3D print high temperature plastic
Best heat resistant 3D printing materials
3D Learning Hub
See all categories
Contents:
- Introduction
- Heat Resistant 3D Printed Polymers
- Heat Resistant 3D Printed Metals
Introduction
Heat Resistant 3D Printed Polymers
According to the results of our annual survey, the State of 3D Printing 2018, plastic is the most common material used in Additive Manufacturing. That’s because plastics allow both for prototyping and production at a relatively low cost than the other 3D printing materials.
Consequently, due to their extensive use, plastics have many variations regarding their mechanical properties. Let’s see which are the best heat resistant 3D printing plastics:
Multijet Fusion PA12
Our Multijet Fusion PA12 parts are created from a fine polyamide powder. This innovative material provided by HP has many outstanding properties over conventional 3D printed plastics, as it’s water resistant, has an excellent resistance to chemicals, alcohols, fuels, detergents, oils, fats etc. On top of that, the Multi Jet Fusion PA12 objects are well suited for applications requiring heat resistance to high temperatures.
The material has gone through many experiments regarding its heat-resistant properties, like Glow Wire Ignition and Flammability testing. According to the White Card provided by HP, “The results obtained certify that the material can resist exposure to a range of 700 °C to 800 °C depending on the dimensions and thickness of the part. The fact that this material has a Glow Wire rating of 700 °C at a minimum thickness means that it can be considered acceptable when application requirements specify temperatures below 700 °C.”
It is important to highlight that HP 3D High Reusability PA 121 was the only 3D printing plastic material whose Glow Wire Flammability and Ignition performance had been certified by UL when the White Card was obtained.
Moreover, regarding its flammability properties, the Multijet Fusion PA 12 material ’s flammability degree is obtained and certified by UL is HB at a 0.75 mm thickness. More specifically, the material tolerates slow burning on a horizontal position (at a burning rate ≤ 75 mm/min for thicknesses < 3 mm or burning stops before 100 mm).
That said, the Multijet Fusion PA 12 material is the perfect plastic to choose for projects where large amounts of heat are generated. For additional info about other technical or mechanical properties of the HP Multijet Fusion PA12 material, check out the dedicated page. Moreover, we invite you to read the UL 94 and UL 746A Certification for our HP Multijet Fusion PA12 for even more detailed information regarding the flammability and electric conductivity of this 3D Printing material.
Ultrasint® PA6 MF
Do you need a strong and heat resistant material? Ultrasint® PA6 MF (Mineral Filled) might be the perfect material for you. Our PA6 MF is built on the chemical base of reinforced PA6; this 3D printing material combines high rigidity, media tightness, and enhanced thermal distortion performance. This plastic material is the perfect choice for any advanced technical applications where properties of mechanically reinforced thermoplastics are required.
With a 3300 MPa Tensile Modulus this material is quite resistant and perfect to create engine parts, and other components for the transportation sector. PA6 is strong enough to hold the whole engine assembly and handle all heat, vibration, and static loads.
The Heat Deflection Temperature of this material is of 207°, making it particularly interesting for projects where heat resistance is needed.
Ultrasint® PA6 FR
Ultrasint® PA6 FR (Flame Retardant) is an interesting high performance material. This 3D printing materials is a Halogen-Free Flame-Retardant PA6 powder for advanced applications, fitting the needs of advanced industries such as electronics, transportation, or automotive. PA6 FR combines excellent mechanical and thermal performance with flammability requirements.
This Ultrasint® PA6 FR is an engineering polymer powder made with an innovative formula, containing a flame-retardant (FR) additive. Its halogen-free formula based on PA6 material is making this 3D printing materials unique. PA6 FR is the perfect 3D printing material to use for flammability-sensitive application fields, his Heat Deflection Temperature (HDT/B) is at 207°.
This high performance PA6 FR material can also be used for electronics projects, its has a UL 94 V-2 rating starting at 0.8 mm, and it has a Glow Wire Flammability Index (GWFI) up to 960 °C.
Glass-Filled Nylon
Glass-filled Nylon is a variation of Nylon, as it’s made out of polyamide powder and glass beads, thus it’s more durable and resistant than the standard Nylon PA 12. It is durable and strong and you can use it in cases that demand high thermal conditions or in applications that require particular high heat distortion temperature. Since its melting point is 176 °C (249 °F), this material is a great choice if you want to create objects that fit the requirements of the technical parts. Thus, it perfectly fits projects with technical requirements, as for example in the automotive industry where it’s used for the creation of final parts of car engines.
Read more about the thermal properties of this material on the dedicated datasheet of Glass-filled Nylon.
Heat Resistant 3D Printed Metals
Titanium
Titanium is a 3D printing material with excellent mechanical properties. Not only it’s very durable, lightweight, highly resistant to oxidation and acid, but it’s also resistant to heat. The melting point of titanium is extremely high (1660° C or 3260° F).
For this reason, it is widely used in high-performance manufacturing applications, such as the Automotive, Aerospace, Medical industries.
You can read more about its mechanical and thermal properties on the dedicated Titanium Datasheet.
Aluminum
Aluminum is one of the most lightweight and durable materials used in 3D printing. It has great mechanical properties and can be used for parts subjected to high voltages. Moreover, it allows for high detail in design and with it, you can create complex geometries. One of its most important features is that it’s highly resistant to mechanical stress and high temperatures. Aluminum’s melting point is at 670°C. This makes Aluminum one of the best materials for prototyping. In addition, it is used to create durable parts and functional models that resist the high temperatures, such as motors, engines etc. Thus, aluminum is widely used in demanding industries, such as the automotive and aerospace industry.
Read more about the thermal treatment tests of Aluminum, and get to know more about its heat resistant properties.
Stainless Steel
Stainless Steel is another metal that has a high melting point: 1400 °C. Since stainless steel is melted at a very high temperature, it is widely used in demanding projects of various manufacturing industries as well as for prototyping. In the medical industry, it’s used for surgical assistance, endoscopic surgery, and creation of customized orthopedics. In the aerospace and automobile industry, it is used for producing mechanical parts that need to resist to heat and abrasion. Additional to the great heat resistant properties of stainless steel, it has a very strong resistance against corrosion and is distinguished for its high ductility.
You can check out the Datasheet for the Stainless Steel material for more information about its mechanical and thermal properties.
Related Topics
- Return to Top
Get the latest 3D printing news delivered right to your inbox
Subscribe to our weekly newsletter to hear about the latest 3D printing technologies, applications, materials, and software.
Exploring The World of High-Temperature 3D Printing Materials « Fabbaloo
Some of the high-temperature materials used in 3D printing [Source: Fabbaloo]In the last 2-3 years there has been a dramatic rise in high-temperature 3D printing, but what are the materials for this type of printing?
For many years most thermoplastic 3D printing was limited to a very small subset of thermoplastics, mainly PLA and ABS, with a bit of PETG. That’s still the case for most desktop equipment, but there have been many commercial devices developed that can handle materials at far higher temperatures.
Higher-temperature materials are extremely useful because they can be applied in more environments. Consider a plastic part in an automobile engine: it would soften or even melt if exposed to sufficiently high temperatures. But if it was made from a material that had higher heat resistance it might be usable.
That’s desirable because plastic parts are often lighter than their metal counterparts, which is advantageous in many ways, particularly in the automotive and aerospace industries. Thus there’s been a bit of rush towards these high-temperature 3D printed parts.
The open-style desktop 3D printers are entirely inadequate for 3D printing high-temperature materials as the heat required must certainly be enclosed and precisely controlled. Several 3D printer manufacturers have emerged recently that focus specifically on this type of machine and material, including Roboze, INTAMSYS, Minifactory and others. Some traditional manufacturers, such as Stratasys, offer high-temperature thermoplastic material options as well.
But what are these materials? What are their properties and how can they be used in 3D printing?
Chemical name “Polyether ether ketone”, this polymer is actually part of the PAEK family and apparently was invented by Victrex in the UK in the 1980s. It’s become one of the most popular high-temp 3D printing materials as it provides significant robustness and therefore is often used for high-stress applications.
Chemical name ”Polyetherketoneketone”, this emerging 3D print material is becoming more popular. PEKK is quite similar to PEEK in more than just its name, as they share many common properties. However, PEKK is able to withstand far greater compressive force. It also tends to have a slightly higher heat resistance level than PEEK.
Chemical name “Polyetherimide”, and also found under the trade name “ULTEM”, a brand of SABIC. It was one of the first high-temp 3D print materials, offered by Stratasys as a material option on their Fortus equipment. While less expensive than PEEK, it also has somewhat less thermal resistance and strength. It’s often used in aerospace applications.
Chemical name “Polyphenylsulfone”. This material offers high strength and chemical resistance. A unique property is that it has no melting point, according to Wikipedia, which says this is due to its amorphous internal structure. Several companies offer this material option, including Stratasys.
Chemical name “Polyaryletherketone”. This material is a relative newcomer to the high-temperature 3D printing space, but it has extremely high temperature resistance of up to 350C, and has less toxin emissions when burned than other high-temperature materials. This allows it to be used in applications where human exposure may occur.
Polycarbonate refers to a class of polymers integrating carbonate in their structure. PC is a very popular material as it offers great durability, as well as very high impact and scratch resistance. As such it is commonly used in consumer products.
Polyamides are a very common 3D printing material, although it may be hard to justify them as being a high-temperature material as some have relatively low glass transition temperatures as compared to other materials on this list. There are several species of PA, usually designated by a number: PA-6, PA-11, PA-12, PA-66, etc. They are also referred to as “nylons”.
Chemical name ”Polyvinylidene fluoride”. This is a very new material to 3D printing, currently supported only by a few 3D printer manufacturers, including Minifactory. The main claim of PVDF is that it is almost completely non-reactive to other materials, thus making it suitable for specific applications where exposure is required, including biomedical applications.
TPI
Thermoplastic polyimide seems to be at only the research stage of 3D printing, where we look to a 2018 paper where researchers tested the possibility of 3D printing with TPI. They found the optimum extrusion temperature for TPI to be 335C, qualifying it for this list. TPI offers abrasion resistance, high-temperature resistance and long-term durability. It could become another material for 3D printing in the future.
High-Temperature 3D Print Material Variations
The above list includes the basic materials, but you’ll find a vastly greater selection in the marketplace simply due to variations.
For example, SABIC offers over 100 unique grades of ULTEM, each having slightly different properties. Some are chemically different, while others are composite materials, where different substances are mixed in with the polymer.
Typical composite variations of the above materials may include the addition of glass fiber to strengthen the prints. Another very popular composite additive is carbon fiber segments, which, although chopped, still offer a significant strength advantage over the polymer alone.
Some variations offer unusual properties, such as ESD rating. These materials are able to prevent electrostatic discharges, which enables their use in specific flammable situations involving.
While the choice of materials is made based on the requirements of the application, there’s another choice to be made: support materials. For many 3D prints overhangs could require supports. Unfortunately, many of the most commonly used support materials are not valid for high-temperature 3D printing since the chamber temperatures will be far higher than their melting points. Thus there are a few specific support materials available for high-temperature applications.
Finally, there’s the possibility of high-temperature thermoset materials. Unlike the thermoplastics used in extrusion-based 3D printing that can be repeatedly softened and hardened, thermosets harden exactly once. Some variations of thermoset mixtures are capable of handling higher temperatures, but for most high-temperature applications the materials above are typically selected.
Overview of high-temperature FDM plastics for industrial 3D printing
The scope of application of additive technologies is wide: on one extreme - desktop printers "only PLA", for decorative applications, on the other - installations for direct printing with metals, between them - equipment and materials in assortment. To understand what materials are needed to obtain a strong and lightweight part, we are moving from personal printing to industrial printing. PLA, ABS, SBS are consumables that are familiar to all printers. PETG, nylon, polycarbonate - rather exotic. But these are far from the most serious materials.
Where are superplastics needed?
Plastics with outstanding properties are very useful in space. No, it’s not yet possible to print a rocket engine out of plastic, the heat resistance is not even close to the same, but it is ideal for various parts around. An example is Stratasys and the "climate control" of Atlas V rockets. 16 printed parts instead of 140 metal parts - faster, lighter, cheaper. And this is not a theoretical project, it has already flown into space.
Another example is aviation. The flight altitude is lower, but the application is more massive. Here, too, there is a reason to reduce the mass of parts, switch to plastic where possible. It is used in the aircraft industry and direct metal printing, when it comes to engine components or fuselage frame parts, but less loaded structural elements, such as cabin ventilation and interior elements, are best made from plastic. This direction is being developed, for example, by Airbus.
We are descending from heaven to earth: here the mass is no longer so critical, other properties of engineering plastics are interesting. Resistance to aggressive chemicals and elevated temperatures, the ability to create structures inaccessible to classical methods. At the same time - a lower price, in comparison with metal printing. Printed products are used in medicine, oil and gas industry, chemical industry. As an example, a mixing block with a complex channel structure, made for illustration in a section.
Difference from conventional plastics
Why not launch PLA into space and make aircraft cabin air vents out of ABS? A number of requirements are applied to engineering plastics related to resistance to high and low temperatures, fire resistance, mechanical strength. Usually all at once. So, it is undesirable to launch PLA “floating” when interacting with the environment or perfectly burning ABS into the sky. Now - to what, in fact, plastics are used in industrial printing using FDM / FFF technology.
Polycarbonate filaments
Polycarbonate is a common industrial plastic with high impact resistance and transparency, also produced for the needs of FDM printing. The material holds temperature better than ABS, is resistant to acids, but is sensitive to UV radiation and is destroyed by oil products.
Clear polycarbonate, PC
The operating temperature limit for polycarbonate products is 130°C. Polycarbonate is biologically inert, products made from it can withstand sterilization, which makes it possible to print packaging and auxiliary equipment for medicine.
- Stratasys PC, PC-ISO for Fortus printers. The first is general purpose, the second is certified for biocompatibility, for medical use.
- Intamsys PC;
- Esun ePC;
- SEM PC;
- PrintProduct PC;
ABS/PC
Polycarbonate/ABS alloy combines the sanding and painting capabilities of ABS with higher impact resistance and operating temperature. Retains strength at low temperatures down to -50 °C. Unlike pure PC, it is better applicable in cases where it is necessary to eliminate the layered structure of the part by grinding or sandblasting. Application: production of housings and elements of controls for piece and small-scale production, replacement of mass-produced plastic parts in equipment, parts for which have ceased to be produced.
- Stratasys PC/ABS;
- Roboze PC-ABS;
- SEM ABS/PC;
- BestFilament ABS/PC.
Polyamide based filaments
Polyamides are used in the manufacture of synthetic fibers, a popular material for laser selective sintering (SLS) printing. For printing using FDM / FFF technology, polyamide-6 (kapron), polyamide-66 (nylon) and polyamide-12 are mainly used. Common features of polyamide-based filaments include chemical inertness and anti-friction properties. Polyamide-12 is more flexible and resilient than PA6 and PA66. Operating temperature approx. 100 °C, some modifications up to 120.
First of all, gears are printed from polyamide. The best material for this purpose, which can be worked with on a regular 3D printer with a closed chamber. Abrasion resistance allows you to make rods, cams, sliding bushings. In the line of many manufacturers there are composite filaments based on polyamide, with even greater mechanical strength.
- Stratasys Nylon 6, Nylon 12, Nylon 12CF. The latter is filled with carbon fiber.
- Intamsys Nylon, PA6.
- Taulman Nylon 618, Nylon 645 - based on PA66 and PA6, respectively. Nylon 680 is approved for use in the food industry. Alloy 910 is a low shrinkage polyamide alloy.
- PrintProduct Nylon, Nylon Mod, Nylon Strong;
- REC Friction;
- BestFilament BFNylon.
Moving on to the fun part
You can work with polycarbonate or polyamide on a regular 3D printer. With the filaments described below, it is more difficult, they require other extruders and maintaining the temperature in the working chamber, that is, you need special equipment for printing with high-temperature plastics. There are exceptions - for example, NASA, for the sake of experiment, upgraded the Lulzbot TAZ popular in the USA to work with high-temperature filaments.
Polyetheretherketone, PEEK
Working temperature of PEEK products reaches 250 °C, short-term heating up to 300 is possible - indicators for reinforced filaments. PEEK has two disadvantages: high price and moderate impact resistance. The rest is pluses. The plastic is self-extinguishing, heat-resistant, chemically inert. Medical equipment and implants are produced from PEEK, abrasion resistance makes it possible to print parts of mechanisms from it.
- Intamsys PEEK;
- Apium PEEK;
- Roboze PEEK, Carbon PEEK. The second is reinforced with carbon fiber.
Polyetherimide, PEI
aka Ultem. A family of plastics developed by SABIC. The characteristics of PEI are more modest than those of PEEK, but the cost is noticeably lower. Ultem 1010 and 9085 are Stratasys' primary materials for printing functional parts. PEI is in demand in the aerospace industry - the mass is much less compared to aluminum alloys. Operating temperatures of products, depending on the modification of the material, reach 217 ° C according to the manufacturer and 213 - according to the results of tests by Stratasys.
The advantages of PEI are the same as those of PEEK - chemical and temperature resistance, mechanical strength. It is this material that Stratasys is promoting as a partial replacement for metal in the aerospace industry, for drones, the manufacture of tooling for molding, the rapid printing of functional parts in pilot production.
The Atlas V rocket cooling system components and Airbus plastic parts shown as an example at the beginning of the review are made of Ultem 9085.
- Stratasys Ultem 1010 and 9085, for Fortus 450mc and 900mc printers.
- Intamsys Ultem 1010 and 9085;
- Roboze Ultem AM9085F;
- Apium PEI 9085.
Polyphenylsulfone, PPSF/PPSU
Another material that combines temperature resistance, mechanical strength and chemical resistance in its properties. Stratasys PPSF is certified for aerospace and medical applications. Positioned as a raw material for the production of auxiliary medical devices, it can be sterilized in steam autoclaves. It is used in the production of parts for laboratory installations in the chemical industry.
- Stratasys PPSF;
- 3DXTech Firewire PPSU.
Polysulfone, PSU
Less common than PPSU, similar physical characteristics, chemically inert, self-extinguishing. 175°C operating temperature, up to 33% cheaper than PPSU.
- 3DXTech Firewire PSU
Filament performance comparison
* Baked for 2 hours at 140°C.
** Apium PEEK 450 natural, no similar impact test results available. Temperature resistance is specified for unfilled PEEK.
Data shown for Stratasys filaments, excluding PEEK. If a range of values is indicated, then the tests were carried out along and across the layers of the part.
About Composite Filaments
Most FDM materials have composite versions. If we talk about PLA, then metal or wood powders are added to it to change the aesthetic properties. Engineering filaments are reinforced with carbon fiber to increase the rigidity of the part. The influence of such additives on the properties of plastic depends not only on their quantity, but also on the size of the fibers. If a fine powder can be considered a decorative additive, then the fibers already significantly change the characteristics of the plastic. By itself, the word Carbon in the name of the material does not yet mean outstanding properties, you need to look at the test results. For example: Stratasys Nylon12CF has almost twice the tensile strength, when tested along the layers, than Nylon12.
An exotic variant of Markforged's implementation of continuous reinforcement. The company offers a reinforcing filament for co-FDM printing with other plastics.
Other specific properties
Engineering plastics are not only high temperature resistance and mechanical strength. For housings or boxes for storing electronic devices, and in environments where flammable volatile liquids are used, materials with antistatic properties are required. In the Stratasys line, this is, for example, ABS-ESD7.
- Stratasys ABS-ESD7;
- Roboze ABS-ESD.
Conventional ABS is not UV resistant, limiting its outdoor use without a protective coating. As an alternative, ASA is offered, which has characteristics similar to ABS, except for the UV resistance.
- REC Eternal;
- SEM ASA;
- BestFilament ASA.
Original alternative
Plastic can replace metal in many areas, as it surpasses it in lightness, thermal and electrical insulation, resistance to reagents. But printouts from the best FDM filaments do not reach the physical indicators of metal products.
Chemical giant BASF offers Ultrafuse 316LX FDM filament with 80% stainless steel by weight. The part is printed on an FDM printer and then placed in an oven where the binder plastic is burned off and the metal is sintered. The part obtained in this way is much cheaper than the one made by direct metal printing. With an FDM printer and a suitable oven, no new equipment is needed at all.
Note that Virtual Foundry offers a similar solution - its Filamet, with bronze or copper powder, is baked in a similar way. The choice of metal hints at decorative rather than engineering applications.
AIM3D has its own implementation of this principle - the ExAM 255 printer does not work with filament, but with granules. This allows the use of raw materials for FDM printing, which are usually used in MIM installations, Metal Injection Molding. For sintering the part, the company offers an ExSO 9 furnace0. It is also possible to print with plastic granules, which is usually cheaper than using traditional filament.
Special machinery for engineering plastics
To recap. In a nutshell: the considered consumables differ from the usual materials in high printing temperature, which requires the use of special equipment, and serious heat resistance and mechanical strength of the manufactured parts. To work with such filaments, 3D printers with an extruder operating temperature of 350 °C and a heat-stabilized working chamber are required. Top 3D Shop specialists will help you with the selection of an industrial 3D printer and plastics for solving the most interesting tasks.
Want more exciting news from the world of 3D technology?
Follow us on social. networks:
Vk
Youtube
Top 3D Shop - Your expert in the 3D technology market
consumer grade 3D printers. But, despite this, most often users turn to polylactide (PLA) threads. This is not only the cheapest of materials, but also the easiest to work with. Its extrusion can already be carried out at a temperature of 180 °C, and good results can be obtained even without preheating the table. The disadvantage of PLA-printed objects is that they are relatively brittle and do not tolerate high temperatures well. For prototyping or printing low-stress components, PLA is great.
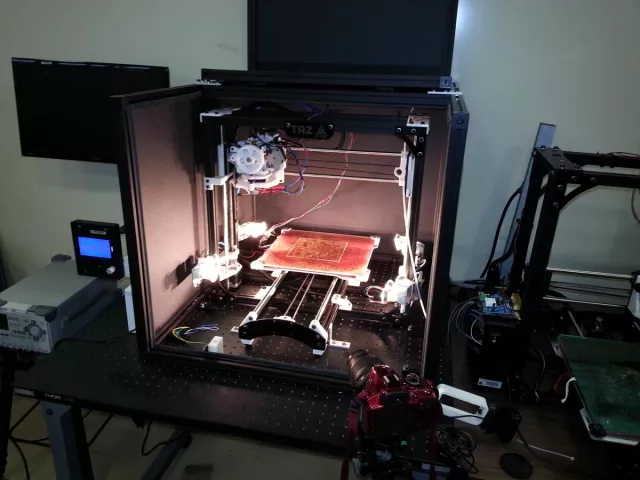
Polyethylene terephthalate (PETG) is usually the next step. It is not much harder to work with compared to PLA, while it is more reliable and can withstand higher temperatures. In general, it is better suited for creating mechanically loaded parts. But if you need to make even stronger and more heat resistant parts, you can switch to acrylonitrile butadiene styrene (ABS), polycarbonate (PC) or nylon. And this is where the problems begin. These materials are extruded at temperatures over 250°C and closed chambers are recommended for best results. These printers are at the top of the budget range that hobbyists are willing to work with.
Industrial 3D printers like this one, the Apium P220, start at around $30,000. (PAEK, PEEK, PEKK). Components made from these plastics are suitable for aerospace applications as they can replace metal while remaining much lighter.
These plastics need to be extruded at temperatures in the order of 400°C and require a hermetically sealed chamber that is constantly above 100°C. The cheapest printers of this kind cost tens of thousands of dollars, and some models even cost six figures.
Naturally, not so long ago, the same could be said about all 3D printers. Once used only by well-equipped research labs, these machines now sit on the workbenches of hackers and hobbyists the world over. It is difficult to predict whether the same price-cutting race will start for high-temperature 3D printers, but the first steps to democratize the technology have already been made.
Engineering difficulties
Simply put, a machine that supports these so-called. "engineering plastics", you need to be a hybrid of a 3D printer and a stove. This, of course, is the main problem. The printer itself - of the type and quality we are accustomed to seeing on our desks - will not survive in such conditions. In order for a consumer printer to produce PEI and PEEK plastic parts, it needs to be seriously redesigned. This is exactly what NASA did with the LulzBot TAZ 4 in 2016.
LulzBot TAZ 4 redesigned to support high temperature printing
The first step was to construct an insulated housing to fit the TAZ 4 and install a set of 35W infrared lamps for heating. Under such conditions, the printer's electronics would naturally overheat - so it had to be taken outside.
Stepper motors would also overheat. But instead of taking them out, the team at the Langley Research Center decided to build cooling shrouds on each of the motors through which the compressed air must circulate.
Like many desktop 3D printers, the TAZ 4 uses several printed components. Since they are ABS, they would quickly break down in a chamber designed to support PEEK. They were printed from PC, but even this material was not resistant enough for permanent use. In classic RepRap tradition, the team printed the last, third set of components on their most modified printer, in PEI plastic, commercially named Ultem.
Surprisingly, the team had no trouble changing the printer's nozzle to one that could extrude plastic at 400°C. The popular E3D-v6 extruder costs less than $100 and has been shown to be able to maintain this temperature. True, the team had to replace the thermistor with a better one, as well as edit the Marlin firmware so that it allowed it to reach high temperatures. For conventional printers, too high a temperature should cause an emergency shutdown.
Printing results from Ultem 1010 plastic on a remanufactured LulzBot TAZ 4.
In the end, the NASA report indicated that the redesign of the LulzBot TAZ 4 was a complete success. They noted that an attempt to print PEI with infrared lamps turned off ended in failure - delamination and distortion of the model, which was to be expected. They did not specify the cost of the conversion, but given that at that time the TAZ 4 cost $2200, the entire project could cost 10 times cheaper than similar commercial proposals.
Starting from zero
A NASA experiment has shown that an existing desktop 3D printer can be converted to print with high-temperature engineering plastics, and quite inexpensively. But hardly anyone believes that this approach is the ideal solution. There are too many repetitive operations involved here, and NASA engineers had to abandon some of the decisions made by the LulzBot developers. Still, the experiment provided a valuable baseline for other projects built from scratch.
In September 2020, a team from Michigan Technological University demonstrated the Cerberus, an open-source, high-temperature 3D printer capable of creating objects from PEI and PEKK that costs as little as $1,000 to build. Without trying to adapt existing designs, the team started development from scratch, aiming for high temperature printing. All electronics are housed separately from the sealed chamber, which uses a kilowatt heating element to quickly raise the temperature in the chamber to operating temperature.
All stepper motors are also outside the chamber. Because of this, the kinematics become more complex than in desktop 3D printers, but Cerberus no longer requires a special motor cooling system.
Building a Cerberus is quite affordable for the aspiring hobbyist. It has a simplified circuit, ready-made control electronics based on the Arduino Mega 2560 and RAMPS 1.4, and the same E3D-v6 extruder as the TAZ 4. In addition, the team posted clear and detailed instructions for assembling the printer - this is not in the NASA report. meet.
Expanding possibilities
Whether it's NASA's redesign of the TAZ 4, or the new Cerberus-type circuits, it's clear that the technical capabilities of PEI and PEEK printing in the home workshop are already available for those who really need them. So far, it's not as easy as buying a $200 3D printer on Amazon, but if there is demand, cheaper machines based on the same principles will appear on the market. The situation is not much different from the current wave of affordable laser cutters hitting the markets in the past few years.
Fans all over the world print PPE
Is there a demand for such machines? A year ago, the answer might have been different from today.