3D printing center of excellence
3D Printing Center of Excellence
At SSM Health Cardinal Glennon Children’s Hospital, we provide world-class health care with compassion and excellence. State-of-the-art technology, combined with clinical professionals who are leaders in their fields, ensures the best possible care for our young patients.
The use of 3D printing has long been recognized as a valuable tool in health care. By using advanced software to process standard 2D images from CT scans and MRIs, doctors at SSM Health Cardinal Glennon are creating anatomically-accurate models of various organs and structures, including hearts, kidneys, blood vessels, jaws and skulls, to assist them in planning complicated, high-risk surgeries on children of all ages.
Generous community support has enabled us to launch our very own 3D Center of Excellence at SSM Health Cardinal Glennon. By having a 3D printing lab onsite, models are created in a matter of hours, instead of the days or weeks it takes when using an outside lab. In many cases, sooner is better when planning and performing surgical interventions, such as a traumatic injury.
3D printers work much like standard office printers, but instead of ink, our 3D printers use surgical-grade plastic resin. Over the course of several hours, layer upon layer of material is laid down until an accurate model is created. Physicians then use these models to visualize and plan complex surgeries, and size their instruments if necessary, before the child even enters the operating room.
The added benefit of using surgical-grade material is that models can be sterilized and taken into the operating room, where surgeons can take continual measurements during surgery, ensuring even greater accuracy.
3D modeling is also being used to educate the next generation of physicians at SSM Health Cardinal Glennon. Over time, we plan to build a library of 3D models of different types for medical students and residents to study.
In addition to the medical, surgical and educational applications, doctors use 3D models to explain procedures to anxious parents, giving them a clearer picture of their child’s condition and the surgeon’s plan for addressing the issue. In times of stress and uncertainty for parents, the use of 3D models has the ability to set their minds at ease.
3D printing is a relatively new technology and is ever-evolving. As a result, it is very expensive. However, the fact that this science is applicable to many fields of pediatric medicine, our dedicated 3D Center of Excellence is a wise investment.
Ongoing costs of running the Center include:
- A full-time technician to operate the 3D printers and assist doctors with making models.
- Ongoing technology upgrades, as newer software and hardware becomes available.
- The cost of materials to make each model. Currently, 3D modeling is not covered by insurance, and we create the models at no cost to families. Each model costs between $100 and $1,000, depending on its size and complexity.
3DCoE – 3D Center of Excellence
Posted on by Jackson Moreland
“Bringing Opportunity and Innovation to America’s Workforce” Welcome to the 3D Center of Excellence. Founded in Detroit, our mission is to provide education and opportunity to all people in the fields of 3D Printing and beyond. 3D Printing and its applied form Additive Manufacturing are rapidly becoming the dominant force in equipment manufacturing, in the United States and around the globe. With the rise of these new technologies, there is also an abundance of opportunities…
Read More
Posted in News Tagged 3D Printing, Additive Manufacturing, Education, Higher Education, Launch, News, UpdatePosted on by Al Ranger
Global Industry Trends, Growth, Share, Size and Forecasts to 2022 According to New Research 3D (three Global Industry Trends, Growth, Share, Size and Forecasts to 2022 According to New Researchdimensional) technology has emerged as a technology that is being used in animation films, motion pictures, displays, imaging, and other products; which have finally extended to the other functions such as three-dimensional modeling, designing, and rapid prototyping. 3D technology provides illusion effects of depth perception; and…
Read More
Posted in 3D Pioneers 1 CommentPosted on by Katylin Jane
Researchers at the University of Michigan (UM) are implementing a new orthotics and prosthetics outfitting system: 3D printed assistive devices that will be customized to individual patients’ needs and reach them faster than ever before. Engineers and clinicians at the UM College of Engineering and Orthotics and Prosthetics Center say their new cyber manufacturing system is a vast improvement over traditional production methods. Currently, assistive device users must wait days or even weeks for essential…
Read More
Posted in 3D Medicine, 3D Pioneers, 3D Printers 228 CommentsPosted on by Katylin Jane
Back in 2013, Oxford Performance Materials’ biomedical division got FDA clearance for the first 3D polymeric implant for cranial reconstruction. A year later it won clearance for its 3D printed facial device. What makes them unique is that they are patient-specific. In fact, OPM Biomedical is the first and only company to receive FDA 510(k) clearance for 3D printed patient-specific polymeric implants and has a total of four 510 (k) clearances. In doing so, the…
Read More
Posted in 3D Medicine, 3D Printers 1 CommentPosted on by Al Ranger
Taubman College of Architecture and Urban Planning Budding young architects get a chance to kick start their dreams and take the first step towards building their future at the University of Michigan’s ArcStart summer program. Run by the university’s renowned Taubman College of Architecture and Urban Planning, ArcStart offers high school students the opportunity to take college-level classes in design, drafting, modeling and other related areas while living on the University of Michigan’s Ann Arbor campus…
Read More
Posted in 3D PioneersPosted on by Amy Banks
The future of running shoes is changing. Photo: iStock 3D printing has long been seen as a tool for making small tools for personal use but some large retailers and smaller-scale businesses have started to delve into using 3D printing for mass-market distribution of customised products. For their first products, they’ve started on the ground level – literally. Some companies are talking about the possibility of having insoles, or even entire shoes, printed from stores or…
Read More
Posted in 3D Printers 1 CommentPosted on by robertkakos
New York – he was held on December 9 at the Star Room of the restaurant Le Cirque in Manhattan breakfast organized by GEI in honor of Dr. Antonio Bernardo, Associate Professor of Neurosurgery and Director of the Laboratory for Innovative Surgery Microsurgery of the skull Weill Cornell Medical College. The GEI, Italian Representatives Group, for years combines the most authoritative representatives of Italian companies in America, and this time wanted to reward with “GEI…
Read More
Posted in 3D Pioneers 265 CommentsPosted on by robertkakos
GRASS LAKE, MI – Joey Cabana placed two wires into pegs on a circuit board. After some code tweaking, a small, blue light began to glow, seemingly in sync with the excitement that lit up the 10-year-old’s eyes. This LED light experiment is part of George Long Elementary School’s latest program focused on STEM, or science, technology, engineering and math subjects. STEM teacher Mike Arbuckle has brought these science and engineering-focused programs into George Long classrooms. Arbuckle…
Read More
Posted in 3D STEM 243 CommentsPosted on by robertkakos
Sumter, SC (WLTX) — In just a few hours, students at Alice Drive Middle School in Sumter are changing strangers lives forever. The STEM Certified school was granted a 3D printer last year. Rather than use it to make items for themselves to enjoy, Library Media Specialist Elma Strong chose to partner with the nonprofit E-Nable and start making prosthetic hands. “When I first heard about it, it just gives you the feeling, a great…
Read More
Posted in 3D STEMPosted on by robertkakos
Michael Peirone, a fourth-year biomedical engineering student at the University of Victoria, displays a 3D printed hand that engineers have produced for amputees in developing countries, during the inaugural B. C. Tech Summit in Vancouver, B.C., on January 18, 2016. (Darryl Dyck / The Canadian Press) VANCOUVER — Virtual reality could be the next instrument in a hospital’s arsenal of cost-fighting tools as nurse teams demo a surgery simulator that makes training feel like a video…
Read More
Posted in 3D Medicine 1 Comment 1 2 »10 reasons to contact the prototyping center
Analytics and business
Rapid prototyping
Experts recommend
Author: Andrey Kombarov
Author: Andrey Kombarov
1. Supply chain management | 2. Large selection of materials | 3. Variety of colors and finishes | 4. Large format 3D printing | 5. Professional quality parts | 6. Cost reduction | 7. Save time | 8. Scalability | 9. Expert advice and assistance | 10. Services of professional designers
The 3D printing services business is growing faster than ever. This happens because more and more people are striving to realize their ideas by means of additive technologies. Many solo enthusiasts, research groups, and manufacturing companies are not interested in investing in 3D printers, but prefer to go to a prototyping center first.
Today, 3D printing services are based mainly on working with professional clients. Of course, orders are also carried out for individuals, but most of the market is the B2B segment.
Even if you have access to a 3D printer, sometimes it's better to hire an outside contractor. Let's say you need a part in a material or color you don't have, and you'd rather not buy the whole lot. It is much wiser to order the missing part, and not to purchase all the equipment and inventory that may not be needed in the future.
We will look at ten reasons why additive manufacturing using a service can be more profitable.
Do you have projects that you would like to realize using 3D printing, 3D scanning or 3D modeling? Order a service from our company!
Leave a request
1.
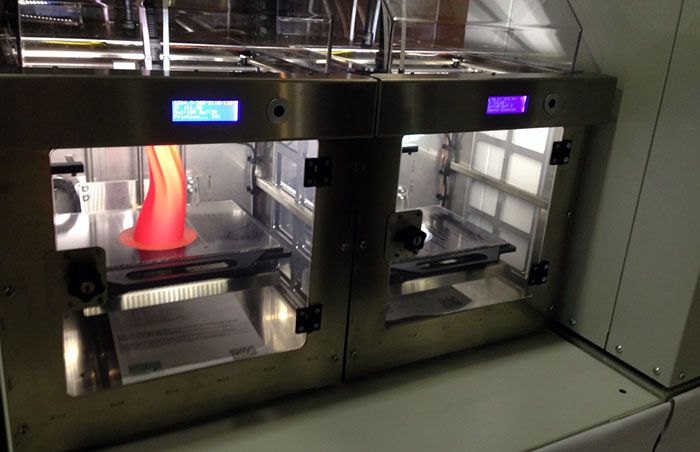
Additive technologies have been improved over the years, and today they allow the production of both prototypes and final parts, especially when solving certain problems.
In general, the development and manufacture of a particular part can be expensive due to high tooling costs. 3D printing is an extremely flexible technology. Manufacture of many different products and refinement of their designs is no longer a complex problem, which makes additive manufacturing a reliable solution to problems with the active use of redesign.
Outsourcing 3D printing jobs saves costs and lead times © Leo Gregurić via All3DP
Today, many research groups and companies rely on 3D printing services as a supply chain. It is extremely useful for them to be able to easily create and deliver custom parts.
2. Large selection of materials
One of the strong selling points for 3D services is the variety of consumables (and technologies) on offer. Thanks to the constant introduction of innovations in this area, service providers are able to work with the latest developments, especially large companies.
Prototyping centers offer, as a rule, the three most popular additive technologies: FDM, SLA and SLS. Accordingly, polymer filaments or granules, photopolymer resin and plastic powders are used as consumables.
A wide range of options gives the customer the opportunity to obtain the material that is required for a particular project, based on mechanical and chemical properties and aesthetic requirements.
The variety of materials is practical not only for professional needs. The Professional 3D Services Center will also offer simple materials that may not be available to a private person. Buying a certain material and printing a product from it on your own can be more expensive than simply ordering the manufacture of a single part from this material.
iQB Technologies experts recommend an article: 9 products that are more profitable to make on a photopolymer 3D printer
3.
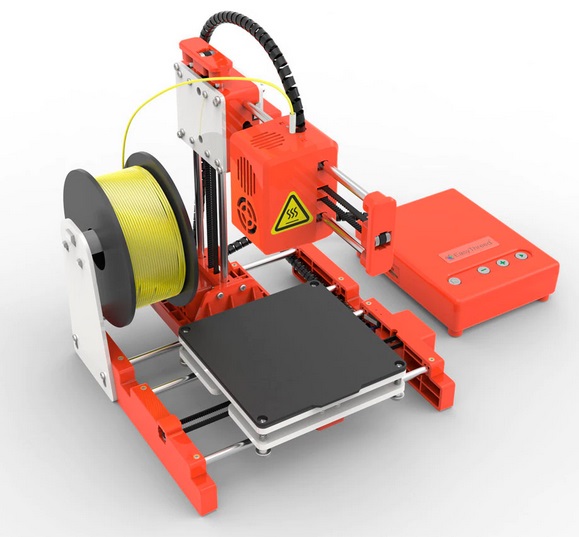
With such a wide range of materials available, 3D printing service customers are not limited in their choice of colors and finishes. Creating the perfect combination for a specific task has never been easier.
Colors
FDM filaments (PLA, ABS, PETG, and others) are typically offered in a wide range of colors. The plastic granules from which the thread is made are easily dyed.
More advanced combinations of plastics in the form of filaments, such as polymer composites or nylon, are difficult to dye and their color range is not as rich.
With regard to SLA technology, various colors are available for photopolymers. True, there are not as many of them as for PLA. Methods like SLS use industrial grade nylon powder, which comes in white, black, or some color in between. This is also due to the difficulty of coloring.
Technology available for full-color 3D printing © Hubs
There are full-color 3D printers that are ideal for creating visually appealing prototypes and teaching models, such as anatomy and geography. Given the high cost of professional machines, the ability to use technology that is not otherwise available through a 3D printing service is of great importance to the end user.
Finish
The surfaces of products created on a 3D printer can be subjected to various post-processing methods. Details are processed until the layers are completely indistinguishable and, as a result, look as if they were not printed at all.
But this is only the beginning. Processing can include sanding, polishing, galvanizing and painting, and many other finishes. Not every 3D printing material is suitable for all post-processing methods, and the service provider should explain this point to you when ordering.
In addition to the huge selection of options, one of the biggest benefits of ordering a finishing service is quality and convenience. Post-processing can take a lot of time, and entrusting the work to professionals, you will be sure of a high-quality and reliable result.
4. Large Format 3D Printing
Sometimes you may need a large printer © WASP Team via Youtube
An additive manufacturing services company typically operates multiple 3D printers to meet high demand (and meet deadlines) and various other requests. This provides a number of advantages, among them - the flexibility of product sizes.
Sometimes splitting a large part into multiple sub-elements is not the best solution, so an additive setup with a large build platform is needed. An individual or company often does not have access to large 3D printers, while many 3D service providers do.
5. Professional quality parts
3D printers are becoming more reliable, and even the most affordable technology is showing impressive accuracy. However, many products (say, jewelry) require more precise workmanship or tighter tolerances to ensure perfect compatibility (for example, functional units). The professional results offered by the 3D printing service guarantee consistently high-quality workmanship in terms of precision and finish.
Professional machines are more reliable in terms of repeatability. This is an important factor to consider when printing a large number of parts that require constant and tight tolerances.
But not only machines determine the final result. The people who work with 3D printers make a significant contribution to the production of professional quality parts. They have the knowledge and experience to advise you on how to best prepare your model, select the most suitable material, and finally create the final part.
A high-quality prototype created on an industrial SLA printer at the TWIZE Prototyping Center © TWIZE
6. Cost reduction
If you need to make something on a 3D printer, there are two options: either buy equipment and print the parts yourself, or order printing and receive finished products. Using a 3D printing service can save you money.
When a business is considering launching its own additive manufacturing, outsourcing through a service provider first makes sense. This will allow an individual or company to access 3D printing technologies while avoiding the cost of equipment, materials and maintenance. Once you understand that 3D printing meets the needs of your business, this may be the right time to start thinking about buying equipment.
There are other scenarios as well. Some businesses can save money in the prototyping phase by having them 3D printed before putting the final version into production through another process such as injection molding.
However, outsourcing a project can save a lot of money until a “tipping point” is reached, at which point the cost of acquiring the equipment becomes a worthy investment.
Considering starting a 3D services business?
We share our experience in the article 3D printing as a business: the most profitable concepts of the RP Center
We will consult and select ready-made solutions. Contact us!
7.
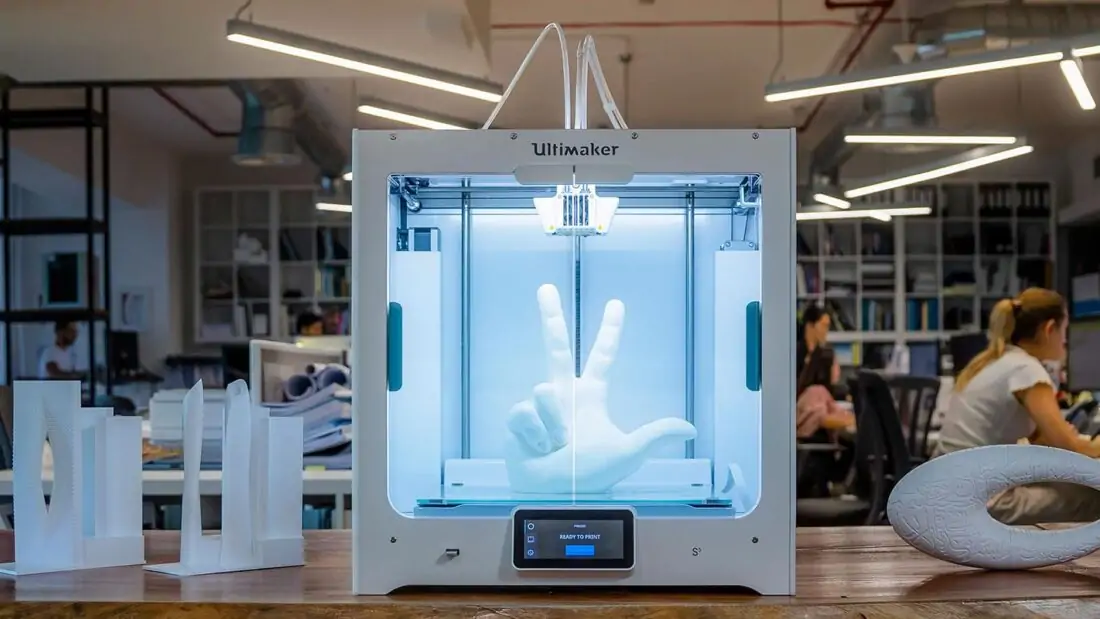
When ordering 3D printing from a service provider, you don't have to worry about printer setup and maintenance. In fact, you make a payment and get the parts you need. Everything is done on a turnkey basis, and you don't have to think about all the additional costs associated with setting up, maintaining and operating the equipment.
3D printing of some parts may require time that you do not have © Leo Gregurić via All3DP
And even if you have printers, they may not be enough to print a large number of products in a short time. Since prototyping centers usually have a large stock of equipment, large batches can be produced very quickly.
Of course, the order may take a long time, so choose the service wisely. But the turnaround time for an order (printing from standard media with standard post-processing) may well be shorter than the total time it takes to set up, maintain, and operate the related equipment. For many, this alone is enough to apply for a service to a contractor.
In addition, the production of an object on a 3D printer takes hours or days - this requires control, which not everyone can do.
8. Scalability
Since the advent of 3D printing, it has been described in the mainstream media as a slow process. What is usually meant is that additive manufacturing cannot compete with traditional methods such as injection molding when it comes to high volume production.
There is some truth in this, but it is important to understand that 3D printing is a very effective process in certain circumstances. When you need to produce large batches of the same parts, this is not the best option, but 3D printers are more than capable of producing in small and medium volumes.
This is especially beneficial when we are dealing with individual designs or iterations, that is, when classical methods involve much more time and money.
For this reason, 3D printing services in particular can provide scalable manufacturing solutions that meet the needs of even medium volume production. Small-scale production is possible in a garage or a small office, something larger is hardly imaginable, and this is where the use of a 3D printing service makes sense.
3D service providers can deliver scalable solutions © BMW Group
9. Expert advice and assistance
As already mentioned, 3D printing services are available to a large number of different customers. These can be both individuals who want to print a cartoon character figurine on a 3D printer, and world-famous corporations seeking to optimize their workflows. In any case, consultation is an important factor that can help close the deal.
The additive manufacturing experts at the 3D Services Center can help customers determine the right course of action before launching a project. Working with the client on the specific needs of his project, he is explained the available options.
Identifying the exact applications for 3D printing as well as discussing technical issues and specifics (such as what material is best for the purpose) are all part of the consulting service. Sometimes good preparation based on consultation can save money as the project progresses. For large projects, this is certainly an important advantage.
10. Professional design services
Most 3D service companies expect you to already have a 3D model ready to print. Often this is the case, but some clients still need additional help. In cases where the customer needs to develop a part from scratch and he does not have 3D modeling experience, a service with the involvement of full-time professional designers will come in handy.
Moreover, not all 3D models are ideal for 3D printing in production. In these cases, the advice (or adjustments) from the AM specialist is really helpful. It may not be useful to all customers, but for new customers it will be a nice bonus.
Author of the material: Leo Gregorich. Source: all3dp.com
Article published on 04/28/2022, updated on 08/01/2022
How a 3D Printing Station Helps Hundreds of AMRC Engineers
At first glance, a former coal mine doesn't seem like a place where the future of industry can be determined, but 40 hectares of reclaimed land near Sheffield has the highest concentration of experienced manufacturing professionals technology in the UK.
The Advanced Manufacturing Equipment Research Center (AMRC) at the University of Sheffield conducts world-class research in advanced processing, manufacturing and materials science. He works with more than 100 industrial companies, from giants like Boeing, Rolls-Royce, BAE Systems and Airbus to small businesses looking to increase their competitiveness. These partner companies approach AMRC with specific needs, and the Center employs the latest technologies and processes to develop concepts and solutions that customers can implement in their plants.
Additive manufacturing has long been a tool to help researchers quickly test concepts and ideas, but the complexity and high cost of the equipment have limited the availability of these technologies. Their problems are not unique. Companies often purchase expensive, state-of-the-art equipment that promises to spur innovation, but then fail to integrate it into work processes to operate it effectively.
AMRC's goal is to lead the integration of technology in a way that encourages innovation. The employees of the Center managed to find an application for 3D printing that companies may be interested in. AMRC recently installed an Additive Manufacturing Station with 12 Form 2 stereolithography (SLA) 3D printers, giving hundreds of engineers working on various projects free access to 3D printing technologies.
“It made our job a lot easier. [At any given time] we're working on hundreds of projects involving hundreds of engineers. Now that employees have access to 3D printers, for every project that requires the use of additive manufacturing technology, the time to manufacture components has been reduced from one and a half weeks to several hours,” says Mark Cocking, technical director of polymer additives of the design and prototyping division at AMRC.
Watch the video to see how AMRC works. In addition, Cocking and other engineers working at the research center will talk about how 3D printing facilitates production in various industries.
AMRC's Design and Prototyping Division works with researchers from all parts of the Center to develop everything from concept design to fully working prototypes for a variety of industries.
“Some of the models we create are just concept demonstrations, but we also often custom-make jigs and fixtures and other parts that are then installed on equipment for various research programs,” Cocking says.
To meet a wide range of needs, from nuclear physics research to composite materials, the station provides a variety of equipment, including industrial laser cutting systems, CNC milling machines, CT scanners, metal laser sintering machines, as well as 3D printers running Based on Filament Deposition Modeling (FDM) and Stereolithography (SLA) technologies.
Learn more about the three most advanced technologies for 3D plastic printing: FDM, SLA and selective laser sintering (SLS).
The design and prototyping department is staffed with a range of tools, including laser cutters, CNC routers, and plastic and metal 3D printers.
Previously, the Center had one industrial stereolithographic 3D printer, which, due to the complexity of the operation process, could only be operated by a few people. These people worked on all the additive manufacturing projects at AMRC, which slowed down the workflow and hindered innovation.
“It was much more profitable for us to make this knowledge open, train many users and give them the opportunity to work with the system, gaining new experience. We have found that if they can work with these devices, they will be able to come up with more and more component concepts obtained through the additive manufacturing process,” says Cocking.
“Engineers no longer need paperwork to turn their idea into a printed model. They can just come down here and do it without wasting time. This removes obstacles in the development of internal concepts, stimulating innovation. Engineers can produce components in a matter of hours and present them to partners the next day or even the same day.”
The design and prototyping department currently has 12 Form 2 3D printers organized into one station. Cocking has placed all the printers on one side for easy access to all resins and patterns, and on the other side has set up an area with four Form Washers and four Form Cures for cleaning and final curing. On the side is a section with storage for platforms, PPE, instructions, risk assessments, and a buffer zone for models passing through the system.
Technician interacts with 12 devices using a touch screen on the side of the station, which is controlled by Formlabs' Dashboard software, providing model status and material quantities.
One technician is responsible for the entire station and monitors all printers. A technician interacts with 12 devices using a touch screen on the side of the station, which runs Formlabs' Dashboard software, providing model status and material quantities. When employees arrive at the Center, all they have to do is press the print button.
At the rear of the station is an area with four Form Washes and four Form Cures for cleaning and finishing. In addition, there is storage.
Employees can sign up for a training course and come to the Center to spend 45 minutes to an hour learning about the software and printing process. Upon completion of the training, they will run their first print job. After training and printing, they remove the platform with the finished models from the printer, pass them through the cleaning and final polymerization system, remove the supporting structures using the post-processing station and get acquainted with the risk assessment. Once they complete this process, they get permission to work with devices at any time.
“I needed devices that were easy to use and convenient, so that employees could quickly learn how to use them and want to continue to do so. The Form 2 is the first compact stereolithography printer that I thought, "Yes, this is truly a revolutionary breakthrough." He is very easy to work with,” says Cocking. “The software is intuitive and the engineers get up to speed very quickly. After mastering the simple basics, they can independently continue their education and gain additional experience. To date, more than 100 engineers have learned how to work with Form 2.”
Models are prepared for printing on Formlabs 3D printers in PreForm. Download and test this software now. This does not require a printer.
The exchange of knowledge occurs predominantly organically, through direct communication. Engineers who start working with 3D printers take manufactured components back to their departments and use them in concept models and prototypes or install them into equipment. Their colleagues find out how these parts were made, and they become interested. As a result, the Center receives more and more requests for training.
Complete brackets hold six arms on a stacking robot designed to automate the stacking of moving composite materials.
Since its installation, the 3D printing station has been used in dozens of research and development projects.
You can find detailed information about what exactly the engineers made with it.
- Drilling caps: 3D printing station produced 500 high-precision drilling caps needed to prevent cross-contamination during drilling testing for the company Airbus , which reduced the order preparation time from several weeks to just two days.
- Robotic Gripper Bracket: Researchers have designed and printed brackets for a complex stacking robot for automating the production of composite materials. It would be very difficult to manufacture such components in another way.
- Temperature Probe Bracket: In an independent nuclear welding process project, researchers fabricated a dozen 3D printed parts such as washers, brackets, and a sensor mounting system designed to withstand high temperatures and be placed in close proximity to the weld site. .
- Roller for Piping System Parts: Composite researchers have created uniquely designed rolls for a winding machine designed to produce pipes, vessels and shafts for the aerospace and automotive industries.
Nuclear Welding Project Probe Mounting System, rated for high temperature exposure and close proximity to the weld site.
Cocking and others in the design and prototyping department are already planning to expand the capacity of AMRC's additive manufacturing equipment.
“Some of our buildings are quite far from the main complex. We plan to take this station as a base and replicate it by placing satellite units in different buildings throughout the Center so that employees can access printers right in their department instead of driving here,” says Cocking.
Cocking and others in the design and prototyping department plan to recreate the 3D printing station at other AMRC locations and partner companies.
“After working in the industry for 12 years, I came to the conclusion that it would be very useful to have additive manufacturing facilities in the field to make it easier for engineers to access them,” says Cocking.
“This would cut the production time for custom-designed components from weeks to hours. Having ordered custom components myself, I understand how this can affect not only innovation but ultimately the release date. You can get your product to market a few months earlier just by using additive manufacturing processes. ”
AMRC's partner companies seem to agree, as the success of the open access platform has also caught their attention.
“Some of our partners have expressed interest in completely recreating this plant at their facility. They need easy-to-use equipment with the ability to scale. You can start with 12 printers, but as your needs increase, you can easily add more stations. Multi-platform printers allow you to organize serial additive manufacturing. It's possible now, and at a reasonable price," says Cocking.
“I'm seeing a shift from building small models to demonstrate concepts to building more and more ready-to-use components. We now print models with complex geometries that pass the same tests as injection molded parts,” says Cocking.
Different projects require models with different material properties. Developers at AMRC use a wide range of engineering polymers, from flexible and heat resistant materials to high tear resistance materials. With their help, employees solve complex problems and improve processes - from prototyping to production.