3D printing of pharmaceutical tablets
3D printing of drugs can revolutionise personalised medicine
February 4, 2021
By GlobalData Healthcare
3D printers can be installed in pharmacies, hospitals, clinics, and remote locations, enabling on-demand production of drugs. Credit: Adul10 / Shutterstock.As the pharmaceutical industry moves away from mass production towards a more personalised model, 3D printing of drugs have the potential to revolutionise the market. The main benefit of using 3D printing technology for personalised pharmaceuticals is the ability to produce small batches with carefully tailored dosages, shapes, sizes, and release characteristics. It also allows flavours to be incorporated into a pill without the need of a film coating, entirely masking the taste of chemical compounds. 3D printers can be installed in pharmacies, hospitals, clinics, and remote locations, enabling on-demand production of drugs, particularly those with poor stability or that have cold chain storage requirements. For pharmaceutical companies, 3D printing can significantly reduce costs, waste, and environmental burden as printers only deposit the exact amount of raw materials required.
Aprecia Pharmaceuticals’ Spritam (levetiracetam), an anti-epileptic drug, is the first and only 3D-printed pharmaceutical. It received the Food and Drug Administration (FDA) approval in 2015 and is made using Aprecia’s proprietary ZipDose technology. The orodispersible tablet achieves full disintegration within seconds when in contact with liquid. Additionally, very high doses are achievable (up to 1,000mg), which are not typically possible through conventional methods. ZipDose technology uses a drop-on-solid printing technique where droplets of a liquid binding agent are deposited by a print nozzle onto a free pharmaceutical powder bed, unifying the free-form powder where it lands. The bed is then lowered to allow for another layer of free-form powder to be added. Further droplets are introduced, adding height to the nascent pill, while the surrounding, unbound powder particles act as a support structure to prevent the collapse of the highly porous pill structure.
In April 2020, UK-based FabRx launched the first commercially available 3D printer for personalised drug manufacturing. M3DIMAKER is an extrusion-based printer that allows the print nozzle to be changed to accommodate different dosage requirements. Alongside the established extrusion-based fusion deposition modelling printing, whereby the printer melts the pharmaceutical mixture and excipients through a nozzle onto the build plate, the M3DIMAKER also uses a different extrusion-based method developed by FabRx: direct powder extrusion (DPE). Similar to Aprecia’s ZipDose technology, DPE deposits a powdered pharmaceutical agent onto a print bed through a nozzle aided by a single extruder. Both methods enable the manufacture of multiple-drug combination pills and sustained or delayed-release tablets.
To date, large biopharmaceutical companies have shown minimal activity in this area. In February 2020, Merck KGaA announced a collaboration with AMCM for the development and production of 3D printed pharmaceuticals for clinical trials and, later, for clinical manufacturing. The stated goal of the partnership is to develop drugs using powder bed fusion, whereby a laser melts and fuses powder together layer by layer. Merck and AMCM expect this to make the manufacturing of tablets both faster and cheaper due to the avoidance of reformulations. GlaxoSmithKline has also shown interest in 3D printing of drugs, partnering with The University of Nottingham on a study that used nozzle printing and ultraviolet curing to produce 3D printed ropinirole tablets to treat Parkinson’s disease.
The traditional one-size-fits-all model of drug development is inefficient and costly. Pharma companies need to adopt new technologies such as 3D printing to make more personalised treatments, improve R&D efficiencies, reduce costs, and minimise waste. This will not only lead to more streamlined and cost-effective supply chains, it will also improve sustainability, which has been touted as one of the most important trends across industries for 2021 and beyond.
Five companies personalizing treatments with 3D printed drugs
There has been a noticeable shift in recent years towards the personalization of medicine, with the pharmaceutical industry showing interest in pills that are tailored to a patient’s needs. Here are five companies that are leveraging 3D printing to produce customizable drugs.
Conventional drug production relies on large-scale batch manufacturing, which is very efficient at churning out large volumes of drugs with uniform characteristics. But this becomes time-consuming and expensive when small batches are needed, such as for clinical trials where the doses need to be adjusted. The process is also associated with an environmental burden resulting from inefficient use of raw materials, expired stock and production of toxic and non-toxic waste.
Additive manufacturing, or 3D printing, is a tool that can allow for small-scale production of medicines. This approach uses 3D modeling software to build an object layer-by-layer; for solid drugs, the 3D printer stacks ink with an excipient — inactive substances in drugs added for specific functions like improved stability and bioavailability — and the active pharmaceutical ingredient to print out a finished product. By adjusting the printing parameters, the drug dosages, drug combinations, release profiles and even flavors can be personalized.
There are many challenges that have limited widespread implementation of 3D printing technology, such as 3D printers not meeting good manufacturing practice standards and a limited range of excipients suitable for 3D printing. Nevertheless, 3D printing has the potential to revolutionize the pharmaceutical industry, and several companies are making strides in the space.
Aprecia PharmaceuticalsHeadquarters: Pennsylvania, U.S.
Aprecia Pharmaceuticals is behind the first and only U.S. Food and Drug Administration (FDA)-validated 3D printing platform for commercial-scale drug development. Their aim is to make medicines easier to take and reduce the number of pills a patient needs. Using this platform, Aprecia developed ZipDose Technology, which allows tablets to hold a high dosage load of up to 1,000 mg and still rapidly dissolve with just a sip of water.
Content continues below
Related Content
ZipDose is used in the production of Spritam (levetiracetam), a fast dissolving oral medicine for the treatment of specific types of epileptic seizures. It is targeted for patients who struggle to swallow pills or are unable to measure out the precise dosage of liquid levetiracetam. In 2015, Spritam became the first and only 3D printed drug to be approved by the FDA.
FabRxHeadquarters: London, U.K.
Founded in 2014 as a spin-out of University College London, FabRx aims to revolutionize medical treatments by facilitating the production of personalized medicines, where the size, shape, dosage and dosage combinations can be customized. In 2020, the company released M3DIMAKER, the first pharmaceutical 3D printer for personalized medicine, allowing clinicians and other professionals to “print” tailored medicines on demand.
Using their 3D printing technology, FabRx has also created a range of personalized Printlets — medicines with customized shapes, flavors, colors, dosages and release profiles, such as tablets with Braille and moon patterns for patients with visual impairments as well as Polypills, which combine several drugs in one pill.
FabRx technology is also being used to print personalized pills for children with a rare metabolic disorder called maple syrup urine disease, which requires treatments to be strictly tailored based on age, weight and blood concentrations of the amino acid isoleucine. Current manual preparation methods are time consuming and costly, so FabRx’s approach could save time and money for caregivers.
MerckHeadquarters: Darmstadt, Germany
Content continues below
Related Content
The biopharma giant Merck is also taking a stab at next-generation tablet manufacturing through 3D printing. In 2020, Merck announced a cooperation with ACMC — sister company of EOS, a worldwide provider of 3D printing solutions — to produce 3D printed tablets for clinical trials at first, before moving towards commercial-scale manufacturing. This partnership aims to advance the industrial applications of 3D printing technology and digitalization.
Triastek, Inc.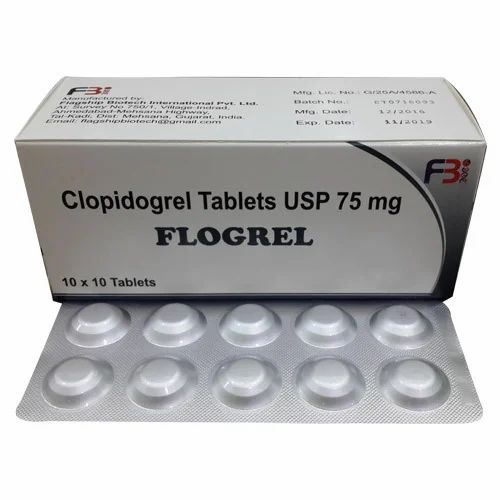
Headquarters: Nanjing, China
Triastek is a global leader in pharmaceutical 3D printing, with 41 patents that account for more than 20% of global 3D printing pharmaceuticals applications. Using their proprietary MED 3D printing technology, Triastek develops their own in-house drugs and partners with others to provide drug development solutions.
The MED 3D printing platform allows for the customizable design of tablets, with the different shapes and geometries controlling drug onset time, duration, and drug interactions with the body. This platform was accepted into the FDA’s Emerging Technology Program in 2020, and two of their 3D printed drugs have been granted investigational new drug clearances from the FDA. The first is a chronotherapeutic drug for rheumatoid arthritis, where the drug is taken at bedtime but its release is delayed until the early morning hours, when pain and joint stiffness are at their peak. The second is a one-dose pill alternative to the twice-daily marketed drug for cardiovascular and clotting disorders.
Triastek recently entered into a research collaboration with Eli Lilly and Company to improve the bioavailability of drugs in the intestine by achieving precise organ targeting and programmed drug release.
GlaxoSmithKlineHeadquarters: Brentford, U.K.
GSK was one of the first big pharma companies to show interest in 3D printing as a manufacturing tool, partnering with the University of Nottingham to study the feasibility of 3D inkjet printing and curing with ultraviolet light to produce solid drug forms; in 2017, researchers demonstrated the successful 3D printing of ropinirole tablets for Parkinson’s disease.
3D inkjet printing deposits liquid materials or solid suspensions layer-by-layer but each deposited layer must first be dried, or “cured,” between the deposition steps. GSK is exploring how to convert active pharmaceutical ingredients into curable ink to enable 3D drug printing.
Pharmacy 3D printing | Remedium.ru
Magazine "Remedium" №9, 2020
DOI: 10. 21518/1561-5936-2020-9-58-60
Yulia Prozherina, PhD,
REM Analytics
3D printing of medicines is an innovative and economical technology that is an important step towards personalized medicine. This direction can be used to develop drugs with controlled release of active substances; preparations containing combinations with fixed doses, as well as for the creation of orodispersible dosage forms. The global 3D drug market is still largely at the research stage, but is expected to grow rapidly in the next decade [1].
3D printing in pharmacy
Yuliya Prozherina, Cand. of Sci. (Bio.),
RM Analytics
3D printing of drugs is an innovative and cost-effective technology, which is a major step towards personalized medicine. This technology can be used for the development of controlled-release drugs; fixed-dose combination drugs, as well as for the creation of orodispersible dosage forms. The global 3D drug market is still largely at the research stage, but its rapid growth is expected in the coming decade [1].
FROM CARS TO DRUGS
3D printing was developed in the late 1980s at the Massachusetts Institute of Technology (MIT) as a rapid prototyping technique. Currently, it has become widespread and is actively used in industries such as automotive, healthcare (primarily in dentistry and orthopedics) and retail.
Important steps are also being taken towards the development and implementation of 3D medicines into clinical practice. By the way, issued by Therics, Inc. (Princeton, New Jersey) at 19The '94 license covers the use of 3D printing for the production of various products, including medicines (MPs). The application of these technologies in the field of drug delivery has been actively investigated, and in 2015 it was implemented in the United States. In August 2015, the first 3D-printed and FDA-approved LP was produced on an industrial scale. It was the orodispersible antiepileptic drug Spritam (levetiracetam) from Aprecia Pharmaceuticals. The creation of this drug laid the foundation for the 3D future in pharmaceuticals, demonstrating the possibilities of 3D printing for the production of complex dosage forms. Research and development in this area is still ongoing [2].
IMPORTANT ADVANTAGES
3D drug printing technology becomes an important step in the development of personalized medicine, as it allows implementing the principle of individual selection of components and their dosage depending on the needs of the patient. In addition, when creating a dosage form (DF) according to the presented technology, it is possible to adjust the release profile of the active ingredient depending on the individual characteristics of the patient. Particularly relevant is the creation on the basis of this technology of easily and quickly soluble orodispersible drugs in the oral cavity.
3D printing of drugs may also be in demand in the orphan drug segment, since these drugs are produced in small quantities.
From a technological point of view, the advantages of additive methods in drug development are the ability to accurately control the spatial distribution of pharmaceutical substances, create complex geometries, precipitate small amounts of pharmaceutical substances, reduce waste, and speed up the production of various compositions for screening studies or the manufacture of individualized drugs. The manufacturing benefits associated with LP printing are moving away from traditionally complex, slow and costly production chains and enabling more personalized products without the need for high volume production [2]. To some extent, 3D printing can become a continuation of the pharmacy tradition of manufacturing medicines based on individual recipes, but at a technologically new level and implemented in a slightly different way.
WORLDWIDE 3D
According to Maximize Market Research, the global 3D medicine market reached $245M in 2019 and is expected to grow to $456M by 2027 (CAGR 8 . 07%).
The key drivers of market growth are innovations in 3D printing technologies, as well as an increase in diseases such as epilepsy, schizophrenia, for which the use of instantly soluble dosage forms in the oral cavity is important. On the other hand, unforeseen technological difficulties, the need for large investments in further research, the introduction of various regulation scenarios for this industry segment, as well as the likelihood of side effects of drugs manufactured by this method can hinder further market growth [1, 3].
The global 3D printed medicines market can be segmented by dosage form, manufacturing technology and geography.
Based on dosage form, the market is categorized into tablets, capsules, multi-drug implant, nanoparticles, solutions, nanosuspensions, encapsulated polymer and implant [1].
In terms of applied 3D drug manufacturing technology, the market is divided into inkjet printing, direct-write, zip dose, thermal inkjet (TIJ), deposition modeling (FDM), powder printing and stereolithography (SLA) [1]. Despite the fact that over the past 15 years a large number of different 3D printing technologies have been introduced into the LP prototyping industry, inkjet printing is still the most popular [2].
Geographically, the market is divided into North America, Europe, Asia Pacific (APAC), South America, and the Middle East and Africa (MEA). The Asia-Pacific region holds the leading market share in the 3D printed medicine market, accounting for 34.1%. It is expected to act as a further growth driver for the segment (CAGR 18.2%). At the same time, countries in the Asia-Pacific region, such as China and India, will grow at the highest rates thanks to huge investments in both R&D and the pharmaceutical industry. In the European region, growth in the development of this technology is also predicted [3].
Drawing. Global 3D Printed Medicines Market, by Region: 2020-2027
Source: Maximize. Market Research PVT. LTD [3]
There are still few players in the global market for 3D printed medicines. The key ones are GlaxoSmithKline PLC and Aprecia Pharmaceuticals LLC, Fabrx Ltd [1]. Merck, Hewlett Packard Caribe, BV, LLC, 3D Printer Drug Machine, Cycle Pharmaceuticals, etc. are actively engaged in development in this direction [4]. In order to stay in the competitive market, the leading players use various strategies such as acquisitions, mergers, expansions, joint ventures and products. For example, GlaxoSmithKline PLC (GSK) has been investing in 3D printing technology for several years. The R&D department of the 3D printing company uses it in a variety of ways, from drug prototyping to drug packaging. The goal of Fabrx Ltd and GSK is to develop approaches to individualized medicine for each patient using 3D printing [1].
Work on the creation of LP using 3D printing technology is also underway in our country. For example, scientists at the St. Petersburg Chemical and Pharmaceutical University plan to create a technology for individual drug dosages using 3D printing. The university has a Russian-made Picasso 3D printer. Another promising project in the field of bioprinting for the university is the creation of drugs with controlled release [5].
DRIVER – COVID
While the creation of 3D medicines still requires more research, the production of medical devices and various parapharmaceutical products is progressing more rapidly. In addition, the COVID-19 pandemic has only accelerated this process. So, for example, in many countries of the world this spring, medical products designed to protect against coronavirus were printed on 3D printers. Printed medical masks in the UK were provided by iMark, and in Russia by Temporum (a resident of the Nagatino technopark). Carbon has been actively printing face shields. In Spain, Consorci de la Zona Franca, HP Inc., Leitat and CatSalut have developed the first 3D printed emergency ventilation device. Devices printed on a 3D printer were actively purchased by hospitals in Italy [6]. And this is not the limit of the possibilities of using additive technologies. According to Forbes, the coronavirus pandemic could be a truly high point for 3D printing [7].
References
- 3D Printed Drugs Market Research and Forecast 2018-2027. available at: https://www.omrglobal.com/.
- Blynskaya E.V., Tishkov S.V., Alekseev K.V. 3D printing technologies for the production of dosage forms. Development and registration of medicines . 2018;(24):10–19.
- Global 3D Printed Drugs Market–Industry Analysis and Forecast (2020-2027) – By Scenario, End User and Region. Available at: https://www.maximizemarketresearch.com/.
- 3D Printed Drugs Market 2019 Top Key Players are 3D Printing Systems, Aprecia Pharmaceuticals, Hewlett Packard Enterprise, Hewlett Packard Enterprise, GlaxoSmithKline PLC and Forecast to 2025. Source: Available at: https://www.medgadget.com/.
- Using 3D printing technology, it is possible to control drug release in the body. Access mode: https://gxpnews.net/.
- 3D printing in medicine.
Access mode: https://zdrav.expert/.
- "Great moment": why the coronavirus pandemic could be the high point for 3D printing. Access mode: https://www.forbes.ru/.
3D drug printing
September 11, 2018
Popular science competition "Bio/mol/text"-2018
Overview
Tablet formed by printing layers of polymer mixed with drug
Alvaro Goyanes
-
Author
- Alexey Korolev
-
Editor
- Andrey Panov
Themes
- "Bio/mol/text"-2018
- Biology
- Biotechnology
- The medicine
- Personalized medicine
- Pharmacology
Article for the bio/mol/text competition: Recently, 3D printing has become one of the most revolutionary and powerful tools in many areas. The pharmaceutical industry is no exception. This article will tell readers about the history of 3D printing in the pharmaceutical industry, the latest developments and achievements in this field, and the prospects for the development of 3D printing in the industry.
This work was published in the nomination "Biopharmaceuticals" of the competition "bio/mol/text"-2018.
The general sponsor of the competition is the Diaem company: the largest supplier of equipment, reagents and consumables for biological research and production.
The partner of the nomination is the medical company Invitro.
The audience award was sponsored by the Genotek Medical Genetics Center.
"Book" sponsor of the competition - "Alpina non-fiction"
Introduction
Now 3D printers can create almost everything. From car parts and fashion accessories to transplant organs and pharmaceuticals. For example, 3D printers can print medical devices with intricate designs, geometries, and features that fit a particular patient's anatomy.
3D bioprinting of organs and tissues is described in the articles " Organs from the laboratory " [1] and " Artificial organs and tissue engineering " [2]. — Ed.
Medical 3D printing is rapidly revolutionizing healthcare. The use of 3D printing in medicine brings wide-ranging benefits: personalization of medical devices, medicines, cost-effectiveness, increased productivity, and democratization of design and production.
Before we start delving into the topic of 3D printing in the pharmaceutical industry, let's figure out what 3D printing actually is.
Three-dimensional (3D) printing is an additive (additive) manufacturing method in which objects are made in layers by melting and sintering solid or solidifying liquid materials (ceramics, plastics, metals, powders, liquids, or even living cells).
There are about two dozen 3D printing methods that use different printing technologies, resolutions and speeds. There are hundreds of materials from which you can recreate a 3D object of almost any shape.
In order for a three-dimensional object to come into being, you must first create a digital model in a 3D editor, or CAD program, and export it to STL format. Using a special slicer program, translate the STL file into a control G-code for a 3D printer, prepare the 3D printer for work, and start printing. The most important elements of the printer are working platform (on which the object is formed) and print head (it forms the object layer by layer). Some time passes (if the object is small - a few minutes or hours, and if it is large, then printing can take more than a day), and voila, the object is ready!
What is 3D printing we learned, move on.
A bit of history
Figure 1. The most important advances in 3D printing in the pharmaceutical industry
- Early 70s. Pierre Ciraud ( Pierre Ciraud ) described the method of applying a powder material and then solidifying each layer under the influence of a high energy beam.
- 1984 Stereolithography (SLA) invented by Chuck Hull ( Chuck Hull ) was the first commercially available 3D printing technology. This method is based on the photopolymerization of liquid resin with ultraviolet light.
- Mid 1980s. Carl Deckard ( Carl Deckard ) developed a method for solidifying layers of powder using a laser beam, which he called the Selective Laser Sintering (SLS) method .
- 1989 Scott Crump ( Skott Crump ) patented Rapid Prototyping (FDM) technology is a method that uses a thermoplastic material to form a 3D object. Otherwise, this technology is called deposition modeling .
- 1990s. Invented DOS method — similar in principle to that used in inkjet printers.
- 2008 The RepRap printer, a self-copying machine for rapid prototyping, is invented.
- 2015 The American company Aprecia Pharmaceuticals has developed ZipDose technology, which makes it possible to form tablets that are convenient because they quickly dissolve in a small amount of water.
This technology was used to produce the first FDA-approved printed drug Spritam® ( Food and drug administration , US Food and Drug Administration) [3].
Dictionary
- DOD
- ( Drop On Drop ) liquid layering.
- DOS
- ( Drop On Solid ) hard overlay.
- FDM
- fused deposition method, additive manufacturing technology.
- SLA
- stereolithography, additive manufacturing technology for models from liquid photopolymer resins.
- SLS
- selective laser sintering, additive manufacturing technology.
- STL
- is a file format widely used for storing 3D object models for use in additive technologies.
How drug printing works
Many different methods of 3D printing have been invented and developed over its 40 year history.
The basic 3D printing methods (fig. 2) are based on:
- solidification of powder material
- hardening fluid
- extrusion [3]
Figure 2. 3D printing methods used to create medicines
Despite the variety of 3D printing methods, each of them includes the following steps, which we talked about at the beginning (Fig. 3) [3] :
- designing a 3D object using software and optimizing the geometry of the object according to the printer specification;
- export of a 3D model to a file format recognized by the printer, for example, STL;
- Importing a file into the software and creating layers in it to be printed. The height of the printed layer significantly affects the quality of the object, as well as the print time;
- fabrication of an object by subsequent application (or curing) of layers of material.
Figure 3. Stages of 3D printing, development
Application of 3D printing in pharmaceuticals (examples) see where these technologies are already being successfully used to create pharmaceutical products.
Example 1
As reported above, the first 3D printed drug was Spritam® (Fig. 4), developed by the American pharmaceutical company Aprecia Pharmaceuticals and approved by the Food and Drug Administration (FDA) . The active substance of the drug is Levetiracetam is an antiepileptic drug. Levetiracetam is able to quickly dissolve in the mouth, the time of disintegration (dissolution) of the drug is from 2 to 27 seconds (average - 11 seconds). A small sip of water is required to disintegrate the drug. The liquid formula, which binds levetiracetam and excipients for the manufacture of the drug, contains flavor-masking additives that improve the patient's condition [4].
Figure 4: Spritam® (levetiracetam), the first 3D printed drug
Aprecia Pharmaceuticals
Example 2
FabRx is a British biotechnology company specializing in the development of 3D printing technology for the production of pharmaceuticals and medical devices. The company was founded by a group of scientists from University College London who saw the potential of 3D printing technology to create drugs [5].
Figures 5-7 show FabRx designs.
Figure 5. Gummy-like drugs in a variety of shapes, sizes, colors, textures and flavors. FabRx makes them attractive to different patient groups, especially young and old people.
fabrx.co.uk
Figure 6. FabRx researchers experimented with the sizes and shapes of preparations and conducted a study that showed that a pyramid-shaped tablet dissolves faster in water than a cylindrical one
fabrx.co.uk
Figure 7. University College London scientists also experimented with different drug forms (octopus, dinosaur, cat, monkey, and others) on a pediatric patient population
The future of 3D printing drugs in pharmacies is closer than you think
There are few examples, since 3D printing is just being introduced into the pharmaceutical industry, and today only a few companies are engaged in 3D printing of drugs.
Benefits and prospects of 3D printing in pharmaceuticals
Benefits
- Customization and personalization.
3D printing technologies allow custom dosage forms, release profiles and dosage for each patient. For example, for small patients, a tablet can be printed in the form of some cute animal of any color (Fig. 7).
- Improving cost efficiency. 3D printing will reduce production costs by reducing the use of unnecessary resources. Some drugs can be printed in forms that can be easily and conveniently delivered to the patient (Fig. 8).
- Democratization. Another feature of 3D printing is the democratization of product design and manufacturing. As the cost efficiency of 3D printing increases, the products become orders of magnitude cheaper. [6]
Figure 8. FabRx products
fabrx.co.uk
Perspectives
In the distant future, perhaps if 3D printing develops, everyone will be able to print a drug at home. So far, this can only be a dream. But in the near future, as the researchers suggest, drugs can be printed in pharmacies and hospitals.
Can 3D drug printing replace traditional drug manufacturing technologies? No - it will require huge investments, trained employees and a number of other things. Yes, and large pharmaceutical companies can prevent the penetration of 3D printing into pharmacies and hospitals. 3D printing is unlikely to catch on in large enterprises, as 3D printers print much more slowly than pharmaceutical production machines. Another significant barrier that may prevent the widespread use of 3D printing in pharmaceuticals is the long and costly obtaining approvals from the quality control services of medicines. In addition, manufacturing regulations and government legal requirements also hinder the spread of 3D drug printing [6].
Pharmaceutical 3D printing is young and still evolving. I think that 3D printing will not be able to capture the pharmaceutical market, since Big Pharma is not going to give up. And as already mentioned, in the world there are only two companies aimed at the development of three-dimensional printing of drugs - this is the American company Aprecia Pharmaceuticals and the British company FabRx.