3D printer not feeding filament
6 Solutions on How to Fix 3D Printer Filament Not Feeding Properly – 3D Printerly
One time, I remember trying to start off a 3D print, but my filament just wasn’t feeding through properly. It took me a while to finally figure out what was happening, why it was happening, and how to fix it. This article will detail that process and some quick solutions to help you if you also experience this.
If your filament is not feeding properly, you should reduce retraction settings, check your PTFE tube for clogs or damage near the ends, unclog your nozzle, check the teeth on your extruder for wear, adjust idler pressure on your feeder gear and check your extruder motor for instability.
Once you do a series of checks and correct them as you find issues, your filament should feed through your 3D printer just fine.
Please keep reading for more details behind these solutions to make sure you get it right.
Why Does Filament Not Feed Properly? Causes & Solutions
- Blockage in Extrusion Path
- Bad Retraction Settings
- PTFE Liner Worn Out
- Incorrect Spring Tension or Idler Pressure
- Worn Out Extruder/Feeder Gears
- Weak Extruder Motor
Blockage in Extrusion Path
You have to make sure your extrusion path is clear and free of obstructions, so your filament can feed through at the proper rate. This goes anywhere from the filament flowing inside the extruder, to the extruder itself, through the PTFE tubing if you have a Bowden set up, through to the nozzle.
Solution
- Check that your filament have a smooth and clear path to feed into the extruder. The spool holder should be close to your extruder and the filament ideally should be coming an angle which is fairly curved in the flat direction.
You can print a filament guide to achieve this.
- Make sure your PTFE tube is clear of obstructions or loose filament. Capricorn PTFE Tubing from Amazon has a smooth internal path which reduces obstructions.
- Clean out your nozzle, especially if you change printing materials a lot – Use some good cleaning filament (Novamaker 3D Printer Cleaning Filament from Amazon) for a good clean.
Once your extrusion path is cleared and allows filament to pass through smoothly, you should be a lot closer to the way of being able to feed your filament properly.
Bad Retraction Settings
I’ve been through this one before, so I know how bad retraction settings can negatively affect your prints, and even cause them to fail altogether. The retraction settings mainly consist of retraction length and retraction speed.
These are the length and speed at which your filament gets pulled back into the extruder, so material doesn’t leak out filament while moving to the next extrusion location.
Solution
People usually have their retraction lengths and speeds way too high. I would lower retraction length to around 4-5mm for Bowden (2mm for a Direct Drive extruder) and retraction speed to 40mm/s as a good starting point, then you can trial and error that as you wish.
I wrote an article called How to Get the Best Retraction Length & Speed Settings
You don’t want your filament to be generating extra strain from the pressure of the back and forth movements from retractions.
The proper way to do this is to find the optimal settings for your 3D printer, whether that is from researching online or doing it yourself.
I would get a small test print and print it several times using different combinations of retraction speeds and lengths to see which one delivers the best quality.
A very popular print file for testing your 3D printer is the ‘Test Your Printer V2‘ from Thingiverse.
PTFE Liner Worn Out
Now come to the PTFE liner, if you observe that it has worn out because of the heat, this can be one of the reasons for the filament not feeding properly. This could even clog the filament to become smaller in diameter than usual.
Heat creep can occur when your heatsink isn’t dissipating heat properly, which is when heat travels to where it isn’t supposed to, back into the end of the PTFE tubing.
Solution
Double-check the ends of your PTFE tube, especially on the hotend side and replace it if necessary. Get yourself a high quality, high temperature resistance Capricorn PTFE Tube from Amazon to prevent heat damage to your Bowden tube.
Incorrect Spring Tension or Idler Pressure
You will find such trouble with the filament not feeding properly if the filament has been eaten away by the feeder gear. A strong spring tension on your extruder idler isn’t always a good thing, especially if it’s eating right into your filament.
If the idler pressure is not enough, it could also be a cause that the filament is not coming out of the extruder because of less pressure.
Solution
Trial and error your spring tension on your extruder, where your filament comes through to. This is a pretty quick fix so you can test it without too much hassle.
Worn Out Extruder/Feeder Gears
Another reason which could disrupt the functioning of the filament and stop it from coming out, is the teeth of the feeder gear being worn out, which affects the continuous flow of filament.
Having a cheap extruder that isn’t made very well can lead to this issue arising after some time.
Solution
If this is the cause of your filament not feeding properly in your 3D printer, I’d advise to get yourself a new all-metal extruder or even better yet, a dual-drive extruder for the higher quality extrusion performance.
A good all-metal extruder would have to be the CHPower Aluminum MK8 Extruder from Amazon. It’s a great replacement extruder to upgrade from the stock one that comes from the factory.
It’s easy to install and gives stronger pressure in pushing the filament through which improves printing performance. Fits the Ender 3, Ender 5, CR-10 Series & more.
If you want to go a step above that, I would go for the Bowden Extruder V2.0 Dual Drive from Amazon.
This extruder is suitable for most 3D printers and implements an internal gear ratio of 3:1 along with sleak designs and CNC-machined hardened steel drive gears, all working to increase feeding strength and minimize slippage.
You’ll be able to print with most filament including the flexible TPU at a firmer level, and it has a high performance ability, allowing it to give more torque and reduce the burden of the motor, leading to an extended motor life.
The packing of this Dual-Drive Extruder is done nicely so it doesn’t experience damage while in transit.
Weak Extruder Motor
Check the motor of the extruder in case it is clicking. It’s a good idea to look at your filament to check whether it is straight or deformed.
I found that when my motor started clicking, it was because the nozzle was too close to the bed, which meant the flow rate of the extruded plastic couldn’t keep up with how much plastic was actually coming out.
If your motor is not working properly, i.e., it is either loose, or the cable is broken from it, and it has a loose connector pin. All this could affect the filament making it not to feed properly.
Solution
Make sure to check over your extruder motor wiring and try changing the motors around to see if it fixes the problem. This is a solution to try after you’ve tried many of the other solutions because it takes a little more work.
Quick Solutions to Filament Not Feeding Properly
- Check hotend temperature and make sure it’s correct
- Check your motor amperage extruder, as you may have little strength behind it
- Make sure the filament isn’t too tight between the gear and the pulley
If you find you can’t push filament through the extruder properly, sometimes just taking apart your extruder and giving it a thorough cleaning and oiling is enough to get it working again. One user who started having printing problems did this and solved the problem.
If your extruder is really dry, it doesn’t have the slip it needs to operate optimally. Doing this also helps when your extruder is not pushing filament or filament is not going into the extruder.
Sometimes the end of your filament can bulge and be larger than the 1.75mm entrance of the extruder pathway, so making sure to snip the end of the filament can help it to feed through into the extruder.
In some cases, you may have to twist the filament as you are putting it through the extruder to ensure it is going through the hole on the other side.
Why is Filament Not Coming out of Nozzle?
Jammed Filament and a Clogged Nozzle
This could happen if your filament is jammed in the nozzle or the extruder and is not coming out because of the clogging. For this, you must clean your nozzle completely.
You can use an acupuncture needle for that purpose to break the particles in the nozzle, but before you must heat the needle to its last temperature.
After the particles are broken, you can use a filament, enter it in the nozzle and then let the nozzle cool down, once it has reached to a low temperature, you should do the cold pull and keep doing it until it gets cleaned.
I wrote an article about 5 Ways How to Fix & Unclog Extruder Nozzle & Prevention which you can check out.
Nozzle Too Close To the Bed
If the nozzle is close to the bed, it jams the way of the filament to come out, which affects its functioning, and you won’t be able to do any kind of printing. For this, you must follow the distance rules and keep your nozzle at a distance during printing.
Why is Filament Not Pulling from Extruder?
Plastic is Not Flowing
If the filament has stuck in the extruder, it might be because of the liquid plastic that got hardened in the cold side of the hot end and nozzle got jammed. You can follow the same trick of removing the debris from nozzle here and get it cleaned for functioning.
Extruder is Not Primed at the Beginning
If the extruder is not primed at the beginning, this could cause the hot plastic from the last printing process to be cooled down, which would ultimately jam the extruder. What you need to do is to get your extruder primed before printing anything. For this, you must clean your extruder before starting.
Applying a few Skirts to the start of your 3D print should fix this issue. You can read my article Skirts Vs Brims Vs Rafts – A Quick 3D Printing Guide for more.
Heat Creep
If the hot end of the extruder hasn’t cooled down properly and you start the printing process, it will make your filament viscous, and you would run into this heat creep issue.
It happens when the filament liquefies too high up, and the extruder would require more pressure to let the filament out. You can feel this because your extruder motor will be making a clicking sound. You can avoid this inconvenience by using a cooling fan to let the hot end cooled properly.
Check out my article How to Fix Heat Creep in Your 3D Printer.
how to solve it! – 3D Solved
The most probable cause that brought you to this article is having a 3d printer that is currently unable to properly feed filament. So let’s make this intro short and go straight to answering the following question: how do you fix a 3d printer that is currently not feeding filament?
The main causes that lead to a 3d printer not feeding filament are a clog along the extrusion path, a damaged PTFE tube, incorrect retraction settings, unwanted filament tension, too high (or too low) extrusion temperature, a clogged nozzle or worn-out driver gear.
I know, this list of issues is not very helpful if we do not address each cause individually, and that is exactly what I’ll do in this article! As is the case with most troubleshooting articles, the readings are of a reactive instead of preventive nature. That’s obviously the way it should be, but I’ll also give tips and tricks to avoid these issues in the future. It’s not that I don’t want you to come back to our blog, but I really think that we have lots of more interesting and happier articles for you to read!
Table Of Contents
- Common causes of 3d printer not feeding filament
- Causes that lead to a clogged nozzle
- How to unclog a nozzle
- Conclusion
- Check out our recommended products section
Common causes of 3d printer not feeding filament
Extrusion path clogged
To properly feed the filament, your 3D printer needs to have a clear extrusion path. Any obstructions here will mess with the flow rate of the filament. To fix this problem make sure your filament has a smooth and clear path, this means checking all the way from the filament spool to the extruder nozzle. Ideally, the filament spool should be close to the extruder nozzle and the filament should be coming at a curved angle.
PTFE tube may be damaged
If your heatsink is not working properly it could lead to heat traveling outside the melting zone. This heat can damage the PTFE tube jamming the filament. Check the PTFE tube ends for any signs of deformation. If necessary, replace the PTFE tube with a higher quality one for better insulation and higher temperatures.
The tube I just linked is the blue Capricorn tube that comes with a tube cutter as well as a couple nozzles, and this tube is much better than the standard white/transparent PTFE tube that comes with most printers, such as the Ender 3.
Incorrect retraction settings
The retraction settings let you control the length and speed at which the filament will retract into the extruder nozzle when changing the extruding location. This is done to avoid leakings while the nozzle moves to a different spot.
If you are retracting too much filament or the retraction speed is too high, the back and forth movement could grind the filament making it harder for the drive gears to keep moving it. Start with a 40mm/s speed and 5mm retraction length, if you see signs of stress in the filament lower those settings.
Filament tension
If the filament tension between the drive gears and the spool is too high, the drive gears will need to work harder to move the filament resulting in the gears eating the filament to a point where it messes with the normal feed flow.
Extruder temperature
If the extruding temperature is too low the filament will have a harder time going through the nozzle. Try increasing the temperature by 5-10 degrees as it will allow for easier filament flow. Always check your filament spool for the recommended melting temperatures. Too high temperatures can also be a problem, melting the filament before time thus jamming the system.
Worn-out drive gear
In some cases after a lot of work, the teeth of the drive gear can get worn out and stop properly feeding the filament. Check them to see if you need to replace them and if necessary get a new extruder hot end. For years of good 3D printing get a high-quality hot end.
Clogged nozzle
Clogged (left) vs unclogged (right). The same nozzle before and after a cold/atomic pull.If you notice that filament is not going through the nozzle or that it is coming out stringy, it might be due to a partially or fully clogged nozzle. Over the lifetime of a 3D printer, you will need to make sure to maintain a clean nozzle to ensure quality 3D prints. As your 3D printer melts the filament and pushes it through the tiny nozzle, some leftovers might get stuck there and eventually jam the system.
Since this is a common issue and most probably the cause of your printer not feeding filament, we will go into further details and explain some tricks to avoid this problem in the future. Additionally, I’ll also explain step by step how to solve it.
Causes that lead to a clogged nozzle
Bad printing temperatures
If your printing temperature is too low, the filament will not melt properly thus making it harder for the drive gears to keep the filament going. At some point, the pressure will be so high in the extruder that the drive gears will start stripping the filament and the filament left in the nozzle will solidify and become a plug.
On the other hand, if your printing temperature is too high, the heat can spread out of the melting zone and start melting the filament before it should have. This effect is called “Heat Creep” and when this happens, the drive gears will have a hard time pushing the softened filament. Eventually, the drive gears can not keep up and the nozzle gets clogged. To prevent this always check the recommended temperatures for the material you are using.
Dust and dirt in the filament
If there are dust or dirt particles in your filament, they will burn as the filament goes through the melting zone. These burnt particles can stick to the inside of the nozzle, alter the proper filament flow, and eventually fully clog the nozzle. This issue is difficult to address, you should try your best to keep the filament clean. Store it in a plastic bag after the package was opened.
Nozzle too close to the print bed
When the nozzle is too close to the print bed, the filament will not be properly extruded as there isn’t enough space. This will cause the filament to be smeared all over the print bed as the nozzle travels. The lack of space between the nozzle and the print bed will produce retrograde extrusion. This means the filament will go back into the nozzle and the extra pressure this generates will likely cause a clog in the nozzle.
As a rule of thumb, the height should never be bigger than the nozzle diameter. A good starting point is to use a quarter of the nozzle diameter as the height. If you are using a 0.4mm nozzle, you can calibrate your printer by using a sheet of paper. The distance between the print bed and the nozzle should be enough for the paper to be placed between them, although relatively tight. This is the most common “calibrating tool” used since it normally has a 1/10 millimeter thickness.
Low-quality filament
Low-quality filaments can be problematic as these filaments don’t get a rigorous test before they go to the market. They can present different diameters at different points, the thinner parts can be difficult for the drive gear to grab, and the thicker parts will take longer to melt.
These variations in the melting point create an uneven and unclean flow of the filament which can lead to clogs. You can use a caliper and check different spots on the filament for diameter changes if those values show big differences you should change your filament.
I wrote loads of posts regarding the different filaments out there and what each one of them is generally used for, and much more.
However, here’s a quick list of the filaments/brands I’d recommend:
- Sunlu PLA
- Polymaker ABS
- Sunlu PETG
- Polymaker Nylon
- Polymaker ASA
- Polymaker Polycarbonate
How to unclog a nozzle
Rest assured: this nozzle is clogged.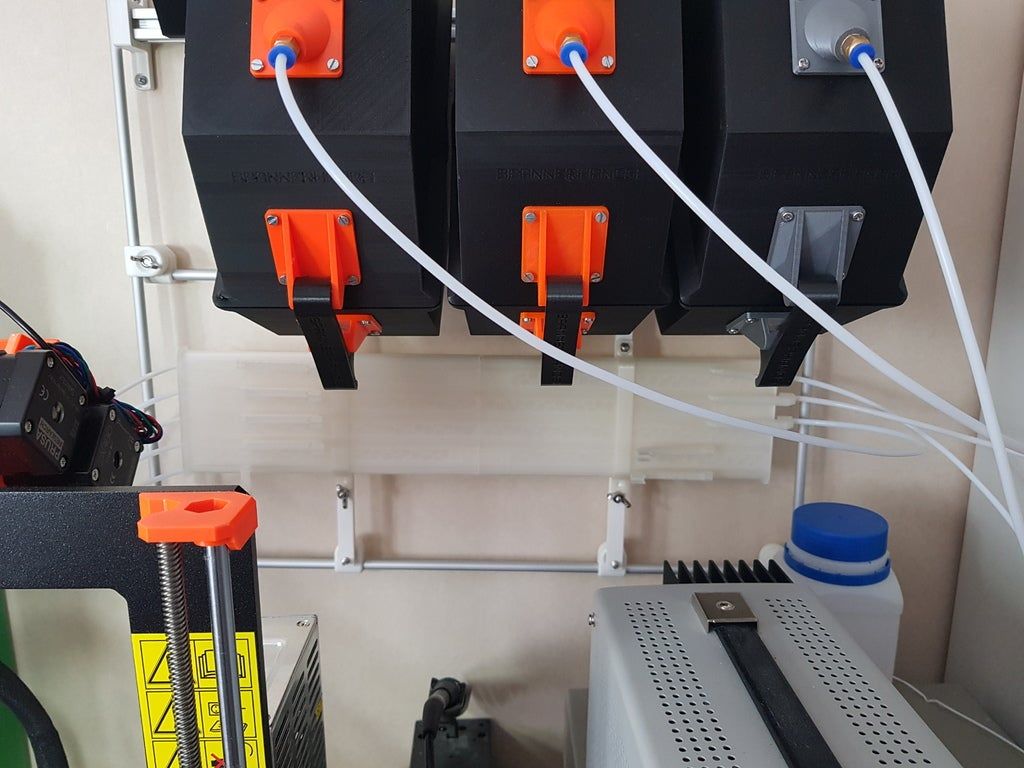
There are a few different methods that you can use to unclog the nozzle. These vary depending on how clogged the nozzle is. Try the following methods.
Unblock a partially clogged nozzle
- Brass wire brushing: The first method you should try is to use a brass wire brush to clean the outside of the nozzle.
- Cleaning filament: Cleaning filaments are specifically made to clean the nozzle. Print with them using the recommended settings on the package. As it goes through the nozzle it should carry with it all the leftovers that were clogging the nozzle. You should be doing this every time you change filaments as it will help to prevent any clogs.
- Manually push the filament: Heat the nozzle to the proper temperature for your filament, then manually push the filament through the nozzle until some of it is extruded. In some cases, the extra force provided is enough to eliminate the obstruction.
Unblock a fully clogged nozzle
- Guitar string/Needle: You can use an acupuncture needle or a high E or B metal guitar string to clean the nozzle. The needle/string needs to have a smaller diameter than the nozzle to avoid damaging it. Heat the nozzle to the correct temperature for the filament you were using and then gently push the needle/string through the nozzle to break the blockage. The next time you extrude filament it should come out with the particles that were clogging the nozzle.
- Atomic/Cold pull: For this method, we recommend using Nylon or ABS as PLA is more fragile. Heat the nozzle up to 250 degrees celsius for at least 5 minutes and then push your chosen filament through the nozzle until it starts oozing out a little. Let it cool down to room temperature so the filament solidifies and then heat it to 120 degrees celsius. Pull out the filament with a steady and firm jerk, you should see the dirt particles in the filament.
Repeat the process until the filament comes out clean and the tip of the filament preserves the shape of the nozzle.
Source
- Acetone: You can try using acetone to free the nozzle from obstructions. Remove the nozzle from the printer and place it in a recipient, then pour acetone until the nozzle is fully submerged. Leave it there for 24 hours, shake the recipient every few hours to help dissolve the obstructions. You can even use a needle while this is going on to see if it helps to break the blockage. After 24 hours, take it out and make sure to dry it with a towel so there aren’t any acetone leftovers.
- Heat gun: Last but not least you can try to melt the obstructions with a heat gun or a blowtorch. Remove the nozzle from the printer and hold it with pliers against the heat gun. Avoid direct heat if you are using a blowtorch as it can melt the nozzle.
Check against a light source to see if the nozzle is clear of obstructions. Use a needle if it is still clogged.
Conclusion
By now, I hope you were able to solve your issue. I think I’ve gone through most of the issues you can come across that lead to having this annoying issue. If your problem still persists, there’s no shame in reaching out to a local 3d printer expert that services 3d printers for a living. He will surely be able to fix your printer and let you know what caused the issue in the first place. If you are like me, you will surely ask him a ton of questions in order to know how he solved the problem!
We created a recommended products section that will allow you to remove the guesswork and reduce the time spent researching what printer, filament, or upgrades to get, since we know that this can be a very daunting task and which generally leads to a lot of confusion.
We have selected just a handful of 3D printers that we consider to be good for beginners as well as intermediates, and even experts, making the decision easier, and the filaments, as well as the upgrades listed, were all tested by us and carefully selected, so you know that whichever one you choose will work as intended.
3D printer does not feed plastic from the nozzle when printing.
Recently, 3D printers are beginning to gain popularity, and this is not surprising, because 3D printing allows you to create almost any shape, and the printers themselves are starting to drop in price, as a result of which they become more affordable. It would seem that it is enough to buy a printer, but after buying a printer comes the understanding that printing is not as easy as it seems, and setting up and calibrating the printer can take a lot of time, from several hours to several days, or even weeks. nine0003
In this article I want to tell you how to solve one of the most annoying problems that you will surely encounter with any 3D printer - when the plastic does not feed when printing or it feeds in pieces.
I will give an example from personal experience. Not so long ago, about a couple of months ago, I purchased my first Anycubic i3 Mega 3d printer, it took me a week to calibrate the printer and study the basic parameters for printing, after which I printed various shapes for a long time without problems on PLA plastic, which went to kit. And so, when the PLA plastic ended, I decided to buy myself ABS plastic for a test to see what the difference was from PLA. I inserted ABS plastic, printed the first figure, and when I started printing the second figure, I got the same result as in the photo - the plastic did not stick to the table, it was squeezed out of the nozzle in pieces, printed lines through one, and eventually stopped printing altogether:
My first suspicions fell on the nozzle (photo), which was eventually confirmed - the nozzle clogged when mixing ABS plastic with the remnants of PLA plastic, which burned into the nozzle.
The solution to the problem was simple: take pliers, clamp the nozzle, take a burner and burn the plastic out of the nozzle for about five minutes. If you want the nozzle to return to its original shiny appearance, then we throw it into a bowl of boiling water and vinegar / citric acid.
A day after cleaning the nozzle, problem No. 2 appeared - the plastic again stopped “going” from the nozzle. I started cleaning the nozzle again, but it didn’t help, by the way, the plastic began to grind against the gear of the stepper motor (the stepper motor could not push the plastic thread into the extruder, as if something was in the way), in the end it turned out that the plastic was clogged / burned in the thermal barrier due to the fact that the sealing tube was not inserted to the end of the thermal barrier, the thermal barrier itself heated up and melted the ABS plastic, creating a “plug”:
Plug:
The solution to the problem is the same as with the nozzle - we disassemble the extruder, “pull out” the plastic with a burner, push the sealing tube to the very end, assemble the extruder, enjoy printing.
Below is a photo of the extruder, in the photo the upper part is a thermal barrier (it must be cooled), the lowest golden part is a nozzle, between the thermal barrier and the nozzle is a heating element that melts plastic.
Below I want to give additional ways to solve the problem when plastic does not come out of the nozzle, let's look at them. nine0003
1. Choose a plastic recommended by the printer manufacturer
Each type of plastic differs not only in color, but also in a number of properties - material, diameter, melting point, so we look at the characteristics of the printer, which plastic can be used. Example: you bought plastic with a diameter of 2.85, and your printer has a sealing tube with a diameter of 1.75, the plastic will simply get stuck in the tube.
2. The plastic has run out or the plastic is tangled in the spool
If you have chosen the right plastic, but printing still does not work, look at the spool, the plastic may have already run out or is tangled. nine0003
3. Plastic has been ground off on the gear of the stepper motor or a problem with the clamping mechanism
We look at the stepper motor that feeds the plastic into the extruder, if the gear is spinning and the plastic does not go, then there may be 5 problems:
- The extruder is clogged, see item 4.
- Slow feed has chipped plastic on gear. We take out the “broken off” plastic from the sealing tube, insert a new plastic.
- The clamping mechanism has broken. Usually it consists of a spring and a roller, we look, maybe the spring has moved away. nine0003
- If you changed the stepper motor drivers, then the motor may not have enough power to push through the plastic.
- Stepper motor failure. We check by replacing the engine from some axis.
4. Extruder clogged
Above, I described what the extruder consists of (thermal barrier, heating element, nozzle). If the extruder is clogged, then you need to understand in which of its parts, for this we disassemble the extruder completely and see where the plastic is, burn it out with a burner. nine0003
If the plastic enters the extruder and the extruder is not clogged, check the wires on the heating element and the heating element itself, it is possible that the contacts are faulty due to which there is no heating, due to which the plastic is not delivered.
5. Insufficient temperature for heating plastic
If everything is ok with the previous points, check the heating temperature for plastic in the print settings. Each type of plastic has certain properties, one of them is the melting point. If the temperature is very low, the plastic will not melt and will not come out of the nozzle, and vice versa, if the temperature is too high, the plastic may burn and clog the nozzle. nine0003
Example of temperatures for the two most popular plastics:
PLA - heating temperature 180 degrees, table heating temperature 60-80 degrees
ABS - heating temperature 240 degrees, table heating temperature 110 degrees
6. Nozzle pressed too hard against the table
If the table is not calibrated and the nozzle is strongly pressed against it, then the plastic will not flow, you need to calibrate the current table so that there is a gap between the table and the nozzle of 0.5-1 mm. You need to calibrate at 5 points (at the edges and the center). nine0003
5 Clogged nozzle causes and remedies・Cults
You are in the middle of a long 3D print, you hear a click and the filament stops extrusion. Your printer may have failed. Seizures and blockages happen to all manufacturers, and luckily they are pretty easy to fix!
Before we start, it's important to define each of the parts we're talking about, as the wording can get a little confusing. We will focus on assembling the extruder, which consists of two parts: a hot end and a cold end. nine0003
The cold end pushes the thread forward. The filament is clamped between the gear and the bearing and is pushed forward by the stepper motor. The filament is fed into the hot end where it first passes through a melting zone to thin the filament before it is deposited outside the nozzle.
There are two types of extruders - bowden and straight. A direct drive extruder sits directly above the hot end and feeds the filament directly through it. The Bowden extruder is usually attached to the frame of the printer and brings the filament through a thin tube to the hot end. nine0003
Direct Drive Extruder
Bowden Extruder
When a filament gets stuck, it is either in the melt zone or the nozzle portion of the hot end, not the cold end. Now that we know what parts of the printer we are dealing with, let's look at some of the symptoms and causes of jams.
If the hot end is stuck, you may notice that less filament or no filament comes out of the nozzle! Here are some of the most common reasons:
1) Thermal creep: This may seem counterintuitive, but if the hot end is not cooled properly, the filament starts sticking too high at the hot end and we run into a problem called thermal creep. This happens when the filament thins too much and the extruder has to work much harder to push it through the nozzle until it becomes unable to do so and jams.
Solution: You will usually hear a squeak or click from the extruder motor when the filament is stuck, and if so, stop printing and remove the filament. Check that the hot end cooling fan is working properly and that the heatsink and heater block are securely fastened. In the case of hot ends like the V6 E3D, it is helpful to apply thermal paste to the thermal break wires. nine0003
2) Hot end temperature too low: If the hot end temperature is too low, the filament cannot be fed through it, causing the extruder to grind the filament, making extrusion more difficult.
Solution: Check the temperature rating for the specific filament. PLA likes to be extruded around 200C while ABS likes to be extruded around 245C. If you're having trouble with these specs, try increasing the iteration by 5 degrees, but make sure you don't exceed your hot end's maximum temperature. When switching filaments, make sure that all previous material has been removed before the temperature change. nine0003
3) Nozzle too close to the bed: If the nozzle is too close to the bed, there is no room for the filament to be squeezed out of the nozzle, resulting in clogging.
Remedy: Make sure your bed is level. See our bed leveling guide for more information.
4) Incorrect filament diameter: Most filament manufacturers claim that their filaments are within 0. 05 mm of the declared extrusion width (usually 1.75 mm or 3 mm). If your filament deviates too much from specification, you may have trouble feeding it through the hot end. nine0003
Solution: If you suspect this is happening, take a caliper and measure the thread in a few random places to see if it is within specification. If the thread diameter is constantly decreasing, it may be time to consider a new brand.
5) Dust or particles: Dust or other small particles can stick to the filament until it reaches the hot end and burns off, causing annoying clogging.
Remedy: Unlock the nozzle using the cold pull method - see below for a more detailed description of its operation. nine0003
Some articles recommend using a cutter or drill to clean the nozzle. For those of us who can't rely on power tools, fire and chemicals, here's a safer way to remove filament from a nozzle called "cold drawing".
The idea behind cold drawing is that you set the hot end to the glass transition temperature of the filament. This is the temperature at which the filament is between the solid and the liquid. This allows you to remove the thread and take all the leftovers with you. It works best with nylon, ABS or PLA. nine0003
Before you start: If you are using a Bowden extruder, remove the tube and any materials in it before starting work, as cold shooting with a Bowden tube can be difficult. After completing the cold firing, replace the Bowden tube.
Step 1: Heat the nozzle to print temperature and manually feed about 10 cm of filament through the hot end (where the Bowden tube was). Try to keep the thread as straight as possible. A natural or light-colored thread is best, so that when it is removed, the remains are visible. If your hot end is too clogged to pull out, take some thin wire and pliers and stick it into the tip of the nozzle to clear the clog. nine0003
Step 2: Once the filament comes out of the nozzle, lower the nozzle temperature (120C for ABS, 90C for PLA and 100-140 for Nylon). Try to use the lowest temperature for this step. It should be hot enough that the thread is pliable, but not so hot that it is too soft. Be sure to cut off the filament dripping from the nozzle before starting the broach.
Step 3: Pull on the top of the thread until you feel it slowly pull away. If it comes off too easily and no sediment is left at the end, lower the temperature. If you find it difficult to get it, increase the temperature until it comes out. nine0003
You'll know you've done it right when there's a small point at the end and possibly some leftover thread (this is more obvious when shooting cold with white or clear thread).
The Mkme lab also has a great video tutorial on how to do this:
You may need to do this a few times to remove any leftovers. As a result of the last cold pull, you should have a smooth, clean piece of thread (no dark residue). When you are sure all blockages have been cleared, replace the Bowden tube and try printing. nine0003
By following these tips, you will be able to clear nozzle clogs and hopefully prevent them from happening again. Happy printing!
via Pinshape
This page has been translated using machine translation. Suggest the best translation
Previous
ShareNext
Similar publications
We love shiny things, so we're making a tutorial on polishing and finishing metal-filled filaments. These techniques open up a world of possibilities for surface finishing of 3D printed parts. nine0003 Read more
While designers often use desktop 3D printers to iterate and test their designs, sometimes the function of 3D printing isn't so much to test form, fit, or function, but to look really good for presentation. However, anyone familiar with the use of desktop 3D printers knows that there are some drawbacks to the look and feel of typical FDM 3D prints.