3D printer knitting
3D Knitwear: How 3D Printing is Revolutionizing Fashion
Published on December 6, 2022 by Mikahila L.
In recent years, 3D printing has become growingly everpresent. From medicine, aerospace, to design, and construction — every day there’s news about breakthroughs, innovations, and developments in the additive manufacturing industry. However, in one particular industry, it’s still pretty quiet regarding developments around 3D printing. We’re talking about the fashion industry. It cannot be denied that the first experiments and advances in 3D printed clothing have only been recorded relatively recently. Yet, if you have followed these developments in fashion a little more closely, you may have noticed that these are high-end fashion, i.e. clothing created for the runways and red carpet and not for everyday wear. The reason why the combination of 3D printing and clothing seems so difficult is quite simple: The materials used in 3D printing, mostly plastic, and metal, are not flexible enough. To counteract this problem, some fashion and 3D enthusiasts have been looking into suitable options and ultimately honed in on one solution: 3D knitwear. But, what exactly is 3D knitwear? How does its production method differ from additive manufacturing and conventional textile production? Will 3D knitwear be available as ready-to-wear for ordinary consumers in the near future? We got to the bottom of this topic in more detail and we clarify all of these questions with the help of various expert opinions from the industry.
In order to understand the principle of 3D knitwear and its differences and similarities to 3D printing, it is first necessary to take a look at the definitions. Gihan Amarasiriwardena, co-founder and CEO of the Ministry of Supply, defines 3D printing as follows: “In 3D printing, molded products (such as plastics) are produced by adding a layer of material (often plastic or synthetic) according to a given digital Design is ‘printed’.” Rosanne van der Meer, designer and founder of New Industrial Order, offers a broader definition: “3D printing is the production of a three-dimensional shape on the basis of a filament that is formed by a machine. “ In fact, 3D printing is all about computer-controlled machines creating three-dimensional objects and building them up layer by layer. The question now remains whether 3D knitwear is made according to the same principle.
In 3D printing, the object is additively manufactured layer by layer.
Production of 3D Knitwear
The manufacturing process of 3D knitted fabrics is quite similar to other 3D objects. Both begin on a computer: CAD software is used to create the design and ultimately to obtain a programming language. The digital codes are then forwarded to the machine, which then begins the manufacturing process. However, the machine used is where knitwear and traditional 3D printing diverge. The primary difference from additive manufacturing is that the machine is not a 3D printer that processes filament or powder through extruders, rather, a knitting machine that can produce a three-dimensional garment in a single pass by uniting it thread by thread. Consequently, it should be noted that the principle is essentially the same both are based on software and are additively manufactured, but the material creates a big difference between the two methods.
Therefore, it is hardly surprising that industry experts agree in saying that 3D knitted goods are not manufactured using 3D printing, but rather, 3D knitting is a technology in its own right. Gerard Rubio, co-founder, and CEO of Kniterate, a company that sells 3D digital knitting machines, adds the following about his company’s machines and the use of the word 3D in connection with the production method: “These machines are capable of 3D knitting. But these machines are not necessarily 3D knitting machines.” This is because flat, single-layer garments like scarves can also be printed with a Kniterate machine, which eliminates the additive manufacturing aspect. Rosanne van der Meer adds that she deliberately uses the term ‘3D printed knitwear‘ for her products in order to make a clear distinction between 3D knitwear and conventionally produced knitwear.
Compared to Conventional Textile Production
Now that the differences and similarities between 3D knitwear and 3D printing have been outlined, the question remains whether and, if so, why 3D knitwear should be preferred to traditionally manufactured clothing. In order to provide a reasonable answer to this, conventional textile production must first be examined more closely.
This is still a touchy subject, with so few companies keeping their value chains and production methods transparent. Obvious and ongoing issues such as child labor, low wages, and inadequate protective measures in low-cost manufacturing countries are joined by the astronomically negative impact the industry has on the environment. From the cultivation of cotton, whereby both the use of pesticides and an enormous waste of water are recorded, to transit once the material has been broken down, and shipped to be processed into yarn and ultimately fabric in another country — this phase alone requires much examination for improvement.
Then, we have the woven fabric being sent back to be bleached or dyed at another factory. The harmful substances used in this process mostly end up in the wastewater, which in turn leads to the pollution of rivers and oceans. Lastly, the garment is sewn, knitted, and finished again in a different facility, with a large amount of material being wasted in the manufacturing process. The finished products are sent to the various branches around the world. The unbelievably long transport routes, which significantly increase Co2 emissions, rounds out the disadvantages of conventionally produced clothing. Although there are of course also smaller manufacturers who pay attention to sustainable, fair, and regional production, large-scale fashion producers that use traditional production channels still dominate the clothing market.
There are many problems with the conventional textile methods of large-scale fashion producers. These include the exploitation of workers in low-wage countries and the negative impact on the environment.
These social and environmental problems are primary focuses for CEOs Gerard Rubio, Gihan Amarasiriwardena, and Rosanne van der Meer, which is why they all pay attention to sustainability in the development of their companies and in the manufacture of their products. Awareness begins with the procurement of materials: While more than half of all clothing is produced using man-made fibers, mainly polyester, but also nylon, elastane, and acrylic, which are obtained from fossil fuels and therefore have a negative environmental impact; new industrial methods use merino wool which is obtained sustainably and as a natural fiber which generally has a smaller footprint compared to synthetic fibers.
Rosanne van der Meer also adds that she relies on high-quality yarn in order to achieve the best possible results and in order to not run the risk of the thread breaking in the middle of the knitting process and thus having to restart production. A special feature here: even if the thread were to break, the half-finished knitted part could be recycled since the knitwear is designed in such a way that it can be separated again. This means that the material used can be recovered — another sustainability factor. As far as the material is concerned, large savings can be made using 3D knitwear, as the machines produce additively In just one pass and therefore only requires the threads that will be used, thereby eliminating numerous production steps and saving a lot of time and costs. Gihan Amarasiriwardena confirms this statement: “With 3D-printed knitwear, only the required fabric is used. This results in approximately 30% less material waste”. Sustainability also plays a role at Kniterate. Gerard Rubio relies on plant-based yarns, which can be recycled, so items of clothing that are no longer wanted can be disposed of properly and not end up in a landfill.
The material plays a huge role in the manufacture of 3D knitted fabrics. (Photo Credit: Kniterate)
Since 3D knitwear is on-demand production, problems such as overproduction and inventory waste can also be avoided. Large-scale fashion producers are not able to react flexibly and quickly to changes in the market mainly due to long supply chains, which results in overproduction and overstocking. This is a fatal flaw in today’s fast fashion industry, where new collections and goods hit stores nearly every week. And where should the “old” items of clothing go that have not been bought? These resource and energy-intensive manufactured textiles mostly end up in the garbage or are partially incinerated. On-demand production that takes place on-site/in-house could be a solution here. Not only are transport costs and emissions saved as a result, but practically significantly less waste is produced.
This goes hand in hand with Rosanne van der Meer’s motto: “The starting point for a better climate balance in the fashion industry is less consumption. If you have timeless clothing that fits you really well, you will also consume less.” Thanks to 3D technologies, it is also possible to personalize 3D knitwear. Since the designs are created digitally and every needle stitch is equivalent to a pixel, patterns can easily be modified and adapted to customer requirements, which allows a lot of freedom. A special program from the start-up Shavatar also helped New Industrial Order to improve the accuracy of fit of their 3D knitwear without a 3D scanner – an essential aspect when it comes to buying clothes. With the help of the open-source system and the knitting machine from Kniterate, users are obviously also open to all creations and personalizations. Last but not least, the typical problems such as the exploitation of workers through in-house, regional productions are also eliminated.
Challenges of 3D Printed Clothing and Predictions for The Future
After explaining the numerous advantages offered by 3D knitwear, the question now remains as to why it is not yet increasingly available in stores. What are the current challenges and what improvements may still need to be made? Will 3D printed clothing and especially 3D knitwear be the future of the fashion industry?
Indeed, additive manufacturing of apparel faces a number of challenges. As mentioned earlier, the material is probably the biggest obstacle – which is why 3D knitwear is being resorted to. When a closer look is taken at previous projects involving 3D-printed clothing, such as products by fashion designer Danit Peleg, it quickly becomes apparent that the options are limited: The materials compatible with a 3D printer are mostly plastics such as ABS, PLA or the currently very popular and very flexible TPU. Although the latter can be used to create stretchy, movable 3D objects, it doesn’t begin to compare to the soft, comfortable texture of fabric. Although it could now be argued that the majority of conventionally produced clothing is also made of synthetic polymers, i.e. plastic, the problem lies with the texture. It makes a big difference what form the material is in: Fibers and threads have a filigree, elastic and flowing state, whereas filament has a comparatively thick, hard and rigid state.
3D-printed clothing differs in texture from conventionally produced goods. (Photo credit: Danit Peleg)
Furthermore, most 3D printers cannot produce fine enough details. Unlike 3D knitting, where the moving threads are processed by many small needles, the extruders of a 3D printer cannot produce anything comparable. The structure and texture of 3D-printed clothing is heavy and pitted, and the surface texture is likely to be quite cold and unpleasant. Gerard Rubio agrees, saying, “At this point, the materials are not developed enough. However, I strongly believe that 3D-printed clothing will be the future.”
With regard to 3D knitwear, other problems are encountered. Rosanne van der Meer particularly emphasized here the difficulty of creating the digital codes for the knitting machine. That is why she relies on extensive databases, suitable non-fiction books and an open-source system. The latter should support New Industrial Order’s goal of creating a workflow that makes the codes for 3D knitwear accessible to all those who show interest. Gerard Rubio echoes this sentiment. He, too, describes developing the right parameters as a major challenge. The road from the prototype to the final, commercializable Kniterate machine, which is very complex, was long and difficult, according to him. Referring to the future, however, Rosanne van der Meer sees no problem in this regard: “The technology is already established and ready to function, but the current system works completely differently.”
The biggest difference between 3D printed objects and 3D knitwear is the material. It is easy to see that much finer structures can be created with threads.
This is because on-demand production, which is the principle of most current 3D knitwear manufacturers, completely contradicts the market flow. The current fashion market is based on mass production and mass consumption. Changing long-established systems and breaking habits is extremely difficult, which is why more sustainable companies specializing in on-demand production and customization face a major hurdle in entering the market. Also, in terms of production costs, 3D knitwear cannot compete with conventional clothing due to low market compatibility. Therefore, the current products from New Industrial Order and Ministry of Supply are still rather in the luxury segment in terms of price, within the framework of which customers are willing and able to spend a lot for personalization, sustainability and quality.
However, the experts are confident that 3D printing will play a greater role in the fashion sector in the future and firmly believe that novel technologies will revolutionize it. Rosanne van der Meer summarizes: “Changes in the textile industry are slow. Yes: in the future we will find more additively manufactured clothing, but how far this progress is in the future cannot be said.”
Ministry of Supply offers, among other things, 3D-printed blazers and masks. (Photo Credit: Ministry of Supply)
What do you think of 3D printed knitwear? Let us know in a comment below or on our Facebook and Twitter pages. Don’t forget to sign up for our free weekly newsletter, with all the latest news in 3D printing delivered straight to your inbox!
Photo Credit: New Industrial Order
Knitting best STL files for 3D printer・Cults
Embroidery Floss Spool
€0.50
sheep knitting bowl
€1.50
Quick Stitch Markers
Free
Pompon tool
Free
Crochet Blocking Board
€1. 69
Stitch marker
Free
Crochet Blocking Board with Drawer
€2.81
Gear suitable for knitting machine
Free
Care Bear button
€0.50
knitting needle caps
Free
Portable Yarn Holder
Free
FORM FOR WEAVING BASKETS 14cm
€1
form for weaving baskets 10cm
€1
CSM Yarn Bobbin & Cone Winder Adapter Legare Knitting Machine
Free
Bent tip darning needle for knitting
Free
Robert Plant knitting with wool
€1. 49
5mm Pusher Combs for Passap Knitting Machine
Free
Knitting yarn holder yarn holder yarn spool holder yarn bowl knitting
€3
Hook hook
€1
Rotating yarn holder
€5.70
A5 Wool Inventory Card
€1.68
Passap Eyelet Bec fil rond
Free
steddy59
Free
Knitting loom
€1.07
Knitting Block Board Rods (3D Printable)
Free
Yarn Bowl V2
€2.26
paraffineur for brother knitting machines (tea candle holder)
Free
Garter Carriage Mast Cap Brother Knitting machines
Free
Prym Maxi drill adapter for M8 hex bolt
€1
Yarn bowl
€2. 11
1-3-1 Needle Selector for Standard 4.5 Knitting Machines
Free
The elasticity jig
€0.50
SENTRO KNITTING MACHINE DRILL ADAPTER
€1.22
Wool Gloves Christmas Candles
€3.76
Christmas Tree Candle 02
€3.76
Christmas Tree Candle
€1.88
Santa Claus crochet style
€1.25
LOOM "knitting "
Free
Knitting Loom
€4.07
Tension Fork // Addi Knitting Machine
Free
Customizable Knitting Needles
Free
Sentro knitting machine crank to hex driver adaptor
€1. 88
Knitting dolly-7
Free
Superba Tension Mast Cap
Free
texture, fabric, knitting, knitting, chainmail, texture cloth knitting
€2.34
sentro knitting machine leg
€0.94
Decorative Tatted Lace
€4
Sentro Circle Knitter Tensioner
Free
3D File 3D Sock Knitting Machine・3D Printed Model Download・Cults
➡️ Share 🔖 Add to 📸 Make ?Quality of creation: 4.5/5 (3 votevotes)
Ratings of participants on printability, usefulness, level of detail, etc.
- 👁 38.5k views
- ♥ 274 i like s
- ⬇️ 77 downloads
- 📸0 makes
Designer
kinko3
- Contact
3D Model Description
Sock Knitting Machine! These machines were originally made of metal in the early 1900s and were a common sight in homes. It's not easy to get hold of the original metal machines now, as most of them have been destroyed or damaged over the last century, and the ones that remain are worth a lot! - So turn around the printer, keep up with the times and let's make socks!
Below is a list of items you will need to complete your machine.
You will need 3mm bolts in different lengths, approximately this length:
Aussel Pan Head Screw Bolts Nuts Stainless Steel M3 Screw Nuts Assortment with Lock Flat Washers 300PCS (Pan Head Screws-300PCS) tools
You will need a 12 mm diameter mild steel rod (aluminum is fine and easier to work with) at least 200 mm long, something like this:
Round bar aluminium, brass, mild steel and stainless steel 3, 4, 5, 6, 8, 10 and 12 mm | eBay
You will need 2 x 24mm bearings with 12mm bore like these:
search card 6901ZZ Deep Groove Ball Bearing 12x24x6mm Double Shielded Chrome Steel Bearings 5Pcs : Amazon.co.uk: Business, Industry & Science
Car the following needles are used (although any needle of the same length and thickness will do):
Agatige 50PCS Steel Knitting Machine Needles, Knitting Machine Needles with Steel Sewing Tools for SK218 SK280 SK580 SK840 SK325 SK360 : Amazon. co.uk: Home & Kitchen
The counter is like this:
Broco electronic counter 5 digits 0-99999 digital click LCD digital electronic counter shock tester magnetic induction proximity switch shock resistant digit counter : Amazon.co.uk: DIY and tools
You will need M5 x bolts 25mm and nuts for the frame (nuts are optional as I didn't use them on my car and they were fine).
You will need 200-300mm, 0.5mm or 0.8mm spring steel to make a yarn tensioner for the hoop and toes.
For the yarn stand you will need a piece of 15 mm diameter aluminum pipe 500 mm long - a 15 mm wooden pin will work for the same job.
Ribber will be released very soon. I'm just working on some bugs :)
Happy knitting, if you have any problems please contact me!
Don't get hung up on "precise" parts, the whole idea of this machine was to keep the prohibitive cost down, so if you have something similar that you think fits the purpose, try this one :)
3D Print Settings
Larger parts are printed at a layer height of 0. 28 mm.
Finer details are printed at a layer height of 0.08 mm.
Large structural parts have 6 perimeters and %25 infill for strength
There are very few parts that require support. Parts larger than 200mm were split to fit on a 200mm x 200mm bed.
3D Printer File Information
- Project number : 666151
- 3D Design Format : PDF and ZIP Folder details close
- CSM.zip
- Cam Shell/Cam Shell Gear (3mm Screws).stl
- Cam Shell/CamMount Mirror.stl
- Cam Shell/CamMount.stl
- Cam Shell/CamShell v4.stl
- Cams/LH Cam v1.5.stl
- Cams/RH Cam v1.5.stl
- Counter/Counter Mount.
stl
- Counter/Lug.stl
- Counter/Screen Frame Rotate.stl
- Counter/Screen Frame.stl
- Counter/Sensor Mount.stl
- Crank/Coupler2.stl
- Crank/Crank Gear Flat.stl
- Crank/Crank Handle M5x25.stl
- Crank/Crank.stl
- Crank/Drill Jig.stl
- Cylinders/48 slot 1.4mm With Recess.stl
- Cylinders/52 slot 1.4mm With Recess.stl
- Cylinders/54 slot 1.4mm With Recess.stl
- Cylinders/60 slot 1.4mm With Recess.stl
- Cylinders/64 slot 1.4mm With Recess.stl
- Cylinders/72 slot 1.4mm With Recess.stl
- Cylinders/75mm Extension.
stl
- Cylinders/84 slot 1.3mm.stl
- Frame/New Front Plate Fixed.stl
- Frame/New LH Side.stl
- Frame/New RH Side.stl
- Frame/New Top Plate.stl
- Frame/Yarn STand Base.stl
- Special Requests/Cam shell spacer.stl
- Special Requests/Cylinder Tool.stl
- Special Requests/Extension Ring.stl
- Special Requests/Needle Gauge.stl
- Special Requests/New Top Plate Bars moved.stl
- Special Requests/New Top Plate test.stl
- Special Requests/Svitlana Top Plate.stl
- Tension Cam/TensionCam v2.stl
- Yarn Feed/AntiRotate LH.stl
- Yarn Feed/AntiRotate RH.
stl
- Yarn Feed/Cam Carrier Fixing.stl
- Yarn Feed/Yarn Carrier Top.stl
- Yarn Feed/Yarn Carrier Vertical.stl
- Yarn Feed/Yarn Carrier X Feed.stl
- Yarn Feed/Yarn Carrier Z Adjuster.stl
- Yarn Stand/Front Yarn Catch.stl
- Yarn Stand/LH Yarn Catch.stl
- Yarn Stand/RH Yarn Catch.stl
- Yarn Stand/Yarn Carrier Front.stl
- Yarn Stand/Yarn Carrier Rear.stl
- Yarn Stand/Yarn STand Base.stl
- Yarn Tensioner/Clamp.stl
- Yarn Tensioner/Movable plate.stl
- Yarn Tensioner/Pipe Dropper.stl
- Yarn Tensioner/Tensioner.stl
- Cam Shell.
pdf
- Counter.pdf
- Crank.pdf
- Cylinder.pdf
- Frame.pdf
- General.pdf
- Main Assembly.pdf
- Part Labels.zip
- threading.pdf
- Yarn Feed.pdf
- Yarn Stand and Tensioner.pdf
Learn more about formats
- CSM.zip
- Last update : 2023-03-12 08:57
- Publication date : 2022-03-16 12:45
License
CULTS - private use
Tags
Barrel filling adapter
€3. 39
Door numbers
1.13 €
Table bowling
1.13 €
Floor supports
1,70 €
Soap holder
0,57 €
Chalk mold
0.51 €
Best 3D Printer Files in the Fashion Category
Candy Cane Charm
Free
Viking shield boss
Free
Steampunk pen holder
1.41 €
MONEY CLIPS
Free
Teutonic knight's helmet with rounded horns
11.74 €
Roshe run
8,72 €
Secret design
VirtualTryOn.
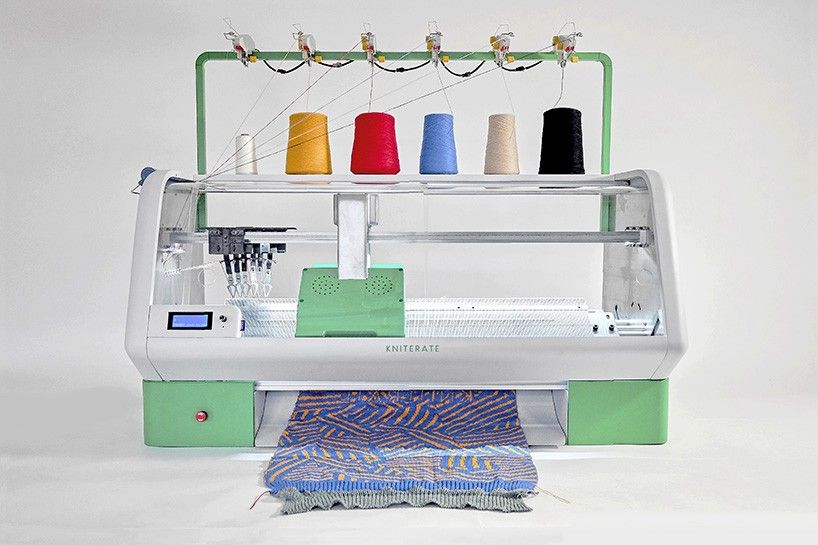
Free
Bestsellers in the Fashion category
Slim - smart wallet
2.18 €
CAP CURVED BAND
1,08 €
CIGARRERA
1,78 €
WHITE MASK OF OBITO, NARUTO
3,67 €
Kawaii cat super cute and funny [piggy bank box pot decorative character]
€2.99
Curved cap band
1.22 €
Articulated skull mask
7.51 €
BATCAT HELMET
3.81 €
Helmet Bomb Girl Reze - Chainsaw Man
15 €
42 IN 1 STORAGE CUBE FOR GAME CARTRIDGES AND MICROSD CARDS FOR NINTENDO SWITCH
€3. 49
Oakley glasses
4 €
Model Nike Air Force 1 Low
1 €
Yeezy foam runner v2 sneakers
5 €
Mary Poppins earrings
0,61 €
Printed Cuban Link Chain
€3.50
Spartan helmet
2.22 €
💖 Do you want to support Cults?
Do you like Cults and want to help us continue our journey on our own ? Please note that we are a small team of 3 people, so supporting us in maintaining activities and creating future developments is very easy. Here are 4 solutions available to everyone:
-
AD: Disable the AdBlock banner blocker and click on our banner ads.
-
AFFILIATION: Shop online with our affiliate links here Amazon.
-
DONATIONS: If you want, you can donate via Ko-Fi here 💜.
-
INVITE YOUR FRIENDS: Invite your friends, discover the platform and the great 3D files shared by the community!
3D printing in the fashion industry
In recent years, 3D printing has become more and more widespread. From medicine, aerospace, to engineering and construction, every day there is news about breakthroughs, innovations and developments in the additive manufacturing industry.
The use of traditional knitwear releases harmful substances used in this process, which mainly end up in sewage, which in turn leads to the pollution of rivers and oceans. Also, a lot of material is wasted. Finished products are sent to various subsidiaries around the world. Incredibly long transport routes, which greatly increase CO2 emissions, add to the shortcomings of traditionally produced clothing. The process of making 3D knitwear is very similar to other 3D objects. Both start on the computer: CAD software is used to create the design and ultimately the programming language. The digital codes are then transferred to the machine, which then starts the production process. However, the machine used is where knitwear and traditional 3D printing diverge. The main difference from additive manufacturing is that the machine is not a 3D printer that processes filament or powder through extruders, but rather a knitting machine that can produce 3D clothing in a single pass by joining it filament by filament. It should be noted that the principle is essentially the same, both based on software and additive manufacturing, but the material creates a big difference between the two methods.
Therefore, it is not surprising that industry experts agree that 3D knitting is not produced using 3D printing, but rather a separate technology. Gerard Rubio, co-founder and CEO of Kniterate, a company that sells 3D digital knitting machines, adds the following about his company's machines: “These machines are capable of 3D knitting. But these machines are not necessarily 3D knitting machines.” This is because flat, single-layer garments such as scarves can also be printed with a Kniterate machine, eliminating the aspect of additive manufacturing. Rosanna van der Meer adds that she deliberately uses the term "3D printed knitwear" for her products to make a clear distinction between 3D knitwear and traditional knitwear.
Since 3D knitwear is produced on demand, problems such as overstocking and shortages can be avoided. This goes hand in hand with Rosanne van der Meer's motto: "The starting point for a better climate balance in the fashion industry is less consumption." Thanks to 3D technology, it is also possible to personalize 3D knitwear. Since designs are created digitally and each stitch is the equivalent of a pixel, templates can be easily modified and adapted to customer requirements, allowing for greater freedom. A custom program from startup Shavatar also helped New Industrial Order improve the fit of their 3D knitwear without a 3D scanner — an important aspect when it comes to buying clothes.
Even if the thread breaks, the semi-finished knitted part can be recycled, because the knitwear is designed in such a way that it can be separated again. This means that the material used can be recovered – another sustainability factor. In terms of material, there are significant savings to be made when using 3D knitting as the machines produce additively in just one pass and therefore only require threads to be used, thus eliminating numerous manufacturing steps and saving a lot of time and cost.
In addition, most 3D printers cannot reproduce small enough details. Unlike 3D knitting, where moving filaments are processed by many small needles, 3D printer extruders cannot produce anything comparable.