3D printed loc line
▷ loc line 3d models 【 STLFinder 】
Loc-Line
grabcad
The comlete Loc-Line SystemCAD-files: http://www.loc-line.com
LOC_LINE COOLANT HOSE
grabcad
LOC_LINE COOLANT HOSE
LOC-LINE 1/4"
grabcad
LOC-LINE 1/4"
1" Loc-Line Segments
thingiverse
A few 1" segments of Loc-line I designed based off of another project. ...These are sized to nicely fit existing Loc-Line brand 1" segments pretty well.
Loc-Line spray nozzle
thingiverse
I just epoxied one of the loc-line joints in place to solve this problem. ...Print Settings Printer Brand: LulzBot Printer: ...
Loc Line Camera Mount
myminifactory
Hardware C270 Camera:https://www.amazon.com/dp/B004FHO5Y6/ref=cm_sw_em_r_mt_dp_U_wrVlCbWNh22KG Loc Line:https://www.amazon.com/dp/B006R9O3HE/ref=cm_sw_em_r_mt_dp_U_RuVlCb1PSKWQWCoupling Adapter to connect Loc Line to. ..
Threaded loc line 1"
thingiverse
Threaded loc line to use with Aquarium Flow the Original Random Turbulent Flow Generator and 1" pipe - use 1th_locline_big to connect with small connectors - use 1th_locline_small to connect with big connectors You can use with...
Loc Line Switch
thingiverse
This is much lighter than the jelly bean switch mount so much less sagging with the loc-line. ... Link for switch:...
Loc Line Switch
myminifactory
This is much lighter than the jelly bean switch mount so much less sagging with the loc-line. ... Link for...
Loc-line Assembly Helper
thingiverse
Loc-Line sells a wrench specifically for assembling them (https://www.amazon.com/gp/product/B006R9O3HE/ref=as_li_tl?ie=UTF8&camp=1789&creative=9325&creativeASIN=B006R9O3HE&linkCode=as2&tag=jeffsportfoli-20&linkId=559ab50045c58f1eb20c286ad1080ce3),...
Loc-Line Popper
thingiverse
I tried the official Loc-Line brand pliers, but unfortunately they did not work with my Chinese knock-off almost-but-not-really-Loc-Line hoses. Print Settings Printer Brand: Ultimaker . ..
Loc-line Mount
prusaprinters
So he needed a glare shield, which he wanted to build out of acrylic glass, but had no idea how to attach it. I had an articulated hose (Loc-Line Flexible Hose style) and now we only needed one piece to attach it to the projector. A few minutes in...
Loc-line Mount
thingiverse
I had an articulated hose (Loc-Line Flexible Hose style) and now we only needed one piece to attach it to the projector. A few minutes in Fusion 360 and we had drawn a part that he could screw on one side to the projector and pick up the arm on the...
Loc-line Mount
cults3d
I had an articulated hose (Loc-Line Flexible Hose style) and now we only needed one piece to attach it to the projector. A few minutes in Fusion 360 and we had drawn a part that he could screw on one side to the projector and pick up the arm on the...
Loc-Line Camera Accessory Mount
thingiverse
... to the Loc-Line as they have a tendency to split when being attached. It's also probably better to print these in ABS rather than PLA if possible, but the PLA ones do OK if you can get them to attach to the Loc-Line without breaking. ...
Loc line MFT 20mm mount
thingiverse
1/4” Loc line 20mm MFT mount - 20.0mm O.D. ...Base - 6.0 mm I.D through hole - I added a M6 x 40mm screw to the base for stiffness
CNC Loc-Line Vacuum Attachment
thingiverse
I designed and 3D printed this to fit on the outside of 2. 5" ID Loc-Line vacuum hose used to suction plastic chips away from the tool on an old Bridgeport CNC mill.
Loc-Line GoPro Camera Mount
thingiverse
... fits to the base to give it some more height without needing a bunch more Loc-Line. This additional extension is currently a little loose on the Loc-Line side, and I've just wrapped a bit of masking tape around it to get the fit that I wanted.
Loc-Line Circular Flow Adapter
thingiverse
This is an adapter designed to hold a 1/4" loc-line circle flow kit (http://www.loc-line.com/product/41479-14-circle-flow-nozzle-kit-1pc/) in a circle with all the jets focused on one point. The adapter was designed to slide onto a 2.2kw spindle for...
Loc-Line Echo Dot Bracket
thingiverse
The I drilled a hole in the clamp for a 1 1/2" long button head cap screw, which was then bolted to a single piece of loc-line with a washer just large enough to fit inside the ball and a nylon lock nut. I experimented a bit with the length of...
Pegboard Loc Line Ball Mount
thingiverse
The loc lines can be purchased on amazon for a little over $7 for 6. ...http://www.amazon.com/gp/product/B008O14864?psc=1&redirect=true&ref_=oh_aui_detailpage_o03_s00 You can actually unsnap and snap sections apart/together to make them different. ..
Samsung S7 Loc-Line Case
thingiverse
Downloaded a 1/4" locline link from here: https://grabcad.com/library/loc-line-1-4-1 By user jswerdlow Used fusion 360 to extrude and join the two models together to make a flexible mount for my phone when shooting live youtube videos.
X-Carve Loc-Line Holder
thingiverse
It connects to an NPT 1/4" pushfit connector on the other side. I sourced the Loc-Line bits from RS (house brand). Thread design taken from polyScrewThread library by aubenc (http://www.thingiverse.com/thing:8796). You can easily replace the thread...
Loc-Line Style Nozzle Aerator
prusaprinters
I'm a homebrewer and I needed to adapt a Loc-Line hose to a Siphon Spray Wort Aerator. So I fired up Fusion360 and combined the original Loc-Line nozzle with the aerator as best as I could. ...I printed this in Prusament PC Blend and wouldn't recommend...
Locking Loc-Line-like Links
thingiverse
Standard Loc-Line type links are a pain to print because tiny variations in the printing process can affect the gripping friction dramatically. These links feature an adjustable clamping screw (4-40 x 1/2"L) that lets you adjust them from...
Modular Hose Loc-Line style
thingiverse
Loc-Line style modular hosing is used in many ways but mainly it is configured to deliver coolant to CNC cutting tools during machining operations. This "thing" is a first stab at making a printable version for the non-wet variety of uses. Snap...
Locking Loc-Line-like Links
prusaprinters
Standard Loc-Line type links are a pain to print because tiny variations in the printing process can affect the gripping friction dramatically. These links feature an adjustable clamping screw (4-40 x 1/2"L) that lets you adjust them from...
X-Carve Loc-Line Holder
prusaprinters
It connects to an NPT 1/4" pushfit connector on the other side. I sourced the Loc-Line bits from RS (house brand). Thread design taken from polyScrewThread library by aubenc (<a. ..
1/2" Loc-Line Mount
thingiverse
This is a clamp for anchoring 1/2" Loc-Line to a machine tool for mounting lights, mist coolant, or anything else that needs flexible placement. You will need to print two parts for the complete clamp. This thing originally contained a FogBuster...
Modular Hoses (Loc-line like)
prusaprinters
DescriptionLoc-line hoses are industrial flexible hoses used in manufacturing machine to provide the coolant accurately on the part and the tool during operations.But those kind of hoses can also be used as very useful helping hands to hold parts,...
Vortex loc-line nozzles.
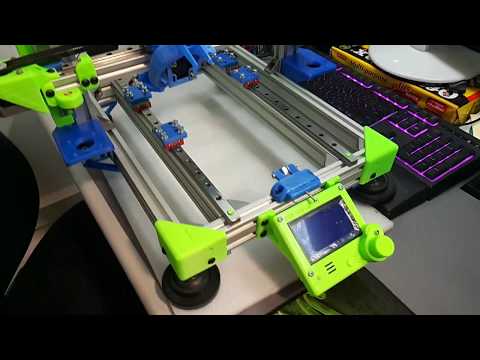
StevenD
Triggerfish
- #1
Have been playing around with our new 3D printer and designed a vortex nozzle to replace the default loc-line duckbills.
The vanes are pretty aggressive and pick up the water jet from the neck of the nozzle for a guaranteed spin. Personally I’ve noticed an increase in flow as I had to tweak the standpipe valves as the emergency trickle picked up the excess.
These are designed to simply clip on a standard loc-line with no other mods.
Here are some pics of the design.
The video below shows a test performed with some Coral Snow. Not really clear but on the far right is a standard duckbill which shows a straight stream, while the vortex is pretty clear at the centre.
Are these things worth it? Has anyone tested them before?
Last edited:
McPikie
Triggerfish
- #2
Interesting. I saw VividCreative making these, but they only had one UK stockist
endorium
Sea Turtle
- #3
It’s a good idea. What type plastic is it made of? I have seen some 3D printed stuff not last long in salt water. Depends on the plastic used though.
StevenD
Triggerfish
- #4
Top grade PETG which is reef safe
endorium
Sea Turtle
- #5
Cool if you can make them cheap enough you will sell thousands
mortie31
Triggerfish
- #6
I was looking at these as recently discussed on an American forum, worth trying if the price is ok, will you also be looking at standard pipe fittings?
StevenD
Triggerfish
- #7
mortie31 said:
I was looking at these as recently discussed on an American forum, worth trying if the price is ok, will you also be looking at standard pipe fittings?
Click to expand.
..
Nothing the 3D printer cannot take care of
I think the best option would be to have a PVC threaded fitting for the system to screw on, as PETG cannot be welded directly with PVC.
The other uses a Venturi as well in the video. The “more” flow they claim is actually the water they pick up from the tank from the Venturi effect.
[email protected] Parts
- #8
I’m also working on one of these. You will get even better results if you incorporate open inlets on the rear of the nozzle as per the ones linked above.
P
StevenD
Triggerfish
- #9
So you reckon the Venturi is required?
I’ll prototype one and see how it goes
Leeblades1889
Triggerfish
- #10
StevenD said:
So you reckon the Venturi is required?
I’ll prototype one and see how it goesClick to expand.
..
Hi Steve, I would be deffo interested in a couple of these as I currently have the double duck bill lock line on My Reefer 170
Lee
Sent from my iPhone using Tapatalk
5678
Angelfish
- #11
If these can be sold at a fair price then I'd be interested. I looked at the US ones but it was a lot of money for some cheap 3d printed parts!
StevenD
Triggerfish
- #12
Well, 3D printing isn’t that cheap as you might’ve thought. Don’t know what others are selling at, but 3D printing takes a lot of time to print each component and the top grade materials don’t come cheap either.
The parts I printed took about 90 minutes each and that’s at the fast setting
Also making moulds for these complicated parts would either cost a lot of money or might not even be possible to make moulds for such an intricate part.
maildcampbell83
Clownfish
- #13
The main problem I seen with these from vivid is how long they are,can they be designed shorter or is it the length that gives it the Randomness?
Sent from my iPhone using Tapatalk
StevenD
Triggerfish
- #14
Yes, for the Venturi some length is required. I’m working on the designs for the venturi version and it is a bit longer and wider.
I’m using a slightly different approach to maximise the venturi effect. If my approach is going to be innovative or not, I don’t know, I’m just following Bernoulli’s principle.
spaghetti reefer
Angelfish
- #15
Got these on my returns now fit filtration been selling them for a while now.
Work really well
davelee
Octopus
- #16
Have you tried it with less of a helix steven? Or just 2 not 3? Its close to being a simple injecton mould design, altho you could have the centre of the jig that rotates in it would add a touch but much better and faster than 3d printing
StevenD
Triggerfish
- #17
Could run a few prototypes and see how it goes I think the three flaps are the minimum you could use, depending on the size of the flaps. They are arranged every 120 degrees to complete the circle.
At the moment I’m working on a venturi design and seems to be coming out really well. I made the helix design a bit different. The inner side of the flaps start pretty aggressive and the angle steepens and pushes the flow towards the cone as it goes further out.
The outer brackets that hold the cone have an angle as well that follows the inner flaps so the flow from the venturi follows the same pattern.
I don’t know if this makes any sense but you’ll see the finished product soon
I think though that this design cannot be moulded as the flaps’s angle steepens as it goes further out
StevenD
Triggerfish
- #18
And here we go:
The non venturi on the left for comparison and the Venturi version on the right:
Size didn’t go overboard on the venturi version as you can see!
McPikie
Triggerfish
- #19
Out of interest, how much do you think you would knock these out for?
StevenD
Triggerfish
- #20
No idea and don’t know if I will yet.
Just prototyping now and need to see if these are eventually worth it.
These were made on the fast setting, need to see how they come out on a better resolution setting and how long it takes to make one with this setting as well.
Construction 3D printing is waiting for a breakthrough The first construction projects using this technology appeared only in 2014. We are talking, first of all, about the so-called small architectural forms (benches, flower beds, fences). They never even dreamed about building houses. But already in 2015, the Russian startup Apis Cor made a splash - it printed a whole house in the Moscow region. Since then, news about new 3D printed houses has periodically appeared. However, despite the fact that the technology proved to be very promising in terms of the speed of construction of housing and the reduction in the cost of construction, no mass implementation followed.
Construction is the world's number one market. And, if many technological innovations are being introduced in the field of high-rise construction, then little has changed in the field of low-rise construction over the past decades. The last 30 years have seen the availability of the internet, mobile phones, mobile internet, robotics have risen to new levels, etc., but when you get to a house construction site, you are unlikely to find many technological innovations. Automation is practically non-existent, and manual labor prevails. 2020 was a test of strength for the whole world, and also led to the highest level of inflation, which, first of all, hit the construction market, there was a dramatic change in prices for metals, cement, wood and much more.
This Internet meme shows what happened to the cost of building materials in just a year. And the process is still going on. At the same time, there is a serious rise in the cost of labor, and there is an acute shortage of it. All this leads to a sharp rise in the cost of building houses. No matter how strange it may sound, statistics show that the growth of automation does not occur when everything is fine, but precisely in crisis situations, during increased competition, reduced demand and the need to urgently look for new technologies to increase production efficiency. So it happened this time, and after some stagnation, construction 3D printing received a new impetus for development.
Preparing to write an article, I turned to the founder of Arkon - Boris Kozlov y. Arkon was established in 2020 and is engaged in the production of construction 3D printers, both a workshop type for creating prefabs (prefabricated houses) and a portal one capable of printing a two-story house. I asked Boris the key, in my opinion, question:
- Construction 3D printing appeared in 2014, but no mass introduction of this technology followed in 7-8 years. Why do you think this happened, and why is there a surge of new projects right now?
- It seems to me that the reason is the snowball effect. The technology had to mature, grow from a hypothesis to a pilot implementation, and finally to commercialization and scaling (what is happening now). In addition, it should be taken into account that construction is one of the most conservative industries, where, unlike even aviation and the automotive industry, there is still an extremely low introduction of digital solutions and automation in the field of the production process itself - the construction itself.
The issue of regulation and certification also plays an important role - this process is long and creates an additional lag.
In 2014-2016 the first samples of building 3D printers and prototypes of printed buildings appeared. The concepts of various form factors of construction 3D printers and types of printing materials were tested.
In 2017-2018 in the world, the first notable investments were made in a number of construction 3D printing start-ups. Further, by 2020, these investments "rolled" in the form of reaching a certain level of technology maturity - the first commercial products (3D printers and houses) appeared.
Finally, in 2020-2022 it became clear that the hypotheses of the effectiveness of construction 3D printing were justified (cheaper, faster, more environmentally friendly), and large investments began in the industry. A striking example is the investment of GE (the French division of General Electric) in the Danish COBOD or the achievement of a capitalization of $ 2 billion by the American company ICON.
![]()
In 2022-2023 over 1,000 buildings will be printed worldwide already, scaling from single buildings/pilot projects to entire villages and major infrastructure/reinforced concrete implementations. In addition, in a number of countries, by now, a regulatory framework has been created or is being actively created for the introduction of additive technologies in the construction industry.
Thus, I believe that the specified time period is a fairly natural cycle of technology development, which is likely to experience exponential growth in the next decade.
According to ResearchAndMarket report, the global construction 3D printing market is valued at USD 354.3 million in 2022 and is projected to reach USD 11068.1 million by 2027, growing by 99.04%.
Various market processes affect the prices and behavior of participants in the global 3D construction printing market. They create price signals that are the result of changes in the demand and supply curves for a product or service. They can be associated with both macroeconomic and microeconomic factors. Even human emotions can also drive decisions, influence the market, and create price signals.
Now let's take a quick look at what the construction 3D printer is. Without delving too deeply into the technology, we can say that construction 3D printers are very similar to classic FDM/FFF printers that print with plastic, but instead of plastic, the material here is a cement mixture, which is fed directly into the nozzle and forms an object by layer-by-layer overlay. Printers are also portal, on the basis of a flying boom, with a robotic arm.
Pictured left is a construction printer based on a boom. The figure on the right is a gantry construction 3D printer
In the figure above, a construction 3D printer in the form of a robot arm installed on a mobile platform.
Everything changed completely when, in the summer of 2021, the American company ICON, which was trying to introduce 3D printing into the construction of various auxiliary facilities, signed a contract with one of the largest American developers, Lennar, to build a village of 100 houses in Texas and immediately became a unicorn , having received 200 million dollars of investments from several investment funds.
At the same time, the Danish company COBOD, created by the world's largest construction formwork company PERRI, began selling its gantry 3D construction printers and participating in construction projects around the world. In the photo below, a modern two-story house built in Germany and a school building in Malawi, built in record time with a minimal budget.
Few things unite developed, developing and poor countries, everywhere their problems and tasks, but Affordable housing shortage is a global agenda . If in poor countries there is an acute problem with the increase in the number of homeless people due to a lack of housing, as such, then in developing countries it is necessary to dramatically accelerate the number of new housing being built to meet the needs of a growing population. In developed countries, the problem is primarily in the cost of housing, which has risen in price to such an extent that it has become practically inaccessible to young people. And with the simultaneous increase in life expectancy in these countries, this problem is only getting worse.
At the same time, the trend towards "green agenda " is developing, reducing CO2 emissions, building with more environmentally friendly materials, etc. But, unfortunately, so far the construction industry is the absolute leader in CO2 emissions, as well as in the amount of garbage that each construction site leaves behind. This is not to say that construction 3D printing solves all these problems, but at least it is moving in the right direction. Let's look at this with a few illustrative examples.
3D printed walls. Today, when we talk about 3D printing houses, we are talking about printing walls. Everything else (foundation, windows, doors, ceilings and roof) is done in the traditional way. 3D printed walls are built as fixed formwork, which significantly saves the amount of cement used , and this, in turn, reduces the cost of construction and reduces the environmental impact of cement production. In addition, with this method of construction, no additional waste is produced, the strength of the structure does not suffer. It can be reinforced, as shown in the photo on the left, and engineering communications can be immediately laid, as shown in the photo on the right, which also affects the final speed of the construction of the object. At the same time, the total weight of the structure is reduced, the remaining cavities can be filled with lightweight foam concrete, insulation, straw or any other available material. Such a lightweight design can use a lighter foundation. The construction method itself is more economical in terms of material, and therefore environmentally friendly.
Eco-concrete with the addition of polymers is being actively developed, the production of which reduces CO2 emissions from 30% to 100%. The Apis Cor company mentioned at the beginning of the article, which built a house in the suburbs in 2015, is now based in hot Florida, plans to start using this material in its projects.
Another startup from Russia, Mighty Buildings, headquartered in California, initially relied on a polymer with the addition of mineral chips. And while the company doesn't build entire homes, it only makes wall panels, it has won numerous design awards, as well as a $400 million valuation in several investment rounds.
As a result, with a rough calculation, we can say that the total savings on the construction of walls can reach 30%, and the total cost of the house can be reduced by 10%. This is true for houses designed for conventional construction. And if you initially design with 3D printing, you can improve this ratio by optimizing the laying of communications, the ability to immediately print interior walls, bookmark niches for bathrooms, fireplaces, built-in wardrobes and kitchens, as was done in the house built by COBOD in Germany.
"There are spots on the sun." Despite all the advantages of construction 3D printing, has several significant disadvantages of . The main one is layering, which cannot be avoided at the current level of technology development.
The photo above shows the layering of the 3D printed walls.
This task can be worked in several directions:
-
Ribbed walls can be plastered, painted and played with as a design element. That's how ICON does it in the US, for example their latest project House Zero is done that way and has won a number of design awards.
-
Use special "shutters" on the print head that allow smooth layers, as COBOD and other manufacturers do. The photo below shows that this does not ensure the complete absence of layering.
-
Fully sand the surface to get the usual smooth wall for plastering, painting, wallpapering or other finishing. It is possible, but it will require huge labor costs, which can reduce the overall efficiency of using 3D printing.
Pictured above is a 3D printed wall sanded smooth.
The second problem is the required temperature. Ideally, printing should take place at temperatures between +5C° and +30C°. Humidity is also important. Using additives, you can push these boundaries, but not indefinitely. At strong sub-zero temperatures, printing will be possible in the field only if the construction site is covered with a dome and the required temperature is reached inside with the help of heat guns. In conditions of intense heat, it is preferable to print at night. Another solution could be to print the wall panels in the shop and assemble them on site. Of course, each of these decisions will have a negative impact on the economic efficiency of the project.
Building 3D printing can be useful not only for the construction of houses . With its help, you can solve many other problems, and there its disadvantages will not matter. For example, the American concern GE uses COBOD printers to build towers for wind turbines in the shop. Ribbed surface and temperature restrictions in this case do not play any role. Construction takes place in the shop, after which the object is transported to the installation site.
Construction 3D printing, or, as it is also called, additive construction, has just appeared, and I want to believe in its bright future. There are many prerequisites for this, but a lot still needs to be done for success. First of all, it is necessary to develop principles for designing houses for building 3D printing. Then it is necessary to attract top architects to create landmark projects, which can be followed by the mass introduction of a new and very promising technology. Construction 3D printing could help solve the global housing shortage and bring more automation to other areas of construction.
Alexander Kornveits
Expert in the field of additive technologies and 3D printing, head of Tsvetnoy Mir company
3D printing of spare parts to replace imported parts
New year - new sanctions serious. The mass withdrawal of foreign companies from the Russian market threatens with an acute shortage of spare parts in a number of industries. But there is good news: many components can be replaced with 3D printed counterparts, and in this article we will share a few illustrative examples.
In fact, the replacement of parts with 3D printed analogues and spare parts has long been practiced by many enterprises around the world - somewhere in an experimental manner, and somewhere in a planned manner.
Siemens Mobility Russia
For example, in 2020, Siemens Mobility purchased two industrial FDM 3D printers for its Russian division to print spare parts for the Sapsan high-speed trains running between Moscow and St. Petersburg. The reason for this decision was not even a shortage of components, but the delivery time, the desire to simplify logistics and achieve 99 percent readiness of rolling stock.
“These numbers would be physically impossible to achieve by relying solely on external sourcing and traditional manufacturing methods, but 3D printers give us the ability to cost-effectively produce parts locally, thereby reducing the need to stock certain spare parts and tools. We have already seen the success of the Easy Sparovation Part program in Germany, where this technology has enabled Siemens Mobility to reduce time costs by up to 95% compared to traditional production methods. The delivery of an additional thirteen Velaro trains will require long-term maintenance of a large fleet with very tight time constraints. Accordingly, 3D printing is an ideal addition to production facilities, providing flexibility in terms of in-house production and replacement of parts at any time, as needed,” explained Alexey Fedoseev, director of service support for the Russian division of Siemens Mobile.
2050.Additive Technologies
The Russian company 2050.Additive Technologies, which is part of the 2050.DIGITAL group, has gone the same way. In 2019, this enterprise undertook the creation of an entire factory for the production of parts for service locomotive depots and transport engineering enterprises, with the support of two industry partners - Transmashholding JSC and the LocoTech group of companies. The enterprise's capacities include several dozen 3D printers, mainly printing with polymer filaments.
Especially for the needs of the new plant 2050. DIGITAL has prepared a database with hundreds of 3D models of various parts created by reverse engineering using 3D scanning: buttons, handles, holders, bushings, fasteners, cabin interior elements and so on. The company calls this approach “seamless contact”: suppliers in the regions can select the necessary spare parts in the catalog and issue a command for 3D printing, quickly receiving the required components.
Abigo Medical
Is it possible to replace metal parts with plastic parts? Yes, you can. This is where refractory engineering thermoplastics such as polyetheretherketone (PEEK) come to the rescue. Due to its strength and temperature characteristics, this polymer is capable of replacing aluminum alloys, and besides, it is non-toxic, which is important, for example, in the medical or pharmaceutical industry.
Our next example is the Swedish pharmaceutical company Abigo Medical, which needed to urgently replace worn rollers on a packaging line. It took at least two months to deliver parts. As a result, the management decided to order branded parts, but at the same time quickly produce 3D-printed counterparts so as not to lose money due to long downtime. The matter was complicated by the fact that the temperature on the broken line fluctuates between 85-87 ° C, so the material had to be not only durable and non-toxic, but also heat-resistant, and here PEEK showed itself in all its glory.
“We expected the 3D printed rollers to last a week or two. By the time the original parts arrived, they had been running for nine weeks. The quality control department ordered that the homemade rollers be replaced with factory ones, but at that time the 3D printed PEEK parts were still in order and cost ten times cheaper than the original ones, ”said Abigo Medical technologist Linus Göhle.
CLAAS
And this is an example from the Krasnodar Territory: a plant of the German machine-building company CLAAS, which produces agricultural machinery, operates here (or, at least, until recently). In 2020, the CLAAS design office took on the task of exploring the possibility of additive manufacturing of individual components and spare parts and immediately achieved interesting results.
One of the first prototypes was a 3D printed FDM-printed steering arm for the TERRA TRAC crawler chassis. The polymer 3D-printed part, with one hundred percent compliance with the original in terms of maximum load, came out six kilograms lighter, and this is nothing less than a 27 percent weight saving. The main point is that spare parts for old, no longer produced models, or rarely requested parts that are impractical to store in a warehouse, can be reproduced on a 3D printer, but they can be quickly printed - within a few hours.
Ford
Some companies generally prefer to rely on 3D printing not even spare parts, but original components. Of course, this doesn't always work. Additive manufacturing is mainly useful when it comes to the production of single or small-scale parts, and there are many such cases, for example, in the automotive industry.
Ford has operated a purpose-built advanced manufacturing technology center in Detroit since 2018, equipped with more than two dozen 3D printers in technologies ranging from FDM/FFF to Selective Metal Powder Laser Sintering (DMLS).
In the same year, the center supplied the first mass-produced 3D printed parts - F-150 Raptor truck components for the Chinese market and the Ford Shelby Mustang GT 500 sports car. Why did the company decide to resort to additive manufacturing instead of casting? Simply because both of these models were planned to be produced in limited quantities, and the deployment of a foundry for the production of several thousand plastic parts turned out to be unprofitable. It turned out that it is faster and cheaper to print the required components with photopolymer resins without spending money on expensive casting equipment.