3D printer air filtration system
Nevermore Is What You Get When Engineers Design Air Filters For 3D Printers
- by: Donald Papp
What happens when an air filter for 3D printers gets designed by engineers with a passion for function, a refusal to compromise, and a desire to do without bad smells or fumes? You get the Nevermore, a design for a recirculating active-carbon filtration system to deal with VOCs (volatile organic compounds) from 3D printing.
3D-printable parts and an easy-to-fill chamber for bulk-activated carbon make this recirculating air filter for VOCs a smart, space-saving design.The Nevermore Micro (and larger Nevermore Max) were originally intended to complement the Voron 3D printer design, but are made such that they can be used with just about anything else. These filters use 3D-printable parts, and are designed to be easily filled (and refilled) using bulk-activated carbon instead of some kind of proprietary pre-packed filter like most commercial offerings. The Voron project is all about a printer without compromises, and the Nevermore comes from that same design ethos.
A Nevermore filter sits inside the build chamber, and works by recirculating air inside while passing it through the activated carbon. The idea is that by concentrating on dealing with the problem at the source inside a relatively small build chamber, one doesn’t need a lot of airflow. A small recirculating air filter can do the job efficiently, though for best results, the build chamber should be as sealed as possible.
One interesting caution is that it seems not all activated carbon is the same, and it is absolutely crucial to use only acid-free, steam-activated (not acid-washed) carbon in a recirculating filter like the Nevermore. There are horrifying photos of oxidized metal surfaces resulting from using acid-residue carbon, some of which took only minutes to occur. Thankfully, there are pointers to trusted sources for the known-good stuff.
It’s known that 3D printing results in chemical and particle emissions. These differ significantly depending on both material and type of printer, but it’s enough of an issue to warrant attention. One deals with particulates with something like a HEPA filter, but VOCs require a carbon filter. This is where the Nevermore comes in. Active carbon filters will wear out simply from exposure to the air, so if one is serious about cleaning VOCs when printing, it is definitely worth looking into bulk carbon with a design like the Nevermore.
Building an Air Filtration System for a 3D Printer
How I used a microcontroller, a fan, and a bunch of sensors to create a smart filtration system.
Posted on January 6, 2021 by Mike Buss
I was thinking of projects to work on, and I thought, gee, it would be nice if our 3D printer didn’t kill us.
I had researched the potential health side effects of owning a 3D printer when I bought it - it turns out they can malfunction and catch fire or release harmful chemicals into the air - but I made excuses. I’m only printing in Polyactic Acid (PLA), one of the least harmful filaments - it’s probably fine. Sure, maybe it releases some tiny plastic into the air, but it’s a big room, and sometimes I keep the windows open. Our smoke detectors are brand new and well tested. We’re probably fine.
Now that we welcomed Theodore, our now 3-month-old, into the world, I wanted to be on the safe side. So, I set out to build an air filtration system and some other safety features.
The Start of an Idea
As with most of my hobby projects, it started out simple. I thought of strapping a fan to a HEPA filter and maybe adding a carbon filter for extra protection. Then I thought: wouldn’t it be cool if it turned on and off automatically when a print started? Surely that wouldn’t be too difficult to build.
And wouldn’t it be even better if the system could tell when the volatile organic compounds (VOC) levels were high and adjust the fan speed accordingly? Since the goal is to make this box less likely to kill everyone in our sleep, why not add a fire sensor and an electric cutoff?
The fan I started with: a 140mm NZXT fan for PC's.Eventually, I landed on building a totally ridiculous, completely overkill air filtration system for our 3D printer that probably wasn’t necessary in the first place. And it was lots of fun.
Here’s how I did it.
Sketching It Out
I’m a firm believer in “measure twice, cut once”, so I started with a sketch of the system. I measured my 3D printer - an Ultimaker S3 - and jotted down a plan for the top enclosure. Then, I sketched out what components I wanted to use and how they’d connect.
Next, I printed the parts I needed to assemble the box and the filtration panel. Isn’t it cool how a printer can print things to augment itself? Next step: Skynet.
Everything except the electronics and Lexan was printed.Building the Partial Enclosure
I bought some Lexan from Home Depot, scored the sheets with a box cutter, and snapped them off using the edge of my workbench. It worked surprisingly well.
If you plan to do this at home, wear protective gear, including glasses.
I used Lexan because it was readily available at the local Home Depot.After cutting the Lexan, I connected all the pieces with 3D-printed parts. Special thanks to Hans Peter for building something similar and releasing the designs on Thingiverse.
The connecting parts were 3D printed. The final Lexan enclosure.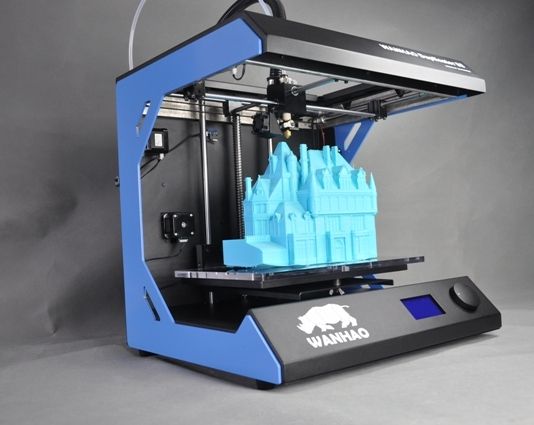
Now that I had the shell, it was time for the guts: the electronics.
Wiring Everything Up
The first rule of wiring electronics is don’t accidentally put 12V into a pin that expects 5V. You’ll get lots of smoke and heat and generally feel bad. After you’ve learned that rule, continue reading.
No electronics project would be complete without a prototype that looks like a rat's nest (top right). I cleaned this up later!I managed to assemble a gaggle of electronics that all needed power. Some needed 12V to work. Others needed 3.3V. Some were controlled with pulse width modulation, others with I2C. Getting them powered and conducting a symphony of functions was, in my opinion, the best part of this project.
I started with a 12V 3A power supply. This, wired into my Arduino Nano 33 IoT, a relay, and (via the relay) the fan, gave life to the essential components. I could now turn the fan on and off through the Arduino, but only at full speed.
To control the fan’s speed, I connected its PWM pin to a PWM pin on the Arduino. It took some math to change the Arduino’s built-in PWM frequency to 25 kHz, but the slower fan speed significantly reduced noise.
Now that the Arduino could control the fan, I wanted to have it start and stop automatically. To do this, I used the built-in WiFi module poll the Ultimaker S3’s API periodically.
The Ultimaker S3 comes with an excellent API.Then, because everyone loves data, I added some logging to my creation. I equipped the inside and outside of the chamber with sensors that measure temperature, humidity, and VOC levels. This data is sent over WiFi to a server running on my NAS (a Synology DS918+). Eventually, I’d like to use this data in real-time to control the fan speed, but for now, it’s just filed away along with information on what was printed and when.
Adding two temperature sensors was a little tricky, considering they share the same hardcoded I2C address. Because of this, the Arduino can’t address them individually. My solution was to use an I2C multiplexer to let me switch between sensors and query them individually.
While all of this is happening, the Arduino is also checking a flame sensor that hovers over the printer. If this sensor detects a fire, the power to the Ultimaker is immediately shut off, and a piezo alarm starts blaring. It’s not as cool as those automatic fire suppression kits you can buy, but the alarm can be heard throughout the house.
The flame sensor (left) will report if it detects a fire in the print chamber. This photo was taken when I was still breadboarding the prototype.Filtration
The fan pulls air out of the chamber, through a HEPA filter and a carbon filter, and then out the back. You can find all the parts I used here.
Future Improvements
The fan I have probably isn’t pushing as much air as I’d like through the two filters. I’d like to upgrade it to something better in the future.
All said and done, this project was fun to build and gives my wife and me some peace of mind. If you’ve created something similar, I would love to hear about it!
Share:
Welcoming Our First
Today, my wife and I welcomed Theodore Frederick Buss into the world!
Fixing the Worst USB Hub in the World
Hewlett Packard makes the world's worst USB hub. No, really. It's truly awful.
Mike Buss is a software engineer from Ohio who works primarily in the healthcare space. His work has been featured on Apple.com and helped hundreds of thousands of patients. In his spare time, he writes about software development and more.
Follow @michaeltbuss on Twitter as he continues to document his software development journey.
Air pollution in 3D printing
Main page
Articles
Smoke from a 3D printer
Smoke from a 3D printer
Introduction How does a printer pollute the air How does a BOFA filter
What is 3D printing
3D printing is also known as additive manufacturing. This means that the product is created by adding material in layers. The process is controlled by a coordinate XYZ robot with digital control. Printers work with plastic or metal. The material is fed to the deposition point in the form of wire or powder. The printer is melting the material. Then it connects to the previously applied base. nine0003
A 3D printer will produce objects of complex shape. This favorably distinguishes the additive process from the subtractive one, when excess is removed from a large piece of material. Machining, laser processing, soldering or welding generate more contamination. And a lot of material is wasted. 3D printing does not consume a lot of extra material. It appears to be a clean process, but it still pollutes the air.
Anyone using 3D printing needs to be aware of the health risks. The 3D printer seems safe. But it can generate toxic fumes and hazardous substance particles. Technological processes that transform the material pollute the air in the workplace. This applies to cutting, engraving, thermal decomposition in a laser machine, soldering with a toxic flux, etc. Molten metals and polymers are no exception. nine0003
Why is a 3D printer dangerous?
Ultrafine particles
Heating a substance causes the release of solid particles, droplets and vapors. They may be harmful if inhaled.
European scientists are gradually revealing the dangers of 3D printing to health. According to the 3D Printer Emissions Report , plastic melting releases small nanoparticles of material into the air. They cannot be seen without special equipment. But that doesn't mean they are safe. nine0003
PLA plastic nanoparticles are used in pharmaceuticals as a means of delivering drugs to various organs, including the brain. Cosmetics use the same effect. Ultrafine particles penetrate the skin. By themselves, PLA particles are not toxic. But no one knows about the consequences of accumulation in human organs. Nanoparticles condense into relatively large formations. It is known for certain about the harmfulness of soot nanoparticles from automobile exhausts . They are associated with degenerative brain diseases, such as Alzheimer's disease. nine0003
ABS plastic is toxic when melted. Nanoscopic ABS particles are just as toxic. These particles are very small. During inhalation, they enter the brain through the olfactory nerve. They spread throughout the body through the bloodstream. Most organs can get rid of them naturally, but the brain and lungs become clogged for a long time.
In fact, particles as small as 10-200nm easily enter the bloodstream through the lungs. Their toxic action differs from the original substance in the usual shapes and sizes. According to study by the Italian Institute of Health and Consumer Protection nanoparticles are deposited in the lungs in greater quantities than e-cigarette smoke.
Gases or vapors
Molten ABS gives off a particularly unpleasant odor. Other plastics including nylon, HIPS and HDPE emit the same toxic fumes but have less odor.
Polymer materials can vaporize some of their constituents. Dioctyl phthalate is often added to them for flexibility and mold resistance. During high heat or laser treatment, benzene is released in hazardous quantities. And while working with PVC, HCl aerosol condenses in the air. nine0003
The high temperature in the area of the printer head causes the air to expand. Vapors quickly spread in the work area along with plastic particles. Thermal degradation products of polymers are shown in the diagram below.
How does BOFA work?
A smoke extractor is an extractor hood with filters placed in one device. She got her name at the time when she removed the smoke of a soldering iron or a laser engraver. But these same devices with special filters are also suitable for a three-dimensional printer. The smoke extractor block for the printer is not much different from the soldering block. nine0003
3D printing is sensitive to changes in air temperature. Therefore, he is afraid of drafts. If you are using a small open printer, then the polluted air can be removed with a conventional smoke extractor. In order not to disturb the climate in the printer, select the minimum air suction speed.
If your 3D printer model is closed, there is a protective cover, then you can install a cleaning curtain. During operation, while the printer window is closed, it can be turned off. But it will clean the outgoing air when you open the box to take out the finished product. nine0003
If your printer is large and completely enclosed, then it will most likely have built-in pipes for connecting the hood. They can be connected to a smoke extractor with large filters. It can operate continuously or turn on at the command of the printer. The fume extractor captures dirty air and returns it back to the printer so as not to change the air temperature during the printing process.
3-stage filtration
A complete smoke extractor is equipped with three filters. The first is the pre-filter. It does not let in coarse dust, so as not to clog the main fine filter with it. The fine filter is HEPA. Particles of all sizes, including aerosols and nanoparticles, settle on its fibers. The gas filter completes the cleaning. It consists of densely packed activated carbon granules with interlayers of fiberglass. Activated carbon traps VOCs and nanoparticles that HEPA missed. nine0003
Smoke extractor against exhaust
The cheapest way to remove smoke is a duct fan and air ducts. The emission of polluted air through the window is prohibited by SanPin standards. And the smoke extractor has advantages.
- Good air purification from all kinds of solid particles and aerosols
- There will be no odors from melted plastic or metal in the room
- You will be sure that your health will not suffer
- The microclimate in the 3D printing machine will be stable
- Supply ventilation with heating or air conditioning is not needed, as for the extract through the window
Eliminate the harmful agent
The hood with filters will solve the problems with harmful emissions from 3D printing with polymers and metal powder. Without proper filtration, ultrafine particles cause skin and eye irritation. Nanoparticles accumulate in internal organs and lead to systemic disorders, heart and vascular diseases, and Alzheimer's disease. The smoke extractor is suitable for household and professional models of printers. Extractor hood with filter, recirculation and airflow adjustment minimally affects the air temperature inside the printer. BOFA will take care of you and the world we live in. nine0003
Smoke extractor catalog PDF
You can familiarize yourself with the models on our website in the section Smoke detectors for 3D printers
During business hours, a showroom or showroom is open in our office. Popular BOFA smoke extractors are on display here.
Watch our video
Visit our YouTube channel where you can get a closer look at the manual editing methods we offer: www.youtube.com/user/ARGUSXvideo nine0003
What air filtration options are available for enclosures?
Considering the emissions that 3d printing produces (ABS = styrene and other chemicals, PLA give some, etc.), what options are there for filtering the air in the case, other than blowing air out the window?
Learn more about chemical 3D printing:
- http://built-envi.
com/portfolio/ultrafine-particle-emissions-from-3d-printers/
Activated carbon filters seem to be a strong performer for ABS (styrene) and PLA (lactide):
- https://www.sentryair.com/activated-carbon-filter.htm
Are there better filter materials or processes for filtering air in an enclosure?
Here is an example filter setup:
- This is the fan mount: https://www.thingiverse.com/thing:780001
- 60mm fan and this filter: https://www.amazon.com/gp/product/B00XNI5SY4
- And a sandwich filter on a fan with this fan grill: https://www.thingiverse.com/thing:11906
▲ 11
My Residential Materials Expert referred me to these links (3D Printing Smoke Extraction Solutions, ABS 3D Printer Nanoparticles and Exhaust Chemical Filter) and thinks you are pretty much on board with the idea of using activated coal.
We both mainly print with ABS with the Replicator Dual and what has worked well for me (over the last 5 years) is keeping my printer near a window or vent in my office at home. A window is obviously a good ventilation option, but the variability it creates with ambient temperature has to do with my prints. I later moved my machine into its own cell, which if possible would greatly improve the overall environment for both the machine and any stored filament. nine0003
We'll keep digging, but hopefully this helps in the meantime.
, @ tbm0115
▲ 11
It depends on how often you use your printer, i.e. how many particles your printer emits per unit of time. If you print non-stop on 5 printers, then this is a completely different situation, the opposite of one print per week.
The best material for passive filtration is carbon foam. It has the ability to trap chemical vapors. See this filter comparison. Having a case with such a filter would be a good start. nine0003
For example, BuzzBox.
I have to say that I don't know the particle size of the 3d printed radiation and how good the filtering ability of the carbon foam is.
The step above is to tie such a housing together with an air purifier.
The best option would be laboratory equipment. But this is the most expensive one. It is designed to filter toxic fumes, vapours, gases and particles.
If you decide to build your own fence, watch Prusa's video on how to build a DIY version from an Ikea table. There is no filtration system, but it should be simple enough to integrate carbon foam with ventilation. nine0003
- video: https://www.youtube.com/watch?v=oS7ZtBNh3hE
- blog post: https://www.prusaprinters.org/cheap-simple-3d-printer-enclosure/
- 3d models: https://www.thingiverse.com/thing:2864118
Here is an article about DIY enclosures: https://all3dp.com/2/3d-printer-enclosure-5-cheap-diy-options/
. @ amra
▲ 5
I was very concerned about this issue when I bought my own 3d printer so I decided to develop a vapor removal solution for this. It is only designed for my Zortrax M200, but I hope this is a good example of how to solve this problem on a budget. nine0003
http://www.thingiverse.com/thing:1158639
. @ mrh
▲ 6
I've done this many times. Especially when I had a chemical engineer girlfriend with a PhD who kept talking about the fumes giving me cancer. To be honest, the system you want is just too expensive. Lab equipment can easily run for 20k, not to mention the noise. What you really want is a backyard barn, but as someone who lives where it snows, I understand that this is rarely a realistic option. nine0003
Buzzbox looks cool and there are other brands. However, their prices are usually the same as flashforge and usually they can't even hold flashforge. More importantly, there are parts where you can make your own. $300 for a Plexiglas enclosure that can only fit a mini printer is not enough today.
Take a product like this air scrubber or build your own like this laser cutter hard drive. nine0003
There should be a large laser cutter in the local hacker space. Plastic should be 100-200, depending on the thickness of the sheet you want. I personally buy scrap metal. Create a square box, add hinges, then seal the edges with silicone sealant. After printing is complete, remove the contents of the camera. Should also be used as a thermal camera.
As for me, I can easily run 5 printers at the same time. So I could take a metal cabinet, seal it up. check it with a fog machine. Cut a hole for the evacuation hose and connect the camera. But I don't have much free time. nine0003
Also, if I can make it airtight, that should reduce the risk of fire.
Take this laser smoke extractor for cutting. There is nothing that will work better than this. I heard that you might smell some smell, but that was for laser cutters.
, @ StarWind0
▲ 3
I designed this self-printing filter housing.