3D printers nyc
3D Printing | Large-Scale | The Factory NYC
3D-Printing
LARGE-SCALE 3D-PRINTING SERVICES
Massive 3D PrintsWe offer large-scale 3d printing for artists, engineers, and designers. Individual parts at 72" (177cm), and even larger with sectional fabrication. Start with a napkin sketch, a physical object to scan, or with fully engineered CAD files. Our design and production team at The Factory NYC will bring your project to life. Start your Project |
Oversized 3D-printed headphones with built-in audio made for City Eventions |
Start thinking in 3DRapid large-scale 3D Printing opens up a world of possibilities.
|
The future of storytelling is sculptural(and it's here)
Click to set custom HTML |
Big Print EnergyThe Factory NYC is the only event fabricator in NYC with a large-format 3D-printer — and its up to a 100x times faster than typical 3D Printing; and there is no size limit. |
Requirements
Adding sculpture to your next event is easy. You don't need 3D modelers on your team — we have you covered. The only requirement is bring your vision with a budget. We can accommodate your design concept for most situations:
Even if you just have a 2D logo or design on pen and paper. We can create a digital model from scratch, and/or use 3D models from open source libraries. There are many ways to get started. |
Huge 3D-Printing — Get Inspired and Imagine
Delivering amazing projects, daily.![]() | Our team of installers works throughout the New York City greater area. Local, domestic, and international delivery available through air, land, and sea. |
Join our Email list:
Sign up, and we'll share the latest event fabrication technologies:
3D Printing Service New York | Instant Quotes Online
Our 3D printing capabilities
We have over 90 3D printing shops in our network and are well known for manufacturing high-quality parts at competitive prices, from rapid prototyping with Fused Deposition Modeling (FDM) to functional end parts made with Selective Laser Sintering (SLS) or Multi Jet Fusion (MJF).
Gallery of 3D printed parts manufactured by Hubs
With over 65,000 customers from every industry, including aerospace, defense, robotics, medical, machinery, automotive and electronics, we have extensive experience meeting a diverse range of 3D printing requirements, from prototyping to production: Visual aids, concept models, injection-molding prototypes, form-fit & function prototypes, tooling and casting patterns, jigs, grips and fixtures, and durable end parts.
HP PA 12 - Dyed Black
Customer | True North Design |
Purpose | Structural and vacuum EOAT components |
Process | SLS / MJF |
Unit price | $69.23 / $34.33 |
Industry | Automotive |
Prototyping PLA
Customer | Allision Conner |
Purpose | End caps and cable strain relief for sheet metal enclosure |
Process | FDM |
Unit price | $7.92 / $4.72 / $2.80 |
Industry | Industrial Automation |
HP PA 12
Customer | US Hammer |
Description | A part for gasoline engine powered jackhammers |
Process | MJF |
Unit price | $22.![]() |
Industry | Construction |
Markforged Onyx - Black
Customer | Autocom Manufacturing |
Purpose | A production part for 3D printed lathe gantry gripper fingers |
Process | FDM |
Unit price | $48.86 |
Industry | Automotive |
PC Stratasys - white
Customer | Terumo medical corporation |
Purpose | Prototyping parts used for a disposable electrical device |
Process | FDM |
Unit price | $55.38 / $32.96 |
Industry | Medical |
Formlabs Clear Resin
Customer | Aversan Inc |
Purpose | A prototyping part of an injection molded component for an automated door mechanism |
Process | SLA |
Unit price | $29.![]() |
Industry | Aerospace |
HP PA 12 - Dyed Black
Customer | True North Design |
Purpose | Structural and vacuum EOAT components |
Process | SLS / MJF |
Unit price | $69.23 / $34.33 |
Industry | Automotive |
Prototyping PLA
Customer | Allision Conner |
Purpose | End caps and cable strain relief for sheet metal enclosure |
Process | FDM |
Unit price | $7.92 / $4.72 / $2.80 |
Industry | Industrial Automation |
HP PA 12
Customer | US Hammer |
Description | A part for gasoline engine powered jackhammers |
Process | MJF |
Unit price | $22.![]() |
Industry | Construction |
Markforged Onyx - Black
Customer | Autocom Manufacturing |
Purpose | A production part for 3D printed lathe gantry gripper fingers |
Process | FDM |
Unit price | $48.86 |
Industry | Automotive |
PC Stratasys - white
Customer | Terumo medical corporation |
Purpose | Prototyping parts used for a disposable electrical device |
Process | FDM |
Unit price | $55.38 / $32.96 |
Industry | Medical |
Formlabs Clear Resin
Customer | Aversan Inc |
Purpose | A prototyping part of an injection molded component for an automated door mechanism |
Process | SLA |
Unit price | $29.![]() |
Industry | Aerospace |
HP PA 12 - Dyed Black
Customer | True North Design |
Purpose | Structural and vacuum EOAT components |
Process | SLS / MJF |
Unit price | $69.23 / $34.33 |
Industry | Automotive |
Prototyping PLA
Customer | Allision Conner |
Purpose | End caps and cable strain relief for sheet metal enclosure |
Process | FDM |
Unit price | $7.92 / $4.72 / $2.80 |
Industry | Industrial Automation |
HP PA 12
Customer | US Hammer |
Description | A part for gasoline engine powered jackhammers |
Process | MJF |
Unit price | $22.![]() |
Industry | Construction |
Markforged Onyx - Black
Customer | Autocom Manufacturing |
Purpose | A production part for 3D printed lathe gantry gripper fingers |
Process | FDM |
Unit price | $48.86 |
Industry | Automotive |
PC Stratasys - white
Customer | Terumo medical corporation |
Purpose | Prototyping parts used for a disposable electrical device |
Process | FDM |
Unit price | $55.38 / $32.96 |
Industry | Medical |
Formlabs Clear Resin
Customer | Aversan Inc |
Purpose | A prototyping part of an injection molded component for an automated door mechanism |
Process | SLA |
Unit price | $29.![]() |
Industry | Aerospace |
HP PA 12 - Dyed Black
Customer | True North Design |
Purpose | Structural and vacuum EOAT components |
Process | SLS / MJF |
Unit price | $69.23 / $34.33 |
Industry | Automotive |
Prototyping PLA
Customer | Allision Conner |
Purpose | End caps and cable strain relief for sheet metal enclosure |
Process | FDM |
Unit price | $7.92 / $4.72 / $2.80 |
Industry | Industrial Automation |
HP PA 12
Customer | US Hammer |
Description | A part for gasoline engine powered jackhammers |
Process | MJF |
Unit price | $22.![]() |
Industry | Construction |
Markforged Onyx - Black
Customer | Autocom Manufacturing |
Purpose | A production part for 3D printed lathe gantry gripper fingers |
Process | FDM |
Unit price | $48.86 |
Industry | Automotive |
PC Stratasys - white
Customer | Terumo medical corporation |
Purpose | Prototyping parts used for a disposable electrical device |
Process | FDM |
Unit price | $55.38 / $32.96 |
Industry | Medical |
Formlabs Clear Resin
Customer | Aversan Inc |
Purpose | A prototyping part of an injection molded component for an automated door mechanism |
Process | SLA |
Unit price | $29.![]() |
Industry | Aerospace |
HP PA 12 - Dyed Black
Customer | True North Design |
Purpose | Structural and vacuum EOAT components |
Process | SLS / MJF |
Unit price | $69.23 / $34.33 |
Industry | Automotive |
Prototyping PLA
Customer | Allision Conner |
Purpose | End caps and cable strain relief for sheet metal enclosure |
Process | FDM |
Unit price | $7.92 / $4.72 / $2.80 |
Industry | Industrial Automation |
HP PA 12
Customer | US Hammer |
Description | A part for gasoline engine powered jackhammers |
Process | MJF |
Unit price | $22.![]() |
Industry | Construction |
Markforged Onyx - Black
Customer | Autocom Manufacturing |
Purpose | A production part for 3D printed lathe gantry gripper fingers |
Process | FDM |
Unit price | $48.86 |
Industry | Automotive |
PC Stratasys - white
Customer | Terumo medical corporation |
Purpose | Prototyping parts used for a disposable electrical device |
Process | FDM |
Unit price | $55.38 / $32.96 |
Industry | Medical |
Formlabs Clear Resin
Customer | Aversan Inc |
Purpose | A prototyping part of an injection molded component for an automated door mechanism |
Process | SLA |
Unit price | $29.![]() |
Industry | Aerospace |
HP PA 12 - Dyed Black
Customer | True North Design |
Purpose | Structural and vacuum EOAT components |
Process | SLS / MJF |
Unit price | $69.23 / $34.33 |
Industry | Automotive |
Prototyping PLA
Customer | Allision Conner |
Purpose | End caps and cable strain relief for sheet metal enclosure |
Process | FDM |
Unit price | $7.92 / $4.72 / $2.80 |
Industry | Industrial Automation |
HP PA 12
Customer | US Hammer |
Description | A part for gasoline engine powered jackhammers |
Process | MJF |
Unit price | $22.![]() |
Industry | Construction |
Markforged Onyx - Black
Customer | Autocom Manufacturing |
Purpose | A production part for 3D printed lathe gantry gripper fingers |
Process | FDM |
Unit price | $48.86 |
Industry | Automotive |
PC Stratasys - white
Customer | Terumo medical corporation |
Purpose | Prototyping parts used for a disposable electrical device |
Process | FDM |
Unit price | $55.38 / $32.96 |
Industry | Medical |
Formlabs Clear Resin
Customer | Aversan Inc |
Purpose | A prototyping part of an injection molded component for an automated door mechanism |
Process | SLA |
Unit price | $29.![]() |
Industry | Aerospace |
HP PA 12 - Dyed Black
Customer | True North Design |
Purpose | Structural and vacuum EOAT components |
Process | SLS / MJF |
Unit price | $69.23 / $34.33 |
Industry | Automotive |
Prototyping PLA
Customer | Allision Conner |
Purpose | End caps and cable strain relief for sheet metal enclosure |
Process | FDM |
Unit price | $7.92 / $4.72 / $2.80 |
Industry | Industrial Automation |
HP PA 12
Customer | US Hammer |
Description | A part for gasoline engine powered jackhammers |
Process | MJF |
Unit price | $22.![]() |
Industry | Construction |
Markforged Onyx - Black
Customer | Autocom Manufacturing |
Purpose | A production part for 3D printed lathe gantry gripper fingers |
Process | FDM |
Unit price | $48.86 |
Industry | Automotive |
PC Stratasys - white
Customer | Terumo medical corporation |
Purpose | Prototyping parts used for a disposable electrical device |
Process | FDM |
Unit price | $55.38 / $32.96 |
Industry | Medical |
Formlabs Clear Resin
Customer | Aversan Inc |
Purpose | A prototyping part of an injection molded component for an automated door mechanism |
Process | SLA |
Unit price | $29.![]() |
Industry | Aerospace |
HP PA 12 - Dyed Black
Customer | True North Design |
Purpose | Structural and vacuum EOAT components |
Process | SLS / MJF |
Unit price | $69.23 / $34.33 |
Industry | Automotive |
Prototyping PLA
Customer | Allision Conner |
Purpose | End caps and cable strain relief for sheet metal enclosure |
Process | FDM |
Unit price | $7.92 / $4.72 / $2.80 |
Industry | Industrial Automation |
HP PA 12
Customer | US Hammer |
Description | A part for gasoline engine powered jackhammers |
Process | MJF |
Unit price | $22.![]() |
Industry | Construction |
Markforged Onyx - Black
Customer | Autocom Manufacturing |
Purpose | A production part for 3D printed lathe gantry gripper fingers |
Process | FDM |
Unit price | $48.86 |
Industry | Automotive |
PC Stratasys - white
Customer | Terumo medical corporation |
Purpose | Prototyping parts used for a disposable electrical device |
Process | FDM |
Unit price | $55.38 / $32.96 |
Industry | Medical |
Formlabs Clear Resin
Customer | Aversan Inc |
Purpose | A prototyping part of an injection molded component for an automated door mechanism |
Process | SLA |
Unit price | $29.![]() |
Industry | Aerospace |
HP PA 12 - Dyed Black
Customer | True North Design |
Purpose | Structural and vacuum EOAT components |
Process | SLS / MJF |
Unit price | $69.23 / $34.33 |
Industry | Automotive |
Prototyping PLA
Customer | Allision Conner |
Purpose | End caps and cable strain relief for sheet metal enclosure |
Process | FDM |
Unit price | $7.92 / $4.72 / $2.80 |
Industry | Industrial Automation |
HP PA 12
Customer | US Hammer |
Description | A part for gasoline engine powered jackhammers |
Process | MJF |
Unit price | $22.![]() |
Industry | Construction |
Markforged Onyx - Black
Customer | Autocom Manufacturing |
Purpose | A production part for 3D printed lathe gantry gripper fingers |
Process | FDM |
Unit price | $48.86 |
Industry | Automotive |
PC Stratasys - white
Customer | Terumo medical corporation |
Purpose | Prototyping parts used for a disposable electrical device |
Process | FDM |
Unit price | $55.38 / $32.96 |
Industry | Medical |
Formlabs Clear Resin
Customer | Aversan Inc |
Purpose | A prototyping part of an injection molded component for an automated door mechanism |
Process | SLA |
Unit price | $29.![]() |
Industry | Aerospace |
HP PA 12 - Dyed Black
Customer | True North Design |
Purpose | Structural and vacuum EOAT components |
Process | SLS / MJF |
Unit price | $69.23 / $34.33 |
Industry | Automotive |
Prototyping PLA
Customer | Allision Conner |
Purpose | End caps and cable strain relief for sheet metal enclosure |
Process | FDM |
Unit price | $7.92 / $4.72 / $2.80 |
Industry | Industrial Automation |
HP PA 12
Customer | US Hammer |
Description | A part for gasoline engine powered jackhammers |
Process | MJF |
Unit price | $22.![]() |
Industry | Construction |
Markforged Onyx - Black
Customer | Autocom Manufacturing |
Purpose | A production part for 3D printed lathe gantry gripper fingers |
Process | FDM |
Unit price | $48.86 |
Industry | Automotive |
PC Stratasys - white
Customer | Terumo medical corporation |
Purpose | Prototyping parts used for a disposable electrical device |
Process | FDM |
Unit price | $55.38 / $32.96 |
Industry | Medical |
Formlabs Clear Resin
Customer | Aversan Inc |
Purpose | A prototyping part of an injection molded component for an automated door mechanism |
Process | SLA |
Unit price | $29.![]() |
Industry | Aerospace |
Instant, online 3D printing quotes
-
Upload a CAD to start (STEP, STP, IGES, IGS, SLDPRT, 3DM, SAT, STL, OBJ or X_T)
-
Price updates in real-time as you change materials, lead time, etc..
-
No hidden costs. Our instant quotes are not just indications, but the actual price, and include shipping and customs up front.
Learn about how our quoting algorithm works
Our ordering process
Receive instant quote
Upload your CAD to our online quoting platform
Confirm specs
Configure your part specifications and select a lead time that suits your schedule
Production
We select the best manufacturer for your order, and production begins immediately
Quality control
We take full responsibility for making sure your parts are manufactured according to our standards
Delivery
Our 3D printing service has been rated 4.
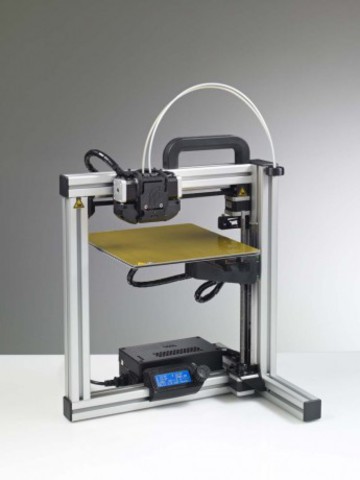
Over 208 customers are satisfied with our 3D printing service.
“Great prints, great communication. Will use this seller again.”
“looks like the photos, was a tough print and will serve its purpose well”
“Just as expected. Fast delivery. No issues.”
“Awesome service and great products. Couldnt ask for more.”
“Great job and shipped quickly. Item was received before quoted delivery date. ”
“Service was quick, friendly and well done. will use in the future. ”
“Quick and courteous,with high qualify results, I would definitely work with them again”
“Very prompt communication, excellent print finish, met all my expectations.”
“The best 3D printing service in the world !”
“Always PERFECT Prints. I measure with calipers. Oh, and fast shipping. What more could you want? Best printer around!”
“Print as expected. Communication and flexibility was excellent.”
“Well packaged, on time, and got frequent updates.”
“Outstanding quality and quick delivery, would order again any time. ”
“Great service. Communications and speed were exceptional.”
“Arrived quickly with updates throughout the process, exactly as requested.”
“My order was printed and shipped quickly. Excellent service and communication.”
“I ordered a print at the cheapest level and the quality is much better than I anticipated. These guys examined my drawings in no time, got the print started, snapped images post-print, and got it out the door in the same day. A+ service.”
“Great part, works and fits exactly as i needed”
“Excellent service. Great person. Very helpful. Quality work!!!”
“Perfect. Prints were started the day of upload and delivered before the deadline. Quality is near perfect! ”
“Great communication and custom part fit perfectly. Thanks! ”
“Always a wonderful experience and perfect print. Thank you!”
“Fast turnaround, quality print, good price.”
“Very quick and professional. Will buy from again. ”
“Great communication and printed parts looked great. Highly recommend!”
Show more reviews
Show less reviews
Teams build better parts
Create your Hubs team and start collaborating
Read more
The Hubs Standard - consistent quality, every time
Hubs takes the stress out of manufacturing by guaranteeing the quality and consistency of every part. Each order is dimensionally and visually inspected to make sure it meets the Hubs Standard.
3D printing materials
We can generate instant 3D printing quotes for 25+ plastics. For metal 3D-printed parts, you can request a quote from our parent company, Protolabs.
Available materials
SLS
PA 12 Glass filled PA 12
Desktop FDM
Prototyping PETG Prototyping ASA Prototyping TPU Prototyping ABS Prototyping PLA
Desktop SLA
Formlabs Standard Resin Formlabs Clear Resin Formlabs Tough Resin 2000 Formlabs Rigid Resin 4000 Formlabs Grey Pro Resin Formlabs Flexible Resin 80A Formlabs High Temp Resin Formlabs Durable Resin
MJF
HP PA 12 Glass filled HP PA 12
Industrial FDM
Markforged Onyx ABSplus Stratasys ULTEM 9085 Stratasys Stratasys ASA ABS M30 Stratasys ULTEM 1010 Stratasys
Industrial SLA
Accura 25 (PP-like) Accura ClearVue Accura Xtreme White 200 (ABS-like)
3D printing locations near New York
Middletown, NY Scranton, PA Binghamton, NY
Kingston, NY East Stroudsburg, PA Union, NY
Utica, NY Poughkeepsie, NY Ramapo, NY
Parsippany
The 3D Printing Handbook
No one understands 3D printing like us - our founders literally wrote the book. Click here to download the sample chapters.
Buy the book from Amazon
FAQ's
How much does your 3D printing service cost?
The cost of your 3D printed parts depends on factors such as part volume, part complexity, choice of material, which 3D printing technology is used, and if any post processing is required. For more details on these cost factors, see our article on the cost of 3d printing. To check the cost of your 3D printed part, simply upload a CAD (.STL) file and select your material and 3D printing technology to receive a quote within seconds.
How do you guarantee the quality of my prints?
Your parts are made by experienced 3D printing shops within our network. All facilities are regularly audited to ensure they consistently meet the Hubs quality standard. We include a standardized inspection report with every order and offer a First Article Inspection service on orders of 100+ units.
We have partners in our network with the following certifications, available on request: ISO9001, ISO13485 and AS9100.
Follow this link to read more about our quality assurance measures.
How do I select the right 3D printing process for my prints?
You can select the right 3D printing process by examining which materials suit your need and what your use case is.
By material: if you already know which material you would like to use, selecting a 3D printing process is relatively easy, as many materials are technology specific.
By use case: once you know whether you need a functional or visual part, choosing a process is easy.
For more help, read our guide to selecting the right 3D printing process. Find out more about Fused Deposition Modeling (FDM), Selective Laser Sintering (SLS), Multi Jet Fusion (MJF) and Stereolithography (SLA).
How can I reduce the cost of my 3D prints?
In order to reduce the cost of your 3D prints you need to understand the impact certain factors have on cost. The main cost influencing factors are the material type, individual part volume, printing technology and post-processing requirements.
Once these have been decided, an easy way to further cut costs is to reduce the amount of material used. This can be done by decreasing the size of your model, hollowing it out, and eliminating the need for support structures.
To learn more, read our full guide on how to reduce the cost of 3D printing.
Where can I learn more about 3D printing?
Our knowledge base is full of in-depth design guidelines, explanations on process and surface finishes, and information on how to create and use CAD files. Our 3D printing content has been written by an expert team of engineers and technicians over the years.
See our complete engineering guide to 3D printing for a full breakdown of the different 3D printing technologies and materials. If you want even more 3D printing, then check out our acclaimed 3D printing handbook here.
We have an extensive range of online resources developed to help engineers improve their capabilities.
Introductory guides
Design guides
Material guides
Applications
CAD & file preparation
Post processing & finishing
Our other manufacturing capabilities
CNC machining
CNC machining
Milling (3-, 4- & full 5-axis), turning and post-processing
-
50+ metals and plastics & 10 surface finishes
-
Tolerances down to ±.0008” (0.020 mm)
-
Lead times from 5 business days
See our CNC machining services
Put your 3D printed parts into production today
Get an instant 3D printing quote
A Brief History of 3D Printing / Sudo Null IT News
3D printing was born 40 years ago and opened up amazing possibilities for creating various models in prototyping, dentistry, small-scale production, customized products, miniatures, sculptures, mock-ups and much more.
Who invented the 3D printer? What was the first 3D printing technology? And what was the first thing they printed on a 3D printer? Let's open the veil of secrecy over a huge number of interesting facts and stories about the emergence of technology. 9. , which layer-by-layer formed a rigid object from a photopolymer resin with the help of UV illumination.
In fact, he described a modern photopolymer printer, but failed to provide the necessary data for patent registration within a year, as required by patent law, and abandoned the idea. However, in many sources it is he who is called the inventor of 3D printing technology.
In 1983, three engineers - Alain Le Meho, Olivier de Witt and Jean-Claude André from the French National Center for Scientific Research, in an attempt to create what they called a "fractal object", came up with the idea of using a laser and a monomer, which, under the influence of a laser, turned into a polymer. They applied for a patent 3 weeks before the American Chuck Hal. The first object created on the apparatus was a spiral staircase. Engineers called the technology stereolithography, and the patent was approved only in 1986 year. Thanks to them, the most famous file format for 3D printing is called STL (from the English stereolithography). Unfortunately, the institute did not see any prospects in the invention and its commercialization, and the patent was not used to create the final product.
Laser Stereolithography At the same time, Chuck Hull was working for a company that made countertop and furniture coatings using UV lamps. The production of small plastic parts for prototyping new product designs took up to two months. Chuck came up with the idea to speed up this process by combining UV technology and layering thin plastic. The company gave him a small laboratory for experiments, where he worked in the evenings and weekends. As a material, Chuck used acrylic-based photopolymers that harden under the influence of ultraviolet radiation. One night, after months of experimentation, he was finally able to print a sample and was so elated by luck that he walked home. Chuck showed his invention to his wife. It was an eyewash cup, more like a communion cup, according to the wife. It is considered officially the first 3D printed model in the world and is still kept by the Hull family, and after their death will be transferred to the Smithsonian Research Institute in Washington.
Chuck Hull filed a patent on August 8, 1984 and was approved on March 11, 1986. The invention was called "Apparatus for creating three-dimensional objects using stereolithography." Chuck founded his own company - 3D Systems, and in 1988 launched the first commercial 3D printer - the SL1 model.
Carl Deckard and Joe Beeman (right), inventors of SLS 3D printing (1987) Another new 3D printing method appeared around the same time as SLA printing. This is selective laser sintering SLS , which uses a laser to turn loose powder (instead of resin) into a solid material. Carl Deckard , a young undergraduate student at the University of Texas at Austin, and his instructor Prof. Dr. Joe Beeman were involved in the development. And the idea belonged to Karl. In 1987, they co-founded Desk Top Manufacturing (DTM) Corp. However, it will take at least another 20 years for SLS 3D printing to become commercially available to the consumer. In 2001, the company was bought out by Chaka Hull, 3D Systems.
Surprisingly simpler and cheaper 3D printing is FDM (Fused Deposition Modeling) was created after SLA and SLS, in 1988. Its author was aeronautical engineer Scott Crump . Crump was looking for an easy way to make a toy frog for his daughter and used a hot glue gun to melt the plastic and pour it into layers. Thus, the idea of FDM 3D printing was born, a technology for layer-by-layer deposition of a plastic thread. Crump patented a new idea and co-founded Stratasys with his wife Lisa Crump at 1989 year. In 1992, they launched their first production product, the Stratasys 3D Modeler, on the market.
Milestone 2: 3D printing becomes available
The first machines built by 3D Systems and Stratasys were bulky and expensive. The cost of one was hundreds of thousands of dollars, and only the largest companies in the automotive and aerospace industries could use them. Printers had a lot of limitations and could not be widely used. The development of technology has been very slow. 20 years later, in 2005, the RepRap (Replicating Rapid Prototyper) project appeared - a self-replicating mechanism for rapid prototyping.
It was inspired by Dr. Adrian Bauer from the University of Bath in the UK. The aim of the project was to "self-copy", replicate the components of the 3D printers themselves. In the photo, all the plastic parts of the "child" are printed on the "parent". But in fact, a group of enthusiasts led by Adrian were finally able to create the budget 3D printer for home or office use.
The idea was quickly taken up by three New York technologists and started a desktop FDM printer company, MakerBot. This was the second turning point in the modern history of 3D printing.
Other technologies were being developed in parallel. One of them is bioprinting. Thomas Boland of Clemson University has patented the use of inkjet printing to 3D print living cells, making it possible to print human organs in the future. Dozens of companies around the world conduct research in this area.
Another important use of the new technology was the creation of prostheses, first conventional, and then bionic. In 2008, the first printed prosthesis was successfully transplanted into a patient and allowed him to return to a normal lifestyle.
Another milestone has been the emergence of open source print files on the Internet. Websites www.thingiverse.com, www.myminifactory.com and many others contain both free and paid files for 3D printing. Users share models online and print them themselves.
Stage 3: 3D printing today
In recent years, 3D printing has become available to the mass consumer: the price of printers has dropped significantly, and their use has become more convenient. Photopolymer 3D printers print detailed models with high precision and resolution. The number of users is growing, including due to the huge community of enthusiasts who are ready to help beginners. This is facilitated by the availability of ready-made files for 3D printing and the availability of software for creating models.
3D printing is already becoming a standard solution in industries such as dentistry, jewelry, orthopedics, and in other industries the implementation is in full swing. The possibilities are endless - from building houses to neurosurgery, from chocolate printing to metal printing.
Alexander Kornveits ,
Expert in the field of additive technologies, founder and CEO of Tsvetnoy Mir
Brief overview of Makerbot 3D printers
No other name in the world is more associated with 3D printing than Makerbot Industries. Makerbot has taken the 3D community by storm with its 3D printers and Thingiverse. The company was formed in Brooklyn, New York and began first sales in April 2009. June 19, 2013 Stratasys Inc. acquired Makerbot Industries for $403 million.
Fast forward to the present. Makerbot has unveiled an impressive lineup of home and semi-professional 3D printers. Consumers approach buying a 3D printer based on their needs and desires, as well as the available space where they want to install their 3D printer. We will try to briefly talk about the capabilities of Makerbot 3d printers, and we hope that we will take the reader one step closer to buying a 3d printer and joining the 3d community.
Makerbot Replicator Mini
This is a small entry level 3d printer that is ideal for beginners. It has an easy-to-use interface that is not overloaded with features and settings compared to more complex 3D printers, which, while allowing the user to deeply influence the printing process, can be difficult for inexperienced users.
The Replicator Mini can be operated over wifi using the makerbot app, or using the included USB cable. You can load the model into the 3d printer while at home, or even if you are away from home. Thanks to the camera built into the 3D printer, you can control the printing process remotely via a computer or smartphone. You can stop or cancel 3d printing as needed, or share photos of your 3d printing on social media. You can also give access to watching online video of the 3d printing process to anyone who wants. Since this is an entry-level 3D printer, it does not require platform leveling, and thus saves users time and, most importantly, nerves. The second great feature of the mini is the closed chamber and transparent plexiglass door on the front side, they keep the child from touching the hot extruder, making it suitable for schools and child care facilities.
Makerbot Replicator Mini comes with an exclusive Makerbot Smart Extruder which is very easy to connect and install thanks to its gold plated contacts and magnetic holder. This makes it easy and effortless to change the extruder or carry out its maintenance or cleaning. Masks, decorations, toys for children are just a few examples of what you can print if you buy a Replicator Mini 3D printer for your home.
This compact and lightweight 3D printer is easy to carry and take on the go. Just put it back in the box and put it in your car while driving. 3D Printer Replicator Mini is a mobile factory that can produce 3D products for you even when you are away from home.
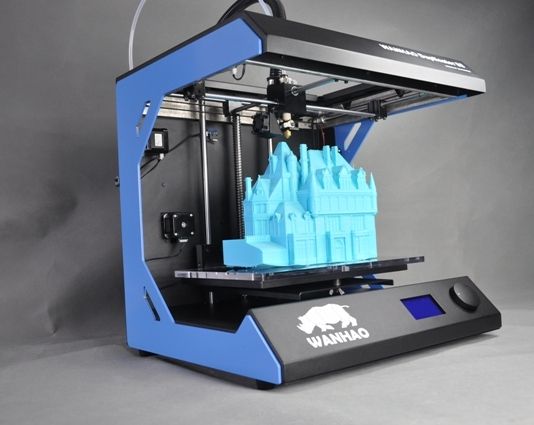
You can connect to the 3d printer and download the model via wi-fi, USB, Ethernet or USB flash drives. The 5th generation replicator is a powerful tool that is suitable for small or home production. It allows you to conveniently and cost-effectively create a working prototype of a device or part. Also, this printer is a great example of an average 3d printer that will fit well into the high school curriculum.
3d modeling and 3d printing is gaining immense popularity due to its versatility and is increasingly used in various industries such as automotive, medical and robotics, etc.
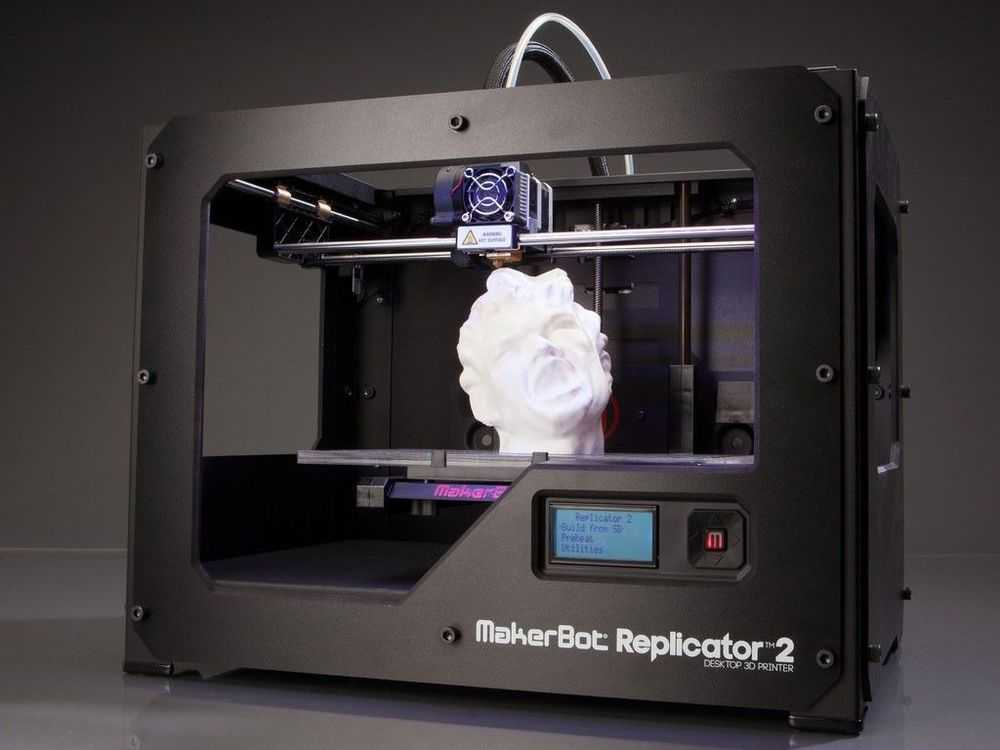