3D printing filament carbon fiber
CarbonX™ PLA+CF 3D Filament | Carbon Fiber Reinforced
$26.95 – $128.00
4 interest-free payments with Learn More
CarbonX™ PLA+CF is made using Natureworks PLA and premium high-modulus carbon fiber. This material offers ease of printing, strength & stiffness, excellent dimensional stability, and an amazing surface finish.
[yith_wcwl_add_to_wishlist]
SKU: Select options above Brand: CarbonX™ Categories: PLA Family, Carbon Fiber Filaments, Sales & Clearance
- Description
- Reviews
- Questions & Support
CarbonX™ PLA+CF is an improved CF reinforced 3D printing filament vs. the competition. Made using High-Modulus Carbon Fiber (not carbon powder or milled carbon fiber). This filament is ideal for anyone that desires a structural component with high modulus, excellent surface quality, dimensional stability, light weight, and ease of printing. Made in the USA using premium Natureworks PLA and high modulus carbon fiber.
PLA is well-known for its incredible ease of printing, stiffness, and extremely high visual print quality. It’s ideal for prototyping, concept models, and end-use printed parts for hobbyists and industry engineers alike!
Extruder Temp
190-220°C
Bed Temp
23-60°C
Heated Chamber
Not required
Nozzle Specs
0.4mm diameter minimum
Hardened Steel Nozzle
Bed Adhesion
Magigoo Bed Prep
Layer Height
0.25mm or higher
Drying Specs
65°C for 4 hours
Supports
Water Soluble Support
Benefits of CarbonX
™ PLA+CF Include:- Ideal for printing without a heated bed, no enclosure required
- Even lower shrinkage and warping, improved by the carbon fiber reinforcement, this PLA prints great on practically any desktop 3D printer
- Very low odor, perfect for 3D printing in home and office environments
- Greatly increased stiffness, modulus, and dimensional stability
- Made from plants, PLA is a renewable biopolymer
- Gorgeous surface quality to make printed parts look beautiful
Filament Specifications:
1. 75mm and 2.85mm +/- 0.05mm in diameter
Recommended Print Settings:
- Extruder: 190-220°C
- Bed Temp: 23-60°C
- Nozzle: We currently recommend a hardened steel nozzle with a minimum diameter of 0.4mm.
- Other: Ideal layer height is 60% of nozzle diameter. We do not recommend printing layers smaller than 0.2mm with carbon fiber reinforced filaments.
- Bed Prep: Magigoo Bed Prep Adhesive gives us the best results
- Heated Chamber: Not required
- Supports: Water soluble AquaTek X1 USM works great for complex parts.
- Drying Instructions: 65°C for 4 hours.
What Is It?
Fibers 5-10 micrometers wide made of carbon. The fibers are aligned following the axis of the material.
This, along with their physical makeup, are what give this material its excellent properties.
What Does It Do?
Carbon Fibers demonstrate a lot of desirable material properties:
- High stiffness
- High tensile strength
- High heat tolerance
- High chemical resistance
- Low weight
- Low thermal expansion
How Does It Work?
Reinforcing plastic with carbon fibers produces a 3D printing filament which exhibits the best properties of both the carbon fibers and the plastic of choice.
What Is It Good For?
Ideal for any applications which require light weight and rigidity.
Carbon fiber reinforced parts, designed to use less material and save weight, is extremely popular in aerospace, civil engineering, the military, and motorsports.
What Is It?
Fibers 5-10 micrometers wide made of carbon. The fibers are aligned following the axis of the material.
This, along with their physical makeup, are what give this material its excellent properties.
What Does It Do?
Carbon Fibers demonstrate a lot of desirable material properties:
- High stiffness
- High tensile strength
- High heat tolerance
- High chemical resistance
- Low weight
- Low thermal expansion
How Does It Work?
Reinforcing plastic with carbon fibers produces a 3D printing filament which exhibits the best properties of both the carbon fibers and the plastic of choice.
What Is It Good For?
Ideal for any applications which require light weight and rigidity.
Carbon fiber reinforced parts, designed to use less material and save weight, is extremely popular in aerospace, civil engineering, the military, and motorsports.
Abrasive Material
This material is particularly abrasive among 3D printing filaments. Users may find standard brass nozzles are chewed through very quickly compared to standard wear and tear. When worn through, the nozzle diameter will widen inconsistently and the printer will experience extrusion issues.
Because of this, it's strongly recommended this material be printed through a hardened steel nozzle rather than a softer metal. Hardened steel nozzles can often be inexpensive and easily installed depending on your printer manufacturer's instructions.
Questions?
Send us a message and we'll reach out as soon as we can!
Please enable JavaScript in your browser to complete this form.
Name *
Business / Organization
Email *
Phone
What can we help you with? *
Newsletter Signup
- Sign me up for the 3DXTECH newsletter
Obsidian Nylon+Carbon Fiber | Markforged ONYX Alternative
$130.00 – $260.00
4 interest-free payments with Learn More
Obsidian™ PA6+CF is an excellent drop-in replacement for Markforged Onyx™ and is compatible for use in all Markforged printers. Obsidian™ delivers excellent performance, appearance, and a significant cost savings.
[yith_wcwl_add_to_wishlist]
SKU: Select options above Brand: Obsidian™ Categories: Carbon Fiber Nylon Family, Nylon 6, Nylon Family, Carbon Fiber Filaments, New Products
- Description
- Reviews
- Questions & Support
Obsidian™ PA6+Carbon Fiber [Markforged ONYX Alternative]
Obsidian™ PA6+CF filament was formulated to be a lower-cost drop-in Markforged Onyx Alternative suitable for all Markforged printers. We developed this material after extensive analysis and testing on our own in-house Markforged printer and many outside beta testers. The result is a seamless printing experience that produces parts with an outstanding appearance and excellent mechanical properties. Made using premium high-modulus carbon fiber and PA6 copolymer, Obsidian™ is an excellent alternative to Onyx™ that allows our customers to save money when using your Markforged printer.
Don’t have a Markforged printer? That’s no problem – Obsidian™ is also compatible with all non-Markforged printers that are suitable for printing PA6+CF. Take advantage of the excellent strength, stiffness, and appearance of this specialty material without over spending on Markforged Onyx™.
Gearbox HT2™ 3D Printer:
Print industrial-grade parts using our Obsidian™ Nylon+Carbon Fiber and more with the new Gearbox™ HT2 High-Temp 3D Printer.
Extruder Temp
265-285°C
Bed Temp
90-110°C
Heated Chamber
Recommended
Nozzle Specs
Hardened Steel Nozzle
Bed Adhesion
Magigoo Bed Prep
Layer Height
0.10mm or higher
Drying Specs
90°C for 4 hours
Supports
Water Soluble Supports
Benefits of Obsidian™ PA6+CF [Markforged Onyx Alternative]:
- Drop-in for Onyx™ without any changes required to print settings
- >30% savings vs. Markforged Onyx™
- Excellent strength and stiffness
- Resistant to aliphatic hydrocarbons (oil/gas/lubricants)
- Superior dimensional stability (low warp/shrink/CTE)
- Compatible with Markforged FX20, X7, X5, X3, Mark Two, Onyx Pro, and Onyx One printers
Filament Specifications:
Diameter: 1.75mm +/- 0.05mm
Markforged Print Recommendations:
- Obsidian™ was formulated to be a drop-in for Onyx™ without any changes to the print settings.
Recommended Print Settings for Non-Markforged Printers:
- Extruder: 265-285°C
- Bed Temp: 90-110°C
- Nozzle: We currently recommend a hardened steel nozzle
- Bed Prep: Magigoo Bed Prep and 3DXTECH Polyimide Tape gives us the best results
- Heated Chamber: Recommended
- Supports: AquaTek™ water soluble X1 USM Universal Support Material is designed to work with complex models
- Drying Instructions: 90°C for 4 hours if the filament exhibits signs of moisture
What Is It?
Fibers 5-10 micrometers wide made of carbon. The fibers are aligned following the axis of the material.
This, along with their physical makeup, are what give this material its excellent properties.
What Does It Do?
Carbon Fibers demonstrate a lot of desirable material properties:
- High stiffness
- High tensile strength
- High heat tolerance
- High chemical resistance
- Low weight
- Low thermal expansion
How Does It Work?
Reinforcing plastic with carbon fibers produces a 3D printing filament which exhibits the best properties of both the carbon fibers and the plastic of choice.
What Is It Good For?
Ideal for any applications which require light weight and rigidity.
Carbon fiber reinforced parts, designed to use less material and save weight, is extremely popular in aerospace, civil engineering, the military, and motorsports.
What Is It?
Fibers 5-10 micrometers wide made of carbon. The fibers are aligned following the axis of the material.
This, along with their physical makeup, are what give this material its excellent properties.
What Does It Do?
Carbon Fibers demonstrate a lot of desirable material properties:
- High stiffness
- High tensile strength
- High heat tolerance
- High chemical resistance
- Low weight
- Low thermal expansion
How Does It Work?
Reinforcing plastic with carbon fibers produces a 3D printing filament which exhibits the best properties of both the carbon fibers and the plastic of choice.
What Is It Good For?
Ideal for any applications which require light weight and rigidity.
Carbon fiber reinforced parts, designed to use less material and save weight, is extremely popular in aerospace, civil engineering, the military, and motorsports.
Abrasive Material
This material is particularly abrasive among 3D printing filaments. Users may find standard brass nozzles are chewed through very quickly compared to standard wear and tear. When worn through, the nozzle diameter will widen inconsistently and the printer will experience extrusion issues.
Because of this, it's strongly recommended this material be printed through a hardened steel nozzle rather than a softer metal. Hardened steel nozzles can often be inexpensive and easily installed depending on your printer manufacturer's instructions.
Questions?
Send us a message and we'll reach out as soon as we can!
Please enable JavaScript in your browser to complete this form.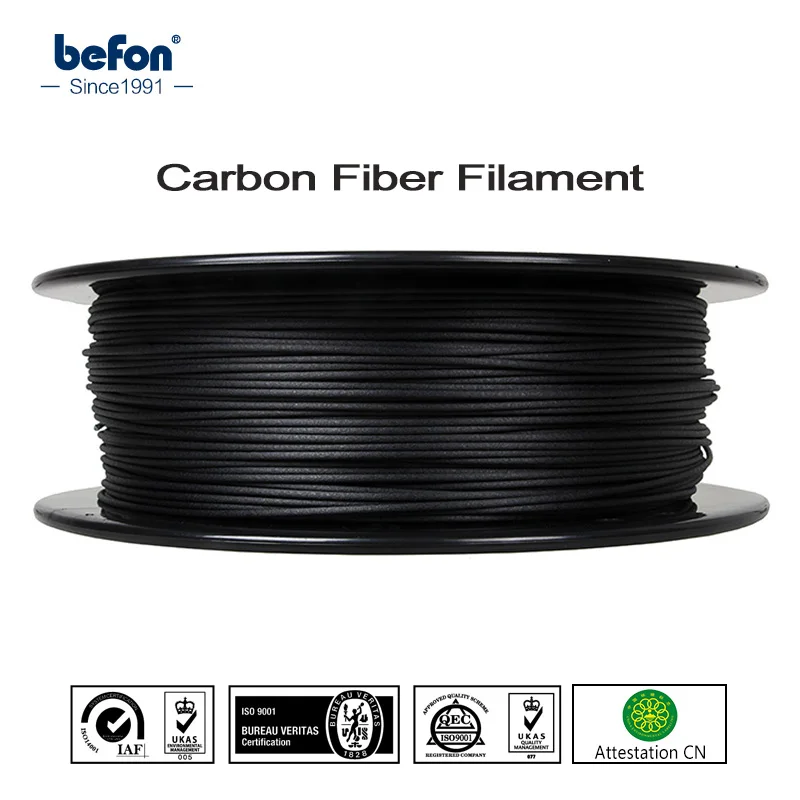
Name *
Business / Organization
Email *
Phone
What can we help you with? *
Newsletter Signup
- Sign me up for the 3DXTECH newsletter
Everything you need to know about 3D printing carbon fiber
First produced by Joseph Swan in 1860, carbon fiber is made up of a long chain of carbon atoms bonded together. The chain is typically 5 to 10 micrometers in diameter and varies in length depending on the application. Over the years, carbon fiber has become popular in many sectors because it offers interesting properties, including high stiffness, high tensile strength, light weight, high chemical resistance, high temperature resistance, and low thermal expansion. Pure carbon fiber is actually five times stronger than steel and twice as stiff but lighter. As you can imagine, these characteristics make carbon fibers suitable for applications in sectors such as aerospace, automotive, military or civil engineering.
As some of you may already know, carbon fibers are rarely used on their own. They are usually combined with other materials to form what we call a composite material - in this particular case, these are materials reinforced with carbon fiber. These composites are made from a matrix material, usually a polymer, although it is possible to use non-polymer materials such as ceramics to which carbon fibers are added. The main advantage is that you end up with a stronger but lighter plastic with a higher level of stiffness.
The body of this bike frame is made of carbon fiber | Source: Arevo
Traditionally, carbon fiber composites have been used for structural design, where added weight results in increased life cycle costs or unsatisfactory performance. Carbon fiber composites can be used to create many products such as bicycle frames, aircraft fenders, propeller blades, automotive components, etc. As you can imagine, given the many benefits of carbon fiber, it is already being used by more than just traditional manufacturing systems. In recent years, more and more 3D printing companies are offering carbon fiber reinforced materials or technologies. They are designed to work with this composite to provide better performance. So how is carbon fiber being used in additive manufacturing?
3D Printing Applications
In its 3D Printing Composites 2020 - 2030 report, IDTechEx reports that the global market for 3D printing composites will reach $1.7 billion by 2030. This figure also includes other composite materials, such as materials reinforced with fiberglass or plastic. However, this trend clearly demonstrates that the 3D printing industry is increasingly using all composites, including carbon, in their manufacturing activities. There are essentially two ways to use carbon fiber in 3D printing, the first is carbon fiber reinforced filaments and the second is continuous carbon fiber reinforcement.
Carbon fiber filament
Carbon fiber filament uses short carbon fibers composed of segments less than one millimeter long, which are mixed with a thermoplastic known as a base material. There are a number of popular filaments available with carbon fiber fill, including PLA, PETG, nylon, ABS, and polycarbonate. These fibers, being extremely strong, cause an increase in the strength and stiffness of the thread, and also reduce its overall weight. The requirements for 3D printing carbon fiber filaments should be the same as for the base material they were added to. The main difference is that fibers can clog 3D printer nozzles, so experts recommend using a hardened steel nozzle. In addition, when a certain threshold of fibers is exceeded, the part printed on a 3D printer loses its surface quality.
Carbon fiber segments embedded in thread for reinforcement | Source: Markforged
Some companies have developed carbon fiber fibers for more technical applications. These yarns use high performance polymers (HPPs) such as PEEK or PEKK as the base material. Consequently, they not only offer the benefits of HPPs such as durability and high mechanical and chemical performance, but also an improved strength to weight ratio. Print settings need to be adjusted as HPPs require extruders that can heat up to 400°C and systems that have heated chambers and build plates. Some of the carbon fiber filament manufacturers are: Roboze, 3DXTech, ColorFabb, Markforged, Kimya, Intamsys, Zortrax, etc.
Continuous carbon fiber reinforcement
Carbon fiber thread is definitely stronger than thread that has not been reinforced. However, to get an even stronger part, another method called continuous carbon fiber reinforcement can be used. Since carbon fiber is not cut into smaller pieces, it retains much more strength. In fact, continuous printing on carbon fiber is strong enough to be half the weight of aluminium. 3D printer manufacturers claim that they can replace metal 3D printing for some applications. And the main advantage is that it is cheaper than metal. Finally, by placing carbon fiber according to DfAM techniques, it is possible to increase the strength of the part while reducing material consumption.
Using DfAM methods, it is possible to strengthen a part using carbon fiber | Source: Anisoprint
There are several players on the market that offer technologies that can continuously print carbon fibers. They can be divided into two main types, depending on when the carbon fiber is added (it can be added before the 3D printing process or during). When added earlier, continuous fiber 3D printing is known as backing prepreg, while when added during extrusion, it is called co-extrusion. In the prepeg technique, you also get a composite thread (or tape), but the carbon fibers have not been cut, instead they have been impregnated with a polymer through a pultrusion process.
Members offering continuous fiber 3D printing include Markforged, Anisoprint, CEAD, etc. More recently, Desktop Metal has also joined the race with a new system called Fiber. Fiber uses Micro Automated Fiber Placement (µAFP). In addition, 9T Labs has developed additive synthesis technology (AFT) to mass-produce carbon composites at a lower cost.
Carbon 3D printing: other technologies
A departure from the better known extrusion process, an interesting technology is the patented AREVO process, based on directed energy deposition technology, in which a laser is used to heat filament and carbon fiber simultaneously as a roller presses them together. Impossible Objects and EnvisionTEC have also added carbon fiber 3D printing systems to their machines, but the technology is slightly different. They weave sheets of carbon fiber using a lamination process. Last but not least, Continuous Composites uses a hybrid technology where a strand of fiber is impregnated with resin and then cured with UV light, similar to SLA 3D printing.
This part demonstrates how continuous carbon fiber 3D printing can increase the strength of a plastic part | Source: Markforged
Source
carbon fiber, composite materials, 3D printing, carbon fiber composites. Additive Manufacturing, PLA, ABS, Polycarbonate, Nylon, 3D Printing Filament, 3D Printer, Anisoprint, Additive Synthesis, 9T Labs, Carbon 3d Printing, 3D SLA
Carbon Fiber 3D Printing Guide: Printers and Materials
Bicycles, racing cars, drones and tennis rackets all have a variety of applications and require high strength and durability without added weight. This combination of properties is typical of carbon fiber composites, which are used in everything from Formula 1 racing car chassis to lightweight road bike frames.
Since many 3D printers commonly use polymer-based materials, including various composites, many people ask the question, "Can a 3D printer print carbon fiber?".
Indeed, there are two methods by which 3D printing can be used to create carbon fiber parts: supporting traditional fabrication methods with 3D printed molds, or direct 3D printing of carbon fiber composites. In this article, we'll look at traditional fabrication methods as well as new workflows for 3D printed carbon fiber molds and direct 3D printed carbon fiber composite parts.
Combining traditional carbon fiber parts with 3D printing
Carbon fiber is a composite material traditionally made by weaving long strands of carbon fibers together and then bonding them with a polymer. The yarns can be woven strategically so that the strength is directed along one specific vector, or so that the final product has multiple strengths in all directions. The resulting material is then molded into the desired end product using one of three processes: wet laid, pre-laminated, or resin transfer molding (RTM).
Wet Laid
Wet laid carbon fiber sheets are cut and pressed in a mould, then dyed with a liquid resin that cures to bind the sheets into the desired final shape. This method requires the least equipment and is the easiest to master for a beginner. Because most of the work can be done by hand, this is one of the cheapest methods, but the trade-off is that the resulting parts are less accurate to the master mold than parts made by other methods.
Prepreg lamination
In this method, the carbon fiber is already impregnated with resin and then placed in a mold that uses pressure and heat to form the final shape. This method is the most expensive due to the need for specialized equipment to store and process the pre-impregnated sheets, as well as a heated and pressurized forming machine. These factors also make it the most repeatable and consistent, and thus the most suitable for serial production of carbon fiber parts.
Resin transfer molding (RTM)
In RTM molding, the dry fiber is inserted into a two-part mold. The mold is clamped, after which high-pressure resin is injected into the cavity. This method is usually automated and is used to produce large volumes of products.
3D printed carbon fiber parts
For each of the previous three methods, 3D printing can be used to reduce costs and improve production times. All three traditional manufacturing methods require the use of a mold or multiple molds, which are traditionally created through labour-intensive subtractive processes such as wood, foam, metal, plastic or wax. 3D printing offers an alternative way to make molds. 3D printed molds are customizable and are more efficient and cost effective for small batch or custom production.
For applications requiring live prototypes, such as the automotive and aerospace industries, the iterative process can require hundreds of different shapes. Producing such iterations with traditional manufacturing methods can be costly and time consuming, so 3D printing provides an efficient way to produce small batches. Although 3D printed molds are not as suitable for high-volume production as metal molds, they can be created in-house, reducing costs, speeding up product development and validation, and short-term production.
Carbon fiber molds can be made in a variety of ways, but the smooth surface and wide choice of materials for SLA 3D printers make them a common choice for mold making in the factory. SLA-created parts have virtually no layer lines or porosity, so carbon fiber sheets can be pressed tightly into the mold without the fear of creating a textured surface.
Panoz, a manufacturer of racing and sports cars, needed a custom race car cabin duct to bleed the air out of the cabin and cool the temperature inside. In collaboration with DeltaWing Manufacturing, they used a Formlabs SLA 3D printer to print a high temperature resin part and then manually molded that printed part using high temperature epoxy for tooling. By using 3D printing, DeltaWing avoided outsourcing the costly metal mold for this custom carbon fiber part, reducing overall costs and delivery times.
Carbon fiber wing duct next to two-piece mold printed with High Temp Resin made by DeltaWing Manufacturing.
Direct Carbon Fiber 3D Printing
Looking for the best carbon fiber 3D printer? There is a strong demand for workflows that combine the strength, durability and wear resistance of traditional carbon fiber parts with the maneuverability, geometric capabilities and cycling of 3D printing. Therefore, it is not surprising that there are many companies offering 3D printing using carbon fiber, with two methods currently available: printing using chopped or continuous fibers.
Chopped Carbon Fiber 3D Printing
Chopped Fiber refers to 3D printing composite plastic materials that are impregnated with small pieces of carbon fibers. These crushed fibers add strength to the composite, which can be carbon fiber filament for FDM modeling or nylon powder for SLS 3D printing.
The main advantages of chopped carbon fiber reinforced materials over other types based on polymers are that they are strong, light, heat resistant and less prone to deformation. Compared to traditionally molded carbon fiber parts, chopped fiber 3D printing provides increased geometric flexibility in part design, especially in SLS 3D printing, potentially eliminating the labor involved with traditional molding or opening up innovative new opportunities for users to incorporate this material into the working process.
The Formlabs Fuse 1+ 30W SLS 3D Printer enables this type of carbon fiber 3D printing with Nylon 11 CF Powder, the strongest material in the Formlabs SLS material library. Fuse 1+ 30W is the most affordable high performance SLS printing option for shredded carbon fibers. Although traditional industrial SLS machines also offer some carbon fiber materials, the initial implementation costs negate much of the added value of 3D printing carbon fiber parts over RTM or prepreg lamination methods.
Formlabs Nylon 11 CF Powder is strong, lightweight and heat resistant making it ideal for the automotive, aerospace and manufacturing industries .
Many FDM 3D printers can handle carbon fiber filaments, but these materials are more difficult to print than standard ABS or PLA filaments, resulting in more clogs and more maintenance as the brass nozzles wear out. FDM 3D printers specifically designed to grind carbon fiber filaments are also available but are more expensive.
The main limitation of chopped-fiber printed parts using both SLS and FDM technologies is that they should be considered as more durable 3D printed parts, rather than a true alternative to traditional woven and continuous carbon fiber parts. fibers. They also provide the greatest increase in strength by positioning them in the X-plane direction for SLS printing, and in the XY-plane direction for FDM printing. Traditional methods of creating carbon fiber parts provide multidirectional strength through careful planning and placement of different carbon fiber sheets in a preform.
Continuous Carbon Fiber 3D Printing
Continuous Carbon Fiber 3D Printing is available on some dedicated FDM 3D printers and produces parts that are close in strength to traditional carbon fiber parts but similar to chopped fiber printers FDM, only in the XY plane. In such printers, continuous filaments of carbon fiber are mixed with a thermoplastic and the filaments can be applied strategically to selectively pressurize certain planes or axes. This method can use either a dual extruder nozzle to lay down a combination of carbon fiber and polymer filaments, or a 2-in-1 in which one nozzle lays down the carbon fiber filaments and the other heats and extrudes the filament.
Continuous carbon fiber 3D printing offers an alternative comparable to traditional molded carbon fiber parts, albeit with limited design freedom. While these parts are incredibly strong, strength only appears in the XY planes and the models must be oriented so that their strength matches the direction of the applied force. In designs where possible, this method can be used to replace aluminum parts, as well as to create durable manufacturing aids or end-use parts.
Applications for 3D printed carbon fiber parts
The high strength, light weight, and impact, heat and chemical resistance of carbon fiber printed parts make them ideal for a variety of applications where 3D printing has never been before. was not considered. Now, these plastic and carbon fiber composite parts can withstand the heat generated by automotive or aerospace engine components, be used as a replacement for machined aluminum parts and manufacturing fixtures, and produce durable and impact-resistant equipment.
3D printed carbon fiber parts are ideal for rapid prototyping, the production of wear-resistant and durable manufacturing fixtures such as tooling and fixtures, and for low-volume production of durable end-use parts with complex geometries.
3D printing technology has opened up new possibilities in design and manufacturing, and 3D printing of carbon fiber composites has further expanded these possibilities, allowing users in the automotive, aerospace, defense, and manufacturing industries to quickly and efficiently produce high-strength, heat-resistant, geometrically flexibility. By bypassing traditional machining or molding processes, these users can more easily create custom parts, replacement parts and functional prototypes. Although carbon fiber printed parts are not a complete replacement for traditional technologies due to the single plane of added strength, they are still stronger than almost all other plastics, making them exceptionally useful in many applications.