Does blender work with 3d printers
Can I Create A 3D Print Directly From Blender 3D? – blender base camp
In addition to modeling for animations and video games, you can also design a model to be 3D printed as a real-world object. But are you able to complete the entire virtual stage of the process using Blender alone, or do you require other platforms and applications for the actual printing?
While Blender can be used to design 3D objects for printing, you cannot create a 3D print directly from Blender. Instead, you need to export your model using either the stl, obj, or ply file formats to software that is dedicated to the 3D printing process. This software can be from the manufacturers of the 3D printers themselves for compatibility reasons or another source.
So if you cannot print a 3D model directly from the Blender software what exactly is the process for designing a 3D model and then print it as a physical object, and what other software do you need to do so?
Why Can I Not Send A Model Directly From Blender For 3D Printing?
There are certain file formats that are suitable for 3D printing objects. The blend file type used by all blender projects is not on this list of suitable file formats for 3D printing, because it is a format created specifically for use within Blender and holds many different types of data that are not related to 3D printing such as rigging and animation data.
In most cases, 3D printers may have their own specialized software associated with them so that you can print out your models using that software as the go-between.
Admittedly, while Blender does possess many of the tools necessary to design 3D printable models the user interface is not particularly suited to the task. This is why other alternatives such as Autodesk fusion 360 are considered better objects for creating 3D printable models.
Get FreeGeometry Nodes Starter Kit
What Do I Need To Do Then Once I Have Designed My Model?
You can always use Blender for the designing phase of your 3D printable model. Once you are done though you will be required to export your model as one of several different file formats that are suited for the task of 3D printing.
There are many different file extensions out there that store data in various forms, with each having its own set of use cases. For example, the FBX format has been extremely popular for many years for storing data of video game assets, but it is not very useful for storing data on assets created for 3D printing.
This is because you need to be able to store specific types of data when performing any task, from video games to 3D prints. The FBX file type can be used to store object data, rigging, animation, and basic material data. This makes it a great option for game assets.
So What Data Is Required To Successfully Print 3D Models?
The data that is required for 3D printing is related to the structure of the object itself. In other words, the file format selected needs to focus purely on the object itself and not additional types of data. For example, a file format that stores animation data is not suited because your printing model is not going to be moving (Hopefully!).
Object data can be broken down into several different forms of information, all of which are important for 3D printing. Below we have a list of the different data types that a file format should contain when used for 3D printing.
- Normals
- Vertex Data
- Vertex Coordinates
- Face Data
- UV Coordinates
All of these relate to the structure of the models’ geometry and are important for when your 3D model needs to map out the object’s form.
What Are The Main File Formats That I Can Export As?
The question now is which file formats are suitable for 3D printing? However, it should be noted that not every file format is currently compatible with Blender. 3D printing is a relatively new field still, and there are some newer formats that have not made the transition to Blender just yet.
That said these formats are newer and less widely used anyway, so it is not that big of a deal. The file formats that are most commonly used for 3D printing are available for use with Blender, so long as the respective add-on has been enabled.
Below is a list of file formats that are suitable for 3D printing AND are currently compatible with Blender.
- OBJ
- STL
- PLY
- 3XD
- GLTF
Of the options listed above, the STL file format is the most commonly used for 3D printing. A good alternative is the OBJ format, which is simple yet versatile and suitable for almost any 3D application.
The Two Ways Of Creating 3D Printed Objects After You Export?
Once you have exported the model that you created in Blender, you then need to send it to an application that is capable of sending that information to the 3D printer to complete the process.
What Software Do I Need For 3D Printing?
After you have created your model you will need to then ‘slice it’. Slicing is a term used in 3D printing to describe the process of dividing up a 3D model into a series of layers. The software assigns an index o numerical value to each layer that is created.
The reason why this is important is that the index values determine the order in which the layers are going to be created by the 3D printer. The software will then generate what is known as a tool path, which uses the file extension .gcode and sends the data to the printer to complete the process. You can consider slicing software almost as a middle man between the design software and the 3D printer.
There are several options out there for good slicing software, but the one that we recommend is Cura, which is free, open-source software like Blender that was developed by Ultimaker, which is a manufacturer of 3D printers.
While it is developed by a specific brand the software will work with the large majority of 3D printers on the market.
An alternative solution that we recommend is AstroPrint, which is a cloud-based solution that can be used for slicing as well as monitoring your 3D printer from anywhere that has an internet connection.
What If I Don’t Have My Own 3D Printer At Home Or At My Workspace?
Not everyone has a 3D printer in their own home. It may be a case that they are just too expensive, or that the added cost of buying material is unappealing. Or it could be a case where you just don’t have enough space in your home, as even the smaller 3D printers can take up a fair bit of space.
If you fall into the category of wanting to try 3D printing but don’t have access to a 3D printer then you can try sending your file off to a 3D printing company to be printed there and then posted to you for a fee.
If you choose this route be mindful that you want to get your model right before you export it and send it off for someone else to print.
A great website that we have used in the past is Sculpteo, which is an online surface that allows you to upload your file to the website and then pay for the product to be printed and shipped to you.
There are a growing number of websites similar to Sculpteo but they are the ones that we recommend as we have ordered from them in the past with no issues.
Thanks For Reading The Article
We appreciate you taking the time to read this article. We have gathered a list of additional articles that we believe you may be interested in reading.
- How To Use The 3D Print Toolbox Addon?
- Is Blender The Only Free 3D Software Out There?
- Does Blender Use The GLTF File Format?
- What Are The Main Features Of The Blender Software?
- Which File Formats Are Compatible With Blender?
-
Where Can I Learn Blender For Free?
If you choose Blender as your 3D modeling software of choice, then one of the key reasons you choose Blender is because it is completely free. If the price is
Continue Reading
-
What Is The Blender Cloud?
When learning how to use Blender, we are always on the hunt for new learning resources that we can use to speed up the timeline for us when it comes
Continue Reading
-
How Do I Access The Blender Cloud?
Blender 3D has a reputation of being one of the most accessible applications because it is both free to use but also has a lot of learning resources to go
Continue Reading
Blender for 3D Printing | is it as awesome as it seems?
A lot of people today use Blender for 3D printing, because in the last decade, it has been developed significantly. Now you can use it to do many important things in different industries. With the most important being manufacturing, medicine, architecture, entertainment, and design.
In this article, we will talk about what Blender is capable of when it comes to 3d printing. In addition to what it can offer to both beginners and professionals.
Image source : i.materialise.com
Blender for 3D printing is possible since 2002. However, when Blender version 2.67 was released, it became even more accessible and powerful in than ever before. To clarify, it’s thanks to the 3D Printing Toolbox and real-time Mesh Analysis features.
And in the last couple of years or so, a lot of other tools and features have been added to Blender that can, directly and indirectly, help you print better 3D models.
3D printing organic modelsImage source : cgmeetup.net
For the most part, if you want to 3D print organic forms such as characters, animals, monsters or anything else that does not represent a solid surface Blender is a great option. This also includes organic shapes in 3D models such as sofas, pillows, trees, and other artistic design shapes.
Blender as a 3D modeling software has a very important advantage, which is the ability to have a lot of control and flexibility. This is very important because Blender for 3D printing is not just about creating solid industrial parts. Actually, it’s also about creating organic shapes, especially in entertainment industries.
For example, 3D printing is being used in the film and entertainment industry. And it has made a great difference in character image design, props, and even the whole scenes sometimes. Which is very efficient in terms of saving time and money.
Blender is very good for modeling organics shapes because it is all the necessary to do so, and you can use it to model everything you can think of. In addition to that, you can find a wide variety of awesome Blender addons for modeling. Probably it is not as easy compared to 3D printing CAD software, but it can reach impressive levels of details and complexity in comparison. Especially knowing that it has the ability to sculpt organic surfaces.
3D printing hard surface modelsImage source : TopChannel1on1
In terms of modeling 3D hard surface models, Blender is considered one of the best 3D packages. Even though it is free for everyone even for commercial use. You can create complex models of machines, robots, mechanical parts using its native tools. But if you want to take it to the next level, you can use some fantastic specialized Blender addons for hard surface modeling that can help you be more accurate. Also do more by saving time and energy.
When it comes to 3D printing industrial parts for mechanical engineering, industrial manufacturing, architecture or design, the most important problem you will face is the tricky nature of accurate measurements in 3D packages such as Blender. Because unlike specialized computer-aided software, working on these models require experience and patience to get to something close to what you can achieve in software that engineers or architects use.
Preparing 3D models for printing in Blender
Once you are done modeling, Blender for 3D printing has a preliminary phase. One of the most important you need to know about creating and preparing 3D models to be printed is that, if you have a model created from several objects or meshes, first make sure that each individual mesh is manifold or what is know as a water-tight 3D model. Because it is not going to be printed correctly or not at all if this is not the case.
Non-manifold geometry is a geometry that cannot exist in the real world. Meaning that a 3D model can be represented digitally, but there is no geometry in the real world that could physically support it. Since the mesh of the 3D model is defined by edges, faces, and vertices, it has to be manifold. If it is a non-manifold mesh, it means there are errors in the 3D model that cannot define with precision the geometry of the 3D model.
The software of the 3D printer is reading the exact geometric representation of a model so as to print it. Thus, in case the 3D design contains non-manifold modeling errors that prevent this precision of geometry, the 3D file will not be recognized by the 3D printer, and consequently, the 3D model will not be printed.
Also, your model should be one piece, not a collection of separate pieces that are not really welded together. Once you’ve got all your meshes manifold, make sure that every mesh is its own object.
And when you carefully make sure that you have no problems for 3D printing when it comes to your mesh, scale your object to the size you want and then export it to a 3D printing software.
3D printing tools in BlenderImage source : Youtube/TopChannel1on1Choosing Blender for 3D printing has advantageous tools. When modeling, there’s the Ruler/Protractor Tool to help you measure the thickness. This is important when you are optimizing for both cost, time, and structural strength.
There’s also the 3D Print Toolbox that comes with Blender—it is an addon that calculates volume, surface area, and overhangs. This is necessary for estimating cost and print-time.
If you want to make sure that everything is going to work fine, Blender files often need little fixes before sending them to the printer. However, there are programs like MeshLab, Meshmixer and NetFabb that help fix your files. Also, if you use a service like Shapeways, they will fix your files automatically before it goes to print.
Blender vs other 3D Printing SoftwareImage source : pluralsight.com
Compared to specialized CAD software that architects and engineers use for designing mechanical or any other functional parts that actually work in the real world like automotive parts, medical devices, or even space industries that require an insane degree of accuracy, Blender for 3D printing can be less accurate, because it is not created for these purposes. But you can do it if you want to, the thing is, it is going to take more time and effort and the results are going less perfect due to the fact that Blender has fewer features for measuring easily, effectively and efficiently like what we can’t find in CAD software. Since It’s more of a sculpting and 3D modeling, and animation tool.
But sometimes, the bottleneck is more on 3D printers’ ability to print with accuracy than in the model file’s accuracy.
On the other hand, CAD software such as Solidworks, Inventor, Fusion 360, and others are very good when it comes to accurate industrial design and they can be very fast as well. Also using CAD software you are probably going to face fewer problems exporting your 3D printing ready files. But it is very tough to create any organic models using it, let alone working on something close to what you can create using Blender.
Should you use Blender for 3D printing or rather CAD software?Image source : 3dstartpoint.
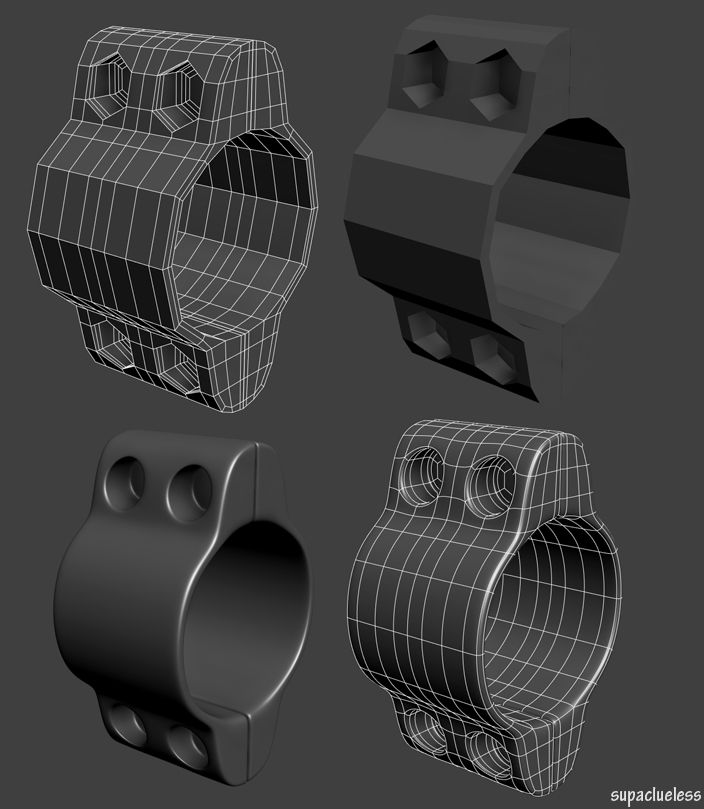
Blender is very good for 3D printing. Especially if you want to model characters, environment props, machines or anything else organic you can think of. It’s an excellent software. As you learn more about it and get used to its tools and features it will become easier to create 3D printing ready models.
So the answer to the question of whether you should use Blender for 3D printing or other computer-aided design software is going to depend completely on the type of 3D models you are planning to create.
If you need perfect precision when 3D printing mechanical pieces or parts of accurate assemblies then you can use CAD software like solidworks, fusion 360 or even some free CAD software for this matter.
3D printing applications using Blender
Knowing that Blender is a powerful 3D package that has the ability to do almost everything including the ability to print 3D Models, it can actually be used to do a lot of different things outside of 3D printing engineering stuff.
1. Miniature Characters/toys
Image source : Youtube/eleotlecramOne of the best applications of Blender for 3D printing actually. It could definitely be used to create a 3D-print ready miniature from start-to-finish, whether you are a beginner or a professional 3D character printer. And there are some artists who use Zbrush in addition to Blender to do final touches. Especially if you have a very complicated character with tens of millions of polygons, but as we said you can do it all in Blender if you want to.
One important difference between video game, animation or film character modeling and 3D-print character modeling is that a 3D-print character model cannot benefit from visual techniques like smooth shading, baking normal maps to a low-poly retopologised model, subdividing only during renders, etc. All the detail that you wish to be present in your printed 3D model, MUST be present in the geometry itself, and that means a very detailed, organic 3D-print model is likely to be far heavier, geometrically, than other kinds of model.
A high-resolution character in a video game might be 20 to 70 thousand polygons after retopology. A very detailed 3D print character might be 20-30million polys prior to decimation, and 500k-1M polys when sent to the printer.
2. Jewelry
Image source : nexusmods.com
Blender is a good 3D software for designing jewelry, that’s why it is being used for this purpose. You can do it using the the tools that modelers and designers usually use. And to make the process easier and to get better results you can use Jewelcraft which is a Blender add-on that will allow you to add gemstones and prongs to the model you have designed. You must have a workable model that you have already drawn up. So basically Jewelcraft helps you to place stones, add prongs and use cutouts to modify your model for jewelry design work and ready it for 3d printing.
3. Entertainment industries
Image source : udemy/mastering-blender-the-properties-editor/Movie studios and special effects artists are now able to use 3D printing to make concept models, and full-size props, set-pieces, and costumes. It is a very good alternative for spending many hours hand crafting hundreds of pieces. Because they can just use a 3D package whether it be Blender or any other 3D package or sculpting software to get the job done.
4. Architecture
Image source : Youtube/TopChannel1on1
Architects can actually use Blender for 3D printing in different architectural structures made from different materials. In order to offer clients a physical representation of what the building is going to look like. And it can also be done using Architecture computer design software which what architects use for the most part.
5. Interior design
Image source : Youtube/Leroy Xie
Interior design is a good application of 3D printing since it is cost effective and less time consuming. Because you can just print the 3D models you created in Blender and start bringing your interior design to life. Also, smaller items that are usually custom made can be printed very fast without wasting human labor, time and money during the process.
3D printing with Blender
3D printing with BlenderWhat is 3D printing?
3D printing is a way to create a specific object from scratch according to a given three-dimensional drawing using the layer-by-layer deposition method (if we talk about FDM technology). In metallurgy or mechanical engineering, parts are obtained by turning, using various cutters and cutters. With this approach, a significant part of the material is wasted. When using 3D printing, maximum material savings are achieved.
3D printing technology is far from new. It has existed for more than 30 years, but only recently has it made a significant leap forward and has become widespread. This happened mainly due to its significant reduction in price and in connection with the spread of home 3D printers. Along with this, a lot of services have appeared that provide 3D printing services, in case the capabilities of a home printer are not enough, or it does not exist at all.
List of lessons
- 1 Introduction
- 2 3D printing applications
- 3 Printer types and companies
- 4 3D printing technologies
- 5 Blender setup and units
- 6 Scale parameter
- 7 Basic model check (non-manifold)
- 8 Version overview 2.
67
- 9Solid and bad contiguos edges checks
- 10Intersections
- 11 Bad edges and edges (Degenerate)
- 12 Distorted
- 13Thickness
- 14Edge sharp
- 15 Overhang
- 16Autocorrect
- 17 Model information and size
- 18Hollow models
- 19Export models
- 20Color model (vertex color)
- 21 Texture paint
- 22 External texture model
- 23 Texture baking (bake)
- 24 Tiger model overview
- 25 Tour model overview
- 26 Pirate model overview
- 27 Factors affecting accuracy
- 28Myths
- 29 Recommendations
- 30Conclusion
Excerpt from lesson
Blender Version
This course is written in Blender 2.73! The differences from Blender 2.8+ are only in the location of the buttons, not their functionality. Therefore, the course is subject to a 33% discount (due to version differences).
Frequently Asked Questions (FAQ)
- 1 What level of knowledge is required to complete this course?
- 2 Where can I contact if I have problems with payment/download?
- 3 On what OS can I watch this course?
- 4 Is there a physical version of the course?
- 5 What payment options are available for this course?
- 6 Can I pay for the book with PayPal?
By and large, advanced knowledge of Blender is not required to successfully complete this course. All actions are explained in detail and difficulties should not arise. But I recommend that you before purchasing this course, take a free course on the basics of Blender. Information about it can be found at the very bottom of this page.
If you have any questions, please send an email that describes the problem in as much detail as possible.
This course can be run on any OS (Windows, Linux, Mac).
No, the course is only distributed electronically. Course size ~ 2.4 GB.
You can pay for the course through a Visa/MasterCard bank card or from an electronic wallet in the Yandex.Money system. You can also pay for the goods using the 4 most popular cryptocurrencies, namely: Bitcoin, Ethereum, Bitcoin Cash and Litecoin.
Yes. Send me an email and I'll show you how to do it.
What you will learn from this course
The goal of this course is to teach you how to create printable 3D models with Blender. Most of the lessons are devoted to the topology of the created objects. This is the most important part when designing a model for 3D printing as not every model can be printed and certain rules must be followed. This will help to avoid errors in the work of slicers, additional costs and unpredictable results of the final models.
In addition, you will learn a little about what 3D printing is and in what areas it is used. Recommendations will be given to improve the quality of printed models and reduce the cost of their creation. Consider typical errors when printing on ready-made models and much more.
After completing this course, you will be able to create models for your own use or start earning on their sales. There are a huge number of services and stocks that sell 3D models for printing, and every day there are more and more of them. You will also save a significant amount of money by avoiding typical beginner mistakes and using the techniques and recommendations from this course.
Blender Basics Course
If you are not familiar with the Blender program, I recommend that you take a free course on the basics before studying the 3D printing course.
In this course you will learn about the main features of Blender. The course consists of 39 lessons, divided into 7 chapters, which show the basic principles of working with Blender. It is designed for absolute beginners and people who got acquainted with Blender relatively recently.
Blender for printers. Chapter 2. Where is this button, where is this item. Fundamentals of working with objects. Part two is practical.
3D modeling
[SIZE=4]In this part of the lesson, we will practice the material presented in the first part. To do this, we will download a model in STL format from this site, check its dimensions, multiply it and slightly play with position and scale. Let's save the resulting models in one file for simultaneous printing and print them. As a result, we should get something similar to KDPV. So let's get started.
[SIZE=4] Let's take Akiko as a model: http://3dtoday.ru/3d-models/art/sculptures/akiko_stl/. Download and save in a convenient place.
[SIZE=4] Start Blender and select File → Import → Stl (.stl) from the main menu.
[SIZE=4] In the menu that appears, go to the folder with the saved model, select it and click on the Import STL button.
[SIZE=4]
[SIZE=4] We admire the model in the editor.
[SIZE=4] Let's check the dimensions of our model. To do this, open the N-panel and look at the Dimensions group of the Transform block.
[SIZE=4] If everything is fine along the X and Y axes, then 190 mm along the Z axis, which is clearly too much. I have a real printable area in Z - 143 mm., And I don't need such a big figurine. Decrease the height of the model. To do this, in each of the fields of the Scale group of the Transform block, set the value to 0.7.
[SIZE=4]
[SIZE=4] Duplicate the model. To do this, select Object → Duplicate Objects from the menu bar of the 3D View window.
You can move the mouse to make sure the object is duplicated. To complete the [SIZE=4] operation, click the left or right mouse button. The difference between these buttons will be that when you click on the left object, it will be saved in the new place where you moved it, and when you click on the right one, it will be saved in its original position. This, by the way, works with all operations. If you started moving, rotating, scaling an object or its faces with the mouse (we will analyze it in more detail in the chapter on keyboard shortcuts) and during the move you realized that you do not want to apply this movement, then just press the right mouse button and the object will return to its original state .
[SIZE=4] Move the duplicate model to a new location using the Location group of the Transform block (I moved it by 70 mm in the X direction) and make the duplicate a little smaller by setting each of the fields in the Scale group of the Transform block to 0.4. The scale will always be calculated relative to the original open model (the one that is 190mm high).
[SIZE=4]
[SIZE=4] If you want to resize or reposition the first model, select it by right-clicking on it.
[SIZE=4] Let's save our project by selecting File → Save As...
[SIZE=4]
[SIZE=4]
named akiko_1) and click on the Save As Blender File button.
[SIZE=4] Export models to STL format for printing. Please note that Blender only exports selected objects. That is, if you want to print both models at the same time, you need to select the second model accordingly. To do this, hold down the Shift key on the keyboard and right-click on the unselected model.
[SIZE=4] Select File → Export → Stl (.stl) from the main menu of the program.
[SIZE=4] In the window that opens, select the export folder, change the name if necessary, and click the Export STL button.
[SIZE=4]
[SIZE=4] Open the model in your favorite[SIZE=4] program for printing, slice and print.
[SIZE=4] That's it. As always, I welcome your questions, feedback and suggestions.
[SIZE=4] Best regards, Maxim.
Follow the author
Subscribe
Don't want
12
More interesting articles
38
Subscribe to the author
Subscribe
Don't want
Recently, the number of customers who ask to convert models has suddenly increased dramatically.