancy. The Evo R3 and its plastic chassis have a tendency to flex, especially over choppier surfaces that can sometimes 'bottom out' the cushioning - but that's not necessarily a bad thing as this actually helps a little when it comes to comfort. The 00 Adaptive is without a doubt the stiffest saddle here boasting a direct ride quality that is rich in feel and feedback. While this may not appeal to everyone, those who race or at least enjoy pushing the boundaries when it comes to lateral adhesion will appreciate the high-definition-like feedback and communication it offers.
Image 1 of 3
The snub-nose, wider design of the Specialized S-Works Power with Mirror saddle suits those who favour comfort over all-out performance (Image credit: Aaron Borrill)The Versus Evo R3 might be a little heavier than the 00 Adaptive but it's just as precise when it comes to pressure dissipation and overall function (Image credit: Aaron Borrill)Polarising in appearance, the Fizik Antares Versus Evo 00 Adaptive saddle is all about high performance (Image credit: Aaron Borrill)So which is the best 3D-printed saddle?
Not one of the three options pictured here is what you'd describe as an affordable road bike saddle. These 3D-printed perches will appeal to those looking to eke out every last gain when it comes to weight savings and communication levels, not to mention find favour with the early-adopting trendsetters.
There's no distinct standout here as both companies have catered for two different audiences. If you're looking for a cutting-edge 3D-printed, performance-infused saddle, the Antares Versus Evo 00 Adaptive can't be ignored. On the other end of the spectrum sits the Specialized Power Mirror which favours comfort but still offers a high degree of all-round performance and top-shelf aesthetics. Both these options, however, are very, very expensive which leaves the Versus R3 Adaptive.
At £249 the Fizik Antares Versus R3 Adaptive saddle is a whopping £141 cheaper than its 00 Adaptive stablemate but comes with a 62g weight penalty and sans the fancy carbon fibre trimmings. It's also £101 less than the equally dolled up Specialized Power Mirror saddle and weighs a scant 23g more. So while it's a little heavier than the 00 and Mirror saddle it still benefits from the same 3D-printed philosophy, performs just as well in respect to comfort/performance and comes in at a much cheaper price point.
The Fizik Antares Versus R3 Adaptive saddle gets my vote.
Today's best road bike saddle deals
Fizik Arione R3
$149
$94.85
View
See all prices
Reduced Price
SELLE SMP WELL SADDLE
$144
$120.24
View
See all prices
Reduced Price
SPECIALIZED POWER PRO SADDLE
$325
View
See all prices
Pro Stealth saddle
$129. 95
$94.98
View
See all prices
Reduced Price
Tech specs:
Fizik Antares Versus Evo 00 Adaptive
- Price: £369.99
- Weight: 153g (actual)
- Dimensions: 139mm
- Rails: Carbon
- Shell: Carbon
- Cushion: Digitally printed polymer lattice
- Colours: Black/green
Specialized S-Works Power with Mirror
- Price: £350
- Weight: 192g (actual)
- Width: 143mm
- Rails: Carbon
- Shell: Carbon with plastic cornicing
- Cushion: Digitally printed polymer lattice
- Colours: Black
Fizik Antares Versus Evo R3 Adaptive
- Rrice: £249
- Weight: 215g (actual)
- Width: 139mm
- Rails: Kium
- Shell: Plastic
- Cushion: Digitally printed polymer lattice
- Colours: Black
Thank you for reading 5 articles in the past 30 days*
Join now for unlimited access
Enjoy your first month for just £1 / $1 / €1
Already have an account ? Sign in here
*Read any 5 articles for free in each 30-day period, this automatically resets
After your trial you will be billed £4. 99 $7.99 €5.99 per month, cancel anytime. Or sign up for one year for just £49 $79 €59
Join now for unlimited access
Try your first month for just £1 / $1 / €1
Already have an account ? Sign in here
Aaron was the Tech Editor Cyclingnews between July 2019 and June 2022. He was born and raised in South Africa, where he completed his BA honours at the University of Cape Town before embarking on a career in journalism. Throughout this career, Aaron has spent almost two decades writing about bikes, cars, and anything else with wheels. Prior to joining the Cyclingnews team, his experience spanned a stint as Gear & Digital editor of Bicycling magazine, as well as a time at TopCar as Associate Editor.
Now based in the UK's Surrey Hills, Aaron's life revolves around bikes. He's a competitive racer, Stravaholic, and Zwift enthusiast. He’s twice ridden the Cape Epic, completed the Haute Route Alps, and represented South Africa in the 2022 Zwift eSports World Championships.
Height: 175cm
Weight: 61.5kg
Rides: Cannondale SuperSlice Disc Di2 TT, Cannondale Supersix Evo Dura-Ace Rim, Cannondale Supersix Evo Ultegra Di2 Disc, Trek Procaliber 9.9 MTB
Fizik extends 3D printed saddle range with new Argo Adaptive model
0Shares
US-based cycling equipment manufacturer Fizik has launched its latest 3D printed saddle, the Argo Adaptive short-nose saddle.
Making its debut at the Sea Otter cycling show, the saddle features a 3D printed lattice cushioning manufactured using Carbon’s Digital Light Synthesis (DLS) 3D printing technology, which is designed to improve comfort and optimize a rider’s posture.
The Argo Adaptive short-nosed saddle’s 3D printed lattice. Photo via Fizik.Fizik and 3D printing
The Argo Adaptive is the latest addition to Fizik’s 3D printed saddle range, which began with the launch of the Antares Adaptive model in 2019. The firm worked with Carbon to produce the 3D printed saddle using the latter’s DLS technology, which at the time was said to have unlocked “a new era” in saddle design and manufacturing by Fizik Brand director Luca Mathia Bertoncello.
The partnership with Carbon was born out of the firm’s ‘Concepts’ initiative, a cross-disciplinary consortium of leading industry experts and academics that aims to position Fizik at the forefront of cycling innovation.
By leveraging 3D printing for the design of its saddles, the Fizik team was able to address elements such as power transfer, shock absorption, stability, and comfort according to a cyclist’s needs.
Fizik’s ‘Adaptive’ 3D printed bike saddle. Photo via Carbon.Carbon DLS for consumer products
Carbon’s DLS 3D printing technology is an SLA-based process that uses digital light projections in tandem with oxygen-permeable optics to cure photopolymer resins into 3D parts. In addition to Fizik, the technology has been leveraged by multiple big-name brands within their consumer products to yield performance benefits under the ‘Crafted by Carbon’ tagline.
For instance, Carbon has worked with fellow bike manufacturer Specialized to 3D print its S-Works Power Saddle in an attempt to establish DLS as the standard in saddle technology, and more recently with backpack manufacturer Osprey to produce a 3D printed lumbar pad for the firm’s new UNLTD pack series.
Perhaps Carbon’s most well-known partnership, though, is with sportswear giant Adidas, with whom it has created the 3D printed 4D midsole, the 4DFWD. The latest version of the 4DFWD was made available to the public in August last year, and was worn by athletes at the 2020 Olympic Games in Tokyo.
The S-Works Power Saddle with Mirror Technology. Photo via Carbon.The Argo Adaptive
Nearly three years on from the Antares Adaptive launch, Fizik has unveiled its second 3D printed saddle, the Argo Adaptive. The Argo is the firm’s short-nosed model, a shape that is becoming increasingly popular on road bikes for riders wishing to maintain an aggressive riding position for extended periods of time.
The aim of the saddle shape and 3D printed adaptive cushioning is to keep the rider locked in place and avoid unnecessary changes of position. Fizik and Carbon have once again combined their expertise to optimize the saddle’s performance with a DLS 3D printed lattice cushioning, which is designed to provide more or less cushioning in certain areas to adapt to different riding positions.
The lattice structure achieves this while also resulting in a lighter saddle than conventional foam cushion pads. The zonal cushioning within the 3D printed lattice reduces the maximum pressure experienced by the rider and accounts for varying sit bone widths to ensure comfort.
The Argo Adaptive is being offered in two widths, 140mm and 150mm. The saddle is available in two models, an R1 with carbon rails, and a cheaper R3 with Fizik’s proprietary K:ium steel alloy rails priced at $299 and $259 respectively. Consumers will be able to purchase their Argo Adaptive at the end of April.
Subscribe to the 3D Printing Industry newsletter for the latest news in additive manufacturing. You can also stay connected by following us on Twitter and liking us on Facebook.
Looking for a career in additive manufacturing? Visit 3D Printing Jobs for a selection of roles in the industry.
Subscribe to our YouTube channel for the latest 3D printing video shorts, reviews, and webinar replays.
Featured image shows the Argo Adaptive short-nosed saddle’s 3D printed lattice. Photo via Fizik.
Tags 4DFWD adidas Antares Adaptive Argo Adaptive Carbon Carbon DLS fizik Luca Mathia Bertoncello Osprey Osprey Fitscape Lumbar S-Works Power Saddle Sea Otter Specialized
Hayley Everett
Hayley is a Technology Journalist for 3DPI and has a background in B2B publications spanning manufacturing, tools and cycling. Writing news and features, she holds a keen interest in emerging technologies which are impacting the world we live in.
3D printing in high energy physics / Sudo Null IT News about cats).
Today I will tell you about 3D printing in relation to solving several problems, one way or another related to high energy physics.
About a month ago, Fermilab Today, a daily magazine of the Enrico Fermi National Accelerator Laboratory, published an article about the hard everyday life of engineers and scientists of this laboratory, and 3D printing as a remedy for all problems.
So, back in 2008, a junior researcher at the Fermi Laboratory, Mauricio Lopes, began creating a model of a kind of spiral solenoid made of cardboard to justify the feasibility of the concept of the model being developed. This process (quite expectedly) was very slow, Lopez's patience snapped, and he attended to the purchase of a 3D printing machine. In October 2009, the laboratory received a long-awaited 3D printer for printing plastic models. And, as they say, away we go - both plastic prototypes began to be printed (here, for example, a photograph of prototypes of superconducting cables made of stannide - Nb3Sn alloy), and metal parts (photo of cores for winding superconducting magnets: on the left - obtained using 3D printing, on the right - made in the traditional way).
A week ago, an interesting seminar was held at CERN, where a report was read on the topic “New 3D printing facility in the laboratory of polymeric materials. Possibilities and limits of its application. You can view the slides here.
The following 3D printing technologies are currently used at CERN:
- Fused Deposition Modeling. A three-dimensional model is formed by layer-by-layer formation from a fusible thread, which then solidifies. The most common 3D printing technology used in almost all 3D printers in the lower price range.
- Laser stereolithography, or Laser Stereolithography. A method for obtaining three-dimensional models from a special liquid - a photopolymerizable composition.
As it is easy to guess from the name, the solidification of the photopolymer occurs under the influence of laser radiation.
- Selective Laser Sintering. The process of obtaining a product is similar to the previous one, with the only difference that the working material in this case is a powder (metal or plastic). The model is also formed layer by layer, by a series of successive laser irradiations.
In the same report, a photograph of the model and a photograph of the final part obtained by laser stereolithography are presented.
It is clear that products made by these methods always have certain disadvantages in relation to parts obtained by traditional processing (lower strength and rigidity of the product material, lower manufacturing accuracy, low resistance to aggressive environmental conditions, etc.). Despite these shortcomings, parts “printed” on local 3D printers are successfully used in such unexpected areas as low-temperature and vacuum technology, high-voltage electrical equipment, and even scintillator lenses.
Also at CERN, research has been carried out on the following properties of "printed" products from various materials:
- mechanical strength at normal temperatures
- mechanical strength at low (~77 K) temperatures
- heat shrink
- high voltage electrical resistance
- mechanical vibration resistance
- and even changes in mechanical properties under the influence of radiation exposure.
Finally, let's take a look at what 3D printers print even at the Large Hadron Collider itself:
- RF antenna plastic shell
- high voltage connectors for transverse beam stabilizer amplifier
- details of windings of superconducting solenoids.
In other scientific institutions of the planet, things are similar: 3D printing is actively used for prototyping, the share of metal “printing” is growing, the expansion of the scope of 3D printing is welcomed, for which, through the efforts of the laboratories themselves, research is being carried out on the applicability of printed products in certain areas. Modern 3D printing is not just gadgets for geeks that can print an exclusive case for iPhone or a beautiful case for Raspberry Pi, but quite a serious and useful tool for prototyping and single-piece production of a wide variety of and, most importantly, responsible products. Ask physicists, they will confirm.
Sources:
http://www.fnal.gov/pub/today/archive/archive_2013/today13-08-21.html
http://indico.cern.ch/getFile.py/access?resId=1&materialId =slides&confId=271447
http://thescience.ru/2013/09/20/3d-printing-in-high-energy-physics/
basic concepts in the field of intensity, studying extremely rare processes, for example, the transformation of muons into electrons. The scientific community took up this issue back in 1940s. It is believed that studying this problem is the key to understanding why particles from one category turn from heavy to light, moving to a state with a more stable mass.
Simplifying the concepts as much as possible, we can say that electrons imply an action (for example, such an action as providing light in a house or powering a computer with energy). On the other hand, muons are a more “heavy” form of electrons, but it is not yet fully understood how these particles relate to each other. Physicists assume that by understanding the relationship between muons and electrons, they will be able to understand the essence of the electrons themselves.
A team of researchers is currently working on a tracking system they have named Mu2e. We are talking about a device consisting of small low-power boards that are located at the ends of the "tubes". Cooling lines are a key element of this arrangement, as they allow the removal of heat that would otherwise fill the necessary vacuum. Achieving the necessary cooling was not easy, since there was very little space in the system to accommodate such lines.
Designers have also experienced that machining curved metal parts with oblong tube holes has been difficult and expensive until recently. Now this problem has been solved with the help of 3D printing, which allows the production of a high-tech version of parts from transparent plastic.
The researchers intend to use a 3D-printed plastic prototype to run an electric charge through a tube and "pinch" it with a magnet, much like playing guitar strings. By measuring the received vibration, scientists can determine the benchmarks for the tube to maintain its original straight position throughout the experiment.
The idea of the Mu2e project is to follow how the muon turns into only one electron, without emitting additional particles. In theory, physicists believe that this is possible, but no one has been able to observe this process in practice.
Such an experiment should be about 10,000 times more accurate than previous ones. The task of scientists is to follow the rapid movement of electrons in order to fix the characteristic energy release of 105 megaelectronvolts that occurs during the decay of the muon. In practical terms, this means that Mu2e developers need to build a detector using the minimum amount of material. There must be so little material that, with a certain degree of relativity, one can say that it does not exist at all.