3D printer aluminium extrusion
How To Build Anything Out Of Aluminum Extrusion And 3D Printed Brackets
The real power of 3D printing is in infinite customization of parts. This becomes especially powerful when you combine 3D printing with existing materials. I have been developing a few simple tricks to make generic fasteners and printed connectors a perfect match for aluminum extrusion, via a novel twist or two on top of techniques you may already know.
Work long enough with 3D printers, and our ideas inevitably grow beyond our print volume. Depending on the nature of the project, it may be possible to divide into pieces then glue them together. But usually a larger project also places higher structural demands ill-suited to plastic.
Those of us lucky enough to have nice workshops can turn to woodworking, welding, or metal machining for larger projects. Whether you have that option or not, aluminum extrusion beams provide the structure we need to go bigger and to do it quickly. And as an added bonus, 3D printing can make using aluminum extrusion easier and cheaper.
Everything is Built from Aluminum Extrusion
Aluminum extrusion beams are no stranger to these pages. We have a general overview of them and we have seen so many projects using extrusions, like satellite trackers, Rubik’s cube solvers, and automated drone charging stations. Many popular 3D printers have frames of aluminum extrusion as they offer higher strength and superior dimension tolerances than 3D printed plastic.
But creativity is quickly stifled by connector selection, as the vast majority of connectors in the catalog are for 90-degree joints of one flavor or another. Angled connectors are in the minority, and usually limited to a few angles like 30, 45, and 60 degrees. There isn’t enough sales volume to justify making connectors with angles that only a few people would ever use. This is where our 3D printer re-enters the picture, as a factory for low volume niche parts.
Custom Doesn’t Mean Hard
Combining custom with stock allows us to design projects leveraging the strengths of each part: the aluminum extrusion provides generic structure, with the 3D printed plastic linking them together in a project-specific way. We’ve covered 3D-printing right angle connectors before (or in conjunction with zip-ties) but today we’re focused on 3D printing’s advantage for very precisely building arbitrary angles.
The CAD to design for these connectors is pretty simple. It is typically a matter of subtracting out a rectangular solid for the beam itself, followed by subtracting a few cylinders to create mounting holes for fasteners. Bolting to an extrusion on three sides (like the rocker arm example here) is usually strong enough for 3D printed plastic projects. This means we can often skip the “top” (relative to print bed) side for easier printing. Sometimes we’ll want that strength badly enough to deal with bridging or some other technique to give us that fourth side, but we’ll leave that challenge aside for now. The point is, that you can give this a try with minimum effort and adopt more of the technique as you get used to it.
An Example: Hard Angles Made Easy
I’ve been working on a design for a rocker arm sub-assembly and it makes a perfect example of this discussion. It is part of the suspension system for a robot I’m building. The entire design is far too large to print as a single piece, so I divided the object into aluminum segments linked together by 3D printed parts. Here are the wireframe diagrams:
Look at the relative angles of these two extrusion segments — no extrusion vendor would stock connectors at these angles and if they did you still wouldn’t get a pair of bearings at its center and a mechanical linkage up top. Such project-specific details make this hub ideal for one-off 3D printing. As for the arms, we could spin up a 3D print job for two long rectangular blocks of plastic. But why? The only project-specific detail here is length, which can be cut far faster than an identical length of plastic can be printed, even if the cutting was done by a hand-held saw.
This article focuses on where the aluminum meets the plastic so I’m not going to go deep into the details on setting up your angle or removing the area for the extrusion. But it’s worth noting a few general 3D printing behaviors that strongly impact this construction technique. Select your layer orientation wisely — when printed parts are pushed beyond their limits, they generally fail by fracturing along layer boundaries. Use at least two fasteners along each axis, spaced approximately as far apart as beam width, to spread out workload. Using just one fastener turns that single point into a fulcrum multiplying forces on our printed parts, and we don’t want that.
One more point to consider is overhang when bolt holes do not align nicely with the print bed. We can help our printer bridge odd bolt head surfaces by creating a thin layer (2-3 print layer heights thick) covering the bolt hole which can be cleaned up with a drill after serving its purpose. These are easier to remove and consume less material than the typical solution of printing supports.
The Secret Sauce: A Replacement for T-slot insert, T-nut, T-whatever
Once we have a project-customized connector designed and printed, we proceed to assembly where we face the other hidden gotcha of aluminum extrusions: specialty fasteners. Called T-slot inserts, T-nuts, or some similar name, they are shaped specifically to fit in the slot of an aluminum extrusion beam. They are also extremely expensive. Not necessarily in an absolute sense, but certainly relative to commodity hex nuts of similar size. Our rocker arm example is designed for 15mm Misumi 3 Series extrusions. Misumi offers several specialty nuts for this extrusion, the least expensive “economy” model HNSQ3 costs $8.28 for a bag of 100. In contrast, our trusty hardware supplier McMaster-Carr offers generic M3 hex nuts at $0.88 for a bag of 100. (Catalog #90592A085)
Before we give in to the temptation of a 90% discount, let’s do a quick review of what we trade off by using generic nuts. The first and most obvious barrier is that a particular extrusion beam’s profile might not allow a generic nut to be used. Second, a generic nut will not engage slot interior surfaces to the same degree as a nut tailored to the extrusion profile. This usually means we can’t torque the bolt down as tightly before something slips. Third, higher end specialty nuts provide friction against the extrusion, either by its shape, size, or an additional thin metal spring that holds the nut in place. Nuts that stay at position instead of sliding around in the slot eases assembly, translating into less time wasted and lower frustration for the assembler. Such labor savings can outweigh a specialty fastener’s cost.
For this rocker arm example, the first concern does not apply as Misumi 3 Series is tolerant of generic M3 nuts. Item number two — reduced fastener torque limit — is acceptable as long as it is still sufficient for what we need on a 3D printed plastic project. And item three — assembly convenience — is something we can get back with some clever 3D printing.
We now apply 3D printing’s strength (a factory for low volume, task specific objects) to generic fasteners in aluminum extrusion beams. Our technique employs a small tool designed specifically for the job. For starters, this tool has a little hump to act as a spring that helps hold its position in the slot. Then, because the tool is designed alongside the part it will be used with, we can design it with trays to hold generic nuts spaced exactly at the distance we need. And as an extra icing on the cake, we add a little hook to the end. This hook — designed to be exposed when hub is in place on the arm — allow us to fine-tune our position without having to take things apart.
To fit within the narrow spaces left in the slot, the tool is printed as thin as possible: the width of our 3D printer’s nozzle. This also makes economical use of filament and it’s very fast to print, both attributes useful for a disposable item since this thin positioning tool can’t be removed once the bolts are tightened down. It is well worth the sacrifice, though, because it turns a frustrating exercise of aligning small fasteners into a trivially simple task.
Give this fastener method a try. I hope you find the technique useful and I look forward to seeing more projects that combine the strengths of 3D printing and aluminum extrusion beams into something that neither could do alone. If you are proud of your result, don’t be shy about letting us know via our tips line or maybe as an entry to our Hackday Prize. Happy building!
Aluminum extrusion|20x20mm | 3D printing experts
Overview Description Documentation Specifications Add-ons
The aluminum extrusions are easiest way to build a solid frame.
- Mostly packed in a separate package due to the size.
- Width x Height: 20x20mm
- Length: 100cm
Stock - NL: >500
€ 9. 91 excl VAT In stock
Dispatches same business day!
Product description
The aluminum extrusions are easiest way to build a solid frame. This 20x20 mm bar is cut to your specified length.
You can use the frame components, like corner connectors, connector plates, in their respective category to connect multiple extrusion bars together to build a frame.Using M5 or M3 t-slots its easy to assemble the different pieces together. This material is easily cut yourself, making it a versatile product to use.
If you order this product, you will get one piece of 100 cm, mostly packed in a separate package due to the size.
Documentation
Drawing
Specifications
sku | ALUEXT2020 |
---|---|
gtin | 8719345000690 |
Price breaks
1 - 4: | excl € 9.![]() |
5 - 9: | excl € 9.41 |
10 - 29: | excl € 9.17 |
30 - : | excl € 8.92 |
Need a larger quantity? Contact our Sales department. |
Explore valuable add-ons that correspond with the Aluminum extrusion - 20x20mm. The components and accessories will enhance performance and guarantee improved efficiency. Select a device or part that will make all the difference!
Wiring and cables
Extrusion end caps
10pcs - for 2020 Aluminum extrusions
These covers can be used for the 20x20 bars and will make your design look neatly and professional.
€ 4.50
Fastening and mounting
Slide nut M4 for 20x20 extrusions (20 pieces)
€ 4. 13
Machine Screw M4X8 Hex (50 pcs)
€ 2.15
Connections
Corner connector
20x20 frame small
Aluminum corner connector for 20x20 aluminum extrusion.
€ 2.47
T-connection plate
for aluminum 20x20 extrusions
This aluminum plate allows you to make a T-connection between 20x20 aluminum extrusion bars.
€ 5.95
L-connection plate
for aluminum 20x20 extrusions
This aluminum plate allows you to make a L-connection of 90° between 20x20 aluminum extrusion bars.
€ 5.95
I-connection plate
for aluminum 20x20 extrusions
Connection plate for lengthening 20x20 extrusions or make a T connection between 20x20 and 20x40 extrusions.
€ 3.22
X-connection plate
for aluminum 20x20 and 20x40 extrusions
Connection plate allows you to connect 20x40 extrusion on a 20x20 bar.
€ 3.22
Corner connector
20x40 frame large
Aluminum corner connector for 20x20 aluminum extrusion.
€ 3.51
Aluminum profile as a one-stop resource for assembling anything. Part 2 / Habr
In the last article, we talked about types of aluminum profiles, types of fasteners and other nuances. Now it's the turn to add another great tool to the profile - 3D printing. Truly, using an aluminum profile and plastic parts printed on a printer, you can assemble anything.
Those of us who are lucky enough to have our own workshops can use woodworking, welding or metalworking. But if there is no workshop or it is small, or it is impossible to use all these methods for some other reason, it is better to turn to 3D printing and aluminum profiles. nine0005
Everything can be built from a profile
In the last article, some projects where an aluminum profile was used were already given as an example. For example, here is this adjustable modular desktop made of chipboard and profile.
Using a 3D printer, you can create custom connections for an aluminum profile that differ from those found in most catalogs. As a rule, standard fasteners are designed to connect the profile at a right angle. Using printing, you can create connections of any shape. nine0003
With their help, you can fasten the profile at any angle - 30, 45 or 60 degrees - it's easy to make this. An example of a non-standard plastic connection is shown above.
Non-standard - does not mean difficult
This is true - we can combine purchased components (profile and part of fasteners) with self-made elements. At the same time, the aluminum profile provides the overall structure of the product, and the plastic ties the guides together, setting a certain shape and maintaining it.
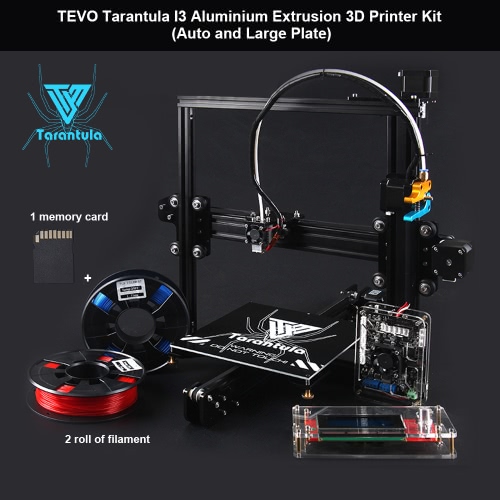
Fastening design is carried out in any CAD program. Typically, this is a task of machining a rectangular solid with several cylinders cut to create mounting holes. A 3D-printed connection with a three-sided profile is usually strong enough to provide the desired structural rigidity. You can start designing small, gradually improving skills.
Example: Difficult corners without problems
My project, an aluminum extrusion robot, is too complex to print as a single unit. Therefore, I divided the case into separate parts, connected together with fasteners printed on a 3D printer. nine0003
Look at the angles at which the profile elements are fixed. No fastener supplier will provide something like this, since the connection is non-standard. Moreover, the already customized plastic element is complicated by additional holes for bearings and some other elements. This is just a task for a 3D printer.
The purpose of the article is to show the possibilities of homemade connections, so for now we will not delve into complex topics. But still, it is worth noting the important features of 3D printing for us, which are important for creating complex structures. nine0003
Thus, the layer orientation and other parameters of plastic parts must be carefully selected, because if the calculated limit (bending load, etc.) is exceeded, the part will simply break, breaking along the layer. For each axle, it is worth using at least two fasteners spaced apart by a certain width to distribute the workload. The use of only one will lead to increased stress and possible structural failure.
Little trick: change t-nut, insert, whatever
After the individual connection for the project is ready, we are faced with another problem - the need to purchase specialized fasteners. In the last article they were discussed in detail.
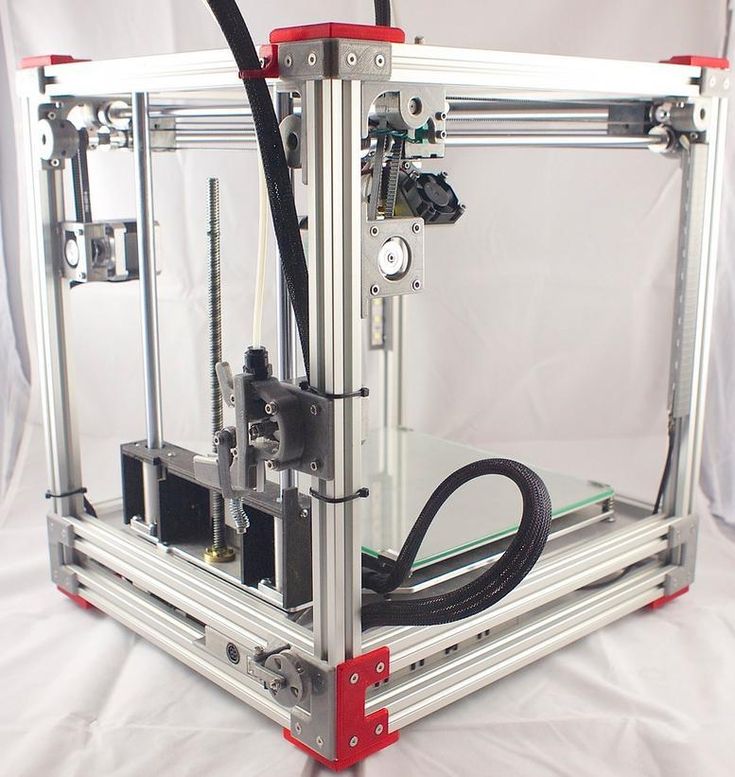
An alternative is to use regular nuts instead of T-nuts. Standard nuts are not compatible with all types of profiles, but only with Misumi 3 Series. Misumi also offers specialized nuts, which cost about 9dollars for 100 pieces. At the same time, regular M3s cost about $0.88 for 100 pieces. We will use them, solving a couple of problems along the way.
The first problem is that a regular nut, although it fits the groove in the Misumi profile, does not provide the same tight and high-quality adhesion to the profile as a specialized nut. Secondly, specialized fasteners are usually held in place by a spring, but if you use a regular nut, we do not get any springs. It turns out that it is better to pay for specialized fasteners so that there are no problems later? nine0003
No, because we have 3D printers. And they are able to print something that will solve both of the above problems. Plus, it will be convenient to collect ready-made elements. The picture below shows a plastic element that eliminates the problems. Firstly, this part has a small protrusion that acts like a specialized spring, securing the connection. Secondly, this plastic element fits around the nut, so that it holds no worse than a specialized one. And thirdly, there is also a specialized ledge (reposition hook), which makes it possible to change the position of the mount without disassembling the entire connection. nine0003
The thickness of the element corresponds to the width of the 3D printer nozzle, which allows you to easily place the plastic mount in the profile groove, save plastic and print quickly. It would be redundant to say that this element is one-time, it cannot be reused after parsing the connection.
Try this method of attaching the profile - perhaps it will come in handy and become the main one.
Accessories for 3d printers and CNC machines
St. Petersburg, Moskovsky pr., 91, office 605
Working hours
Login:
Password:
Forgot your password?
Remember me
Register
After registering on the site, you will be able to track the status of orders, personal account and other new features
8 800 550 77 89
8 905 270 87 77 nine0005 8 960 263 77 78
Login:
Password:
Forgot your password?
Remember me nine0003
Register
After registering on the site, you will be able to track the status of orders, personal account and other new features
Login:
Password:
Forgot your password?
Remember me nine0003
Register
After registering on the site, you will be able to track the status of orders, personal account and other new features
Opening a new warehouse!
Moscow, Silikatny pr-d, 34, building 1
More details
IMPORT SUBSTITUTION
aluminum profiles
In connection with recent events, we are doing a complete import substitution of aluminum profiles.
We develop profile constructs and tooling for profile manufacturing free of charge. We need a sample or profile drawing from you.
You pay only for ready-made profiles.
Production time 3-5 weeks.
Product catalog
Die making
for aluminum profile extrusion
More details
Promotions and discounts for regular customers
Quality services and service
Wide range of products
Fast and convenient delivery on time
Aluminum profile
Fastener
Accessories and fittings
Cylindrical guides and carriages
Rail guides and carriages
Structural profile
nine0004 Linear rail guidesFasteners
Ball Screws
nine0004 Trapezoidal screwsPhoto gallery
Photo gallery
Cutting Profile in the amount of
Powder painting
Monitoring for connectors
Structures
Drill
Cutting
Treak processing 9,0003 9000
08/16/2020
New Arrival!!! nine0003
03/04/2019
Low price guarantee
02/06/2019
New functionality added Our company is a recognized leader in the sale of structural machine aluminum profiles and components for CNC machines in the North-West region of the Russian Federation.