3D printing aircraft engine
GE's 3D-Printed Airplane Engine Will Run This Year
The last time engineers designed a civilian turboprop engine from scratch for mass-production, humans had not yet landed on the moon. Unlike jet engines, turboprops typically power small commercial shuttles and personal aircraft, but they still represent a multibillion-dollar market. As a result, a new machine created by a team at GE Aviation is now causing a stir.That’s because their engine, called the Advanced Turboprop (ATP), will be the first commercial aircraft engine in history with a large portion of components made by additive manufacturing methods, which include 3D printing. The designers reduced 855 separate parts down to just 12. As a result, more than a third of the engine is 3D-printed.
Engineers working on the ATP are planning to run it for the first time in a special test cell in Prague, Czech Republic, later this year. It should see its first test flight in late 2018, and full production is expected to begin in 2020. It will eventually provide the thrust for Cessna’s new single-engine, 10-person business aircraft design called Denali.
Additive manufacturing has helped the GE team bring the ATP from an idea to a working machine in record time. Announced in 2015, “the ATP is going from a dream to a reality in just two years,” says Gordie Follin, the executive manager of GE Aviation’s ATP program. The normal cycle to get to a running engine is usually twice as long, and it can take as much as 10 years to develop, Follin says. “With additive manufacturing, we’re disrupting the whole production cycle,” he says.
Overall, the 3D-printing effort will pay off by decreasing the finished ATP engine’s weight. The engine is 5 percent lighter, which means it will take the aircraft less fuel to attain the same speed. Design changes will allow the ATP to burn 20 percent less fuel and achieve 10 percent more power than its competitors.
Additive design, which accounts for 35 percent of the engine, is also disrupting maintenance because the ATP will have fewer assembled parts and opportunities for wear. The engine is expected to run 1,000 hours longer between overhauls compared to its competitors. “We’re no longer constrained by traditional design and engineering processes,” Follin says. “3D printing is letting us be more creative than we’ve ever been before.”
Follin’s group has already made all of the engine’s parts. They are now putting them together, adding instrumentation and getting ready to test critical sub-units.
Additive manufacturing also simplifies the supply chain and lowers the opportunities for delays. “These reductions are real,” Follin says. “We’re not putting so much effort into additive manufacturing because it’s a sexy new technology for its own sake. It’s demonstrably better. It lets us disrupt the process.”
GE has been aggressively developing its 3D-printing capabilities in recent years, so far spending $1 billion to mature the technology for its businesses. Last year, the company acquired two manufacturers of 3D-printing machines and launched GE Additive, a new GE business dedicated to supplying 3D printers, materials and engineering consulting services.
Additive manufacturing makes products stronger and more durable. In production aircraft engines, those investments have started paying dividends. CFM International, a joint venture between GE Aviation and Safran Aircraft Engines, is producing the advanced LEAP engine, which is being installed on Airbus’ and Boeing’s new fleet of narrow-body commercial airliners. Complex 3D-printed fuel nozzles on the engine contribute to LEAP’s 15 percent cut in fuel burn and emissions.
Integza's latest 3D printing project: a working electric jet engine
0Shares
Tech Youtuber Integza has showcased his latest 3D printing project, a fully-functional electric jet engine built from scratch.
Loosely based on the design of a conventional turbojet engine, the miniature device doesn’t use jet fuel at all. Instead, it leverages an electric motor, a DIY body made of tin, and an entirely 3D printed compressor fan, generating enough thrust to move a skateboard.
Integza has been trying to 3D print a working jet engine (that doesn’t melt) for some time now, so his latest project is a step towards realizing his long-standing dream.
He said, “I’m very happy about the fact that I built a jet engine and it didn’t melt in the first ten seconds. I mean I’m so happy that I don’t even care about the fact that I accidentally burnt my microphone.”
The electric jet engine generated enough thrust to power a skateboard. Photo via Integza.The beauty of the turbojet engine
The turbojet engine is often regarded as the crème de la crème of jet engines.
What makes the engineering marvel so great is that it actually has a fairly simple working premise. A fast-spinning bladed compressor sucks in air, which is mixed with fuel and ignited in a combustion chamber. The exhaust from the reaction is then directed out the back of the engine, generating thrust.
Turbojet designs are also self-sustaining in that the energy from the exhaust is recycled back into the compressor to keep the entire assembly moving. This is done via a turbine at the back that’s connected to the compressor at the front. This rear turbine is placed in the path of the high-speed exhaust which spins it, in turn spinning the compressor at the front to create a feedback loop. This is also the basic idea behind turbochargers in cars.
While the theory behind turbojets is actually quite digestible, actually building one is an entirely different beast. For turbojets to work, all of the components need to be perfectly balanced and all of the turbines need to spin at up to 25,000RPM or more. This is impossible to achieve in a garage workshop so Integza simply replaced the rear turbine with an electric motor to power the compressor.
Building the electric jet engine
The first step of the project was to build the engine’s casing. For this, he had the idea of repurposing two butane canisters as they already had the right size and shape for the jet engine. Integza emptied the cans out and welded them together to create the body.
Next up was the compressor. Luckily, the compressor is stored in the cold part of the engine away from any heat, so it’s possible to simply 3D print the impeller blades using any run-of-the-mill polymer like ABS.
Now comes the tricky part: creating and controlling the combustion. It wasn’t enough to simply inject butane gas into the body and ignite it, as this would be far too inefficient to generate thrust. The engine needed a steady stream of low-speed, high-pressure air directed towards the back. To enable this, modern-day turbojets use a special type of combustion chamber called an annular combustion chamber, so Integza built his own using a DIY spot welder. He also built a low-cost spark plug for ignition.
Once assembled, he strapped the jet engine to a skateboard and connected it to a battery-powered electric motor to spin the compressor. Amazingly, it worked. Despite weighing in at only 325g, the electric jet engine generated enough thrust to push the 3.2kg skateboard (albeit at a snail’s pace).
Content creators like Integza provide an accessible way for us to learn more about 3D printing and its capabilities. Last year, he also used 3D printing technology to develop a low-cost functional rocket engine inspired by an old, experimental Nazi design. Based on the engine of a 1930s German aircraft called the Heinkel He 176, the 3D printed rocket engine doesn’t rely on burning fuel or combustion at all, instead generating its thrust via a volatile chemical reaction.
More recently, YouTuber Austen Hartley designed and 3D printed his own pair of custom, low-cost Crocs. Armed with nothing but a standard desktop FFF 3D printer and flexible TPU filament, the mechanical engineer even printed a few additional accessories to provide that much-needed flair, including a logo and a sports car spoiler.
Subscribe to the 3D Printing Industry newsletter for the latest news in additive manufacturing. You can also stay connected by following us on Twitter, liking us on Facebook, and tuning into the 3D Printing Industry YouTube Channel.
Looking for a career in additive manufacturing? Visit 3D Printing Jobs for a selection of roles in the industry.
Featured image shows Integza and his electric jet engine. Photo via Integza.
Tags Integza
Kubi Sertoglu
Kubi Sertoglu holds a degree in Mechanical Engineering, combining an affinity for writing with a technical background to deliver the latest news and reviews in additive manufacturing.
Rostec launched serial 3D printing of parts for the PD-14 aircraft engine
Photo: Alexander Utkin
The Center for Additive Technologies (TsAT) of the State Corporation Rostec has started serial 3D printing of parts for the Russian aircraft engine PD-14, developed by the United Engine Corporation. By 2024, it is planned to manufacture about 2 thousand elements of the engine fuel system. nine0007
The Center for Additive Technologies (TsAT) of the State Corporation Rostec has started serial 3D printing of parts for Russian aircraft engines. At the first stage, serial production of elements of the fuel system of the PD-14 engine for the MS-21 aircraft was mastered. By 2024, it is planned to manufacture about 2 thousand elements of the engine fuel system.
Thanks to industrial 3D printing, it is possible to reduce the production time of individual components from six months to three weeks. In addition, additively manufactured components are lighter while maintaining functional properties. This allows you to increase the payload and improve other aircraft characteristics. nine0003
“Modern approaches to the design and manufacture of engines for the domestic aircraft industry, including the use of 3D printing, allow us to increase the production of components that meet the highest international standards of quality and reliability. We see great potential in additive technologies - in the near future, with their help, we will be able to manufacture not only aircraft engines, but also complex components for the space industry, high-tech medicine, automotive industry and other high-tech industries,” the aviation cluster of Rostec State Corporation said. nine0003
PD-14 is the first turbofan engine created in modern Russia. It was developed using modern advanced technologies and domestic materials. It is assumed that the operating costs of PD-14 will be 14-17% lower than those of existing analogues, and the life cycle cost will be 15-20% lower.
In September 2021, TsAT of Rostec received a license from the Russian Ministry of Industry and Trade for serial 3D printing of aviation products, becoming the first and only Russian enterprise to date to confirm its competence in mass industrial 3D printing in the interests of the aviation industry. The license enables the company not only to mass-produce experimental parts and blanks, but also to carry out full-fledged cooperation with the aviation industry. nine0003
TsAT engineers participated in the manufacture of parts for experimental demonstrator engines PD-35, VK-650V and VK-1600V manufactured by the United Engine Corporation, case products for the Ansat-M helicopter, and many others. Today, the Center for Additive Technologies has mastered the production of 450 types of parts.
3D printing Russian Aviation
Tag: 3D printing
nine0002 Photo © Perm Polytechnic University Perm Polytechnic University has developed a methodology that allows designing parts with a complex internal structure, including those consisting of several materials with different characteristics, for which the shape and internal structure are developed for specific production conditions.
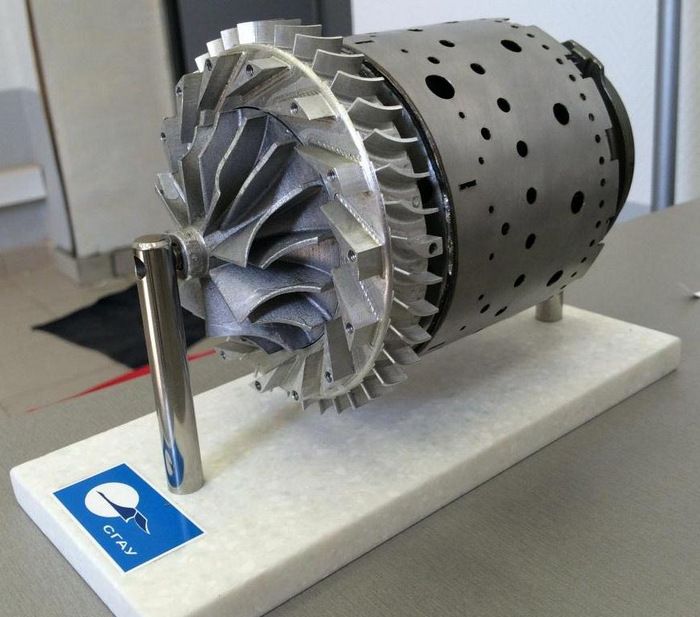
Read more
Aviation News / Technology
Photo © NTU MISiS The National Research Technological University MISiS (Moscow Institute of Steel and Alloys) has developed an economical and highly efficient method for the production of composite metal matrix powders for 3D printing. The obtained materials can be used, in particular, in the aerospace industry in the production of engine parts. Their […]
Read more
Aviation News / Technology
PD-14 engine in the assembly shop of JSC UEC-Perm Motors / Photo © UEC The Center for Additive Technologies (TsAT) launched mass production of components for the PD-14 engine using 3D printing. At the first stage, serial production of engine fuel system elements was mastered. Until 2024, it is planned to produce about […]
Read more
Aircraft Engines / Aviation News
Center for Additive Technologies JSC received a license from the Russian Ministry of Industry and Trade for mass production of products using 3D printing. This is the first Russian enterprise with competencies in the mass industrial application of additive technologies in the interests of the aviation industry. The license allows serial production and testing of components for civil airliners, […]
Read more
Aviation News / Technology
The use of 3D design has a number of significant advantages: it is readability, the use of annotated models as design documentation, and full accounting of all adjacent nodes. All design documentation for the demonstrator of the VK-1600V power plant being created at UEC-Klimov has been released in electronic form. "VK-1600V - the first […]
Read more
Aircraft Engines / Aviation News
The Center for Additive Technologies of the Rostec State Corporation put into operation an automated laser machine with the largest construction area in Russia. The new equipment will make it possible to “grow” large-sized parts of the VK-1600V engine for the Ka-62 helicopter using the 3D printing method. The corporation was told about it. To create components […]
Read more
Aircraft Engines / Aviation News / Technology
The Moscow Aviation Institute announced the launch of a new project - an online 3D printing course of the Laboratory of Additive Technologies, operating on the basis of the Department 904 "Engineering Graphics", the MAI press service reported. “The unique content and experience of MAI teachers will help everyone to immerse themselves in the world of additive technologies, even […]
Read more
Aviation News / Technology
The Center for Additive Technologies put into operation 24 new pieces of equipment for the manufacture of aircraft engine parts using industrial 3D printing. This will allow to increase production volumes by 261% in 2021. The center also received the status of a full cycle service company, which allows organizing mass production […]
More
Aircraft Engines / Aviation News / Technology
In Tatarstan, on the basis of the Kazanbash aviation center, for the first time in Russia, flight tests of the MGTD-20 gas turbine engine manufactured by 3D printing were carried out, the press service of the Advanced Research Foundation (FPI) reported.