3D scanner accuracy
How Accurate Are 3D Scanners? Central Scanning
It is understandable, when choosing one, that you’d want to know how accurate are 3d scanners. But the concept of accuracy in 3D scanning is not a straightforward one.
This is because accuracy may not be what you think it is in a 3D scanner.
Is There A Standard For Accuracy In 3D Scanners?
Normally, to understand the accuracy of something, you’d need a common standard to work off.
In 3D scanning, however, this standard does not exist.
The accuracy spec for a tripod-mounted 3D scanner could be 2cm. Therefore, the scanner will return measurements within 2cm of the actual dimensions it is recording.
But if you compare this figure with another type of scanner, say a handheld model, it does not take into account other critical factors which will determine the accuracy of your scan.
When replicating an object, you may need to scan it several times to capture every angle. Once you’ve done this, you can merge all these registered parts into one.
What happens if you use this same process to arrive upon the accuracy specification of a scanner?
Is this methodology the same for different models of 3D scanner, and if so, where are they measuring the zero point of the scanner? And what characteristics of the object they are scanning might influence the readings?
Why Is Reflectance Important?
Even with 3D scanning technology that has highly accuracy specifications, you can arrive at very different results depending on whether a surface is reflective or not.
Dark, shiny and transparent surfaces are difficult to scan. Optical light-based 3D scanners use light as a source of projection. They capture images of patterns as they hit the surface of an object and deform. These images calculate the distances between the scanner and the object and are the basis for the point clouds that enable production of a 3D digital replica.
Actions can be taken to improve the scanning surface, such as using sprays. However, these are usually temporary and only improve the surface so much.
But with certain reflective surfaces, the light patterns become distorted, causing interference.
On these shiny surfaces, light scatters and bounces in directions that are hard to control.
What Is Accuracy In The Field?
Even if you took issues like reflectance into account and were able to standardise accuracy specs across 3D scanning devices, there is still the issue of accuracy in the field.
There are different ways to approach 3D scanning. For example, do you measure off the point cloud points themselves? Or first model a plane over them and measure from that?
Different scanning methods will derive a measurement from a scan, but will give different results.
Therefore, accuracy becomes something that is not a defined figure, but something subject to methodology.
Other elements can affect the accuracy of scanning in the field, such as the complexity of the environment in which you are scanning.
How tightly registered are the multiple scans you are taking when you’re determining accuracy?
What if there is an error midway in the process, which skews the results?
Should Accuracy Be About Problem-Solving First?
The simplest way to define how accurate 3d scanners are, is whether it enables you to capture a scan that will solve your problems or answer your questions.
In other words, the accuracy of your scanner should align with the environment you’re using it in, the object you’re scanning, and the end-purpose of doing it in the first place.
Therefore, if you choose your 3D scanner purely on the basis of specifications for accuracy, you could be missing out on the right scanner for your intended purpose.
This is a more flexible approach, because it focuses on the functionality of the 3D scanner, and making sure this matches what you want to achieve with it.
Accuracy, therefore, does not need to be a fixed standard. But, rather good enough to achieve the results you are looking for.
A less expensive handheld model, for instance, may be the right choice for giving you the data you need for your purposes. What it loses in accuracy, it gains in flexibility and adaptability to the environment you are using it in.
If your tripod scanner boasts millimetre-accuracy, this won’t necessarily be an advantage if it will mean that it takes you weeks to capture your entire project. Whereas a handheld model will do the job much faster.
When selecting a scanner, always weigh up its accuracy against your specific needs. In addition, how practical a piece of kit is, that you need it to be in the field.
For more information on how accurate are 3d scanners, please contact us, to discuss your 3D scanning requirements in detail.
What you need to know
Introduction
Generally, accuracy means how close a measurement is to its true value. In 3D scanning, accuracy generally refers to single scan accuracy, but then there’s also volumetric accuracy.
When it comes to resolution, whose general definition is how sharply an image can be displayed, there can also be two values in 3D scanning. 3D scanner OEMs generally refer to mesh resolution– i.e., the distance between points within a point cloud (3D mesh)– when specifying resolution. But, some also specify measurement resolution.
All of these terms can be a bit confusing, and 3D scanning is already a complex enough technology. Let’s go over the basics!
3D scanning accuracy
What is accuracy?
The general definition of accuracy is how close the measurement is to its true or tolerable value. It is often confused with precision, which is how close different measurements (of the same target) are to each other. The simple graphic below illustrates the difference between accuracy and precision:
Simple representation of precision and accuracy. Source: AniwaaIn 3D scanning, accuracy is how close the scanner’s measurements are to the object’s true size. If you measure a cube with an industrial caliper and obtain a width of 200mm, but your scanner captures the cube as 205mm-wide, then it is quite off.
Two types of accuracy specifications exist in 3D capture: single scan accuracy and volumetric accuracy.
Single scan accuracy vs volumetric accuracy
In spec sheets, accuracy often means single scan accuracy. It is the accuracy of one image capture.
Example: 0.05mm accuracy.
Most 3D scanner OEMs also specify volumetric accuracy. It is the accuracy of several captures, and this global accuracy diminishes the bigger the scanned part is.
Example: 0.05mm + 0.15mm/m.
Following our example, if your part measures 2 meters long, the accuracy of your scanner will be 0.05 + (0.15*2) = 0.035mm. That’s quite a difference from the original, single scan accuracy! Volumetric accuracy is thus more important to consider than single scan accuracy, especially if you are going to 3D scan large objects (e.g., cars).
That said, some 3D scanners with integrated photogrammetry modules can build up a sort of 3D skeleton of the object (with adhesive markers) before filling it in with the rest. Markers are precise reference points for 3D scanners, like a connect-the-dots drawing. By using a photogrammetry-sourced “skeleton”, your data is bound to be more accurate.
Note: Photogrammetry is a 3D scanning technology that involves taking multiple photographs of an object from different angles in order to calculate its shape and size.
A part fitted with markers. Source: Aniwaa (SIMSCAN review)How accurate are these specifications?
Manufacturers indicate specifications which are maximums that were obtained in ideal conditions. If the manufacturer recorded an accuracy of 0.05mm in its lab, it doesn’t mean you will be able to achieve the same accuracy in-house.
A scanner’s accuracy can depend on a number of factors:
- Temperature (a 3D scanner will perform differently at 40°C than it will at 20°C)
- Calibration (how well did you calibrate your 3D scanner? Do you calibrate it regularly?)
- The person performing the scan (though there is less room for error with today’s and tomorrow’s sensors, and more intuitive software)
On another, important note, 3D scanner manufacturers don’t all follow the same standards to measure their scanners’ accuracy. If high accuracy is of utmost importance for your applications, look for brands that have VDI/VDE and/or ISO certifications, for example.
3D scanner resolution
What is resolution?
Resolution can mean many different things depending on what you are talking about (photography, filmography, printing, …), but it has the same fundamental meaning. It is a technical computer science term that characterizes “how well the reality was captured”.
With screens, for example, the resolution is linked to the number of pixels available to recreate an image. The more pixels, the better the resolution and the image quality (the cleaner and crisper your image will seem). We can see this clearly with the circle example below:
Pixel density affects the visual quality of an image. Source: Research Gate (Ivan Terol-Villalobos)In 3D scanning, there is one main type of resolution: the resolution of your 3D mesh, a. k.a. “mesh resolution”. But some manufacturers also specify “measurement resolution”.
Mesh resolution
Most often, “resolution” or “3D resolution” in spec sheets refers to the resolution of the resulting 3D mesh. It is mainly measured in point-to-point distance– ie., the distance between two 3D points in a dot cloud– as it is the easiest to comprehend. The closer your mesh’s points are together, the better it will look. Point-to-point distance is sometimes called “spacial distance between points” or “point distance”.
Resolution can also be measured in PPS (points per scan). The more points your mesh includes, the smoother, more detailed it will look. This can be compared to 2D print quality, where the more PPI (points per inch) your file contains, the sharper your print.
Keep in mind that a higher mesh resolution means longer loading times and heavier files. If you don’t really need an extremely high definition, then there’s no use in putting strain on your RAM/GPU and weighing down your hard drive.
Note: In any case, you will likely need to invest in a high-end, gaming-quality PC in order to run 3D scanning software and load the enormous amount of captured data. Some of the computers we’ve worked with for high-end scanners cost over $5,000.
Measurement resolution
The measurement resolution translates to how many points the sensor is capable of capturing in a given area. The more points per unit of surface, the better.
But, in the end, what really matters is the mesh resolution that can be obtained and used in the software after computation. In some cases, the software calculates an average of several measurement points to generate a single mesh point (a vertex).
Note that the requirements for mesh resolution are relative and not absolute: on a sharp edge, you need a good resolution; on a flat surface, only a few points are necessary. Some 3D scanning software suites optimize meshes accordingly to avoid stocking heavy, unusable data (and choking your PC) for nothing.
Note: As a metaphor, let’s take the human body and its sensory receptors. We have thousands of receptors at the tip of our fingers, which we use to touch and interact with almost everything. Our backs, however, have very few sensory receptors, as we don’t really use our backs to feel things.
This mesh is optimized: corners and edges feature a high point density, while points in flat areas are more spaced out. Source: Aniwaa (GOM ATOS Q review)Conclusion
Many different terms are thrown around manufacturer websites and spec sheets. What really matters is volumetric accuracy and mesh resolution, and how well they answer your specific needs.
Furthermore, while accuracy and resolution specs are useful to easily and quickly compare one 3D scanner to another, they shouldn’t be deciding factors on their own. You should also consider a brand’s certifications, history, software, customer service, and more.
Feel free to reach out if you’re having trouble deciding on a 3D scanner or unsure of what you’ll actually need for your use case (and budget!).
3D scanner: the illusion of accuracy
When ordering a 3D scan, a customer often asks: “ What is the accuracy of your scanner? ". It seems that the more accurate the scanner, the better. However, it is important to understand why high accuracy is required and how it can be achieved.
What is the accuracy of a 3D scanner
The accuracy of a 3D scanner is a rather vague concept. At the household level, this is usually understood as the degree of compliance of the resulting 3D model with the actual geometric dimensions of the scanned sample.
In physical terms, the accuracy can be expressed as the maximum allowable deviation from the actual size. That is, if the accuracy of the scanner is declared as 7 microns, this means that each size of the resulting 3D model will differ from the real one by no more than 7 microns.
However, it is important to understand that the accuracy claimed by the manufacturer is the maximum deviation under IDEAL scanning conditions, which in reality is NEVER.
This value is obtained by performing a series of tests on an ideal sample under LABORATORY conditions, comparing the dimensions with the scanned sample, and averaging the resulting deviations.
In practice, we have a lot of deviations from the ideal, including both the objective conditions of scanning and the state of technology, and the subjective skill of the scanner and scan processor.
Fig.1. Comparison of the raw scanned cover model and the point cloud obtained after processing: green - exact match, red - deviations.
Fig.2. Re-comparison of the scanned and processed model after additional transformations. The result is much better, basically the whole model in the green zone.
What affects the accuracy of the final 3d model:
1.
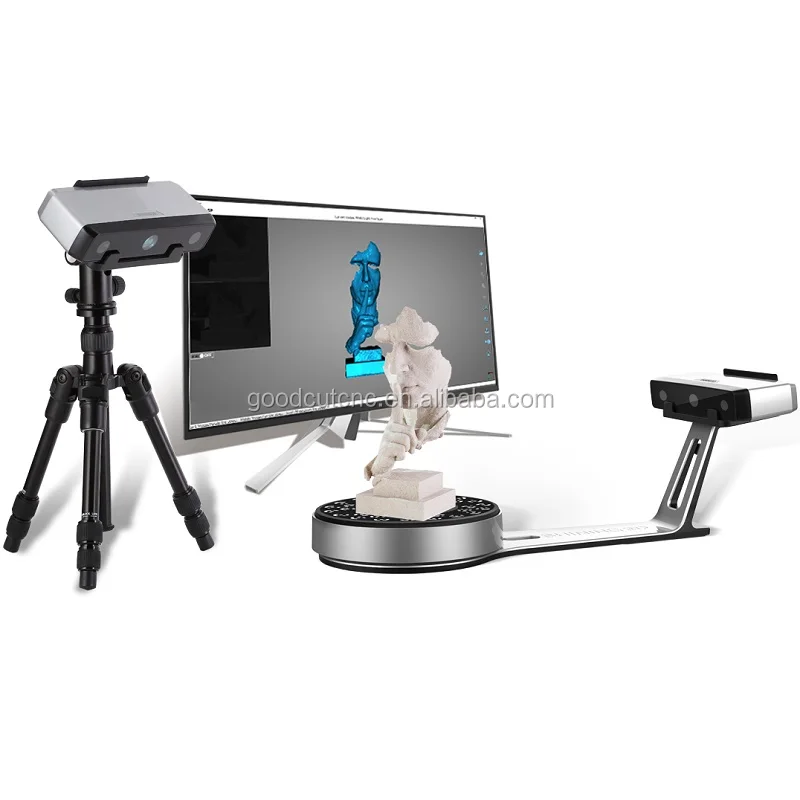
Due to the characteristics of scanners using structured illumination or a laser beam, the scanned object must have a number of characteristics to maintain maximum accuracy: it must be a clean, hard, white, matte object without flat sharp edges, holes, hard-to-reach places, wear, small size , so that the object is completely placed in the scanning area.
How deviation from ideal performance affects scanning, see here.
Any deviation from the ideal will degrade accuracy. For example, if the object is black, dark, transparent or shiny, it must be covered with a matting spray, which, firstly, has its thickness of about 50-100 microns, and secondly, forms microgranules on the surface, the height of which will be averaged during processing, which means , the accuracy will decrease further.
2. Technical condition of the scanner
Ideally, the scanner should be calibrated with an accuracy not exceeding the permissible one, warmed up to operating temperature, the requirements for the distance between the cameras, as well as from the cameras to the object, are met.
3. Scan conditions
A change in temperature causes the material to expand or contract according to its coefficient of linear or volume expansion. For example, a steel railway rail that is 8 meters long at 0°C will expand by almost 4 mm (or 4,000 microns!) at 40°C.
The difference between the temperature at which scanning is carried out and laboratory conditions will inevitably lead to an increase in the error.
Additionally create error:
- excess daylight from a window, uneven lighting;
- vibrations of the floor, if someone walks, or the surface on which the object is installed;
- as well as many other less significant factors.
4. Qualifications and experience of the
scanner How to apply the thinnest possible layer of Matting Spray where no spray is needed at all, how to scan in such a way that it is easier to process scans, how to ensure perfect scan stitching, how to create conditions for scanning that are close to ideal - all these issues are under the responsibility of the scanner and are highly dependent from his experience. And the quality of the scanned model will depend on this.
In addition, in our practice, the scanner also performs sketches of the critical parts of the product, for the final control of the accuracy of the resulting model.
5. Qualifications and experience of the model
handlerAfter scanning and stitching, the model is sent for processing - in order to obtain a high-quality stl-file, it is necessary to eliminate debris, remnants of marks in it, properly sew up holes and make holes. At this stage, a large number of errors can be made, which will then result in deviations of the resulting model from the original sample.
If further work is carried out - obtaining a solid CAD model, the number of operations on the model increases, proportionally increasing the probability of error. It could also be a simple human error. There is a hole on the model, there is a hole on the scan, but in the final CAD model, the processor did not notice and sewed it up.
What is affected by the error in scanning
It is important to understand when accuracy matters and when it does not make any sense to pursue it.
Accuracy is important when scanning mounting dimensions and critical surfaces, such as gear teeth or products, where the error causes a critical change in technological characteristics. But due to the problems listed above, 100% accuracy cannot be achieved even with the most advanced equipment.
Therefore, when scanning critical surfaces, we always make sketches with dimensions and eliminate all scanning errors by finalizing the 3D model. Or we check the entire assembly in the 3D model together with the counterpart. In this case, it is not so important with what accuracy the scanner scanned - 5 or 50 microns, the accuracy will be 100% guaranteed.
In the case of gears, where the shape of the teeth is a complex curve, 100% accuracy can only be achieved by calculating the parameters of the gear together with its counterpart.
In other less important surfaces, in art products, in design elements, it is absolutely not necessary to observe micron accuracy. With a good scanner resolution, after scanning and, for example, 3D printing of a product, the original and the copy will be visually indistinguishable.
CV :
Don't chase after impressive scanner accuracy parameters, because for the vast majority of tasks, accuracy is an abstract concept that does not affect the result. You need to pay attention to factors such as:
- the resolution of the cameras, it depends on how small objects the scanner can "see";
- quality of processing and refinement of scanned 3D models to ensure the accuracy of critical surfaces. And this parameter directly depends on the experience and qualifications of the performer.
In any case, if accuracy is important during scanning, it is highly recommended to make a prototype and check its geometric characteristics before manufacturing a product from expensive material or starting a series.
What determines the accuracy of 3D scanning
Speaking about the accuracy of a 3D scanner, they usually mean the level of compliance of the obtained three-dimensional model with the real characteristics of the sample.
This parameter defines the error of the 3D scanner or the interval within which the comparison results can vary.
The accuracy of a 3D scanner depends not only on the hardware, that is, on the device’s own characteristics, but also on a number of other factors, in particular, the accuracy is affected by: increases the error
The same scanner can give different accuracy values depending on the subject being scanned and the skill of the performer. That is why many scanner manufacturers avoid specifying accuracy in device specifications, replacing it with other, more objective parameters (see Table 1), such as resolution. Resolution and accuracy are different concepts, although higher resolution does increase accuracy. The manufacturer's accuracy specification usually corresponds to an ideal object under ideal scanning conditions (see Table 2).
Standard value for 3D scanner: 1 mm.

Accuracy tables are usually written for ideal objects under ideal conditions - a hard smooth product scanned at a constant temperature, etc. Any deviation from the reference conditions affects the resulting accuracy value. The table shows the main parameters that affect the accuracy of 3D scanning.
Table 2. Causes of accuracy loss in 3D scanning
Ideal Conditions | Conditions that cause difficulties | result of work in imperfect conditions | |
Tworted object | 900Parts of the object scanned from different angles are distorted. There are problems when combining parts into a single product|||
Statical Object | of the object movements relative to the scanner during the scan process | Any movement leads to a distortion of the result and deterioration of detail | |
Light object | Dark Object | Most of the Scanners does not scannes not scanning the scanners do not scanner scanners.![]() | |
Matte Object | shiny or translucent object | in 3D models in these places will be holes, their preliminary matting | |
Smooth object | The presence of acute ribs | Sharp edges are slightly softened, preferably soften observe the rules for the relative positioning of the scanner and sharp edges | |
Part without holes | Product with edges of sheet material | The edge of a thin sheet in 3D data always breaks, not reaching the real boundary of the object | |
Good geometric features of the object | | degeneracy along one or more axes Separate fragments cannot be qualitatively combined, accuracy becomes uncontrollable without the use of markers | |
0131 | Large or long object, need to scan in fragments | Errors appear when combining fragments | |
Object is scanned perpendicular to the surface | Scanned “at an angle” | Decreased accuracy.![]() | |
Scanner warmed up to operating temperature and then calibrated | 3D scanner not warmed up to acceptable operating temperature | Measurements knowingly contain errors | |
The calibration field was measured at a current temperature of | Scanning is carried out in conditions of an unnecessary temperature | The scale of the result will differ from the real object | |
The lighting does not interfere with the process. | Bright directional ambient light | increased noise level in the data or the inability to operate | |
The cameras are located at the recommended distance of | The chambers are shifted for scanning of the hollows and undercuts | increased noise in data | |
The temperature in the room is stable stabil | Indoor temperature changes according to external weather conditions | Change of product parameters depending on external temperature |
Effect of temperature on accuracy
Most substances expand when heated. The effect of thermal expansion reduces the accuracy of 3D scanning. In an unprepared room, the temperature can fluctuate within 10 or more degrees. At the same time, the sizes of objects, depending on the material of their execution, will change up or down. Thus, for some objects there is no significant value of more than 0.1-0.2 mm/meter accuracy.
Accuracy when combining scans of an object
When scanning an object from different angles, it becomes difficult to process further results, since errors arise when combining different fragments. Several matching technologies are used:
1. Matching by surface geometric features. The accuracy of this technology is the highest, but only if the object has a sufficient number of characteristic features. If the entire object is placed in the scan area, the drop in accuracy during alignment is insignificant. If the geometric features are not enough (scanning large smooth objects), other alignment technologies are used.
2. Alignment by markers. Before the scanning process, the model is prepared for work - in an arbitrary chaotic manner, markers of a contrasting (in relation to the object) color are glued evenly over the surface. The scanner automatically reads the coordinates with a marker and combines the fragments.
3. Marker alignment using a photogrammetric system. For large objects, a technology is used when marker coordinates are estimated in advance using a photogrammetric system, which ensures high accuracy.
Application examples and accuracy requirements
Perfect accuracy requires expensive equipment. However, not all products require high accuracy values. Therefore, it is necessary to understand whether it is worth investing in such parameters.
For example, the high precision requirement is used in applications such as controlling the manufacture of turbine blades or artificial heart valves.
In general, when scanning most other products, an accuracy of 0. 1% of the measured length is sufficient. When scanning a car bumper, that is, a part connected to other parts, 1 mm or less is considered the minimum sufficient accuracy. In most design and creative tasks, for example, when scanning plaster molds, sculptures and jewelry, there are elementary requirements for accuracy, first of all, it is necessary to reduce noise, improve detail, and work out the surface of the object as carefully as possible.
Table 3. Examples of tasks and requirements for accuracy
Example of the task | GIPS INDUMENT, COMPARIS ABOUT THE PUPA , a statue. Reduced copies of the sculptures are supposed to be made using CNC machines or printed on a 3D printer. | In this case, there is no need for high precision. It is of great importance to obtain a visually identical result, i.e. high detail, minimum noise level is required.![]() |
Scanning a bicycle fork, pedal, frame. Scan results will be the basis for modeling another fork, pedal, frame. | The surfaces of the old fork and pedal are not of interest. Attachment points, landings and connection lines are of particular importance. An accuracy of about 0.5 mm is required at the specified locations. |
Scanning a glass bottle. Based on the result, a new form will be created. | The requirements for accuracy are minimal. The neck shape and thread elements are taken from the CAD model. The shape of the vessel itself will be recreated. T.K. the shape is smooth, the values of the noise level and detail are not significant. |
Scanning a family ring, earrings, pendant. Precision values are not important. |
Accuracy in the development of a solid 3D model
From the scanner we get a raw file (point cloud or polygonal model), which we then bring to a solid 3D model in a CAD program, for example, SoliDWorks.
When modeling objects based on the received data, the dimensions are usually rounded to integer values. For example, when scanning, we received an aluminum case with dimensions of 327.18 x 240.05 x 194.76 mm - in this case, the designer will almost always adjust the dimensions in the work to 327.00 x 240.00 x 195.00 mm.
In addition, the shape of new CAD objects, built according to STL data from the scanner, may differ significantly from the actual surface, since the functions of mathematical approximation, smoothing and surface simplification are used when it is built using CAD packages.
P.S.
For applications where accuracy is critical, additional measuring systems are often used in addition to the scanner. It must be understood that although a 3D scanner has outstanding technical characteristics, it is still not a measuring device. In this regard, before launching a part into mass production, it is necessary to make a trial series in order to check the result in work and correct possible shortcomings.