3D printer hub
3D Printing Service UK | Instant Quotes Online
Our 3D printing capabilities
We have over 90 3D printing shops in our network and are well known for manufacturing high-quality parts at competitive prices, from rapid prototyping with Fused Deposition Modeling (FDM) to functional end parts made with Selective Laser Sintering (SLS) or Multi Jet Fusion (MJF).
Gallery of 3D printed parts manufactured by Hubs
With over 65,000 customers from every industry, including aerospace, defense, robotics, medical, machinery, automotive and electronics, we have extensive experience meeting a diverse range of 3D printing requirements, from prototyping to production: Visual aids, concept models, injection-molding prototypes, form-fit & function prototypes, tooling and casting patterns, jigs, grips and fixtures, and durable end parts.
HP PA 12 - Dyed Black
Customer | True North Design |
Purpose | Structural and vacuum EOAT components |
Process | SLS / MJF |
Unit price | $69. |
Industry | Automotive |
Prototyping PLA
Customer | Allision Conner |
Purpose | End caps and cable strain relief for sheet metal enclosure |
Process | FDM |
Unit price | $7.92 / $4.72 / $2.80 |
Industry | Industrial Automation |
HP PA 12
Customer | US Hammer |
Description | A part for gasoline engine powered jackhammers |
Process | MJF |
Unit price | $22.18 |
Industry | Construction |
Markforged Onyx - Black
Customer | Autocom Manufacturing |
Purpose | A production part for 3D printed lathe gantry gripper fingers |
Process | FDM |
Unit price | $48.![]() |
Industry | Automotive |
PC Stratasys - white
Customer | Terumo medical corporation |
Purpose | Prototyping parts used for a disposable electrical device |
Process | FDM |
Unit price | $55.38 / $32.96 |
Industry | Medical |
Formlabs Clear Resin
Customer | Aversan Inc |
Purpose | A prototyping part of an injection molded component for an automated door mechanism |
Process | SLA |
Unit price | $29.83 |
Industry | Aerospace |
HP PA 12 - Dyed Black
Customer | True North Design |
Purpose | Structural and vacuum EOAT components |
Process | SLS / MJF |
Unit price | $69.![]() |
Industry | Automotive |
Prototyping PLA
Customer | Allision Conner |
Purpose | End caps and cable strain relief for sheet metal enclosure |
Process | FDM |
Unit price | $7.92 / $4.72 / $2.80 |
Industry | Industrial Automation |
HP PA 12
Customer | US Hammer |
Description | A part for gasoline engine powered jackhammers |
Process | MJF |
Unit price | $22.18 |
Industry | Construction |
Markforged Onyx - Black
Customer | Autocom Manufacturing |
Purpose | A production part for 3D printed lathe gantry gripper fingers |
Process | FDM |
Unit price | $48.![]() |
Industry | Automotive |
PC Stratasys - white
Customer | Terumo medical corporation |
Purpose | Prototyping parts used for a disposable electrical device |
Process | FDM |
Unit price | $55.38 / $32.96 |
Industry | Medical |
Formlabs Clear Resin
Customer | Aversan Inc |
Purpose | A prototyping part of an injection molded component for an automated door mechanism |
Process | SLA |
Unit price | $29.83 |
Industry | Aerospace |
HP PA 12 - Dyed Black
Customer | True North Design |
Purpose | Structural and vacuum EOAT components |
Process | SLS / MJF |
Unit price | $69.![]() |
Industry | Automotive |
Prototyping PLA
Customer | Allision Conner |
Purpose | End caps and cable strain relief for sheet metal enclosure |
Process | FDM |
Unit price | $7.92 / $4.72 / $2.80 |
Industry | Industrial Automation |
HP PA 12
Customer | US Hammer |
Description | A part for gasoline engine powered jackhammers |
Process | MJF |
Unit price | $22.18 |
Industry | Construction |
Markforged Onyx - Black
Customer | Autocom Manufacturing |
Purpose | A production part for 3D printed lathe gantry gripper fingers |
Process | FDM |
Unit price | $48.![]() |
Industry | Automotive |
PC Stratasys - white
Customer | Terumo medical corporation |
Purpose | Prototyping parts used for a disposable electrical device |
Process | FDM |
Unit price | $55.38 / $32.96 |
Industry | Medical |
Formlabs Clear Resin
Customer | Aversan Inc |
Purpose | A prototyping part of an injection molded component for an automated door mechanism |
Process | SLA |
Unit price | $29.83 |
Industry | Aerospace |
HP PA 12 - Dyed Black
Customer | True North Design |
Purpose | Structural and vacuum EOAT components |
Process | SLS / MJF |
Unit price | $69.![]() |
Industry | Automotive |
Prototyping PLA
Customer | Allision Conner |
Purpose | End caps and cable strain relief for sheet metal enclosure |
Process | FDM |
Unit price | $7.92 / $4.72 / $2.80 |
Industry | Industrial Automation |
HP PA 12
Customer | US Hammer |
Description | A part for gasoline engine powered jackhammers |
Process | MJF |
Unit price | $22.18 |
Industry | Construction |
Markforged Onyx - Black
Customer | Autocom Manufacturing |
Purpose | A production part for 3D printed lathe gantry gripper fingers |
Process | FDM |
Unit price | $48.![]() |
Industry | Automotive |
PC Stratasys - white
Customer | Terumo medical corporation |
Purpose | Prototyping parts used for a disposable electrical device |
Process | FDM |
Unit price | $55.38 / $32.96 |
Industry | Medical |
Formlabs Clear Resin
Customer | Aversan Inc |
Purpose | A prototyping part of an injection molded component for an automated door mechanism |
Process | SLA |
Unit price | $29.83 |
Industry | Aerospace |
HP PA 12 - Dyed Black
Customer | True North Design |
Purpose | Structural and vacuum EOAT components |
Process | SLS / MJF |
Unit price | $69.![]() |
Industry | Automotive |
Prototyping PLA
Customer | Allision Conner |
Purpose | End caps and cable strain relief for sheet metal enclosure |
Process | FDM |
Unit price | $7.92 / $4.72 / $2.80 |
Industry | Industrial Automation |
HP PA 12
Customer | US Hammer |
Description | A part for gasoline engine powered jackhammers |
Process | MJF |
Unit price | $22.18 |
Industry | Construction |
Markforged Onyx - Black
Customer | Autocom Manufacturing |
Purpose | A production part for 3D printed lathe gantry gripper fingers |
Process | FDM |
Unit price | $48.![]() |
Industry | Automotive |
PC Stratasys - white
Customer | Terumo medical corporation |
Purpose | Prototyping parts used for a disposable electrical device |
Process | FDM |
Unit price | $55.38 / $32.96 |
Industry | Medical |
Formlabs Clear Resin
Customer | Aversan Inc |
Purpose | A prototyping part of an injection molded component for an automated door mechanism |
Process | SLA |
Unit price | $29.83 |
Industry | Aerospace |
HP PA 12 - Dyed Black
Customer | True North Design |
Purpose | Structural and vacuum EOAT components |
Process | SLS / MJF |
Unit price | $69.![]() |
Industry | Automotive |
Prototyping PLA
Customer | Allision Conner |
Purpose | End caps and cable strain relief for sheet metal enclosure |
Process | FDM |
Unit price | $7.92 / $4.72 / $2.80 |
Industry | Industrial Automation |
HP PA 12
Customer | US Hammer |
Description | A part for gasoline engine powered jackhammers |
Process | MJF |
Unit price | $22.18 |
Industry | Construction |
Markforged Onyx - Black
Customer | Autocom Manufacturing |
Purpose | A production part for 3D printed lathe gantry gripper fingers |
Process | FDM |
Unit price | $48.![]() |
Industry | Automotive |
PC Stratasys - white
Customer | Terumo medical corporation |
Purpose | Prototyping parts used for a disposable electrical device |
Process | FDM |
Unit price | $55.38 / $32.96 |
Industry | Medical |
Formlabs Clear Resin
Customer | Aversan Inc |
Purpose | A prototyping part of an injection molded component for an automated door mechanism |
Process | SLA |
Unit price | $29.83 |
Industry | Aerospace |
HP PA 12 - Dyed Black
Customer | True North Design |
Purpose | Structural and vacuum EOAT components |
Process | SLS / MJF |
Unit price | $69.![]() |
Industry | Automotive |
Prototyping PLA
Customer | Allision Conner |
Purpose | End caps and cable strain relief for sheet metal enclosure |
Process | FDM |
Unit price | $7.92 / $4.72 / $2.80 |
Industry | Industrial Automation |
HP PA 12
Customer | US Hammer |
Description | A part for gasoline engine powered jackhammers |
Process | MJF |
Unit price | $22.18 |
Industry | Construction |
Markforged Onyx - Black
Customer | Autocom Manufacturing |
Purpose | A production part for 3D printed lathe gantry gripper fingers |
Process | FDM |
Unit price | $48.![]() |
Industry | Automotive |
PC Stratasys - white
Customer | Terumo medical corporation |
Purpose | Prototyping parts used for a disposable electrical device |
Process | FDM |
Unit price | $55.38 / $32.96 |
Industry | Medical |
Formlabs Clear Resin
Customer | Aversan Inc |
Purpose | A prototyping part of an injection molded component for an automated door mechanism |
Process | SLA |
Unit price | $29.83 |
Industry | Aerospace |
HP PA 12 - Dyed Black
Customer | True North Design |
Purpose | Structural and vacuum EOAT components |
Process | SLS / MJF |
Unit price | $69.![]() |
Industry | Automotive |
Prototyping PLA
Customer | Allision Conner |
Purpose | End caps and cable strain relief for sheet metal enclosure |
Process | FDM |
Unit price | $7.92 / $4.72 / $2.80 |
Industry | Industrial Automation |
HP PA 12
Customer | US Hammer |
Description | A part for gasoline engine powered jackhammers |
Process | MJF |
Unit price | $22.18 |
Industry | Construction |
Markforged Onyx - Black
Customer | Autocom Manufacturing |
Purpose | A production part for 3D printed lathe gantry gripper fingers |
Process | FDM |
Unit price | $48.![]() |
Industry | Automotive |
PC Stratasys - white
Customer | Terumo medical corporation |
Purpose | Prototyping parts used for a disposable electrical device |
Process | FDM |
Unit price | $55.38 / $32.96 |
Industry | Medical |
Formlabs Clear Resin
Customer | Aversan Inc |
Purpose | A prototyping part of an injection molded component for an automated door mechanism |
Process | SLA |
Unit price | $29.83 |
Industry | Aerospace |
HP PA 12 - Dyed Black
Customer | True North Design |
Purpose | Structural and vacuum EOAT components |
Process | SLS / MJF |
Unit price | $69.![]() |
Industry | Automotive |
Prototyping PLA
Customer | Allision Conner |
Purpose | End caps and cable strain relief for sheet metal enclosure |
Process | FDM |
Unit price | $7.92 / $4.72 / $2.80 |
Industry | Industrial Automation |
HP PA 12
Customer | US Hammer |
Description | A part for gasoline engine powered jackhammers |
Process | MJF |
Unit price | $22.18 |
Industry | Construction |
Markforged Onyx - Black
Customer | Autocom Manufacturing |
Purpose | A production part for 3D printed lathe gantry gripper fingers |
Process | FDM |
Unit price | $48.![]() |
Industry | Automotive |
PC Stratasys - white
Customer | Terumo medical corporation |
Purpose | Prototyping parts used for a disposable electrical device |
Process | FDM |
Unit price | $55.38 / $32.96 |
Industry | Medical |
Formlabs Clear Resin
Customer | Aversan Inc |
Purpose | A prototyping part of an injection molded component for an automated door mechanism |
Process | SLA |
Unit price | $29.83 |
Industry | Aerospace |
HP PA 12 - Dyed Black
Customer | True North Design |
Purpose | Structural and vacuum EOAT components |
Process | SLS / MJF |
Unit price | $69.![]() |
Industry | Automotive |
Prototyping PLA
Customer | Allision Conner |
Purpose | End caps and cable strain relief for sheet metal enclosure |
Process | FDM |
Unit price | $7.92 / $4.72 / $2.80 |
Industry | Industrial Automation |
HP PA 12
Customer | US Hammer |
Description | A part for gasoline engine powered jackhammers |
Process | MJF |
Unit price | $22.18 |
Industry | Construction |
Markforged Onyx - Black
Customer | Autocom Manufacturing |
Purpose | A production part for 3D printed lathe gantry gripper fingers |
Process | FDM |
Unit price | $48.![]() |
Industry | Automotive |
PC Stratasys - white
Customer | Terumo medical corporation |
Purpose | Prototyping parts used for a disposable electrical device |
Process | FDM |
Unit price | $55.38 / $32.96 |
Industry | Medical |
Formlabs Clear Resin
Customer | Aversan Inc |
Purpose | A prototyping part of an injection molded component for an automated door mechanism |
Process | SLA |
Unit price | $29.83 |
Industry | Aerospace |
Instant, online 3D printing quotes
-
Upload a CAD to start (STEP, STP, IGES, IGS, SLDPRT, 3DM, SAT, STL, OBJ or X_T)
-
Price updates in real-time as you change materials, lead time, etc.
.
-
No hidden costs. Our instant quotes are not just indications, but the actual price, and include shipping and customs up front.
Learn about how our quoting algorithm works
Our ordering process
Receive instant quote
Upload your CAD to our online quoting platform
Confirm specs
Configure your part specifications and select a lead time that suits your schedule
Production
We select the best manufacturer for your order, and production begins immediately
Quality control
We take full responsibility for making sure your parts are manufactured according to our standards
Delivery
Our 3D printing service has been rated 4.9/5
Over 261 customers are satisfied with our 3D printing service.
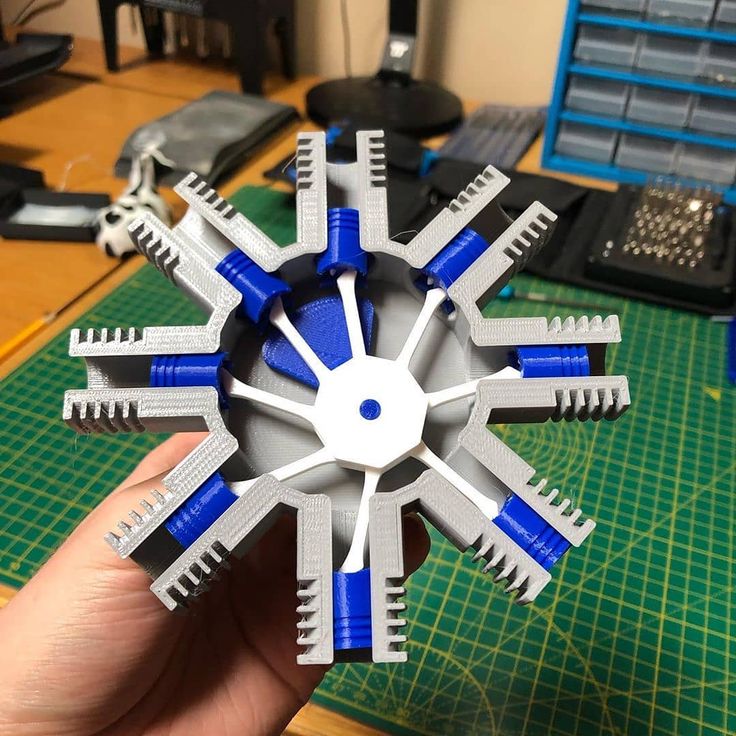
“Couldn't be happier, service and quality is brilliant.”
“Absolutely spot on! Will be using this again! ”
“This is my second order from this company and everything could not have been easier, communications were fast and the finished product was spot on. Will not hesitate to use them again.”
“Really good quality print Item arrived the day that was estimated Quick response time and really helpful/flexible”
“Speedy service, valuable advice. Excellent communication. highly recommended!”
“On time, design as expected. Many thanks!”
“Great help and solved issues fast and effect. A+”
“Very responsive and helpful, would highly recommend.”
“Great print and very speedy production and delivery.”
“Very helpful and friendly service would happily use this service provider again.”
“Thank you for the super quick service and response. ”
“The piece was perfect, exactly as I expected”
“Really quick service and I'm really pleased with the result. ”
“Excellent service and delivery even down to the care taken with the packaging. This was the first time I have used Hubs and I would highly recommend.”
“Good printer, well packaged, quick delivery. Recommended.”
“Thanks for an excellent service Felix! Very happy :)”
“Excellent service & communication. Parts quality even better than expected as well :) Couldn't be happier with the service I received :)”
“Brilliant . Many thanks Will share this with the Pebble community”
“Spot on service, really happy with the results”
“Again fantastic service and brilliant communication ”
“Very good experience. Excellent service, would certainly use again. very pleased”
“Great service, print quality and communication. Will be ordering again. ”
“The print was great quality and it shipped quickly, thanks!”
“Quality of the parts was great, good communication and prompt service. Would definitely use again for any future needs”
“I have no prior experience with 3D printed objects, but as far as I can tell this is a very clean print. The plastic is nice and flexible so it's not likely to snap under general use.”
Show more reviews
Show less reviews
Teams build better parts
Create your Hubs team and start collaborating
Read more
The Hubs Standard - consistent quality, every time
Hubs takes the stress out of manufacturing by guaranteeing the quality and consistency of every part. Each order is dimensionally and visually inspected to make sure it meets the Hubs Standard.
3D printing materials
We can generate instant 3D printing quotes for 25+ plastics. For metal 3D-printed parts, you can request a quote from our parent company, Protolabs.
Available materials
SLS
PA 12 Glass filled PA 12
Desktop FDM
Prototyping PETG Prototyping ASA Prototyping TPU Prototyping ABS Prototyping PLA
Desktop SLA
Formlabs Standard Resin Formlabs Clear Resin Formlabs Tough Resin 2000 Formlabs Rigid Resin 4000 Formlabs Grey Pro Resin Formlabs Flexible Resin 80A Formlabs High Temp Resin Formlabs Durable Resin
MJF
HP PA 12 Glass filled HP PA 12
Industrial FDM
Markforged Onyx ABSplus Stratasys ULTEM 9085 Stratasys Stratasys ASA ABS M30 Stratasys ULTEM 1010 Stratasys
Industrial SLA
Accura 25 (PP-like) Accura ClearVue Accura Xtreme White 200 (ABS-like)
3D printing locations near UK
Stoke Derby Birmingham
Manchester Sheffield Telford
Coventry Nottingham Bradford
Leeds
The 3D Printing Handbook
No one understands 3D printing like us - our founders literally wrote the book. Click here to download the sample chapters.
Buy the book from Amazon
FAQ's
How much does your 3D printing service cost?
The cost of your 3D printed parts depends on factors such as part volume, part complexity, choice of material, which 3D printing technology is used, and if any post processing is required. For more details on these cost factors, see our article on the cost of 3d printing. To check the cost of your 3D printed part, simply upload a CAD (.STL) file and select your material and 3D printing technology to receive a quote within seconds.
How do you guarantee the quality of my prints?
Your parts are made by experienced 3D printing shops within our network. All facilities are regularly audited to ensure they consistently meet the Hubs quality standard. We include a standardized inspection report with every order and offer a First Article Inspection service on orders of 100+ units.
We have partners in our network with the following certifications, available on request: ISO9001, ISO13485 and AS9100.
Follow this link to read more about our quality assurance measures.
How do I select the right 3D printing process for my prints?
You can select the right 3D printing process by examining which materials suit your need and what your use case is.
By material: if you already know which material you would like to use, selecting a 3D printing process is relatively easy, as many materials are technology specific.
By use case: once you know whether you need a functional or visual part, choosing a process is easy.
For more help, read our guide to selecting the right 3D printing process. Find out more about Fused Deposition Modeling (FDM), Selective Laser Sintering (SLS), Multi Jet Fusion (MJF) and Stereolithography (SLA).
How can I reduce the cost of my 3D prints?
In order to reduce the cost of your 3D prints you need to understand the impact certain factors have on cost. The main cost influencing factors are the material type, individual part volume, printing technology and post-processing requirements.
Once these have been decided, an easy way to further cut costs is to reduce the amount of material used. This can be done by decreasing the size of your model, hollowing it out, and eliminating the need for support structures.
To learn more, read our full guide on how to reduce the cost of 3D printing.
Where can I learn more about 3D printing?
Our knowledge base is full of in-depth design guidelines, explanations on process and surface finishes, and information on how to create and use CAD files. Our 3D printing content has been written by an expert team of engineers and technicians over the years.
See our complete engineering guide to 3D printing for a full breakdown of the different 3D printing technologies and materials. If you want even more 3D printing, then check out our acclaimed 3D printing handbook here.
We have an extensive range of online resources developed to help engineers improve their capabilities.
Introductory guides
Design guides
Material guides
Applications
CAD & file preparation
Post processing & finishing
Our other manufacturing capabilities
CNC machining
CNC machining
Milling (3-, 4- & full 5-axis), turning and post-processing
-
50+ metals and plastics & 10 surface finishes
-
Tolerances down to ±.0008” (0.020 mm)
-
Lead times from 5 business days
See our CNC machining services
Put your 3D printed parts into production today
Get an instant 3D printing quote
What is 3D printing? How does 3D printing work?
Select chapter
What is 3D printing?
3D printing and additive manufacturing
3D printing and rapid prototyping
When was 3D printing invented?
How does 3D printing work?
Additive vs traditional manufacturing
3D printing technology
The different types of 3D printing
3D printing processes
Selecting the right 3D printing processes
3D printing materials
A complete 3D printing material overview
3D printing software
What software should you use for 3D printing?
3D printing design guidelines
Design guidelines applicable for all 3D printing processes
Design guidelines for specific processes
Design guidelines for specific parts
Applications of 3D printing
Medical 3D printing
Automotive 3D printing
3D printing jewelery
What are the benefits of 3D printing?
The future of 3D printing
How to get something 3D printed
Buy a printer or use a 3D printing service?
How to decide which 3D printer to buy
How to use a 3D printing service
Further reading
The 3D printing handbook
Guides to other manufacturing technologies
What is 3D printing?
3D printing is an additive technology used to manufacture parts. It is ‘additive’ in that it doesn’t require a block of material or a mold to manufacture physical objects, it simply stacks and fuses layers of material. It’s typically fast, with low fixed setup costs, and can create more complex geometries than ‘traditional’ technologies, with an ever-expanding list of materials. It is used extensively in the engineering industry, particularly for prototyping and creating lightweight geometries.
3D printing and additive manufacturing
‘3D printing’ is commonly associated with maker culture, hobbyists and amateurs, desktop printers, accessible printing technologies like FDM and low-cost materials such as ABS and PLA (we’ll explain all those acronyms below). This is largely attributable to the democratization of 3D printing through affordable desktop machines that sprung from the RepRap movement, like the original MakerBot and Ultimaker, which also led to the explosion of 3D printing in 2009.
By contrast, additive manufacturing (AM) is almost always associated with commercial and industrial applications.
3D printing and rapid prototyping
‘Rapid prototyping’ is another phrase that’s sometimes used to refer to 3D printing technologies. This dates back to the early history of 3D printing when the technology first emerged. In the 1980s, when 3D printing techniques were first invented, they were referred to as rapid prototyping technologies because back then the technology was only suitable for prototypes, not production parts.
In recent years, 3D printing has matured into an excellent solution for many kinds of production parts, and other manufacturing technologies (like CNC machining) have become cheaper and more accessible for prototyping. So while some people still use ‘rapid prototyping’ to refer to 3D printing, the phrase is evolving to refer to all forms of very fast prototyping.
When was 3D printing invented?
3D printing began as an idea for accelerating industrial product development through faster prototyping. Even though there were a few patents beforehand, Chuck Hull is typically credited with the invention of the 3D printer via his Stereolithography Apparatus (SLA), patented in 1984.
SLA 3D Printing - What is SLA 3D printing?Foundations
Despite Chuck’s fame, multiple technologies were being developed in parallel in the late 1980s, and there were several companies founded in this period that was critical to the development of the technology.
- 1981 - the first patent for a device using UV light to cure photopolymers was awarded to Hideo Kodama in Japan. He designed it for ‘rapid prototyping’ as it was intended for making models and prototypes, but there was no interest and the patent was abandoned.
- 1984 - French inventors Alain Le Mehaute, Olivier de Witte, and Jean Claude André submitted a patent in which, like Hideo’s, UV light was used to cure photopolymers.
General Electric abandoned the patent citing a lack of significant business potential.
- 1984 - only a few weeks after Le Mehaute, American Charles ‘Chuck’ Hull filed his own patent for an ‘Apparatus for Production of Three-Dimensional Objects by Stereolithography’, thus also coining the term ‘stereolithography’ (SLA).
- 1987 - Hull invented the STL file, and in the same year founded 3D Systems.
- 1987 - American Carl Deckard filed a patent for Selective Laser Sintering (SLS), and in the same year co-founded Desktop Manufacturing (DTM) Corp. (acquired by 3D Systems in 2001).
- 1989 - American S. Scott Crump submits a patent for Fused Deposition Modeling (FDM), and in the same year founded Stratasys with his wife.
Commercialization
From the late 1980s to the early 1990s the industry underwent very rapid commercialization. The first machines were big and expensive and their makers competed for industrial prototyping contracts with mass-market manufacturers in the automotive, aerospace, health, and consumer goods industries.
- 1987 - 3D Systems released the first commercial SLA printer, the ‘SLA-1’.
- 1992 - The FDM patent was finally granted to Stratasys, which led them to release the first FDM printer, the ‘3D Modeler’.
- 1992 - DTM released the first commercial SLS printer, the ‘Sinterstation 2000’
- 1994 - German company Electro Optical Systems (EOS), founded in 1989, unveiled its ‘EOSINT M160’, the first commercial metal 3D printer
Democratization
In the early 2000s the fierce competition for profits, developments in material science, and the ending of many patents created an environment in which 3D printing finally became affordable for the masses. This was the decade that 3D printing took off in the popular imagination - manufacturing, which had always been the domain of heavy industry and big money, came to the people.
- 2005 - The open-source RepRap Project (for ‘Replicated Rapid Prototyper’) launched with the aim of creating self-replicating 3D printers capable of printing their own parts, causing popular interest in the technology to skyrocket.
- 2009 - Key FDM patents fell into the public domain and MakerBot launched their desktop 3D printer, the ‘Cupcake CNC’. It cost hundreds of dollars, not thousands, and all components were downloadable from Thingiverse, a website dedicated to the sharing of user-created digital design files.
- 2012 - Formlabs release the ‘Form 1’, the first affordable SLA printer, through a record-breaking Kickstarter campaign that raised $2.95 million in funding. They were sued by 3D Systems for patent infringement, but the case was settled in favor of Formlabs
- 2013 - Hubs launches as a peer-to-peer 3D printing service, allowing mass transactions between people buying prints and people with machines. It quickly grew to be the single biggest 3D printing platform in the world with over 50,000 printing ‘hubs’, before pivoting to focus on helping its business customers by making all forms of custom manufacturing more accessible.
- 2014 - Key SLS patents fell into the public domain, leading to a whole crop of companies making smaller and more affordable SLS printers.
Maturity
From 2018 the hype around 3D printing had largely disappeared from mass media, but interest in commercial applications for businesses of all sizes has never been higher. Today there are thousands of companies producing printers and offering all sorts of services leveraging 3D printing technology.
Learn more about the history of 3D printing
There are many articles out there, most are just fun reads. For those looking to really delve deep into history, Wikipedia and Wohler Associates are the best resources.
- Wikipedia - 3D printing
- Wohlers Report 2016 - History of Additive Manufacturing
How does 3D printing work?
Additive vs traditional manufacturing
Additive manufacturing has only been around since the 1980s, so the manufacturing methods developed before it are often referred to as traditional manufacturing. To understand the major differences between additive and traditional manufacturing, let's categorize all methods into 3 groups: additive, subtractive and formative manufacturing.
Additive manufacturing
Additive manufacturing builds up 3D objects by depositing and fusing 2D layers of material.
This method has almost no startup time or costs, making it ideal for prototyping. Parts can be made rapidly and discarded after use. Parts can also be produced in almost any geometry, which is one of the core strengths of 3D printing.
One of the biggest limitations of 3D printing is that most parts are inherently anisotropic or not fully dense, meaning they usually lack the material and mechanical properties of parts made via subtractive or formative techniques. Due to fluctuations in cooling or curing conditions, different prints of the same part are also prone to slight variations, which puts limitations on consistency and repeatability.
Subtractive manufacturing
Subtractive manufacturing, such as milling and turning, creates objects by removing (machining) material from a block of solid material that's also often referred to as a 'blank'.
Almost any material can be machined in some way, making it a widely used technique. Because of the amount of control over every aspect of the process this method is capable of producing incredibly accurate parts with high repeatability. Most designs require Computer Aided Manufacturing (CAM) to plot customized tool paths and efficient material removal, which adds setup time and costs, but for the majority of designs, it’s the most cost-effective method of production.
The major limitation of subtractive manufacturing is that the cutting tool must be able to reach all surfaces to remove material, which limits design complexity quite a lot. While machines like 5-axis machines eliminate some of these restrictions, complex parts still need to be re-orientated during the machining process, adding time and cost. Subtractive manufacturing is also a wasteful process due to the large amounts of material removed to produce the final part geometry.
Formative manufacturing
Formative manufacturing, such as injection molding and stamping, creates objects by forming or molding materials into shape with heat and/or pressure.
Formative techniques are designed to reduce the marginal cost of producing individual parts, but the creation of unique molds or machines used in the production process means setup costs are very, very high. Regardless, these techniques can produce parts in a large range of materials (both metals and plastics) with close to flawless repeatability, so for high volume production, they’re almost always the most cost-efficient.
How these methods compare
Manufacturing is complex, and there are too many dimensions for comprehensively comparing each method against all others. It is near impossible to optimize all at once for cost, speed, geometric complexity, materials, mechanical properties, surface finish, tolerances, and repeatability.
In such complex situations heuristics and rules of thumb are more valuable:
- Additive manufacturing is best for low volumes, complex designs, and when speed is essential.
- Subtractive manufacturing is best for medium volumes, simple geometries, tight tolerances, and hard materials
- Formative manufacturing is best for the high-volume production of identical parts.
Cost per part is usually the governing factor determining which manufacturing process is best. As a rough approximation the unit costs per method can be visualized like this:
Learn more about 3D printing vs CNC machining.
3D printing is becoming cheaper every year and in some instances, it is starting to compete with injection molding for cost efficiency. However it’s usually 3D printing and CNC machining that are considered interchangeable for particular jobs, so we’ve written a thorough guide comparing them side by side. Read more about 3D printing vs CNC machining.
CNC Machining vs 3D Printing - Which Do You Need?3D printing technology
With so many different 3D printing technologies on the market, it can be hard to understand the whole landscape. The International Organization for Standardization created the ISO/ASTM standard 52900 to standardize the exploding terminology around 3D printing and we’ve pulled together the most-used language into this glossary of 3D printing terms.
The different types of 3D printing
3D printers can be categorized into one of several types of processes:
- Vat Polymerization: liquid photopolymer is cured by light
- Material Extrusion: molten thermoplastic is deposited through a heated nozzle
- Powder Bed Fusion: powder particles are fused by a high-energy source
- Material Jetting: droplets of liquid photosensitive fusing agent are deposited on a powder bed and cured by light
- Binder Jetting: droplets of liquid binding agent are deposited on a bed of granulated materials, which are later sintered together
- Direct Energy Deposition: molten metal simultaneously deposited and fused
- Sheet Lamination: individual sheets of material are cut to shape and laminated together
Click here to download a high-resolution version of this poster.
3D printing processes
There are seven main 3D printing processes. Within each type of process there are unique technologies, and for every unique technology there are also many different brands selling similar printers.
Vat photopolymerization
Photopolymerization is the process of a photopolymer resin being exposed to certain wavelengths of light and becoming solid.
Stereolithography (SLA), direct light processing (DLP) and continuous direct light processing (CDLP) are additive manufacturing processes that fall under the category of vat photopolymerization. In SLA, an object is created by selectively curing a polymer resin layer-by-layer using an ultraviolet (UV) laser beam. DLP is similar to SLA but uses a digital light projector screen to flash a single image of each layer all at once. CDLP is a lot like DLP but relies on the continuous upward motion of the build plate. All vat photopolymerization processes are good for producing fine details and smooth surface finishes, making them ideal for jewelry and medical applications.
Benefits
- Smooth surface
- Fine details
- Good for prototyping of IM
Limitations
- Brittle
- Usually requires supports
- UV sensitive
- Extensive post processing required
Powder bed fusion
Powder bed fusion (PBF) technologies use a heat source to induce fusion (sintering or melting) between the particles of a plastic or metal powder one layer at a time. Selective Laser Sintering (SLS), electron beam melting (EBM) and multi jet fusion (MJF) all fall within this technology. The metal 3D printing processes selective laser melting (SLM) and direct metal laser sintering (DMLS) also use powder bed fusion to selectively bind metal powder particles.
Benefits
- Strong parts (nylon)
- Complex geometry
- Scalable (fits size)
- No support
Limitations
- Longer production time
- Higher cost (machines, material, operation)
Material extrusion
Material extrusion technologies squeeze a material through a nozzle and onto a build plate, layer by layer. Fused deposition modeling (FDM) falls under this category and is the most widely used 3D printing technology.
Benefits
- Fast
- Low cost
- Common thermoplastics
Limitations
- Rough surface finish
- Anisotropic
- Usually requires supports
- Not scalable
- Limited accuracy
Material jetting
Material jetting technologies use UV light or heat to harden photopolymers, metals or wax, building parts one layer at a time. Nano particle jetting (NPJ) and Drop-on-demand (DOD) are two other types of material jetting.
Benefits
- Realistic prototypes
- Excellent details
- High accuracy
- Smooth surface finish
Limitations
- High cost
- Brittle mechanical properties
Binder Jetting
Binder jetting uses an industrial printhead to deposit a binding adhesive agent onto thin layers of powder material. Unlike the other 3D printing technologies, binder jetting does not require heat.
Benefits
- Full-color options
- Range of materials
- No support
- No warping or shrinking
Limitations
- Low part strength
- Less accurate than material jetting
Direct energy deposition
Direct energy deposition (DED) creates 3D objects by melting powder material as it is deposited. It is mostly used with metal powders or wire and is often referred to as metal deposition. Laser engineered net shape (LENS) and Electron Beam Additive Manufacture (EBAM) also fall within this category.
Benefits
- Strong parts
- Range of materials
- Larger parts
Limitations
- High cost
- Poor surface finish
Sheet lamination
This technology stacks and laminates thin sheets of material to make parts. There are a few different types of lamination to choose from: bonding, ultrasonic welding or brazing.
Benefits
- Fast
- Low cost
- No support structures necessary
- Multi-material layers
Limitations
- Post processing is required
- Limited materials
- Finishing may vary
The whole landscape of additive manufacturing technologies can be summarized in a simple tree-diagram:
Click here to download a high-resolution version of this poster.
Our article on The Seven Official Types Of 3D Printers gives a broad overview of how each type of printer works, the materials available, the price and speed of printing, geometric properties (size, complexity & resolution), mechanical properties (accuracy, strength & surface finish) and common applications.
Looking for more in-depth information on the topic? We also wrote a handbook on 3D printing. If you’re a professional looking to truly master the key aspects of 3D printing, this book is for you.
Selecting the right 3D printing processes
Selecting the optimal 3D printing process for a particular part can be difficult as there’s often more than one suitable process but each one will produce subtle variations in cost and output. Generally there are three key aspects to consider:
- The required material properties: strength, hardness, impact strength, etc.
- The functional & visual design requirements: smooth surface, strength, heat resistance, etc.
- The capabilities of the 3D printing process: accuracy, build size, etc.
These correspond to the three most common methods for selecting the right process:
- By required material
- By required functionality or visual appearance
- By required accuracy or build size
For an in-depth look at how to use these methods read our complete guide to Selecting the right 3D printing process. The following comparison guides will also help inform your decision.
- HP MJF vs. SLS: A 3D printing technology comparison
- Industrial SLA/DLP vs. desktop SLA/DLP
- Industrial FDM vs. desktop FDM
3D printing materials
A complete 3D printing material overview
The number of available 3D printing materials grows rapidly every year as market demand for specific material and mechanical properties spurs advancements in material science. This makes it impossible to give a complete overview of all 3D printing materials, but each 3D printing process is only compatible with certain materials so there are some easy generalizations to make.
Thermoplastic and thermoset polymers are by far the most common 3D printing materials, but metals, composites and ceramics can also be 3D printed.
Another way of categorizing materials is by their properties: cheap, chemically resistant, dissolvable, flexible, durable, heat resistant, rigid, water resistant, UV resistant. Many industrial applications require durable plastics such as Nylon 12, and most hobbyist applications use either PLA or ABS, which are the most common materials used in FDM 3D printing.
For a more thorough overview of each of the main 3D printing materials see these articles.
- FDM 3D printing materials compared
- PLA vs. ABS: What's the difference?
- SLA 3D printing materials compared
- 3D printed injection molds: Materials compared
3D printing software
3D printing starts with software and there are many different programs to aid with each stage of the design and printing process, from 3D modelling, to print simulations and slicer programs.
What software should you use for 3D printing?
The two main methods of 3D modelling are ‘solid modelling’ and ‘surface modelling’, and there are different CAD software packages for each approach. Solid modelling refers to the creation of virtual objects through defining and joining 3D shapes that are usually predefined and to which refined surface details are added later. Surface modelling is similar except the designer starts with 2D surfaces and shapes them in ‘freeform’ to create 3D shapes.
Both approaches can produce exactly the same output, but solid modelling is faster for simple and non-organic shapes, whereas surface modelling is faster for more organic shapes. SolidWorks, Fusion 360 and Rhino 3D are the most popular software with professionals, and there are many free programs for amateurs.
Other useful 3D printing software include print simulation tools and file error fixers.
3D printing design guidelines
The exact best practices and rules of thumb vary between the different 3D printing technologies, but there are certain features you always need to pay attention to:
- Supported wall thickness
- Unsupported wall thickness
- Supports and overhangs
- Embossed and engraved details
- Horizontal bridges
- Holes
- Connecting or moving parts
- Escape holes
- Minimum feature size
- Minimum pin diameter
- Maximum tolerance
The process-specific design rules for each of these features are summarized in the graphic below:
Click here to download a high-resolution version of this poster.
Design guidelines applicable for all 3D printing processes
What can’t 3D printers do? Understanding and overcoming 3D printing geometry limitations What are the key design elements for 3D printing? What are supports in 3D printing? When and why do you need them? How does part orientation affect a 3D print? Practical design tips for additive manufacturing What is dimensional accuracy in 3D printing and how do you achieve it? How important is layer height for 3D printing? 3D print better parts with the right layer thicknessDesign guidelines for specific processes
How to design parts for FDM 3D printing How to design parts for SLA 3D printing How to design parts for SLS 3D printing How to design parts for material jetting 3D printing How to design parts for metal 3D printing How to design parts for binder jetting 3D printing What are the optimal shell and infill parameters for FDM 3D printing?Design guidelines for specific parts
How do you design enclosures for 3D printing? A step-by-step guide How to design living hinges for 3D printing How to design interlocking joints for fastening 3D printed parts How do you design snap-fit joints for 3D printing? How do you assemble 3D-printed parts? Practical tips on threads & screws for 3D printingApplications of 3D printing
3D printing is exceptionally useful for prototyping. Speed is everything in prototyping, and the ability to move from CAD to print with close to zero set up costs means 3D printers can produce parts fast and have great unit economics for single-part and small runs.
For printing production parts, speed and price are also important, but the characteristics most commonly exploited are design freedom and ease of customization. In aerospace and automotive, topology optimized structures with a high strength-to-weight ratio are used for high-performance parts, and components that previously required assembly can be consolidated into a single part. In healthcare, customization is critical - most hearing aids manufactured in the US are made almost exclusively using 3D printing. In manufacturing, low-run injection molds can be 3D printed from stiff, heat-resistant plastics instead of machined from metal, making them much cheaper and faster to produce.
Medical 3D printing
There are many applications for 3D printing in the medical industry, and each year doctors and scientists come up with new and creative ways to use this fast-growing technology. The speed and versatility of 3D printing makes it perfect for developing customized prosthetics and implants and patient-specific replicas of bones, organs and blood vessels. It is also used for 3D printing surgical tools, anatomical models, personalized medical equipment and a range of other life-saving innovations.
Automotive 3D printing
In the automotive industry, automakers use 3D printing to test form and fit, to experiment with aesthetic finishes and make sure that all parts operate and interact as intended. It also provides a flexible solution for the quick turnaround of jigs, fixtures and grips; creating bellows; engineering complex ducting; and rapidly manufacturing complex, lightweight mounting brackets.
3D printing jewelery
There are a few reasons that so many designers use 3D printing to create jewelry. The technology allows jewelers to produce very complex, highly customizable designs, sidestepping some of the limitations of previously popular jewelry making techniques such as CNC machining, handcrafting and lost-wax casting. Today, precious metals can be 3D printed in a variety of patterns and designs quickly and cost effectively.
To learn more about the many different applications of 3D printing, check out these articles.
- 3D printed rapid tooling
- 3D printing for grips, jigs and fixtures
- 3D printing low-run injection molds
- Producing low-cost cast metal parts using 3D printing
What are the benefits of 3D printing?
3D printing is an exceptional tool for custom parts and rapid prototyping with a unique set of advantages but also lags behind traditional manufacturing in some ways. The key benefits and limitations can be summarized as follows:
Benefits
- Very low start-up costs
- Very quick turnaround
- Large range of available materials
- Design freedom at no extra cost
- Each and every part can easily be customized
Limitations
- Less cost-competitive at higher volumes
- Limited accuracy & tolerances
- Lower strength & anisotropic material properties
- Requires post-processing & support removal
For a more thorough overview read our article about the benefits and limitations of 3D printing
The future of 3D printing
So where is 3D printing today? Is the hype over? Yes, and now the technology is reaching maturity. Hubs has been around since 2013, and we’ve produced a 3D Printing Trend Report every year since 2017. Over those years we’ve watched the technology reach the height of the hype cycle, drop through the ‘trough of disillusionment, and bounce back to where it is now - on the ‘slope of enlightenment.
The hype of the previous years was based on the idea of widespread consumer adoption. This was a misleading interpretation of where the technology could add value to the world. The most promising applications of 3D printing are in very specific roles in the world of manufacturing.
To understand where 3D printing is headed in the next few years, consult the most recent version of our annual 3D printing trend report.
- Hubs 3D Printing Trend Report - Most Recent Report
- Hubs 3D Printing Trend Report - Past Trends
How to get something 3D printed
3D printing has come a long way since its inception and it’s now very easy to get something 3D printed quickly and affordably.
Buy a printer or use a 3D printing service?
3D printing has come a long way since its inception and it’s now very easy to get something 3D printed very fast for pretty cheap.
Should you buy your own 3D printer or use an online service? It’s an important decision to make, so we’ve collected arguments for both sides to help you make the right choice.
Buy a 3D printer if… | Use an online service if… |
---|---|
You need to print regularly, but not in huge volumes (10-25 times a week) | You will need only a few (less than 10) or large volumes (25+) of parts printed per week |
You have one specific application in mind for the printer | You want to print using multiple processes and materials, including industrial printers |
You are ready to make a sizeable investment | You want to access the latest technologies at all times |
You are prepared to set up, tinker and optimize your machine | You prefer to focus your time on designing and perfecting your models |
You have the necessary space and time to install and operate the printer | You want to test and learn first before deciding what printer to buy |
How to decide which 3D printer to buy
If you’ve decided it’s a good idea to buy your own 3D printer, you may be overwhelmed by the range of choices now available. To help people make sense of the 3D printer market, we reached out to our entire customer base and our global network of 3D printing service providers to find out about the 3D printers they own and their experiences in using them.
With reviews from more than 10,000 3D printer owners, who’ve completed about 1.48 million prints on 650+ different 3D printer models, our research is the most comprehensive 3D Printer Guide available.
Read our guide to finding the best 3D printer for you.
How to use a 3D printing service
At Hubs, we’re building the smartest manufacturing solution on the planet. One of our main offerings is our 3D Printing service.
When you upload a part to our online 3D printing service our proprietary pricing algorithm gives you a quote in a matter of seconds. As you specify your requirements the price will update automatically, and if you’re happy with the price and the lead times you can submit the order in just a few minutes.
Further reading
If you have more questions about 3D printing, check out our Knowledge Base and filter on ‘3D printing’ to see everything all at once.
The 3D printing handbook
If you’re interested in diving deeper into any of the topics covered above, we literally wrote the book on 3D printing. If you’re a professional looking to truly master the key aspects of 3D printing, this book is for you. It provides practical advice on selecting the right technology and how-to design for 3D printing, based upon the first-hand experience from the industry’s leading experts.
Here’s what Tony Fadell (creator of the iPod and founder of Nest) had to say about it:
“The Handbook” will help to guide you on your own path as you look to leverage 3D printing and its potential to create your own breakthrough products, that hopefully will change the world.
Every designer and engineer should keep it close as it paves your way into new manufacturing technologies that will spur your creativity and unlock your ideas as they become reality. Creation is changing, manufacturing is changing and design is changing, turn the page, it's time to stay ahead...
If you’re ready to purchase, The 3D Printing Handbook is available on Amazon. Or, if you like, you can download the first two chapters for free first.
Guides to other manufacturing technologies
Hubs' online manufacturing service offers more than just 3D printing. We also offer CNC machining, injection molding, and sheet metal fabrication, and to try to help our customers understand all these technologies we’ve written guides similar to this one for each of them.
Learn more about other manufacturing technologies
STL File Under Desk Mount USB Hub Amazonbasics・3D Printing Design Download3D・Cults
Wander Arcane Cosplay Belt Buckle
1. 01 €
Vander Knee Pad and Arcane Cosplay Jacket Buttons
1 €
Vander's gauntlets arcane cosplay
10.78 €
Arcane Cosplay Vander Brassknuckles
1.52 €
Arcane Cosplay Claggor Goggles
2.78 €
Best 3D Printer Files in the Gadget Category
Simula 5 Robot Developers Kit
Free
Gift Card Maze Puzzle Box
4.04 €
Stereo Speaker - Kitronik
Free
HALLOWEEN Key Hanger
2 €
TACTICAL WALLET WITH CARD HOLDER
Free
GoPro Cable Dolly
Free
Smartphone Stabilizer
Free
Ercoupe Golden Age Aircraft
Free
Bestsellers in the Gadget category
Keychain application
3. 68 €
Perritos fantasma / Creepy dogs
3,30 €
Bumper DJI Avata
3 €
Dice box with mechanical rotating top
4 €
Tactical onion (TRB)
10 €
Keychain "Fussy Cauldron" - Halloween
1.89 €
WALL KEY HOLDER - EYE (FULL COLLECTION)
1,88 €
Survival pistol with arrows
6.27 €
Fantastic business card application
3.68 €
Mount for GoPro DJI AVATA
2,50 €
Case for PIXEL 7 PRO (two designs)
0,94 €
Brush rinse
2.25 €
Gato fantasma / creepy cat
3.30 €
Case for iPhone 14 PRO MAX (2 pcs)
0,94 €
G17- DD17 Frame with rails
7. 50 €
Double text illusion application
3.68 €
Do you want to support Cults?
Do you like Cults and want to help us continue our journey on our own ? Please note that we are a small team of 3 people, so it is very easy to support us in maintaining activities and creating future developments. Here are 4 solutions available to everyone:
-
AD: Disable the AdBlock banner blocker and click on our banner ads.
-
AFFILIATION: Shop online by following our affiliate links here Amazon.
-
DONATIONS: If you want, you can donate via PayPal here.
-
* INVITE FRIENDS: * Invite your friends, discover the platform and great 3D files shared by the community!
Free 3D File Hanging USB Hub・3D Printed Design Download・Cults
Rooftops Individual hanging box V2
Free
Checkers Cracker Barrel
Free
Charlie Customized Storage Box
Free
Alien3d December 2018 Ice Skating Project Base Extension/Battery Holder
Free
Stand holder 4" (100 mm)
Free
Lithophane Stand
Free
Cutting board holder/stand
Free
LED display blocker at night
Free
Best 3D Printer Files in the Gadget Category
TilK - 'Tile Sticker' key ring holders - (Updated for 2022 version)
1,28 €
boogie bomb / usb rgb led stripe version / fortnitebattle royale
free
Ben and Jerry at the Gymnasium
Free
COW FOR SD AND MICROSD CARD STORAGE.
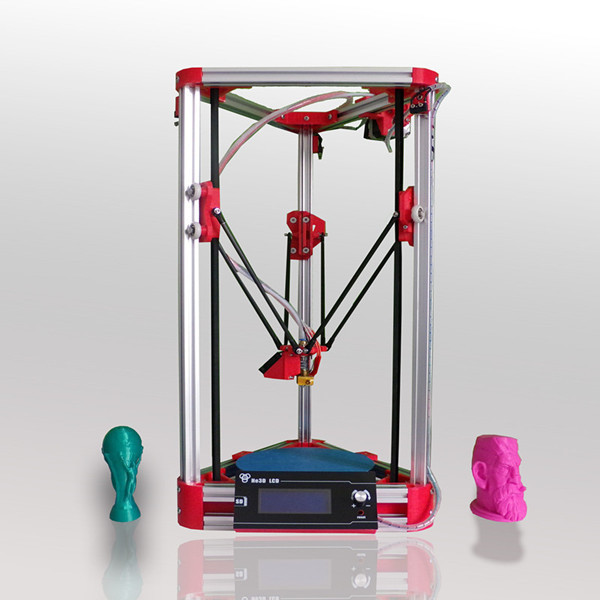
2.49 €
beer cap
Free
EDC WALLET MODULAR- (INTERCHANGABLE MODULE CLIPS)
Free
Deactivated
Bestsellers in the Gadget category
Mount for GoPro DJI AVATA
2,50 €
wall key holder (dragon ball)
1.25 €
Double text illusion application
3.68 €
Working steam engine, printed on site, fully assembled, no supports
3.34 €
AR-15 LOWER MULTI-CAL. REINFORCED DESIGN
8,50 €
Case for iPhone 14 PRO MAX (2 pcs)
0,94 €
ENGINE BLOCK - WALL KEY HANGER
1,81 €
Survival pistol with arrows
6. 27 €
Keychain application
3.68 €
Case for PIXEL 7 PRO (two designs)
0,94 €
Gato fantasma / creepy cat
3.30 €
Keychain "Fussy Cauldron" - Halloween
1.89 €
CYLINDER WALL/PISTON 2-STROKE
0,90 €
G17- DD17 Frame with rails
7.50 €
Halloween pumpkin keychain
1.89 €
Tactical onion (TRB)
10 €
Do you want to support Cults?
Do you like Cults and want to help us continue our journey on our own ? Please note that we are a small team of 3 people , so support us at maintaining the activities of and creating future developments of is very simple.