Can you make action figures with a 3d printer
Tips and Tricks for 3D Printing Your Own Action Figures
3D Insider is ad supported and earns money from clicks, commissions from sales, and other ways.
If you’ve ever considered collecting action figures, then you’ve probably realized one thing – they can get very expensive. It’s not uncommon to see highly detailed action figures that cost $200 or more. A collection of these action figures can be considered a small fortune.
One of the joys of owning a 3D printer is that you can just make your own action figures. With some skill, you can even create custom 3D models for printing, so you won’t need to settle for the designs that are available in the market. If this sounds like something you’re interested in, then check out our tips and tricks for getting the best results.
Where to download 3D models
Every 3D printing project starts with a 3D model. The only question is – where is the model going to come from? If you just want to get to the 3D printing step as quickly as possible, then you can simply download models from any of these sites.
For those who are looking for professional-grade 3D models that were designed specifically for action figures, we have two recommendations. Toy Forge is a relatively new site that hosts high-quality 3D models for action figures. These are some of the most intricate action figure models we’ve seen with a lot of articulation points. The only drawback is that their selection is quite small – right now there are only four unique models.
CGTrader is another good option for downloading professional-quality 3D models. This site hosts a wide range of high-fidelity models with a much wider selection including toys, figures, and architectural models, among others. Not all of the models are ready for 3D printers, so make sure to check the tags before downloading.
Both Toy Forge and CGTrader offer high-quality models at a price. Models generally don’t cost more than $20, but there are a few particularly expensive ones. The quality, however, is almost always top-notch.
If you’re up to paying for a 3D model, then there’s always the ever-reliable and free 3D model hosting sites like Thingiverse and MyMiniFactory. With a huge database of user-submitted designs, just these two sites will ensure that you are never going to run out of new 3D models to print.
Since these models are user-submitted, consistency and quality are not guaranteed. You may have to leaf through several dozen models to find one that you’re satisfied with. Searching for “action figures” or “figurines” would be a good place to start. Just make sure that you’re downloading a 3D model that is 3D printer-ready.
Create your own 3D models
Conversely, you can also create your own 3D models. 3D modeling from scratch is quite a complex process. There are two ways to do this: use digital sculpting software, or 3D scan a real-world object.
Digital sculpting
If you’ve never done digital sculpting before, then it’s going to take a lot of practice before you can come up with something that looks really good. The good news is that there a few software platforms that are decidedly user-friendly and make the learning process easier.
Sculptris is an oft-recommended digital sculpting software for beginners not only because of its intuitive interface but also because you can use it for free. One thing you need to know is that Sculptis is no longer being actively developed and that the last version was released way back in 2011. Thus, many of its features are considered outdated by today’s standards.
Once you’re confident with your digital sculpting skills, then it’s time to graduate to the industry standard – ZBrush. One of the most advanced digital sculpting software platforms today, ZBrush is widely used by professional artists, filmmakers, and game developers. The learning curve of ZBrush is definitely steeper than Sculptris, but that’s only because of its wider array of tools.
If you can manage to become an expert in ZBrush, then you can probably come up with action figures that can rival the level of detail and quality of professional action figure makers.
3D scanning
A faster way to create 3D models is to generate them by scanning real-world models. Although this is certainly a quicker method, there’s still a considerable level of skill needed to prepare a 3D scanned model for 3D printing.
The amazing thing about 3D scanning is that you don’t even need sophisticated equipment for it – even your phone’s camera can do the job. This is possible through a technique called photogrammetry. By stitching together a series of overlapping photos of an object, photogrammetry software infers the dimensions of an object’s features in 3D space. The result is a reasonably accurate 3D model which requires minimal processing.
If you want to use your phone’s camera for photogrammetry, there are several apps that you can download and install. We’ve written about these 3D scanning apps in the past. Our top picks include Trnio, Qlone, and SCANN3D.
Something you should know is that a model from 3D scanning will rarely be good enough for 3D printing without having to make some repairs. Depending on how well you’ve done the 3D scan, the model will almost certainly have multiple defects. These can include misaligned features distortions, and areas where the model is not fully sealed. CAD software will be the best option for making these repairs.
No matter which option you take, there really is no “easy” way to create a 3D model. 3D sculpting and modeling is considered a highly technical craft that requires a combination of training and experience. 3D scanning may be considered a shortcut to creating 3D models but said models are not going to look good without some considerable skill.
Use ABS or PLA filament
When it comes to filament materials for action figures, either of the two most popular 3D printing filaments is equally suitable. Each option has benefits and drawbacks, but they are both easily available. You might even already have spools of these filaments on hand.
ABS
ABS is known for its strength and heat stability. It doesn’t crack easily, does not warp when exposed to heat, and is fairly stable when exposed to chemicals. If you want your action figure to last a long time, then ABS would be a better bet.
One of our primary reasons for choosing ABS as a material for action figures is the fact that it can be finished by an acetone vapor bath. By exposing an ABS print to dissolved acetone, the outer surface of the print dissolves in a very controlled manner. This results in the disappearance of its layer lines and an overall smoother finish. The acetone vapor method is one of the easiest finishing methods that result in remarkably consistent quality.
The problem with ABS is that it’s not exactly an easy filament to work with. It’s prone to warping, requires very good bed adhesions aids, and emits a particularly noxious gas while printing. If it weren’t for its superior physical properties, we would have little reason to recommend ABS.
PLA
PLA isn’t known to be a strong or long-lasting filament. Its impact strength is subpar, it’s vulnerable to chemical attack, and it can easily deform when exposed to heat. However, it remains one of the most popular filament materials because of how beginner-friendly it is. Not only is it one of the more forgiving 3D printing filaments, but it’s also the only plastic filament that is sustainable and completely biodegradable.
Finishing a PLA print will require a more old-fashioned technique – sanding. By using sandpaper of different grit sizes, irregularities on the surface of a PLA print can be removed bit by bit. Take note that sanding too vigorously can generate enough heat to deform PLA, so it’s best to do so using gentle circular strokes. Alternatively, you can also use a wet sanding method which may speed up the whole process.
The advantage of the more traditional process is that it gives you better control of the finished product. Do you want certain sections of your action figure to be rougher than the others? Are there nubs from support structures that you want to remove? With sanding, you can achieve just about any kind of finish for each section of your finished print.
To put it in simpler terms, ABS is better if you want your printed action figures to last longer and be stronger. If you don’t want to handle the complexities of printing with ABS, PLA provides a much easier 3D printing experience. Both filaments provide finishing options that will help your action figures achieve a smoother and more uniform look. As the next step shows, the finishing process doesn’t stop with just a smooth surface.
Polish and paint your finished prints
Very rarely would you see an action figure with just a single color. If you’re aiming for a professional look, then you will certainly need to paint your finished prints. This is especially true if you’re trying to create an action figure modeled from a popular cartoon or video game character.
To successfully paint your print, make sure that you’ve gone ahead and sanded it already or finished It with an acetone vapor bath. The next step is to apply a coat of primer, which is meant to enhance paint adhesion. This spray primer from Rust-Oleum is as good an option as any. Make sure to apply the primer in thin and even coats.
Apply at least two coats of the primer, allowing the previous coat to dry before reapplication. The layer of dried primer can also be sanded to retain a smooth surface.
Once multiple layers of the primer have been applied and have dried, you can proceed to apply paint based on your desired color scheme. Spray paint is a good option to achieve uniformity, but you may also need to apply paint using a brush for those small details. In any case, you should not have much trouble. The ease of paint adhesion is also one of the reasons for us recommending either ABS or PLA for this particular enterprise.
Accessorize!
If you really want to make your custom action figure pop, then you might need more than just 3D printed objects. How about giving your action figure some clothes or props? Clothes made with a real fabric look best, especially if you’re handy with a needle and some thread. If you’d rather buy miniature clothes from someone who knows what they are doing, then you can check out handmade crafts sites like Etsy.
Props are a little more challenging because they are usually too small to be 3D printed. If you have old action figures lying around, you can consider borrowing some of their props. The model toy community calls this practice “kitbashing.” You may also come across someone on Etsy who is willing to hand-craft some custom accessories for you.
Final thoughts
Creating custom action figures is a huge undertaking. From coming up with a 3D model to fully painting and accessorizing a finished print, a custom action figure isn’t exactly the type of project that you can finish over one afternoon.
Despite the difficulty, creating custom action figures is still one of the most fun things that you can do with a 3D printer. This is especially true if you’re a huge fan of some video game franchise or comic book. By adding a touch of your own creativity, you can create action figures that are truly unique and would make a great addition to any collection.
Warning; 3D printers should never be left unattended. They can pose a firesafety hazard.
Can You 3d Print An Action Figure? – Home 3d Prints
Bruce Lee action figure by Fervent JanMarvel and DC movies are everywhere these days. Starwars is never far out of reach. For most of us, to own a piece of these universes is to own an action figure.
Can you 3d print an action figure? With the correct files, you can print either a static or an articulated action figure. If the design isn’t readily available, you may need to create your own, and that requires some artistic talent.
In the simplest form, you can download an STL file from Thingiverse.Com, like this Blastoise Action Figure: https://www.thingiverse.com/thing:2456077. With that STL file, you can bring it into your slicer software, prepare it for your home 3d printer, and then transfer it to the printer. Print away!
Printing Static Action Figures
When I think of action figures, I think of two types. First, there’s the display action figure that is a miniature model of the subject that I’m interested in. It’s in a pose, but it doesn’t move. Second, there’s the articulated action figure. I grew up in the 70’s where GI Joe was a big deal (and a big deal taller than the later, smaller ones). He was articulated, and could be moved into all sorts of positions. Star Wars action figures were next in my world, and they could at least move arms and legs.
You may be wanting to make a simple display piece for your desk or shelf. If you have a 3d printer already, the process is simple. Have a look at places like Thingiverse.Com or Pinshape.Com for STL files. Do a search on “Action Figures” and you’ll find a lot of examples. Not surprisingly, you won’t find that many Marvel or DC action figures, or Star Wars characters. These are all covered by trademark and copyright laws, and their owners want to control the rights very tightly. If you do find an STL file of an action figure like this, it’s likely being done outside the law. Caveat Emptor, or buyer beware!
Most action figures, even the static ones, come as multi-part models.
Steps to Creating and Painting a Static Action Figure
- Print each pieces of the STL
- If you’re using an FDM printer, sand the pieces to remove the layer ridges.
- On a Resin DLP printer, at 25 micron Z-height, you’ll find that it takes no sanding, or very light sanding to remove these lines.
- You may wish to paint the parts separately before assembly.
- Spray lightly with a primer paint (like a cheap Walmart Krylon White paint)
- Once dry, spray with the color of paint that you want. Use multiple super-thin coats here. It’s slow, but let each layer dry before spraying the next.
- Once the pieces are painted, assemble the print using superglue. Usually, less glue is better than more glue. Use the minimum necessary.
- Once assembled, you may wish to go back and add details to your model. To do this, you would take hobby paint and a fine brush, and paint on any additional details that you’d like.
- This step is fiddly and difficult for first-timers. That doesn’t mean you shouldn’t do it! Give it a try. If you mess it up, simply wipe away the paint you’ve added. Once the remainder is dry, mask off that area (using masking tape), leaving only the messed up part visible. Respray lightly with the color that was originally underneath. Once dry, you can try again!
- That’s it! You have a great action figure to put on display!
Posable Action Figures Printed Statically
Posable action figures are what first come to mind when I think of the term “Action Figure”. Again, Thingiverse.Com or Pinshape.Com are great places to find models to print. There are likely more parts to a posable action figure, as these have to have separate pieces for upper and lower arms, upper and lower legs, head and torso at the minimum.
The process is the same as for a static action figure. Print the parts, and prepare them. Sand as necessary. Prime, then paint the pieces before assembly.
Most posable action figures use a snap fit ball-and-socket style connection. These can be troublesome, as they can break during assembly. Press fitting them together can sometimes snap the ball off, so it’s best to do this carefully. If you find that the ball will not go into the socket without excessive pressure, take a rat-tail file and open up the socket some. You will want to do this in stages and test, to ensure that you haven’t made it too loose.
The worst case is that you’ll have to reprint a broken part or a too loose socket part. It’s good to remember that this isn’t just a model kit that you put together from a box. You created the parts, and you can create them again if you need them. Just remember that it’s not a fast process. It’s unlikely that you can download, print, prepare, paint and assemble a model in a day. With practice, this is very doable, but when starting out, give yourself time to learn and understand. You’ll have more fun that way!
Printing Articulated Action Figures
Theoretically, action figures can be printed already assembled, with their articulation already in place. The balls are printed already inside the sockets as necessary. I haven’t found any files for such already-assembled figures but I’m sure they’re around.
You’ll want to use a good FDM printer for this sort of print. It prints “dry”, or without more curable material around the pieces. If you try this with a resin DLP printer, the model may print, but the parts won’t articulate. The liquid resin can’t escape the ball and socket joints, so when the model cures in UV light, this excess trapped resin hardens too, jamming the ball and socket in one place, unable to articulate.
Have a look at these excellent action figures that you can print. The Iron Man figure is unbelievable! You do have to be careful assembling these, as the ball joints are very tight (which you want). If you’re using a DLP resin 3d printer, I recommend assembling after cleaning the parts but before UV curing the parts.
- https://www.myminifactory.com/category/action-figures

Digitally Sculpting Your Own Action Figure
3d CAD software that we use for making boxes, building models and car models is not well suited to creating organic forms. Instead, you’ll want to use a software that allows “Digital Sculpting”. With this style of software, you can create human (or alien) organic shapes. I’m no sculptor, so this is well beyond my comfort zone!
Some helpful softwares are out there.
- Maya
- Autodesk Mudbox
- Brush
- MakeHuman
Mastering these software can take some time, and just as with other skills, practice will be key. All of the listed softwares have the ability to export 3d STL files for use with a 3d printer. All that’s left is you, your imagination, and some 3d sculpting to create you own action figure. It’s beyond my skillset, but I’ve seen others do it, and create amazing pieces!
Take a look at the Wikipedia page for MakeHuman. It has some interesting ideas on how to start with a bare-formed human body and push, pull and prod it to make whatever figure you’re wanting.
Scanning Yourself For An Action Figure
Have a look at https://www.shapify.me/. This is a service that will create your action figure for you. You’ll have to go to them to get scanned, or find them at conventions that you may be attending! They produce some amazing models, and the best part is that they’re creating you, or more accurately, a mini you!
http://www.myfaceonafigure.com/ does a similar service, but you can send them your photos. Instead of a full body scan, they’re creating your face on a head, then matching that with an existing body. It means that flabby me doesn’t have to have flabby me action figure. It can be my face on Superman’s torso. That sounds much better!
These services are expensive. You can get just a head created for under $50 US, but a full body model will cost you $100 US or more!
Autodesk has created software to convert photos into 3d objects. It takes a lot of photos, but it can work nicely. I’ve seen this done with architecture mostly, but it could be used for people, too. It’s called Photogrammetry and it’s a relatively new technique. Check out https://www.autodesk.com/solutions/photogrammetry-software and see if it fits your needs.
Services also exist like My3DSelfie that will make 3D print action figures for you. Upload up to four images of the figure of your choice, and you’ll receive it on your doorstep in 3-5 weeks. It too can be a bit expensive, but you’ll find coupons on their website to get a significant discount, so well worth the look! What a cool way to make a birthday or Christmas present! They even do customized wedding cake toppers, so prospective brides and grooms, take note!
Related Questions
How much does it cost to make an action figure of yourself?
http://www.myfaceonafigure.com/ can create a 6” to 8” model for around $90 US or a 12” model for around $120 US. They come with packaging, and look professional grade.
Can you 3d Print Anime Figures?
An anime figure is no different than an action figure. It’s just the subject. If you can find the STL files for what you want, then you’re set. Download and print away! If they don’t exist where you can find them, it’s likely because the rights holder of the intellectual property wants to control that likeness and doesn’t want it readily available. In this case, you may need to sculpt your own 3d model for printing.
Tweet
09.03.2022
Content
- How to choose a 3D printer for miniatures
- Advantage of 3D printing for miniatures 9000 9000 FDM 9000 LCD/ DLP
- FDM
- LCD
Miniature figurines with amazing detail attract the eye. A little grotesqueness and slightly wrong proportions (otherwise it would be inconvenient to play or transport such a “little one”) are more than compensated by detailed elaboration and an abundance of small, at first glance, insignificant details. These are no longer just small table soldiers, but heroes with their own unique history.
Warhammer 40k 9 miniature soldier0044
Miniatures come in different sizes: from 6mm and more. The most popular today is the 28mm format. The creation of such figurines is really almost jewelry work.
A 3D printer will help not only in the production of miniatures, but also in related areas, such as the creation of figurines, details of game locations, or, for example, elements of dioramas. To understand the advantages of 3D printing over classical manufacturing methods, it is worth remembering how such models are usually made at home. nine0003
Advantage of 3D printing for miniatures
Not everyone was ready to shell out a substantial amount for the purchase of a set of table soldiers, and sometimes the necessary heroes simply were not on sale. Then baked and self-hardening plastics for modeling were used.
First you need to make a wire frame, so the finished figure will turn out to be more durable, and it will be much easier to keep all the proportions. The wire frame can be attached to the stand, which will make the miniature statue more stable, and it can be easily fixed in any position without fear of smearing small parts with your fingers. nine0003
Wire frame for miniature
Gradually, layer by layer, the volume of plastic increases on the frame. Each layer must be baked or dried well, depending on which plastic is used - self-hardening or baked.
Gradually, we begin to add small details and work out the details. In fact, this is a very painstaking process that requires perseverance and some sculpting abilities. For a convenient study of small details, you may need special stacks for modeling, but they can be successfully replaced with improvised tools. nine0003
Sculpting tool set
The result is such a miniature statue.
Miniature 28mm baked plastic
By the same principle, large table figures, or some elements of dioramas, can be made.
Sometimes a sculptor is more accustomed to working with plasticine. Then, after sculpting, the stage of preparation and casting of the figurine into a silicone mold is added. This method is suitable for small-scale production of a small desktop army. nine0003
But it is necessary to properly prepare the figurine for casting. The finished "warrior", most likely, will have to be divided into several parts, so that it would be more convenient for the caster to remove the molds and make castings. During the cutting process, it is worth adding a few locks so that the finished castings can be easily assembled, like pieces of a puzzle.
Molded figurine against silicone mold
Some craftsmen have learned to cast metal copies. Such soldiers are usually made of low-melting metals (for example, lead) and cast in plaster molds. Sometimes a special silicone is used, but it is a little more difficult to achieve good shedding of a small product in a silicone mold. nine0003
Cast metal soldier
In addition to making figurines from scratch, some craftsmen remake ready-made miniatures. This is called conversion.
Conversion in miniatures is a refinement, stylization or alteration of a finished figure. Unfortunately, not every hobbyist has good sculpting skills, and this alteration helps to achieve good results regardless of artistic skills. The main thing is to act very carefully. nine0044
Conversion helps enthusiasts achieve amazing figurine detail, add some detail, change the pose, or create a new character that is not yet on sale.
Lord of the Astral Claws turned to Chaos
In addition to making the figures themselves, modelers create colorful locations to immerse themselves in the world of their favorite game. This is true not only for 28mm miniatures, but for example for DND games. Such voluminous locations allow you to immerse yourself in the world of your favorite game much better and make the game more exciting. nine0003
Game location for board game Warhammer40k
The creation of such locations is painstaking work, and both improvised and special equipment are used as material.
Role play location
A 3D printer allows you to produce miniature figures and game locations much faster. On the Internet you can find many paid and free models of 28mm figures from different universes or various elements of locations - houses, fences, mechanisms, etc. Adapting or slightly changing the finished 3D model for yourself is much easier than cutting and gluing a finished figure. And creative people with modeling skills are unlikely to have difficulties with the transition to “digital clay”. nine0003
Warhammer40k universe 3D miniature model
And of course, dioramas are worth noting. This is a separate art form with a scene or location frozen in time. Dioramas come in different sizes, but each of them impresses with its detail and careful study.
Diorama based on the game STALKER
nine0003
Each diorama is unique, so the craftsmen use improvised materials to make it. Everything is limited only by the imagination and ingenuity of the artist.
Diorama “Desert Hero”
The main advantage of 3D printing is high detail and repeatability. If you need to make a small batch of miniatures, it will be much easier to print them than to cast, for example. Casting small items is a painstaking process that requires some skill and equipment. It is very difficult to achieve good pourability of small products the first time. nine0003
From model to finished figure
And for the manufacture of piece products, such as a diorama element, a 3D printer can replace many materials and tools for modeling. In addition, by using and combining different materials, it is possible to create models that are difficult or almost impossible to create manually. For example, using a special polymer, you can print optically transparent products that can imitate glass. nine0003
Which technology to choose
To begin with, it is important to determine the requirements for the printer - will it be used only for the manufacture of 28mm personal army or should it be a universal printing machine? It is important to understand what size the finished model will be, how detailed it should be, and how much time can be spent on post-processing.
Depending on this, it is worth deciding on the technology by which the 3D printer will work. You can choose one of two technologies - FDM or photopolymer printing (there are several technologies, but DLP and LCD printers are currently popular). nine0003
FDM
FDM 3D printers use a plastic filament as a material. In a heated extruder, the filament is melted and extruded through a thin nozzle, so layer by layer, a three-dimensional model is grown.
Working principle of FDM 3D printer
Layer thickness and nozzle diameter can be changed in some printer models. The minimum layer is usually 0.1 mm. In some models of 3D printers, a layer of 0.05 is available, but for printing with such a layer, it is important to choose the right many settings and the print speed will be quite slow. nine0044
Pros:
-
Large print area
-
Many different materials are available for every “taste and budget”
-
Inexpensive Consumables
Cons:
Of course, FDM printers are hardly suitable for making miniature figures, but they can be successfully used to print large souvenir figures, create game locations and some parts of dioramas. nine0003
LCD/DLP
The principles of operation of LCD and DLP printers are very similar. The material used is polymers that harden under the action of UV light. The only difference is that an LCD printer uses an LED matrix in conjunction with an LCD screen as a source of UV radiation, while a DLP uses a projector.
Working principle of photopolymer 3D printer
Pros:
- nine0002 The ideal surface of the finished figure
-
Many different materials available
-
High print accuracy even for the smallest items
Cons:
Photopolymer 3D printers are able to create miniature products that cannot be made using FDM technology. This technology will be an ideal choice for creating miniatures, small poster models, etc. nine0003
Print examples
Robot printed on Asiga Pro 4k
Figurine made with Phrozen Sonic Mini 4k
28mm 3D printed miniatures
3D Printed Halloween Miniature
3D printed play models
FDM Cube Thrower
Figure making process from 3D model to painting
Best Printer Ranking
FDM
Creality3D Ender 3 (Build Kit)
nine0210 Features:
Print technology: FDM/FFF
Working area size: 220x220x250 mm
Number of extruders: 1
Max. extruder temperature: max. 255℃
Closed Camera: No
Heated table: Yes
Plastic type: ABS, PLA, PETG, Flex, Decorative plastics, others
A popular and unpretentious 3D printer that many makers liked. Creality3D Ender 3 is sold as a kit (assembly kit), but thanks to the detailed instructions, there should be no problems with assembly. nine0003
Wanhao Duplicator 6 Plus
Features:
Print technology: FDM/FFF
Working area size: 200*200*180mm
Number of extruders: 1
Max. extruder temperature: max. 260°C
Closed Camera: Optional
Heated table: Yes
Plastic type: ABS, PLA, PETG, Flex, Decorative plastics, others nine0003
Wanhao Duplicator 6 Plus is an updated version of the Duplicator 6. The new modification adds automatic calibration, printing resume after a power outage, and others. You can immediately purchase a printer with a closed case, this will allow you to easily print with composites. Wanhao Duplicator 6 Plus will become a trouble-free workhorse, and thanks to the “omnivorous” extruder, even a beginner will be able to print exotic materials without any problems, such as soft flexes or rubbers. nine0003
FlashForge Creator Pro 2
Features:
Print technology: FDM/FFF
Working area size: 200x148x150 mm
Number of extruders: 2
Max. extruder temperature: max. 240°C
Closed Camera: Yes
Heated table: Yes
Plastic type: ABS, PLA, PETG, Flex, Decorative plastics, others nine0003
FlashForge Creator Pro 2 is an almost professional dual extruder 3D printer. Thanks to the closed body, Creator Pro 2 has no problem even with composite materials, and two extruders allow the use of soluble support for complex models. Moreover, FlashForge extruders are independent, this allows you to print 2 mirror or identical models at the same time. This allows you to speed up the production of the same type of models. FlashForge Creator Pro 2 will not only be a good home printer, but also a great helper for a workshop or small production. nine0003
LCD
Anycubic Photon Mono 4K
Features:
LCD display resolution: 3840x2400 (4K)
UV wavelength: 405 nm
Working area size: 132x80x165 mm
Layer thickness: 0.01-0.15mm
Inexpensive, but fairly modern 3D printer with a 4K monochrome display. Anycubic Photon Mono 4K will be a good tool for printing miniature models. nine0003
Phrozen Sonic Mini 4K
Features:
LCD resolution: 6.1" 4K Mono LCD
XY positioning accuracy: 35 microns
UV wavelength: 405 nm
Working area size: 134x75x130 mm
Layer thickness: 0.01-0.30mm
The Phrozen Sonic Mini 4K is a compact high resolution 3D printer. It allows you to get accurate models even with an abundance of small details. Sonic Mini 4K is a good choice for those who need to print quickly and accurately. nine0003
Phrozen Sonic Mighty 4K
Features:
LCD resolution: 9.3" 4K Mono LCD
XY positioning accuracy: 52 microns
UV wavelength: 405 nm
Working area size: 200x125x220 mm
Layer thickness: 0.01-0.3mm
With a larger work area, the Phrozen Sonic Mighty 4K allows you to quickly produce large models or small batches of small items. Such a 3D printer will be a good help for a small workshop or a hobby circle. nine0003
Phrozen Sonic Mini 8K
Features:
LCD resolution: 7.1" 8K Mono LCD
XY Positioning Accuracy: 22 µm
UV wavelength: 405 nm
Working area size: 165x72x180 mm
Layer thickness: 0.01-0.3mm
Phrozen Sonic Mini 8K is one of the representatives of 8K photopolymer printers, which can still be counted on the fingers of one hand. The high resolution LCD-matrix allows you to print figures with amazing surface quality and amazing detail. Such a printer is suitable for demanding printers who care about accuracy and the perfect surface of the finished model. nine0003
Totals
3D printers are gradually showing themselves to be great helpers in many areas, not only in medicine and industry, but also in home hobbies. Thanks to 3D printing, it is possible to produce small figurines or elements of dioramas much faster, paying more attention to the elaboration of details, rather than painstaking modeling or the search for exotic materials.
And digitalization makes it much easier to share your work and finished models in the community or adjust them to your needs, for example, change the scale or adjust the pose. nine0003
Free Shipping
Add to compare
Item added to compare Go
Manufacturer | Phrozen
Free Shipping
Add to compare
Product added to compare Go
Manufacturer | nine0487 Anycubic
Free Shipping
Add to compare
Product added to compare Go
Manufacturer | Phrozen
Free Shipping
Add to compare
Product added to compare Go
Manufacturer | Phrozen
Free Shipping
Add to compare
Product added to compare Go
Manufacturer | FlashForge |
Add to compare
Product added to compare Go
Manufacturer | nine0487 Creality
Free Shipping
Add to compare
Product added to compare Go
Manufacturer | Wanhao |
#Application
Share
all materials
3D printer printing figurines, printing 3D models to order.
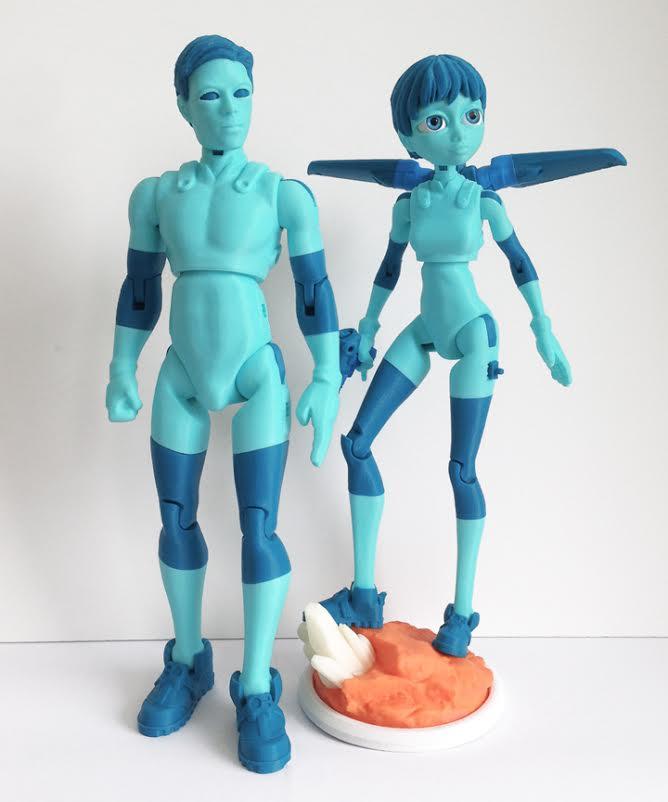
Printing 3D models to order is becoming an increasingly popular service, as it allows you to turn a virtual model into a real product in a short time.
One of the world's most popular applications - 3D printer printing figures - in the future is quite capable of replacing the usual photographs.
You can make a unique and unforgettable gift for friends and family by choosing to print 3D models to order and choosing one of the many options:
- own miniature;
- figurines of loved ones;
- 3 d sculptures of newlyweds;
- picture of friends and colleagues;
- images of idols;
- figurines of your favorite characters;
- ultrasound baby;
- 3D printed children's drawing;
- figurine of a pet;
- miniature vehicle;
- 3d copy of a work of art, etc.
Any 3d model is made by professional designers based on photographs taken from different angles, or based on 3d scanning using computer technology. In both cases, the work consists of two stages. At the first stage the designer creates a virtual 3D model, which can then be repeatedly printed. The second stage of is the making of the figurine itself.
When planning to print 3D models to order, you can choose the size convenient for you, stylish monochrome or realistic colorful option. Printing of 3D models is carried out on special equipment using modern high-quality environmentally friendly materials. nine0588 Colored Gypsum Resin provides photographic accuracy, Monochrome Resin delivers the finest details, and 1 or 2-colour plastic printing is the best value for money. In addition to the choice of material, the cost of a 3d portrait is also affected by its scale and degree of detail.