3D printing markham
3D Printing Service Markham | Instant Quotes Online
Our 3D printing capabilities
We have over 90 3D printing shops in our network and are well known for manufacturing high-quality parts at competitive prices, from rapid prototyping with Fused Deposition Modeling (FDM) to functional end parts made with Selective Laser Sintering (SLS) or Multi Jet Fusion (MJF).
Gallery of 3D printed parts manufactured by Hubs
With over 65,000 customers from every industry, including aerospace, defense, robotics, medical, machinery, automotive and electronics, we have extensive experience meeting a diverse range of 3D printing requirements, from prototyping to production: Visual aids, concept models, injection-molding prototypes, form-fit & function prototypes, tooling and casting patterns, jigs, grips and fixtures, and durable end parts.
HP PA 12 - Dyed Black
Customer | True North Design |
Purpose | Structural and vacuum EOAT components |
Process | SLS / MJF |
Unit price | $69. |
Industry | Automotive |
Prototyping PLA
Customer | Allision Conner |
Purpose | End caps and cable strain relief for sheet metal enclosure |
Process | FDM |
Unit price | $7.92 / $4.72 / $2.80 |
Industry | Industrial Automation |
HP PA 12
Customer | US Hammer |
Description | A part for gasoline engine powered jackhammers |
Process | MJF |
Unit price | $22.18 |
Industry | Construction |
Markforged Onyx - Black
Customer | Autocom Manufacturing |
Purpose | A production part for 3D printed lathe gantry gripper fingers |
Process | FDM |
Unit price | $48.![]() |
Industry | Automotive |
PC Stratasys - white
Customer | Terumo medical corporation |
Purpose | Prototyping parts used for a disposable electrical device |
Process | FDM |
Unit price | $55.38 / $32.96 |
Industry | Medical |
Formlabs Clear Resin
Customer | Aversan Inc |
Purpose | A prototyping part of an injection molded component for an automated door mechanism |
Process | SLA |
Unit price | $29.83 |
Industry | Aerospace |
HP PA 12 - Dyed Black
Customer | True North Design |
Purpose | Structural and vacuum EOAT components |
Process | SLS / MJF |
Unit price | $69.![]() |
Industry | Automotive |
Prototyping PLA
Customer | Allision Conner |
Purpose | End caps and cable strain relief for sheet metal enclosure |
Process | FDM |
Unit price | $7.92 / $4.72 / $2.80 |
Industry | Industrial Automation |
HP PA 12
Customer | US Hammer |
Description | A part for gasoline engine powered jackhammers |
Process | MJF |
Unit price | $22.18 |
Industry | Construction |
Markforged Onyx - Black
Customer | Autocom Manufacturing |
Purpose | A production part for 3D printed lathe gantry gripper fingers |
Process | FDM |
Unit price | $48.![]() |
Industry | Automotive |
PC Stratasys - white
Customer | Terumo medical corporation |
Purpose | Prototyping parts used for a disposable electrical device |
Process | FDM |
Unit price | $55.38 / $32.96 |
Industry | Medical |
Formlabs Clear Resin
Customer | Aversan Inc |
Purpose | A prototyping part of an injection molded component for an automated door mechanism |
Process | SLA |
Unit price | $29.83 |
Industry | Aerospace |
HP PA 12 - Dyed Black
Customer | True North Design |
Purpose | Structural and vacuum EOAT components |
Process | SLS / MJF |
Unit price | $69.![]() |
Industry | Automotive |
Prototyping PLA
Customer | Allision Conner |
Purpose | End caps and cable strain relief for sheet metal enclosure |
Process | FDM |
Unit price | $7.92 / $4.72 / $2.80 |
Industry | Industrial Automation |
HP PA 12
Customer | US Hammer |
Description | A part for gasoline engine powered jackhammers |
Process | MJF |
Unit price | $22.18 |
Industry | Construction |
Markforged Onyx - Black
Customer | Autocom Manufacturing |
Purpose | A production part for 3D printed lathe gantry gripper fingers |
Process | FDM |
Unit price | $48.![]() |
Industry | Automotive |
PC Stratasys - white
Customer | Terumo medical corporation |
Purpose | Prototyping parts used for a disposable electrical device |
Process | FDM |
Unit price | $55.38 / $32.96 |
Industry | Medical |
Formlabs Clear Resin
Customer | Aversan Inc |
Purpose | A prototyping part of an injection molded component for an automated door mechanism |
Process | SLA |
Unit price | $29.83 |
Industry | Aerospace |
HP PA 12 - Dyed Black
Customer | True North Design |
Purpose | Structural and vacuum EOAT components |
Process | SLS / MJF |
Unit price | $69.![]() |
Industry | Automotive |
Prototyping PLA
Customer | Allision Conner |
Purpose | End caps and cable strain relief for sheet metal enclosure |
Process | FDM |
Unit price | $7.92 / $4.72 / $2.80 |
Industry | Industrial Automation |
HP PA 12
Customer | US Hammer |
Description | A part for gasoline engine powered jackhammers |
Process | MJF |
Unit price | $22.18 |
Industry | Construction |
Markforged Onyx - Black
Customer | Autocom Manufacturing |
Purpose | A production part for 3D printed lathe gantry gripper fingers |
Process | FDM |
Unit price | $48.![]() |
Industry | Automotive |
PC Stratasys - white
Customer | Terumo medical corporation |
Purpose | Prototyping parts used for a disposable electrical device |
Process | FDM |
Unit price | $55.38 / $32.96 |
Industry | Medical |
Formlabs Clear Resin
Customer | Aversan Inc |
Purpose | A prototyping part of an injection molded component for an automated door mechanism |
Process | SLA |
Unit price | $29.83 |
Industry | Aerospace |
HP PA 12 - Dyed Black
Customer | True North Design |
Purpose | Structural and vacuum EOAT components |
Process | SLS / MJF |
Unit price | $69.![]() |
Industry | Automotive |
Prototyping PLA
Customer | Allision Conner |
Purpose | End caps and cable strain relief for sheet metal enclosure |
Process | FDM |
Unit price | $7.92 / $4.72 / $2.80 |
Industry | Industrial Automation |
HP PA 12
Customer | US Hammer |
Description | A part for gasoline engine powered jackhammers |
Process | MJF |
Unit price | $22.18 |
Industry | Construction |
Markforged Onyx - Black
Customer | Autocom Manufacturing |
Purpose | A production part for 3D printed lathe gantry gripper fingers |
Process | FDM |
Unit price | $48.![]() |
Industry | Automotive |
PC Stratasys - white
Customer | Terumo medical corporation |
Purpose | Prototyping parts used for a disposable electrical device |
Process | FDM |
Unit price | $55.38 / $32.96 |
Industry | Medical |
Formlabs Clear Resin
Customer | Aversan Inc |
Purpose | A prototyping part of an injection molded component for an automated door mechanism |
Process | SLA |
Unit price | $29.83 |
Industry | Aerospace |
HP PA 12 - Dyed Black
Customer | True North Design |
Purpose | Structural and vacuum EOAT components |
Process | SLS / MJF |
Unit price | $69.![]() |
Industry | Automotive |
Prototyping PLA
Customer | Allision Conner |
Purpose | End caps and cable strain relief for sheet metal enclosure |
Process | FDM |
Unit price | $7.92 / $4.72 / $2.80 |
Industry | Industrial Automation |
HP PA 12
Customer | US Hammer |
Description | A part for gasoline engine powered jackhammers |
Process | MJF |
Unit price | $22.18 |
Industry | Construction |
Markforged Onyx - Black
Customer | Autocom Manufacturing |
Purpose | A production part for 3D printed lathe gantry gripper fingers |
Process | FDM |
Unit price | $48.![]() |
Industry | Automotive |
PC Stratasys - white
Customer | Terumo medical corporation |
Purpose | Prototyping parts used for a disposable electrical device |
Process | FDM |
Unit price | $55.38 / $32.96 |
Industry | Medical |
Formlabs Clear Resin
Customer | Aversan Inc |
Purpose | A prototyping part of an injection molded component for an automated door mechanism |
Process | SLA |
Unit price | $29.83 |
Industry | Aerospace |
HP PA 12 - Dyed Black
Customer | True North Design |
Purpose | Structural and vacuum EOAT components |
Process | SLS / MJF |
Unit price | $69.![]() |
Industry | Automotive |
Prototyping PLA
Customer | Allision Conner |
Purpose | End caps and cable strain relief for sheet metal enclosure |
Process | FDM |
Unit price | $7.92 / $4.72 / $2.80 |
Industry | Industrial Automation |
HP PA 12
Customer | US Hammer |
Description | A part for gasoline engine powered jackhammers |
Process | MJF |
Unit price | $22.18 |
Industry | Construction |
Markforged Onyx - Black
Customer | Autocom Manufacturing |
Purpose | A production part for 3D printed lathe gantry gripper fingers |
Process | FDM |
Unit price | $48.![]() |
Industry | Automotive |
PC Stratasys - white
Customer | Terumo medical corporation |
Purpose | Prototyping parts used for a disposable electrical device |
Process | FDM |
Unit price | $55.38 / $32.96 |
Industry | Medical |
Formlabs Clear Resin
Customer | Aversan Inc |
Purpose | A prototyping part of an injection molded component for an automated door mechanism |
Process | SLA |
Unit price | $29.83 |
Industry | Aerospace |
HP PA 12 - Dyed Black
Customer | True North Design |
Purpose | Structural and vacuum EOAT components |
Process | SLS / MJF |
Unit price | $69.![]() |
Industry | Automotive |
Prototyping PLA
Customer | Allision Conner |
Purpose | End caps and cable strain relief for sheet metal enclosure |
Process | FDM |
Unit price | $7.92 / $4.72 / $2.80 |
Industry | Industrial Automation |
HP PA 12
Customer | US Hammer |
Description | A part for gasoline engine powered jackhammers |
Process | MJF |
Unit price | $22.18 |
Industry | Construction |
Markforged Onyx - Black
Customer | Autocom Manufacturing |
Purpose | A production part for 3D printed lathe gantry gripper fingers |
Process | FDM |
Unit price | $48.![]() |
Industry | Automotive |
PC Stratasys - white
Customer | Terumo medical corporation |
Purpose | Prototyping parts used for a disposable electrical device |
Process | FDM |
Unit price | $55.38 / $32.96 |
Industry | Medical |
Formlabs Clear Resin
Customer | Aversan Inc |
Purpose | A prototyping part of an injection molded component for an automated door mechanism |
Process | SLA |
Unit price | $29.83 |
Industry | Aerospace |
HP PA 12 - Dyed Black
Customer | True North Design |
Purpose | Structural and vacuum EOAT components |
Process | SLS / MJF |
Unit price | $69.![]() |
Industry | Automotive |
Prototyping PLA
Customer | Allision Conner |
Purpose | End caps and cable strain relief for sheet metal enclosure |
Process | FDM |
Unit price | $7.92 / $4.72 / $2.80 |
Industry | Industrial Automation |
HP PA 12
Customer | US Hammer |
Description | A part for gasoline engine powered jackhammers |
Process | MJF |
Unit price | $22.18 |
Industry | Construction |
Markforged Onyx - Black
Customer | Autocom Manufacturing |
Purpose | A production part for 3D printed lathe gantry gripper fingers |
Process | FDM |
Unit price | $48.![]() |
Industry | Automotive |
PC Stratasys - white
Customer | Terumo medical corporation |
Purpose | Prototyping parts used for a disposable electrical device |
Process | FDM |
Unit price | $55.38 / $32.96 |
Industry | Medical |
Formlabs Clear Resin
Customer | Aversan Inc |
Purpose | A prototyping part of an injection molded component for an automated door mechanism |
Process | SLA |
Unit price | $29.83 |
Industry | Aerospace |
HP PA 12 - Dyed Black
Customer | True North Design |
Purpose | Structural and vacuum EOAT components |
Process | SLS / MJF |
Unit price | $69.![]() |
Industry | Automotive |
Prototyping PLA
Customer | Allision Conner |
Purpose | End caps and cable strain relief for sheet metal enclosure |
Process | FDM |
Unit price | $7.92 / $4.72 / $2.80 |
Industry | Industrial Automation |
HP PA 12
Customer | US Hammer |
Description | A part for gasoline engine powered jackhammers |
Process | MJF |
Unit price | $22.18 |
Industry | Construction |
Markforged Onyx - Black
Customer | Autocom Manufacturing |
Purpose | A production part for 3D printed lathe gantry gripper fingers |
Process | FDM |
Unit price | $48.![]() |
Industry | Automotive |
PC Stratasys - white
Customer | Terumo medical corporation |
Purpose | Prototyping parts used for a disposable electrical device |
Process | FDM |
Unit price | $55.38 / $32.96 |
Industry | Medical |
Formlabs Clear Resin
Customer | Aversan Inc |
Purpose | A prototyping part of an injection molded component for an automated door mechanism |
Process | SLA |
Unit price | $29.83 |
Industry | Aerospace |
Instant, online 3D printing quotes
-
Upload a CAD to start (STEP, STP, IGES, IGS, SLDPRT, 3DM, SAT, STL, OBJ or X_T)
-
Price updates in real-time as you change materials, lead time, etc.
.
-
No hidden costs. Our instant quotes are not just indications, but the actual price, and include shipping and customs up front.
Learn about how our quoting algorithm works
Our ordering process
Receive instant quote
Upload your CAD to our online quoting platform
Confirm specs
Configure your part specifications and select a lead time that suits your schedule
Production
We select the best manufacturer for your order, and production begins immediately
Quality control
We take full responsibility for making sure your parts are manufactured according to our standards
Delivery
Our 3D printing service has been rated 4.9/5
Over 315 customers are satisfied with our 3D printing service.
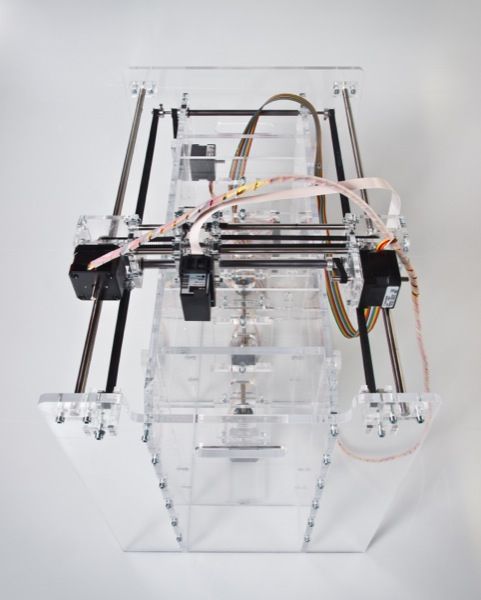
“Amazing service and incredibly fast delivery. I was super happy and surprised when I came home to the package already printed in such short time. High recommended!”
“The print was very well done and completed quickly. I will use this company again in the future.”
“Great turnaround time and prompt replies!”
“Great communication, fast pickup. Great transaction.”
“Excellent product, communication and quality.”
“Good results, quality as expected, communication was fast and technically very competent. ”
“Happy with the service, first time using, was not disappointed.”
“The prints came out fantastic, very smooth and crisp. He kept me updated every step of the way. Thank you again!”
“Very Helpful as always! Great Parts! Would Highly Recommend!”
“Very straightforward print, no issues, great print quality!”
“Delivered in time and the quality is good.”
“Great service. Fast turnaround and parts quality great and as expected. ”
“Great service provider. Went above the call of duty. Highly recommended. ”
“Good communication, fast and ressourceful. Highly recommended.”
“Parts came out great and super fast, great experience. Would order from John again.”
“No issues, quick print time. Easy to deal with. ”
“Great prints! Everything was well done. Thanks!”
“Everything works well, thanks for the backup. Will print again with you guys in the future.”
“Prints were completed very quickly. Responsive and helpful when I had questions. Great service!”
“Thanks for your service. The part fit perfectly for my project. Now I'm convinced to get my own 3D printer.”
“Great turn around time, product much like the photos.”
“Very helpful at every step. Fast printing and delivery. Prints turned out wonderfully. ”
“It arrived almost on time, and was a fine quality”
“Printed 4 times through communitaion and feedback without change the price. Can't appreciate more. ”
“Thank you, amazing service you provide. ”
Show more reviews
Show less reviews
Teams build better parts
Create your Hubs team and start collaborating
Read more
The Hubs Standard - consistent quality, every time
Hubs takes the stress out of manufacturing by guaranteeing the quality and consistency of every part. Each order is dimensionally and visually inspected to make sure it meets the Hubs Standard.
3D printing materials
We can generate instant 3D printing quotes for 25+ plastics. For metal 3D-printed parts, you can request a quote from our parent company, Protolabs.
Available materials
SLS
PA 12 Glass filled PA 12
Desktop FDM
Prototyping PETG Prototyping ASA Prototyping TPU Prototyping ABS Prototyping PLA
Desktop SLA
Formlabs Standard Resin Formlabs Clear Resin Formlabs Tough Resin 2000 Formlabs Rigid Resin 4000 Formlabs Grey Pro Resin Formlabs Flexible Resin 80A Formlabs High Temp Resin Formlabs Durable Resin
MJF
HP PA 12 Glass filled HP PA 12
Industrial FDM
Markforged Onyx ABSplus Stratasys ULTEM 9085 Stratasys Stratasys ASA ABS M30 Stratasys ULTEM 1010 Stratasys
Industrial SLA
Accura 25 (PP-like) Accura ClearVue Accura Xtreme White 200 (ABS-like)
3D printing locations near Markham
Oshawa Markham Toronto
Peterborough, Canada Mississauga Barrie
Brampton Oakville Amherst, NY
Buffalo, NY
The 3D Printing Handbook
No one understands 3D printing like us - our founders literally wrote the book. Click here to download the sample chapters.
Buy the book from Amazon
FAQ's
How much does your 3D printing service cost?
The cost of your 3D printed parts depends on factors such as part volume, part complexity, choice of material, which 3D printing technology is used, and if any post processing is required. For more details on these cost factors, see our article on the cost of 3d printing. To check the cost of your 3D printed part, simply upload a CAD (.STL) file and select your material and 3D printing technology to receive a quote within seconds.
How do you guarantee the quality of my prints?
Your parts are made by experienced 3D printing shops within our network. All facilities are regularly audited to ensure they consistently meet the Hubs quality standard. We include a standardized inspection report with every order and offer a First Article Inspection service on orders of 100+ units.
We have partners in our network with the following certifications, available on request: ISO9001, ISO13485 and AS9100.
Follow this link to read more about our quality assurance measures.
How do I select the right 3D printing process for my prints?
You can select the right 3D printing process by examining which materials suit your need and what your use case is.
By material: if you already know which material you would like to use, selecting a 3D printing process is relatively easy, as many materials are technology specific.
By use case: once you know whether you need a functional or visual part, choosing a process is easy.
For more help, read our guide to selecting the right 3D printing process. Find out more about Fused Deposition Modeling (FDM), Selective Laser Sintering (SLS), Multi Jet Fusion (MJF) and Stereolithography (SLA).
How can I reduce the cost of my 3D prints?
In order to reduce the cost of your 3D prints you need to understand the impact certain factors have on cost. The main cost influencing factors are the material type, individual part volume, printing technology and post-processing requirements.
Once these have been decided, an easy way to further cut costs is to reduce the amount of material used. This can be done by decreasing the size of your model, hollowing it out, and eliminating the need for support structures.
To learn more, read our full guide on how to reduce the cost of 3D printing.
Where can I learn more about 3D printing?
Our knowledge base is full of in-depth design guidelines, explanations on process and surface finishes, and information on how to create and use CAD files. Our 3D printing content has been written by an expert team of engineers and technicians over the years.
See our complete engineering guide to 3D printing for a full breakdown of the different 3D printing technologies and materials. If you want even more 3D printing, then check out our acclaimed 3D printing handbook here.
We have an extensive range of online resources developed to help engineers improve their capabilities.
Introductory guides
Design guides
Material guides
Applications
CAD & file preparation
Post processing & finishing
Our other manufacturing capabilities
CNC machining
CNC machining
Milling (3-, 4- & full 5-axis), turning and post-processing
-
50+ metals and plastics & 10 surface finishes
-
Tolerances down to ±.0008” (0.020 mm)
-
Lead times from 5 business days
See our CNC machining services
Put your 3D printed parts into production today
Get an instant 3D printing quote
462 Forbidden Region - DOSarrest Internet Security
462 Forbidden Region - DOSarrest Internet Security
|
|||||
|
3D-printing
Subscribe to the author
Subscribe
I do not want
25
Anyone who spent some time with a desktop 3D printer, familiar with the concept of support . If you are working with a complex model that has overhanging elements, it is often necessary to print supports from the base material. Unfortunately, supports can be difficult to remove and often leave marks on the finished model that need to be removed.
In an effort to improve the situation, Tumblebeer (User from the prusaprinters.org forum) has come up with a very unique approach that we think certainly deserves closer scrutiny. This does not eliminate the need for the support material, but makes it much easier to remove. This method is cheap, relatively easy to implement, and doesn't require multiple extruders or switching multiple filaments, as is the case with something like water-soluble supports.
The trick is to use the permanent marker as a spacer between the top of the support and the print area it actually touches. The marker coating prevents the two surfaces from fusing while providing the physical support needed to prevent the model from sagging or breaking.
To test this concept, the Tumblebeer fitted a Prusa i3 MK3S with a marker holder that hangs from the side of the extruder assembly. The coil is powered by the GPIO pins of a Raspberry Pi running OctoPrint and enabled by a custom command in the G-code file. It keeps the marker out of the way during normal printing and lowers it when it's time to lay down the interface cover.
Tumblebeer says that this method requires a bit of manual coding, and that some automated G-code scripts or custom slicer plugins can make this process much easier. We are very interested in further development of this concept in the community, as it seems to have significant potential. Having a marker tied to the side of the extruder may sound complicated, but it's nothing compared to switching filament on the fly.
Video Demonstration of the method:
Article author: Tom Nardi
Link to the post Tumblebeer on the Peni forum: TITS
Author of the translation: I and Googol
even more interesting articles
9000 BRTV6666 Loading
10/16/2022
2278
9
Subscribe to the author
Subscribe
Don't want
Hello my friend! Today I decided to assemble a simple pneumohydraulic generator or Generator . ..
Read more
302
Subscribe to the author
Subscribe
Don't want
Hello dear community!
If the experiment was successful, then something is wrong here...
Read more
261
Subscribe to the author
Subscribe
Don't want
I continue the series of articles started with the part devoted to polymers.
This part will focus on...
Read more
Metal 3D printing on a home 3D printer. Technologies today and near future
While consumer 3D printing has become simple and inexpensive enough for home use, and the range of consumables is growing by leaps and bounds, there remains one area that has not reached its full potential. It's about metal 3D printing.
Actually, no one can be surprised by metal printed products. Enthusiasts and professionals are aware of the possibilities of technologies such as selective laser sintering or electron beam melting. These methods make it possible to create three-dimensional metal models that are practically indistinguishable from cast or stamped parts, but often surpass their traditional counterparts in lightness and affordability, although somewhat inferior in strength.
Unfortunately, the above technologies require the creation of complex, expensive devices with considerable dimensions. Worse, consumables are scarce and often quite expensive, since sintering and smelting methods require the use of powdered materials produced in relatively small quantities.
What are the prospects for 3D metal printing with the now-familiar extrusion printers?
Let's start with the fact that it was extrusion printers, that is, devices that print by layer-by-layer deposition (FDM), and became the first 3D metal printers. The existing technology allows the use of a mixed material of metal particles and a binder. The finished model may look like a metal product, but will not have the appropriate mechanical characteristics. As an option, it is possible to fire the finished model for sintering metal particles or, more typically, for melting a binder material with simultaneous impregnation with a relatively low-melting metal or alloy, such as bronze. Naturally, the finished product will not differ in the strength of cast analogues, and the process itself requires the use of special pottery kilns, which leads to an increase in the cost of technology.
Metal model example,
In general, this method is well suited for creating models that are not designed for high mechanical loads and do not require high wear resistance - for example, jewelry. The demand for such metal 3D printers is quite high, with several promising metal clay printers currently under development, including the Mini Metal and Newton 3D. A real breakthrough would be the ability to 3D print finished metal products using FDM technology alone. However, the capabilities of existing extrusion devices are quite limited.
Problems are constructive. To begin with, the temperature of the extruder rarely exceeds 300°C, and the extruders themselves are often made of aluminum with a melting point of about 650°C. Of course, this excludes the possibility of printing with steel, titanium or any other refractory metals and alloys. On the other hand, extruders, in turn, can be made of refractory materials in order to increase the operating temperature range. Among enthusiasts, even the possibility of ceramic printheads is being considered.
The second problem is the background temperature. Although, in general, an increased temperature in the build chamber is welcome, the heat radiation near the extruder when trying to print with refractory metals can be high enough to damage plastic parts and wiring in the printer itself.
The third challenge is to ensure that the consumable heats up fast enough to extrude on time.
Finally, the use of metal as a consumable can lead to heavy clogging of the extruder. If cleaning the print head from hardened plastic is a headache, then cleaning from hardened aluminum or steel can be overwhelming.
Until now, attempts to print with homogeneous metal or alloys have been limited to low-melting materials such as solder or pure tin. The results can hardly be called successful. Even such fusible materials quickly clogged the nozzle and also caused increased wear: according to the testers, the diameter of the aluminum nozzle increased from 1 mm to 2 mm after passing 500 grams of solder used during the experiment. Nevertheless, some progress at minimal cost is evident.
An illustration of an amateur tin extrusion experiment. According to the developers, Scott and Zack Vader, their device is capable of extrusion printing with aluminum. Only one simple fact is alarming - the developers did not provide a single sample of printed models, and later admitted that the device does not yet have a suitable extruder. At the same time, the designers make bold statements: the maximum resolution will be 50 microns, and it will be possible to buy a 3D metal printer for “only” $10,000. Well, let's wait and see.
Printer "for metal printing" is. There is no extruder.
As it turns out, everything is not so simple
However, the development of metal printing methods continues on an industrial scale. Developers at the University of Texas at El Paso have received over $2 million in funding to build the world's first closed-loop 3D printing production line. The goal of the project is to create a device capable of creating high-tech devices, including unmanned aerial vehicles. One of the features of the system will be the possibility of automatic mechanized installation of finished electronic components and the manufacture of electrical wiring.
Hybrid Fab - prototype 3D printed production line
Of course, wiring printing involves 3D printing with metal, and even in combination with plastic and ceramics. Even the most advanced industrial laser sintering systems are not capable of producing heterogeneous objects due to the nature of the technology. You can print with metal, you can print with plastic, but not at the same time. NASA is currently working on EBFȝ technology, which combines elements of electron beam melting and extrusion printing, which may allow practical printing of composite structures, but this technology promises to remain inaccessible to the layman due to its high complexity and cost. On the other hand, if the developers at the University of Texas at El Paso achieve positive results, then a real revolution could happen in the world of 3D printing: the combination of plastic and metal printing could lead to affordable printers capable of printing electronic components.
The technology under development is based on a new consumable supply system optimized for the use of metals. The extruder is equipped with a special heating element of a large length, which allows melting the metal before it is fed to the nozzle, and thermal insulation avoids damage to the structure of the device. And although printing with steel or titanium is likely to remain beyond the capabilities of this technology, stable printing with copper or aluminum can already be considered a breakthrough. In principle, even if the new metal printing technique does not justify itself, the project still has a chance of success, because the main goal is to create a production complex that obviously uses some ready-made components. Nevertheless, one would like to hope for the complete success of the development, including printing on metal.
Expectations are high as the developers have already provided concrete examples of their work. The results shown are still very far from the resolution required for microchip printing, but a start has been made. If the technology is successful, it will at least be possible to manufacture electromechanical components, such as the stepper motors used to drive extruders, work platforms and fans. In this case, it will be possible to create full-fledged RepRap devices - self-replicating 3D printers. Remarkably, the main partner of scientists in the development of the experimental production line is Stratasys, one of the pioneers and current leaders in the 3D printing market. An interesting point was the fact that Stratasys did not invest in the development or acquisition of laser or electron beam sintering technologies. It is possible that Stratasys sees the development of FDM-based metal 3D printers as more promising.
Parallel to the development of FDM 3D printing, an open project is developing to adapt electron beam melting technology for domestic use, called MetalicaRap. For now, consumer and semi-professional metal 3D printing will remain limited to the creation of composite materials based on metal chips with the possibility of additional heat treatment to create all-metal models. And although such products are inferior in strength to cast products, enthusiasts still have a pleasant opportunity in the arsenal that is inaccessible to expensive industrial devices - the ability to print multi-colored metal-based models, because the color of polymer fillers is easy to change.