3D printed wheel truing stand
▷ wheel truing stand 3d models 【 STLFinder 】
DIY Wheel Truing Stand
grabcad
A 3D design for a DIY non welded Bicycle Wheel Truing Stand
Bike, Wheel, Truing Stand
thingiverse
Bike Wheel, Truing stand, Simple easy to use and build. Print both sides (symmetrical) slotted to move in and out side to side. This allows centering of the wheel to build in the proper offset. Truing gage and wheel concentric allow you to use...
bike wheel truing stand
thingiverse
This is a bike wheel truing stand that was made with 3d printed parts, a harbor freight dial indicator gauge, and 1" (1/16" wall) steel tubing, which should cost about 1$/foot. ... Parts total should come out to ~5$ or ~20$ counting the gauge.
bicycle wheel truing stand
grabcad
My concept of bicycle wheel truing stand. Horizontal and vertical legs are made from solid wood. Other materials are aluminum for dropouts and calipers and stainless steel for pivot bolts, nuts and washers. Adjusting knobs are plastic.Unlike Park...
Bicycle Wheel Truing Stand
thingiverse
This fully adjustable compact bicycle trueing stand will fit wheel axles from 100 mm to 157 mm and wheel sizes up to 29" (700C) with tires. The stand has an adjustable truing caliper with a friction fit swivel base It is assembled using 7 pre-cut. ..
Bicycle Wheel Truing Stand
thingiverse
These are the main components of a bicycle wheel truing stand. You will need some threaded rod, nuts, and uprights (either steel or wood posts) to complete the build. The total cost should be about $10, and assembly is easy. There are several...
WielRichter - Wheel Truing Stand
thingiverse
Printed parts: 1x Frame 4x Voet 2x Klem 2x Voeler 2x Knop All the things you need: 100cm 30x6mm flat bar 16 bolts m5 10 nuts m5 20 washers m5 12mm axle to put the wheel on Cut the 100cm bar is 2 pieces of 35cm and 2 pieces of 15cm Put everything. ..
Wheel hub bracket for wheel truing stand
thingiverse
Wheel hub bracket for wheel truing (truing stand with a diameter of 10 mm): - For a hub with 12 mm inner diameter - For a hub with 15 mm inner diameter
Wheel truing stand for big tires
thingiverse
Bike wheel truing head to be mounted however you like (I will add mounts in the future) the hole spacing on the back plate is 30mm x 4mm. Made for wide MTB rims and plus size tires and will probably work fine for the fatties and roadies too. you...
DTS-1 DIY wheel truing stand
thingiverse
# Github If you would like to make a change feel free to make a pull request https://github. com/Magum23/DTS-diy-wheel-truing-stand Material I printed the parts from PLA, seems to be fine. However if you want the parts to last a lot longer I would go...
Wheel Truing Stand
grabcad
Easy to build with profiles and other parts you can buy from Aluxprofiel.nl
Bicycle wheel truing stand
thingiverse
I haven't printed this myself yet because I don't have a big enough printer. I figured I would put it out in the world for someone else to try if they want. I designed it all to be put together with 5/16" socket cap screws. ...Should be able to tap...
wheel truing stand for bicycle/Stand centrare roti bicicleta
thingiverse
Then I was deciding to make one stand at home, but I did not find something which fits with components which I already have them from past projects on the Ethernet. Then I was deciding to design a stand for my needs. Part 1 and 2 need to be...
Spacers for DTS-1 DIY wheel truing stand
thingiverse
The original thingiverse stand is quite loose at the lower side, thus these spacers help to keep it stiff and sturdy
Zentrierständer für Fahrrad-Laufräder / bicycle wheel truing stand
thingiverse
Feel free to improve the Design: https://github.com/VirToReal/Centering-Stand-for-Bicycle/ Its fully customizable with the help of parameters in OpenSCAD. The Thingiverse-Customizer wont work here, because the "gears_helical. scad" must be in the same...
Wheel Truing Stand adapter for any MTB Hubs
thingiverse
I bought the most tipical wheel truing in Ebay/aliexpress (see the last picture) but when I used I discovered that it only was usefull for a small hubs so I needed to improve to adapt it to the normal bikes like mine with a 142x12mm rear hub or...
Bicycle wheel truing stand remix for fatbike rim
thingiverse
This is a remix of the great thing from @Hardy, thanks for the design. I needed to modify the original thing so that it could fit my 80mm fatbike rim.
...
Changes:
- enlarged the gears to 52.5mm and created rimgrabber_gear_d variable
- longer...
spoke wheel truing adapter on balancing stand
thingiverse
It's an add-on for my wheel-balancing stand with a frame of 60x30mm. You will need pair of M8 nuts and bolts to complete the thing, and some pointed stick or pen with a diameter between 6 to 9mm to point at the rim. Some photo of the completed...
Wheel truing
thingiverse
... Some threaded holes M3, M4, M5.
This will fit many kids of bicycles.
There is two files. The only difference is between them distance between M8 thread 50 mm
and 60 mm. I recommend file " wheel_truing_parts_bigger_hole distance.stl" for printing.
Truing Stand
grabcad
Truing stand is made for motorcycle wheel lacing and truing
Wheel truing frame adapter
thingiverse
Perfect if you dont own a truing stand or like me, want something small to bring on roadtrips to fix up your wheels after you cased that gap jump... They'll fit seat stays up to 20 mm wide or so, depends a bit on their shape. ...In addition you'll...
Bicycle Wheel Truing Jig
thingiverse
The bracket to moutn the wheel can be screwed in, or just can be glued in.
The marker holder is splitted in two to make it easily printable. Just glue the two pieces together.
The knob has a hole all the way though to tighen against the holder...
Bike wheel truing tool
prusaprinters
Wheel truing tool for bike mechanics designed for the needs of Gambian bike workshops, where getting a commercial jig is difficult. Can be used to trim the front or rear wheel. Print instructionsPrusament ASA, 0.3mm layer height, 100% infill. Print...
DIY Bike Truing Stand
thingiverse
Print these two things to convert any bike display stand into a truing stand. ...Minimalistic and saves space.
Handmade truing stand
grabcad
I want to build a truing stand based on this project
Xtreme truing stand adapter
thingiverse
An adapter for the Xtreme truing stand, it will help the rim to sit more firm to the stand and help you while truing the spokes. ... Instructions Print the adapter with a width of 30 mm, you need 2 of...
Bicycle Wheel Buckle Truing Gauge
thingiverse
Clamp the wheel horizontally in a bench vice (pictured). Clamp it by the nut, not the thread on the axle (obviously). Offer up the gauge to the rim. Coarse adjust the arms with the collars and fine adjust the arms with the two grub screws on each...
M5 wheel truing frame adaptor
thingiverse
Didn't have an M6 bolt handy so I sketched this to use as a wheel truing adaptor. It is very unrefined and far from perfect, but it does the job and it's tiny. ... I have around 4 sets of these with me when I go touring/camping.
bicycle wheel truing gauge clamp
thingiverse
This is to measure the warp in a bicycle wheel (rim) so you can tighten up the spokes and make it true again (don't forget to pay attention to roundness as well - make small adjustments working around the wheel until it looks good - the nipple is. ..
Thru-axle truing stand adapters
thingiverse
Adapters to make it easier to true thru-axle axles on a truing stand. I looked at the Park Tool TS-2TA product, & decided I could integrate the spring & spacer piece into one overly-complicated stacked wave spring. Based on overall dimensions from...
▷ truing a bike wheel 3d models 【 STLFinder 】
Bike wheel truing tool
prusaprinters
Wheel truing tool for bike mechanics designed for the needs of Gambian bike workshops, where getting a commercial jig is difficult. Can be used to trim the front or rear wheel. Print instructionsPrusament ASA, 0. 3mm layer height, 100% infill. Print...
Bike, Wheel, Truing Stand
thingiverse
Bike Wheel, Truing stand, Simple easy to use and build. Print both sides (symmetrical) slotted to move in and out side to side. This allows centering of the wheel to build in the proper offset. Truing gage and wheel concentric allow you to use...
bike wheel truing stand
thingiverse
This is a bike wheel truing stand that was made with 3d printed parts, a harbor freight dial indicator gauge, and 1" (1/16" wall) steel tubing, which should cost about 1$/foot. ... Parts total should come out to ~5$ or ~20$ counting the gauge.
Bike Wheel Truing Adapter
thingiverse
I really liked the idea of the source design, but needed to lengthen it to fit a carbon fork for my 2018 Specialized Roubaix Comp. It's a cheap, ugly print, but it worked really well. Print two of them so you have one for each side. ...I had to add...
BIke wheel truing holder
thingiverse
If we have a 3D printer, why not use 3D printed screw, and I found one somewhere.
If you want the screw and screwholder, put the comment below and I uploaded here (and sure I'll be searching for the source).
I used some double sided tape to. ..
Wheel truing
thingiverse
This is a simple truing tool to fix your wheels on the bike. M8 x 50 mm main screws. Some threaded holes M3, M4, M5. This will fit many kids of bicycles. There is two files. The only difference is between them distance between M8 thread 50 mm ...
TrueGirl – a bicycle wheel truing aid for dial gauges
thingiverse
Allows to use a dial guage for truing wheels that are still mounted on a bike. Needs threaded rods M6 and lots of nuts. ...Use a few wing nuts to make use easier.
Trispoke Wheel Build a Bike
thingiverse
This tri spoke wheel is a part of my Build a Bike series, designed to allow for easy, detailed customization using interchangeable parts. As a result this wheel should be fully compatible with all other parts in the series, please let me know if...
Rear wheel of a bike
grabcad
This rear wheel of the bike was designed as a part of the American Chopper Project from the learning site; Skill-lync. The original file isn't uploaded here due to copyright. ...Visit the link for the full American Chopper design...
DIY Bike Truing Bench
grabcad
My references were:About truing a wheel: https://www.youtube.com/watch?v=MFOng1UXn-gAbout building a wheel: https://www.youtube.com/watch?v=X5gs00ttvdgLastly, if you think you don't have time to build this setup or you wish you had some of the. ..
DIY Bike Truing Stand
thingiverse
Print these two things to convert any bike display stand into a truing stand. ...Minimalistic and saves space.
Bicycle Wheel Truing Jig
thingiverse
... The knob has a hole all the way though to tighen against the holder to prevent the wobbling that swolebro talked about in his video. Future possible upgrades: - Mount to use a dial indicator - openScad spacer generator - Smaller marker tip
Bicycle Wheel Truing Stand
thingiverse
These are the main components of a bicycle wheel truing stand. You will need some threaded rod, nuts, and uprights (either steel or wood posts) to complete the build. The total cost should be about $10, and assembly is easy.
There are several...
DIY Wheel Truing Stand
grabcad
A 3D design for a DIY non welded Bicycle Wheel Truing Stand
Wheel truing frame adapter
thingiverse
Perfect if you dont own a truing stand or like me, want something small to bring on roadtrips to fix up your wheels after you cased that gap jump... They'll fit seat stays up to 20 mm wide or so, depends a bit on their shape. ...In addition you'll need...
Bicycle Wheel Truing Stand
thingiverse
The stand has an adjustable truing caliper with a friction fit swivel base It is assembled using 7 pre-cut 2020 B-Type profile aluminum extrusions. The 3d printed fittings are fastened using M5 10 mm socket cap bolts, chosen for strength and ease of...
WielRichter - Wheel Truing Stand
thingiverse
Printed parts: 1x Frame 4x Voet 2x Klem 2x Voeler 2x Knop All the things you need: 100cm 30x6mm flat bar 16 bolts m5 10 nuts m5 20 washers m5 12mm axle to put the wheel on Cut the 100cm bar is 2 pieces of 35cm and 2 pieces of 15cm Put everything...
bicycle wheel truing stand
grabcad
My concept of bicycle wheel truing stand. Horizontal and vertical legs are made from solid wood. Other materials are aluminum for dropouts and calipers and stainless steel for pivot bolts, nuts and washers. Adjusting knobs are plastic.Unlike Park...
Bicycle wheel truing stand
thingiverse
I haven't printed this myself yet because I don't have a big enough printer. I figured I would put it out in the world for someone else to try if they want. I designed it all to be put together with 5/16" socket cap screws. ...Should be able to tap...
Carbon Disc Wheel Build a Bike
thingiverse
This Carbon Disc Wheel is a part of my Build a Bike series, designed to allow for easy, detailed customization using interchangeable parts. As a result this wheel should be fully compatible with all other parts in the series, please let me know if. ..
Portable Truing Caliper (For Bike Wheels)
thingiverse
I couldn't justify myself to be getting an expensive truing stand to straighten out my wheels so I thought to myself why not create something portable since I have a local 3d printer. So I created this and you hook it onto the seat stay of the back...
Bike Wheel
grabcad
A normal bike wheel
Bike Wheel
grabcad
A simple bike wheel
Bicycle Wheel Buckle Truing Gauge
thingiverse
Clamp the wheel horizontally in a bench vice (pictured). Clamp it by the nut, not the thread on the axle (obviously). Offer up the gauge to the rim. Coarse adjust the arms with the collars and fine adjust the arms with the two grub screws on each...
M5 wheel truing frame adaptor
thingiverse
Didn't have an M6 bolt handy so I sketched this to use as a wheel truing adaptor. It is very unrefined and far from perfect, but it does the job and it's tiny. ... I have around 4 sets of these with me when I go touring/camping.
bicycle wheel truing gauge clamp
thingiverse
This is to measure the warp in a bicycle wheel (rim) so you can tighten up the spokes and make it true again (don't forget to pay attention to roundness as well - make small adjustments working around the wheel until it looks good - the nipple is. ..
Bike wheel
grabcad
Bike wheel
bike wheel
grabcad
bike wheel
bike wheel
grabcad
bike wheel
bike wheel
grabcad
bike wheel
3D printed car wheel storage rack
Application
In this article, if you can call it that, there will be nothing special, just an experience of creating a compact wheel storage rack in the garage using 3D printed parts.

It all started when I needed a compact car wheel rack with the wheels along the wall. All options for ready-made racks or racks in stores or on the Internet were offered with the location of the wheels across the wall. But in the garage there is already little space, and I wanted a compact narrow rack. Ready-made fasteners were also offered separately for each wheel in the form of a bracket fixed directly to the wall. But I excluded this option, as it is not entirely reliable. Such a bracket may, for one reason or another, eventually fall out of the wall under the weight of the wheel. In general, I wanted to make a stand that would rest on the floor, and in which the wheels would be parallel to the wall. Therefore, I modeled the following welded structure:
Later I changed this design a little, but the essence remained the same. I welded it from a steel rectangular profile measuring 40x20x1.5 and 20x20x1.5. By the way, it is better to take a metal thickness of 2 mm, since it is much easier to cook. But I don’t see the point in writing in detail about welding, since the story is about 3D printing. In the future, it was necessary to come up with some large cylindrical parts that would be put on four metal pipes, and the wheels would be attached to these parts. It was at this moment that the idea to print these parts on a 3D printer matured. So I sat down in CAD and modeled the design in the right way.
The dark part is a flange that is put on the central steel pipe. The light detail - the sleeve, is put on the flange and is made of a softer material because it interacts with the wheel disk. Both parts have small holes perpendicular to the axis of the pipe. M5 screws are installed in them so that the sleeve and flange cannot rotate around the steel pipe or fall out of it. The flange has holes for M12 bolts and nuts. Fastening the wheel to the flange will occur in the same way as on the hub of the car. Only the fixing nuts will not be 5, but 3. And in fact, it will be possible to tighten only 1-2 nuts, so long as the wheel does not fall.
The details to be printed are directly shown below.
According to the materials at that time, I just had almost a whole coil of blue Petg, which was very rarely used, as well as black Petg. I printed flanges from Petg. There were also two SBS coils, which I used to use often, but over time I realized that this is not a very valuable material. However, for bushings for automobile wheels, it will be just right. In addition, SBS is a soft material, and therefore there is no possibility of any damage to the rim when installing it on the bracket.
The photo shows the printing process:
The parts turned out to be quite large in size and with thick walls. But despite this, there was an idea that plastic could not withstand the load from the weight of the wheel. Yes, the weight there is simply distributed through the walls of the bushings onto the metal pipe. However, there were concerns about this. Although after testing the design, it turned out that everything was in order. The weight of each part shown in the photo below is approximately 230 g. The height of the layer is 0.25 mm. Nozzle 0.5 mm. It was printed in 4 perimeters with approximately 75-80% infill.
Details have not been coated or processed in any way. Although SBS is afraid of ultraviolet radiation, it will be in a closed garage 99% of the time, and the sun will not be able to influence it. Petg also does not require a protective coating.
Actually, here are the finished assemblies:
After printing, I installed them on a welded structure. The following photo shows what the rack looks like with one wheel mount installed. The steel pipes on which the printed bushings are mounted are made removable. Therefore, you can put at least one fastener, at least two, at least four. The rack itself stands securely on the floor and is bolted to the wall with dowel-nails.
And the next photo shows the finished structure with wheels. The stand is compact and durable.
Here's an easy way to use 3D printing to store wheels in your garage! Of course, this could have been done in a different and perhaps simpler way. But I have a 3D printer and a desire to print!)
Join my VK group: https://vk.com/alexmaker_3dprint
Even more interesting articles
3
Subscribe to the author
Subscribe
Don't want
Microtia is a congenital deformity in which the auricle is underdeveloped. The doctors of the hospital in Guiga...
Read more
3
Subscribe to the author
Subscribe
Don't want
(Photo: University of Basel, Christian Flierl)
Using additive manufacturing...
Read more
257
Subscribe to the author
Subscribe
Don't want
Hello dear community!
In this topic, I would like to deviate a bit from the 'home. ..
Read more
5 ways 3D printing is changing the automotive industry / Sudo Null IT News
You can't buy a fully 3D printed car at a car dealership yet, but additive technologies have been used in car design for many years. Every year, especially in recent years, 3D printing is taking an increasingly important place at all stages of production. This is evidenced by the rapid growth of 3D printing market share in automotive manufacturing, which is projected to reach $2.5 billion by 2023.
For example, luxury car companies including Bentley, Porsche, BMW and Ferrari are using 3D printing to create custom car interior parts. GM, Volvo, Ford are using 3D printing to produce tooling to save money, improve designs and reduce delivery times.
Source 3dprinting.com
3D printing is constantly emerging with new opportunities, it is becoming more accessible. If the first 3D printers cost about $20,000, now you can find 3D equipment for $100. Now companies can, with the help of additive technologies, produce the necessary components directly at their own enterprises and not depend on suppliers.
With new materials, 3D printers can print high-precision, functional end parts. Additive technologies facilitate the production of custom products and increase productivity.
But this is only the beginning of the journey. Here are five key ways 3D printing is driving innovation in the automotive industry, from car design to production. Plus one bonus.
1. Changing the prototyping process
It was with the manufacture of prototypes that the use of 3D printers in the automotive industry began. 3D printed prototypes took much less time than traditional methods required.
Using Raise3D 3D printers and ideaMaker software, Crazy Grandpa Garage was able to automate the process of creating custom car parts. Production costs have been reduced by 50%, design reliability has improved significantly, and lead time has been reduced by 83%. The parts now come out very well fitted to the car.
Source: facebook.com
Using 3D printing, car designers can quickly create prototypes of individual parts or assemblies, from an interior detail to a dashboard, or even full-size car models. Thanks to 3D prototyping, the initial idea quickly turns into a physical embodiment of the concept - a conceptual model. The concept can then be developed into full-featured, high-fidelity prototypes, and after several validation steps, mass production begins. For the automotive industry, getting through these steps quickly is vital, and the entire downtime of an automobile production line in just an hour is very costly for the company.
For example, the assembly plant of the American car manufacturer General Motors claims to have saved more than $300,000 by purchasing a 3D printer in 2016.
Ringbrothers designers and engineers are not dependent on third parties to implement laser stereolithography (SLA) in their facility. The cost is reduced, the development time is reduced. Source: formlabs.com
Hose for Eventuri BMW M4, Source: ultimaker.com
Traditional prototyping was time consuming and costly, in part because the product went through more iterations. With 3D printing, you can create high-quality prototypes in one day and at a much lower cost. More examples.
The Ford Fiesta ST with 3D printed parts, ext. SEMA 2016, ultimaker.com
For example, General Motors has partnered with Autodesk to produce low cost, lightweight automotive parts using 3D printers. Tools, fixtures and fittings can now be produced at a fraction of the cost, according to Autodesk. For example, a 3D printed tool used to align engine and transmission ID numbers costs less than $3 at General Motors. A traditionally produced instrument will cost $3,000. In addition, downtime due to faulty tools can be significantly reduced as new tools are produced in-house.
2.
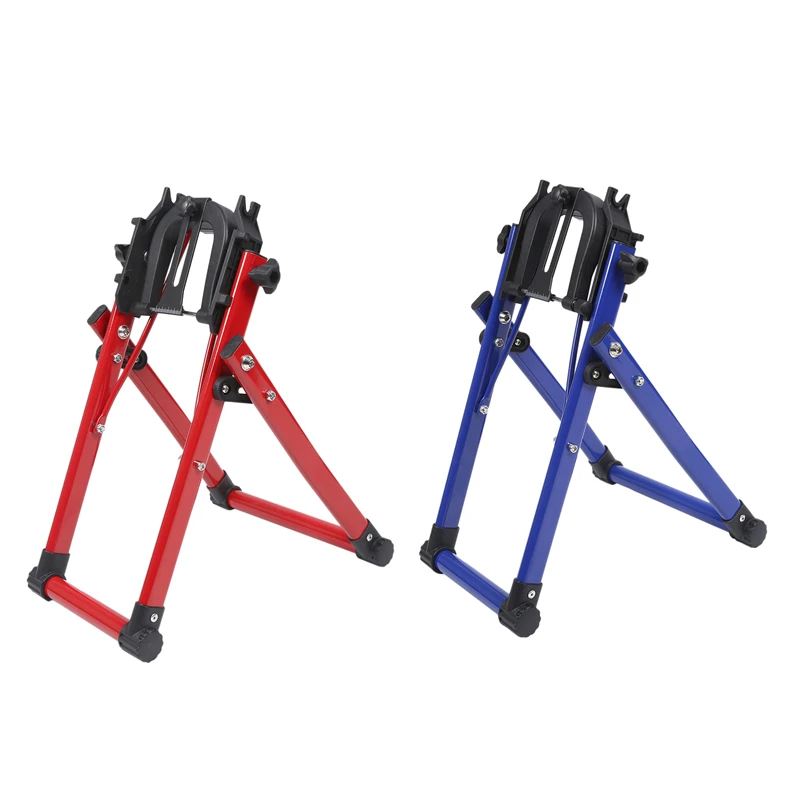
Daihatsu, Japan's oldest car manufacturer, launched a project in 2016 to customize its Copen model.
Source: 3dprint.com
In partnership with Stratasys, Daihatsu customers can design and order custom 3D printed panels for their front and rear bumpers with a choice of over 15 basic patterns in 10 different colors.
Source: 3dprint.com
In Europe, the BMW MINI brand also uses 3D printing to create personalized car parts. Since the beginning of 2018, MINI customers have been able to personalize various trim elements such as the instrument panel, LED treadplates and illuminated bumpers, as well as choose from different colors and textures. These parts are then 3D printed using a range of technologies from DLS Carbon to SLS.
Source: formlabs.com
Volkswagen Motorsport's I.D. R Pikes Peak is designed with over 2000 3D printed test parts.
Source amfg.ai
The use of 3D printers makes it possible to experiment in the development of non-standard designs, reduces the cost of their production. Long production processes for custom-made products are becoming much shorter.
Ringbrothers uses 3D printing to create customized end pieces, such as ventilation grilles. Source: formlabs.com
Large companies are merging 3D printing technologies with traditional manufacturing methods. Volkswagen has recreated its iconic 1962 Microbus by replacing the petrol engine with a 120 hp electric one. The Type 20 concept electric minivan has received many improvements using 3D printed parts. These improvements include cast aluminum wheels. Even the wheel hubcaps, while looking like stamped steel, are actually printed on a Formlabs SLA 3D printer, then electroplated and polished. 9another example Bentley has used cutting-edge metal 3D printer technology to produce a grille, side vents, door handles and exhaust pipes much more complex than those used on current production models.
Bentley has used metal 3D printing to create intricate micron precision parts. Source: formlabs.com
Source: youtube.com
3D printing has also made it possible to create parts that could not be made in any other way.
Bugatti's monobloc brake caliper is a prime example. For some components, Bugatti would have preferred titanium due to its high performance, but processing this metal with traditional methods is expensive and difficult. 3D printing has allowed Bugatti to produce a titanium alloy brake caliper. Due to the thin walls, the caliper turned out to be very light - almost two times lighter than forged aluminum. At the same time, the strength of the 3D-printed monoblock is superior to that of aluminum. The 3D printed titanium monoblock has a tensile strength of 1250 N/mm2. This means that a force of just over 125 kg will be applied per square millimeter of this titanium alloy without tearing the material. The new titanium caliper is 41 cm long, 21 cm wide and 13.6 cm high and weighs only 2.9kg compared to currently used aluminum, which weighs 4.9 kg.
Source: youtube.com. Source: formlabs.com
3. Tool making
Various devices help to facilitate and speed up the production and assembly processes, improve the safety of workers. Automotive factories and component suppliers use a large number of non-standard tooling that is specifically designed and optimized for end use. As a result, a lot of non-standard equipment and tools are made, which increases production costs.
This 3D protective wheel disc was purchased for 800 euros but can now be printed for just 21 euros. Tool development time has been reduced from 56 to 10 days.
Source: ultimaker.com
Delegating custom tooling and fixtures to service providers who machine parts from solid metal or plastic stock can delay production by weeks.
For example, the development and prototype of a commutator motor using traditional manufacturing methods can take up to four months and cost about half a million dollars. Thanks to 3D printing, Ford was able to develop several variants in just 4 days and 99.4% cheaper - only $3,000.
Source: youtube.com
Additive technologies allow you to complete the task in a few hours and significantly reduce costs compared to ordering from a third-party enterprise. Since increasing the complexity of a 3D printed model does not incur additional costs, products can be better optimized for their application. New elastic materials for 3D printing in many cases allow you to print plastic parts instead of metal or create prototypes on a 3D printer to test the tool before using it in production
Gradually, the production of 3D printed accessories and tools is becoming one of the largest applications of additive technologies.
Pankl Racing Systems uses 3D printed fixtures to fasten workpieces to a conveyor belt. Source: formlabs.com
For example, Pankl Racing Systems uses multiple Formlabs SLA 3D printers to make critical manufacturing tools. The multi-stage production of parts for transmissions on automatic lathes requires a series of fixtures and tools designed for each specific part.
With the help of 3D printing, Pankl's engineers have reduced the production time for the aids by 90%, from 2-3 weeks to around 20 hours. Costs were also reduced by 80-90%, saving $150,000.
The transition to 3D printing has enabled Volkswagen Autoeuropa to cut tooling development costs by 91% and tooling time by 95%.
4. Troubleshooting Parts
Spare parts have always been a problem for the automotive industry. The demand for them is either there or not, so the production of spare parts is not economically viable, and the storage of pre-fabricated replacement components is also costly. But if there are no repair parts available, difficulties arise and the main product becomes less valuable.
3D printing could solve the problem of parts in the automotive industry in many ways. The main factors are printed materials, which can match the characteristics of traditional materials used in parts and be cost-effective. There are prerequisites for this.
Using computer-aided design, drawings of all parts can be stored digitally, so there is no need to store the parts themselves. The parts needed by the client can be printed on a 3D printer right in the workshop.
Even obsolete parts whose drawings have not survived can in principle be recreated by making a 3D scan of existing parts of this type and applying reverse engineering (reverse engineering). You can read more about this on our blog. Old projects can take on new life. There are many lovers of vintage cars, with the help of 3D printing it would be possible to create parts for them.
Ringbrother 3D printed the Cadillac emblem for a custom built old car. Source: formlabs.com
5.
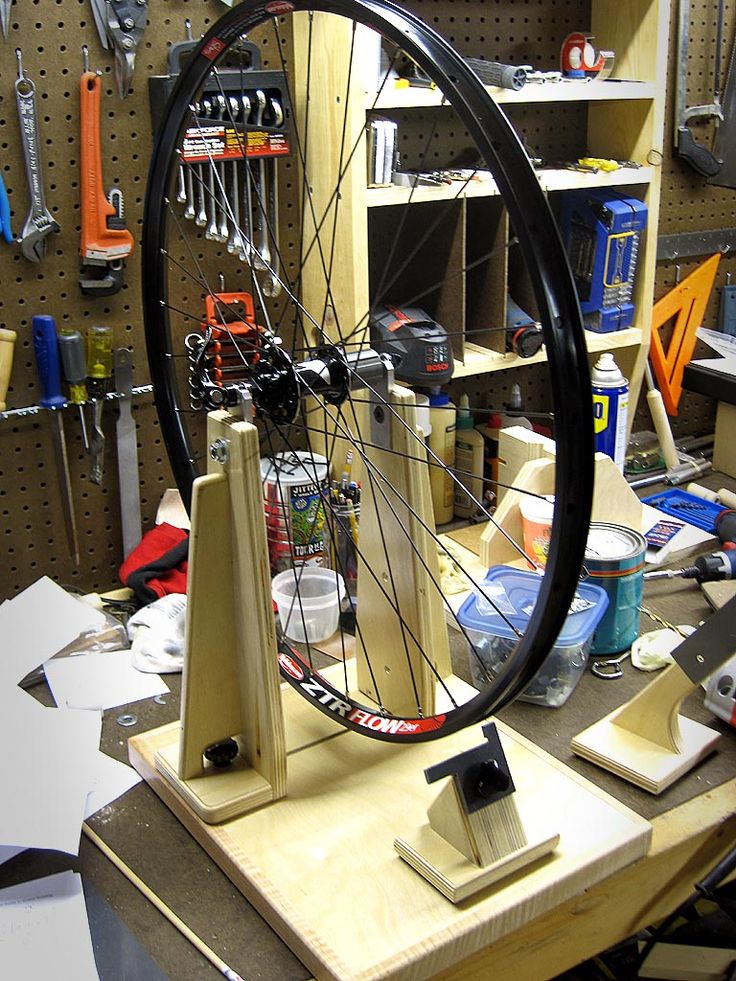
As 3D printers and materials for 3D printing become more affordable, a gradual transition to the production of mass-produced automotive parts using additive technologies is possible.
3D printing makes it possible to combine components into a single whole. Let's say there is a mechanism assembled from six or seven car parts that can be combined into one printed part. It will save time and assembly costs. With 3D printing, it is also possible to reduce the weight of the combined assembly, as a result, the car will use fuel more efficiently.
3D Systems has developed an advanced exhaust pipe for a sport bike. In the image below, you will see 20 sheet metal and hydroformed parts needed to assemble the original exhaust pipe. On the right is a monolithic exhaust pipe that does not require assembly, made using metal 3D printing.
Source designnews.com
The 3D printed tube was produced using Grade23 titanium in just 23 hours, compared to three weeks for traditional production. Design development time reduced from 6 weeks to 6 days. Additive manufacturing also eliminates the need for tooling, fixtures, multiple welding and multiple inspections.
Geometry optimization has reduced the amount of material required for maximum productivity. All elements of the original exhaust pipe are incorporated into the new design and, when printed with a typical wall thickness of 0.5mm, the 3D printed exhaust pipe is about 25% lighter than the original one.
A wide range of 3D printing materials is beginning to meet the requirements of various vehicle components. Since additive methods reduce costs compared to traditional methods (such as molding and injection molding), it makes a lot of sense from a production and financial point of view to further introduce 3D printing into the production of basic parts.
Volkswagen, one of the world's largest and most innovative car manufacturers, is using an HP Metal Jet 3D printer to produce high-performance functional parts with special design requirements, such as shift knobs and mirror mounts. Volkswagen's long-term plans to work with HP include accelerating the production of mass-customized parts such as key rings and exterior nameplates.
Source: youtube.com
+1. 3D printed cars
While 3D-printed cars have yet to hit the market, there are some interesting designs and concepts that can suggest a possible direction for the automotive industry.
Light Cocoon . German engineering firm EDAG was clearly inspired by nature to create the 3D printed supporting structure of the Light Cocoon concept car. The frame resembles the veins of a tree leaf or its branch. Despite the fact that the design of the EDAG took less material than a conventional frame, all the strength requirements for structurally significant components are met. Outside, the case is covered with a lightweight and durable waterproof fabric.
The cover protects the EDAG Light Cocoon from the weather and gives the car a unique personality. Source: formlabs.com
Blade . Blade ("Blade") announced as "the world's first 3D-printed supercar." It meets supercar standards but is made from inexpensive materials: carbon fiber tubes and aluminum rods, combined with 3D printed metal parts. Blade turned out to be very light and does not take long to assemble.
The world's first 3D printed Blade supercar. Source: formlabs.com
Strati . The American company Local Motors 3D printed and assembled the Strati electric car right at the exhibition stand, in just 44 hours. Most of the components were printed - the body, seats, interior parts. A car is made up of less than 50 assemblies, far fewer than the thousands of parts that go into a traditional car. The company intends to reduce the print time to 10 hours.
The Local Motors Strati has less than 50 individual parts*. Source: formlabs.com
LSEV. Developed by the Italian company XEV, the LSEV could be the first in the 3D printed electric vehicle market when it goes on sale.