3D printed acoustic panels
A digital workflow for designing tailored 3D printed acoustic panels » 3D Printing Media Network
Stay up to date with everything that is happening in the wonderful world of AM via our LinkedIn community.
Designing an interior space is more than just coming up with the size and form of rooms: to really build an environment for human-use other elements must be taken into account, like sound. Acoustics play an integral role in how humans experience a space, whether it’s a concert arena, restaurant or even their own home. Acoustic panels, which can help absorb unwanted sound waves, are traditionally made from fabric and wood, foam or high-density fiberglass. The acoustic panels of the future, however, could very well be crafted using 3D printing.
A multidisciplinary team headed by the architecture department at TU Delft in the Netherlands is exploring the use of additive manufacturing for the design and production of customized acoustic panels. These panels, tailored to a given space, could help create a more user-friendly environment in large multi-use spaces, such as concert halls or sports arenas.
The research project, called “ADAM: Acoustics by parametric Design and Additive Manufacturing”, was advanced with the help of a user committee made up of companies from a range of industries. Among them was Materialise, a Belgium-based leader in additive manufacturing, which provided support for the production of the panels. The ADAM project is funded by the Netherlands Organization for Scientific Research.
The overall goal of the project was to develop acoustic panels that could be tailored to spaces to block out certain ambient frequencies and echoes. 3D printing was central to the project because of its ability to produce a practically limitless set of geometries as well as its propensity for mass customization. Further, AM enabled the team to create panels that were aesthetically interesting and could be installed as is.
“We use additive manufacturing because of its potential to produce a large variety of complex shapes,” elaborated Michela Turrin, Associate Professor of Design Informatics at TU Delft. “It gives a lot of freedom in the complexity of the geometry, but it also enables production to be made in unique pieces that are not necessarily based on industrial repetition.”
The panels are designed using a special digital workflow developed by the TU Delft team which gives designers, architects and engineers the tools to create custom 3D printable panels optimized for acoustic performance. The panel structures, for their part, consist of a series of tubes integrated into a curved panel or freestanding form, which provide Passive Destructive Interference to effectively cancel out specific frequencies. According to the research team, the tube-based designs are especially good at blocking out lower frequency ranges generated by heavy machinery or airplanes.
“The results are really promising, especially when it comes to lower frequencies and the reduced thickness of the applied materials,” said researcher Foteini Setaki. “We are hoping that we will be able, very soon, to launch a ready product that can enter the construction industry market.”
Once the panels are designed, they can then be manufactured using 3D printing. In its own demonstration, the team worked with Materialise to print the panels using selective laser sintering (SLS), which provided a cost-effective solution for creating the puzzle-like pieces.
“As 3D printing experts, we are there to empower our customers to build their solutions,” said Toon Roels, Director Process Engineering and Quality at Materialise. “When we work with others in collaborations such as this one, it’s our mission to ensure that the project incorporates the full value of AM to accomplish its goal. ”
Related Articles
Back to top button
TU Delft partners with Materialise to 3D print sound enhancing ‘acoustic panels’
0Shares
The Delft University of Technology (TU Delft) has worked with Belgian 3D printing software and service provider Materialise to develop 3D printed sound absorbing acoustic panels.
Created as part of a joint multidisciplinary research project, the fabricated tiles were custom-designed to improve the acoustic and auditory experiences of those in concert halls or sports arenas. Leveraging 3D printing rather than conventional manufacturing methods, the TU Delft team were also able to create the panels at a lower cost, and in more complex geometries than was previously thought possible.
“We used additive manufacturing because of its potential to produce a large variety of complex shapes,” said Michela Turrin, Associate Professor of Design Informatics at TU Delft. “It gives a lot of freedom in the complexity of the geometry, but it also enables production to be made in unique pieces that are not necessarily based on industrial repetition.”
Controlling the sound of music
Large open spaces such as concert or exhibition halls are often utilized by performers from a variety of disciplines. As a result, venues aren’t currently optimized for the sounds generated by each individual performance, and this can lead to the creation of unflattering, irritating frequencies for both the performer and the listener.
At present, tiresome frequencies are difficult to cancel out, because conventional panels don’t provide the architectural freedom or customization necessary to effectively dampen the sound. In order to overcome this issue, TU Delft set up a multidisciplinary committee of companies and began a research project with funding from the Netherlands Organization for Scientific Research.
The overarching aim of the program was to design enhanced panels that could be used to block loud noises, or bothersome frequencies and echoes. Materialise was chosen to optimize the production element of the process, as 3D printing provides intrinsic freedom of design, and enables the creation of structures with complex geometries.
Consequently, the panels could theoretically be created in a functional way to block out specific sound frequencies, but without ruining the aesthetics of the venue.
The researchers’ 3D printed panels were custom-designed to absorb certain sound frequencies. Photo via TU Delft.The prototype sound-absorbing panels
Materialise’s services were combined into a digital workflow, whereby designers, architects, and engineers used 3D modeling to craft the acoustics of parts for optimal performance. During the process, the panels were custom-designed to achieve Passive Destructive Interference (PDI), a self-cancellation technique that uses a part’s own form to cancel out a specific, tuneable, frequency band.
Once the design files were ready, the parts were summarily printed using a Selective Laser Sintering (SLS) process, yielding a number of puzzle-like components. The panels, consisting of a series of tubes with varying lengths and diameters, could then be slotted together into a curved freestanding structure, capable of blocking out specific sounds and echoes.
“Inside quarter wavelength tubes, a standing wave emerges, which determines the frequency at which sound absorption appears,” explained Martin Tenpierik, Associate Professor at TU Delft. “The length and the radius of the tube both determine that specific frequency, and we can also achieve broadband sound absorption, by including different kinds of tubes in one product.”
To evaluate the performance of their panel, the researchers placed their prototypes into a ‘reverberation room,’ in which sound absorbers were used to accurately measure their acoustic performance. The structures proved to be especially effective at absorbing lower frequencies, and following the successful tests, potential clients from a range of sectors have shown an interest in the devices.
“The results are really promising, especially when it comes to lower frequencies and the reduced thickness of the applied materials,” concluded Foteini Setaki, a researcher on the project. “We are hoping that we will be able, very soon, to launch a ready product that can enter the construction industry market.”
Other acoustic additive applications
Additive manufacturing enables users to create an almost unlimited number of geometries, and this has led many researchers to experiment with the acoustic potential of the technology.
Engineers from Duke’s Pratt School of Engineering have developed 3D printed cloak cover devices, that are able to reflect sound waves as soon as they hit a designated object. The cloak alters the trajectory of waves to give the impression that they did not hit anything at all, and they progress without changing frequency.
Physicists from the University of Texas at Dallas (UT Dallas) and China’s Wuhan University have used 3D printing to create a Weyl sonic crystal cube that’s capable of reflecting sound. The novel device could inspire new research in wave manipulation such as acoustic cloaking, or advances in user electronics.
Elsewhere, guitar manufacturer Nik Huber Guitars, partnered with amorphous metal specialists Heraeus AMLOY, to install a 3D printed bridge onto one of its guitars. The amorphous metals enabled the vibrations of the instrument to be transmitted differently, improving the acoustics of the instrument.
Nominations for the 2020 3D Printing Industry Awards are still open, let us know who is leading the industry now.
The fourth edition of the 3D Printing Industry Awards Trophy Design Competition is now underway. Enter your design for the chance to win a CraftBot Flow 3D printer.
To stay up to date with the latest 3D printing news, don’t forget to subscribe to the 3D Printing Industry newsletter or follow us on Twitter or liking our page on Facebook.
Are you looking for a job in the additive manufacturing industry? Visit 3D Printing Jobs for a selection of roles in the industry.
Featured image shows a member of the TU Delft team holding one of their 3D printed prototype panels. Photo via TU Delft.
Tags Delft University of Technology Duke Pratt School of Engineering Foteini Setaki Heraeus AMLOY Martin Tenpierik Materialise Michela Turrin Netherlands Organization for Scientific Research Nik Huber Guitars University of Texas at Dallas Wuhan University
Paul Hanaphy
Paul is a history and journalism graduate with a passion for finding the latest scoop in technology news.
TU DELFT and MATERIALISE develop process for designing 3d printed acoustic panels
You are here
Home
Acoustic panels that absorb unwanted sound waves are traditionally made of fabric and wood, high density foam or fiberglass. However, in the future, they may well be made using 3D printing.
A multidisciplinary team led by the Department of Architecture at the University of Delft in the Netherlands is exploring the use of additive technologies to design and manufacture room-specific acoustic panels to block certain ambient frequencies and echoes. These panels can help create a more comfortable sound environment in large, multifunctional spaces such as concert halls or sports arenas.
The research project was named "ADAM: Acoustics by parametric Design and Additive Manufacturing". 3D printing has taken center stage in the project, as it allows the creation of virtually any variation of geometries. In addition, according to the researchers, it can be used to create panels that would be aesthetically interesting and can be installed as is.
Acoustic panel design uses a custom digital workflow developed by the TU Delft team. With it, designers, architects and engineers can create custom 3D printed components with optimized acoustic performance. Panel designs consist of a set of tubes integrated into a curved surface or freestanding shape that provide effective rejection of certain frequencies. According to the research team, these designs are particularly good at blocking the lower frequency bands generated by heavy vehicles or aircraft.
Once custom panels are designed, they can be 3D printed. As part of the demonstration, the team worked with Belgian company Materialize to print the finished elements using SLS technology, which provided a cost-effective production solution.
"The results are really promising, especially when it comes to lower frequencies and reduced material thickness," said researcher Foteini Setaki. construction industry".
Source
Other materials:
- The Volgograd Region Prototyping Center helps implement innovative business ideas
- Scientists have learned how to 3D print a prototype of artificial muscles
- Rodinlabs 3D printing studio: a new brand - new opportunities
- Henkel discusses the development of materials for 3D printing
2 Project
Taimen — 3D printing of heavy-duty metal products
Attention!
We accept news, articles or press releases
with links and images. [email protected]
STL file Acoustic panel・Design for download and 3D printing・Cults
Acoustic panel
0,99 €
Acoustic panel cube
0,50 €
Panel Acousik
0,99 €
Acoustic panel
0,99 €
Engine V8 LS
5 €
Chopper Custom Moto
3 €
FGM-148 Javelin
1 €
Acoustic panel
0,99 €
Acoustic panel
0,99 €
Acoustic panel
0,99 €
Harley Davidson
5 €
An-225 "Mriya"
5 €
Best 3D Printer Files in Home Category
Horror story
Free
Outdoor Water Tap Knob
Free
Repair part for SEB electric mixer type 8141
Free
Braukmann Honeywell M40x1.
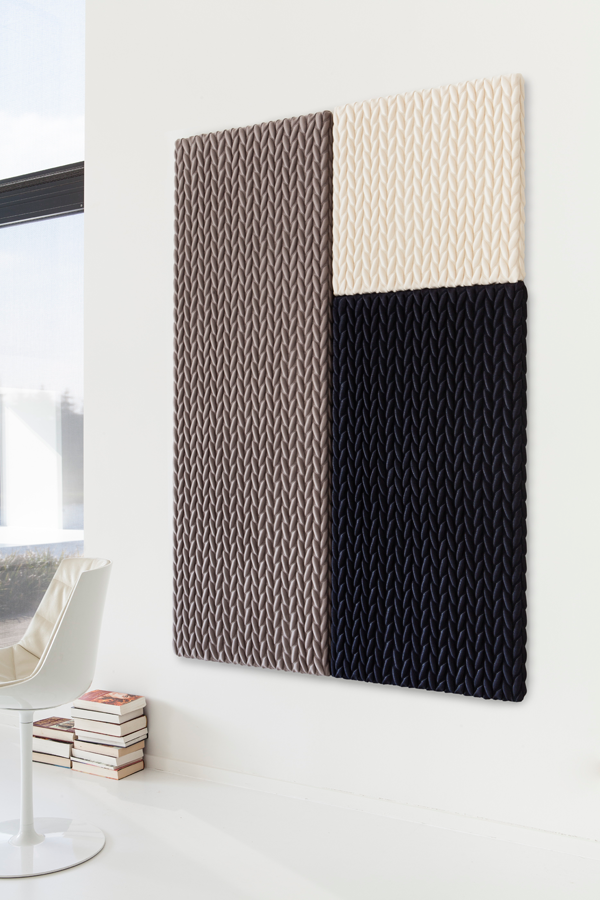
5 €
Filtom3D - Euqinom Vase
0,50 €
💀 Halloween Keychain ☠
0,90 €
SKULL - VAMP
Free
Ad hoc lamp v2
Free
Bestsellers in the Home category
Kawaii dim sums in a cute basket
1.46 €
Wall shelf "Amanita mushroom"
2,40 €
Bag stopper
1 €
Another quick-change paper towel roll holder (fold-out)
1 €
Die Hard Advent Calendar
6.28 €
Pumpkin girl
2. 90 €
Ladle for boiler
3.64 €
Super cute paw pen cup
1.37 €
Spider in a pumpkin
1.58 €
Venus and Aphrodite
3.60 €
Wallet card holder (universal package)
1.31 €
Notepad
2.60 €
Candlestick - Arbre de vie
1,20 €
Hooks for jewelry "Holly and the Dragon"
2.41 €
Cat in pencil holder
1.05 €
Articulated Christmas tree in lingerie
1.93 €
Do you want to support Cults?
Do you like Cults and want to help us continue our journey on our own ? Please note that we are a small team of 3 people, so support us in maintaining the activities of and creating future developments is very simple.