3D printing heated chamber
Bringing High Temperature 3D Printing To The Masses
Despite the impressive variety of thermoplastics that can be printed on consumer-level desktop 3D printers, the most commonly used filament is polylactic acid (PLA). That’s because it’s not only the cheapest material available, but also the easiest to work with. PLA can be extruded at temperatures as low as 180 °C, and it’s possible to get good results even without a heated bed. The downside is that objects printed in PLA tend to be somewhat brittle and have a low heat tolerance. It’s a fine plastic for prototyping and light duty projects, but it won’t take long for many users to outgrow its capabilities.
The next step up is usually polyethylene terephthalate glycol (PETG). This material isn’t much more difficult to work with than PLA, but is more durable, can handle higher temperatures, and in general is better suited for mechanical parts. If you need greater durability or higher heat tolerance than PETG offers, you could move on to something like acrylonitrile butadiene styrene (ABS), polycarbonate (PC), or nylon. But this is where things start to get tricky. Not only are the extrusion temperatures of these materials greater than 250 °C, but an enclosed print chamber is generally recommended for best results. That puts them on the upper end of what the hobbyist community is generally capable of working with.
But high-end industrial 3D printers can use even stronger plastics such as polyetherimide (PEI) or members of the polyaryletherketone family (PAEK, PEEK, PEKK). Parts made from these materials are especially desirable for aerospace applications, as they can replace metal components while being substantially lighter.
These plastics must be extruded at temperatures approaching 400 °C, and a sealed build chamber kept at >100 °C for the duration of the print is an absolute necessity. The purchase price for a commercial printer with these capabilities is in the tens of thousands even on the low end, with some models priced well into the six figure range.
Of course there was a time, not quite so long ago, where the same could have been said of 3D printers in general. Machines that were once the sole domain of exceptionally well funded R&D labs now sit on the workbenches of hackers and makers all over the world. While it’s hard to say if we’ll see the same race to the bottom for high temperature 3D printers, the first steps towards democratizing the technology are already being made.
Engineering Challenges
Put simply, a machine that supports these so-called engineering plastics needs to be an amalgamation of a traditional 3D printer and an oven. But of course, therein lies the problem. The printer itself, especially of the type and quality that we’ve become accustomed to at the desktop level, wouldn’t survive in such an environment. For a consumer 3D printer to successfully produce parts in PEI and PEEK, it would need to be extensively modified; which is exactly what NASA did with a LulzBot TAZ 4 back in 2016.
LulzBot TAZ 4 modified for high temperature printing.
The first step was building an insulated enclosure that could fit around the TAZ 4, and installing an array of 35 watt infrared heating lamps inside of it. Naturally the machine’s exposed electronics would overheat in such an environment, so they had to be relocated to the outside of the box.
The stepper motors would overheat as well, but rather than trying to move them, the team at Langley Research Center opted to design cooling jackets to fit over each motor through which pressurized air could be circulated.
Like other desktop 3D printers, the TAZ 4 also utilized a number of printed parts in its construction. Printed in ABS , these parts would have quickly failed inside the heated chamber meant to support PEEK. The parts were reprinted in PC, but even this material wasn’t resilient enough for permanent use. So in classic RepRap tradition, the team printed the third and final set of parts on the modified printer itself in a form of PEI known commercially as Ultem.
Somewhat surprisingly, the team had little trouble upgrading the TAZ 4 with a hotend and nozzle that could extrude plastics at up to 400 °C. The popular E3D-v6 hotend costs less than $100 USD and was found to be capable of reaching these temperatures, though the team did need to replace its thermistor with a higher-rated model and make some adjustments to the printer’s Marlin firmware to allow it to reach temperatures that under normal circumstances would trigger a thermal shutdown.
Ultimately, the NASA report concluded that the modifications to the LulzBot TAZ 4 were a complete success. They noted that attempting to print PEI with the IR heating lamps off lead to serious print issues such as warping and delamination, though this was to be expected. No final dollar figure is given for the cost of the modifications, but considering the base price of a TAZ 4 was approximately $2,200 USD at the time, the entire project was likely 1/10th the cost of comparable commercial offerings.
Starting from Scratch
NASA’s experiment showed that it was possible to modify an existing open source desktop 3D printer to print high temperature engineering plastics, and they even showed it could be done relatively economically. But nobody would say that bootstrapping this way was an ideal solution. There was too much duplicated effort involved in the conversion, as the engineers had to specifically undo design choices originally made by LulzBot. Even so, the experiment did create a valuable baseline for other projects that want to start from scratch.
Just last month, a team from the Michigan Technological University unveiled Cerberus, an open source high temperature 3D printer capable of producing parts in PEI and PEKK that can be built for just $1,000 USD. Rather than attempting to adapt an existing design, the team started from the ground up with high temperature printing in mind. All of the sensitive electronic components are mounted well away from the sealed build chamber, which uses a mains-powered 1 kW space heater core to rapidly bring it up to operating temperature.
Crucially, all of the stepper motors have also been moved outside of the build chamber. While this does make the kinematics somewhat more complex than what you’d see in a traditional desktop 3D printer, it means the Cerberus doesn’t need a dedicated motor cooling system like NASA’s modified TAZ did.
A simplified design combined with the use of off-the-shelf control electronics including the Arduino Mega 2560 and RAMPS 1.4 board, and the same E3D-v6 hotend used on the modified TAZ 4, puts the Cerberus well within the means of the motivated hobbyist. Especially since the team has provided clear and detailed assembly instructions for their printer, something notably missing from NASA’s report.
Expanding Possibilities
Between NASA’s TAZ 4 retrofit and all-new designs such as the Cerberus, it’s clear that the technical capability to print PEI and PEEK objects in the home workshop is there for anyone who wants it badly enough. It’s not quite as easy as buying a $200 3D printer on Amazon yet, but if the demand is there, more low-cost machines based on these core principles will certainly start hitting the market. It’s really not much different than the current wave of affordable laser cutters that have been taking over makerspaces these last few years.
Makers all over the globe have been printing PPESo, is there a demand for them? This time last year, the answer might have been different. But with the world still combating the COVID-19 pandemic, there’s a new demand for rapidly produced personal protective equipment (PPE) that nobody could have anticipated.
As explained in the documentation for Cerberus, the team at Michigan Technological University was inspired to look into developing an affordable high temperature 3D printer specifically because it could be used to create PPE that would survive heat sterilization. Rather than being disposable, the team believes items such as face masks printed in PEKK could be used over the long term.
Printed parts that can be repeatedly sterilized would obviously have other potential medical applications. A portable low-cost machine that can produce these components could potentially save lives in remote areas of the world were rapid access to traditional supplies and equipment may be unavailable.
Critics of 3D printing have often said that the core failing of the machines is that the parts they print are rarely robust enough to be used as anything more than a rough prototype. But when a $1,000 printer can produce parts in aerospace-grade materials, it seems like we’re closer to a manufacturing revolution than ever before.
Open, and enclosed passive/active chamber 3D printers
All plastics, when extruded at high temperature, undergo a shrinkage during cooling which can be between 0.3 % and 4 %. This shrinkage can cause deformations, if the cooling is not smooth and homogeneous, giving rise to problems such as warping, delamination of layers or dimensional deformations of the part.
Material |
% of contraction during cooling |
---|---|
PLA |
0.3 - 0.5 |
PETG |
0.2 - 1.0 |
Nylon 12 |
0. |
Nylon 6-6 |
0.7 - 3.0 |
ABS |
0.7 - 1.6 |
ASA |
0.4 - 0.7 |
PP |
1.0 - 3.0 |
HIPS |
0.2 - 0.8 |
PC/ABS |
0.5 - 0.7 |
Fibre-reinforced nylon |
0.5 - 1.0 |
PEEK |
1.2 - 1.5 |
Fibre-reinforced PEEK |
0.5 - 0.8 |
PVDF |
2. |
Table 1. Percentage shrinkage of various plastics used in FFF 3D printing. Source: SpecialChem.com
To avoid this problem, the temperature around the part should ideally be slightly lower than the material's glass transition temperature (Tg) throughout the printing process, and should be slowly reduced to room temperature after printing.
Material |
Tg (ºC) |
Printing temperature (ºC) |
---|---|---|
PLA |
40 - 60 |
190 - 215 |
PETG |
75 - 85 |
220 - 260 |
Nylon 12 |
55 - 65 |
260 - 290 |
Nylon 6-6 |
75 - 85 |
255 - 280 |
ABS |
90 -100 |
220 - 240 |
ASA |
90 - 100 |
240 - 260 |
HIPS |
80 - 90 |
210 - 240 |
PC/ABS |
100 - 150 |
270 - 285 |
PEEK |
140 -160 |
380 - 400 |
PEI |
190 - 210 |
350 - 400 |
Table 2: Tg and printing temperature of various filaments.

Those materials that suffer low shrinkage rates (less than 0.5%) do not require heating the part environment, as the shrinkage effects are practically negligible, so they can be printed perfectly well on open 3D printers, even large parts. These materials are mainly PLA and most PETg filaments (but not other copolyesters such as PET or CPE), as well as their derivatives.
It is possible to print materials with higher shrinkage percentages on open printers, however this possibility is limited to small parts, so with this type of materials it is advisable to use closed printers or printers with an active heated chamber.
Image 1: An open 3D printer. Source: Prusa3D
Open printers are mainly recommended for printing PLA, PETg and flexible filaments.
Closed printers or printers with a passive heated chamber
Closed printers are those whose printing area is completely enclosed. Some manufacturers use the term passive heated chamber, as they tend to accumulate the heat generated by the printing platform.
The internal temperature that these printers can reach varies greatly from one printer to another depending on the material they are made of, their volume, the temperature of the printing platform, the quality of the insulation and the temperature of the room where they are located. In general, the best quality printers are capable of providing temperatures between 45°C and 65°C at best.
Although these temperatures are not very high, they are close to the Tg of materials such as Nylon, ABS or ASA, making them easier to print and allowing the production of larger parts. Although these types of printers substantially improve the printing of these types of materials, they can fail with large volume parts. These printers are recommended for printing small to medium sized parts in PETg, ABS, ASA, Nylon or HIPS.
Image 2: A 3D printer with a passive heated chamber. Source: Raise3D
In general, it is not advisable to use PLA in this type of printers when they are completely closed, as the heat generated can exceed the Tg of the filament, causing it to soften inside the hotend and cause a jam.
Closed printers with an active heated chamber
These are 3D printers capable of controlling the temperature inside the chamber. They are usually more complex and cost more than the previous ones. They also incorporate high temperature hotends (400 ºC - 500 ºC) and liquid cooling systems.
There are two types: high temperature and low temperature.
Low-temperature heated chamber
Low-temperature active heated chamber printers typically allow controlled maximum temperatures of between 80 ºC and 120 ºC. These printers are designed for the production of high quality, large ASA, ABS, Nylon or PC parts.
Image 3: A 3D printer with a low-temperature heated chamber. Source: 3ntr
Although these types of 3D printers are sometimes advertised as compatible with PEEK, they are not usually compatible with all types of PEEK, only with some low-temperature PEKK, and always limited to small parts.
These types of 3D printers are ideal for producing ABS, ASA, Nylon and PC parts that require good dimensional stability and low deformations, making them the best option when producing technical parts or functional components with these materials.
High temperature heated chamber
In general, they allow temperatures in the range of 160 ºC - 180 ºC to be controlled. These printers are specifically designed for the production of parts in PEEK, PEKK and PEI, so it is not common to use other types of materials. This equipment is expensive and requires specialized and trained personnel for its use.
Image 4: A 3D printer with a high temperature heated chamber.
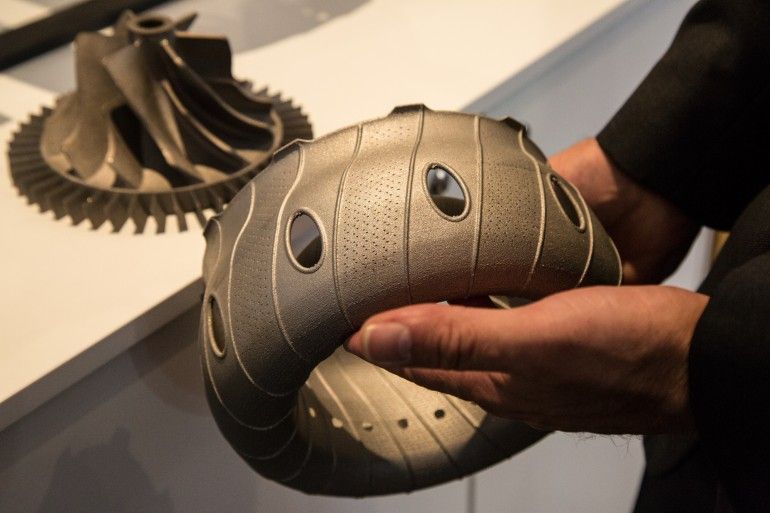
When selecting a type of printer, it is very important to determine beforehand what type of parts and materials will be used.
This guide discusses the concepts in a general way and does not focus on a specific make or model, although they may be mentioned at some point. There may be important differences in calibration or adjustment procedures between different makes and models, so it is recommended that the manufacturer's manual be consulted before reading this guide.
Subscribe to our monthly newsletter and you will receive every month in your email the latest news and tips on 3D printing.
* By registering you accept our privacy policy.
Heating in the print chamber
3D printing
Let's take Nylon as an example. As you know, this is a very capricious plastic in terms of shrinkage and separation from the table. I could not work with him for a long time, I managed to do only small details, and there was no talk of larger ones.
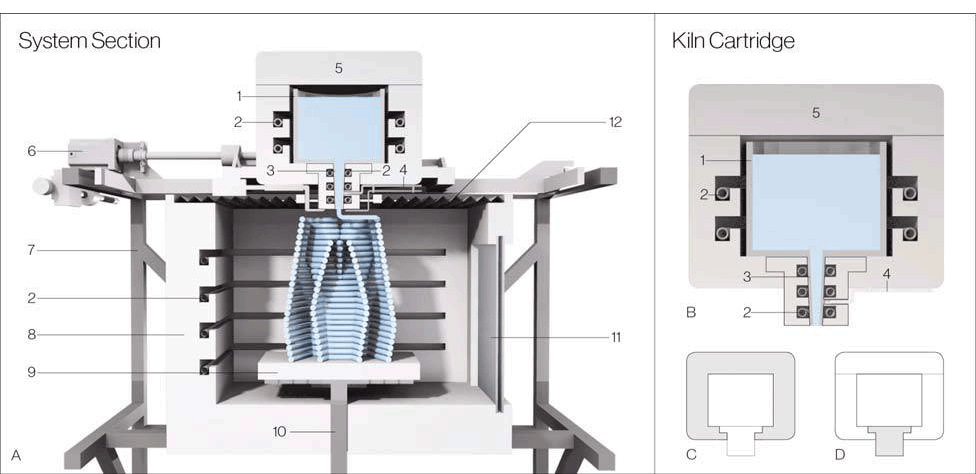
At first I thought about throwing a heater, then a soldering gun for pipes, an iron, etc., but it was not safe, and then I got the idea with a silicone mat, but just throwing it into the camera will not work, because they need something warm. I ordered an abum for 220V and a power of 600W, 200 * 300mm in size, then I began to look for radiators, the whole one costs 1500r more, so I took 6 pieces and assembled them into one. Beauty is not the main thing here, the main thing is that it gives off warmth.
I also ordered a PID controller with a 1300 degree sensor, although it is possible that something else would have come up, but I already bought it. Also a 40A relay with a radiator, in short, everything with a large power reserve.
Then I assembled a plywood box, as they say, I blinded it from what was at hand. I also took 2 80mm 24V fans for blowing. I put a 10mm insulation under the bottom of the rug so that the plywood does not heat up.
Then I lightly varnished it and put it all together. I connected everything to my converted case and that's it.
I fixed the heater on the back wall and that's it. The result is that it heats up just super, it gains 40 degrees in 10 minutes, 50 degrees in 20 minutes, well, it depends on how much you set the heating temperature, the heating rate depends on it. As a result, along with the printer table, the temperature rises rapidly. After a while, it reaches 60, then I stop heating and keep it in these ranges, but I think this is not the limit. Stepper motors work flawlessly.
Now I will try more refractory plastics like PP, PC, PA66-CF-30 and other whimsical plastics. By the way, now Nylon cannot be torn off the table, it sticks very well. I didn’t exactly count the money, but something like this:
Rug 983 rub.
PiD regulator 994 rub.
Radiators 2040r.
Fans 713 rub.
Total: 4730r.
P.S. I do not regret the money spent, as it will quickly pay off thanks to the new printing capabilities.
TEVO Black Widow Table warmer
Subscribe author
Subscribe
Don't want
21
More interesting articles
6
Subscribe to the author
Subscribe
Don't want
Introduction
So, good day to all! This is my second post...
Read more
Leoluch
Loading
09/07/2015
359795
347
Follow the author
Subscribe
Don't want
Good afternoon, dear visitors of the portal.
Today I decided not to leave in art...
Read more
142
Subscribe to the author
Subscribe
Don't want
So the time has come for the second article
I will try to write about everything that I managed to find out in ...
Read more
Overview of High Temperature 3D Printers with Formnext 20170001
We continue to publish materials on the results of the exhibition Formnext 2017 held in Frankfurt am Main. Read a general overview of new products here. Today, we note the significantly increased number of 3D printers since last year for working with high-temperature engineering plastics, starting with polycarbonate and further to polyamides, Ultem, PEEK, PPSU and composites based on them.
These materials are used in the aerospace industry, the chemical industry, and medicine, where properties such as low weight, high temperature resistance, mechanical strength, chemical inertness, and biocompatibility are in demand. We wrote more about engineering filaments and their application here.
Differences between industrial 3D printers
To work with engineering plastics, the printer must have a high temperature extruder. There are two classes of equipment here. Junior - up to 300 ° C, this is enough for modifications of ABS, polycarbonate and polyamides. Senior - above 300 ° C. For PEEK or Ultem you need about 400.
Extruder is not everything. A heated platform or vacuum table is a must to keep the part in place. And printing should take place in a working chamber isolated from the outside world, maintaining a predetermined temperature. Failure to comply with the mode leads to deformation or violation of the integrity of the printed object.
So, let's look at the samples we've seen.
Intamsys
The Chinese manufacturer offers four models of 3D printers. The basic Funmat and Funmat Pro work with common plastics, from PLA to nylon, and composites. Funmat HT and Funmat Pro HT are already capable of printing in PEEK, Ultem and PPSU.
Intamsys FUNMAT, FUNMAT HT
- Working chamber: 260 x 260 x 260 mm;
- layer thickness: from 50 microns;
- nozzle diameter: 0.4mm;
- FUNMAT: extruder up to 280°C, bed up to 150°C;
- FUNMAT HT: extruder up to 450°C, bed up to 160°C.
Compact printers with a closed working chamber, in the HT version it is equipped with heating, maximum temperature 90 °C.
Intamsys FUNMAT PRO, FUNMAT PRO HT
- Working chamber: 450 x 450 x 600 mm;
- layer thickness: from 50 microns;
- nozzle diameter: 0.4mm;
- FUNMAT PRO: extruder up to 280°C, bed up to 150°C, chamber up to 60°C;
- FUNMAT PRO HT: extruder up to 450°C, bed up to 160°C, chamber up to 120°C.
Industrial printers for printing large parts with high-temperature plastics, equipped with a heated working chamber.
ROBOZE
One of the leading companies producing high-temperature 3D printers, we wrote more about it here. Offers three printers for engineering filaments. Roboze One is the basic model for common plastics - from PLA to polyamide inclusive. Roboze One +400 - with a high-temperature extruder, Roboze Argo 500 - a large installation, with a working chamber of 500 x 500 x 500 mm. Roboze printers are interesting in the rejection of drive belts and the use of a rack-and-pinion transmission to move the print head.
Roboze One +400
- Working chamber: 200 x 200 x 200 mm;
- extruder temperature: up to 400 °C;
- layer thickness: from 50 µm.
The printer is designed with an emphasis on reliability, all parts of the extruder are made of metal.
Roboze Argo 500
- Working chamber: 500 x 500 x 500 mm;
- layer thickness: from 50 microns;
- extruder temperature: up to 550 °C;
- chamber temperature: up to 180 °C.
The older Roboze model has a vacuum table to hold the part. Compartments for filament are equipped with heating. When one coil runs out, the machine automatically switches to the next one.
VSHAPER
A Polish manufacturer whose product range includes high-temperature printers for medical applications and five-axis 3D printing machines.
VSHAPER 270 Med
- Working chamber: 270 x 270 x 200 mm;
- extruder temperature: up to 450 °C;
- layer thickness: from 50 µm.
A medical-grade printer with an anti-microbial chamber coating and a built-in UV sterilizer that sterilizes every layer as it prints. The main purpose is the printing of implants and additional equipment for surgical operations.
VSHAPER 5-Axis Machine
- Working area: cylinder 300 mm in diameter and 300 mm high;
- automatic change of hotends;
- heated working chamber;
- the ability to print one model with several materials.
The five-axis design allows complex shapes to be printed without supports. The ability to print one model with several materials with different properties allows you to create parts with complex composition, for example, with an inner core made of a stronger material, or with a coating or inserts made of flexible. For the convenience of printing with different materials, the platform is also optimized - it is divided into cells that can be set to different heating temperatures.
The printer is already available for pre-order, and shipments will begin, according to the manufacturer, from January 2019.
3DGENCE INDUSTRY F340
- Working chamber: 260 x 340 x 340 mm;
- layer thickness: from 150 microns;
- chamber temperature: up to 85 ˚C;
- extruder temperature: up to 500 ˚C.
The printer can be equipped with one of three printing modules. Standard - up to 265 ˚C, medium - up to 350 ˚C, high temperature - up to 500 ˚C. Printed modules - with two hotends, for the main and auxiliary materials. Among other interesting features, we note the preheating of the plastic and the coil mass sensor.
Apium
Apium Additive Technologies GmbH is a German manufacturer of small printers for high temperature PEEK, Ultem and PPSU filaments and composites. Apium is translated from Latin as "celery". For products, support for printing with metal-filled filaments is declared for further baking.
Apium P155
- Working chamber: 155 x 155 x 155 mm;
- extruder temperature: up to 520 °C;
- table temperature: up to 160 °C;
- layer thickness: from 100 µm.
Desktop high temperature printer with a small printable area. It is the successor to the Indmatec HPP 155. Apium also offers a slightly larger model - P220, with a print area of 200 x 160 x 160 mm.
GEWO 3D
The German manufacturer offers one high-temperature printer, with a very serious margin for the heating temperature of the printing platform and the working chamber.
GEWO HTP 260
- Working chamber: 350 x 150 x 165 mm;
- layer thickness: from 20 µm;
- extruder temperature: up to 450 °C;
- table temperature: up to 270 °C;
- chamber temperature: up to 260 °C.
Prints with all common engineering plastics, equipped with two extruders. Possibility of installation of a spindle for machining of a detail is provided.
MiniFactory Innovator 2
- Working chamber: 300 x 160 x 160 mm;
- layer thickness: from 30 µm.
Finnish dual extruder printer, the manufacturer focuses on PEEK printing. Other engineering plastics such as ABS, polycarbonate or Ultem are also supported.
Omni3D Factory 2.0
- Working chamber: 500 x 500 x 500 mm;
- layer thickness: from 140 microns;
- extruder temperature: up to 360 °C;
- table temperature: up to 130 °C;
- chamber temperature: up to 70 °C.
An industrial printer from Poland is equipped with two extruders and can print large parts from ABS, polycarbonate, polyamide and composites based on them.
DynamicalTools DT600
- Working chamber: 600 x 450 x 450 mm;
- layer thickness: from 140 microns;
- extruder temperature: up to 500 °C;
- table temperature: up to 150 °C.
The Spanish printer with two independent printheads, in addition to normal printing, supports printing modes for two identical or mirror parts at the same time. Works with all high temperature filaments up to PEEK, Ultem, PPSU. Equipped with systems for heating plastic and automatic change of coils.
HAGE3D 140L
- Working chamber: 700 x 500 x 400 mm;
- layer thickness: from 50 microns;
- extruder temperature: up to 450 °C;
- chamber temperature: up to 85 °C.
Austrian industrial machine that supports most engineering filaments and composites. Heated working chamber, three-zone heating table.
AIM3D
The company offers a complex of equipment for the manufacture of metal objects. At the first stage, the part is printed on a 3D printer, at the second stage it is placed in an oven, where the binder plastic burns out and the metal filler is sintered.
AIM3D ExAM 255
- Working chamber: 255 x 255 x 255 mm;
- layer thickness from: 20 µm;
- table temperature: up to 120 °C.
The printer does not work with filament, but with granules. This allows the use of raw materials for FDM printing, which are usually used in MIM installations, Metal Injection Molding. You can also print with plastic pellets, which is usually cheaper than using filament.
AIM3D ExSO 90
- workpiece diameter, up to: 90 mm;
- 6-sided heated;
- isolation and collection of fumes generated during sintering;
- temperature: up to 1350 °C.
Furnace for high-temperature sintering of parts printed on AIM3D ExAM 255 in an inert gas atmosphere.
How to purchase an industrial 3D printer
Looking for an industrial 3D printer? Top 3D Shop is the official representative of most of the manufacturers mentioned in the review, we are ready to supply equipment, commissioning, training and maintenance.
We have made a comparison table for these machines, with technical nuances - print and camera temperatures, materials used, number of extruders and estimated cost.