3D print a guitar
3D printed guitar accessories - Original Prusa 3D Printers
The ultimate 3d printed accessory for playing guitar is most likely a guitar pick. It’s a super easy and quick print – we have a whole article and video about it. However, it doesn’t end there! You can 3D print many more useful accessories and gadgets – capos, wall mounts, strap locks… Here’s the selection of our favorite models.
Capos
“Oh the song needs a capo, I’m sure I have one… somewhere.” A metal spring-loaded capo costs about $10, the problem is, you never have it on hand when you need it. Somehow, it always ends up in the wrong guitar bag or simply forgotten at home. So it would be really helpful to have a few backup ones.
Download the Ratcheting capo
What does a capo do? Capos are used on fretted string instruments to shorten the string and as a result, raise the pitch. This means that you can play in different keys with the same fingering, rather than having to transpose all the chords to different ones. Changing the key is often used to move the song into your vocal range. Sometimes you can also use it the other way around, to play an easier sequence of chords, while maintaining the original key of the song.
On ukuleles and mandolins, you can get away even with simpler designs. But on the guitar, the force with which the strings need to be held down is quite significant. Without enough pressure, the strings will either be muted or produce an annoying buzzing sound when played. After some searching, we’ve discovered a fantastic design by LoboCNC. It uses a print-in-place hinge and a ratcheting mechanism to clamp down the strings. This makes it very quick to put on and release again. An important feature of a capo, that you’ll often switch its position or remove it completely between songs.
We’ve modified the design slightly (lengthened the ratchet arm) and created a rubber sleeve that can be printed from a flexible filament. It makes it easier to clamp all the strings with enough pressure without having to overtighten the ratcheting mechanism. We would also suggest putting some padding on the side that touches the back of your guitar’s neck. The hard plastic could scratch it, which you definitely want to avoid. A couple of pieces of electrical tape stacked on top of each other will do the job nicely. The ratchet was printed from Prusament PETG Prusa Orange.
Guitar string winder bit
If you’re the kind of person who hasn’t changed the strings on your guitar in years, please, do it for us.😁 Even if you’re not a frequent player, it’s a good idea to change the strings at least once a year, you’ll feel and hear the difference.
If you own a guitar with locking tuners, replacing a guitar string is a breeze. However, on standard tuners, twisting them can get quite tedious. Especially if you’re replacing an entire set of strings. With a printed string winder bit, you can use an electric screwdriver to make the process much faster. For unwinding the string, it’s fantastic. Be extremely careful using it for winding the new string though. As soon as you feel the string getting any tension whatsoever, it’s time to continue winding it by hand. We tested the guitar string winder drill bit by Keksa and Guitar string winder drill bit by bassklampfe, both worked great.
Under String radius gauges
Guitar string height (or action) is something that you can adjust on most electric guitars. Typically, you want the strings as low as possible for comfortable fingering. But also high enough so that even at maximum vibration the string won’t hit the metal frets beneath it and start buzzing. The strings should form a nice arc, matching the radius of the guitar’s neck. You do not want a sudden height change between them. This can be fairly difficult to achieve, especially if it’s the first time you’re adjusting it. With these 3D printed under-string radius gauges by Chris, you can simply raise the strings all the way up and then slowly lower them down, until they touch the gauge. Quite handy!
Wall mounts
Even though the primary purpose of a guitar is obviously to be played, it can also work as a nice room decoration. A few guitars hanging on the wall can completely change the vibe of a room. We were initially a bit skeptical whether a 3D printed wall mount will be strong enough to support the weight of a guitar. But we were pleasantly surprised with how sturdy they are. We tried breaking them, pulling on the guitar or hitting the hanger from the top. The only holder we managed to break was the Guitar holder (normal/wide) – wall mount by Mellloun printed from Silk PLA. The additives which make filament shiny also decrease the layer adhesion. Which is exactly the way the holder failed, clean separation along the layer line. Other filaments we tested did not have this problem, including the Prusament PLA Galaxy Black. When printing these, we suggest using at least 4 perimeters, to increase the mount’s strength.
Guitar wall mount by XYZ_Pierre
Guitar holder (normal/wide) – wall mount by Mellloun
Strap lock
This 10-minute print can prevent your guitar from being dropped and getting damaged. Hopefully, it never happened to you, but some straps have quite a loose fit and catching the guitar just in time after the strap slipped is nerve-wracking. With the strap lock, you don’t have to worry about it anymore. You can print it in black, which will make it almost invisible, match the color of your guitar or choose a nice accent color.
Strap lock on PrusaPrinters.org
Guitar pick holders
One way to mitigate the picks disappearing seemingly into thin air is to print a pick holder. There are tons of designs on PrusaPrinters. The design by Lucas. G a attaches to a mic/guitar stand, it can hold just 3 picks, but they are extremely accessible. The guitar pick holder by Mike VvT is a super simple design, that you can fairly easily re-scale to fit most pick sizes. And the Telecaster guitar pick stand by Ettyl Vrye holds just one pick, but it just looks so funny, it would work great even as a gift for a friend.
What’s next?
In the past, we covered 3D printing and playing on recorders, ocarinas and kazoos. And when talking about playing guitar specifically, we investigated if it’s possible to 3D print guitar picks and how well they perform. But we’re already working on a new project and let’s just say, that this time it’s much bigger than a guitar pick. 😉 Stay tuned for more articles and videos about 3D printed musical instruments and as always – happy printing!
10 3D Printed Guitars You Can Download & Print At Home
Guitars are the first thing many people think of when they hear the words ‘musical instrument.’ While anyone can go out and buy one that can already be found in thousands of homes, a lot of people have taken their hobby to the next level with 3D printed guitars.
Any musician will tell you that the only thing that makes music more satisfying is playing it on an instrument you’ve made yourself, so 3D printed guitars have increased in both popularity and function in recent years.
Guitars are complicated instruments, and so they’re more than a simple click and print job. Many designers have shared their cool and unique creations online, many of which come with detailed instructions and information on where to buy the parts that can’t be easily 3D printed.
Here, we’ll look at some of the coolest looking and sounding 3D printed guitars, pics, and accessories available online, most of which are free!
- See also: our ranking of the coolest 3D printable musical instruments.
- We also have a guide to the coolest things you can 3D print.
The Electric Guitar Project – Amazing Electric 3D Printed Guitar
This design, simply titled ‘Electric Guitar Project’, comes courtesy of a user who claims to be passionate about two things: 3D printing and music.
The Electric Guitar project is a fully playable 3D printed guitar with one of the coolest designs around. The classic Les Paul shape combined with the minimalist body makes for one cool looking 3D printed guitar you can really play!
After much trial and error, the designer was pleased enough to upload all files and information for free, so anyone can 3D print this guitar themselves. If you don’t believe us, check out the video above to hear how it sounds.
Along with the files found here are links to the extra pieces such as strings and an output jack to ensure you have everything you need. Many of these come with video tutorials so you can be as confident as possible when 3D printing this guitar yourself.
The Geartar – 3D printed guitar with gears
One look at the aptly named Geartar, and you’ll have trouble believing it came from a joke request from the designer’s friend.
The shape was copied from the designer’s neglected guitar, and reworked to fit small, battery-powered gears that really turns heads.
Alongside the files for this guitar are in-depth instructions from the designer, including sizes and infill recommendations. As the Geartar was printed using a 1:1 scale of a store-bought model, it can be shrank or grown to any size.
When it comes to 3D printed guitars, the fewer prints the better, but the designer of the Geartar explains that smaller 3D printers can handle this project as long as post-print assembly is done carefully.
All files and instructions for both the Geartar are available for free here, and the gears (which were taken from a different design), can also be downloaded free of charge here.
The AMGP – The Thing of the Week!
The AMGP (or Adapter Modular Guitar Pro) is a guitar made for both guitar aficionados and ‘wannabes’ who are looking for an old school, but no less cool, rock guitar with built in, replaceable pic holster.
This 3D printable guitar is a popular choice for anyone wanting to put their own spin on an old look.
While the instructions and files can be found for free on Thingiverse, the designer recommends going here to ensure the files are as up to date as possible.
The Giger Guitar – Out of This World
The works of H.R. Giger are recognizable to many at a first glance. Their dark, twisted shapes have inspired many artists, but his work is perhaps best known through the Xenomorph of the classic sci-fi horror ‘Alien.’
Musical instruments weren’t to be left out of his influence, thanks to the designer of the Giger Guitar, a 3D printed guitar with Giger’s work (most prominently the alien themself). Any fan of Giger or Ridley Scott’s immensely popular film will definitely want to add this guitar to their 3D print list.
With the files found here, simply follow the laid-out instructions and you’ll have your own 3D printed guitar that’s sure to turn a few heads. The user comments alongside these files show overwhelmingly positive results in both look and playability.
The Black Widow – Deadly Licks
Few guitars, let alone 3D printed guitars, look as cool as The Black Widow. From its meshed design to its light weight, it is without a doubt one of the most attractive 3D printed guitars available online, and the designer has been gracious enough to make the files available for free!
The Black Widow is made from a simple PLA filament, and has a relatively simple post-print assembly. This makes it an ideal first project that’s far less complicated than it looks.
With just a few purchased add-ons, The Black Widow makes an attractive, elegant, and extremely metal guitar!
The Black Widow 3D printed guitar even made it on to our list of the coolest 3D printed musical instruments!
The Compact Bass
Bass guitars may be the definition of cool, but they are known for being larger and heavier than most other kinds of guitar. And so one designer came up with this 3D printed compact bass guitar that’s fully playable and has even been used in gigs!
Like the other guitars on this list, the files are completely free and come with assembly instructions and necessary add-ons to turn this design into a working 3D printed instrument.
They do suggest caution, however, as this 3D printable guitar’s pickup wire has proven to be fragile.
Playable Mini Guitars
Something on an honorable mention on this list are these mini guitars that are still tunable and playable with nothing more than a few rubber bands.
By adjusting the tension on these miniatures, you can change the pitch of the tune played. With enough practice (and some finger strength) you’ll be able to string out a basic tune, strum for a relaxing noise, or tinker and toy away to see what tunes you can play.
While not ‘guitars’ per se, these 3D printed mini guitars are great for musically-inclined fidgeters.
3D Printed Guitar Accessories
Every guitar needs a place to live. For many, this is as simple as buying a case, but for something as special as a 3D printed guitar, you’re going to want a stand or a mount to make sure it’s in view. Fortunately, they can also be 3D printed!
Or, why not make your own 3D printed guitar pick to complete the collection and make each strum that much more your own?
There are plenty of 3D printed guitar stands, mounts, picks, and add-ons to choose from, here we’ll look at some of our favorites.
3D Printed Guitar Stands
Guitar stands are simple structures that keep your guitar stood upright for easy access and even to double as a part of a room’s décor.
This design is a simple print-and-place 3D printed guitar stand for electric guitars that don’t fit comfortably in normal stands.
Acoustic guitar owners may also like this 3D printed guitar stand with a wider base and secure back rest to ensure the instrument heft doesn’t exclude it from being an attractive decoration when not in use.
Guitar Mounts
Whether trying to save space or just prefer the look, 3D printed guitar wall mounts are a cool way to display your instrument in style.
Whether 3D printed or not, a guitar’s wall mount needs to be sturdy and strong. This design for a wall bracket comfortably holds an instrument of 4kg (about 8.8lbs), and can hold a variety of guitars in different sizes.
For a more whimsical look, this Incredible Hulk wall mount is adjustable to wall mount that can hold just about anything, including guitars.
3D Printed Guitar Picks
What guitar player doesn’t want a personal pick to go with their instrument? 3D printed guitar picks are simple, customizable, and always add a personal touch to your sessions.
From this simple design for a standard guitar pick, to this pick complete with spider engraving, 3D printed guitar picks can be made in any color, size, and thickness to match you and your instrument.
For something more creative, these Queen of Hearts guitar picks are beautiful multicolored designs that easily stand out. Their design also allows for the picks to be worn as necklaces or charms which not only looks cool, but also makes them difficult to lose.
Speaking of, guitar picks are notorious for vanishing into thin air. It’s not uncommon to carry spares or wearable ones to ensure they stay on you and in sight, but another way is to make your own 3D printed guitar pick holders.
These holders range from small boxes like the one found here, to this creative design for a 3D printed guitar pick stand that looks like an actual guitar!
A guitar on a 3D printer or a summer project
Good afternoon, dear readers. Today's article will no longer be an overview, but a creative and practical one, dedicated to hobbies and hobbies.
Introductory lyrics.
In my student years, I happened to play the rhythm guitar in a musical group whose work was in the style of Heavy / Speed Metal (in a simple way - they played ROCK).
Every year, I and probably many of you think that life flies by, accelerating and accelerating, and somewhere far away there are dreams and there is absolutely no time for their fulfillment. But nostalgia and the desire not to give in to despair sometimes help make dreams come true or return to a long-forgotten hobby. This happened to me as well. I managed to escape from the working routine, and pick up the guitar again. Having acquired a tool, I began to restore long-forgotten skills. nine0003
At one fine moment, the instrument became "not enough" and I wanted to buy something else that sounded different. I considered various options, and at some point the thought came - why not assemble the guitar myself. There is a 3D printer, there are filaments, examples of manufacturing are in plain sight. So the idea of a 3D printed guitar slowly began to flicker, until an interesting project caught my eye:
Why not, I said to myself. Found the description of the project on thingiverse. The body of this instrument was based on the design of guitars from the "state" manufacturer Strandberg guitar. Exactly what is needed! But without backlight - it's superfluous. nine0003
Preparation
"Wishlist" is not enough to make wishes come true, so a rough list of everything needed for manufacturing was compiled:
3D printer
Picaso Designer Classic. None of them were suitable for the project, because did not have enough printable area for those models that are hosted on Thingiverse. There was no desire to break / saw the finished models, especially the central part of the guitar, to which the neck was to be attached, the pickups were to be placed, and also where the tremolo was installed. This is the most loaded part of the case and should have been printed in its entirety without breakdown. nine0003
As a result, after turning and twisting the models in slicers, it was decided to print on Picaso, because in principle, everything was placed at an angle, except for the central part, and the quality of the printed wall on this machine was quite suitable for my tasks. It was decided to print the central part at a printing studio or ask friends with larger printers.
Printable plastic
The author of the project on Thingiverse made a guitar from PLA plastic, but I did not like this option at all, since in this case the guitar would have to be primed and painted. My task was to make a tool without post-processing and painting, so that it could be seen that it was made using 3D printing, but at the same time, it did not have a completely collective-farm look. After looking through the reviews of plastics on 3Dtoday, I decided to focus on composites, especially since I had a shareware promo reel of FormaX composite from REC3D. Once, at one of the 3D printing exhibitions, I happened to turn a part made of this material in my hands, and then I also noticed an interesting visual effect that hides layers and makes the surface of products pleasant to the touch. An additional plus in this solution was the presence of carbon fiber additives in the filament, which should create additional shielding (so that the guitar does not "start" when played). nine0003
Donor guitar
Inventing a printed neck is, of course, beyond the bounds, so only the body should be printed, but let's look for the neck, and at the same time all the electronics from the donor guitar will come in handy. There were a lot of options on avito, and in the end, Jackson, who had seen life, was purchased as a donor:
At home, the guitar was immediately dismantled, the neck was washed, polished and put in order. (guitars need to be looked after, of course).
Electronics from the guitar was also included in the project. I really liked the black and white combination of pickups. Yes, and FormaX is also black. The only thing that didn't fit the project from the donor was the tremolo bridge - "that iron thing with twists on the body, to which the strings are attached." nine0003
In a music store I picked up an inexpensive option + they also gave me cheap Olympia strings as a gift:
Test printing and fitting of the model x).
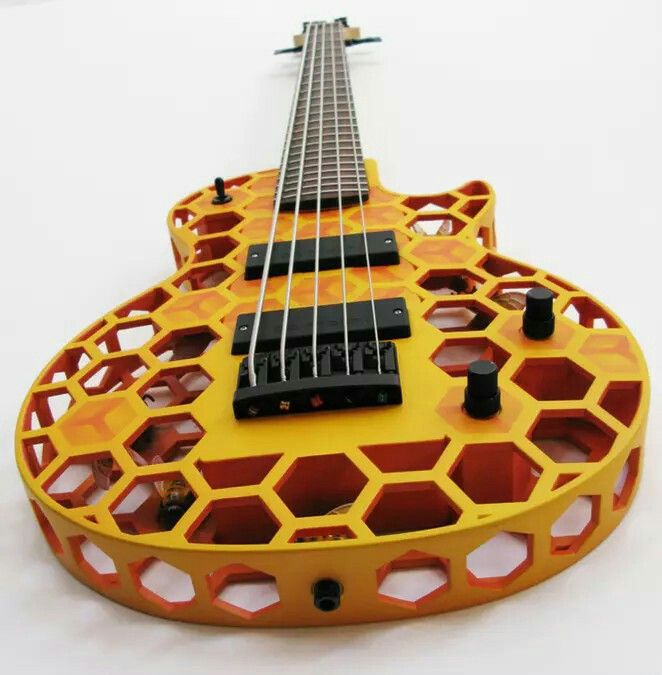
Pleasant enough structure.
Another test - printing a piece of the central part of the guitar to assess the strength with a given infill.
Print settings:
- Nozzle temperature: 280°C.
- Table temperature: 95 °C.
- No airflow
- Table adhesive: PICASO 3D printing adhesive.
- Supports strictly from the table (otherwise the internal communication channels will be flooded)
Nozzle in thermoblock steel: 0.5 mm.
The model shows a defect on the wall. Most likely the reason is in the feed - the material is abrasive and can get stuck in the nozzle. Therefore, we will play with temperatures and retracts during further printing.
Also during the test prints with "formax" it became clear that in order to obtain a better surface, it is better to place the part at an angle. In this case, the top, covering layers (which are the front side of the case) will be just as perfect as the side ones. nine0003
Running a little ahead of the story , I show a photo with examples of printing the same part printed at an angle (left) and just on a table (right). The question of further orientation of the model on the table immediately disappeared.
The right part was printed by the PICASO 3D 3D printer farm on the PICASO Designer XL PRO printer at my request. By my mistake in the TOR - the location of the part was flat on the platform and using supports not only from the surface, which led to the fact that the internal cavities for laying communications were filled with plastic, and the surface itself had an unpresentable appearance. I will write about the left part a little later - but I managed to fit it into PICASO Classic and it was printed at an angle. nine0003
As a result of all the trials and tests, it was decided to print all parts at an angle and spend plastic on supports (walk, walk) - I didn’t want to stop the project. To celebrate, another FormaX coil was purchased.
The first quality print result met all expectations:
From different angles, the plastic plays with both color and texture.
Here are some photos of the rest of the print:
All photos are attached in the original size - you can click the mouse and look closer. The material is absolutely fantastic. After it, I don’t want to look in the direction of PLA and ABS.
I had to stop printing several times due to problems:
As a result, I got parts for assembling as many as two guitars. In the photo below, parts rejected for various reasons.
As for the central part of the guitar - I still managed to fit it on the table in the slicer at a certain angle, but when printing, the corner of the model was "eaten", although everything should have fit. nine0003
The problem was found during communication with the representative of PICASO, Kapiton (very competent specialist) . It turned out that with the declared height of the print area, in fact, almost half a centimeter is missing. As it turned out, there was a special revision of the part that protects the coupling under the table screw, and the one that was installed on my printer was larger. They promptly sent me an STL model, I printed it from ABS and replaced it - everything immediately began to fit in height)
Such a stunning surface of parts made from this material. Without post-processing:
While the parts were printed and reprinted, I gutted the donor:
Everything was neatly disassembled, cleaned and set aside for further assembly of the printed version.
During the work, a problem was found in the central part - the neck did not fit into place. He crawled onto the body and covered the part of the pickup with an overlay:
I did not want to cut the neck and it was decided to increase the size of the platform on which it is attached. Since I'm not good at editing STL, I asked Ivan (Plastmaska) for help.
Thanks to Ivan, the printing of the third version of the central part of the body was launched on the same day and the next I had the opportunity to join the parts and evaluate what happened:
Next, the parts were fastened together with using 7 screws M3x10 and 2 screws M3x20 and followed by the assembly of electronics, wiring, installation of the tremolo bridge and neck:
Here I ran into the problem that the power of my "children's" soldering iron for soldering electronics is not enough. I had to call out in 3D chats and Ivan Kashirin (known to many printers in St. Petersburg) came to the rescue. The guitar was carefully transported to Vanya's office and all the electronics were carefully soldered:
After assembly and soldering, it remained to put the strings, set their height, adjust the scale and install printed covers that cover the technological connectors on the back of the case. nine0003
Tuning and maintenance of the guitar was handled by Mikhail Marchenko, a professional in his field. I highly recommend those. who needs to put the instrument in order - https://vk.com/marchenko_mikhail.
A few photos:
Surely many people have a question - why did the project take the whole summer. In general, everything could be done slowly in 3-4 days, but summer is vacations, summer cottages, a lot of work for yourself and that guy, and there wasn’t much time to get down to business. nine0003
Well, a quick video. Happy listening everyone.
A new development for guitars - 3D printed pickups (+ video)
Now 3D printing has reached the point where it can be used to print a guitar that sounds exactly the same as a traditionally produced instrument. However, in addition to this, 3D printing technologies can be used to radically change the way you play the guitar. nine0003
Looking for an innovative way to use guitars, Andrew Strassell, owner of an independent custom guitar company, came up with an idea that could really revolutionize the industry. One of the main disadvantages of electric guitars is that the pickups that pick up the vibrations of the strings are almost impossible to replace. Since different types of pickups produce different tones, players who want to experiment with sound usually have to use multiple guitars. This is not only expensive and irrational with a limited budget, but also not very convenient, since you have to constantly change tools during the game. nine0003
It's not that the pickups can't be replaced, it's just that the process is time consuming and requires the entire instrument to be taken apart and reassembled, so there is a risk of damage to the guitar. However, Strassell has designed a guitar that uses a 3D-printed cartridge cartridge that is as easy to replace as inserting a different game cartridge into a video console. Thus, musicians will be able to easily switch between the traditional sound of hard rock, blues or country if they wish. In addition, guitarists will be able to install the cartridge upside down - thereby obtaining a reverse polarity, which opens up new facets of sonic experimentation. All this can be done in seconds on the same guitar. nine0003
“The biggest beneficiaries of this development are small local groups. They no longer have to spend $1,500 on a Les Paul that they would never take apart because it cost so much. Our solution is much more advanced than the cheap Korean-made guitars, and provides a lot more options,” says Straussell.
“There is a lack of innovation in this area, it's just that no one is promoting it. Fewer people want to play the guitar, and I believe that this is one of the fundamental musical instruments. Guitar manufacturers are basically reissuing the same half-century-old models. I think there is a demand for innovation in this industry and we need to rethink our vision of tools,” Strassell explains.