3D printing carpet
3d Print Rug - Etsy.de
Etsy is no longer supporting older versions of your web browser in order to ensure that user data remains secure. Please update to the latest version.
Take full advantage of our site features by enabling JavaScript.
Find something memorable, join a community doing good.
( 1,000+ relevant results, with Ads Sellers looking to grow their business and reach more interested buyers can use Etsy’s advertising platform to promote their items. You’ll see ad results based on factors like relevancy, and the amount sellers pay per click. Learn more. )
Dutch designers create rugs using 3D printing, offcuts and a giant loom
Ali Morris | Leave a comment
Four studios are presenting very different floor coverings in a Dutch design showcase at London Design Festival, demonstrating a range of innovative techniques and technologies.
Colourful geometric rugs 3D-printed from polyamide fibres, and blankets and rugs made using a bespoke giant loom are just a few of items on show at Dutch Stuff.
The exhibition, which forms part of the London Design Fair in the Old Truman Brewery, features the work of 25 studios based in the Netherlands.
Studio Plott's rugs are 3D-printed from polyamide fibreAmong the four rug designers featured in the show is Eindoven-based Studio Plott, founded by designers Rudi Boiten and Mireille Burger. Their project called Crossing Lines, is a series of colourful triangular and lozenge-shaped mesh rugs that feature geometric patterns.
Available in 10 colours, the rugs are 3D-printed from polyamide fibre.
Studio Plott's mesh rugs collection is called Crossing Lines and features geometric patterns"The designs are a clear visualisation of our fascination with technology, traditional craft, geometric pattern, colour and shape," explained the designers.
"Each pattern has its own playful interplay of lines where the open mesh arrangements and bright colours create a visual dialogue between the rugs and their underlying surfaces. "
Studio Ro Smit, founded by designer Roland Pieter Smit, presents a series of seven rugs and blankets made in collaboration with craftspeople working at the Maartenhuis – a social work community for people with disabilities on the island of Texel in the Netherlands.
Realising that people with different types of disability are more suited to working with different types of yarn, Smit developed specific yarns for the craftspeople.
Studio Ro Smit developed enlarged weaving frames for the new yarns used in the collectionBecause ordinary looms couldn't process the new yarns, Smit developed his own weaving frames, in which he enlarged and simplified the weaving process. This in turn encouraged social interaction among the makers.
Muuto launches bobbly rugs designed by Margrethe Odgaard to feel like pebbles
"The result is a beautiful series of woollen blankets and rugs with a recognisable authentic look, each with the unique 'signature' of the creator," said Smit.
Studio Simone Post presents carpets she made for high-end wax-printed fabrics brand Vlisco, using leftovers and misprints.
Meanwhile Nina van Bart is showing a series of rugs developed in collaboration with Dutch brand Carpet Sign using a new 3D-tufting technique.
The materials used were sourced from the factory of high-end wax-printed fabrics brand VliscoMany of the other products showcased in Dutch Stuff also feature innovative techniques and digital tools. Some of the materials the studios are exploring include chipboard and repurposed industrial waste plastic, while techniques include marquetry made using computer programs and dyeing processes.
The showcase forms a continuation of last year's Dutch Stuff, where the work of more than 60 Dutch collectives, studios and independent designers was exhibited.
The show organisers believe that this year's more refined offering will provide the exhibited work with more "space to breathe".
London Design Fair runs from 20 to 23 September the Old Truman Brewery.
Other exhibitions in the show include the Nordic Happiness Hotel, which will display new Finnish design and technology brands. Meanwhile Southern Sweden Creatives will feature work by 13 design companies from southern Sweden, exhibited within a timber pavilion created by architect Karin Sundberg.
Other collections on show as part of London Design Festival include architect Henning Stummel's flat pack furniture cut from a single piece of wood, and Another Country and Ekkist's furniture collection designed to promote health and wellbeing in the home.
Subscribe to our newsletters
Your email addressDezeen Debate
Our most popular newsletter, formerly known as Dezeen Weekly. Sent every Thursday and featuring a selection of the best reader comments and most talked-about stories. Plus occasional updates on Dezeen’s services and breaking news.
Sent every Tuesday and containing a selection of the most important news highlights. Plus occasional updates on Dezeen’s services and breaking news.
Dezeen DailyA daily newsletter containing the latest stories from Dezeen.
Dezeen JobsDaily updates on the latest design and architecture vacancies advertised on Dezeen Jobs. Plus occasional news.
Dezeen AwardsNews about our Dezeen Awards programme, including entry deadlines and announcements. Plus occasional updates.
Dezeen Events GuideNews from Dezeen Events Guide, a listings guide covering the leading design-related events taking place around the world. Plus occasional updates.
We will only use your email address to send you the newsletters you have requested. We will never give your details to anyone else without your consent. You can unsubscribe at any time by clicking on the unsubscribe link at the bottom of every email, or by emailing us at [email protected].
For more details, please see our privacy notice.
Thank you!
You will shortly receive a welcome email so please check your inbox.
You can unsubscribe at any time by clicking the link at the bottom of every newsletter.
13 notes about 3D printing, after 3 years of owning a 3D printer / Habr
This article will be, first of all, of interest both to those who have directly dealt with 3D printing, that is, who owns a 3D printer, but also to those who are just about to join the ranks of 3D printers and are thinking about buying their own printer.
In the framework of this article, I want to present my observations, as a direct owner of a 3D printer, for more than 3 years.
Despite the fact that 3D printers have been known for a long time and, in my memory, have become widely used, judging by the information on various resources, starting around 2010 (I may be wrong, these are my subjective observations), for a long time I ignored this area, it’s hard to say why…
Probably thought it was some kind of "childish pampering", another hype topic for which there is simply not enough time. ..
The turning point happened when one of the wheels on my travel suitcase wore out. You know, a big plastic suitcase, with four spinning wheels on the bottom. Unfortunately, it is a “rather disposable thing”, due to the lack of bearings on the wheels, which is why the wear of the friction point of the axle and wheel allows the suitcase to last no more than one or two seasons.
And it’s like “lightning flashed in the middle of the day: 3D printer!” It is with his help that I can fix this problem! Looking ahead, I’ll say that I didn’t succeed in fixing the suitcase in this way, so I had to use a different approach ...
As a result, I “upped” it - installing wheels from unnecessary roller skates. Thanks to this “up”, the suitcase has become a real all-terrain vehicle and, even being very loaded, it rides easily - pushed forward even with “one finger”. And even in the snow, 5-6 cm thick. A tank, not a suitcase turned out! By the way - I took spinning wheeled "units" in Leroy. Then he took off and threw out his native plastic wheels from there, inserting from roller skates:
But this thought itself became a kind of trigger that allowed me to finally join the world of printers and buy my first 3D printer.
Like many, before buying it, I studied various forums and sites for a long time, delving into all the subtleties. And for some reason, I immediately liked the type of printer called the delta printer. Probably because during operation it looks like some kind of "alien device".
If at your leisure you like to sit “looking into the carpet”, then with the advent of such a printer you will have a much more interesting activity, even hypnotizing, one might say :-))
And this, in fact, is my delta (if anyone is interested), which went through, let's say, the "ultimate up": all the electronics are placed upstairs, on a self-made welded frame, covered with polyethylene and a magnetic door is made. The coil with a bar is installed at the top, on the frame. The axis on which the coil is put on is machined on a lathe from aluminum and a bearing from the VAZ timing is inserted into it. As a result, the coil - "rotates even from the passage of a fly nearby":
Well, yes, I won’t argue for a long time, let’s start reviewing the main facts that I have accumulated as a result of owning this car ... The facts are purely subjective and may differ from your vision. In any case, I will be glad to comments, clarifications, etc.
▍ NOTE 1. Delta is good, but...
Here I should give a number of my observations regarding the delta printer:
- It contains a completely finished frame of the future box, which makes it easy to form a heat chamber. I understand that many printers are made in the form factor of a “certain box” (but this point cannot be ignored), which greatly facilitates the process of wrapping this box with heat-insulating material.
In my case, as such a material, I used a plastic film.
- Already thanks to its design, delta allows you to work at much higher speeds than XY printers. By the way, it is on the delta principle that many modern high-speed industrial robots are built to sort various parts directly on the conveyor belt:
However, this plus does not allow to fully realize the occurrence of parasitic vibrations, even despite their suppressors:
Thus, accurate printing is possible, only at speeds (at least that was the case for me), no more than 60 mm per second. A complex procedure for aligning the movement of the head parallel to the table, which is why, for many, the so-called "lens" appears. People struggle with it with varying degrees of success, but I have not encountered this on my printer and for me, therefore, the “lens” has never been a problem. At the same point, it is worth noting the calibration of the table, which was initially absent on the first deltas, and I had to use an external third-party solution from one American do-it-yourselfer called EZBED. This solution was a hardware-software complex that allows you to quickly and easily calibrate the printing table, that is, to let the printer understand its geometry. Modern printers do not have this issue as they come with a built-in calibration solution. It is worth noting that I solved this problem by attaching a limit switch to the print head, and using the Marlin-1.1.9 firmware.
▍ NOTE 2. "Size doesn't matter..." :-)
When I got the printer, I was impressed by the possibility of huge printouts, a la the handguards of some futuristic rifles, huge body parts, etc.
However, if you try to analyze the results of your many years of practice, it turns out that in most cases, rather small objects were printed that easily fit in the palm of your hand, a maximum of two palms. Despite such a seemingly small size, the printing of these details took a significant amount of time. Of course, this very much depends on which nozzle you print with. But, despite this, it is difficult to disagree with the fact that most of the printed parts will be quite utilitarian and small in size.
Therefore, to be honest, the need for a printer that allows you to print "Venus de Milo in life size" is not obvious.
Of course, you can object to me that “I’m going to buy a printer, I’ll get used to it a little and I’ll get started!!!”
One simple point must be taken into account here: there are no universal things. And in order to understand how much 3D printing in general and your printer, in particular, you will need to solve your problems, and how much it will be able to solve such problems, you just need to first try the 3D printing method personally and then a lot will become clear to you .
Therefore, for a beginner, I recommend taking a small printer that allows you to print extremely small items that fit in the palm of two. With such a device, you will definitely never lose, as it will always be needed. In addition, with its help you will be able to get used to the printing process and, if necessary, purchase a larger device, already clearly understanding its capabilities and ability to solve your set of tasks.
▍ NOTE 3. "What type of printer to get."
Based on the foregoing, I do not recommend taking a delta printer and this can be said right away.
Not because it is bad, in fact, it prints quite accurately, its main problem (in my opinion) is the inability to print rectangular flat, fairly large case components, as well as the inability to fully realize high-speed work, since the quality drops critically. Here it turns out to be a rather offensive situation - the printer can work quickly, but this cannot be done, since the quality will be “nothing”.
And then what kind to take? Depending on the budget and capabilities, I recommend taking any cube printer, for example, the same Core XY (the head moves, and the table goes down as the model “grows”, from top to bottom):
Image source: thingiverse.com
Such a printer allows you to easily print fairly large flat parts of cases, has good speed and accuracy. In addition, the presence of a rigid box-shaped frame allows it to be easily covered with polyethylene to create a sealed heat chamber. In addition, the very fact that the table does not move while working reduces the number of problems with model peeling.
However, the advantages of this printer will not be fully revealed if it has a direct extruder. On the one hand, it will allow printing with rubber-like materials, on the other -
large inertia and head weight. And these are parasitic vibrations, wear of the fur. parts, etc. (like everything in life, “we treat one thing and cripple another” :-))
At the initial stages, this may not be necessary, but in the future it may be necessary to print, for example, tires for your homemade car. And with this, the Bowden extruder has obvious problems. Although, in fairness, printing with such a rubber-like material is far from a daily need. However, whoever seeks will always find: over time, I found a way to “upgrade” my printer with a Bowden extruder to print with flexible materials. "Crutches" of course. But even so.
By the way, there are printers of a cheaper type, the so-called "drygostol", printing by moving the table and head:
They are inexpensive, moderately accurate, but they require a sufficiently high-quality gluing of the printed model to the table, because the table moves, and the model can come off when the table is jerked sharply. When printing large models, this can be a problem.
▍ NOTE 4. What to print with?
It's only a matter of taste and purpose. That is, if your printout will only stand on a shelf and should differ in some kind of aesthetic appearance, these are some requirements, if the printout is an engineering part that will be operated under conditions of increased mechanical load, these are different requirements. That is, in the first case, you can use any PLA, SBS plastics, and others with similar properties.
For engineering parts, for example, I only use ABS. It combines high hardness, strength and low price. Although I understand that now this last statement will cause a storm of comments in the style of “no! - there is even stronger, even better, the same PETG, etc. ":-)
Just here I wanted to say that thanks to the low price and the practical experiments that I conducted with ABS plastic, I realized that it is completely meets all my requirements.
However, the fact that ABS plastic releases carcinogenic substances when heated is quite annoying and forces you to take measures to prevent poisoning. For this, my printer prints completely closed and on an open balcony. After printing, the printer chamber opens, and it remains open in this form until it is completely ventilated and cools down.
▍ NOTE 5. "ABS is difficult to type on, it flakes, peels off the table, etc..."
With a properly configured printer (in my case, at a print temperature of 205 degrees, a thermal chamber and a desktop temperature of 100 degrees), the use of auxiliary techniques, for example, among which, one can name the so-called ABS juice (which is ABS- plastic dissolved in acetone), you can create wear-resistant and durable things, without any hypothetical problems.
For example, my printer has been printing for many hours at temperatures well below freezing. And this happened more than once, not twice, not three! And the print quality was excellent:
12-hour ABS printing at -4 C
▍ NOTE 6. Acetone for post-processing and ABS juicing
At one time, I wrote a fairly detailed article on this topic and I will try to give the main excerpts from it. The essence of the issue here is as follows: due to the fact that different GOSTs are used for the production of acetone, acetone differs in quality. Despite the fact that it would seem that “acetone is also acetone in Africa,” nevertheless, one type of acetone can differ significantly from each other. For example, ordinary acetone, which can be bought at any hardware store, such as "1000 little things", "store near the house" and the like, is very low quality acetone, smells disgusting (although someone like it, maybe someone likes its pleasant building aroma and "aftertaste" :-))).
In contrast to it, there is a much higher quality acetone, which, however, is not found at all in any household stores, even large chain stores, such as Auchan or Leroy Merlin.
This type of acetone is found exclusively in shops that sell varnishes and paints for automotive work, i.e. these are highly specialized shops for car workshops:
Acetone, which can be purchased there, is of excellent quality, smells almost like alcohol, quickly disappears,
:-) - this is a joke, of course, don't even try it.
However, its main advantage, compared to household type acetone, is that it perfectly dissolves ABS plastic and does not allow it to precipitate. For me personally, it was a very surprising observation when the same ABS plastic was perfectly dissolved with acetone from an auto shop, and completely precipitated when I tried to use household acetone (I just ran out of good acetone, and I had to use "what is ").
Therefore, if you want your results to always be excellent, then here is the right acetone. It should be labeled "for professional use":
▍ NOTE 7. What about ABS juice?
"ABS juice" is what printers call a mixture of acetone and pieces of ABS plastic dissolved in it. This mixture is smeared on the surface of the desktop before printing and allowed to dry. Thanks to this spread, the model easily sticks to the desktop and does not peel off during the printing process. After printing is completed and the platen has cooled down, the model can be easily separated.
All that needs to be said here is that, after trying different approaches over time, I settled on using flexible metal spatulas, also called "Japanese type spatulas":
According to the results of many tests, this method of spreading turned out to be one of the most convenient options, such spatulas can be cleaned very quickly and easily after work. In other words, highly recommended!
▍ NOTE 8. "Yes, nothing sensible can be done on it, I indulged a little and decided to sell it - you can't use it for anything good anyway"
I absolutely disagree with the statement above, which is periodically heard from newcomers to 3D printing. You can even say more: at the moment I can’t even imagine how I used to live without a 3D printer! Since it is he who makes it possible for any do-it-yourselfer to significantly expand their capabilities and make piece products, almost of factory quality! Of course, for this, appropriate hands must be applied to the 3D printer, but that’s another question… and take on things that I would never have thought to take on before!
For example, among my homemade products, the following can be listed:
- Heated sole for boots, which is a hose integrated into the insole (and filled with household silicone from a household store), through which water flows, heated with a catalytic type hand warmer.
Water is pumped using a small peristaltic pump. The engine with a metal gearbox, which is used in the creation of this pump, allows you to develop a force of 3 kg, which is even redundant for this homemade product. The engine is powered by Peltier elements mounted next to the catalytic heater. The project is currently in progress.
- Centrifugal water pump mounted on the shaft of an internal combustion engine that drives a high pressure wearable air compressor with a pressure of 500 bar. The pump pumps coolant through the casing of the high pressure pump, or rather its second stage. Despite the fact that the pump is 3D printed and runs at over 6000 rpm, nothing “fell apart, fell apart, didn’t break.” As you can see in the photo, the pump is installed instead of the “starter”, that is, the armstarter. The compressor scheme as a whole is as follows: 2 engines. Connected by clutch. One is heavy duty. The second is modified and turned into a high pressure compressor:
Yes, before assembling this, I also did not believe that this was possible. Moreover, even when I collected it, I did not believe my eyes :-))). However, it is a fact…
- I printed a number of Rank-Hilsch test tubes, the essence of which I have described in detail in this article.
- Printed mass of parts, more than 100 pieces, to create 10 web-controlled robots. There was also a detailed article about this here.
Well, and a bunch of all sorts of useful and not very crafts. As you can see from my crafts above, I have a special passion for creating some useful things, a utilitarian direction. That is, so that the printout is useful, and does not belong to the type “yyy breathe, Mikola, what am I doing here” :-), and then put it on the shelf and that's it. Although, engineers are also not alien to beauties, and this will be my next fact below.
▍ NOTE 9 Proper placement of the model when printing is half the battle
It would seem an obvious fact, but many underestimate it. Here I mean the following: by experience, I accidentally discovered that when printing various statues (in which I, completely unexpectedly for myself, discovered another passion of mine), it is advisable to place the statues at an angle to the printing table.
This allows the layers in the printout to run at an angle of approximately 45-50 degrees to the model. The result of this is that the printed model is almost completely invisible layers and the model looks like it has been post-processed, but at the same time retains a deep matte color, which, to my personal taste, is more like a marble than a glossy result of processing in an acetone bath :
An additional advantage of this method is that the layers going at an angle of 45-50 ° to the model give it additional strength. This is especially true for printing statues, which contain many thin elements that are easily chipped when the statue is accidentally dropped from a table or shelf (learned from bitter experience, this happened to me many times, and ruined some fairly decent prints).
That is, the layers going across the model, if the model has a large length in height, does not allow it to maintain sufficient strength. For better understanding, I tried to illustrate this point in the figures below:
▍ NOTE 10. Bleeding must be taken into account when printing, especially if the model is composed of separate parts and must be assembled by joining these parts to each other, entering into each other, etc.
I tried to illustrate this point in the figures below. The implication here is that if you're printing a composite model, you need to correct for the amount of bleed on the plastic (I'm not sure what it's called, but at least I tried to convey what I mean). If this is not taken into account, then the model will not fit.
For example, in my case this correction is 0.2 mm per diameter - if I want the model to fit more tightly; if I need a free joint, without excessive density, then 0.3 mm per diameter:
That is, suppose that the blue part has a size of 10x10mm. So it must be modeled in a CAD program as 9.8x9.8 mm (if we want it to sit tight) or 9.7x9.7 mm (to sit freely). Well, or expand the hole in the green part, and leave the blue one as it is.
This is often a problem when you download a prefabricated model from the Internet - but it is not going to, even if you crack! And because no amendments have been made…
For your particular case, the amendments may be different.
▍ NOTE 11. What if...
In fact, this note complements note number 8. Using a 3D printer allows you to create metal parts using a printed 3D model. For this, the casting method is used according to the lost wax or burnt model. In our case, we will deal mainly with metal casting on a burnt model.
Briefly, it looks like this: printing a 3D model (using PLA plastic) → pouring it with plaster → burning PLA plastic, simultaneously with burning the mold, in a conventional stove oven → pouring the resulting mold with molten metal (melted in a conventional microwave) .
Image source: 3dtopo.com
I told about a simple method of melting metals in a home microwave oven here.
There was even a good article about casting on Habré.
▍ NOTE 12. Durability?
Despite the fact that ABS plastic is called exposed to ultraviolet radiation and, accordingly, burns out, losing its strength in the sun, in my practice, even printouts that are constantly exposed to the sun have not lost their strength and color at all, continuing to be successfully used and Currently.
It should also be added here that printouts are constantly exposed not only to the rays of the sun, but also work continuously in damp conditions!
As such printouts, I can give an example of winglets for technical cranes, which I printed out, but, unfortunately, did not photograph this process; as well as fasteners on shoes that I use “both in the snow, and in the heat and in the pouring rain, and in general are always with me”:
▍ NOTE 13.
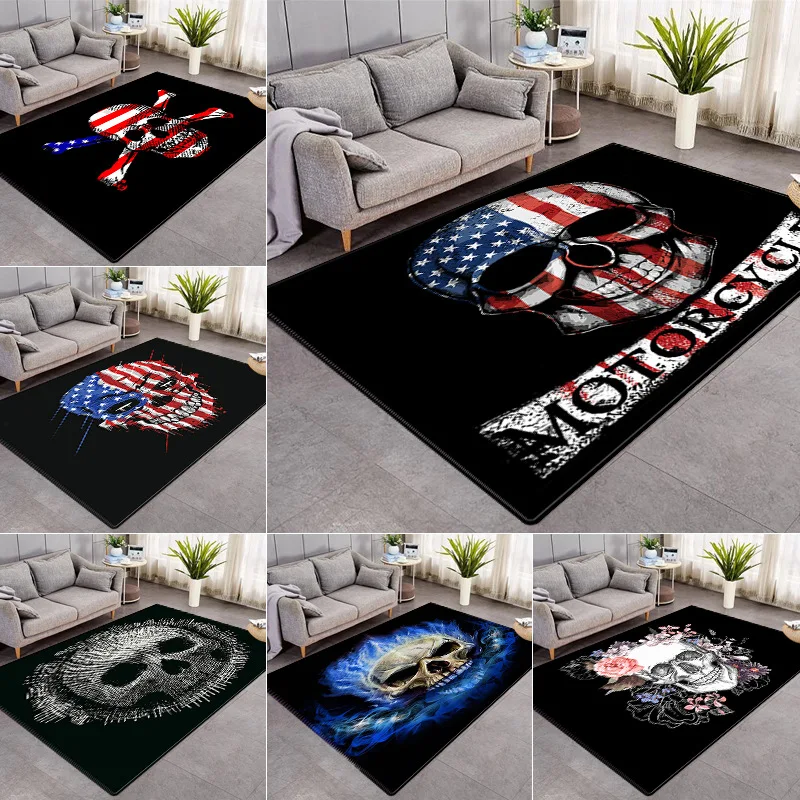
Periodically, there is a need to print parts containing a particular thread. Modeling such products requires a good understanding of what a thread is in general, as well as what corrections need to be made in your particular case, which I have already described above.
But since I've owned a metal lathe for a long time, I'm not at all happy with the 3D printed carving that looks like "something very carving-like".
I am satisfied with an exceptionally perfect carving. Therefore, I keep in stock a large set of various taps and dies, with which I cut all my threads in plastic printouts:
I posted a photo of dies and taps not to brag, but to make the reader understand that serious carving requires a serious approach (unfortunately). And considerable costs for all this thread-cutting iron ...
To create your own threads (both threaded channels and threaded pins), I recommend the following reference materials: for holes, for pins.
Well, that's where I want to end my story and note that he does not claim to be exceptionally accurate and exhaustive. Nevertheless, I tried to state a number of my observations. It will be interesting to read yours, in the comments!
specifications, photos and customer reviews
1 448 – 5 570 ₽Go to storeThe product is no longer sold, look at the similar
links copied, share it with
or send it through social networks
This product is no longer sold, but there are similar and similar 9000 9000
The price decreased by 157 ₽
₽ ₽ ₽ ₽ ₽ ₽ ₽ ₽ ₽ ₽ . Cheaper than average, slightly-3
%
Reliability of the seller - 55%
Be very careful, Shop4786012 Store
- On the site for more than 3 years
- Poor overall rating (788)
- Customers satisfied with communication for the last 3 months
Prices from other sellers from 321.
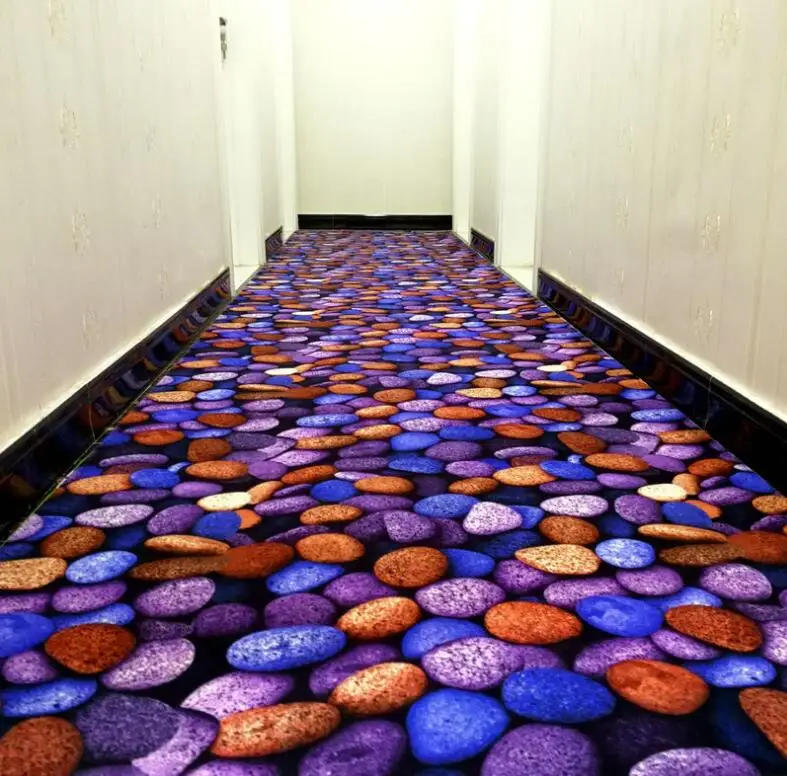
770.14 – 15 306 ₽
Pink Flowers 3D Printed Rugs Corridor Aisle Anti-slip Carpets for Living Room/Bedroom Rugs Floor Kitchen Rugs
0002 0OTOTICS0 PrOSS
Reliability - 73%
Seller SHOP3005003 Store
In the store in the store
321.12 - 510.22 ₽ 9000
0orders
Reliability - 89%
Seller RUBYLOVE Secret Store
ShopGo to Store study rug, dressing room rug
0 OTOCHOK
0 Prosals
Reliability - 43%
Seller Limetree Home Decor Co., Ltd
In the store
found 36 similar products
9000 - 4 052 ₽ 9000 living room, large Indian anti-slip protective carpets for kids room, home bedroom carpet0
0
Seller reliability 43%
-1
%
3 030 – 18 813 ₽
3d carpet for corridor, home/office, stairs, custom modern carpet, bedroom rug/corridor rug, living room rug
0
0
Reliable seller %
481. 34 – 4 910 ₽
Cobblestone 3d printing, hallway carpet, soft flannel children's bedroom rug/carpet, modern home carpets, hallway carpets, living room
0
0
Reliable sellerReliable
-16
%
3 139 – 19 484 ₽
3d flower corridor carpet for living room home decorative stair carpet for hotel walkway carpet entrance/hallway rug anti slip bedroom rug
0
0
Seller Reliability 55%
Chinese national flower, ink painting, 3d carpets for living room, bedroom, sofa mat, coffee table, yoga mat, custom Christmas decor3 9000
0
0
Reliable seller 89%
-6
% hallway, living room carpet
0
0
The reliability of the seller 55 %
9000 -3%
481. 34 -15 306 ₽
3D Exciting carpets for the living room bedroom rugs Kitchen carpet carpet carpet passage carpet
0
0
Seller Reliability 61%
Can custom 3d printed hallway carpet anti slip carpets for living room bedroom rugs for home coffee table large size carpet
0
0
Reliable Seller 73%
30003
0
Seller Reliability 43%
4 425 - 42 237 ₽
Large size, living room rugs, marble pattern, 3d carpet, coffee table, blanket, bedroom rug, modern geometric, Scandinavian, custom, floor mat
0
0
The reliability of the seller is 89 %
-11
%
3 139 -19 484 ₽
3D laconic carpet for stairs, living room, houses, decorative carpet for the corridor, hotel, passage, long carpet , entrance door, custom bedroom rug
0
0
Seller Reliability 55% , wedding carpets
0
0
The reliability of the seller 68%
2 732 - 20 658 ₽
Europe corridor carpets Hotel Corporate decorative input/rug for anti -slip carpet for stairs floor, wedding carpets
0
0
Reliability of the seller 55%
-5
%
3 139 – 19 484 ₽
Modern stair mats for the living room home/office carpet in the hallway hotel wing rug entrance/entrance rug custom bedroom rug
0
0
The reliability of the seller 55 %
9000 -4%
596. 86 -8 568 ₽
3D carpet, bedroom carpets, living room, large carpet, floor mats, children's rugs and carpets For a house, a living room for an entrance hall
0
0
The reliability of the seller 78 %
-2
%
1 109 -116 ₽
Scandinavian passage, geometry, luxurious carpet for the Corridor, modern carpet for stairs, long hotel kitchen mat, corridor, aisle carpet
1
3
Reliability of the seller 55%
770.14 – 14 825 ₽
Creative 3d rose print carpets, rugs for living room, bedroom, kitchen rugs, floor, carpet for home, corridor , rug
0
0
Reliability of the seller 61%
1 396 – 4 236 ₽
decorative carpet
0
0
The reliability of the seller 66 %
-0. 8
%
3 247 -20,57 ₽
Long carpet for the Corridor, decorative flower carpet for the stairs, home entrance/rug for the hallway hotel carrier for the Corridor , carpets for the living room and bedroom
0
0
The reliability of the seller is 85 %
-0.5
%
1 553 -4 419 ₽
3D Flower Scandinavian carpet for stairs, European corridor, hotel carpets, long walk-through carpet, home entry/hallway rug, anti-slip floor mats
0
0
Reliability of the seller 55%
-6
%
4 175 – 21 481 ₽
Rugs and carpets for bedroom, coffee table in the home rug/carpet for decoration
0
1
Reliability of the seller 55%
-0. 9
%
3 139 – 19 484 ₽ carpet for the entrance to the hotel for entrance hall individual rug for sofa and carpets
0
0
The reliability of the seller 68 %
9000 -4%
673.87 -15 788 ₽
High quality, 3D artistic carpets for the living room, bedrooms, rugs, anti -exceling kitchen rug/mat, Fashionable home carpet
0
0
The reliability of the seller is 66 %
-3
%
1 082 -12 240 ₽
3D Fate Scandinavian stairs, European rugs for halls, long runners, carpet home, entrance / corridor / aisle, party floor mats
2
0
The reliability of the seller 32%
3 247 - 20 157 ₽
3D Big Flower Stairs The living room rod decorative corner carpet entrance/carpet for the hallway Individual carpet for the bedroom 9000 9000 0 9000
0
Reliability of the seller 85%
-4
%
4 813 – 18 676 ₽
Creative kitchen rug hd 3d printing rugs for the hallway, bedroom, living room rugs for the corridor, aisle, anti-slip mats for the bathroom,
0
0
Reliability of the seller 73%
-4
%
3 139 – 19 484 ₽
carpet rug for hotel entrances Sophies and carpets
0
0
The reliability of the seller is 55 %
-1
%
1 151 -13 612 ₽
Scandinavian geometric carpet for the hallway, rugs for the bedroom, carpet for the Corridor, Corridor, Corridor, Corridor, Corridor. rug for home, hotel, aisle, custom carpet decor
0
0
The reliability of the seller 32 %
9000 -3%
671.12 -5 322 ₽
ZEEGLE FELENTAL CARLS, DOWNODAM, CAROP, Anti -Spear of POWN WARS, Children's Carpets, Carpet for a nursery bedrooms, bedside rugs
0
0
The reliability of the seller is 85 %
-3
%
1 358 -164 314 ₽
3D Pastoral long carpet in the corridor home entrance/carpet for the hallway decorative balcony mat. stairs mat aisle carpets
0
0
The reliability of the seller 55 %
-8
%
2 473 -4 343 ₽
Scandinavian style carpet SPALISTIC 3D stamped soft rugs of large area anti -excelled carpets and carpets for the decor of the living room
0
0
Reliability of the seller 68%
-9
%
1 903 – 30 600 ₽
decor, custom-made carpets
0
0
The reliability of the seller 60 %
9000 -7%
1 206 -11,296 ₽
Long carpet for stairs, artificial carpet in the Scandinavian style for the house, corridor, corridor, pebble for parties, weddings, red rugs
1
0
Reliable seller 55%
-0.