3D printer supports
What are supports in 3D printing? When and why do you need them?
What are support structures in 3D printing? Depending on the technology you use to produce parts, you may need to print support structures to maintain part geometry. This article covers what support structures are in 3D printing, when they’re needed and how supports may affect the quality and price of your part.
3D printing builds parts layer by layer, so there always has to be a previous layer to build upon. Depending on the specific 3D printing technology and complexity of the 3D model, you may need to produce your part with support structures.
When deciding which 3D printing technology to use, it’s essential to consider support structures and how they affect the quality and price of your part. As well, support structures will have an impact on your part’s surface finish. Removing supports from a part often results in blemishes or surface roughness.
This article defines what support structures are for 3D printing, how they’re implemented for each technology and how using supports can affect your choice of manufacturing technology.
How do supports work for FDM 3D printing?
Fused deposition modeling (FDM) extrudes a metal filament onto a build surface along a predetermined path. As the material is extruded, it cools, forming a solid surface that provides the foundation for the next layer of material.
With FDM printing, each layer is printed as a set of heated filament threads which adhere to the threads below and around it. Each thread is printed slightly offset from its previous layer, allowing a model to be built up to angles of 45 degrees. This way, prints can expand beyond the width of preceding layers of filament.
When a feature is printed with an overhang beyond 45 degrees, it can sag enough to potentially ruin the print. This is when you need support structures.
Depending on the degree of the overhang, your FDM part may need supportsWhen do you need support structures for FDM?
Let’s imagine you have to 3D print models of the letters Y, H and T.
An FDM printer can easily print the arms of the letter Y without requiring support structures. Even though these features are outstretched, they don’t extend past 45 degrees.
The letter H, on the other hand, is a bit more complicated. If the center bridge is under 5 mm, it can be printed without support or any sagging. Support is required if the bridge exceeds 5 mm. In the example shown here, the center bridge is over 5 mm, so it’s printed with support structures.
The letter T requires support for the top features extending from either side of the model. There is nothing for these out arms to be printed on and the material will fall down without supports.
The image below illustrates these three examples. The support material is shown in light gray.
An illustration of when you need support structures for FDMHere is how these models look when printed. The second image shows the result of the T printed without support. The surface has significant sagging and will require a lot of post-processing to clean up.
What is bridging in FDM?
In some cases, there is an exception to this overhang rule.
Hot material can be stretched short distances between two points of a print. This method is known as bridging. Bridging allows parts to be printed without support materials and with minimal sagging. If a bridge is over 5 mm long, support structures are required if you’re hoping to achieve an accurate surface finish.
Curious about the price and material options for FDM?
Explore our FDM services Get a free, instant quote today
What are the disadvantages of support structures in FDM?
The potential need to use support structures is one reason why FDM is not always the right technology for your application. One of the limitations of using supports in FDM printing is that post-processing is then required, which results in marks or damage to the surface in contact with the support materials.
Another issue is that layers printed on support structures will be less even because the supports won’t be stationary like solid layers of extruded filament. On top of this, supports can be difficult to remove from small, intricate features. This bit of post-processing could break your model.
Furthermore, having to print support structures adds to the cost of FDM. Supports require additional printing material that later needs to be removed, creating more work (and waste) for the operator. More materials and more human intervention equal higher costs.
An FDM-printed puzzle piece with supports removed to show surface roughnessHow much support material do you need for your FDM print?
The amount of material you’ll need for support structures will ultimately depend on the design. If you’re printing a replica of the Gateway Arch in St. Louis, for instance (like the example below), you’ll only need a limited amount of support placed in the correct location to allow accurate printing.
Now, if you’re printing a “ball in a cube” (shown below), you’ll need quite a lot of support material, which means a sizable amount of removal time as well.
Removing the supports in this example is complex and involves getting rid of each support element with needle-nose pliers while attempting to limit the damage to the surfaces surrounding the supports. Sanding or smoothing these surfaces after support removal presents another difficulty.
However, without support materials, this model can’t be printed with FDM, unless you want to compromise on quality and accuracy. In this case—despite the added cost and print time—the additional support material used is essential to being able to print this design.
What are the two types of support structures for FDM?
FDM 3D printing uses two types of support structures. The most common (and best suited for most FDM partS) is a sort of flat accordion or lattice structure. The other is “tree-like” support, which has less contact with the print surface and can leave you with better surface finishes after post-processing. Though it’s less common, the latter is much preferred by some operators.
The FDM printer operator will generally specify the type of support that best suits your application and minimizes the cosmetic impact it’ll have on your design.
These are two different types of support structures: According (left) and tree (right)Are there dissolvable supports for FDM?
Finely-tuned printers with two print heads can print support structures with a dissolvable material that doesn’t tear away from the part. Instead, you can dissolve this material in a chemical solution that won’t adversely affect the printed model.
This results in a better surface finish where the support is in contact with the main material, however, it can be expensive and time-consuming.
All industrial FDM machines are equipped to use dissolvable support materials. For instance, you have the Ultimaker 3, which can print PVA that dissolves quite easily post-print.
Do you need support structures for SLA & DLP 3D printing?
Stereolithography (SLA) and Digital Light Processing (DLP)create 3D printed objects from a liquid (photopolymer) resin by using a light source to solidify the liquid material.
Depending on the exact type of printer, you have two main methods of producing a model. Certain printers pull a model out of a vat that contains liquid material, solidifying it via a light source through a translucent window at the bottom (bottom-up). Others submerge the model into the liquid as the top layer is tread by a light source from the top (top-down).
To make sure that the prints adhere to the print platform and don’t float around in the vat, SLA and DLP printers almost always use supports.
Support structures from these printers look like thin ribs, with only small tips actually touching the model to save material and printing time. The number of supports, their location, where they touch the model and the structure are calculated by the software and are dependent on the shape, orientation and weight of the part being printed.
SLA and DLP are some of the most accurate technologies, capable of printing even the smallest and most intricate objects with accurate detail. With proper post-processing, printing with support does not impact the quality of the part.
An SLA print with support structuresHow do you remove support materials from SLA & DLP prints?
First, Isopropyl Alcohol (IPA) is used to wash liquid resin off your completed parts. Support structures can be either broken off the surface of the model or removed using pliers. The spots where the support was in contact with the object are then sanded to remove any remaining marks.
Removing support structures from an SLA printCurious about the cost and materials available for SLA/DLP?
See all SLA/DLP materials Get a free, instant quote today
Do you need support structures for material jetting?
Material Jetting (Stratasys PolyJet and 3D Systems MultiJet Modeling) technologies are similar to inkjet printing, but instead of jetting drops of ink onto paper, these 3D printers jet layers of liquid photopolymer onto a build tray and cure them instantly using UV light.
These printers require the use of support material in all cases where there are overhanging features, regardless of the angle. Supports are either water-soluble or are removed during post-processing using plyers, water jetting, ultrasonic baths and sandblasting.
Unlike FDM, supports for these technologies are in no way detrimental to a part’s cosmetic appearance, surface quality or technical properties. After proper post-processing, it’s practically impossible to distinguish where support materials were removed from your part.
Removing water soluble support material from a Polyjet (material jetting) printerPost-processing for material jetting involves power tools like waterjets and sandblasters, and using these tools may damage or bend the more intricate features of your model. We recommend that you follow our Material Jetting rules to avoid these sorts of issues. In fact, you may want to opt to print your parts using SLS if your model has intricate features and thin wires.
Do you need support structures for SLS?
Selective Laser Sintering (SLS) 3D printers fuse powdered material in a chamber using a laser.
For SLS, there’s no need for support structures since the powder acts as a form of support when the object is built up layer by layer. This gives a lot of design freedom but also generally increases the cost and time to print a part. SLS requires time for the build chamber to cool down and cleaning the print requires a multi-step finishing process, including removing unfused powder, typically with an air gun.
When printing with SLS, the unfused powder surrounding the print functions as a natural support structure that's also easy to removeCurious about the cost and materials available for SLS?
See all SLS materials Get free, instant quote today
Do you need support structures for binding jetting?
Binder jetting is similar to SLS in that the printer uses thin layers of powdered material to build up an object. Instead of using a laser to sinter layers together, however, binder jetting printers use a binding agent extruded from a nozzle to bind the powder together.
Similar to SLS, there’s no need for support structures with binder jetting since the powder supports the object as it’s built. As well, you have to clean and post-processing the print over several steps, including removing unfused powder with an air gun or another tool.
Unfused powder being removed from a binder jetted printDo you need support structures for metal 3D printing?
Metal 3D printing technologies use support structures to keep models fixed to a base plate during the building process. However, overhangs with an angle greater than 35 degrees can be printed without support.
When you do need supports for metal 3D printing, it’s important to ensure that they are easy to access, or else it’ll be challenging and maybe even infeasible to remove them during post-processing.
Using supports won’t impact the overall quality of your part, and with the proper post-processing methods, you can remove all marks from the printed model.
These metal prints, which are still attached to the print bed, still have visible support structuresHubs' top tips & tricks for optimizing 3D printing with support structures
Whether or not you need to use support materials for your specific application, it’s important to know the best practices for this aspect of the 3D printing process.
-
Support structures will generally affect the cosmetic appearance of a part, so you’ll need to rely on post-processing to improve the surface finish after removing supports.
Material Jetting is the exception to this rule.
-
The more support structures you print, the more complex a design can be for certain 3D printing technologies. You can optimize the amount of support material you use by addressing part orientation and part accuracy (among other design and manufacturing factors) to lower the cost and print time.
Which 3D printing technologies require support structures?
At the end of the day, this is the most essential question. The table below summarizes whether support is required for each of the 3D printing technologies we offer at Hubs.
3D printing technology | Do I need support structures? |
---|---|
FDM (desktop & industrial) | Depends on model geometry |
SLA & DLP | Always |
Material Jetting | Always (dissolvable) |
SLS & MJF | Never |
Binder Jetting | Never |
Metal 3D printing | Always |
Ready to transform your CAD file into a custom part? Upload your designs for a free, instant quote.
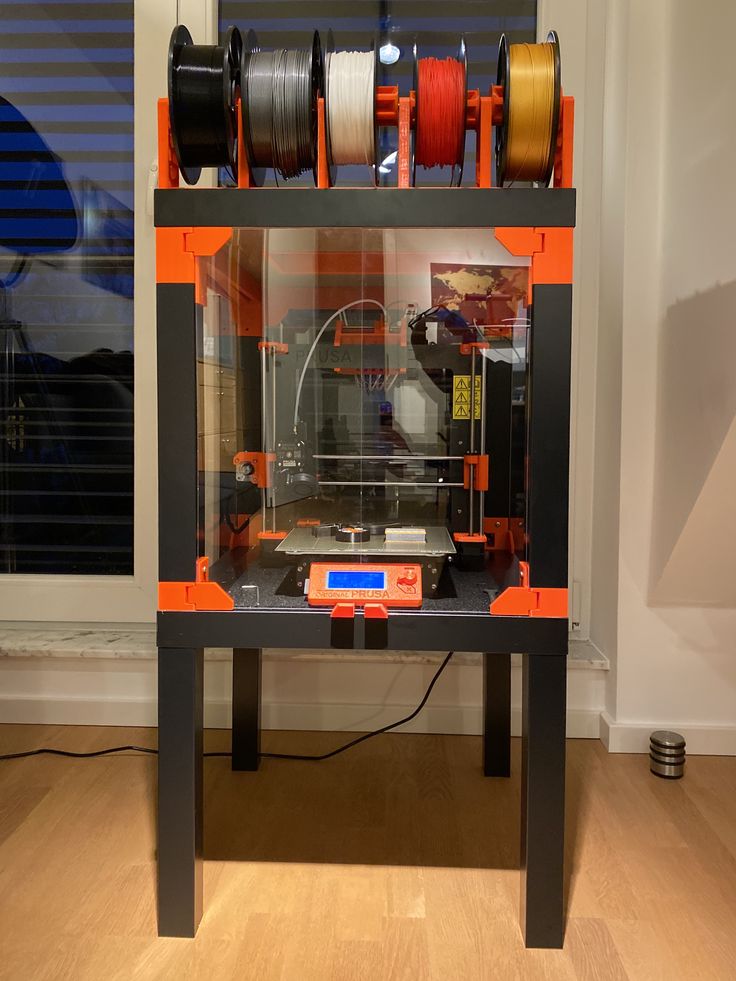
What is important to know about 3D printing supports?
3D Learning Hub
Be at the forefront of innovation and see how you can use Additive Manufacturing today!
Do you need a 3D printing service?
- Innovation
- Adaptability
- Scalability
See all categories
Contents:
- Introduction
- Printing Supports: When to use them?
- What are the different types of 3D Printing supports?
- Removing your 3D Printing supports
- The downsides of using 3D printing supports
- How to avoid using supports?
Introduction
3D printing can help you achieve pretty impressive models. But getting your part printed out as neat as it appears on your design may involve in-between steps. 3D printing supports for instance, is one of the first things you may have to take into account based on the additive manufacturing technology you use and the complexity of your design.
Making adapted 3D printing supports brings about a few doubts, such as when they are needed, how to choose from the different types of supports, how to remove them, and of course, what the downsides of using supports are. In this article, we are going to tackle these questions and provide you with a few tips to help you use supports efficiently.
Credit : Hackaday, When does moving to resin 3D printing make sense?Printing Supports: When to use them?
To settle that question, you first need to know what 3D printing technology you are going to use. If you haven’t made up your mind yet, note that the way 3D printers function raises different technical constraints.
FDM printers, for instance, function by extruding filament layers successively. In other words, if your part includes an overhang that isn’t maintained by any surface underneath, your 3D print is going to fail. This type of issue is one of the main reasons why supports are very useful for FDM prints.
3D printed parts made using Stereolithography also require support structures. These supports are needed to print correctly any overhangs and bridges during the SLA printing process, for example. You can choose the part’s orientation, choosing which exposure requires less support structure.
If you are using Selective Laser Sintering or Jet Fusion technologies, on the other hand, the powder your part is going to be printed out of will surround the print and act as a support. In other words, you will never have to bother with supports if you go for SLS or Jet Fusion technologies. If you are looking into more advanced technologies, the supports that may be used in processes such as metal printing will generally not affect the print quality.
The complexity of your part is the second criterion that will determine whether or not it will need supports. First, if your design contains overhangs, you have to figure out their tilt. If your overhangs don’t tilt more than 45°, most FDM printers will be able to print them properly. If angles exceed this value on the other hand, you might need to use supports or your overhangs are likely to sag.
You might also want to consider using 3D printing supports if a part of your design bridges a gap between two elements. Basically if the length of your bridge doesn’t exceed 5mm, you won’t need any support structure to fill the gap.
What are the different types of 3D Printing supports?
The 3D printing process you have chosen will orient you towards different support types. For FDM printers for instance, the most commonly used supports are the lattice and the tree types.
The first type can be used to build columns and hold parts steady, which is effective with steep overhangs. These lattice structures are the most widespread thanks to how fast they can be generated and to their compatibility with most 3D prints.
Tree type supports start with trunks and evolve in thin branches as they reach the model, which appear to be useful if one needs to selectively support parts. You might consider using such types of support if your design contains many overhangs but aren’t too vertical.
If you can rely on a two-extrusion head printer, you can opt for a soluble support. Soluble materials such as limonene can be loaded in one extruder and be applied along with your printing material. If you are fine with investing in more expensive supports, dissolvable ones will enable you to wash them away by soaking them in water. Using dissolvable supports is the best way to keep a nice surface finish without adding extra steps to your post-processing. Yet, because the soluble support material and 3D printing materials can’t be extruded together, 3D printers with only one print head can’t make such a process. Also, as this last support type suggests, the ease of removing supports is an important criterion to look at when it comes to choosing one.
Removing your 3D Printing supports
We have just seen that lattice, tree-type and dissolvable supports have different properties. On top of that, their ease of removal isn’t equal. Keep in mind that the more your model is in contact with supports, the more likely their removal may result in partial marks or breaks. Lattice structures are for instance supposed to support surfaces completely, which makes them hard to remove without impacting the surface quality.
Tree type supports, if used wisely to support key areas of your parts only, will translate to fewer contacts with your print and make it easier to remove them.
Once the printing process is over, removing the supports is your next step. Using pliers is a good choice if you want to grab, twist and pull your supports off your part. If the support you want to take off is accessible and big enough, you can gently start with your fingers. Depending on how much the visual aspect of your part is important to you and how many marks have been left by your supports, you might need to sand the areas in contact with the supports to get a better surface finish.
The downsides of using 3D printing supports
Using supports implies quite a few limitations and removing them, is as we have seen, definitely part of the list. Another overt drawback of using supports is the increase in lead time.
Depending on the type of support you want to use, its size and complexity, printing supports themselves will add to your total production time. Tree-shape supports can in that sense be quite demanding for your printer. Also, the post-processing steps we have mentioned beforehand need to be taken into account here, since removing the supports off your parts and cleaning them can turn tedious.
The main downside that naturally comes next is the costs of using supports, as the amount of material needed can increase. If steep overhangs account for a big part of your design and you need to use lattice structures to support them, the half of your material can possibly fall into the creation of your supports.
Fortunately, there are multiple ways one can rely on to mitigate the impacts your supports might have on your design and on your wallet.
How to avoid using supports?
If you would like to optimize the integration of your supports, there are multiple options that 3D slicers and your 3D printer can offer you.
When printing supports for your 3D prints, your goal should be to balance the density & thickness of your supports with the cooling speed. To put it simply, the more your supports will be exposed to high temperatures (and the longer it takes to cool off), the more they will stick to your part. Hence the colder they remain, the easier it will be to remove your 3D printing supports.
Apart from having efficient coolers, the density of your supports is going to impact its temperature. Reducing the amount of matter within your supports will help them release heat. If your overhang is long, heavy or especially steep, you might need to make your supports dense to prevent your part from sagging. But keep in mind that the denser and thicker your supports are, the higher goes the risk of damage when removing the supports.
These are parts of the support generation options 3D slicers can help you tweak. But before you get to change that, there are a couple of ways you can optimize your 3D printing support structures in your design.
First of all, you have to figure out which orientation is the most consistent in terms of support generation. If you take a look at the two bridges, you will notice one difference: The second one is flipped upside-down, of course, but unlike the other one, it doesn’t need any support.
If you have already tried to play with the orientation of your part but believe it still requires too many supports, you may be able to tweak your overhangs. If for instance their angles are a bit too round and tilt over 45°, see if you can replace them using a single, less steep angle in your design. Another option you might want to try is to separate your design into two separate models. Going for this solution will definitely help you save on support materials, but in return, you will have to figure out how to reassemble your parts.
We have covered all the key points you need to know about when it comes to 3D printing using supports, or not. Also remember that another way you can get rid of support issues is to switch to a printing technology that doesn’t need any. Selective Laser Sintering 3D printers could in that way help you achieve high geometry 3D prints without dealing with the downsides of 3D printing supports. You can try Sculpteo’s online 3D printing service if you want to have access to SLS printers, and you can also contact us if you have any questions pertaining to your 3D printing needs.
Related Topics
- Return to Top
Get the latest 3D printing news delivered right to your inbox
Subscribe to our weekly newsletter to hear about the latest 3D printing technologies, applications, materials, and software.
What is support in 3D printing?
One of the most frequently asked questions when working with clients is “What is 3D printing support?”. In this section, we will clearly show what is commonly called support and what types of support exist at a given point in time.
Support material (supportmaterial) is an auxiliary material used in 3D printing to build complex objects and increase the quality and stability of construction. Without the use of support, it is impossible to 3D print models with cavities, overhanging structures, complex detailing, thin walls or ceilings, and other complex elements.
Simply put, support serves as a kind of temporary foundation for the printed product. Layered construction assumes that each next layer of the product relies on the previous one. In the case when the design of the product does not provide support under the first layer in one place or another, support comes into play.
It must be understood that the removal of supporting structures is one of the most difficult types of work.
Therefore, this article was written, fully explaining what support structures are and why they are needed in 3D printing.
How to determine where support is needed?
This is done automatically by the software supplied with all professional 3D printers. You just need to upload a file in STL format, and the program will independently calculate where the use of auxiliary material is necessary for high-quality construction. It is worth noting that most software also allows the user to edit the number and location of auxiliary structures. The software is directly related to the capabilities of a 3D printer and will automatically show you where support is needed and where it is not.
In addition, the program calculates the amount of auxiliary material needed before printing.
If we do not agree with the automatic calculation of supports by software for a three-dimensional printer, then software comes to our aid where supports can be placed manually. The picture shows an example of manually building supports in the AutoDesk MeshMixer program.
Types of support materials
Soluble
There are 2 types of soluble auxiliary materials such as HIPS and PVA. These types of plastics are used for printing supports in complex models, where high quality of the resulting product is an important component.
Each type of plastic has its pros and cons.
For example, HIPS can be used both as a base material and as an auxiliary. This plastic is soluble in limonene, so it is excellent for printing supports, where the main plastic is ABS, since they do not interact with each other. It also has its drawbacks - this is the high cost of limonene.
PVA, on the other hand, is used exclusively as an auxiliary material. It dissolves well in water and is only compatible with plastics where PLA is the main material. But there are two important differences from HIPS: the high cost of the material and the more simplified post-processing of the finished product.
3D printer in the process of printing with support structures.
The finished product immediately after 3D printing.
Detail after washing out the supporting structures.
Mechanically removed
Excess material is broken off, sawn off, scraped off. In this case, the support is the same material from which the model itself is built. But, in order to facilitate its subsequent removal and reduce the consumption of model material, the support is built more “sparsely” compared to the object itself. It has a much lower density and strength, only sufficient to temporarily support the weight of the object being grown.
Fused
Melts and flows out with slight heating (much lower than the deformation temperature of the main product). Usually has a wax base. Advantages: delicacy, accuracy of application. Used in photopolymer and wax 3D printers of the ProJet series by 3D Systems.
Powder support
Separately, it is worth mentioning powder 3D printing technologies. Here, the same material acts as auxiliary and main. However, that part of the powder that was "auxiliary", after cleaning, can be reused as the main material. Due to this, such technologies are practically waste-free. The only exception to the rule is metal 3D printing. When printing with metal, metal shrinkage must be taken into account. In order for your part not to twist or warp during the printing process, it is necessary to fix it with supports.
Tags: 3D printing, 3D printer, 3D printers, Additive technologies, Parts, Inventions, Body parts, support material, support
What is support material in 3D printing
Support material — an auxiliary material used in 3D printing to build complex objects and increase the quality and stability of construction. Without the use of support, 3D printing of models with cavities, overhanging structures, complex detailing, thin walls or floors, and other complex elements is impossible.
Support serves as a kind of temporary foundation for the printed product. Layered construction assumes that each next layer of the product relies on the previous one. In the case when the design of the product does not provide support under the first layer in one place or another, support comes into play.
Support serves as a kind of temporary foundation for the printed product. Layered construction assumes that each next layer of the product relies on the previous one. In the case when the design of the product does not provide support under the first layer in one place or another, support comes into play.
Detail of complex geometry before and after removal of support.
Complex geometry detail before and after removal of support.
Benefits of using support material
- Ability to print more complex objects (than without support).
- High accuracy and stability of building complex and small elements (does not allow them to "disperse", deform under the weight of the following layers).
- Significant reduction in CAD file constraints (slopes, wall thicknesses, corners, cavities, etc.).
Benefits of using support material
- Ability to print more complex objects (than without support).
- High accuracy and stability of building complex and small elements (does not allow them to "disperse", deform under the weight of the following layers).
- Significant reduction in CAD file constraints (slopes, wall thicknesses, corners, cavities, etc.).
How to determine where support is needed?
The software that comes with all professional 3D printers does this automatically. You just need to upload a file in STL format, and the program will independently calculate where the use of auxiliary material is necessary for high-quality construction. It is worth noting that most software also allows the user to edit the number and location of auxiliary structures.
How to determine where support is needed?
The software that comes with all professional 3D printers does this automatically. You just need to upload a file in STL format, and the program will independently calculate where the use of auxiliary material is necessary for high-quality construction. It is worth noting that most software also allows the user to edit the number and location of auxiliary structures.
Model placed in virtual print chamber
Model in the virtual print chamber with automatically calculated support
Model placed in the virtual print chamber
Model in the virtual print chamber with automatically calculated support
In addition, the program calculates the amount of support material required before printing.
In addition, the program calculates the amount of auxiliary material required before printing.
Types of support materials
Mechanically removed
Excess material is broken off, sawn off, scraped off. The simplest type, usually used in cheap desktop printers that work with plastic. In this case, the support is the same material from which the model itself is built. But, in order to facilitate its subsequent removal and reduce the consumption of model material, the support is built more “sparsely” compared to the object itself. It has a much lower density and strength, only sufficient to temporarily support the weight of the object being grown.
Types of support materials
Mechanically removed
Excess material is broken off, sawn off, scraped off. The simplest type, usually used in cheap desktop printers that work with plastic. In this case, the support is the same material from which the model itself is built. But, in order to facilitate its subsequent removal and reduce the consumption of model material, the support is built more “sparsely” compared to the object itself. It has a much lower density and strength, only sufficient to temporarily support the weight of the object being grown.
Manual support removal process video
Manual support removal process video
Soluble
Auxiliary material dissolves in a special liquid. This method of removing support, for example, is used in Stratasys' uPrint SE professional plastic 3D printers. Advantages: withstands significant loads and temperatures, dissolves without damage to the base material.
Soluble
Auxiliary material is soluble in a special liquid. This method of removing support, for example, is used in Stratasys' uPrint SE professional plastic 3D printers. Advantages: withstands significant loads and temperatures, dissolves without damage to the base material.
In the photos you can see the whole process of calculating, building and removing the soluble support material. 3D printer - uPrint SE Plus. Dissolution time - 1.5 hours.
Lost wax
Melts and flows out at low heat (well below the deformation temperature of the main product). Usually has a wax base. Advantages: delicacy, accuracy of application. Used in photopolymer and wax 3D printers of the ProJet series by 3D Systems.
In the photos you can see the whole process of calculating, building and removing the soluble support material. 3D printer - uPrint SE Plus. Dissolution time - 1.5 hours.
Lost wax
Melts and flows out at low heat (well below the deformation temperature of the main product). Usually has a wax base. Advantages: delicacy, accuracy of application. Used in photopolymer and wax 3D printers of the ProJet series by 3D Systems.
Lost-wax master wax and after removal
Lost wax master model and after removal
Washable
Special gel-like material that can be washed out of the master model with warm water. Advantages: simple removal process, high construction accuracy, does not damage the model material when removed. Used in photopolymer 3D printers of the Objet series from Stratasys.
Washable
Special gel-like material that can be washed out of the base model with warm water. Advantages: simple removal process, high construction accuracy, does not damage the model material when removed. Used in photopolymer 3D printers of the Objet series from Stratasys.
Model before printing
Model in build chamber with support material
Finished model after removal of support material
Model before printing
Model in build chamber with support material
Finished model after removal of support material
9014 Powder Support We should also mention powder 3D printing technologies (CJP, SLS, SLM). Here, the same material acts as auxiliary and main. However, that part of the powder that was "auxiliary", after cleaning, can be reused as the main material. Due to this, such technologies are practically waste-free.Powder support
We should also mention powder 3D printing technologies (CJP, SLS, SLM).