3D printer ventilation requirements
How to Ventilate a 3D Printer Properly – Do They Need Ventilation? – 3D Printerly
3D printer fumes and pollutants are usually overlooked by people, but it’s important to ventilate your 3D printer properly.
There are some great ventilation systems that you can make use of to have your 3D printing environment safer and less harmful to people around it.
The best way to ventilate a 3D printer is to put your 3D printer in an enclosure and have a ventilation system that properly tackles the small particulates that 3D printers emit. Make sure you have carbon filters and a HEPA filter to tackle odors and smaller particles.
The rest of this article will answer some key questions on 3D printer ventilation, as well as detail some nice ventilation systems that you can implement yourself.
Do You Need Ventilation for a 3D Printer?
During the printing process, you might have smelled the odor that is produced by the printer. To expel this odor out of the machine and workspace, you can use good ventilation.
However, the quality and smell of odor depends on the type of material that is used for printing purposes. For example, PLA is much safer when it comes to the smell than other filaments such as ABS.
Other than the smell, we also have small particles that are emitted from heating thermoplastics at such high temperatures, the higher the temperature, the worse the particles usually.
It also depends on the chemical makeup of the thermoplastic in the first place. If you are printing with ABS, Nylon or resin material in SLA 3D printers, proper ventilation is highly recommended, along with a mask.
A good enough ventilation system can work very well for ensuring that the surrounding air is clean and not contaminated.
It is said that the average running time for a 3D print can be around 3-7 hours, which is almost a quarter of the whole day when it is producing fumes.
To avoid any kind of harmful effect on your health or body, you seriously need to set up a ventilation system.
Ventilation While Using PLA
PLA is made up of eco-friendly material that produces sweet-smelling fumes that are laced with ultra-fine particles (UFPs) and volatile organic compounds (VOCs).
Technically, these both materials are not harmful to your health according to the research, but exposure to them daily may cause issues, especially to those with respiratory issues.
An open window or air purification system should work well enough for ventilating PLA.
Although many studies and research mention that PLA is safe, it is hard to measure the marginal health risks over time, and they take many years to properly test for. The risk may be similar to other ‘hobby-type’ activities such as woodworking, painting or soldering.
One study did test PLA for its emissions, and they found that it mostly emits Lactide which is known to be quite harmless. You should keep in mind that different types of PLA are created differently.
One brand and color of PLA could be harmless, while another brand and color of PLA isn’t as safe as you may think.
Many of the studies on emissions from 3D printers are in proper workplaces with many things going on, rather than your standard desktop home 3D printer, so its hard to generalize the findings.
Although it may not be completely safe, the studies show that PLA isn’t very risky, especially compared to other activities that we do on a regular basis.
Even going into a big city with all the pollution from vehicles and factories are said to be a lot worse than 3D printers.
Ventilation for ABS
According to the Journal of Occupational and Environmental Hygiene, materials commonly used for 3D printing such as PLA, ABS, and nylon can be a source of potentially dangerous VOCs.
ABS has been shown to result in high VOC emissions when heated at those higher temperatures, the main one being a compound called Styrene. It isn’t harmful in small portions, but breathing in a concentrated amount on a daily basis can be harmful to your body.
The concentration of the VOCs however, aren’t as dangerously high as it requires to have serious negative health effects, so printing in a well-ventilated, large room should be good enough to 3D print safely.
I would recommend not 3D printing ABS in a space where you are occupying for long periods of time. If you are 3D printing in a small room with poor ventilation, the rise of VOC concentration in the air can be troublesome.
The UFPs and VOCs produced by ABS during the 3D printing process contains Styrene. This material is not harmful in small portions; however, breathing in it on a daily basis can harm your body.
This is the reason why ventilation is needed during the printing process with ABS.
I would ensure that you are at least using an enclosure with some type of ventilation, ideally in a larger room.
How to Ventilate a 3D Printer
The best thing you can do to ventilate a 3D printer is to make sure your 3D printer chamber or enclosure is sealed/airtight, then to connect a vent from your chamber to the outside.
Some people use a window fan and put it near a window where your 3D printer is to then blow air out of the house. When printing with ABS, many users do this, and it works well to eliminate noticeable smells.
Installing Air Purifiers
Air purifiers have become common in major cities to keep the air clean. Similarly, you can use these air purifiers for your places where 3D printing is being performed.
Purchase a small air purifier and install it next to your 3D printer. Ideally you can put an air purifier within an enclosed system that contains your 3D printer so that the contaminated air passes through the purifier.
Look for the enlisted features in an air purifier:
- Have high efficient particulate air (HEPA) filters.
- A charcoal air purifier
- Calculate the size of your room and select the purifier according to it.
Air Extractors
Air Extractors are considered to be one of the best solutions to improve the ventilation of an enclosed room. Its working is explained below for you:
- It sucks in the heated air.
- Exchange the heated air with the cool air from outside.
- It uses a fan and suction pipes.
There are two main types of extractors that you can easily purchase from the market, i.e., Twin Reversible Airflow Extractors with and without Thermostats.
Building a 3D Printer Enclosure
You can consider building an enclosure for your printer. It basically involves creating an airtight enclosure equipped with carbon filters, a fan, and a dry-hose that runs outside your home.
In the enclosure, the carbon filter will trap styrene and other VOCs, while the hose will let the air pass through. This is an effective ventilation process which you can make at home.
3D Printer with Built-in Filtration
There are very few printers that come with a built-in HEPA filtration. Even the manufacturers are aware of the fumes, but nobody bothers installing a filtration.
For example, UP BOX+ is one of the printers that come with HEPA filtration solutions that filter out tiny particles.
You can choose to get a 3D printer with built-in filtration, but these are usually more expensive so be prepared to pay extra for this feature.
The Elegoo Mars Pro is a good example of this which has a built-in carbon air filter to remove some VOCs and resin odor from the air.
How to Ventilate a Resin 3D Printer?
The best way to ventilate a resin 3D printer is to create a negative pressure enclosure which directs air away the enclosure to a space outside. Long term exposure to resin fumes are unhealthy, even if they don’t smell.
Most people don’t have a dedicated ventilation system and are looking for a simple fix to help ventilate their resin 3D printers.
Following the video above should improve your ventilation for a resin 3D printer.
Remember, resins are toxic and can become allergic to your skin, be careful while using them.
Are 3D Printer Fumes Dangerous?
Not all, but some 3D printer fumes are dangerous and can cause serious damage to the health. As previously described, those UFPs are the more dangerous kind of emissions, where they can be absorbed into the lungs, then into the bloodstream.
According to the research done by the Georgia Institute of Technology, 3D printer fumes can negatively impact the quality of indoor air leading to potential respiratory health issues.
The regulations provided by OSHA actually throw light on the fact that 3D printer fumes are dangerous for health and the environment.
According to the research done on 3D printing filament, ABS is considered more toxic than PLA.
PLA is made up of eco-friendly substance so it is less harmful. This is one of the reasons why PLA is so commonly used, especially over ABS, because of its safety and non-smelling properties.
How Much Ventilation Does a 3D Printer Need? – 3dprintscape.com
One of the biggest health and safety concerns surrounding 3D printers comes from fumes. The printer melts the plastic from the filament reel, and the longer the plastic melts, the more fumes that accumulate. Particularly the fumes like ABS and Nylon pose a danger since they emit high levels of styrene, a suspected carcinogen, that is already known to cause headaches, drowsiness, and fatigue. This danger should highlight a good reason for ventilation.
How much ventilation does a 3D printer need? Opening a window or door, along with an air purifier, in an enclosed space will provide enough ventilation in most cases, but large 3D printers may require more ventilation since they operate for longer periods that may be up to several days and accumulate a greater number of toxins.
If you’d like to learn more about ventilation and your 3D printer, keep reading for further information.
Enclosed Spaces vs Open Spaces
Enclosed spaces require more ventilation because it doesn’t vent as well and may accumulate more hazardous fumes. The danger of toxic fumes in an enclosed space can also be that they would displace the oxygen in the room causing suffocation. Excessive heat in the space from the 3D printer may cause heatstroke.
Some of the most common environments for a 3D printer in an enclosed space include:
- Bedroom
- Living room
- Basement
- Workshop
With enclosed spaces, you must especially exercise caution with small rooms because of how the toxic fumes can build up much faster. Even in a large room, you should take precautions. Some people use a window fan to blow the fumes out. This action eliminates the unpleasant odor that you might smell when printing.
Open spaces, on the other hand, don’t pose as much danger because the gases don’t accumulate, and you have plenty of cross ventilation to keep the fumes from building up. For example, garages reduce the risk of fumes. You can open the door to let the toxic fumes out and keep them from building up.
An open space is an ideal setting for 3D printing, but not everyone has access to it, which makes an enclosed space necessary. For those situations, choose the larger room to allow for the most ventilation. Small rooms can accumulate toxic fumes faster and pose a greater risk.
Use an Air Purifier in Enclosed Spaces
Most air purifiers for 3D printing will feature two types of filters to lower the pollutants in the space. The first and most common air purifier that you will encounter is the HEPA filter. Experts rank this as the international standard of air filtration. They must comply with international standards on air filtration. To put it into perspective, the air filter must remove 99.97 percent of the pollutants at 0.3 micrometers in size.
HEPA filters have an advantage in removing the toxic fumes from spaces with 3D printers because of how they can remove 100 percent of the smaller pollutants under 0. 3 micrometers. A 3D printer will produce pollutants in a variety of sizes, but the smallest particles will be at 0.01 micrometers.
Second, you have the Carbon Activated filter. This air purifier does especially well with removing gaseous pollutants like odors and VOCs. The HEPA and Carbon Activated filter often work best in partnership with each other. Due to that, you may want to look for an air purifier that will include both types to cut the most pollutants from the 3D printer. Be aware of how a carbon-based purifier will require replacement every three to six months.
The next important thing is to look for an air purifier rated for a room area rated slightly larger than yours to guarantee it eliminates the most pollutants.
Can You Safely Put a 3D Printer in Your Room?
You need some level of ventilation in the room with an open window being the minimum. Along with that, we wouldn’t advise putting a 3D printer in your bedroom. It ranks as one of the worst locations.
Most experts today would call it safe, but we don’t understand the long-term effects of exposure. PETG and PLA plastics may do all right, but ABS can put out harsh chemicals that you wouldn’t want in your living space, much less in your bedroom. The best location to put a 3D printer is somewhere out of the way like a spare bedroom or office with good ventilation.
Beware of PLA because most think of it as safer to breathe in, but it can still shed VOCs and nanoparticles.
Best Well-Ventilated Areas for a 3D Printer
Most 3D printers at the hobbyist level won’t require a ton of ventilation, but you do want some. Let’s have a look at the best places to put a 3D printer. The garage ranks as the perfect location for 3D printing because the ventilation is perfect, especially for ABS printing. Keep in mind, 3D printers could be seen as a high-ticket item targeted by burglars, and you may want to keep it out of sight in the garage.
Your next best location would be an open-air workshop since it takes away the noxious fumes. Beware of an enclosed workshop without good ventilation.
The last best location is a home office or spare room with the window open for ventilation and an air purifier in the room. We would advise against putting a 3D printer in your living quarters or a bedroom because of how it exposes you to fumes over a long duration. Even the fumes thought to be less deadly are still potentially dangerous. We don’t understand the long-term effects of the fumes from 3D printing.
Some Models Don’t Require as Much Ventilation
Several models include exhaust ventilation or filtration. This design eliminates the need for ventilation where you might only need a window opened. Pay attention to the odor in the room because that can indicate the fumes built up. While 3D printers with exhaust ventilation may lower the need, you can never harm yourself by including as much ventilation as possible. If you have the option to create more ventilation, it makes sense to do so.
How to Use Enclosures
An enclosure will ventilate the 3D printer, so you want to have one if possible. Connect the vent from the chamber to the outside. Having this enclosure matters because of how it ensures that the surrounding air stays clean.
The airtight enclosure will come equipped with a carbon filter meant to purify some of the smaller fume particles. Most airtight enclosures will use a carbon filter, a hose, and a fan that runs outside the home. The fan directs the toxic fumes out of the home in what has become known as a negative pressure chamber.
Important to note, one of the best things that you can do to ventilate it would be if you were to seal the enclosure for air tightness. Be aware of how even if the fumes have no odor, it could still have potentially negative consequences on your health over time.
Building a Ventilation System for Your 3D Printer
If you plan to build a ventilation system, you want to do it right. Hiring a professional guarantees that the fumes won’t return to the room. An improperly constructed ventilation system risks the fumes coming back into the room. For hobbyists, they may not need to worry because of how hobbyist 3D printer don’t throw out as much for fumes. Someone getting into 3D printing professionally may want to consider a ventilation system because they will work with the fumes daily. They want to minimize the risk of developing health problems, which some of the fumes are known to cause.
Related Articles
- 3D Printer Enclosure – Do I Actually Need One?
- Create a Temperature Tower Using Cura – The Easy Way
- Cura Profiles
- 3D Printer Filament Storage Options
- All About 3D Printer Plastic
- Can a 3D Printer Print Anything?
Conclusion
How much ventilation a 3D printer needs will largely depend on its size and if a filtration system was built in. As a warning, never leave 3D printers unattended because of how they pose a fire hazard. Some examples exist where the printer caught fire because of a heated bed failure or faulty wires. You want to keep a close eye on it, and during that time, you need good ventilation.
Make sure you check out our YouTube channel, and if you would like any additional details or have any questions, please leave a comment below or join us on Discord. If you liked this article and want to read others click here.
Instructions for labor protection when working with a 3D printer
Good evening everyone.
I decided to write something useful, so I adapted the instructions for t.b. for 3d printer.
The instruction can be rewritten for any specific printer, I expect that it will be used in educational institutions or in any organization where there is a 3D printer.
In the near future, perhaps, I will lay out a methodological manual, but not a fact.
Link to the day and personally to me, quoting, etc. is welcome! Companies, if you complete your printers with this, I'm all for it, but have a conscience)
Instruction No. ____
on labor protection when working with a 3D printer
1. General requirements of the safety instructions for working on a 3D printer
1.1. Persons who have reached the age of 18 and have studied these instructions when working on a 3D printer are allowed to work independently with a 3D printer.
0003
- plastic fumes;
- temperature;
- noise.
1.3. When working on a 3D printer, it is not allowed to locate the workplace in rooms without natural or artificial ventilation.
1.4. To protect the plastic on the reel from direct sunlight, sun protection devices (curtains, film with a metallized coating, adjustable blinds with vertical panels, etc.) should be provided.
1.5. In the office and in the workplace, it is necessary to maintain cleanliness and order, to carry out systematic ventilation.
1.6. All equipment malfunctions identified during operation must be reported to the manager; in the event of a breakdown, work must be stopped until the emergency circumstances are eliminated. If a possible danger is detected, warn others and immediately inform the manager; keep the workplace clean and not clutter it with foreign objects.
2. Safety requirements before starting work on the 3D printer
2.1. Inspect and verify that equipment and electrical wiring are in good condition. In case of malfunctions, do not start work. Report it and only after troubleshooting and permission to start work.
2.2. Check the availability and reliability of the protective earthing of the equipment.
2.3. Check the condition of the electrical cord and plug.
2.4. Check the operation of the switches and other controls of the 3D printer.
2.5. If any malfunctions are detected, do not turn on the printer and immediately notify the manager about it.
2.6. Thoroughly ventilate the room with the 3D printer, make sure that the microclimate in the room is within acceptable limits: the air temperature in the cold season is 22–24°C, in the warm season it is 23–25°C, relative air humidity is 40–60% .
3. Safety requirements while working on a 3D printer
3.1. Turn on and turn off the 3D printer only with switches, it is forbidden to turn it off by pulling the plug out of the socket.
3.2. It is forbidden to remove the protective devices from the equipment and work without them, as well as touch the heated extruder and stage.
3.3. Do not allow unauthorized persons who are not involved in the work to the 3D printer.
3.4. Do not move or carry the 3D printer during printing.
3.5. It is forbidden to drink any drinks or eat food nearby while the 3D printer is in operation.
3.6. Any physical intervention during their operation of the 3D printer is prohibited, with the exception of an emergency stop of printing or an emergency shutdown.
3.7. Do not leave the switched on equipment unattended.
3.8. Do not place objects on or into the 3D printer.
3.9. Strictly comply with the general requirements for electrical safety and fire safety, the requirements of this instructions for labor protection when working on a 3D printer.
3.10. It is strictly forbidden to disassemble and repair the 3D printer on your own. These works may only be carried out by a specialist.
3.11. The total time of direct work with the 3D printer during the working day should not exceed 6 hours.
4. Safety requirements after finishing work with 3D printer
4.1. Disconnect the 3D printer from the mains, for which you need to turn off the toggle switch on the back, and then pull the plug from the outlet.
4.2. Remove and wipe the 3D printer table, which has cooled to room temperature, with a clean, damp cloth, or rinse with running water and wipe dry. Put the table back.
4.3. Remove workplace. Remove plastic scraps and waste in a separate bag for recycling.
4.4. Thoroughly ventilate the room with the 3D printer.
Document link: here and here.
Selective Laser Sintering (SLS) 3D Printing Guide
Selective Laser Sintering (SLS) 3D printing is a technology trusted by engineers and manufacturers across industries to create durable and functional models.
In this detailed guide, we will explain selective laser sintering technology, the different systems and materials on the market, the workflow and different applications of SLS printers, and when to choose 3D printing with this technology over others. additive and traditional manufacturing methods.
White Paper
Looking for a 3D printer to create durable, functional models? Download our white paper to learn how selective laser sintering (SLS) technology works and why it is popular in 3D printing for functional prototypes and end-use products.
Download white paper
Selective laser sintering (SLS) is an additive manufacturing technology that uses a powerful laser to sinter fine polymer powder particles into a solid structure based on a 3D model.
SLS 3D printing has been popular with engineers and manufacturers for decades. With its low model cost, high productivity, and common materials, this technology is well suited for a wide range of applications, from rapid prototyping to low-volume production, limited trial runs, or custom-made products.
Recent advances in technology, materials and software have opened up the possibility of SLS printing to a wider range of companies. Previously, such tools were used only in a few high-tech industries.
Introducing the Fuse 1 high performance SLS 3D printer, finally available.
Webinar
Watch our product demo to learn about Fuse 1 and SLS 3D printing from Formlabs.
Watch webinar
Schematic representation of the selective laser sintering process. The SLS method uses a powerful laser to sinter small particles of polymer powder into a solid structure based on a 3D model.
-
Seal: A thin layer of powder is applied to the top of the platform inside the working chamber. The printer preheats the powder to just below the melting point of the feedstock. This allows the laser to more easily raise the temperature of certain areas of the powder bed and monitor the solidification of the model.
The laser scans the cross section of the 3D model, heating the powder to the material's melting temperature or just below. Particles are mechanically joined together to form a single solid object. The unsprayed powder supports the model during printing and eliminates the need for special support structures. The platform is then lowered into the working chamber one layer, typically 50-200 µm thick, and the process is repeated for each layer until the models are complete.
-
Cooling down: after printing and before post-processing, the build chamber should cool down a little in the printer body and then outside the body to ensure optimal mechanical properties of the models and avoid their deformation.
-
Post-Processing: finished models must be removed from the working chamber, separated from each other and cleaned of excess powder. The powder can be recycled and printed models can be blasted or tumbled.
To learn more about the workflow, see the SLS 3D Printing Workflow section below.
SLS models have a slightly grainy surface, but the layer lines are almost invisible. To achieve a smooth surface, SLS models are recommended to be blasted or tumbled. This sample was printed on a Fuse 1 industrial 3D printer with SLS technology for workshops from Formlabs.
The green powder supports the model during printing and eliminates the need for special support structures. This makes SLS ideal for complex geometries, including internal features, undercuts, thin walls, and negative draft features.
Models created using SLS 3D printing have excellent mechanical properties: their strength is comparable to that of injection molded models.
Compare Selective Laser Sintering (SLS) 3D printing with other common plastic modeling technologies: Fused Deposition Modeling (FDM) and Stereolithography (SLA).
Selective laser sintering (SLS) is one of the first additive manufacturing technologies developed in the mid-1980s by Dr. Carl Deckard and Dr. Joe Beeman at the University of Texas at Austin. Since then, the method has been adapted to work with a variety of materials, including plastics, metals, glass, ceramics, and various powdered composite materials. Today, all of these technologies are classified as wafer synthesis, additive manufacturing processes that selectively sinter regions of a powder layer under the influence of thermal energy.
The two most common substrate synthesis systems currently available are a plastic based method commonly referred to as Selective Laser Sintering (SLS) and a metal based method known as Direct Metal Laser Sintering (DMLS) or Selective Laser Melting (SLM). ). Until recently, both systems were very expensive and complex, which limited their use to the production of small batches of expensive models or custom-made products, such as aerospace components or medical devices.
Innovation in this area will make plastic-based SLS as affordable as other 3D printing technologies such as stereolithography (SLA) and Fused Deposition Modeling (FDM) and widely available in affordable, compact systems.
All selective laser sintering 3D printers use the process described in the previous section. Basically, such printers differ in the type of laser, the volume of printing and the complexity of the system. Different solutions are used for temperature control, powder dosing and layering in different devices.
Selective laser sintering technology requires high precision and strict control during the printing process. The temperature of the powder and (incomplete) models must be controlled within 2°C during the three stages of production: preheating, sintering and storage before extraction, in order to minimize warping, stress and thermal deformation.
For decades, selective laser sintering has been one of the most popular professional 3D printing technologies, but due to its complexity, strict requirements and high price, only service bureaus and large enterprises could use it.
Conventional industrial SLS 3D printing systems have one or more powerful lasers. An inert atmosphere (nitrogen or other gases) is needed to prevent the powder from oxidizing and breaking down during the printing process, which requires specialized air handling equipment.
These installations also require special heating, ventilation and air conditioning (HVAC) systems and industrial power supplies. In addition, even the smallest industrial installations occupy an area of at least 10 square meters. m.
Due to the high initial cost of approximately $100,000 (and much more for complete solutions), traditional industrial systems with SLS technology were out of reach for many enterprises.
As with other 3D printing technologies such as Fused Deposition Modeling (FDM) and Stereolithography (SLA), more affordable, compact systems with SLS technology have recently begun to appear on the market. However, these solutions had significant drawbacks. These include low quality models and complex manual workflows due to a lack of post-processing solutions. This severely limited their use in industrial production.
The Formlabs Fuse 1 printer is in a new category with these deficiencies fixed . It is the first industrial SLS 3D printer for the workshop, delivering high quality, compact size, streamlined workflow, and cost far less than traditional industrial systems of the same type.
The Fuse 1 printer does not require any special infrastructure and will easily fit into your workplace.
The Fuse 1 uses a single laser and has a smaller working chamber that requires less heat. The powder is exposed to elevated temperatures for a shorter period of time, so there is no need for inert gases and specialized ventilation equipment. Thanks to its lower power consumption, it can run on a standard AC power supply without requiring special infrastructure.
The Fuse 1 features patent pending Surface Armor technology. This creates a semi-baked shell that heats evenly around the models as they are printed. This results in excellent surface quality, stable mechanical properties, high reliability and a high material renewal rate.
In addition to providing a compact, self-sustaining ecosystem and complete powder processing capability, Fuse 1 is complemented by the Fuse Sift Station, a separate stand-alone device for model retrieval, recovery, storage and powder mixing.
Overall, the Fuse 1 industrial 3D printer with SLS for workshops has a slightly smaller print volume than traditional entry-level SLS systems, but is smaller, easier to work with and less expensive.
Fuse 1 Industrial SLS Workshop Printer | Traditional Industrial SLS 3D Printers |
---|
from 18,500 US dollars | 100 000 - 500,000 US dollars and more than | ||||||||
Press volume | to 165 x 165 x 300 mm | to 550 x 550 x 750 mm | 9 Benefits | Availability High quality models High performance Simplified workflow Compact dimensions Low maintenance | High print volume High quality models High performance Many material options | ||||
---|---|---|---|---|---|---|---|---|---|
Disadvantages | Less print volume Limited material options | Expensive equipment Big sizes Infrastructure Requirements Large amount of maintenance Special Operator Required |
The most common selective laser sintering (SLS) material is nylon. It is a high performance engineering thermoplastic for both functional prototyping and end-use fabrication. Nylon is ideal for the production of complex knots and strong models with high environmental resistance.
3D printed SLS nylon for strength, rigidity and durability. The final models are impact-resistant and highly wear-resistant. Nylon is resistant to UV, light, heat, moisture, solvents, temperature and water. Nylon models printed on a 3D printer are also biocompatible and do not cause allergic reactions. This means that they can be worn and used safely in many situations.
Nylon is ideal for a range of functional applications, from consumer product design to healthcare applications.
Nylon is a synthetic thermoplastic polymer from the polyamide family. It is available in several versions, each designed to print different products. Nylon 12 Powder has a wide range of applications and is a general purpose, general purpose SLS 3D printing powder. Nylon 12 GF Powder is a composite material with a high fiber content, increased stiffness and heat resistance for difficult industrial conditions. Nylon 11 Powder helps fill a gap in prototyping and end-use applications where increased ductility, impact resistance and the ability to withstand wear without brittle fracture are required.
- Impact proof prototypes, fixtures and fittings
- Thin-walled pipes and bodies
- Rivets, clips and latches
- Orthopedic products and prostheses*
- High Performance Prototyping
- Small batch production
- One-piece clamping and holding fixtures and tooling
- Conventional SLS models
- Heavy-duty clamping and fastening fixtures and spare parts
- Continuous models
- Threads and sockets
- High temperature models
* Material properties may vary depending on model design and manufacturing method. It is the manufacturer's responsibility to confirm the suitability of printed models for their intended use.
211 40%
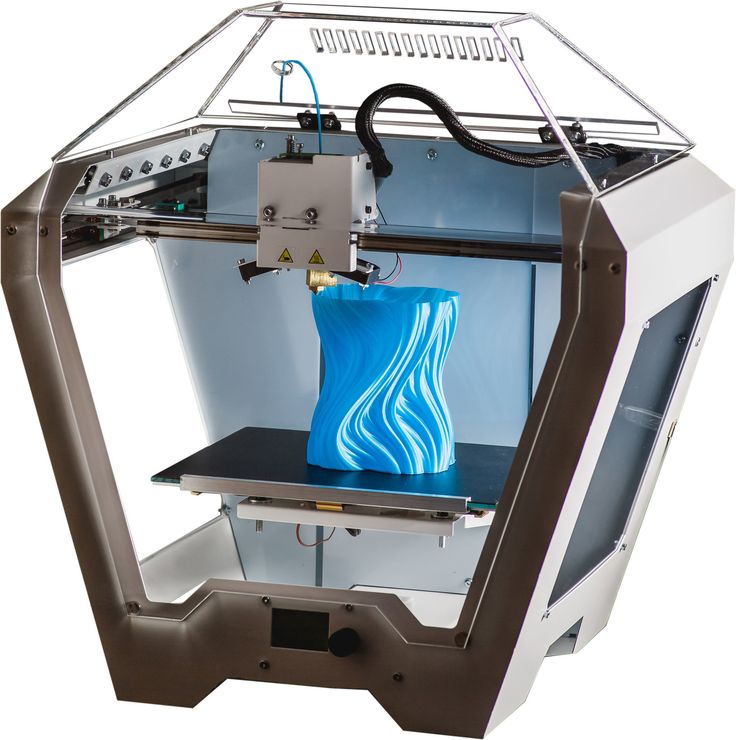
Nylon 12 Powder and Nylon 11 Powder are one-component powders, but some SLS 3D printers can also use two-component powders, such as coated powders or powder blends.
Nylon 12 GF Powder is a composite material with a high fiberglass content, while other nylon composites with aluminide, carbon or glass are designed to increase the strength, stiffness or flexibility of models. In such two-component powders, only the component with the lower glass transition point is sintered, which binds both components.
SLS 3D printing accelerates innovation and helps businesses in a wide range of industries such as engineering, manufacturing and healthcare.
Manage the entire product development process, from iterations of first concept design to production of ready-to-use products:
- Rapid Prototyping
- Product mockups for user feedback
- Functional Prototyping
- Functional testing of products under severe conditions (e.
g. piping, brackets)
Manage your supply chain and respond quickly to changing needs:
- End-Use Manufacturing
- Small batch production
- Mass production of new customized consumer products
- Spare parts manufacturing, supply chain sustainability
- Durable, durable clamping and fastening devices (such as clamps and clamps) and accessories
- Custom manufacture of automotive, motorcycle, and marine equipment parts, and restock military items on demand
Self-manufacturing of ready-to-use medical devices, taking into account the individual characteristics of patients:
- Prototyping of medical devices
- Prostheses and orthotics (e.g. prosthetic limbs and orthoses)
- Surgical models and instruments
- End use products (nylon 12 biocompatible and sterilizable*)
* Material properties may vary depending on model design and production method. It is the manufacturer's responsibility to confirm the suitability of printed models for their intended use.
Use any CAD software or 3D scan data to design the model and export it to a 3D printable format (STL or OBJ) file. All printers with SLS technology use software that allows you to adjust settings, position models, estimate print times, and layer your digital model. Once set up, the model preparation software sends commands to the printer via a wireless or cable connection.
The Fuse 1 uses PreForm print preparation software (free to download). It allows you to easily duplicate and place multiple models on a 3D grid to maximize your print volume. PreForm automatically suggests the optimal orientation and position of models with the ability to make manual changes.
The workflow for preparing the printer varies from system to system. Most traditional SLS systems require extensive training, tools, and physical actions to prepare and maintain them.
Fuse 1 redefines the SLS workflow, making it simple and efficient, as well as providing trouble-free printing and complete powder handling thanks to modular components.
The Fuse 1 can be easily loaded with powder using a special cartridge.
The Fuse 1 uses a detachable build chamber so you can start a new print while the previous build chamber is still cooling.
Once all pre-checks have been completed, the machine is ready to print. Depending on the size and complexity of the 3D models, as well as their density, printing using SLS technology can take from several hours to several days.
When printing is completed, the build chamber in the housing should cool down a bit before proceeding with the next step. To start the next print, you can remove the build chamber and insert a new one. Before post-processing, the working chamber must cool down to ensure optimal mechanical properties of the models and avoid their deformation. This can take up to half of the total print time.
Fuse 1 is equipped with a touch screen, where you can see in real time how each new layer is formed during the printing process. This camera image can also be transferred to a computer using PreForm to monitor the print without leaving the workplace.
Compared to other 3D printing processes, post-processing of SLS-printed models requires minimal time and effort. With no supporting structures, it is easy to scale and provides consistent results across batches of models.
After printing is completed, remove the finished models from the build chamber, separate them and clean them of excess powder. As a rule, this is done manually at the cleaning station using compressed air or a jet apparatus.
The excess powder left after the creation of the model is filtered to remove large particles from it. After that, it can be recycled. Under the influence of high temperature, the properties of green powder deteriorate slightly, so for subsequent printing it must be mixed with new material. Due to the possibility of reusing materials, SLS technology produces a minimum amount of waste.
Typically, SLS technology uses separate devices for powder recovery, storage and mixing. The Fuse 1 workflow uses a single Fuse Sift to retrieve patterns and greens, store, dispense, and mix material streams.
Fuse Sift completes the Fuse 1 SLS printing workflow. This system is used for safe and efficient model retrieval and powder recycling.
Fuse Sift automatically doses and mixes used and new powder, reducing waste and controlling powder delivery.
After the powder has been sifted, the 3D models printed using selective laser sintering technology are ready for use. However, there are a few more post-processing steps you can perform on these models.
By default, the surface of 3D models created using SLS technology remains grainy. To achieve a smooth surface, Formlabs recommends blasting or tumbling models made using this method. Models can be spray painted, lacquered, electroplated or otherwise to achieve the desired color, surface quality and properties such as water resistance (special coating) and electrical conductivity (electrolytic coating). Models created with SLS Formlabs are dark in color and therefore not well suited for staining.
Immersion printed SLS model from Partial Hand Solutions.
SLS models can be electroplated to give a metal-like surface.
Selective laser sintering is preferred by engineers and manufacturers for its wide design options, high productivity, low model cost and proven end use materials.
Most additive manufacturing processes such as stereolithography (SLA) and Fused Deposition Modeling (FDM) require specialized support structures to fabricate overhangs.
Selective laser sintering does not require support structures because the unsintered powder surrounds the model during printing. SLS printing makes it easy to create overhangs, intricate geometries, interconnecting parts, internal channels and other intricate details.
Intricately patterned arm splint for weight reduction.
Engineers typically design models to meet the capabilities of the final manufacturing process, also known as design-to-technology (DFM). When additive manufacturing is only used for prototyping, it comes down to creating models and designs that can be replicated in the manufacturing process using traditional tools.
Selective laser sintering is emerging as a viable rapid manufacturing method and its application area continues to expand, so it can open up new possibilities in design and construction. 3D printers with SLS technology can create complex geometries that are impossible or incredibly expensive to manufacture using traditional processes. SLS technology also allows design professionals to combine complex assemblies into a single model that would normally require multiple models to be created. This helps avoid the problem of loose connections and saves assembly time.
Selective laser sintering can unleash the potential of generative design, as it allows the creation of lightweight models that use complex lattice structures that cannot be fabricated with traditional methods.
Selective laser sintering is the fastest additive manufacturing technology for making functional, durable prototypes and end-use products. Lasers used for powder sintering have much faster scanning speeds and are more accurate than the layering methods used in other processes such as Industrial Fused Deposition Modeling (FDM).
To maximize the available print volume in each printer, multiple models can be placed side by side. Operators can use the software to optimize print volume and maximize productivity by leaving only minimal clearance between models.
SLS technology allows operators to fill the build chamber with as many models as possible, as it allows them to be printed without supporting structures, saving time in post-processing.
SLS 3D printing requires the right materials for functionality and versatility. Nylon and its composites are proven, high quality thermoplastic materials. Laser-sintered nylon models have close to 100% density and mechanical properties that are comparable to products made using traditional manufacturing methods such as injection molding.
Screwdriver printed in Nylon 12 Powder. After a simple post-processing, nylon models have a smooth, professional quality surface.
SLS Printable Nylon is an excellent replacement for conventional injection molded plastics. The latches and other mechanical connections produced from it are superior to products created using any other additive manufacturing technology. It is ideal for making functional plastic parts that will work and not break down over time like products created through other additive manufacturing methods.
When calculating the cost of one model, it is usually necessary to take into account the cost of ownership of equipment, material costs and labor costs:
-
Equipment cost of ownership: The more models a printer can produce over its lifetime, the lower the cost per model. Therefore, higher performance results in a lower cost of ownership per model. With high laser scanning speeds, the ability to produce multiple models at once to maximize the working volume, and a simple post-processing process, SLS 3D printing guarantees the highest productivity of any additive manufacturing method.
-
Material: Most 3D printing technologies use proprietary materials, while nylon is a common thermoplastic that is produced in large quantities for industrial applications.
This makes it one of the most inexpensive raw materials for additive manufacturing. SLS 3D printing requires no support structures and allows you to print with recycled powder with minimal waste.
-
Labor: Labor is a disadvantage of many 3D printing solutions. Work processes in most technologies are quite laborious and difficult to automate, which can significantly affect the cost of one model. Easy post-processing with SLS printing reduces manual labor and allows for easy scalability.
A 3D printer with SLS technology is a significant investment initially, but this investment often pays off even faster than buying smaller devices. SLS for workshop technology significantly reduces initial acquisition costs and also reduces model costs in most applications.
If your business rarely uses 3D printing, it is recommended that you use a third party service bureau. But in this case, the cash costs will be higher and you will have to wait longer for the order to be completed. One of the main advantages of 3D printing is its speed compared to traditional production methods. But this advantage loses its value when it takes up to several weeks for a third-party company to deliver a model.
REEKON Tools