Cdlm 3d printer
Products - ETEC
Skip to content
Team DM
Platforms
Metal and composites 3D printing 3D printing solutions for health care Industrial-grade polymer 3D printing™
Sand and tooling 3D printing solutions 3D printers for sheet metalMaterials
Breakthrough photopolymer development Advancing 3D printed upcycled woodApps & More
The hydraulic additive manufacturing experts Multi-material powder recoating technology Driving digital transformation in dentistry· Systems
Our Systems
- Printer technology
- Build envelope
- Models
- XY Resolution
- Z Resolution
- Printer technology
- Build envelope
- Models
- XY Resolution
- Z Resolution
- Printer technology
- Build envelope
- Models
- XY Resolution
- Z Resolution
- Printer technology
- Build envelope
- Models
- XY Resolution
- Z Resolution
- Printer technology
- Build envelope
- Models
- XY Resolution
- Z Resolution
· Key Features
Why ETEC?
High Accuracy + Feature Detail
High-resolution printing with Industrial DLP Chips
DLP chips come in a variety of configurations, from industrial chips designed for 3D printing to less expensive chips intended for video projectors found in many offices. While some DLP print technologies choose to use these inexpensive chips to reduce costs, ETEC only uses true industrial DLP chips, which allow for higher contrast ratios, resulting in finer part details.
High-resolution printing with CDLM Domeless Printing
https://etec.desktopmetal.com/wp-content/uploads/2022/01/MS_DM_EnvisionTec_E1_CDLM_320.mp4
To print continuously (without peeling) requires flowing oxygen through a permeable film just above the print bed to create a “dead zone”. Within this ‘dead zone’ the polymerization process is inhibited ensuring the layer being printed adheres to the layer above and not the printing bed film. This ‘dead zone’ is what enables continuous printing, where the build plate can continually move in the Z axis, leading to faster, more reliable prints.
On competitor “dead zone” printers, by comparison, air pressure from the flowing oxygen causes the film to dome up. Printing parts on that domed surface greatly impacts resolution along the Z axis, as well as the ability to print flat parts on the build plate.
ETEC’s CLDM technology uses over 200,000 pillars to hold the film perfectly flat, resulting in significantly better Z-axis resolution and allowing for the printing of flat parts straight to the bed with no supports.
Smooth Surface Finish
Smooth surface finish with Pixel Shifting
Projectors deliver light in square-shaped pixels, which creates volumetric pixels, or voxels, as resin cures.
Along curved edges, however, square pixels create a jagged edge – what the industry often refers to as “stair stepping.”
As the size of printed objects and build volumes increase, stair stepping becomes more pronounced.
ETEC printers use patented pixel-shifting technology to move pixels at the edge of parts half a pixel in both the X and Y directions, cutting stair-stepping by half and delivering significantly improved surface finish.
Smooth surface finish with Pixel Tuning
Anti-aliasing technologies are ubiquitous today — used virtually everywhere digital images appear, from cell phones to TV screens and more.
ETEC brings the same technology to the 3D realm by using anti-aliasing techniques at the edge of print layers to improve surface finish. Since voxels grow from the center of a part to the edges, applying less power to these outside pixels ensures they only grow to the desired edge of the part and not beyond. (Less power = slower polymerization growth)
Called pixel tuning, that process dramatically reduces pixelation on the edges of parts, resulting in a surface finish that requires little to no post-processing.
Smooth surface finish with CDLM and Top-down Printing
https://etec.desktopmetal.com/wp-content/uploads/2022/02/top-down-1-1-1.mp4
Most forms of DLP require each layer to be peeled off the film between each layer as the build plate moves up. As each layer is peeled, a small lip is formed on the part, which roughens the surface finish.
The patented CDLM process of the Envision One and top-down printing of the Xtreme 8K eliminate the need for peeling. With no peeling, lipping does not occur, resulting in a significantly better surface finish than other DLP processes.
During top-down printing, parts are fully submerged in the resin. With the parts supported by the resin, fewer support structures are needed, ultimately resulting in a better final surface finish.
High Throughput
High throughput via Large Build Volumes
With a variety of build volumes, ETEC DLP printers are capable of printing a wide variety of part sizes, from large single parts to high volumes of smaller parts in a single build.
Since build times are entirely dependent on Z-axis height, having large build volumes in the X- and Y-axes allow for potentially thousands of parts to be printed at once, in the same time required to print one part.
High throughput via Faster Polymerization
DLP build times are determined by Z-axis height because much of the print time is related to the time it takes to cure, or polymerize, each layer.
ETEC’s DLP technology enables the fastest layer polymerization through the use of the highest-power projectors and a highly efficient optical train.
By allowing for shorter exposure times per layer, ETEC systems ultimately deliver shorter print times and higher throughput.
High throughput via CDLM or Top-Down Printing
https://etec.desktopmetal.com/wp-content/uploads/2022/02/MS_DM_EnvisionTec_E1_CDLM_1080-1.mp4
Many forms of DLP require each layer to be peeled off the film as the build plate moves up between layers. This peeling takes time and must be done slowly to ensure parts are not damaged.
The patented CDLM process of the Envision One and top-down printing of the Xtreme 8K eliminate the need for peeling, reducing the time needed to print each layer and overall print times.
High throughput via Lights-Out Manufacturing
https://etec.desktopmetal.com/wp-content/uploads/2022/01/MS_DM_EnvisionTec_X8K_320_v043. mp4
Get the most out of your ETEC DLP system with high throughput, 24/7 manufacturing designed to rival the volumes of traditionally-manufactured plastic parts.
An automated system for lights-out manufacturing and a dashboard for monitoring all operations and remote control of each machine, further increase uptime for each system.
Superior Part Properties
Superior part properties with New Backbone Chemistry
For decades, polymer 3D printing has been used for prototyping and tooling applications, but the technology hasn’t been widely adopted for the production of end-use parts.
One key to unlocking those end-use applications is the ability to create long-chain molecules in printed parts, resulting in significantly improved material properties, including isotropic strength – a key factor for many end-use parts.
ETEC printers and the DLP process include a number of hardware features – including high-powered projectors, custom-designed optics that minimize power loss– ensuring the creation of those long-chain molecules.
Superior part properties with Isotropic Material Properties
Isotropic material properties are essential for end-use components, but until recently have rarely been achievable with polymer 3D printing.
With FDM printing, very weak mechanical – not chemical – bonds form between each layer, resulting in anisotropic properties, or greater weakness along the Z axis than on the X or Y axes. This lack of uniformity has long kept FDM parts from being used as end-use parts.
With DLP printing, by comparison, each layer is left in a slightly uncured state, allowing it to chemically bond with the next layer as it prints. That bonding helps to create long chain polymers throughout parts, resulting in truly isotropic parts which are strong enough for end-use applications, and rival the properties of injection molded parts.
Superior part properties with 385nm Wavelength
All UV-curable resins require the addition of photoinitiators to start the polymerization process. Resins cured with 385-nm wavelength light require significantly less than many other materials, because the 385-nm wavelength is where absorption peaks for most common photoinitiators. Limiting the amount of photoinitiator in a part is particularly important for clear materials, because higher concentrations of photoinitiator result in parts with a yellow tint.
Quality Materials
Quality materials via Industry-Leading Material Suppliers
ETEC is determined to provide its customers with the best materials in the 3D printing industry. To do it, they utilize a world-class material science team to produce ETEC-exclusive materials, and partner with world-leading material suppliers. The printer systems are designed to be selectively open, giving users flexibility.
Quality materials via 190+ qualified materials
With more than 190 materials, from hard plastics to high-performance elastomers to high-temperature materials, ETEC’s material portfolio can address the widest range of applications.
Quality materials that break the stigma of resins
Though they have been available to print for decades, resins have long been stigmatized as brittle and possessing mechanical properties that deteriorate quickly. A new generation of resins is emerging to erase that stigma, and open the door to a host of new applications.
The superior properties delivered by this new generation of resins includes vital features for end use parts, including mechanical properties that remain stable over time, highly ceramic-filled materials for added toughness and improved surface finishes, and high-temperature materials without brittleness, which are ideal for demanding environments.
In addition to those materials, ETEC offers resins with high wax content, making them ideal for casting jewelry and other products.
Easy To Use
Easy to use Software-Controlled Workflow
https://etec.desktopmetal.com/wp-content/uploads/2022/02/2022-01-24_15-55-16-3.mp4
The software that powers all ETEC printers, Envision One Rapid Prototype (RP) simplifies the process of setting up and starting a print.
With optimized support strategies for every material and automatic part orientation calculation, Envision One RP helps ensure printing success. For users who want more control over prints, the software allows for manual editing of a range of support parameters, including tip thickness, beam thickness, beam spacing and more.
To help increase productivity, prints can even be started remotely.
Easy to use Fast Material Switching
https://etec.desktopmetal.com/wp-content/uploads/2022/02/materiial-switch-1.mp4
With the ability to swap between any of ETEC’s 190-plus materials in just minutes, users can tailor their material choice to each specific application.
All ETEC materials come in a single pot, with no two-pot mixing required, simplifying the process of adding resin to the printer.
While the short shelf life of many competitor resins means they must be used within hours of being opened, all ETEC materials feature shelf lives of more than a year, ensuring no material ever goes to waste.
Envision One - ETEC
Skip to content
Team DM
Platforms
Metal and composites 3D printing 3D printing solutions for health care Industrial-grade polymer 3D printing™
Sand and tooling 3D printing solutions 3D printers for sheet metalMaterials
Breakthrough photopolymer development Advancing 3D printed upcycled woodApps & More
The hydraulic additive manufacturing experts Multi-material powder recoating technology Driving digital transformation in dentistryDesktop Family
Rapid production of strong, fully-isotropic end-use parts
• Overview
The Envision One features patented CDLM (continuous digital light manufacturing) technology, which enables the ability for continuous printing. With little to no delay between layers, the Envision One delivers exceptional speed, print resolution, surface finish, and part properties.
· Key Features
High-speed continuous printing
Finish an entire 3L build volume in just 4. 5 hours – 30% faster than competing systems and 10x faster than desktop SLA.
Best-in-class part performance
The Envision One leverages long-chain polymer chemistry to produce strong, stable parts. The result is isotropic parts suitable for end-use applications and capable of standing up to the most demanding conditions.
High accuracy and resolution
Featuring patented “domeless” printing technology, the Envision One eliminates any concerns about how “doming” may impact accuracy on the Z axis. High-resolution (60 um XY) printing and patented pixel tuning technology make it easy to create fine features and smooth surface finishes suitable for end-use parts.
· Feature 1
High-speed continuous printing
The cDLM process allows for continuous printing without the need to peel each layer off the film after it is polymerized.
A ‘dead zone’ is formed by flowing a thin layer of oxygen above the film of the printing bed. Within this ‘dead zone’ the polymerization process is inhibited ensuring the layer being printed adheres to the layer above and not the printing bed film. This ‘dead zone’ is what enables continuous printing, where the build plate can continually move in the Z axis, leading to faster, more reliable prints.
Made Possible By:
Patented CDLM print process
Patented domeless print basement
· Feature 2
Best-in-class part performance
The Envision One cDLM produces end-use parts with properties that meet or exceed that of traditionally manufactured plastic components, such as injection molded plastics
Unlike most plastic additive manufacturing methods, parts created via CDLM are made up of entangled long-chain polymers, making them fully isotropic. This is vastly different from processes like FDM, which create anisotropic parts with few, if any, polymer chains between each layer. To create those long-chain polymers, printers must be able to process highly viscous resins which require large amounts of power to polymerize. Their high viscosity means these resins cannot be jetted (PolyJet), and would take too long to process with vector based polymerization methods (SLA).
Made Possible By:
Long-chain molecules
Isotropic material properties
High-power projector
· Feature 3
High-resolution printing
The Envision One cDLM delivers best in class part resolution and accuracy to print incredibly crisp features and hold tightest tolerances.
DLP is known for having incredibly high resolution parts and the EnvisionONE CDLM takes accuracy to new heights.
By using industrial DLP chips, verus cheaper consumer grade chips, and a custom designed optical train enable high contrast and minimal distortion for the projected picture resulting in accuracy down to the micron level.
The cDLM domeless printing process eliminates the “dome” effect to deliver incredible Z accuracy.
Made Possible By:
CDLM domeless printing
Industrial DLP chips
Custom-designed optics
· Feature 4
Easy to use software
The brains of the Envision One cDLM is EnvisionONE RP which streamlines the entire fabrication process, ensuring optimal part orientations, print settings, and printer productivity.

Intuitive, easy-to-use Envision One RP software automates support generation and part orientation, while an integrated file repair tool patches meshes and readies the parts for print. Cloud software allows users to remotely manage the system, send jobs to multiple printers and monitor job progress, while over-the-air software and firmware updates ensure users have access to the most up-to-date tools and processes.
Made Possible By:
Build it print profiles for each material
Automated support generation
Optimized part orientation calculator
Customer Story
3D Composites
We make parts that go from outer space all the way to 10,000 feet below the ocean, and everywhere in between because of the versatility of the ETEC machines. In four months, we’ve probably done over 4,000 parts already. With the Envision One, we can hold tolerances down to two-tenths of a millimeter, and the build time is just phenomenal for 3D printing – there’s nothing anywhere close to it.
We’re excited to grow with ETEC, the technology is amazingly repeatable.
Kim Gustafson, Owner, 3D Composites
· Systems
Our Systems
- Printer technology
- Build envelope
- Models
- XY Resolution
- Z Resolution
- Printer technology
- Build envelope
- Models
- XY Resolution
- Z Resolution
- Printer technology
- Build envelope
- Models
- XY Resolution
- Z Resolution
- Printer technology
- Build envelope
- Models
- XY Resolution
- Z Resolution
- Printer technology
- Build envelope
- Models
- XY Resolution
- Z Resolution
New EnvisionTEC cDLM technology makes precision casting a matter of five minutes
News
Recently, EnvisionTEC introduced a new amazing technology cDLM or Continuous Digital Light Manufacturing (“Continuous Digital Light Processing”), for which it has already filed a patent.
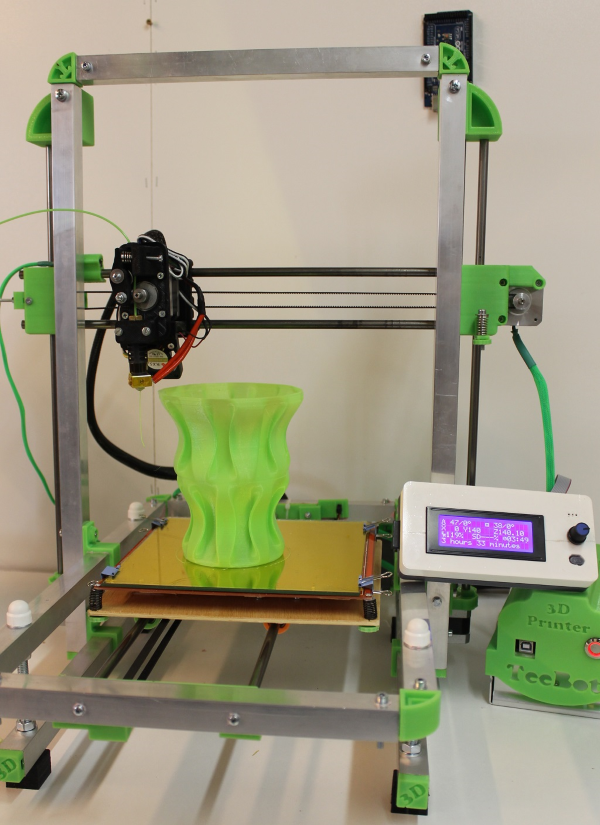
The first cDLM-powered 3D printer, dubbed the Micro Plus cDLM, was designed for precision jewelry casting and completes set tasks in minutes, not hours. The company demonstrated its capabilities to the visitors of the exhibition, right before their eyes, growing products from industrial injection molding material for 3D printing of its own PIC 100 and QView polymer, which currently cures faster than all EnvisionTEC materials.
“The advent of the Micro Plus 3D printer based on continuous digital light processing technology could be a turning point for the jewelry industry,” says EnvisionTEC CEO Al Siblani. “It usually takes a few hours to make a 3D printed molded material like our PIC 100. With the opening of cDLM, wedding bands are designed, manufactured and pre-cast in one day, which is a huge advantage in today's jewelry market.”
On average, the Micro Plus cDLM grows 2.5 cm in the Z-axis in 10-20 minutes depending on the media selected, with the full working volume of the printer (45mm x 28mm x 75mm). The Micro Plus cDLM uses the same industrial UV LED light source. It also has a built-in PC with Wi-Fi and a user-friendly touch screen.
“The focus of our R&D team is to find real solutions to existing problems,” Siblani adds. “By adding the speed capabilities of continuous digital lighting technology to our range of services, we are ready to offer our customers the highest level of service in the jewelry market.”
Micro Plus cDLM will begin shipping in August 2016.
Source
Subscribe author
Subscribe
Don't want
2
Article comments
More interesting articles
7
Subscribe to the author
Subscribe
Don't want
A team of scientists from the Perm National Research Polytechnic University has developed. ..
Read more
7
Subscribe to the author
Subscribe
Don't want
The F2 Gigantry system will allow manufacturing companies, in particular aerospace companies, to...
Read more
sarkazm
Loading
04/01/2016
39826
68
Follow the author
Subscribe
Don't want
News from the world of printing in a short line
FDplast announced the release of a free...
Read more
Industrial 3D printers
Calculation online
Home \ Equipment \ Industrial 3D printers
AM 300 - Russian-made SLM metal printer
AM 300 - Russian-made additive machine for layer-by-layer laser metal fusion (SLM). The AM300 machine allows manufacturing parts used in various industries, medicine, military-industrial complex. They are also used in universities, in design bureaus, and are used in research and experimental work. The AM300 unit provides the possibility of melting the following powder materials: aluminum alloys, stainless steels, maraging steels, cobalt-chromium alloys, nickel alloys, titanium alloys. Suitable for use with titanium powders that meet the requirements of ISO 5832, ASTM F 136, GOST R ISO 5832
Price
on request
Details
Onsint SM200 - industrial system for selective laser sintering (SLS)
Onsint SM200 - industrial system of domestic production in desktop version with chamber dimensions 230 * 230 * 230 mm. Has a 30W CO2 laser and open source software. It has the ability to work with any known materials, including polyamide PA2200 and glass-filled PA3200GF, as well as materials of domestic production. Perfectly will be suitable both for production, and for research works.
Price
on request
More details
Onsint SM300 - industrial selective laser sintering system (SLS)
Onsint SM300 - domestic industrial SLS system with chamber 330*330*450 mm. Has a 30W CO2 laser and open source software. Perfectly will be suitable both for industrial enterprises, and for carrying out research works.
Price
on request
More
Raplas FPS 850 / 850 plus - systems for digital production of foundry sand molds
FPS 850 / 850 (plus) is a high performance industrial system for digital mold production. Allows you to create complex sandforms, complex geometries and undercuts directly from CAD data. The high quality printheads are optimized for continuous sand printing.
Price
on request
More details
Raplas RPS 450 HD+ and RPS 700 HD+ prototyping systems
High-tech complex for stereolithography additive manufacturing of prototypes, master models and small batch sizes with an unbeatable price-performance-to-accuracy ratio cameras! Made in Germany!
Price
on request
Learn more
Envisiontec Vector 3SP
EnvisionTEC's EnvisionTEC 300 x 200 x 275 mm wide format photopolymer 3D printer with a build area of 300 x 200 x 275 mm allows you to produce especially large parts with high speed and without quality loss and accuracy of performance.
Price
from €52,500
More details
EnvisionTEC Ultra 3SP
The ULTRA® 3SP™ series uses the innovative 3SP™ technology to quickly and accurately print parts of any geometric complexity from STL file data. Construction area - 266 x 175 x 193 mm. The ULTRA® 3SP™ and 3SP™ HD (high resolution) systems come with all the necessary software for automatic support creation and production.
Price
from €41,400
More
Envision One
The Envision One cDLM is the largest, most advanced desktop photopolymer 3D printer ever built. It's bigger, faster, easier to use and more innovative than any other 3D printer on the market.
Price
on request
More details
SISMA mysint 100
Mysint 100 is a machine for additive manufacturing of metal models by selective laser fusion of metal powder. With this installation, you can quickly produce a variety of dental structures: crowns, bridges, frames, individual implants.
Price
on request
More details
SLM Solutions SLM® 125
9The 0002 SLM 125 is a compact selective laser melting machine with a printable area of 125 x 125 x 125 mm that can produce complex parts from special metal powders: stainless steel, tool steel, aluminium, titanium, inconel and cobalt chromium.Price
on request
More details
SLM Solutions SLM® 280 2.0
The SLM® 280 2.0 system can be equipped with one fiber laser (400 and 700 W), two or a combination of 40 W and 70 W each lasers (power 700 and 1000 watts), which operates on a special technology based on the simultaneous operation of several lasers with different laser beam profiles. Construction area 280 x 280 x 365 mm.
Price
on request
More
SLM Solutions SLM® 280 PRODUCTION SERIES
The SLM®280 Production Series has a 280 x 280 x 365 mm build area and patented multi-laser technology for serial production. In the build workflow using 2 lasers, which is optimal for medium-sized machines, the build area is exposed using
3D scanning optics.
Price
on request
More
SLM Solutions SLM® 500
The SLM 500 selective melting system is a powerful manufacturing tool for quickly producing metal products of any configuration. The unit is equipped with two lasers (400W or 700W each) or four lasers (400W or 700W each) that can be used simultaneously or in parallel and independently - this greatly increases productivity. SLM 500 working chamber 500x280x365 mm in size.
Price
on request
More details
SLM Solutions SLM® 800
SLM®800 with an impressive build area of 500 x 280 x 850(H) mm and 4 large lasers with a power of 400 or 700 W creates large components with build rates up to 171 cm3/h.
Price
on request
Read more
Fill out the form and our specialist will contact you!
ITs AT LLC was established in January 2018 as a center for coordination, creation, selection and adaptation of solutions for the use of 3D technologies at enterprises in various industries.