Additive manufacturing 3d printing ppt
PPT – 3D Printing Future And Benefits PowerPoint presentation | free to download
About This Presentation
Transcript and Presenter's Notes
Title: 3D Printing Future And Benefits
1
3D Printing Future And Benefits
- Current and future applications of 3D Printing
2
Biomedical Engineering
- In recent years, scientists and engineers have
already been able to use 3D printing technology
to create body parts and parts of organs. The
first entire organ created through 3D Printing is
expected to be done in the coming years. The
process of creating the organ or body part is
exactly the same as if you were to create a
plastic or metal part, however, instead the raw
material used are biological cells created in a
lab.By creating the cells specifically for a
particular patient, one can be certain that the
patients body will not reject the organ. - Another application of 3D printing in the
biomedical field is that of creating limbs and
other body parts out of metal or other materials
to replace lost or damaged limbs. Prosthetic
limbs are required in many parts of the world due
to injuries sustained during war or by disease.
Currently prosthetic limbs are very expensive and
generally are not customized for the patients
needs. 3D printing is being used to design and
produce custom prosthetic limbs to meet the
patients exact requirements. By scanning the
patients body and existing bone structure,
designers and engineers are able to re-create the
lost part of that limb.
3
Aerospace and Automobile Manufacturing
- High technology companies such as aerospace and
automobile manufacturers have been using 3D
printing as a prototyping tool for some time now.
However, in recently years, with further
advancement in 3D printing technology, they have
been able to create functional parts that can be
used for testing. This process of design and 3D
printing has allowed these companies to advance
their designs faster than ever before due to the
large decrease in the design cycle. From what
used to take months between design and the
physical prototype, now within hours the design
team can have a prototype in their hands for
checks and testing. - The future of 3D printing in these industries
lies with creating working parts directly from a
3D printer for use in the final product, not just
for testing purposes. This process is already
underway for future cars and aircraft. The way in
which 3D printing works (creating a part layer by
layer) allows the designer to create the part
exactly the way is needs to be to accomplish the
task at hand.Extremely complex geometry can be
easily created using a 3D printer, allowing for
parts to be lighter, yet stronger than their
machined counterparts.
4
Construction and Architecture
- Architects and city planners have been using 3D
printers to create a model of the layout or shape
of a building for many years.Now they are looking
for ways of employing the 3D printing concept to
create entire buildings. There are already
prototype printer systems that use concrete and
other more specialized materials to create a
structure similar to a small house. - The goal is the replace many cranes and even
construction workers with these printing systems.
They would work by using the 3D design model
created on CAD software, to create a layer by
layer pattern on the building just as a normal 3D
printer works today. Most of the innovation in
this area will have to come from the creation of
the appropriate materials.
5
Product Prototyping
- The creation of a new product has been always one
that involves many iterations of the same
design.3D Printing revolutionized the industry by
allows designers to create and the next day see
and touch their design. No longer did it take
several meetings for everyone to agree on one
design to create, and then wait months for the
actual part to arrive. Nowadays a version of each
idea is created and the next day, all are
reviewed together, thus giving the ability to
compare and contrast each ones features.Plastic
parts, for example, require molds and tooling to
be created, these custom parts are expensive to
create, therefore one must be certain the part
designed meets the requirements. With 3D printing
you can create a part that will look and feel
exactly like the finished product. Some parts can
also be tested just as the real injection molded
part would.
6
3D Printing Benefits Value
- 3D printing, whether at an industrial, local or
personal level,brings a host of bene fits that
traditional methods of manufacture (or
prototyping) simply cannot. - Customisation
- 3D printing processes allow for mass
customization the ability to personalize
products according to individual needs and
requirements. Even within the same build chamber,
the nature of 3D printing means that numerous
products can be manufactured at the same
time,according to the end-users requirements at
no additional process cost.
7
- Complexity
- The advent of 3D printing has seen a
proliferation of products (designed in digital
environments), which involve levels of
complexity that simply could not be produced
physically in any other way. While this advantage
has been taken up by designers and artists to
impressive visual effect, it hasalsomade a
significant impact on industrial applications,
whereby applications are being developed to
materialize complex components that are proving
to be both lighter and stronger than their
predecessors.Notable uses are emerging in the
aerospace sector where these issues are of
primary importance.
8
- Tool-less
- For industrial, manufacturing, one of the most
cost-, time- and labor-intensive stages of the
product development process is the production of
the tools. For low to medium volume applications,
industrial 3D printing or additive
manufacturing can eliminate the need for tool
production and, therefore, the costs, lead times
and labour associated with it. This is an
extremely attractive proposition, that an
increasing number or manufacturers are taking
advantage of. Furthermore, because of the
complexity advantages stated above, products and
components can be designed specifically to avoid
assembly requirements with intricate geometry and
complex features further eliminating the labour
and costs associated with assembly processes.
9
- Sustainable / Environmentally Friendly
- 3D printing is also emerging as an energy-e
efficient technology that can provide
environmental efficiencies in terms of both the
manufacturing process itself, utilizing up to 90
of standard materials, and, therefore, creating
less waste, but also throughout an
additivelymanufactured products operating life,
by way of lighter and stronger design that
imposes a reduced carbon footprint compared with
traditionally manufactured products.!Furthermore,
3D printing is showing great promise in terms of
fulfilling a local manufacturing model, whereby
products are produced on demand in the place
where they are needed eliminating huge
inventories and unsustainable logistics for
shipping high volumes of products around the
world.
10
- Thank You
- www.
jewelkreator.com
About PowerShow.com
What is 3D Printing? - Technology Definition and Types
3D printing, also known as additive manufacturing, is a method of creating a three dimensional object layer-by-layer using a computer created design.
3D printing is an additive process whereby layers of material are built up to create a 3D part. This is the opposite of subtractive manufacturing processes, where a final design is cut from a larger block of material. As a result, 3D printing creates less material wastage.
This article is one of a series of TWI frequently asked questions (FAQs).
3D printing is also perfectly suited to the creation of complex, bespoke items, making it ideal for rapid prototyping.
Contents
- What materials can be used?
- History
- Technologies
- Process types
- How long does it take?
- Advantages and disadvantages
- What is an STL file?
- Industries
- Services
- FAQs
TWI
TWI is an Industrial Membership based organisation. TWI's experts can provide your company with an extension to your own resources. Our experts are dedicated to helping industry improve safety, quality, efficiency and profitability in all aspects of materials joining technology. Industrial Membership of TWI currently extends to over 600 companies worldwide, embracing all industrial sectors.
You can find out more by contacting us, below:
There are a variety of 3D printing materials, including thermoplastics such as acrylonitrile butadiene styrene (ABS), metals (including powders), resins and ceramics.
Who Invented 3D Printing?
The earliest 3D printing manufacturing equipment was developed by Hideo Kodama of the Nagoya Municipal Industrial Research Institute, when he invented two additive methods for fabricating 3D models.
When was 3D Printing Invented?
Building on Ralf Baker's work in the 1920s for making decorative articles (patent US423647A), Hideo Kodama's early work in laser cured resin rapid prototyping was completed in 1981. His invention was expanded upon over the next three decades, with the introduction of stereolithography in 1984. Chuck Hull of 3D Systems invented the first 3D printer in 1987, which used the stereolithography process. This was followed by developments such as selective laser sintering and selective laser melting, among others. Other expensive 3D printing systems were developed in the 1990s-2000s, although the cost of these dropped dramatically when the patents expired in 2009, opening up the technology for more users.
There are three broad types of 3D printing technology; sintering, melting, and stereolithography.
- Sintering is a technology where the material is heated, but not to the point of melting, to create high resolution items.
Metal powder is used for direct metal laser sintering while thermoplastic powders are used for selective laser sintering.
- Melting methods of 3D printing include powder bed fusion, electron beam melting and direct energy deposition, these use lasers, electric arcs or electron beams to print objects by melting the materials together at high temperatures.
- Stereolithography utilises photopolymerization to create parts. This technology uses the correct light source to interact with the material in a selective manner to cure and solidify a cross section of the object in thin layers.
Types of 3D printing
3D printing, also known as additive manufacturing, processes have been categorised into seven groups by ISO/ASTM 52900 additive manufacturing - general principles - terminology. All forms of 3D printing fall into one of the following types:
- Binder Jetting
- Direct Energy Deposition
- Material Extrusion
- Material Jetting
- Powder Bed Fusion
- Sheet Lamination
- VAT Polymerization
Binder Jetting
Binder jetting deposits a thin layer of powered material, for example metal, polymer sand or ceramic, onto the build platform, after which drops of adhesive are deposited by a print head to bind the particles together. This builds the part layer by layer and once this is complete post processing may be necessary to finish the build. As examples of post processing, metal parts may be thermally sintered or infiltrated with a low melting point metal such as bronze, while full-colour polymer or ceramic parts may be saturated with cyanoacrylate adhesive.
Binder jetting can be used for a variety of applications including 3D metal printing, full colour prototypes and large scale ceramic moulds.
Direct Energy Deposition
Direct energy depositioning uses focussed thermal energy such as an electric arc, laser or electron beam to fuse wire or powder feedstock as it is deposited. The process is traversed horizontally to build a layer, and layers are stacked vertically to create a part.
This process can be used with a variety of materials, including metals, ceramics and polymers.
Material Extrusion
Material extrusion or fused deposition modelling (FDM) uses a spool of filament which is fed to an extrusion head with a heated nozzle. The extrusion head heats, softens and lays down the heated material at set locations, where it cools to create a layer of material, the build platform then moves down ready for the next layer.
This process is cost-effective and has short lead times but also has a low dimensional accuracy and often requires post processing to create a smooth finish. This process also tends to create anisotropic parts, meaning that they are weaker in one direction and therefore unsuitable for critical applications.
Material Jetting
Material jetting works in a similar manner to inkjet printing except, rather than laying down ink on a page, this process deposits layers of liquid material from one or more print heads. The layers are then cured before the process begins again for the next layer. Material jetting requires the use of support structures but these can be made from a water-soluble material that can be washed away once the build is complete.
A precise process, material jetting is one of the most expensive 3D printing methods, and the parts tend to be brittle and will degrade over time. However, this process allows for the creation of full-colour parts in a variety of materials.
Powder Bed Fusion
Powder bed fusion (PBF) is a process in which thermal energy (such as a laser or electron beam) selectively fuses areas of a powder bed to form layer, and layers are built upon each other to create a part. One thing to note is that PBF covers both sintering and melting processes. The basic method of operation of all powder bed systems is the same: a recoating blade or roller deposits a thin layer of the powder onto the build platform, the powder bed surface is then scanned with a heat source which selectively heats the particles to bind them together. Once a layer or cross-section has been scanned by the heat source, the platform moves down to allow the process to begin again on the next layer. The final result is a volume containing one or more fused parts surrounded by unaffected powder. When the build is complete, the bed is fully raised to allow the parts to be removed from the unaffected powder and any required post processing to begin.
Selective laser sintering (SLS) is often used for manufacture of polymer parts and is good for prototypes or functional parts due to the properties produced, while the lack of support structures (the powder bed acts as a support) allows for the creation of pieces with complex geometries. The parts produced may have a grainy surface and inner porosity, meaning there is often a need for post processing.
Direct metal laser sintering (DMLS), selective laser melting (SLM) and electron beam powder bed fusion (EBPBF) are similar to SLS, except these processes create parts from metal, using a laser to bond powder particles together layer-by-layer. While SLM fully melts the metal particles, DMLS only heats them to the point of fusion whereby they join on a molecular level. Both SLM and DMLS require support structures due to the high heat inputs required by the process. These support structures are then removed in post processing ether manually or via CNC machining. Finally, the parts may be thermally treated to remove residual stresses.
Both DMLS and SLM produce parts with excellent physical properties - often stronger than the conventional metal itself, and good surface finishes. They can be used with metal superalloys and sometimes ceramics which are difficult to process by other means. However, these processes can be expensive and the size of the produced parts is limited by the volume of the 3D printing system used.
Sheet Lamination
Sheet lamination can be split into two different technologies, laminated object manufacturing (LOM) and ultrasonic additive manufacturing (UAM). LOM uses alternate layers of material and adhesive to create items with visual and aesthetic appeal, while UAM joins thin sheets of metal via ultrasonic welding. UAM is a low temperature, low energy process that can be used with aluminium, stainless steel and titanium.
VAT Photopolymerization
VAT photopolymerization can be broken down into two techniques; stereolithography (SLA) and digital light processing (DLP). These processes both create parts layer-by-layer through the use of a light to selectively cure liquid resin in a vat. SLA uses a single point laser or UV source for the curing process, while DLP flashes a single image of each full layer onto the surface of the vat. Parts need to be cleaned of excess resin after printing and then exposed to a light source to improve the strength of the pieces. Any support structures will also need to be removed and additional post-processing can be used to create a higher quality finish.
Ideal for parts with a high level of dimensional accuracy, these processes can create intricate details with a smooth finish, making them perfect for prototype production. However, as the parts are more brittle than fused deposition modelling (FDM) they are less suited to functional prototypes. Also, these parts are not suitable for outdoor use as the colour and mechanical properties may degrade when exposed to UV light from the sun. The required support structures can also leave blemishes that need post processing to remove.
The printing time depends on a number of factors, including the size of the part and the settings used for printing. The quality of the finished part is also important when determining printing time as higher quality items take longer to produce. 3D printing can take anything from a few minutes to several hours or days - speed, resolution and the volume of material are all important factors here.
The advantages of 3D printing include:
- Bespoke, cost-effective creation of complex geometries:
This technology allows for the easy creation of bespoke geometric parts where added complexity comes at no extra cost. In some instances, 3D printing is cheaper than subtractive production methods as no extra material is used. - Affordable start-up costs:
Since no moulds are required, the costs associated with this manufacturing process are relatively low.The cost of a part is directly related to the amount of material used, the time taken to build the part and any post processing that may be required.
- Completely customisable:
Because the process is based upon computer aided designs (CAD), any product alterations are easy to make without impacting the manufacturing cost. - Ideal for rapid prototyping:
Because the technology allows for small batches and in-house production, this process is ideal for prototyping, which means that products can be created faster than with more traditional manufacturing techniques, and without the reliance on external supply chains. - Allows for the creation of parts with specific properties:
Although plastics and metals are the most common materials used in 3D printing, there is also scope for creating parts from specially tailored materials with desired properties. So, for example, parts can be created with high heat resistance, water repellency or higher strengths for specific applications.
The disadvantages of 3D printing include:
- Can have a lower strength than with traditional manufacture:
While some parts, such as those made from metal, have excellent mechanical properties, many other 3D printed parts are more brittle than those created by traditional manufacturing techniques. This is because the parts are built up layer-by-layer, which reduces the strength by between 10 and 50%. - Increased cost at high volume:
Large production runs are more expensive with 3D printing as economies of scale do not impact this process as they do with other traditional methods. Estimates suggest that when making a direct comparison for identical parts, 3D printing is less cost effective than CNC machining or injection moulding in excess of 100 units, provided the parts can be manufactured by conventional means. - Limitations in accuracy:
The accuracy of a printed part depends on the type of machine and/or process used.Some desktop printers have lower tolerances than other printers, meaning that the final parts may slightly differ from the designs. While this can be fixed with post-processing, it must be considered that 3D printed parts may not always be exact.
- Post-processing requirements:
Most 3D printed parts require some form of post-processing. This may be sanding or smoothing to create a required finish, the removal of support struts which allow the materials to be built up into the designated shape, heat treatment to achieve specific material properties or final machining.
An STL file is a simple, portable format used by computer aided design (CAD) systems to define the solid geometry for 3D printable parts. An STL file provides the input information for 3D printing by modelling the surfaces of the object as triangles that share edges and vertices with other neighbouring triangles for the build platform. The resolution of the STL file impacts the quality of the 3D printed parts - if the file resolution is too high the triangle may overlap, if it is too low the model will have gaps, making it unprintable. Many 3D printers require an STL file to print from, however these files can be created in most CAD programs.
Due to the versatility of the process, 3D printing has applications across a range of industries, for example:
Aerospace
3D printing is used across the aerospace (and astrospace) industry due to the ability to create light, yet geometrically complex parts, such as blisks. Rather than building a part from several components, 3D printing allows for an item to be created as one whole component, reducing lead times and material wastage.
Automotive
The automotive industry has embraced 3D printing due to the inherent weight and cost reductions. It also allows for rapid prototyping of new or bespoke parts for test or small-scale manufacture. So, for example, if a particular part is no longer available, it can be produced as part of a small, bespoke run, including the manufacture of spare parts. Alternatively, items or fixtures can be printed overnight and are ready for testing ahead of a larger manufacturing run.
Medical
The medical sector has found uses for 3D printing in the creation of made-to-measure implants and devices. For example, hearing aids can be created quickly from a digital file that is matched to a scan of the patient's body. 3D printing can also dramatically reduce costs and production times.
Rail
The rail industry has found a number of applications for 3D printing, including the creation of customised parts, such as arm rests for drivers and housing covers for train couplings. Bespoke parts are just one application for the rail industry, which has also used the process to repair worn rails.
Robotics
The speed of manufacture, design freedom, and ease of design customisation make 3D printing perfectly suited to the robotics industry. This includes work to create bespoke exoskeletons and agile robots with improved agility and efficiency.
TWI has one of the most definitive ranges of 3D Printing services, including selective laser melting, laser deposition, wire and arc additive manufacturing, wire and electron beam additive manufacturing and EB powder bed fusion small-scale prototyping, and more.
Additive Manufacturing
TWI provides companies with support covering every aspect of metal additive manufacturing (AM), from simple feasibility and fabrication projects to full adoption and integration of metal AM systems.
Laser Metal Deposition
TWI has been developing LMD technology for the last ten years. For full details of our capabilities in this area, and to find out more about the process and the benefits it can bring to your business.
Selective Laser Melting
TWI has been developing selective laser melting technology for the last decade. Find out full details of our capabilities in this area and the benefits it can bring to your business.
Can 3D Printing be used for Mass Production?
While there have been great advances in 3D printing, it still struggles to match other manufacturing techniques for high volume production. Techniques such as injection moulding allow for much faster mass production of parts.
Where is 3D Printing Heading in the Future?
As 3D printing technology continues to improve it could democratise the manufacture of goods. With printers becoming faster, they will be able to work on larger scale production projects, while lowering the cost of 3D printing will help its use spread outside of industrial uses and into homes, schools and other settings.
Which 3D Printing Material is most Flexible?
Thermoplastic polyurethane (TPU) is commonly deemed to be the most flexible material available to the 3D printing industry. TPU possesses bendable and stretchy characteristics that many other filaments do not have.
Which 3D Printing Material is the Strongest?
Polycarbonate is seen as the strongest 3D printing material, with a tensile strength of 9,800 psi, compared to nylon, for example, with just 7,000 psi.
Why is 3D Printing Important?
3D printing is important for the many benefits it brings. It allows users to produce items that have geometries which are difficult or impossible for traditional methods to produce. It also allows users with a limited experience to edit designs and create bespoke, customised parts. On-demand 3D printing also saves on tooling costs and provides an advanced time-to-market. 3D printing is important for industries such as aerospace, where it can create lightweight yet complex parts, offering weight saving, the associated fuel reductions and a better environmental impact as a result. It is also important for the creation of prototypes that can advance industry.
Will 3D Printing Replace Traditional Manufacturing?
3D printing has the capability to disrupt traditional manufacturing through the democratisation of production along with the production of moulds, tools and other bespoke parts. However, challenges around mass production mean that 3D printing is unlikely to replace traditional manufacturing where high volume production of comparatively simple parts is required.
Are 3D Printing Fumes Dangerous?
3D printing fumes can be dangerous to your health as the process produces toxic filament fumes. These emissions are produced as the plastic filaments are melted to create the product layer-by-layer. However, correct procedures such as ensuring sufficient ventilation or using extractors can solve this issue.
Related Frequently Asked Question (FAQs)
What are the Pros and Cons of 3D Printing?
The demand is growing due to some of the revolutionary benefits that it can provide. Like almost all technologies it has its own drawbacks that need considering.
How Long Does 3D Printing Take?
There are several factors that determine the time it takes to 3D print a part. These include the size, height, complexity and the printing technology used.
Can 3D Printing Use Metal?
Yes, it is possible to 3D print items from metal. There are several types of process which fall under the heading of metal additive manufacturing.
What is Additive Manufacturing?
Additive manufacturing (AM) is a computer controlled process that creates three dimensional objects by depositing materials, usually in layers.
3D printing - online presentation
Similar presentations:
3D Printing Technologies and Trends
Additive technologies: 3D printing
Additive manufacturing technologies
3D printing
3D printing technologies at the enterprise "3D Techno"
Methods and technologies for prototyping products. (Lecture 7)
Control of technological processes based on computer CAD systems in mechanical engineering. (Lecture 7)
Additive Manufacturing
Additive technologies in mechanical engineering
Additive technologies
3D printing
3D printer
3D printer (fabber, Rapid Prototyper) is a peripheral device that uses the
method of layer-by-layer creation of a physical object from a digital 3D model.
Charles Hull - founder of 3D Systems Corporation
3D printing - additive manufacturing
Application:
• prototyping (rapid prototyping),
• production of finished products (fast production).
Printer resolution - thickness
applied layers (Z-axis) 16-200 microns.
Accuracy
printer
-
accuracy
positioning of the print head in
horizontal plane (along the X and Y axes)
10-100 microns.
Two types of materials:
support materials.
Structural
and
Method
Extrusion
Technology
Fusion Deposition Modeling
(FDM or FFF)
Wireframe
Free Form
Electron Beam Melting (EBFȝ)
Direct Metal Laser Sintering (DMLS)
Powder
Electron Beam Melting (EBM)
Selective Laser Melting (SLM)
Titanium Alloys, Cobalt Chromium Alloys
Stainless steel, aluminum
Heat selective sintering (SHS)
Thermoplastic powders
Laser selective sintering (SLS)
Thermoplastics, metal powders,
ceramic powders
Gypsum, plastics, metal powders,
sand mixtures
Paper, metal foil,
plastic film
Photopolymers
Photopolymers
Inkjet
3D Inkjet Printing (3DP)
Lamination
Object Fabrication
Lamination (LOM)
Digital LED Projection (DLP)
Polymerization
Materials used
Thermoplastics (such as polylactide
(PLA), acrylonitrile butadiene styrene (ABS)
etc. )
Almost any metal
alloys
Almost any metal
alloys
Titanium alloys
products by layer-by-layer laying of the melted
thread from the fusible working material.
Developed by S. Scott Trump in the late 1980s
Trademark of Stratasys Inc.
FDM variant
Testing of a device prototype
operating on EBFȝ technology
Laser sintering of powder materials
(Selective Laser Sintering, SLS)
SLS
additive manufacturing technology
for the production of models, prototypes and finished products
from fusible powder material
(plastic, metal ) by melting it under
laser radiation.
Designed by Carl Deckard and Joseph Beeman,
University of Texas at Austin Mid 1980s.
Acquired in 2001 by competing
company 3D Systems.
The last of the SLS
technology patents was filed on January 28, 1997,
expired on January 28, 2014, and
technology is publicly available.
Rapid Prototyping
Solutions
Five Star Plastics
New Balance
uses
SLS technology to create
footwear
Selective Laser Melting (SLM)
Developed by the Institute for Laser Technology (ILT)
Fraunhofer Aachen and F&S
Stereolithographietechnik GmbH in Paderborn.
Today the technology belongs to SLM
Solutions GmbH and ReaLizer GmbH
A variation of SLS
technology The process takes place in a working chamber filled with
inert gases (argon). Oxygen-free
avoids oxidation of consumable
(can be printed with metals).
J2-X rocket engine part printed by NAS
Direct Metal Laser Sintering (DMLS)
Developed by EOS, Munich
A variation of Selective Laser Sintering or SLS
and Selective Laser Melting or SLM.
DMLS allows the
to create solid
metal parts.
print resolution ~20 µm
DMLS setup
Rocket engine parts
Super Draco
Elon Musk, Space X
Nickel-chromium material
Inconel superalloy
Electron beam melting (EBM)
A variation of SLS and SLM
The main difference is the use of electronic emitters instead of lasers
Titanium implant obtained using EBM
Industrial EBM machine manufactured
by the Swedish company Arcam AB
Craniofacial
implant manufactured using
using EBM technology
Selective heat sintering ( SHS)
A variant of SLS technology
Used for fusible materials
Desktop SHS printer - Blueprinter
Models printed with SHS method
• Institute for Problems of Laser and Information Technologies
RAS.
Resolution
down to 15 microns
Desktop
stereo lithography
OWL printer
Nano
Digital LED projection (DLP)
A variation of SLA technology
Difference - the use of LED projector
Helisys Inc.
LOM
-
technology
forming
layer-by-layer bonding (heat, pressure)
thin
films
working
material
with
cutting (using a laser beam or
cutting tool
)
corresponding
contours on each layer.
Mcor 3D Printer
Matrix Plus
3D Inkjet Printing (3DP)
Developed by Massachusetts Institute of Technology (MIT)
, 1993
Name Variations:
• Ink Jet Modeling
• Multi-Jet Modeling, MJM,
• Poly25, 900 • Drop-On-Demand-Jet, DODJet.
support materials - wax,
modeling materials
-
gypsum,
metal powders, sand mixtures
plastics,
Powder bonding technology (Binding
powder by adhesives)
Manufacturing company: Z Corporation.
1-2 - the roller applies a thin layer of starch and cellulose powder to the work surface;
3 - inkjet printhead prints with drops of binding liquid on the powder layer,
locally reinforcing part of the solid section;
4 - process 1-3 is repeated for each layer until the model is ready, the remaining powder is
removed
UV irradiation through
photomask (Solid Ground Curing, SGC)
Manufacturer: Cubital Inc
English Russian Rules
🎓 Additive manufacturing technologies — presentation on Slide-Share.ru
one
First presentation slide: Additive Manufacturing
Slide image
2
Slide 2: Charles Hull
In 1986, he received a patent for stereolithography and founded 3D Systems. Hull's device "grew" a computer-simulated 3D object from a liquid photopolymerizable composition (PPC), layer by layer, onto a moving platform immersed in a PPC bath. The thickness of each individual layer was approximately 0.1–0.2 mm. Charles Hull is also the inventor of the STL format, which is used by all leading commercial CAD packages when exporting models for rapid prototyping.
Slide image
3
Slide 3: 3D printer
The term “3D printer” itself appeared only in 1993 thanks to two professors from the Massachusetts Institute of Technology (MIT), Michael Cima (Michael Kim) and Emanuel Sachs (Emanuel Sachs). By the way, this is the same Michael Kim who in 2013 made a real revolution in medicine by creating a remotely controlled implantable microchip for dosed and targeted administration of drugs.
Slide image
four
Slide 4: Additive manufacturing processes are growing products on a 3D printer from a CAD model (a software package designed to create drawings, design and / or technological documentation and / or 3D models).
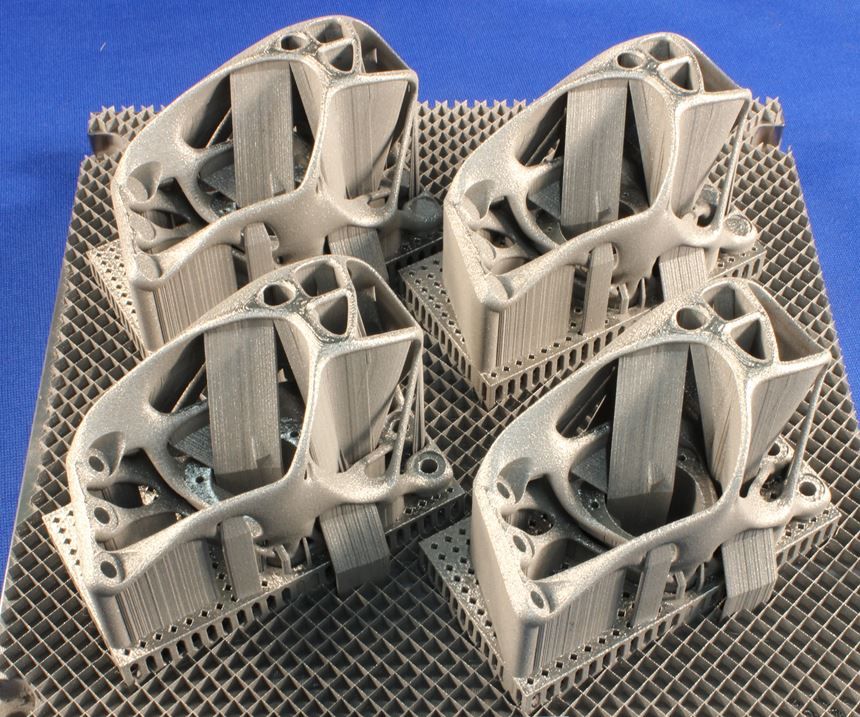
Slide image
5
Slide 5: Differences in traditional and additive manufacturing
Slide image
6
Slide 6: Advantages of additive technologies
Improved properties of finished products. Due to the layered construction, products have a unique set of properties. For example, parts created on a metal 3D printer in terms of their mechanical behavior, density, residual stress and other properties are superior to analogues obtained by casting or machining. Great savings in raw materials. Additive technologies use almost the amount of material that is needed to produce your product. Whereas with traditional manufacturing methods, the loss of raw materials can be up to 80-85%. Possibility of manufacturing products with complex geometry. Equipment for additive technologies makes it possible to produce items that cannot be obtained in any other way. For example, a part within a part. Or very complex cooling systems based on mesh structures (this cannot be obtained either by casting or stamping). Mobility of production and acceleration of data exchange. No more drawings, measurements and bulky samples. At the heart of additive technologies is a computer model of a future product, which can be transferred in a matter of minutes to the other side of the world - and production can immediately begin.
Slide image
7
Slide 7: General scheme of additive manufacturing
Slide image
eight
Slide 8: Classification of additive technologies according to the state of aggregation of the material used in the formation of the part
Slide image
9
Slide 9: Classification of additive technologies by type of material used
Today, the following main additive manufacturing technologies can be distinguished: FDM ( Fused deposition modeling ) - layer-by-layer construction of a product from a molten plastic thread. SLM (Selective laser melting) - selective laser melting of metal powders. SLS (Selective laser sintering) - selective laser sintering of polymer powders. SLA (short for Stereolithography) is laser stereolithography, the curing of a liquid photopolymer material under the action of a laser.
Slide image
ten
Slide 10
FDM ( Fused deposition modeling ) - layer-by-layer construction of a product from a molten plastic thread. This is the most common 3D printing method. FDM printers work with various types of plastics, the most popular and affordable of which is ABS
Slide image
eleven
Slide 11
SLM (Selective laser melting) is an innovative technology for the production of complex products by laser melting of metal powder using mathematical CAD models (3D metal printing).
Slide image
12
Slide 12
SLS (Selective laser sintering) - consists in layer-by-layer sintering of powdered material particles to form a physical object according to a given CAD model.
Slide image
13
Slide 13
SLA (short for Stereolithography) - laser stereolithography, curing liquid photopolymer material under the action of a laser.
Slide image
fourteen
Slide 14: Rapid prototyping technologies should be placed in a separate category. These are 3D printing methods designed to obtain samples for visual evaluation, testing or master models for creating molds
MJM (Multi-jet Modeling) - multi-jet modeling using a photopolymer or wax material. This technology makes it possible to produce burnt or smelted master models for casting, as well as prototypes of various products.