Edible 3d printing filament
Top food 3D printers available this year
What is food 3D printing?
Although it may sound like something from a sci-fi movie, food 3D printers do actually exist. Edible 3D printing is becoming more and more popular not only for professionals but also for personal use. That said, how does food 3D printing work? To what extent is it similar to standard 3D printing?
Most food 3D printers use extrusion 3D printing technology, much like regular desktop FFF (FDM) 3D printers. Instead of using plastic material, though, food 3D printers use paste-type ingredients. The most common ingredients are chocolate, pancake batter, and cream, although there are many other possibilities (even pizza!). They are 3D printed layer after layer, generally through a syringe-like extruder.
To get a better overview of this niche, we have put together a comprehensive list of food 3D printers on the market. This selection is based on available food 3D printers under $6,000. We also mention a few other food customization solutions, including coffee 3D printing, food ornament 3D printing, and 3D printing food molds.
Bon appétit!
Best food 3D printers available on the market
Brand | Product | Build size | Country | Price Approximate starting prices based on supplier-provided information and public data. Prices may vary by region, over time and do not include additional products or services (taxes, shipping, accessories, training, installation, …). | |
---|---|---|---|---|---|
Micromake | Food 3D printer | 100 × 100 × 15 mm3.94 × 3.94 × 0.59 in | – | $ 9991 015 €886 £148,907 ¥ | Contact |
Choc Edge | Choc Creator V2.0 Plus | 180 × 180 × 40 mm7.09 × 7.09 × 1.57 in | – | $ 2,6832 727 €2,380 £399,929 ¥ | Quote |
ZMorph | VX | 250 × 235 × 165 mm9.![]() | – | $ 2,7992 845 €2,483 £417,208 ¥ | Quote |
byFlow | Focus | 208 × 228 × 150 mm8.19 × 8.98 × 5.91 in | – | $ 3,6303 300 €3,220 £541,073 ¥ | Quote |
Natural Machines | Foodini | 250 × 165 × 120 mm9.84 × 6.5 × 4.72 in | – | $ 4,0004 066 €3,548 £596,224 ¥ | Quote |
Mmuse | Chocolate 3D printer | 160 × 120 × 150 mm6.3 × 4.72 × 5.91 in | – | $ 5,4995 590 €4,878 £819,659 ¥ | Quote |
Expand to see more specs
The products in the table are ranked by price (low to high).
Brand | Product | Build size | Country | Price Approximate starting prices based on supplier-provided information and public data. Prices may vary by region, over time and do not include additional products or services (taxes, shipping, accessories, training, installation, …). | |
---|---|---|---|---|---|
Micromake | Food 3D printer | 100 × 100 × 15 mm3.![]() | – | $ 9991 015 €886 £148,907 ¥ | Contact manufacturer |
Choc Edge | Choc Creator V2.0 Plus | 180 × 180 × 40 mm7.09 × 7.09 × 1.57 in | – | $ 2,6832 727 €2,380 £399,929 ¥ | Get a quote |
ZMorph | VX | 250 × 235 × 165 mm9.84 × 9.25 × 6.5 in | – | $ 2,7992 845 €2,483 £417,208 ¥ | Get a quote |
byFlow | Focus | 208 × 228 × 150 mm8.19 × 8.98 × 5.91 in | – | $ 3,6303 300 €3,220 £541,073 ¥ | Get a quote |
Natural Machines | Foodini | 250 × 165 × 120 mm9.84 × 6.5 × 4.72 in | – | $ 4,0004 066 €3,548 £596,224 ¥ | Get a quote |
Mmuse | Chocolate 3D printer | 160 × 120 × 150 mm6.3 × 4.72 × 5.91 in | – | $ 5,4995 590 €4,878 £819,659 ¥ | Get a quote |
Pros and cons of food 3D printing
Benefits of 3D printing food
Time-saving
Edible 3D printing can be less time-consuming than traditional cooking. Indeed, users can launch a food 3D print and move on to other activities. Once the food 3D print is launched, there is no more need for manual operation.
Customization
Food 3D printing enables users to customize their food according to special events or simply to their mood. It can vary from writing a name on a birthday cake to 3D printing a heart-shaped pancake, for instance.
Creativity
Edible 3D printing enables cooking aficionados to unleash even more creativity in the kitchen. Users can imagine and actually create intricate designs. Amazing 3D-printed food artwork already exists!
3D printed food art by Marijn Roovers. Source: Marijn RooversLimits to food 3D printers
Type of food
Not just any sort of food can be 3D printed. The food must be in the form of a paste, such as cream or mashed potatoes.
Partial cookingThe 3D printing process doesn’t encompass every step of a meal’s preparation. For instance, food 3D printers cannot bake a cake or sprinkle oregano over a pizza.
Price
Food 3D printers are a bit expensive, generally in a price range between $1,000 and $5,000 (although there are exceptions).
Risk of failure
Just like with any other type of 3D printing, food 3D prints can be unsuccessful – too bad if it’s a birthday cake!
Food 3D printers: overview
The byFlow Focus is a compact food 3D printer made by byFlow, a Dutch 3D printing company specialized in edible 3D printing. This food 3D printer targets mostly professionals in the bakery industry.
The Focus works with refillable cartridges containing any kind of paste-type food to create customized meals. Furthermore, users have the possibility to access downloadable recipes.
Contact manufacturer Get a quote Add to comparison
The Choc Edge Choc Creator is a chocolate 3D printer targeting mostly professionals in chocolate and confectionery industries.
In addition, Choc Edge develops three apps, CHOC DRAW, MIX & MATCH and CHOC TEXT, to help users to draw and write on their chocolate 3D prints. A slicing software, ChocPrint, is also available.
Contact manufacturer Get a quote Add to comparison
The Micromake Food 3D printer can 3D print all kinds of paste-type ingredients, such as tomato sauce, chocolate sauce, and salad sauce. Also, the removable heated build plate is able to bake ingredients such as pancake batter.
Contact manufacturer Add to comparison
The Mmuse Chocolate 3D printer is a closed-framed chocolate 3D printer made by Muse, a manufacturer from China. This 3D printer uses chocolate beans as consumables: they melt in the extruder, just as with regular FFF/FDM 3D printing.
Contact manufacturer Get a quote Add to comparison
The Natural Machines Foodini is a 3D printer able to 3D print all kinds of paste-type food. Users can fill the Foodini’s capsules with any type of paste food they wish.
Furthermore, if users choose a specific Foodini recipe, the 3D printer gives instructions on which ingredients to insert into the capsules.
Contact manufacturer Get a quote Add to comparison
Thanks to its thick-paste extruder, the ZMorph VX can 3D print ceramics as well as food!
This multifunctional 3D printer is indeed able 3D print with chocolate, cookie dough, cream cheese, frosting and more.
In addition to paste extrusion, the VX is features CNC milling and laser engraving capabilities.
Contact manufacturer Get a quote Add to comparison
Special mention: Cakewalk
- Materials: chocolate, meringue, royal icing, ketchup, guacamole, cream cheese, butter, mashed vegetables, Swiss butter cream
- Price:
- During KS campaign: €49 to €89
- After KS = €119
Cakewalk 3D is a precise and practical extruder that converts your desktop 3D printer into a food printer. The screw-in extruder is designed to be easily installed on any type of Cartesian 3D printer. All parts are food-safe and easily washable in your dishwasher.
To adapt Cakewalk 3D to your printer, you just need to 3D print 3 or 4 pieces of support in plastic. Disassembling your plastic extruder, screwing in the support parts, and connecting the motor to your card takes less than 30 min. The extruder then works with your usual slicer.
Cakewalk3D Kickstarter campaign
Edible 3D printing: who is it for?
Restaurants and bakeries
Edible 3D printing is indeed very useful for professionals in the food industry. 3D printed food can be attractive to new customers seeking different food experiences. A restaurant serving 3D-printed food, the Food Ink. pop-up store already exists.
Industrial food production
In the industrial food production sector, edible 3D printing allows manufacturers to vary their product ranges with new creations. Furthermore, food 3D printers can achieve a high level of precision. Barilla, an Italian food company, 3D prints some of its pasta products.
Food 3D printing at home
Food 3D printers are also adapted for personal use. They allow for more creativity in the kitchen with food customization.
What food can be 3D printed?
Ingredients
Virtually any type of fresh food can be 3D printed as long as it’s a paste, or “purée”. For instance, ingredients could be:
- Chocolate, candy and sugars
- Pancake batter or cookie dough
- Dairy products
- Pasta, wheats and grains
- Fruits and vegetables
Even pizza can be partly 3D printed! However, users will have to sprinkle their favorite toppings manually.
3D printed pizza by Beehex. Source: BeehexFood 3D models
To 3D print food, we can let our imagination take over. Users indeed have the opportunity to create their own food 3D models with special CAD software. However, it is also possible to directly download any 3D model on dedicated STL file websites.
How much does a food 3D printer cost?
Food 3D printer price
There are various price points for food 3D printers. Prices can depend on the food 3D printer’s build volume and/or on the variety of 3D printable ingredients it is compatible with.
In general, the minimum price for a food 3D printer is around $1,000 (although the PancakeBot is available for under $400). However, prices may decrease in the future, just as they have for regular extrusion (FFF/FDM) 3D printers.
Other promising food 3D printing applications
Here are a few industries where food 3D printing is already beneficial.
Sustainable food
Food 3D printing could be a part of the answer to the world hunger crisis. Indeed, some food 3D printers use hydrocolloids as a consumable.
This chemical, gel-like substance can mimic food. 3D printed meals with hydrocolloids could also include sustainable ingredients, such as algae.
Medical
As explained above, certain food 3D printers use hydrocolloids to create different shapes and textures for meals. Also, like the EU’s PERFORMANCE program is proving, it can be very useful to make softer meals for people with chewing or digestion problems, especially elders.
In addition, medicine can be presented in the shape of yummy food, instead of pills or powder.
Army
The US Army is carrying out scientific research to provide personalized food for their soldiers.
According to Lauren Oleksyk, a food technologist leading the team at the Army’s Natick research center, a sensor installed in soldiers’ bodies could detect their specific dietary needs. This sensor would be interfaced with a food 3D printer, to produce customized meals.
Aerospace: NASA food 3D printer
Beehex, an American startup, has received a grant from NASA to develop a food 3D printer.
Indeed, the aerospace agency aims to allow astronauts to produce their own food during long-term space missions to go to Mars!
3D printed food ecosystem
Food ornament 3D printers
Coffee 3D printers: 3D printing on coffee
There seems to be no connection between the portrait of the Mona Lisa and coffee. However, thanks to coffee 3D printers, it is possible to see the beautiful smiling lady in a cup of coffee. Indeed, a combination between 3D printing and inkjet printing technologies allows these machines to draw images on top of any foam-covered beverage.
As such, the Ripple Maker, a coffee 3D printer made by Ripples, can help users print “their own selfies, favorite quotes, or special messages and images on their drinks”. Another existing coffee printer is the Lixian 3D CafeMaker.
Cake ornament 3D printers
Bakery industry professionals also use 3D printers to adorn cakes or pastries. Thanks to edible sheets of paper and ink, any kind of image (including photos) can be 3D printed to decorate cakes.
Food extruders
If users already have an FFF 3D printer at home, another solution exists to 3D print food: food extruders. These tools generally feature universal compatibilities with regular extrusion 3D printers. Some of them, such as the Structur3D Discov3ry, allow 3D print with non-only edible food and clay, silicone, etc. An open-source extruder, the BotBQ Extruder, can 3D print raw meat – a good fit for your future barbecue!
3D printed food molds
3D printers can also 3D print very useful tools for food production: this is the case of 3D printed food molds. Users can create their own molds and print them in 3D to customize cakes, for example.
Conclusion
Food 3D printers are suitable for professional, industrial, and personal use-cases. Only paste-type ingredients are printable, but a wide range of food – from pizzas to cakes – can be created. As 3D-printed food can be customized according to users’ needs, it can be helpful in many fields, such as medicine.
3D printed food may also represent a hope for the world hunger crisis in the future. What food 3D printers are still missing is the ability to actually cook or bake. That is why cooking robots could be more and more popular in the future.
The Essential Guide to Food Safe 3D Printing
3D printing offers unparalleled design freedom to produce custom parts and complex or organic shapes that would be costly or impossible to manufacture with traditional manufacturing methods.
These benefits can be compelling for a range of food-related applications. However, if 3D printed parts are intended for food contact items, you‘ll have to consider safety practices and regulations to avoid contact with toxic substances and prevent the buildup of harmful bacteria.
Food safe 3D printing is possible and the variety of materials approved as food safe is increasing, but there is a high degree of ambiguity around the workflows and finding the appropriate applicable regulations can be a challenge.
Read on for an introduction to food safety, food safety considerations for 3D printing, and a variety of methods to produce food safe products with common 3D printing processes, including stereolithography (SLA), fused deposition modeling (FDM), and selective laser sintering (SLS).
Please note
No Formlabs resins are food safe unless users take additional steps.
Video Guide
Having trouble finding the best 3D printing technology for your needs? In this video guide, we compare FDM, SLA, and SLS technologies across popular buying considerations.
Watch the Videos
To begin, it’s important to clarify a few key terms:
- Food grade means that the material is either safe for human consumption or permitted to come in contact with food.
- Food safe means that a food grade material meets the requirements determined by the intended use and will not create a food-safety hazard.
- Food contact surfaces include any surface that may come into direct contact with food. These surfaces must be made of nontoxic materials and designed to withstand the environment of their intended use, including exposure to cleaning compounds, sanitizing agents, and cleaning procedures.
Food grading and food safety concern a specific way to ingest parts, called migration. Particles as small as a few nanometers and up to several hundred nanometers may get transferred each time various materials encounter with each other, for example from components of the 3D printer to the 3D printed object, and from the object to the food.
Because migration levels are very low on occasional contact, food grading typically concerns items that are in prolonged contact with food such as containers, straws, utensils, plates, and food molds. Different testing institutions will adhere to different government-imposed risk tolerances and approved substances, which for the US is described by the FDA CFR 21 and for the EU in guidelines 10/2011.
Look for these labels indicating FDA and EU approval. Beware that a material being ‘compliant with’ doesn’t mean that it is explicitly approved by the institutions, so always check the technical datasheets for a certificate.
To be considered food safe according to the FDA Food Code, a material has to meet the following requirements:
- No migration of deleterious substances
- Does not impart colors, odors, or tastes
- Safe under normal use conditions
- Durable, corrosion-resistant, and nonabsorbent
- Sufficient in weight to withstand repeated washing
- Finished to have a smooth, easily cleanable surface without breaks and sharp internal angles
- Resistant to pitting, chipping, crazing, scratching, scoring, distortion, and decomposition
- Accessible to inspection
Any FDA or EU approved material includes not only the raw polymer but also the additives or masterbatch. These might contain components such as plasticizers, impact and heat distortion modifiers, UV-stabilizers, flame retardants, anti-fouling, anti-static, anti-slip, foaming and clarifying agents, anti-oxidants, aromatic nucleators, carbon alloys, phosphorescents, fillers, thickeners, chain extenders, metal deactivators, dyes, and a carrier resin.
A 3D printed part can turn into a petri dish squirming with bacteria within weeks. Even though some materials will survive the dishwasher, so will dangerous bacteria such as E. coli and salmonella that live in the little nooks and crannies. Some toxic molds find favorable growth conditions on several types of plastic and are hard to remove. Neither cleaning with bleach nor microwaving your polymers is an option for eliminating germs.
While bacteria buildup might not be an issue for disposable items, if you’re planning to create a part for long-term use, using a food safe coating is highly recommended.
The best option to reduce the risk of particle migration and bacteria buildup is by dip coating the 3D printed parts with a food grade epoxy or polyurethane resin, such as Masterbond’s EP42HT-2FG or ArtResin or an FDA approved PTFE (known as Teflon®) to seal their surface.
However, note that coating also doesn’t guarantee food safety for prolonged use as not all of these coatings are dishwasher safe, and they may degrade over time, exposing the original, potentially non-safe surface.
Most 3D printing materials have a low heat deflection temperature (HDT), which means that the 3D printed parts might become brittle and crack, or deform and warp at elevated temperatures. If you’re planning to clean a 3D printed part in a dishwasher, make sure to double check that the material is dishwasher safe and if there are any specific recommendations for washing temperature.
As particles might migrate from components of a 3D printer to 3D printed parts, it is crucial that any components that might come in contact with the 3D printing material or the part are food grade and do not contain or leach harmful chemicals.
This includes taking precautions when using multiple materials, as some materials previously used in the 3D printer might have contained toxic particles and made contact with some components.
Many 3D printing materials are not food safe and might contain toxic chemicals. Only use materials to 3D print parts intended for food contact that are certified for food safety.
As may be expected, the risk of migration is higher if the food is exposed to the 3D printed part for an extended time period. In general, try to limit food contact time and take further precautions for parts that will be in contact with food for longer periods of time.
Think about the reason why you’d like to use 3D printing for a food contact item. If it’s to create custom shapes and forms, in most cases, there are indirect ways to use 3D printing to create these custom parts, for example with molding. See an example in the next section.
SLA 3D printing uses a laser to cure liquid resin into hardened plastic in a process called photopolymerization, resulting in parts that have the highest resolution and accuracy, the clearest details, and the smoothest surface finish of all plastic 3D printing technologies.
Is resin food safe? The answer is no. Substances may migrate from SLA parts which makes none of the resins and printed parts food safe by default. While some resins for dental and medical applications are certified biocompatible, that doesn’t mean that they’re food safe. These materials are certified for specific applications and should not be used for food contact products.
SLA parts have a smooth surface finish that makes it easier to use coatings to seal their surface and prevent the buildup of bacteria. The factors which affect the ultimate smoothness of a part include resin type, layer thickness, build orientation, mesh triangulation resolution of the 3D model, and the curing profile of the SLA resin. Printed parts require washing and post-curing according to the manufacturer's instructions before the coating is applied. However, note that coatings don’t guarantee food safety, as the coating may interact with the resin or degrade over time, exposing the original, potentially non-safe surface.
White Paper
Looking for a 3D printer to realize your 3D models in high resolution? Download our white paper to learn how SLA printing works and why it's the most popular 3D printing process for creating models with incredible details.
Download the White Paper
Creating custom molds is a common way to leverage the benefits of SLA 3D printing to produce highly detailed custom parts without having the 3D printing parts come into direct contact with food. While SLA 3D prints aren’t suitable for directly molding foods, SLA 3D printers are perfect tools to create mold negatives, which can be vacuum formed using food safe plastic.
The tools and techniques for creating 3D printed food molds are easy to master, and the results are often stunning.
3D printed molds for thermoforming and silicone enabled the creation of unique shapes and designs.
Learn more about creating molds for vacuum forming in our in-depth tutorial.
Electroplating is the process of coating parts with metal using an electric current. The process is most commonly used for decorative purposes or to prevent corrosion by creating a durable surface.
SLA parts are ideal for electroplating due to their smooth surface finish. However, as plastics are nonconductive surfaces, SLA 3D prints have to be rendered conductive by coating with graphite, conductive lacquer, electroless plate, or a vaporized coating.
Food safe metal coatings are available, but as the process involves various chemicals, making sure that the workflow is approved for food contact is the developer’s own liability.
SLA 3D printing offers the unique possibility to produce ceramic parts. After 3D printing, parts can be fired in a kiln to burn out the resin and form a true ceramic part that is strong and heat-resistant. With subsequent food safe glazing, the parts will become more hygienic and resistant to most chemicals.
A variety of food safe glazes are available on the market, but make sure to follow the manufacturer’s instructions in accordance with food safety guidelines.
3D printing in ceramics is ideal for fabricating complex geometries that wouldn’t be possible by hand.
Learn More About Ceramics
Sample part
See and feel Formlabs quality firsthand. We’ll ship a free sample part to your office.
Request a Free Sample Part
FDM is a 3D printing process that builds parts by melting and extruding thermoplastic filament, which a print nozzle deposits layer by layer in the build area.
The extruded material is circular in cross-section, which leaves very narrow crevices in between layers with a depth directly proportional to layer height. It is recommended in any case to print at the lowest feasible layer height for food safe parts.
Consequently, the main challenge with FDM parts is avoiding the buildup of bacteria. To be truly food safe in the long term, an FDM 3D print needs to have a smooth surface. Chemical smoothing with solvents like acetone, d-Limonene, or ethyl acetate removes many of the irregularities of the print resulting in a smooth, glossy appearance. However, applying a subsequent food safe coating is still highly recommended.
Layers showing on FDM (left) and SLA (right) 3D prints.
Food grade filaments do not contain any composite particles so will not wear down the nozzle into the print. Nevertheless, avoid brass nozzles that contain lead and use a dedicated stainless steel nozzle instead for all food contact items.
Always check the compatibility of your 3D printer’s components with the filament. For example, PEI is a material that is FDA compliant and offers great mechanical benefits but needs to be processed at over 300 °C, which requires a specific printer solution.
The most common questions around FDM food safety concern two popular materials. Is PLA food safe? Is ABS food safe? The answer is, it depends.
Food safe 3D printing filaments include PLA, PP, co-polyester, PET, PET-G, HIPS, and nylon-6, as well as some brands of ABS, ASA, and PEI. Having to run parts through the dishwasher rules out PET, nylon, and PLA because these plastics soften and distort around 60–70 °C. For applications involving hot liquids, co-polyester, High Temperature PLA or PEI are most suited.
While not reflected in the regulations, some studies suspect that polystyrene may leach styrenes, co-polyesters might cause health concerns and that food grade FDM filaments might lose their safe status due to oxidation and thermal degradation from the printing process.
Filament | Brand | FDA | EU | Smoothable | Dishwasher safe | Hot liquids |
---|---|---|---|---|---|---|
ABS | Adwire PRO | Approved | NA | Yes, acetone | Yes | Yes |
Innofil3D | Approved except red, orange, and pink | Approved except red, orange, and pink | Yes, acetone | Yes | Yes | |
ASA | Innofil3D | NA | Compliant | Yes | No | |
Bendlay | Orbi-Tech | NA | Compliant | Yes, brake cleaner | No | No |
Biocompound | Extrudr GreenTEC | NA | Compliant | |||
Co-Polyester | Colorfabb XT | Approved | Compliant | No | Yes | Yes |
HIPS | Easyfil | Compliant | Compliant | Yes, d-limonene | Yes | No |
Fillamentum | NA | Compliant | Yes, d-limonene | Yes | No | |
InnoFil3D | Approved | Approved | Yes, d-limonene | Yes | No | |
Nylon | Taulman Nylon 680 | Compliant | NA | No | No | |
PEI | ULTEM® 1000 | Compliant | NA | Yes | Yes | |
PET | InnoPet EPR | Approved except red and orange | Approved except red and orange | Yes, ethyl acetate | No | No |
Refil | Approved | NA | Yes, ethyl acetate | No | No | |
Taulman T-Glase | Approved | NA | Yes, ethyl acetate | No | No | |
Verbatim | Compliant | NA | Yes, ethyl acetate | No | No | |
PET-G | Extrudr MF | NA | Approved | Yes, ethyl acetate | No | No |
HDGlass | Approved | Approved | Yes, ethyl acetate | No | No | |
PLA | Filaments.![]() | Approved | NA | No | No | No |
Fillamentum | NA | Compliant | No | No | No | |
Innofil3D | Approved except red, orange, pink, apricot skin, grey, and magenta | Approved except red, orange, pink, apricot skin, grey, and magenta | No | No | No | |
Copper3D PLActive Antibacterial | Approved | Compliant | No | No | No | |
Makergeeks | Approved | NA | No | No | No | |
Purement Antibacterial | Approved | Approved | No | No | No | |
PLA-HT | Makergeeks Raptor | Approved | NA | No | Yes | Yes |
Makergeeks Raptor | Approved | NA | No | Yes | Yes | |
PP | Centaur | Compliant | Compliant | No | Yes | Yes |
InnoFil3D | Approved | Approved | No | Yes | Yes | |
Nunus | Compliant | Compliant | No | Yes | Yes | |
Verbatim | Compliant | NA | No | Yes | Yes | |
SBS | Filamentarno | NA | Approved only in Russia | Yes, d-limonene | Yes | Yes |
Selective Laser Sintering is a 3D printing process that use a high-powered laser to fuse small particles of polymer powder. The most common material for laser sintering is nylon, a popular engineering thermoplastic with excellent mechanical properties.
While some SLS powders are graded food safe, the particles on the surface of printed parts might not fuse completely, resulting in parts that are inherently porous and do not deal well with moisture and mold growth. Even though the nylon 12 powder can be steam cleaned in an autoclave, it is best to coat SLS parts with food safe coatings to seal their surface.
A common post-processing step for SLS parts is dying. But note that after an SLS part has been dyed, the dye may leach into the printed part which renders the item not food safe.
White Paper
Looking for a 3D printer to create strong, functional parts? Download our white paper to learn how SLS printing works and why it's a popular 3D printing process for functional prototyping and end-use production.
Download the White Paper
Food safety with 3D printing is not a simple matter that will boil down to a clear yes or no answer. Producing 3D printed parts for food contact items requires careful consideration of the risks depending on their intended use.
For further information on food safety and 3D printing, we recommend reading the following:
- FDA Regulations CFR 21
- EU Guidelines 10/2011
- Risk Assessment of 3D Printers and 3D Printed Products
- The Tricky Business of Choosing Plastic for Food Contact Applications
Review of the best PETG plastics for 3D printing
3D printers can produce not only plastic toys and high-tech car parts, but also all sorts of exotic designs, from prosthetics to edibles. And with the best PETG materials, you will have durable and reliable 3D models. The low shrinkage makes this material an excellent choice for 3D printing with large, flat surfaces.
Moreover, with the rapid development of 3D technology, all different grades of PETG plastics are entering the market. And each of the manufacturing companies considers it their duty to report that it is their PETG plastic that is the best. It is not easy to stop at a really good product when there are so many manufacturers in stores. You will have to spend a lot of time going through all the available options in order to choose the best option. In this article, we will help you understand the question: "What kind of PETG plastic should I buy?".
What should I consider when choosing PETG filament for a 3D printer?
Stability, cost-effectiveness, durability, flexibility and reliability are among the important factors when choosing a PETG plastic. This type of 3D printing material is different from other plastic filaments because its polymer chains can be easily rebuilt for later use. Chemical resistance allows it to act as a barrier when used with alcohol and solvents.
In terms of safety, this material is food safe and has been approved by the FDA.
Make sure you only buy the highest quality PETG thread from a trusted source, otherwise results may differ from photos of satisfied users online.
So, let's move on to the top 10 PETG materials
OVERTURE PETG Filament 1.75mm with 3D Build Surface
Overture 3D PETG Filament is made and developed with an anti-clog patent, which guarantees you stable and smooth 3D printing. Before packaging in aluminum foil, 24 hours of complete drying is required. This protects the PETG material from moisture, which can destroy it. Each PETG spool comes with a 200 x 200mm 3D printable surface.
The large inner spool diameter ensures a smoother material feed during 3D printing. The manufacturing company has over eight years of experience in producing thousands of tons of 3D printing materials per month.
Overture can produce all types of top quality materials in high volume. This definitely adds to the reliability and cost effectiveness of Overture filament for most 3D printers including FlashForge, Monoprice, Ender 3 and Prusa MK2/MK3.
DPC :
- Provides stable and smooth 3D printing
- wide compatibility and efficiency
- easily use
Disocations :
- BACT 1.
0037 9000 DURAMIC 3D PENTG
Duramic PETG 3D printer plastic features stable and smooth extrusion with excellent adhesion. When used with the recommended settings, you won't have any problems with the 3D model stretching or warping. Through strict production quality control, the company ensures that there are no bubbles, clogs or tangles, ensuring smooth and stable 3D printing. This PETG thread comes in a resealable aluminum bag, where you can store the spool even if you start using it and decide to replace it with another plastic. The required nozzle temperature is 240±10°C, and the table heating temperature is 70°C to 80°C.
Duramic plastics are manufactured using high precision measuring systems and quality control systems. These manufacturing techniques ensure that the plastic diameter is accurate to a tolerance of ±0.05 mm on a 1.75 mm filament thread.
The color is even, without traces of other shades. It is produced using pure American raw materials without recycled secondary waste.
Duramic PETG filament guarantees exceptional reliability and quality, providing all your wishes in terms of material quality at an adequate price for such quality.
There are additional goodies. For example, there is a scale on the bobbin that can be used to navigate in terms of the remaining current length of the filament and its weight. Naturally, this quality PETG plastic is odorless.
DPC :
- Ecological and without smell
- provides stable and smooth 3D printing
- Exceptional quality and reliability
- Guarantee of money return
Disadvantages :
- Brass nozzle may cause problems
AmazonBasics PETG 3D Printer 1.75mm Blue Filament
AmazonBasics PETG filament is one of those filaments that will turn your creative ideas into high quality material. This PETG plastic has a diameter of 1.75mm and is designed for use with the most common 3D printer models.
The spool has a built-in sensor that shows the approximate length and percentage of material remaining. In developing this material, the company focused on reducing the chance of jamming during 3D printing and improving first layer adhesion.
Filament comes with a resealable storage bag. In addition to PETG plastic, you can also find PLA and ABS plastics from the same manufacturer. Their quality is excellent too.
This PETG plastic from Amazon comes with a one year warranty. There are not only blue, but also other colors.
Advantage :
- High strength
- Spool with built-in gauge
- Fits most standard 3D printers
- is easy to use and reduces the likelihood of jamming
- Guarantee one year
- provides good grasping the first layer with a 3D printer table
Disadvantages :
- You can find bubbles on the printed 3D
- some users complain, that users complain, that storage bag not resealable
OVERTURE 1.
75mm Transparent PETG Filament
Overture transparent filament is made of high quality PETG plastic that combines the advantages of other materials such as good flow, high impact strength, low shrinkage, no smell and security. Each of these PETG coils has a quality surface for easy material glide.
This filament is manufactured and developed with an anti-clog patent to ensure stable and smooth 3D printing. You can store this PETG material for up to 24 hours without a vacuum bag and you won't experience the moisture problems associated with PETG.
This PETG material comes with a "self-adjusting" diameter measurement control system that ensures dimensional accuracy and feed stability and therefore 3D printing. The company has been producing plastics for 3D printers for about 8 years. Production volumes are thousands of tons of materials.
Values :
- Size accuracy and the constant size of the thread along the entire length of the coil
- is supplied with vacuum aluminum foil for packaging
- is not clogged in the hollow and does not leave bubbles
SUNLU PETG Filament 1.
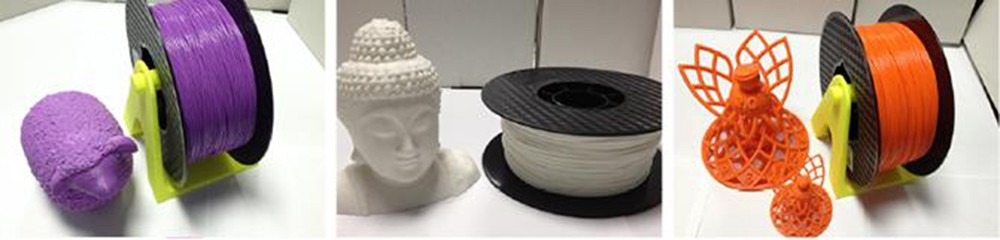
PETG filament for SUNLU GT 3D printer is a high quality polyethylene terephthalate filament with a wide range of applications, with the advantages of durability and ease of use. This material does not require heating of the table and provides rigidity, reliable adhesion to the table and a glossy surface. The recommended nozzle temperature is 235–245 °C (455–473 °F). SUNLU PETG plastic has a diameter of 1.75mm with a dimensional tolerance of ±0.02mm.
This PETG material is produced with high precision and is suitable for most 3D pens and 3D printers. This plastic has a patent that describes a manufacturing procedure that reduces bubbles, nozzle clogging, and tangles, which guarantees stable and smooth 3D printing.
The spools of this PETG material undergo a full cycle of mechanical winding and strict manual testing, which guarantees accuracy and ease of feeding during 3D printing. SUNLU GT thread is completely dry in 24 hours. Like any other PETG plastic, this plastic is sensitive to moisture, so remember to always put it in an airtight bag after use. Large inner diameter spool design ensures smooth feeding during 3D printing.
Values :
- Provides smooth and stable 3D printing
- The Bobin design is different, which provides ease of supply during 3D print
- A wide spectrum of use - from 3D printers to 3D handles
- Strong
- No notches for evaluating material remaining
- No manufacturer warranty
SUNLU PETG 3D Printer Filament With Dimensional Accuracy
This SUNLU PETG filament has a diameter of 1.75mm and is perfect for 3D pens and 3D printers with a nozzle diameter of 1.75mm, such as Makerbot, Prusa, Geetech, Ante, Anycubic, 3D Hero and SUNLU. The recommended 3D printing temperature for SUNLU PETG plastic is 200-220°C and the bed temperature is 60-80°C. These recommended temperatures will help produce smoother 3D models that require minimal calibration. Problems with nozzle clogging and the need for further cleaning should also not arise.
This PETG plastic makes it possible to obtain smooth 3D models and even a glossy surface with the right 3D print settings. The manufacturer has several patents that make it possible to maintain high quality 3D printing with low shrinkage. This PETG plastic stands out among others for its high hardness, good viscosity and absence of bubbles.
Supplied with a vacuum packing bag that makes it easy to store the reels in optimal conditions, away from dust and moisture. Like the others, this PETG filament is moisture sensitive. SUNLU offers a 100% lifetime warranty on this filament and they can replace the filament if any problem occurs.
DPC :
- is characterized by high compatibility with different models of 3D printers and pens
- The result is smooth 3D models
- does not score the 23D -type
- -shaped stool
- is a long -term guarantee 9000 Disadvantages of :
- Essentially none, but for optimal 3D printing results, you will need to experiment with the temperatures of the 3D printer's nozzle and bed
- Made from high quality and environmentally friendly raw materials.
- Ensures stable and smooth 3D printing
PETG materials from Prusa are characterized by very high strength and are guaranteed to meet the stated parameters of diameter accuracy and filament composition.
Again, you can use these PETG spools on any 3D printer, as long as you print critical components that must meet high strength criteria. This plastic is practically not subject to deformation, has excellent adhesion of layers, including the first layer, which seizes with the table of your 3D printer.
Values :
- The production process is fully controlled, and the coils are tested before the sale of
- Strutary material with high heat resistance
- Universal use
75mm PETG Black Filament
The eSun PETG 3D Black Filament has a diameter of 1.75mm and a dimensional accuracy of +/- 0.05mm. This is an excellent material that combines the advantages of materials from other manufacturers. These include excellent glossy surface, good fluidity, high toughness, outstanding toughness, hydrophobicity, low shrinkage and no odor. The black plastic is sold in 1kg spools and is easy to feed into your extruder. Naturally, like most of the high quality PETG plastics on this list, it comes vacuum-packed with a desiccant that protects the moisture-sensitive PETG material from moisture. The company provides a choice of 16 shades of colors.
The recommended extrusion/nozzle temperature is 240 - 255℃, printing speed 30~60mm/s, and travel speed 30~60mm/s. Note that eSun's PETG material requires a slower print speed than other PETG media.
Advantages :
- Combines the advantages of other materials from the current top
- Provides a smooth and stable 3D printing process
- 100% biodegradable 9003 7
- No markings on the spool for evaluating material remaining
- No manufacturer's warranty
- Great combination of many 3D printing materials
- Eco-friendly material
- Compatible with any 3D printer
- Very high -quality results 3D print
- There is no control of the remaining thread on the coil
- There is no guarantee from the manufacturer
Disadvantages :
HATCHBOX PETG 3D Printer Filament
This is one of the best filaments on the list.
If you want to get the most out of PETG plastic 3D printing, this is definitely the option to try. These filaments are suitable for most 3D printers with a diameter of 1.75mm and an accuracy of +/- 0.03mm. HATCHBOX PETG is the perfect combination of flexibility and strength and is a great alternative to PLA or ABS. PETG plastics from this manufacturer have a combination of unique properties, such as rigidity, reliable adhesion and strength. A product printed on a 3D printer in compliance with the recommended 3D printing modes will have a glossy surface.
It is environmentally friendly and does not require table heating. The recommended nozzle temperature is 230°C - 260°C, and the spool design makes it easy to dispense. HATCHBOX filament is vacuum packed and sealed with desiccant to keep its properties for a long period of time.
Benefits :
Disadvantages :
Frequently asked PETG PETG
What is Petg plastic for 3D printer?
PETG plastic in the current context is plastic filaments that are fed into a 3D printer's extruder.
The filament is melted and extruded onto the print bed by an extruder to create physical 3D models. This is a very durable material that does not emit odor when 3D printed. PETG is more flexible than ABS or PLA. It is difficult to break and has very low shrinkage; hence, there is no deformation during 3D printing. It is worth noting that this is not a brittle plastic, but it is easier to scratch than ABS. It has good chemical resistance as well as water, acid and alkali resistance. Extremely durable material that allows you to get durable and reliable 3D models.
What are the benefits of using PETG plastics for 3D printing?
PETG plastics combine many of the useful properties of PLA and ABS materials. PETG provides uninterrupted and stable 3D printing. Among the advantages of PETG plastics over PLA and ABS plastics are reduced shrinkage, warping resistance, good layer adhesion, no smell during 3D printing, chemical resistance to alkalis and acids. Naturally, you will receive all these advantages only if you follow the recommendations for the temperature and high-speed modes of 3D printing, which are indicated by the manufacturer.
Conclusions
PETG filament is a 3D printing filament that is rapidly gaining popularity in the market. Many people use this plastic to get high-quality and durable 3D models. PETG is ideal for those who want to experiment and ditch ABS due to the problems that arise with its use, or replace PLA, which is much more fragile and sometimes not suitable for making critical mechanical components.
Consumables for 3d printers
Our warehouse always has the widest range of materials for professional 3D printing: various types of plastics, photopolymers, composite powders, waxes, as well as support materials and special solvents.There are currently about ten different 3D printing technologies in use, each of which involves the use of a particular material. The most widely used thermoplastics (PLA, ABS), foundry wax, photopolymer resin, gypsum. But every year this list is supplemented - individual models of 3D printers can print with concrete, metal alloys, edible substances, and even biomaterials.
ABS plastic (ABS)
ABS plastic is known as acrylonitrile butadiene styrene. This is one of the best consumables for 3D printing. Such plastic is odorless, non-toxic, impact-resistant and elastic. The melting temperature of ABC plastic is from 240°C to 248°C. It is available for retail sale in the form of a powder or thin plastic threads wound on bobbins.Polylactide (PLA)
Polylactide is the most biocompatible and environmentally friendly material for 3D printers. It is made from the remains of biomass, sugar beet or corn silage. Having a lot of positive properties, polylactide has two significant drawbacks. Firstly, the models made from it are short-lived and gradually decompose under the influence of heat and light. Secondly, the production cost of polylactide is very high, which means that the cost of models will be much higher than similar models made from other materials. Used in 3D printing technologies: SLS and FDM.HDPE
This is the most common type of plastic in the world, from which PET bottles, canisters, pipes, films, bags, etc. are made. In 3D printing, low-density polyethylene is the unsurpassed leader. This material can be used in any 3D printing technology.Polypropylene (PP)
Polypropylene is the lightest of all currently existing plastic masses. Compared to HDPE, it melts worse and resists abrasion better. At the same time, it is vulnerable to active oxygen and deforms at low temperatures.Polyphenylsulfone (PPSU)
This material came to 3D printing from the aircraft industry. It practically does not burn, is characterized by heat resistance, high hardness. It resembles ordinary glass, but surpasses it in strength. Used in 3D printing technologies: SLS and FDM.Acrylic
Acrylic is used in 3D printing to create transparent models. When using acrylic, the following features must be taken into account: this material requires a higher melting point than ABS plastic, and it cools and hardens very quickly.A lot of small air bubbles appear in heated acrylic, which can cause visual distortions of the finished product.
Concrete
Currently, test samples of 3D printers for printing with concrete have been made. These are huge printing devices that painstakingly, layer by layer, "print" construction details and structures from concrete. Such a 3D printer can “print” a residential two-story house with a total area of 230 m2 in just 20 hours.
For 3D printing, an improved grade of concrete is used, the formula of which is 95% the same as that of ordinary concrete.Plaster
Gypsum materials are widely used in modern 3D printing. Models made of gypsum are short-lived, but have a very low cost. Such models are ideal for making objects intended for presentations. They can be shown as a sample to customers and clients, they will perfectly convey the shape, structure and size of the original product. Since plaster models are highly resistant to heat, they are used as casting samples.Wood fiber
Inventor Kai Parthi has developed a special wood fiber for 3D printing. The fiber consists of wood and a polymer and is similar in properties to polyactide (PLA). The combined material allows you to get durable and solid models that look like wooden products and have the smell of freshly sawn wood. Currently, the innovative material is only used in self-replicating RepRap printers.Metal powder
No plastic can replace metal with its pleasant soft sheen and high strength. Therefore, 3D printing often uses powder from light and precious metals: copper, aluminum, their alloys, as well as gold and silver. However, metal models do not have sufficient chemical resistance and have high thermal conductivity, so fiberglass and ceramic inclusions are added to the metal powder for printing.Nylon
Nylon printing has a lot in common with ABS printing. The exceptions are the higher printing temperature (about 320°C), high water absorption capacity, longer curing time, the need to evacuate the extruder due to the toxicity of the nylon components.Nylon is a rather slippery material, for its use it is necessary to equip the extruder with spikes. Despite these shortcomings, nylon is successfully used in 3D printing, since parts from this material are not as rigid as those made from ABS plastic, and sliding hinges can be used for them.
Polycaprolactone (PCL)
Polycaprolactone is close in properties to biodegradable polyesters. It is one of the most popular consumables for 3D printing. It has a low melting point, hardens quickly, provides excellent mechanical properties to finished products, easily decomposes in the human body, and is harmless to humans. In addition, it can be used in several 3D printing technologies at once: SLS, ZCorp and FDM.Polycarbonate (PC)
Polycarbonate is a hard plastic that is able to maintain its physical properties in conditions of extremely high and extremely low temperatures. It has high opacity, has a high melting point, and is suitable for extrusion processing.At the same time, its synthesis is associated with a number of difficulties and is not environmentally friendly. Used to print heavy duty models in several 3D printing technologies: SLS, LOM and FDM.
Chocolate
The printer applies each next layer of chocolate on top of the previous one. Due to the ability of chocolate to quickly solidify and harden when cooled, the printing process is quite fast. In the near future, such printers will be in demand in confectionery and restaurants.Ceramic
3d printing with ceramics is under development, but today's samples already show promise for full-fledged ceramic productsWhere to buy plastic for 3D printing? In 3dcorp.ru!
In our assortment you will find not only all the necessary equipment for 3D printing, but also a wide range of consumables at extremely attractive prices. You can buy ABS or PLA plastics from us, as well as other materials for the implementation of projects of any complexity.Learn more
YOYI 1.

YOYI PETG 3D plastic in red color is usually imported from Europe and does not contain impurities, which ensures its high quality. In order to obtain a quality PETG plastic, strict procedures are followed during its production, guaranteeing the absence of bubbles, little or no smell, high accuracy of the thread diameter along its entire length and, therefore, achievement of the REACH standard.
This PETG plastic has a diameter of 1.75 mm and a tolerance of ± 0.03 mm. It is designed with a tangle-free and clog-free patent, which guarantees you stable and smooth 3D printing. At optimal settings, there is minimal buckling.
As a 3D filament manufacturing enterprise with many years of production experience, they can withstand all the strict requirements of 3D filaments and keep improving. The recommended printing temperatures for these PETG plastics are 250℃ - 275℃.
This PETG plastic is the best choice that guarantees you high quality 3D printing and is made from environmentally friendly materials that degrade gradually in the natural environment. If the quality of the plastic does not satisfy you, then YOYI offers a free return option within 30 days after purchase.
Advantages of :