3D metal printer desktop
Studio System™ | Desktop Metal
_Studio System™ applications
Studio System™ applications span a variety of industries including manufacturing, tooling, automotive, consumer, electronics, and oil & gas.
-
Extrusion Die
h23This die is used in the manufacture of extruded plastic framing.
Extrusion Die
-
Size (mm) 74 x 74 x 56
Cost to print ($) 156.00
Cost to machine ($) 329.67
Cost reduction 52.68%
-
Metal 3D printing reduces lead times and costs - allowing for rapid iteration and refinement of the die design.
Furthermore, lower tooling costs and lead times makes low volume custom extrusion dies economically feasible.
-
Rook Chess Piece
316LOne of six types of movable objects used in the game of chess.
Rook Chess Piece
-
Size (mm) 46 x 46 x 72
Cost to print ($) 46.00
Cost to machine ($) 329.67
Cost reduction 52.68%
-
Unique chess piece designs can easily be 3D printed without the long lead times and costs associated with tooling.
The Studio System’s high resolution print head produces small parts with fine features and surface finish.
-
YE6 Burner Tip
316LThis burner tip is used to shape the flame in industrial burners.
YE6 Burner Tip
-
Size (mm) 139 x 139 x 86
Cost to print ($) 193.46
Cost to machine ($) 694.00
Cost reduction 72.00%
-
This burner tip was originally cast in the 1950s, and the tooling has since been lost for it.
When a customer needed a replacement, the quote for new tooling was in the tens of thousands of dollars.
With the Studio System, the company was able to recreate the part with properties similar to the original cast part, with no tooling cost or long lead times for the customer.
-
Putter
17-4 PHCustom designed golf putter is an example of the customization that is possible with 3D printing.
Putter
-
Size (mm) 135 x 92 x 38
Cost to print ($) 128.
00
Cost to machine ($) 2203.00
Cost reduction 94.00%
-
Golf clubs, especially putters, are typically cast or machined. With the Studio System, manufacturers can achieve excellent material properties without tooling or expensive CNC machining.
The Studio System allows for customization of parts like putters, so each player can have a design that is best suited to them. And when those designs go into mass production, they can be manufactured via binder jetting.
-
Flower Nozzle
316LThis flower nozzle is used to atomize fluid in industrial equipment.
Flower Nozzle
-
Size (mm) 123 x 123 x 45
Cost to print ($) 184.00
-
Due to its complex geometry, these parts would typically be cast followed by extensive secondary machining. With the Studio System, the nozzle can be 3D printed without the lead times and setup costs of casting, enabling one-off and small batch orders.
-
Impeller
316LThis impeller is used to control the pressure and flow of fluids in equipment like pumps and compressors.
Impeller
-
Size (mm) 82 x 82 x 28
Cost to print ($) 63.00
Cost to machine ($) 2138.00
Cost reduction 97.05%
-
Their complex vanes make impellers expensive and difficult to manufacture. When a custom impeller is needed metal 3D printing accelerates design optimization and product development by dramatically reducing lead time and cost.
-
Sheet Metal Embosser
4140This custom embosser is used in sheet metal fabrication.
Sheet Metal Embosser
-
Size (mm) 47 x 28 x 15
Cost to print ($) 14.00
-
Sheet metal tools are used for a broad range of fabrication operations, including stamping, bending, countersinking and embossing.
3D printing with the Studio System reduces tool fabrication costs, shortens production run lead time, and enables rapid iteration and refinement of the sheet metal designs and associated tooling.
-
Zipper Mold
h23This part is an Injection mold insert for manufacturing zinc zippers.
Zipper Mold
-
Size (mm) 46 x 27 x 18
Cost to print ($) 16.00
-
3D printing the mold inserts shortens production run lead time and allows rapid iteration and refinement of zipper designs. Using a high resolution printhead allows for smaller parts with finer features, requiring less post processing.
-
Skateboard Truck
17-4 PHThis part attaches wheels to a skateboard deck, and was optimized using generative design tools
Skateboard Truck
-
Size (mm) 201 x 76 x 52
Cost to print ($) 161.
00
Cost to DMLS ($) 1163.00
Cost reduction 86.00%
-
Generative design and 3D printing allows for the fabrication of innovative designs impossible with casting (the traditional production method for skateboard trucks).
The Studio System can print that previously impossible geometry, resulting in trucks that are more aesthetically pleasing, stronger, and lighter.
-
Master Drilling Sun Gear
17-4 PHThis part is a sun gear used in a planetary gearbox for an earth-drilling machine.
Master Drilling Sun Gear
-
Size (mm) 118 x 118 x 118
Cost to print ($) 658.
00
Cost to machine ($) 916.00
Cost reduction 28.17%
-
After exploring a number of alternative manufacturing methods to produce the parts needed to keep crucial machinery up and running, Master Drilling chose 3D printing. The switch to 3D printing cut their lead time for replacement parts from about three months for off-shore castings, to just three weeks printing on-site, thereby reducing downtime for the earth drilling equipment.
-
Mouthpiece Mold
h23Mold insert is used to injection mold medical inhaler mouthpieces.
Mouthpiece Mold
-
Size (mm) 104 x 93 x 48
Cost to print ($) 345.00
Cost to machine ($) 716.77
Cost reduction 51.87%
-
3D printing the hard steel insert to near-net shape eliminates 95% of the required CNC machining and associated tool wear.
Because cooling accounts for 95% of the mold cycle time, the ability to incorporate conformal cooling channels into the mold can reduce mold cycle time and increase throughput.
-
UMC End Effectors
17-4 PHThese grippers are used to fixture and move aerospace forgings on a manufacturing line.
UMC End Effectors
-
Size (mm) 55 x 32 x 16
Cost to print ($) 23.00
Cost to machine ($) 194.00
Cost reduction 88.14%
-
The complex geometry of end effectors requires extensive CNC machining, resulting in long lead times that occupy valuable CNC capacity.
Using metal 3D printing allows for on-demand manufacturing of custom end effectors while lowering part cost and lead time.
-
APG Thread Checker Fixture
17-4 PHThis fixture pushes a thread checker into a part on a manufacturing line.
APG Thread Checker Fixture
-
Size (mm) 47 x 28 x 15
Cost to print ($) 14.00
-
This fixture pushes a thread checker into a part on a manufacturing line.
As a wear item, it needs to stand up to repeated use, and must be easily produced to keep the manufacturing line up.
The fixture must be regularly replaced as it wears out. Printing the part with the Studio System eliminates CNC lead time and frees up the machine shop for more critical work.
-
BattleBots Bot Support
17-4 PHThis part is a structural member for use in the bot's robotic arm.
BattleBots Bot Support
-
Size (mm) 130 x 117 x 64
Cost to print ($) 106.
00
Cost to machine ($) 551.90
Cost reduction 81.00%
-
This support is designed to carry a heavy load and withstand punishment. Engineers working on a bot used on a Discovery Channel program BattleBots had less than a month to produce a custom structural element on robotic arm. Using the Studio system, they were able to print a bracket capable of resisting bending and lateral motion while providing the stiffness, strength, weldability and fire resistance required.
-
APG Chuck Jaws
h23This part is used to hold a workpiece in place during machining lathe operations.
APG Chuck Jaws
-
Size (mm) 84 x 78 x 42
Cost to print ($) 117.00
Cost to machine ($) 426.36
Cost reduction 72.56%
-
These chuck jaws closely match the geometry of the part being machined - making them complex to machine. Printing them using the Studio System eliminates CNC lead time and frees up the machine shop for more critical work.
-
O-Ring End Effector
17-4 PHThis end effector is used to stretch and install O-rings on a hydraulic fitting.
O-Ring End Effector
-
Size (mm) 42 x 13 x 17
Cost to print ($) 7.00
Cost to machine ($) 152.17
Cost reduction 95.40%
-
Small, detailed parts like these end effectors typically require expensive CNC machining and have long lead times. Using the Studio System’s high resolution (250μm) printhead allows manufacturers to print small parts with fine features which would be difficult to machine
-
APG Coining Fixture
h23This fixture is used to achieve critical tolerances on metal injection molded (MIM) parts.
APG Coining Fixture
-
Size (mm) 110 x 57 x 31
Cost to print ($) 92.00
Cost to machine ($) 392.00
Cost reduction 75.63%
-
Fixture like this require custom geometry for each application, as well as superior wear resistance. The faster these parts are manufactured, the quicker a company can get get manufacturing lines running.
Printing these parts with the Studio System eliminates CNC lead time and frees up the machine shop for more critical work.
-
Helical Heat Exchanger
CopperUsed in chemical processing to cool a hot gas as it flows through a pipe.
Helical Heat Exchanger
-
Size (mm) 78 x 64 x 58
Cost to print ($) 443.00
Cost to machine ($) 2138.00
Cost reduction 79.28%
-
This heat exchanger enables a much higher heat transfer rate than a traditionally manufactured part.
Featuring thin external fins and a complex, internal helical cooling channel, this exchanger would not be manufacturable as one component via CNC machining.
The Studio System allows for the complex geometry of the heat exchanger to easily be printed as a single component.
-
UHT Atomizer
316LThis part is a fuel atomizer for a steam boiler on a liquid natural gas (LNG) tanker.
UHT Atomizer
-
Size (mm) 74 x 74 x 71
Cost to print ($) 129.
00
Cost to DMLS ($) 1089.00
Cost reduction 88.00%
-
This 3D printed atomizer features complex internal channels and oblong shaped holes, which could not be manufactured with traditional methods. With the Studio System, the engineers were able to radically redesign their conventional atomizers for significantly better performance.
-
Octopus Ring
316LExample of the unique jewelry that can be customized and scaled for a tailored fit.
Octopus Ring
-
Size (mm) 38 x 38 x 30
Cost to print ($) 14.
00
-
Unique jewelry pieces can be 3D printed without the design lock-in, long lead times and costs associated with tooling. The Studio System’s high resolution print head produces small parts with fine features and surface finish.
-
Lathe Gear
17-4 PHThis part is a replacement gear for vintage (circa 1940) lathe.
Lathe Gear
-
Size (mm) 82 x 82 x 27
Cost to print ($) 58.
00
Cost to machine ($) 260.67
Savings vs. machining 77.70%
-
In some cases, replacement parts are no longer available, either off the shelf or from the OEM. Fabricating custom gears via hobbing and broaching is often prohibitively expensive, but metal 3D printing allows for the fabrication of legacy parts at much lower cost.
-
Tri Manifold
Alloy 625This manifold is used to combine three flows into one common flow.
Tri Manifold
-
Size (mm) 108 x 101 x 98
Cost to print ($) 906.
00
Cost to DMLS ($) 4069.28
Savings vs. machining 77.74%
-
This part converges three flow paths into one via internal channels. These channels would be impossible to machine, and instead would need to be drilled as straight holes and plugged.
Printing on the Studio System allows these channels to be designed for their function rather than their manufacturing method. This part can be produced in just a few days with very little hands on work.
-
Generative Piston Head
4140Prototype piston head for a reciprocating engine, optimized with generative design.
Generative Piston Head
-
Size (mm) 105 x 105 x 54
Cost to print ($) 271.00
Cost to machine ($) 568.13
Savings vs. machining 52.30%
-
Typically CNC machined from aluminum alloy, pistons can be time consuming and difficult to rapidly prototype and test - often taking months or even years to move from design to production.
With the Studio System, various piston designs can be easily prototyped and tested—speeding up product development timelines, reducing time to market, and introducing new opportunities for optimization, including generative design—all while avoiding CNC backlog and lead times.
-
Pump Housing
17-4 PHThis is part of the housing for a hydraulic pump.
Pump Housing
-
Size (mm) 136 x 131 x 47
Cost to print ($) 243.00
Cost to machine ($) 708.68
Savings vs. machining 65.68%
-
This part would typically be cast, followed by secondary machining operations - resulting in long lead times and high costs.
By printing on the Studio System, the long lead time associated with casting can be avoided, and the cost to machine from scratch is greatly reduced - allowing the manufacturer to produce the part in-house and enabling cost-effective rapid design iteration and pilot runs.
-
Guitar tailpiece
17-4 PHThe guitar tailpiece anchors one end of the guitar strings.
Guitar tailpiece
-
Size (mm) 127 x 28 x 20
Cost to print ($) 36.00
Cost to machine ($) 343.
28
Savings vs. machining 89.51%
-
The guitar tailpiece is typically cast from aluminum, and can be fairly expensive to customize for short manufacturing runs.
Printing in steel allows design freedom and part customization while eliminating tooling costs. Steel tailpieces also exhibit more pleasing resonance and sustain characteristics for some genres and playing styles.
-
Cuff Ring
316LExample of the unique jewelry that can be customized and scaled for a tailored fit.
Cuff Ring
-
Size (mm) 59 x 54 x 80
Cost to print ($) 43.
00
-
Unique jewelry pieces can be 3D printed without the design lock-in, long lead times and costs associated with tooling. The Studio System’s high resolution print head produces small parts with fine features and surface finish.
X-Series | Desktop Metal
Team DM
Platforms
Metal and composites 3D printing 3D printing solutions for health care Industrial-grade polymer 3D printing™
Sand and tooling 3D printing solutions 3D printers for sheet metalMaterials
Breakthrough photopolymer development Advancing 3D printed upcycled woodApps & More
The hydraulic additive manufacturing experts Multi-material powder recoating technology Driving digital transformation in dentistryBinder jet 3D printing featuring patented Triple ACT for excellent surface quality and specialty materials, including both metals and ceramics.
Systems Overview
-
— 01
InnoventX
The most compact binder jet 3D printer for the production of metal, ceramic or composite parts.
Launched in 2018, this easy-to-use system features Triple ACT and a piezoelectric printhead. It’s suitable for education, research, prototyping, rapid product development, and short-run production of small components.
InnoventX
InnoventX
The most compact binder jet 3D printer for the production of metal, ceramic or composite parts. Launched in 2018, this easy-to-use system features Triple ACT and a piezoelectric printhead. It’s suitable for education, research, prototyping, rapid product development, and short-run production of small components.
[SPECS]
Download Spec SheetInnoventX
Print Technology
Triple Advanced Compaction Technology™
Print direction
Uni-directional
Build box size
160 x 65 x 65 mm (6.
3 x 2.5 x 2.5 in)
Max build rate (65μm layer thickness)
54 cc/hr
Binder Systems
AquaFuse™, CleanFuse™, FluidFuse™, PhenolFuse™
External dimensions
1203 x 1016 x 1434 mm (47.4 x 40.0 x 56.5 in)
-
— 02
X25Pro
This mid-volume advanced binder jet 3D print system is already being used globally for the production of metal, ceramic and composite parts.
Launched in 2020, this system features Triple ACT and a piezoelectric printhead. It’s suitable for research, prototyping, rapid product development, short-run production or continuous 24/7 production.
X25Pro
X25Pro
This mid-volume advanced binder jet 3D print system is already being used globally for the production of metal, ceramic and composite parts. Launched in 2020, this system features Triple ACT and a piezoelectric printhead. It’s suitable for research, prototyping, rapid product development, short-run production or continuous 24/7 production.
[SPECS]
Download Spec SheetX25Pro
Print Technology
Triple Advanced Compaction Technology™
Print direction
Uni-directional
Build box size
400 x 250 x 250 mm (15.
75 x 9.84 x 9.84 in)
Max build rate (65μm layer thickness)
1,200 cc/hr
Binder Systems
AquaFuse™, CleanFuse™, FluidFuse™, PhenolFuse™,
External dimensions
2300 x 1800 x 2300 mm (90.5 x 70.9 x 90.5 in)
-
— 03
X160Pro
The world’s largest binder jet 3D printer for the production of metal, ceramic or composite parts.
This system features Triple ACT and a piezoelectric printhead. It's designed for continuous 24/7 production, yet supports short-run production, rapid product development, and even research and prototyping
X160Pro
X160Pro
The world’s largest binder jet 3D printer for the production of metal, ceramic or composite parts. This system features Triple ACT and a piezoelectric printhead. It's designed for continuous 24/7 production, yet supports short-run production, rapid product development, and even research and prototyping
[SPECS]
Download Spec SheetX160Pro
Print Technology
Triple Advanced Compaction Technology™
Print direction
Uni-directional
Build box size
800 x 500 x 400 mm (31.
5 x 19.7 x 15.8 in)
Max build rate (65μm layer thickness)
Up to 3,120 cc/hr
Binder Systems
AquaFuse™, CleanFuse™, FluidFuse™, PhenolFuse™,
External dimensions
3300 x 3300 x 2700 mm (130 x 130 x 107 in)
Applications by Industry
_Industries
Explore applications for 3D printing across a range of industries.
Keep Up with the Latest News
How metal 3D printers work. Overview of SLM and DMLS technologies. additive manufacturing. 3D metal printing.
Metal 3D printing. Additive technologies.
SLM or DMLS: what's the difference?
Hello everyone, Friends! 3DTool is with you!
BLT metal 3D printer catalog
Selective laser melting ( SLM ) and direct metal laser sintering ( DMLS ) are two additive manufacturing processes that belong to the family of 3D printing using the powder layer method. The two technologies have much in common: they both use a laser to selectively melt (or melt) metal powder particles, bonding them together and creating a pattern layer by layer. In addition, the materials used in both processes are metals in granular form.
The differences between SLM and DMLS come down to the basics of the particle bonding process: SLM uses metal powders with a single melting point and completely melts the particles, while in DMLS the powder consists of materials with variable melting points.
Specifically:
SLM produces single metal parts while DMLS produces metal alloy parts.
Both SLM and DMLS technologies are used in industry to create final engineering products. In this article, we will use the term "metal 3D printing" to summarize the 2 technologies. We will also describe the main mechanisms of the manufacturing process that are necessary for engineers to understand the advantages and disadvantages of these technologies.
There are other manufacturing processes for producing dense metal parts, such as electron beam melting (EBM) and ultrasonic additive manufacturing (UAM). Their availability and distribution is rather limited, so they will not be presented in this article.
How 3D printing with SLM or DMLS metal works.
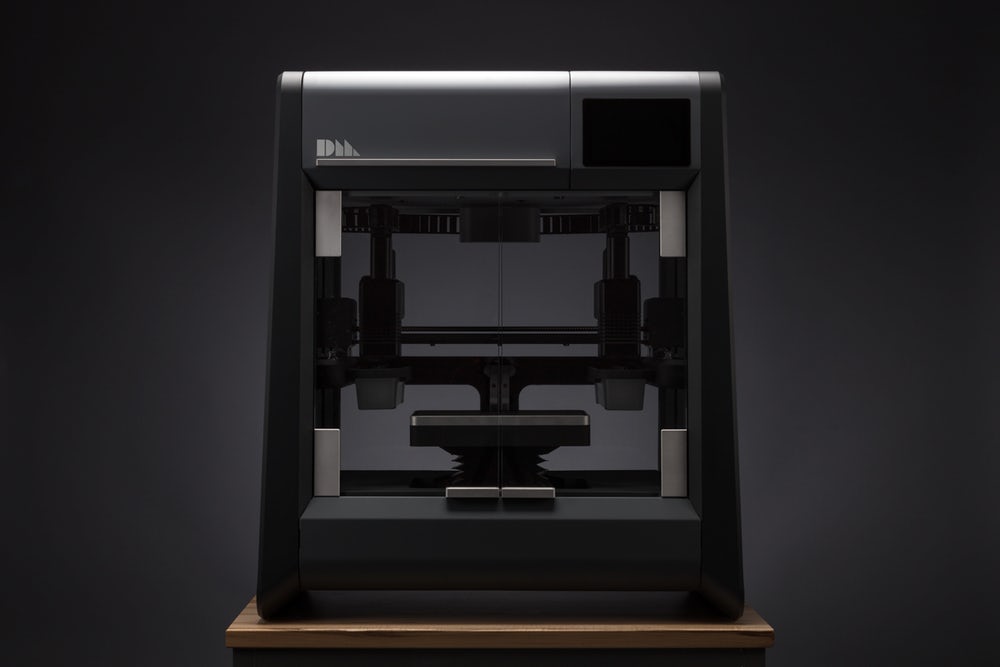
How does metal 3D printing work? The basic manufacturing process for SLM and DMLS is very similar.
1. The printing chamber is first filled with an inert gas (such as argon) to minimize the oxidation of the metal powder. It then heats up to the optimum operating temperature.
2. A layer of powder is spread over the platform, a powerful laser makes passes along a predetermined path in the program, fusing the metal particles together and creating the next layer.
3. When the sintering process is completed, the platform moves down 1 layer. Next, another thin layer of metal powder is applied. The process is repeated until the entire model is printed.
When the printing process is completed, the metal powder already has strong bonds in the structure. Unlike the SLS process, parts are attached to the platform via support structures. The support in metal 3D printing is created from the same material as the base part. This condition is necessary to reduce deformations that may occur due to high processing temperatures.
When the 3D printer's chamber cools down to room temperature, excess powder is removed manually, such as with a brush. The parts are then typically heat treated while they are still attached to the platform. This is done to relieve any residual stresses. They can then be further processed. The removal of the part from the platform occurs by means of sawing.
Scheme of operation of a 3D printer for metal.
In SLM and DMLS, almost all process parameters are set by the manufacturer. The layer height used in metal 3D printing varies from 20 to 50 microns and depends on the properties of the metal powder (fluidity, particle size distribution, shape, etc. ).
The basic size of the print area on metal 3D printers is 200 x 150 x 150 mm, but there are also larger sizes of the working area. Printing accuracy is from 50 - 100 microns. As of 2020, metal 3D printers start at $150,000. For example, our company offers 3D metal printers from BLT.
metal 3D printers can be used for small batch production, but the 3D printing capabilities of such systems are more like those of mass production on FDM or SLA machines.
The metal powder in SLM and DMLS is recyclable: typically less than 5% is consumed. After each impression, the unused powder is collected and sieved, and then topped up with fresh material to the level required for the next production.
Waste in metal printing, are supports (support structures, without which it will not be possible to achieve a successful result). With too much support on the manufactured parts, the cost of the entire production will increase accordingly.
Adhesion between coats.
3D metal printing on BLT 3D printers
SLM and DMLS metal parts have almost isotropic mechanical and thermal properties. They are hard and have very little internal porosity (less than 0.2% in 3D printed condition and virtually non-existent after processing).
Metal printed parts have higher strength and hardness and are often more flexible than traditionally made parts. However, such metal becomes “tired” faster.
3D model support structure and part orientation on the work platform.
Support structures are always required when printing with metal, due to the very high processing temperatures. They are usually built using a lattice pattern.
Supports in metal 3D printing perform 3 functions:
• They form the basis for creating the first layer of the part.
• They secure the part to the platform and prevent it from deforming.
• They act as a heat sink, removing heat from the model.
Parts are often oriented at an angle. However, this will increase the amount of support required, the printing time, and ultimately the overall cost.
Deformation can also be minimized with laser sintering templates. This strategy prevents the accumulation of residual stresses in any particular direction and adds a characteristic surface texture to the part.
Since the cost of metal printing is very high, software simulations are often used to predict how a part will behave during processing. These topology optimization algorithms are otherwise used not only to increase mechanical performance and create lightweight parts, but also to minimize the need for supports and the likelihood of part distortion.
Hollow sections and lightweight structures.
An example of printing on a BLT 3D printer
Unlike polymer powder melt processes such as SLS, large hollow sections are not typically used in metal printing as the support would be very difficult to remove, if at all possible.
For internal channels larger than Ø 8 mm, it is recommended to use diamond or teardrop cross-sections instead of round ones, as they do not require support. More detailed recommendations on the design of SLM and DMLS can be found in other articles on this topic.
As an alternative to hollow sections, parts can be made with sheath and cores, which in turn are machined using different laser power and pass speeds, resulting in different material properties. The use of sheath and cores is very useful when making parts with a large solid section, as it greatly reduces printing time and reduces the chance of warping.
The use of a lattice structure is a common strategy in metal 3D printing to reduce part weight. Topology optimization algorithms can also help design organic lightweight shapes.
Consumables for 3D metal printing.
SLM and DMLS technologies can produce parts from a wide range of metals and metal alloys, including aluminum, stainless steel, titanium, cobalt, chromium and inconel. These materials meet the needs of most industrial applications, from aerospace to medical applications. Precious metals such as gold, platinum, palladium and silver can also be processed, but their use is of a minor nature and is mainly limited to jewelry making.
The cost of metal powder is very high. For example, a kilogram of 316 stainless steel powder costs approximately $350-$450. For this reason, minimizing part volume and the need for supports is key to maintaining optimal manufacturing cost.
The main advantage of metal 3D printing is its compatibility with high-strength materials such as nickel or cobalt-chromium superalloys, which are very difficult to machine with traditional methods. Significant cost and time savings can be achieved by using metal 3D printing to create a near-clean shape part. Subsequently, such a part can be processed to a very high surface quality.
Metal post-processing.
Various post methods. treatments are used to improve the mechanical properties, accuracy and appearance of metal printed products.
Mandatory post-processing steps include the removal of loose powder and support structures, while heat treatment (heat annealing) is typically used to relieve residual stresses and improve the mechanical properties of the part.
CNC machining can be used for critical features (such as holes or threads). Sandblasting, plating, polishing, and micro-machining can improve the surface quality and fatigue strength of a metal printed part.
Advantages and disadvantages of metal 3D printing.
Pros:
1. Metal 3D printing can be used to make complex custom parts, with geometries that traditional manufacturing methods cannot provide.
2. Metal 3D printed parts can be optimized to increase their performance with minimal weight.
3. Metal 3D printed parts have excellent physical properties, metal 3D printers can print a wide range of metals and alloys. Includes difficult-to-machine materials and metal superalloys.
Cons:
1. Manufacturing costs associated with metal 3D printing are high. The cost of consumables is from $ 500 per 1 kg.
2. The size of the working area in metal 3D printers is limited.
Conclusions.
• Metal 3D printing is most suitable for complex, one-piece parts that are difficult or very expensive to manufacture using traditional methods, such as CNC.
• Reducing the need for building supports, will significantly reduce the cost of printing with metal.
• 3D printed metal parts have excellent mechanical properties and can be made from a wide range of engineering materials, including superalloys.
And that's all we have! We hope the article was useful to you.
Catalog of 3D printers for metal BLT
You can purchase metal 3d printers, as well as any other 3d printers and CNC machines, by contacting us:
• By email: Sales@3dtool. ru
• By phone: 8(800)775-86-69
• Or on our website: http://3dtool.ru
Also, don't forget to subscribe to our YouTube channel:
Subscribe to our groups in social networks:
In contact with
American and Turkish engineers assembled a desktop 3D metal printer
News
0013 A team of scientists from California State University and Osman Ghazi University of Eskisehir has taken on the holy of holies — the creation of a budget 3D printer capable of printing all-metal products. Let's talk about what they did.
Direct 3D printing with metals (without intermediate steps such as growing polymer-metal blanks, and then etching and sintering) can be divided into two areas, referred to in Russian GOST as “synthesis on a substrate” (in the English terminology Powder Bed Fusion or PBF ) and "direct energy and material supply" (Directed Energy Deposition or DED). Synthesis on a substrate involves sintering or fusing metal-powder compositions in containers using laser emitters or electron beam guns. In the direct supply of energy and material, various energy sources can also be used, for example, the same lasers or electron beams, and the materials can be either powders deposited into the sintering or fusion zone or metal wire.
A project by scientists from California State University and Osman Ghazi University of Eskisehir is a variant of the second track called Wire Arc Additive Manufacturing or WAAM. Here, the material is wire, and the products are grown by arc welding, specifically in this case, with a non-consumable electrode in a protective inert atmosphere. WAAM is already being used in industry, for example in the repair and even additive manufacturing of ship parts: in 2017, the Dutch production center RAMLAB produced the first type-certified 3D printed ship propeller ( in the illustrations above and below ).
The resolution of WAAM 3D printers is, to put it mildly, small and requires a lot of post-processing, but they are easily scaled up and do not require fuss with relatively expensive, and often dangerous powders, and at the same time outperform traditional methods in terms of producing geometrically complex products with minimum waste. But you can scale both up and down, and the heroes of our story decided to create such a device not on the basis of an expensive industrial-grade multi-axis robotic arm, but by redesigning a budget desktop FDM 3D printer with the intention of keeping within one thousand dollars.
As a basis, the guys took an open-source "drygost" called Bukobot by the Californian company Deezmaker. The team assembled the device themselves by printing plastic parts on a Stratasys uPrint SE Plus 3D printer, and the power source for the head is an Everlast-branded welding machine. The movable electrode is mounted on one carriage with a mechanism that feeds a metal wire into the melt zone.
Inconel 718 single layer metallography
Experiments were carried out with two types of consumables - AISI 1030 high-carbon steel wire and Inconel 718 heat-resistant nickel-chromium alloy with a diameter of 0.8 mm using tungsten electrodes with a diameter of 2.37 mm and blowing with an inert gas - argon. A series of experiments included experiments on 3D printing at different speeds with the appropriate adjustment of the material feed rate and current strength. For steel, these parameters varied within 2.5-3.5 mm/s with a feed rate of 14-18 mm/s at 45-55A, and with Inconel they tried to print at speeds of 4.88-5.03 mm/s with a feed rate wire 7.69-10.49 mm/s at 40-50A.
View and section of a 30 layer Inconel 718 specimen
Predictably, the team faced a host of challenges, including mechanical failures, errors in machine code, overheating and even burnout of electrical connections, and electronic and stepper motor failures caused by welder interference.
When working out the parameters, the results varied greatly: when working with the same steel, even at a current of 50A, 3D printing at high speeds produced a series of drops instead of solid lines, so the combination of a paving speed of 3 mm / s with material feed at a speed of 18 mm / s at a current of 55A ( option number 8 in the illustration above ). With these settings, we managed to get a wall of twenty-five layers in the illustration below.
In general, the experiment was recognized as successful, as the very possibility of WAAM 3D printing with metals on budget, self-assembled equipment with a total cost of around one thousand dollars was proved without significant defects, such as interlayer oxidation or cracking. The team's full report can be found at this link.
Do you have interesting news? Share your developments with us, and we will tell the whole world about them! We are waiting for your ideas at [email protected].
budgetary metal printing WAAM
Follow author
Follow
Don't want
13
More interesting articles
6
Subscribe to the author
Subscribe
Don't want
REC, one of the leading Russian manufacturers of consumables for FDM/FFF 3D printer.