3D printing uv resistant
Best 3D Printing Filament for Outdoors? UV Resistance Guide
With 3D printing increasingly used for end-use applications, there is growing demand for 3D printing materials that can withstand external environments, such as weathering and direct sunlight. As a provider of 3D printing filament, this article seeks to explore what makes a filament suitable for outdoors use, as well as reviews the most popular 3D printing materials with respect to UV stability.
What makes a 3D printing filament suitable for outdoors use?
When it comes to the suitability of a 3D printing material for outdoors use, the key aspect is the impact of UV light (i.e. sunlight) – the electromagnetic radiation the vast majority of us learn about in school science lessons!
UV light is potentially detrimental to 3D prints left or exposed to the outdoors because UV light tends to bleach the colour over time and can even cause the print to become brittle – impacting performance. The higher the amount of sunlight – and associated temperature increase – the higher the risk and rate of degradation of the 3D printing.
How UV resistant is PLA?
PLA is the most common filament for 3D printing – used by more than 95% of 3D printer users. It is used widely by both hobbyists and industry users to 3D print prototypes; certain PLA grades such as Tough PLA are also now unlocking opportunities to produce end-use parts made from PLA.
PLA is considerably UV resistant – however it is important to note that, as a bioplastic, PLA has a much lower heat resistance – at around 57 °C Tg. Whilst temperatures on Earth do not (yet) reach this, the impact of increased air temperature and humidity risks degrading PLA. In short, whilst PLA may be suitable for light applications outdoors it should not be considered for structurally-critical components.
How UV resistant is PETg?
PETg 3D Printer Filament is increasingly popular within 3D printing – due to its superior strength, durability and chemical resistance, versus PLA. It is also odour-neutral when printing which gives it an advantage over the traditionally-used ABS when it comes to functional prototypes, manufacturing aids and even end-use applications. PETg, as a polymer, is also 100% recyclable.
PETg filament exhibits high UV resistance – making it suited to applications for the outdoors and / or require exposure to direct sunlight. As explored in our Best Heat Resistant Filament Materials for 3D Printing article, PETg also offers enhanced heat resistance versus PLA – exhibiting HDT of 70ºC and Tg of 77ºC.
How UV resistant is ABS?
During the early years of desktop 3D printing, ABS emerged as the most popular choice of material – mostly, due to its availability and also its ubiquitous use in Injection Moulding which provided a direct comparison of 3D printing versus traditional manufacturing. Whilst usage of ABS has decreased because of the increased demand for PLA – and increasingly, PETg – ABS filament is still widely used in 3D printing.
In raw form, ABS does not resist ultraviolet degradation, however with regard to 3D printing, additives in the formula positively impacts this, thus giving ABS good UV resistance.
How UV resistant is ASA?
ASA filament usage within 3D printing is growing significantly, especially in industry. It has a similar chemical makeup to ABS plastic but offers three distinct advantages: improved mechanical properties, superior aesthetics and UV resistance.
ASA filament is the most UV resistant material in 3D printing – ten times more weather resistant and UV-resistant than ABS.
What is the Best 3D Printing Filament for Outdoors use?
The conventional 3D printing materials – PLA, PETg, ABS – all exhibit high UV resistance. Because of its very high UV resistance, ASA is the best filament for 3D printing applications outdoors, and / or those in direct sunlight.
UV-resistant materials: A beginner's guide
Adam Kohut13 August 2020
Applications
UV resistance refers to a substance’s ability to resist ultraviolet (UV) light, including sunlight. UV light can cause discoloration or degradation in a final part.
Why are UV-resistant materials important?
In 3D printing, UV-resistant materials are necessary should a part or model be exposed to sunlight – or other UV light – for prolonged periods of time. UV-resistant plastics, in particular, will not typically change in appearance be in through yellowing, leaching dye color, bleaching, or the formation of stress cracks. With UV-resistant materials, mechanical properties will also remain intact; they will maintain strength, elasticity, and hardness, and will not become brittle.
Common uses of UV-resistant materials
Applications intended for outdoor use are one common use of UV-resistant materials. Weatherproof applications, in particular, are great candidates for UV-resistant materials.
What else should you know?
UV light affects polymers through a process called “photooxidative degradation,” which results in the breaking of polymer chains – and eventually resulting in a material’s complete degradation.
"UV-stabilized" materials have had a stabilizer added to the resin that resists UV rays and prevents UV degradation
When creating a part, you should be sure to know the difference between “continuous” and “intermittent” exposure to UV rays, with continuous exposure being the more serious of the two
FFF 3D printing materials, such as ASA – a variation of ABS developed for UV resistance – and PVDF have good UV-resistant properties. The UV resistance of these FFF materials can also be increased using additives. This gives FFF 3D printing materials an advantage over SLA materials, as the process is based on UV light, and are not usually UV-resistant unless they undergo post-processing
Our material partners
Here are some details about Ultimaker’s UV-resistant material partners. You can find out more on the Ultimaker Marketplace.
Arkema
FluorX™ is a tough, semi-crystalline fluoropolymer made from Arkema’s Kynar® PVDF. It is formulated for printability, and is a great option for parts subjected to demanding conditions, such as solvents, acids, fire, and UV radiation.
"Kynar® PVDF has a 50 year legacy in outdoor applications due to its tremendous resistance to sunlight and UV rays,” Steven Serpe, Market Manager, Specialty Powders and 3D Printing at Arkema, said. “Some of the world’s most famous buildings have been coated in Kynar® PVDF based paint to last decades without degrading or discoloring. This same performance can now be achieved in 3D printed objects."
A part printed in Arkema FluorX™ PVDF
BASF
Ultrafuse ASA is a high-performance thermoplastic with similar mechanical properties as ABS, but offering additional benefits, making it a good choice for many types of applications.
DSM
Arnitel® ID 2045 is a highly flexible TPC (thermoplastic copolyester) that can be used in a broad range of applications. It has better UV and chemical resistance compared to others of its type, such as TPU (thermoplastic urethane).
MCPP Netherlands BV
DURABIO™ is a bio-based, BPA-free engineering 3D printing material developed by Mitsubishi Chemical. With high transparency similar to PMMA but better impact behavior and improved heat resistance, DURABIO™ closes the gap between PC and PMMA.
With excellent weathering, UV stability, impact performance, and stiffness, 3Diakon™ is an ideal material of choice for outdoor applications and uses and for casting processes where a clean burn to ensure low ash residue is critical to performance.
"We believe that DURABIO™ and 3Diakon™ have outstanding print results when using our print suggestions,” Sales & Marketing Manager at MCPP Netherlands BV, said. “The Ultimaker Marketplace helps the end-user with finding the optimized print properties.”
Solvay
Solef(R) PVDF AM Filament is not only UV resistant but also resistant to a broad range of harsh chemicals, intrinsically fire retardant, and temperature resistant up to 130°C. This unique combination of properties with the ease of printing the material enables the access to a broad range of applications.
"Solef(R) PVDF AM Filament is not only UV-resistant, but also resistant to a broad range of harsh chemicals, intrinsically fire retardant, and temperature-resistant up to 130°C,” Sophia Song, Business Incubation - Additive Manufacturing at Solvay, said. “This unique combination of properties with the ease of printing the material enables the access to a broad range of applications.”
A part printed in Solvay Solef(R) PVDF AM Filament
Interested in learning more about Ultimaker’s UV-resistant material partners? Visit the UV-resistant materials page on the Ultimaker Marketplace.
You can also explore Ultimaker’s range of 3D printers that are compatible with UV-resistant materials.
Discover Ultimaker 3D printers
comparative testing of 3D-printed products made of ABS and ASA plastics / Sudo Null IT News
Two types of similar plastics took part in the test - white ABS and white ASA.
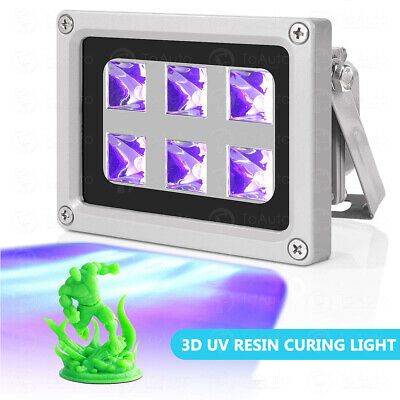
If ABS plastic is known to everyone, then ASA plastic appeared on sale not so long ago, and is positioned as protected from ultraviolet radiation.
We were interested to know how much more UV resistant ASA is than ABS.
Introduction. Goals, objectives and means of testing:
degradation of ABS and ASA polymers under the influence of UV radiation.
Testing was carried out with a 30 W T8 HNS germicidal lamp from OSRAM (Ledvance). This lamp emits ultraviolet of the hardest "C" range.
In nature, this radiation is delayed by the atmosphere.
This lamp was chosen for the accelerated test.
Many polymers used in consumer products degrade when exposed to UV light. The problem manifests itself in the disappearance of color, tarnishing of the surface, cracking, and sometimes the complete destruction of the product itself. The rate of destruction increases with increasing time of exposure and intensity of sunlight. The described effect is known as UV aging and is one of the varieties of polymer aging.
Sensitive polymers include thermoplastics such as polypropylene, polyethylene, polymethyl methacrylate (organic glass) as well as special fibers such as aramid fiber. UV absorption leads to the destruction of the polymer chain and loss of strength at a number of points in the structure.
The electromagnetic spectrum of UV radiation can be divided into subgroups in different ways. The ISO standard for the definition of solar radiation (ISO-DIS-21348) gives the following definitions:
The near UV range is often referred to as "black light" because it is not recognizable by the human eye, but when reflected from some materials, the spectrum goes into the visible radiation region due to the phenomenon of photoluminescence. But at relatively high luminances, such as from diodes, the eye notices violet light if the radiation captures the visible light boundary of 400 nm.
The term "vacuum" (VUV) is often used for the far and extreme range, due to the fact that waves in this range are strongly absorbed by the Earth's atmosphere.
Experiment preparation.
For the test, tubes with a diameter of 30 and a length of 50 mm were printed from both plastics. 7 tubes of each type of plastic. We used white ASA and ABS plastic from the same manufacturer (BestFilament). Printed in one run with a 0.5 mm nozzle with a layer thickness of 0.2 mm. The wall thickness of the model is 0.5 mm. All tubes were numbered from I to VII. The first six test samples were put on the lamp, and we left the samples with the number VII as a reference for comparative analysis. The samples were continuously irradiated with UV "C" range for varying amounts of time, that is, we removed one pair of tubes approximately every 20 days. All taken samples were stored in a plastic ZIP bag in a dark place until the end of the test.
Photos of all samples in the bag and on the HNS lamp.
Irradiation of polymers.
So we started testing. The photo shows that UV is visible through ABS.
This means that the degradation of this plastic must occur throughout the volume.
ASA, on the contrary, staunchly restrained hard radiation.
We removed the first pair after 18 days (432 hours) of UV exposure. It immediately became noticeable that the label on the ABS plastic burned out, but there were no changes on the ASA outwardly. The inner surface of the tubes turned yellow and became matte. Visually ABS yellowed more, even on the outside. Samples smell of pollen and burnt sugar.
We removed the second pair after 36 days (864 hours) of UV exposure. Compared to the first pair, no significant changes were noticed.
The third pair was removed after 57 days (1368 hours) of UV exposure. ABS has become a little more transparent. ASA is unchanged from the first withdrawal.
The fourth pair was removed after 75 days (1800 hours) of UV exposure. ABS became even more yellow. It feels like it's blooming. Also, changes began to occur with the paper that covered the edges of the lamp. The paper began to crackle.
The fifth pair was removed after 97 days (2328 hours) of UV exposure. Strong differences from the previous sample are not visible.
We decided to keep the sixth pair longer. As a result, she hung for 122 days (almost 3000 hours) under continuous hard UV ... For comparison, we took several photos by hanging a standard with VI samples. The glow of the standards is more transparent.
It is a pity that the camera does not convey these shades. During this time, holes from ultraviolet radiation appeared in paper packaging.
Testing of prepared samples.
It's time for mechanical tests.
Yes, everyone crushed and tore on special equipment. For this, two stands were used.
The first bench SHIMPO FGV-10XY dynamometer determines the maximum pressure force acting on the object. The second stand Regmed PU-2 determined the maximum tensile strength, the amount of deformation before rupture.
First, we crushed the tubes by placing them in a similarly shaped cradle. After that, strips 5 mm wide were made from the samples, and they were torn on the second stand. All results were captured on video and summarized in a table.
Test video: part 1
Diagrams were built according to the received data.
Results of comparative testing of ABS and ASA polymers.
Testing has shown that ASA plastic tolerates long-term exposure to hard UV radiation quite well without serious loss of physical properties. For 122 days of continuous irradiation, there was a slight drop in the elasticity of the sample with an increase in the tensile strength characteristic.
As for the ABS plastic, it sharply reduced elasticity almost at the beginning of the test. Under the influence of hard UV radiation, the structure of the material degraded, and the plastic became brittle. It was not possible to test a sample that had sagged for 122 days in UV. It broke when trying to clamp the ring in the installation.
Results and conclusions of testing.
The use of precisely the hard version of the C-band radiation made it possible to speed up the process and obtain results more quickly.
It is worth making the assumption that under the influence of sunlight, the processes proceed in a similar way, only the degradation of plastic takes longer, since UV "C" of the range is absorbed by the atmosphere, and in everyday life it is found only in water disinfection installations or in medical institutions in antibacterial air treatment devices .
Obviously, both of these plastics can be used in everyday printing. But if you are thinking about printing parts for use under the influence of sunlight (signs, machine parts) it is better to use ASA.
Especially if you plan to launch your satellite, or give a friend a doctor a ceiling lamp for a quartz cabinet lamp.
Testing conducted by: Roman Silin, Smolensk
Printing ASA plastic in Moscow to order, inexpensively on time, with delivery
ASA is a weather-resistant high-impact 3D printing plastic. The material has high strength and resistance to external factors, has a wide range of operating temperatures for a long time (from -40°С to +80°С). It is also UV resistant and virtually unaffected by lubricants, dilute acids and diesel fuel.
not afraid of direct sunlight
waterproof and water repellent
does not change its properties in contact with fuels and lubricants
retains its shape and does not collapse under significant impact loads
does not turn yellow and does not become brittle
does not warp at elevated temperatures
is easy to stain
shape and color stability
Properties of ASA plastic products
The material has many advantages:
- Rigidity, strength.
- UV resistant, some solvents. The material is resistant to lubricating and mineral oils, acids.
- Temperature resistant, impact resistant.
- Antistatic. The material does not accumulate static charges, does not attract dust.
This ensures easy maintenance and practicality.
- Water-repellent, moisture-resistant performance.
Solubility in acetone allows chemical polishing
Quality printing and correct post-processing allows us to create the best products for your orders
Cases and products according to individual drawings
Printing of housings for various applications that are exposed to UV radiation.
external parts
Satellite dish housing parts. Landscape gardening equipment. Sprinklers for watering. Carts. Equipment for beaches, pools.
souvenirs and toys
Housing parts for household appliances. Cases of telephones, mobile phones. Housing parts for kitchen equipment (coffee makers, microwave ovens, cheese cutters, etc.). Cases of electric toothbrushes. Grilles for air conditioners. Case parts of fans.
outdoor furniture
Lighting technology. Plafonds of lamps. Sensors for outdoor use. Outdoor switches. Bathroom switches. Housing parts of electrical equipment for outdoor use.
landscape items
Road signs. Signal lights. Details of outdoor advertising. Chair details. Mailboxes. Boxes for fire extinguishers.
sports equipment
Golf accessories. Recreational equipment. Bathroom equipment. Toys. Models of cars and ships. Sporting goods. Surfboards.
Products retain their shape, do not collapse from impacts, do not turn yellow when exposed to ultraviolet radiation. But during printing, shrinkage, deformation and cracking of the surface may occur. Also, during production, hazardous fumes are formed, so you need to organize ventilation or use equipment with a closed chamber.
Also, the cost of products made of ASA plastic will be higher in comparison with products from its counterparts.
ASA is generally printed with a safe and practical material. Specialists follow all the recommendations of the manufacturers, performing facade signs, building components, parts of the automotive exterior, garden and other equipment.