3D printing methods comparison
FDM vs. SLA vs. SLS
Additive manufacturing, or 3D printing, lowers costs, saves time, and transcends the limits of fabrication processes for product development. From concept models and functional prototypes in rapid prototyping to jigs, fixtures, or even end-use parts in manufacturing, 3D printing technologies offer versatile solutions in a wide variety of applications.
Over the last few years, high-resolution 3D printers have become more affordable, easier to use, and more reliable. As a result, 3D printing technology is now accessible to more businesses, but choosing between the various competing 3D printing solutions can be difficult.
Which technology is suitable for your particular application? What materials are available? What equipment and training do you need to get started? How about costs and return on investment?
In this article, we’ll take a closer look at the three most established plastic 3D printing processes today: fused deposition modeling (FDM), stereolithography (SLA), and selective laser sintering (SLS).
Trying to decide between FDM and SLA 3D printers? Check out our in-depth FDM vs. SLA comparison.
Video Guide
Having trouble finding the best 3D printing technology for your needs? In this video guide, we compare FDM, SLA, and SLS technologies across popular buying considerations.
Watch the Videos
Download the high-resolution version of this infographic here.
Fused deposition modeling (FDM), also known as fused filament fabrication (FFF), is the most widely used form of 3D printing at the consumer level, fueled by the emergence of hobbyist 3D printers. FDM 3D printers build parts by melting and extruding thermoplastic filament, which a printer nozzle deposits layer by layer in the build area.
FDM works with a range of standard thermoplastics, such as ABS, PLA, and their various blends. The technique is well-suited for basic proof-of-concept models, as well as quick and low-cost prototyping of simple parts, such as parts that might typically be machined.
FDM parts tend to have visible layer lines and might show inaccuracies around complex features. This example was printed on a Stratasys uPrint industrial FDM 3D printer with soluble supports (machine starting at $15,900).
FDM has the lowest resolution and accuracy when compared to SLA or SLS and is not the best option for printing complex designs or parts with intricate features. Higher-quality finishes may be obtained through chemical and mechanical polishing processes. Industrial FDM 3D printers use soluble supports to mitigate some of these issues and offer a wider range of engineering thermoplastics, but they also come at a steep price.
FDM printers struggle with complex designs or parts with intricate features (left), compared to SLA printers (right).
Stereolithography was the world’s first 3D printing technology, invented in the 1980s, and is still one of the most popular technologies for professionals. SLA resin 3D printers use a laser to cure liquid resin into hardened plastic in a process called photopolymerization.
See how stereolithography works.
SLA parts have the highest resolution and accuracy, the clearest details, and the smoothest surface finish of all plastic 3D printing technologies, but the main benefit of SLA lies in its versatility. Material manufacturers have created innovative SLA photopolymer resin formulations with a wide range of optical, mechanical, and thermal properties to match those of standard, engineering, and industrial thermoplastics.
SLA parts have sharp edges, a smooth surface finish, and minimal visible layer lines. This example part was printed on a Formlabs Form 3 desktop SLA 3D printer (machine starting at $3,750).
SLA is a great option for highly detailed prototypes requiring tight tolerances and smooth surfaces, such as molds, patterns, and functional parts. SLA is widely used in a range of industries from engineering and product design to manufacturing, dentistry, jewelry, model making, and education.
White Paper
Looking for a 3D printer to realize your 3D models in high resolution? Download our white paper to learn how SLA printing works and why it's the most popular 3D printing process for creating models with incredible details.
Download the White Paper
Sample part
See and feel Formlabs quality firsthand. We’ll ship a free sample part to your office.
Request a Free Sample Part
Selective laser sintering is the most common additive manufacturing technology for industrial applications, trusted by engineers and manufacturers across different industries for its ability to produce strong, functional parts.
See how selective laser sintering works.
SLS 3D printers use a high-powered laser to fuse small particles of polymer powder. The unfused powder supports the part during printing and eliminates the need for dedicated support structures. This makes SLS ideal for complex geometries, including interior features, undercuts, thin walls, and negative features. Parts produced with SLS printing have excellent mechanical characteristics, with strength resembling that of injection-molded parts.
SLS parts have a slightly rough surface finish, but almost no visible layer lines. This example part was printed on a Formlabs Fuse 1 benchtop SLS 3D printer (machine starting at $18,500).
The most common material for selective laser sintering is nylon, a popular engineering thermoplastic with excellent mechanical properties. Nylon is lightweight, strong, and flexible, as well as stable against impact, chemicals, heat, UV light, water, and dirt.
The combination of low cost per part, high productivity, and established materials make SLS a popular choice among engineers for functional prototyping, and a cost-effective alternative to injection molding for limited-run or bridge manufacturing.
White Paper
Looking for a 3D printer to create strong, functional parts? Download our white paper to learn how SLS printing works and why it's a popular 3D printing process for functional prototyping and end-use production.
Download the White Paper
Sample part
See and feel Formlabs SLS quality firsthand. We’ll ship a free sample part to your office.
Request a Free Sample Part
Each 3D printing technology has its own strengths, weaknesses, and requirements, and is suitable for different applications and businesses. The following table summarizes some key characteristics and considerations.
Fused Deposition Modeling (FDM) | Stereolithography (SLA) | Selective Laser Sintering (SLS) | |
---|---|---|---|
Resolution | ★★☆☆☆ | ★★★★★ | ★★★★☆ |
Accuracy | ★★★★☆ | ★★★★★ | ★★★★★ |
Surface Finish | ★★☆☆☆ | ★★★★★ | ★★★★☆ |
Throughput | ★★★☆☆ | ★★★★☆ | ★★★★★ |
Complex Designs | ★★★☆☆ | ★★★★☆ | ★★★★★ |
Ease of Use | ★★★★★ | ★★★★★ | ★★★★☆ |
Pros | Low-cost consumer machines and materials Fast and easy for simple, small parts | Great value High accuracy Smooth surface finish Fast printing speeds Range of functional applications | Strong functional parts Design freedom No need for support structures |
Cons | Low accuracy Low details Limited design compatibility | Sensitive to long exposure to UV light | Rough surface finish Limited material options |
Applications | Low-cost rapid prototyping Basic proof-of-concept models | Functional prototyping Patterns, molds, and tooling Dental applications Jewelry prototyping and casting Modelmaking | Functional prototyping Short-run, bridge, or custom manufacturing |
Print Volume | Up to 300 x 300 x 600 mm (desktop and benchtop 3D printers) | Up to 300 x 335 x 200 mm (desktop and benchtop 3D printers) | Up to 165 x 165 x 300 mm (benchtop industrial 3D printers) |
Materials | Standard thermoplastics, such as ABS, PLA, and their various blends.![]() | Varieties of resin (thermosetting plastics). Standard, engineering (ABS-like, PP-like, flexible, heat-resistant), castable, dental, and medical (biocompatible). | Engineering thermoplastics. Nylon 11, Nylon 12, and their composites. |
Training | Minor training on build setup, machine operation, and finishing; moderate training on maintenance. | Plug and play. Minor training on build setup, maintenance, machine operation, and finishing. | Moderate training on build setup, maintenance, machine operation, and finishing. |
Facility Requirements | Air-conditioned environment or preferably custom ventilation for desktop machines. | Desktop machines are suitable for an office environment. | Workshop environment with moderate space requirements for benchtop systems. |
Ancillary Equipment | Support removal system for machines with soluble supports (optionally automated), finishing tools.![]() | Washing station and post-curing station (both can be automated), finishing tools. | Post-processing station for part cleaning and material recovery. |
Ultimately, you should choose the technology that makes the most sense for your business. Prices have dropped significantly in recent years, and today, all three technologies are available in compact, affordable systems.
Calculating 3D printing costs does not end with upfront equipment costs. 3D printing material and labor costs have a significant influence on cost per part, depending on the application and your production needs.
Here’s a detailed breakdown by technology:
Fused Deposition Modeling (FDM) | Stereolithography (SLA) | Selective Laser Sintering (SLS) | |
---|---|---|---|
Equipment Costs | Budget printers and 3D printer kits start at a few hundred dollars. Higher quality mid-range desktop printers start around $2,000, and industrial systems are available from $15,000.![]() | Professional desktop printers start at $3,750, large-format benchtop printers at $11,000, and large-scale industrial machines are available from $80,000. | Benchtop industrial systems start at $18,500, and traditional industrial printers are available from $100,000. |
Material Costs | $50-$150/kg for most standard and engineering filaments, and $100-200/kg for support materials. | $149-$200/L for most standard and engineering resins. | $100/kg for nylon. SLS requires no support structures, and unfused powder can be reused, which lowers material costs. |
Labor Needs | Manual support removal (can be mostly automated for industrial systems with soluble supports). Lengthy post-processing is required for a high-quality finish. | Washing and post-curing (both can be mostly automated). Simple post-processing to remove support marks. | Simple cleaning to remove excess powder. |
Interactive
Try our interactive ROI tool to see how much time and cost you can save when 3D printing on Formlabs 3D printers.
Calculate Your Savings
Prototypes of a ski goggles' frame printed with FDM, SLA and SLS technology (from left to right).
We hope this article has helped you focus your search for the best 3D printing technology for your application.
Explore our additional resources to master the intricacies of 3D printing, and dive deeper into each technology to learn more about specific 3D printing systems.
Learn More About 3D Printing
SLS vs FDM & SLA vs DLP
As technology advances, different 3D printing technologies have also emerged and introduced. Currently, the most used and popular technologies are SLS (Selective Laser Sintering), FDM (Fused Deposition Modelling), SLA (Stereolithography) and DLP (Digital Light Processing). These 3D printing technologies follow similar principles but produce significantly different outputs.
Understanding each 3D printing method helps user identify what they really need and what to expect from final 3D prints. They can also learn how to maximise the potential of each type of 3D printer.
To understand this topic more, below is the side by side comparison of the popular and most used 3D printing methods today.
Describing the process- SLS vs FDM
SLS or Selective Laser Sintering is known to be the most common 3D printing technology that is used for industrial applications. Its main material is nylon/polyamide in powdered form. This is a process which uses high powered laser to fuse together small particles of the material.
FDM is a 3D printing method wherein layers of filament materials are melted and fused while it is positioned in a structured way to create an object.
- SLA vs DLP
Both SLA and DLP are technologies that create a 3D part by selectively curing polymer resin layer by layer. The only difference is the light source and how it is being used in the process.
SLA utilises UV laser beam to cure or harden the resin material. The laser beam also cures the material layer by layer, and in series of points. DLP, on the other hand uses projector to flash an image across the entire platform at once.
The overall cost is one of the factors when choosing what type of method is appropriate for your project. Here is the side by side comparison of its printing cost.
- SLS vs FDM
SLS is mainly used for industrial applications such as in aerospace, healthcare, electronics, etc. Because of that, SLS printers are usually large and can be very expensive.
Among all the printing technologies, FDM is the cheapest method. It is often used by individuals who do not have big budget to buy expensive printers and 3D printing materials.
- SLA vs DLP
Both SLA and DLP uses resin material to print 3D parts. Resin can be very expensive as it costs around $80 to $150 per litre. The difference on their printing costs will only depend on the printer and the manufacturer of the resin material.
There are many factors that influence the printing speed. These factors include part orientation and amount of material to be printed.
Other factors may also include the temperature of the print nozzle, filament thickness, the material to heat, the laser power for SLA, number of supports required for FDM, etc.
- SLS vs FDM
Lead times for SLS 3D printing are typically shorter compared to FDM. Printing speed for SLS may reach up to 48 mm/h while FDM can print up from 50 to 150 mm/h depending on the printer.
- SLA vs DLP
When it comes to printing speed, DLP has the advantage. Since the entire layer of a 3D part is exposed to light at once, the printing process is quicker compared to SLA.
Post-processingAfter the 3D part is taken out from any printer, there are some finishing touches that need to be done on the 3D part. Post-processing is a stage where the 3D part undergoes a number of processes to enhance its appearance.
- SLS vs FDM
Post-processing for SLS is not as complicated as the other technologies. You just have to clean up the unused or unsintered powder which served as support during printing. This can be done manually or with the use of compressed air.
When it comes to FDM, post-processing can be difficult. Improper dissolving of support structure can damage your print or may leave holes on the surface. It also needs specialized equipment such as glass containers or ultrasonic bath.
- SLA vs DLP
Post-processing for SLA can be time-consuming. There are some processes wherein the 3D part is required to be disposed and stored in special containers.
Moreover, since DLP printers render images using rectangular voxels, there is also an effect of vertical voxel lines on the surface. Thus, post-processing is also required. The appearance of voxel lines requires sanding process.
When to use these methodsIn order to choose the best 3D printing method that will suit your project, here is a guideline on when to use a specific 3D printing method.
SLS
- For more advanced industrial 3D printing projects
- For objects with complex designs
- Rapid and functional prototyping
- Low-volume production
FDM
- Rapid prototyping
- Building low-cost models
- Great for hobbyists and fabricators
- Projects where precision and surface finish isn’t crucial
SLA
- Printing many small intricate parts at once
- Detailed large prints
- Creating moulds for mass-production
DLP
- One-off small and very complicated parts
- Quickly printing large parts without much detail
Choosing what 3D printing method to be used will always depend on what you will need for your project and your intended budget. With this guide, it can be easier to decide whether FDM, SLS, SLA or DLP is suitable for you.
But if you are still confused about what 3D printing method to use, then you can ask for professional help. You can look for a 3D printing service provider to cater your 3D printing needs.
Comparison of 3D printing technologies: FDM, SLA and SLS
Additive manufacturing or 3D printing reduces costs, saves time and expands the technological possibilities in product development. 3D printing technologies offer versatile solutions for applications ranging from rapid concept and functional prototypes in the field of prototyping to fixtures and clamps or even final parts in manufacturing.
Over the past few years, high resolution 3D printers have become more affordable, more reliable and easier to use. As a result, more companies have been able to use 3D printing technology, but choosing between different competing 3D printing solutions can be difficult. nine0003
Which technology is right for your needs? What materials are available for her? What equipment and training is needed to get started? What are the costs and payback?
In this article, we take a closer look at three of today's most well-known plastic 3D printing technologies: Fused Deposition Modeling (FDM), Stereolithography (SLA), and Selective Laser Sintering (SLS).
Choosing between FDM and SLA 3D printer? Check out our detailed comparison of FDM and SLA technologies. nine0012
Download this high resolution infographic here.
VIDEO MANUAL
Can't find the 3D printing technology that best suits your needs? In this video tutorial, we compare Fused Deposition Modeling (FDM), Stereolithography (SLA), and Selective Laser Sintering (SLS) technologies in terms of the top factors to consider when purchasing.
Watch Video
Fused Deposition Modeling (FDM), also known as Fused Filament Manufacturing (FFF), is the most widely used form of 3D printing at the consumer level, fueled by the rise of consumer 3D printers. On FDM printers, models are made by melting and extruding a thermoplastic filament, which the printer's nozzle applies layer by layer to the model being built. nine0003
The FDM method uses a range of standard plastics such as ABS, PLA and their various blends. It is well suited for making basic experimental models, as well as for quickly and inexpensively prototyping simple parts, such as parts that are usually machined.
FDM models often show layer lines and may have inaccuracies around complex features. This sample was printed on a Stratasys uPrint FDM industrial 3D printer with soluble support structures (printer price starting at $15,900).
FDM printers have the lowest resolution and accuracy of SLA or SLS and are not the best option for printing complex designs or parts with complex features. Surface quality can be improved by chemical and mechanical polishing processes. To address these issues, industrial FDM 3D printers use soluble support structures and offer a wider range of engineering thermoplastics, but they are also expensive. nine0003
FDM printers do not handle complex designs or parts with complex features well (left) compared to SLA printers (right).
Invented in the 1980s, stereolithography is the world's first 3D printing technology and is still one of the most popular technologies among professionals today. SLA printers use a process called photopolymerization, which is the conversion of liquid polymers into hardened plastic using a laser.
See stereolithography in action.
Models printed on SLA printers have the highest resolution and accuracy, the sharpest detail and the smoothest surface of all plastic 3D printing technologies, but the main advantage of the SLA method is its versatility. Materials manufacturers have developed innovative formulas for SLA polymers with a wide range of optical, mechanical and thermal properties that match those of standard, engineering and industrial thermoplastics. nine0003
Models created using SLA technology have sharp edges, a smooth surface and almost invisible layer lines. This sample was printed on a Formlabs Form 3 Desktop Stereolithographic 3D Printer (price starting at $3499).
SLA is an excellent option for making highly detailed prototypes that require tight tolerances and smooth surfaces such as molds, templates and functional parts. SLA technology is widely used in industries ranging from engineering and design to manufacturing, dentistry, jewelry, modeling, and education. nine0003
White Paper
Download our in-depth white paper to learn how SLA printing works, why thousands of professionals use it today, and how this 3D printing technology can be useful in your work.
Download white paper
free sample
Experience Formlabs print quality firsthand. We will send a free 3D printing sample directly to your office.
Request a free sample
Selective laser sintering is the most common additive manufacturing technology used in industry.
Selective Laser Sintering (SLS) 3D printers use a high power laser to sinter fine polymer powder particles. The unsprayed powder supports the model during printing and eliminates the need for special support structures. This makes SLS ideal for complex geometries, including internal features, grooves, thin walls, and negative taper. Models produced using SLS printing have excellent mechanical characteristics: their strength can be compared with the strength of injection molded parts. nine0003
Models created with SLS technology have a slightly rough surface, but almost no visible layer lines. This sample was printed on the Formlabs Fuse 1 SLS workshop 3D printer (price starting at $18,500).
The most common selective laser sintering material is nylon, a popular engineering thermoplastic with excellent mechanical properties. Nylon is light, strong and flexible, resistant to impact, heat, chemicals, UV radiation, water and dirt. nine0003
The combination of low part cost, high productivity, and widely used materials makes SLS a popular method for engineering functional prototyping and a cost-effective alternative to injection molding in cases where production runs are limited.
White Paper
Looking for a 3D printer to create durable, functional models? Download our white paper to learn how selective laser sintering (SLS) technology works and why it is popular in 3D printing for functional prototypes and end-use products. nine0003
Download white paper
Each 3D printing technology has its strengths, weaknesses, limitations and applications. The following table summarizes the key characteristics and factors.
Modeling method (FDM) | Stereolithography (SLA) | Selective laser sintering (SLS) | |
---|---|---|---|
★★★★☆ | |||
accuracy | ★cle ★cle \ ★★★★★ | ||
Easy to use | ★★★★★ | ★★★★★ | ★★★★★★★★★★★★★0104 |
Benefits | Speed Inexpensive custom machines and materials | High cost efficiency High accuracy Smooth surface Wide range of functional applications | Robust functional parts Design flexibility No need for supporting structures |
Disadvantages | Poor accuracy low detail Limited Compliance with Design Design | Susceptibility to prolonged UV exposure | Uneven surface Material Limitations |
Applications | Inexpensive Rapid Prototyping Basic experimental models | Functional prototyping Templates, forms and tools Dental products Prototyping jewelry and molds Model building | Functional prototyping Small-scale and custom manufacturing |
Print volume | Up to ~300 x 300 x 600 mm (desktop 3D printers) | Up to ~300 x 335 x 200 mm (Desktop and Workshop 3D printers) | Up to 165 x 165 x 300 mm (Workshop 3D printers) |
Materials | ABS plastic, PLA and their various mixtures.![]() | Various polymers (thermosets). Standard, engineering (with properties of ABS plastic, polypropylene, flexible, heat-resistant), molding, dental and medical (biocompatible). | Engineering thermoplastics. Nylon 11, Nylon 12 and their composites. nine0104 |
Training | Minimum training in equipment setup, machine operation and surface treatment; short maintenance training. | Plug and play concept. Minimal training in equipment setup, maintenance, machine operation and surface treatment. | Short training in equipment setup, maintenance, machine operation and surface treatment. |
Room requirements | Air-conditioned environment or preferably individual ventilation for desktop machines. | Desktop machines suitable for office use. | Workshop systems have moderate space requirements and can be installed in a production environment. |
Accessories | Support removal system for machines with soluble support structures (optionally automated), finishing tools.![]() | Finishing station, washing station (optionally automated), finishing tools. | Post-processing station for cleaning models and restoring materials. |
Either way, you should choose the technology that best suits your business. Prices have dropped significantly in recent years, and today all three technologies are offered in compact and affordable systems.
3D printing costing doesn't end with initial equipment costs. Material and labor costs have a significant impact on the cost of each part, depending on the application and production needs. nine0003
Below is a detailed breakdown by technology.
Modeling method (FDM) | Stereolithography (SLA) | Selective laser sintering (SLS) | Equipment costs and sets for 3D-dimensions for 3Ds and sets several hundred dollars. Offering higher quality, mid-range desktop printers start at $2,000, while industrial systems start at $15,000.![]() | Professional desktop printers start at $3,500, large-format workshop printers start at $10,000, industrial systems for large-scale production start at $80,000. |
---|---|---|---|
Material cost | $50-$150/kg for most standard and engineering yarns and $100-$200/kg for auxiliary materials. | $50-$150/L for most standard and engineering polymers. | $100/kg for nylon. SLS does not require supporting structures and unused powder can be reused, reducing material costs. |
Labor | Manual removal of support structures (may be automated for industrial systems with dissolvable supports). Long post-processing is required to obtain a high quality surface. | Washing and final polymerization (both can be automated). Simple post-processing to remove supporting structures. nine0104 | Easy cleaning to remove excess powder. |
INTERACTIVE MATERIAL
Try our interactive ROI tool to see how much time and money you can save by printing with Formlabs 3D printers.
Calculate savings
FDM, SLA and SLS printed prototype ski goggle frames (left to right).
We hope this article has helped you narrow down your search for the 3D printing technology best suited to your needs. nine0003
Take advantage of our additional resources to learn the ins and outs of 3D printing, learn more about each technology and learn more about specific 3D printing systems.
Learn more about 3D printing technologies
3D printer comparison guide 2020
The market for 3D printing and additive manufacturing has changed significantly in recent years. While technology used to be mostly a hobbyist business, high-end desktop machines have turned it into an indispensable tool for businesses. After 3D printing became the main tool for prototyping and product design, it has become widely used in manufacturing, dentistry, jewelry and many other fields. nine0003
Fused Deposition Modeling (FDM) and Stereolithography (SLA) printers are the two most popular types of 3D printers on the market. Both 3D printing technologies have been adapted and enhanced for desktop use, increasing their accessibility, functionality and usability.
In this comprehensive buyer's guide, we take a closer look at FDM and SLA 3D printers and compare them in terms of print quality, materials, application, workflow, speed, cost, and more to help you determine which method is the most suitable for your business. nine0003
VIDEO MANUAL
Can't find the 3D printing technology that best suits your needs? In this video tutorial, we compare Fused Deposition Modeling (FDM), Stereolithography (SLA), and Selective Laser Sintering (SLS) technologies in terms of the top factors to consider when purchasing.
Watch Video
Fused Deposition Modeling (FDM), also known as Fused Filament Manufacturing (FFF), is the most widely used form of 3D printing at the consumer level. The working principle of FDM 3D printers is to extrude thermoplastic filaments such as ABS (Acrylonitrile Butadiene Styrene), PLA (Polylactide) through a heated nozzle, melt the material, and deposit the plastic on the build platform layer by layer. Layers are applied sequentially one after another until the model is ready. nine0003
See how FDM 3D printing is done.
FDM 3D printers are well suited for making basic experimental models, as well as for quickly and inexpensively prototyping simple parts, such as parts that are usually machined.
Invented in the 1980s, stereolithography is the world's first 3D printing technology and is still one of the most popular technologies among professionals today. SLA 3D printers use a process called photopolymerization, which is the conversion of liquid polymers into hardened plastic using a laser. nine0003
See how SLA 3D printing is done.
Resin-based SLA 3D printers have become extremely popular due to their ability to produce highly accurate, isotropic and waterproof prototypes and models with excellent detail and smooth surfaces. SLA polymers offer a wide range of optical, mechanical and thermal properties that match those of standard, engineering and industrial thermoplastics.
Resin 3D printing is an excellent option for producing highly detailed prototypes that require tight tolerances and smooth surfaces such as molds, templates and functional parts. SLA 3D printers are widely used in industries ranging from engineering and design to manufacturing, dentistry, jewelry, modeling, and education.
White Paper
Download our white paper to find out how SLA printing works, why thousands of professionals use it today, and how this 3D printing technology can be useful in your work. nine0003
Download white paper
When additive manufacturing builds a model layer by layer, each layer contains the potential for inaccuracies. The layering process affects the surface quality, the level of accuracy and correctness of each layer, and therefore the overall print quality.
FDM 3D printers form layers through the application of lines of molten material. During this process, the resolution of the model is determined by the size of the extrusion nozzle, and when lines are drawn with the nozzle, voids are created between the rounded lines. As a result, the layers may not be completely adjacent to each other, they are usually clearly visible on the surface, and, in addition, there is no ability to reproduce the complex details that other technologies offer. nine0003
In SLA 3D printing, each layer is formed by curing a liquid polymer with a high-precision laser, which allows you to get models with greater detail and achieve high quality on a consistent basis. As a result, SLA 3D printing is known for excellent detail, smooth surfaces, high precision models and accurate rendering.
3D Printing Accuracy, Accuracy and Tolerance are terms that are not entirely clear and often misunderstood. Find out what they mean to get a better idea of 3D printing quality. nine0012
Models created using SLA technology have sharp edges, smooth surfaces and almost invisible layer lines. This sample was printed on a Formlabs Form 3 desktop stereolithography 3D printer.
Using light instead of heat in the printing process is another way to ensure the print quality of SLA printers. Since 3D models are printed at close to room temperature, they do not suffer from the thermal expansion and contraction distortions that can occur during FDM printing. nine0003
Due to the high-precision laser, SLA 3D printers are better suited for making complex parts (FDM printed part on the left, SLA printed part on the right).
While FDM printers create a mechanical bond between layers, SLA 3D printers create chemical bonds between photopolymers by cross-linking photopolymers, resulting in dense, waterproof and airtight models. These bonds provide a high degree of shear strength resulting in isotropic parts, which means that the strength of the parts does not change depending on the direction. This makes the use of SLA 3D printing especially useful in the field of engineering and manufacturing, where material properties are important.
The difference in quality is less noticeable on relatively simple parts. However, SLA parts are dense and isotropic, so they find more use in design and manufacturing (left - FDM printed part on the left, right - SLA printed part on the right). nine0003
free sample
Experience Formlabs print quality firsthand. We will send a free 3D printing sample directly to your office.
Request a free sample
Extrusion 3D printers use a range of standard thermoplastic filaments such as ABS, PLA and their various blends. The popularity of FDM 3D printing among hobbyists has led to a large number of colors available. There are also various experimental mixtures of plastic threads designed to create models with a surface that mimics wood or metal. nine0003
Engineering materials such as nylon, PETG, PA or TPU and high strength thermoplastics such as PEEK or PEI are also available, but in most cases only certain professional FDM printers support them.
FDM filaments and blends offer various color options. (source: All3DP.com)
The advantage of SLA polymers is 's wide range of formulations offering a variety of characteristics: they can be soft or hard, contain additives such as glass and ceramic, have special mechanical properties such as high bending temperature under load or shock resistance. The polymers offer a wide range of optical, mechanical and thermal properties that match those of standard, engineering and industrial thermoplastics. nine0003
SLA 3D printers provide access to a variety of materials for design and production.
In some cases, it is this combination of versatility and functionality that leads businesses to adopt SLA 3D printing in-house. Once a solution has been found with a particular functional polymer, other applications are usually quickly discovered, and the printer becomes a tool for exploiting the diverse properties of different polymers. nine0003
Some properties of SLA polymers are unique. Among them:
SLA is the only 3D printing technology that allows you to create transparent models on a desktop printer. Ideal for enhancing the visibility of complex assemblies, (micro)fluidic elements, mold making, optics, lighting elements and any product requiring transparency.
Learn more
Parts printed with this material look and feel like silicone; They are durable enough to be used multiple times. nine0003
Learn more
Offers the highest HDT of 238°C at 0.45 MPa, the highest temperature resistance of any desktop 3D printing material.
Learn more
Resin with 20% wax for investment casting and pressing of dental and jewellery.
Learn more
Specialty resins for dental products such as biocompatible surgical guides, splints, permanent casts and dentures, clear aligner patterns, and complete dentures. nine0003
Learn more
Resin for 3D printing of models with a stone-like texture and subsequent production of a ceramic product by firing.
Learn more
Material selection
Our interactive materials wizard helps you select the right material from our growing range of polymers based on the future application of the material and the properties that matter most to you.
Get material recommendations
Both FDM and SLA 3D printing workflow consists of three steps: design, 3D printing, and post-processing. nine0003
First, a model is designed using CAD software or 3D scan data and exported to a 3D print file format (STL or OBJ). Then you need to use the software to prepare the 3D model for printing, in particular, set the print parameters and separate the digital model into layers.
Budget FDM or SLA 3D printers are not very convenient in terms of usability: finding the right print settings for them requires experimentation and often takes hours. Even so, when using a new design or material, the print result may change, and the probability of rejection remains high. This not only causes delays in projects, but can also cause printer failure that will take a long time to resolve. nine0003
Professional SLA 3D printers such as the Form 3 and some professional FDM printers come with their own proprietary software and presets for each material that have been rigorously tested to ensure the best printing results.
With advanced print preparation tools such as PreForm, print setup is plug and play. PreForm software is available as a free download and you can try it right now. nine0318 .
Once the 3D printing process has started, most 3D printers can run it without an operator, even overnight, until the model is finished. Advanced SLA 3D printers such as the Form 3 automatically refill resins from cartridges.
The last step in the workflow is post-processing. Models produced by SLA require rinsing with isopropyl alcohol (IPA) or alternative solvents to remove uncured polymers from their surface. The standard workflow involves first removing the models from the build platform and then manually soaking them in a solvent bath to remove excess resin. nine0003
Professional solutions such as Form Wash automate this process. Models from the printer are transferred to the Form Wash station, which cleans the models by stirring the solvent around them and automatically removes the models from the alcohol bath when the process is complete.
After the washed models have dried, some SLA resins require final polymerization of , a process that helps models achieve the highest possible strength and stability. nine0003
The advantage of the FDM method is that it does not require cleaning; models without supporting structures are ready for use or post-processing immediately after the printing process is completed.
In both FDM and SLA printing, support structures can be used to facilitate 3D printing of complex shapes, and their removal is the last step in post-processing.
On FDM models, the supporting structures must be separated manually or dissolved in water, depending on the material of the structure. nine0003
Obtaining a high quality surface on FDM models with supporting structures requires additional post-processing (source: 3D Hubs).
Removal of the supporting structures on SLA models consists of cutting off the supporting structures and lightly sanding the models to remove traces of the supports. Formlabs Low Force Stereolithography (LFS) ™ technology offers easy-to-release supports that allow separation of the object from the supporting structure in seconds and with minimal marks, reducing post-processing costs. nine0003
In additional post-processing, both FDM and SLA models can be machined, primed, painted or assembled depending on the application. However, before priming or painting, FDM models require additional sanding, and for machining or drilling, a higher filling density is required.
Use our easy-to-use interactive tool to help you calculate model costs and lead times using your Form 2 3D printer and compare time and cost savings with other manufacturing methods. nine0003
One of the main advantages of FDM 3D printers is the low cost of the device. Entry-level FDM printers are available for as little as a few hundred dollars, giving hobbyists and small businesses a chance to see 3D printing in action and decide whether to add the technology to their toolbox. For novice users, the lower cost of an entry-level FDM printer is often an argument for making a purchase. However, inexpensive FDM printers can be unreliable and often require specialized knowledge for long-term use. nine0003
Professional desktop FDM printers are easier to use and more suitable for business applications and are priced between $2,000 and $8,000. Such 3D printers typically offer higher reliability, higher print quality, and higher print volumes. Although these devices are suitable for the production of functional models, competition in this price category is strong, since the scope of SLA printers is wider and the print quality is better.
SLA 3D printers start at $3750 and only Formlabs releases SLA Large Format 3D Printer priced under $11,000.
In terms of materials, FDM filaments also have a relatively low cost compared to materials used in other 3D printing technologies. Commonly used FDM materials such as ABS, PLA and their various blends typically cost around $50/kg, while specialized FDM filaments for engineering applications can cost $100-150/kg. Soluble support materials for dual extrusion FDM 3D printers sell for $100-200/kg. By comparison, most standard and engineered resins for SLA 3D printers cost $50-$150/L. nine0003
Labor is the last and often overlooked part of the equation. FDM models of simple form, which do not need support structures when printed, require almost no post-processing. For FDM models with supporting structures and parts where high surface quality is important, lengthy manual post-processing is required.
SLA models require rinsing and, depending on the material, also final polymerization, but in most cases both processes can be automate with accessories , thus minimizing labor costs. SLA models with support structures require only minimal sanding to remove support marks and achieve a high quality finish.
INTERACTIVE
Try our interactive ROI tool to see how much time and money you can save by printing with Formlabs 3D printers.
Calculate savings
FDM printers can print in thicker layers and typically use lower infill density to speed up the 3D printing process. FDM also has fewer post-processing steps for simple models. Depending on the specific project, this means that the models are ready for use shortly after printing is completed. This is very useful for tasks such as rapid prototyping - users can quickly evaluate the result and move on to printing another model or project. nine0003
However, the speed advantage of FDM is currently waning due to the emergence of faster SLA resins such as Draft Resin which prints 40% faster than FDM 3D printers. With a layer thickness of 300 µm, Draft Resin achieves sufficient precision to meet the needs of prototyping while enabling faster design iteration cycles. If the model occupies the entire working volume, it can take up to 20 hours for the SLA printer to produce it using standard resins, which will require printing at night. Printing the same part in 300 micron layers with Draft Resin takes less than six hours. nine0003
These are six prototype pump housings printed using Draft Resin. It took 3 hours and 7 minutes to print one prototype with standard resins, and 47 minutes with Draft Resin. The final model was printed using Tough Resin and Rigid Resin.
With the same layer thickness, the print speed of FDM and SLA printers becomes comparable. Please note that due to the way the layers are formed, a part printed with 100 micron layers on an FDM printer is very different from a part printed with 100 micron layers on an SLA printer. Achieving comparable quality on an FDM printer would require a thinner layer—which means two to four times longer print times—or more and longer post-processing to improve surface quality. nine0003
Webinar
In this webinar, two Formlabs experts will teach you when to use Draft Resin and how to incorporate this resin into your 3D printing workflow to speed it up and shorten your product development cycle.
Watch the webinar now
Print volume is an area where FDM printers have traditionally dominated. Due to the specifics of the technology, the production of large-format FDM printers is less complicated. There are many large format FDM solutions on the market for applications that require 3D printing of large parts. nine0003
Inverted stereolithography used in desktop SLA printers reduces printer space and cost, but the intensive layer separation process creates material and print volume limitations, and strong support structures are required to successfully print larger parts.
The development of Formlabs Low Force Stereolithography (LFS) technology, used in the Form 3 and Form 3L printers, has revolutionized the approach to resin 3D printing and drastically reduced the forces on models during the printing process. Uniform linear illumination and a force-reducing elastic reservoir mean that Low Force Stereolithography technology can be seamlessly scaled to a wider print area using the same powerful print engine. nine0003
The first affordable large-format stereolithography printer, the Form 3L prints large details quickly using two stepped Light Processing Units (LPUs) that work simultaneously on an optimized print path. Offering up to five times the print volume of current SLA printers, the Form 3L eliminates size constraints that can be found on small desktop devices at a competitive price.
Each 3D printing technology has its strengths, weaknesses, limitations and applications. The following table summarizes the key characteristics and factors. Fused Deposition Modeling (FDM)
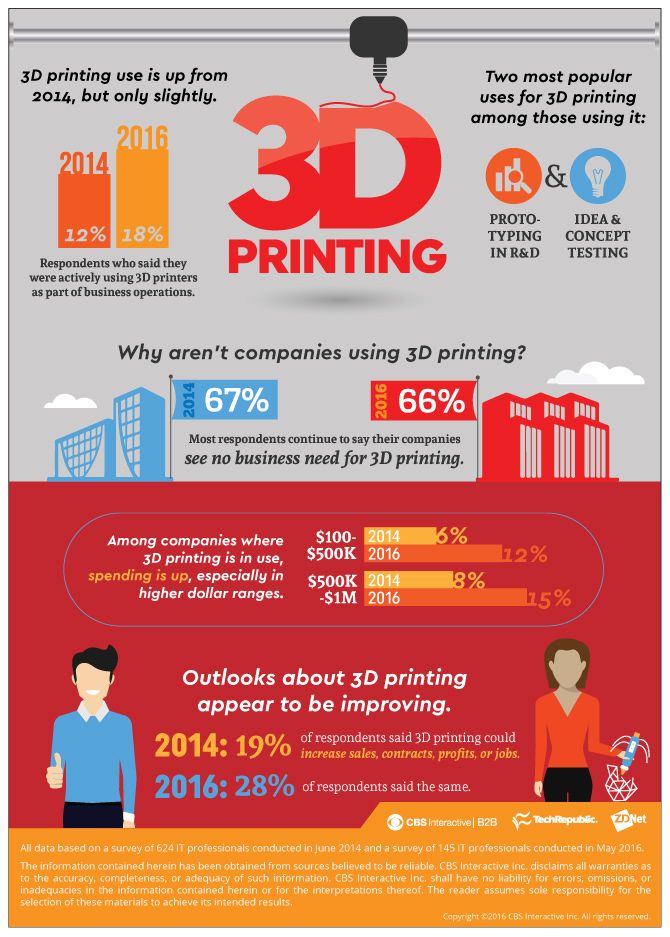
Comparing the two technologies, we can conclude that FDM and SLA printers have similar, often complementary features. These two types of 3D printers are not always in competition; many companies use both FDM and SLA 3D printers. In this way, you can get the best of both worlds: inexpensive rapid prototyping combined with high-quality functional model production allows you to solve a wide range of problems. nine0003
Some practical examples:
-
When developing products, FDM models or SLA printing with Draft Resin are ideal for basic proof-of-concept testing and faster iteration. As you move into the next stages of development, SLA 3D printing is indispensable for producing detailed concept models or functional prototypes that may require higher quality and materials with different properties.
nine0678 -
Both FDM and SLA 3D printing are often used in manufacturing to make clamps, fasteners and other tooling. FDM is best suited for large and simple parts, SLA for complex fixtures, precision fixtures and molds.
-
FDM and SLA printers are being used effectively in education.
Learn more