3D printed electric skateboard parts
Thoughts on 3d printed esk8 parts - ESK8 Mechanics - Electric Skateboard Builders Forum
Sk8Board
#1
I made this thread for those who really want to get good electronics, but don’t want to spend a truckload on mechanical parts.
Sk8Board
#2
I am currently looking into @solidgeek’s motor mount and 3d printed pulleys on thingiverse. Motor mount @solidigeek : https://www.thingiverse.com/thing:2429445 Other Motor mount without steel rods: https://www.thingiverse.com/thing:2578901 40t Pulley for flywheels: https://www.thingiverse. com/thing:545345 20t pulley: https://www.thingiverse.com/thing:686273
CemraJC
#3
My opinion is that most 3D printed parts won’t cut it unless they’re for a minimal load/wear application. Plastic wont last long enough in this application. My general experience with 3D printing is that the parts just aren’t tough enough - for example, a 3D printed motor mount would tend to crack and loosen around the contact surface with the trucks and eny screws you put through it will lose their grip over time.
Of course, there are higher-quality-than-average prints that can probably handle it, but you end up paying more for them anyway, so why not invest a bit more to get some metal parts that will last much longer?
Note that this somewhat changes if you have your own printer and can be re-printing your parts every 6 months(?) or so. With your own printer, it’s so cheap that who cares if it wears out? Just make sure you have an appropriate maintenance window so you aren’t using parts that are going to fail on you while you’re actually on the board.
Sk8Board
#4
True, I agree that some parts you should get metal parts like the motor pulley and the motor mount, You can get a motor mount for 9 bucks from hobby king and a 20t aluminum pulley for like 5 bucks, but for the wheel pulley, I think you could get away with that for a while, but like you said, you want to have a 3d printer to print new parts.
Sk8Board
#5
personally, I think that you should only use 3d printed parts if you have your own 3d printer. If you don’t, just buy a metal one which will definitely last longer.
1 Like
florensvb
#6
Electric Skateboard Builders Forum | Learn How to Build your own E-board – 5 Oct 17First 3D Printed Wheel Pulley
Hey guys, I am looking to print my first 3D wheel pulley as i am currently interning at a company that allows me to use the printers. Question is: Whats the best kind of material I could be using that doesn’t melt or break? Cheers!
Reading time: 2 mins 🕑 Likes: 10 ❤
Crossfire
#7
I have as much as possible parts on my board 3D printed. They hold out pretty good, in case of design flaws I redesign them and then print a few more pieces. My entire battery enclosure is glass fiber enforced PLA. VESC enclosure was printed with more temperature resistant material than PLA - GreenTEC.
Speaking of motor mounts - CF reinforced PETG: thingiverse.com
ESK8 evo motor mount with cover by X_fire
Caliber II motor mount for 63XX motors and 265mm belts. Motor mount was printed with XT-CF20 and Aprinta PETG XT-CF20 and both work great. Caliber mount was printed with Extrudr GreenTEC which is flexible enough to hold on to the truck. Setup is...
Sk8Board
#8
NIce dude. I have a 3d printer too so replacement parts are easy
1 Like
PolyD, Parts of Electric Skateboard
Date: 02/12/2022
Posted by: caterina
Good morning Engineers and 3D printing enthusiasts!
As you have already read in the article on the presentation of polyDlab, and in the first episode where we told you about Valerio and his bladeless fan, PolyD-Lab is the MJF 3d printing technical lab. PolyD has created this lab to create, with your contribution, extreme and complex components and parts on projects submitted by our followers. The initiative is called 'polyDlab Contest'.
PolyDlab tests the limits of Multi Jet Fusion 3D printing and provides the technologies, skills and experience of PolyD's technicians.
The Contest
At polyDlab we print your prototypes and industrial and professional parts. If you would also like to participate in the online 3D printing contest of your project, send us your file to [email protected]
Our team of experts will select one every month. The piece will be 3d printed and sent to the designer free of charge. For each piece, we will make a video explaining its special features in detail, with the collaboration of the selected customer or follower.
In the PolyD lab we therefore print and analyse projects of parts, prototypes and components, based on 5 simple criteria:
- Resolution quality of the Stl file;
- Degree of optimisation of the 3D print;
- Aesthetics and Details;
- Printability;
- Usefulness of the part.
At the end of the video we give an overall grade to the project. Each month the ranking is updated, so you can find all the pieces rated episode by episode!
3D Printing of Scooter and Skateboard Parts
This month, the piece selected by our experts is that of Marco Sarracino; the main motivation behind the selection is ease of use.
Marco is passionate about 3D printing and electrical systems. For his skateboard, he needed a prototype gear that could sustain high performance even at high temperatures. Almost all the materials he tried had performance difficulties. For Marco, we moulded
a pulley in Nylon PA12 and the performance was fully comparable to 1 metal;
a plate to house the motor on the plastic plate. Here the mechanical stress is minimal, but temperature still plays a key role. The PolyD-moulded piece in Nylon PA12 fulfils the function perfectly.
As mentioned above, the parts are moulded in Nylon PA12, then sandblasted and finally coloured in UV-resistant black.
The evaluation team, having listened to the problems submitted by Marco and studied the design, decided on the following scores:
1. QUALITY OF THE STL FILE
The quality of the STL file received is undoubtedly very good and without burrs.
Rated 5/5
2. 3D PRINTING OPTIMISATION
Looking at the files, one does not get the impression that the parts were designed solely for 3D printing, but rather that they may appear to be designed for CNC machining. How can we tell? There are no obvious optimisations such as emptying some internal parts of the pulley to lighten the part. We suggest Marco use less material and consequently make the part more economical, while still guaranteeing the same mechanical characteristics.
Rated 2/5
3. AESTHETICS AND DETAILS
We have a real obsession with gears, pulleys and bearings; however, to be impartial, we admit that Marco's design has nothing we haven't seen before.
Rated 2/5
4.
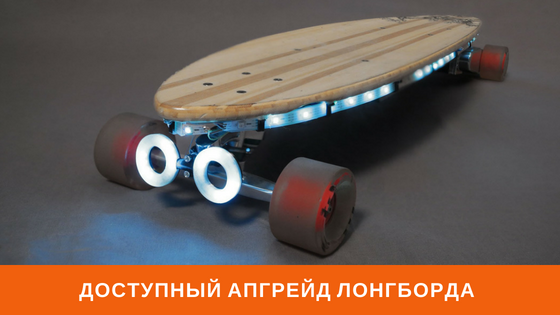
As for the quality of the STL file, there are no problems to report. The print as you can see came out very well indeed.
Rated 5/5
5. UTILITY
The parts are undoubtedly functional and useful; our follower Marco showed us this through his video. Marco went from using a very expensive steel part to using MJF 3D printing, which saved him time and money.
Rated 5/5
Conclusions
We summarise the grades awarded to the project:
- File quality 5/5
- 3D printing optimisation 2/5
- Aesthetics and details 2/5
- Printability 5/5
- Finally usefulness 5/5
The final grade, obtained by adding up all the scores and dividing them by the number of criteria, i.e. 5, is 3.8. The design of the skateboard gears takes second place in the ranking.
First place still remains firmly in the hands of Valerio's bladeless fan.
Thanks to Marco for participating in our MJF 3D Printing Workshop!
Follower Marco Sarracino
marcosarracino85@gmail. com
PolyD is the MJF 3d printing service. Rapid prototyping and professional and industrial 3d printing are our business: we print on different materials such as 3d nylon printing. You can find out more at the links Materials and Finishes.
Estimate your part now online and enjoy 3D printing!
Subscribe to Newsletter
So you can be always updated on our offers
E-mail:
I confirm i've read the Privacy Policy.
I agree to the use of my personal data for marketing finality, trough commercial communications, promotional and periodic newsletter, also automatizated trough my navigation history on the web
7 Real 3D Printed Vehicles
3D Printed Vehicles
Just a few years ago 3D printers had modest features and dimensions. But even now they can be used to print even the most complex and large-scale constructors, for example, cars and airplanes. And today we will talk about 7 real vehicles created using three-dimensional printers.
Cavity - 3D printed skateboard
Standard modern skateboards have a seven-layer wooden board as a base, to which the wheels are attached. The quality of this vehicle is highly dependent on the level of pressing and bonding of the layers. But students from the University of California, together with Cavity Boards, have developed a new technology for creating such boards. They started printing them with a 3D printer.
Cavity 3D printed skateboard
The Cavity board was the first sports equipment of its kind. It was printed using laser sintered nylon. The first tests of this board by professional skateboarders showed that it obeys them no worse than the most expensive boards from famous manufacturers.
Cavity - 3D printed skateboard
3DP-F1 - 3D printed bicycle
In April 2014, the Australian company Flying Machine 3D printed one of the world's first bicycles. The frame of the bike, called 3DP-F1, is made up of titanium tubes printed using the mentioned digital simulator.
3DP-F1 3D printed bike
The 3DP-F1 bike itself was designed according to the parameters of the director of Flying Machine. Thus, the manufacturer wanted to show that in the future, thanks to 3D printers, people will be able to receive vehicles that are ideal for each individual. At the same time, their cost will not differ much from serial products.
3DP-F1 - 3D printed bike
Energica Ego is the world's first 3D printed electric motorcycle
Energica Ego is the world's first 3D printed electric motorcycle. True, not all the details of this bike were printed in this way. Only fairings, headlights and some other structural elements were produced on the printer. Still, when it comes to high speeds, it is better to trust traditional rather than experimental technologies.
Energica Ego is the world's first 3D printed electric motorcycle
And the Energica Ego can reach 240 kilometers per hour. At the same time, the parts printed on the printer using innovative laser technology promise to be as strong as possible and resistant to changes in temperature and humidity.
Energica Ego - the world's first 3D printed electric motorcycle
Vagina Kayak - a 3D printed boat
Vagina Kayak is one of the most unusual vehicles in the world. This small sports boat is the author's project of the famous Japanese artist named Megumi Igarashi, made with the help of money raised on one of the crowdfunding sites.
Vagina Kayak - a 3D printed boat
This kayak is unusual in that it repeats the appearance of the above-mentioned artist's vagina with its shapes. For its production, she photographed her womb, made a three-dimensional model of the reproductive organ based on the picture, and then printed a boat with these unusual shapes on a 3D printer in a few days.
Vagina Kayak - 3D printed boat
With her project, Megumi Igarashi wanted to break the information blockade in Japan regarding the vagina. After all, the very mention of this female organ in the press and public discussion in the Land of the Rising Sun is considered unacceptable.
Urbee Hybrid - 3D printed car
And the world's first full-fledged car was 3D printed back in 2010, when the technology was just beginning to develop. So the appearance of a car with the name Urbee Hybrid was a real breakthrough in the field of 3D printing.
Urbee Hybrid - 3D Printed Car
The Urbee Hybrid is a small two-seater hybrid car whose body is almost entirely 3D printed. It has an electric motor and a traditional internal combustion engine. The maximum speed of the Urbee Hybrid is 112 kilometers per hour, while on electricity alone the car can travel 64 km.
Urbee Hybrid - a 3D printed car
Sulsa - the world's first 3D printed aircraft
. There are so far only small experimental drones. The first of these was the Sulsa aircraft, which appeared in the summer of 2011.
Sulsa is the world's first 3D printed aircraft
Only the body of the Sulsa was printed using the printer. The engine was installed separately. And, despite the fact that Sulsa is far from the size and functionality of real aircraft, this aircraft was the first “brainchild” of a 3D printer to take to the air on its own.
Sulsa is the world's first 3D printed aircraft
Sulsa's batteries last for 30 minutes at a maximum speed of 145 kilometers per hour. The wingspan of this aircraft is 2 meters.
The world's first 3D-printed rocket
NASA has been 3D-printing parts of rockets and space equipment for several years, but it's too early to talk about creating full-fledged vehicles in this way for flights to Earth's orbit.
The world's first 3D printed rocket
In any case, big rockets that can take a person or tons of payload into space. But a British team of scientists and engineers has 3D-printed a miniature spacecraft.
The world's first 3D printed rocket
This rocket is expected to be launched into orbit by the end of 2014. First, a balloon will lift it to a height of about 20 km, and then it will fly on its own, accelerating for some time to a speed of 1600 kilometers per hour.
Like
3D printing applications
Aerospace engineers use 3D printing to produce high quality products. Now the most popular printing methods are being actively introduced: stereolithography (SLA), deposition method (FDM), selective laser sintering (SLS) and printing with metals.
The technology enables the creation of topologically optimized structures with a high strength-to-weight ratio and the ability to combine multiple components into a single part.
Optisys is a supplier of micro antennas to the aerospace and defense industries. They used metal 3D printing to reduce the number of individual pieces of tracking antenna arrays from 100 to 1. With this, Optisys was able to reduce the lead time from 11 months to 2 months, while achieving a weight reduction of 95%.
There are also 3D printed parts in the systems that propel the aircraft. As a rule, these are metal products made by laser metal sintering. So, in the Boeing 777, the compressor is connected to the temperature sensor using a 3D-printed adapter. In the F-15K Slam Eagle military aircraft, 3D printing is used to make the casing of the turbines, reducing the cost of the part from $34,000 to $2,550 and cutting its production time in half.
Automotive
3D printing is taking over the automotive industry with its speed and ease of change.
Volkswagen has traditionally used CNC machining to create custom fixtures and tools. But using CNC machines usually means longer production times and higher costs. The same fixtures can be printed within hours and tested on the assembly line. The test results will be instantly taken into account and the engineers will make adjustments to the 3D model of fixtures the very next day.
Robotics
In the field of robotics and automation, non-standard parts are often required to develop new mechanisms. 3D printing has become one of the main manufacturing technologies in this industry due to its speed, great design freedom and ease of making adjustments to the product.
A team of engineering students from the University of Antwerp have created a robotic arm that can translate speech into sign language. They used 3D printing to produce most of the custom parts for their robot.
Industrial tools
The emergence of new materials with high heat resistance and rigidity in the 3D printing market, combined with the ability to quickly and inexpensively create custom geometries, has pushed manufacturers to widely use the technology to create industrial tools.
For example, today 3D printing is used to make injection molds for the production of short run products. These molds are used to make several hundred parts (compared to 10,000+ using metal molds), but they cost less than "traditional" molds and can be made in a day. This makes them ideal for low volume, low cost production or testing before full scale production.
Health
The use of 3D printing technology in global healthcare began in the 2000s. Since then, the use of 3D printing for medical purposes has evolved significantly.
The first area in which products printed on a 3D printer were involved was dentistry. Dental prostheses, for obvious reasons, are the easiest to replace with products made of plastic and similar materials. To date, there are examples of implantation of whole jaws made of titanium. The first such operation was carried out in 2012 by the private dental company LayerWise.
3D printing has proven to be extremely effective in creating prosthetic bones. In addition to high speed, modern technologies help to ensure the desired weight, and most importantly, the porosity of the product. The latter is extremely important for reducing the duration and improving the quality of osseointegration. There are many examples of successful pelvis, scapula, collarbone and other commonly operated bones performed around the world.
Product design
3D printing allows designers to easily make changes to the product they are developing at no additional cost. They can also create high quality functional prototypes to test new concepts. The use of 3D printing speeds up the design cycle and reduces risks before the product is introduced into full-scale, high-cost production.
Paul Kohlhaussen designed and built a functional prototype of his latest camera. He combined camera parts from different models under one printed body.
Entertainment
3D printing has found widespread use in cinematography due to its ability to create believable props. The near-limitless possibilities of 3D printing to create intricate designs allow entertainment professionals to bring objects from their imagination to life. Thanks to technology, this can be done quickly and at a much lower cost than in the past.
One example is Vitaly Bulgarov, a concept designer whose resume includes work with film studios such as Paramount and Dreamworks. He used 3D printing to quickly turn his computer sketches into props for a movie he was working on.