3D print filament extruder
3D Printer Filament Maker/Extruder and Recycler
Free Shipping in North America! *NEW: ProtoCycler+ Grinderless Model!* *NEW* ProtoCycler+ Grinderless Model Available Now! Free Shipping within the Continental USA and Canada on All Models!
Trusted by Researchers and Educators in the world’s largest institutions. We are Independently Certified and Globally Compliant.
Filament Extrusion
We build the best filament extrusion system on the market, against any competitor, at any price point. Our advantage stems from our patented MixFlow™ filament extrusion technology that has a thermally isolated auger, allowing for independent temperature and pressure control. This allows our system to outperform other extruders, even those that use multiple heat zones.
This all results in a far superior quality of 3D printer filament.
Our system also boasts a unique dual optical diameter feedback system, integrated cooling and spooling, and our advanced software that lets you extrude filament in autopilot.
BUY NOW
Recycle your 3D Printing Waste
Our system comes with a mechanical grinder that can shred any unneeded 3D prints, rafting or support material, and other 3D printing waste into granules that can be used to make new filament. Our system allows for compounding of plastics with a single screw. Safe for a classroom environment, and you can recycle PLA, ABS, PETG, HIPS, Nylon 12, and more!
Save your wallet, and the planet! Reduce 3D printing filament costs by 80% and recycle all your waste in the process. Whether it's your bottom line, or the planet's... ProtoCycler+ just makes sense.
DON'T REQUIRE A GRINDER? TRY PC+ GRINDERLESS
Research and Develop New Materials
The ProtoCycler+ comes with our Command Center software that tracks 20+ parameters related to filament extrusion, allowing you to experiment and create new materials for 3D printing or otherwise. Command Center is the most comprehensive filament extrusion software available.
Powered by artificial intelligence, it is able to learn and optimize new plastics, and can be safely run on autopilot. Frequent firmware updates ensure your system is always top of class, and are free for life.
Learn more
-
Superior Filament Extrusion
Our patented filament extrusion technology (MixFlow™) is 3x more efficient than the competition. And produces better quality plastic filament.
-
Advanced Control Systems
ProtoCycler+ combines a full suite of digital control systems (optical sensors, cooling and spooling, software control) for perfect filament every time.
-
Advanced Extrusion Software
We boast the most comprehensive filament extruder software. It can assist with creating new plastics or run the filament extrusion process on auto pilot.
-
Integrated Filament Spooler
Fully integrated distributed spreading and spooling system ensures your filament is neatly spooled and ready to use with any 3D printer.
learn more
BUY NOW
I was impressed at the control my team had in filament prototyping. The hardware and software were much more accessible and comprehensive than the large filament extruder we use for fiber infused PLA. It was very easy to know what parameters to change when prototyping new filaments. The data outputted by the sensors allows you to know what parameters to adjust from basic temp and speed to PID weights. We were able to prototype and extrude new filaments in a relatively short time span. We got the results we wanted. Best filament extruder for prototyping without a doubt!
I love making good quality filament with my ProtoCycler! The menu structure is easy to understand and the ability to load and create new profiles is great. Having the ability to change settings on the fly (through the software) is really useful while experimenting with new materials as changes can be made in real time.
I tried the ProtoCycler+, and it is a perfectly functional device! The filament extrusion software works great. I have nothing but praise!
Very cool tech! I have had a lot of fun being able to personally recycle my own prints and make my own filament using the ProtoCycler+
Reduce, Reuse, Recycle, Reprint
Reduce costs and eliminate waste by recycling your 3D printing filament and other wastes with the built-in grinder. With ProtoCycler+, you can 3D print sustainably, and make your filament go further.
HAVE A GRINDER? SEE PC+ GRINDERLESS
A Fully Equipped Filament Factory
Cooling fan? Check. Filament spreading and spooling system? Check. Twin diameter sensors with intelligent control? Check, check, and check!
learn more
Cutting Edge Filament Extrusion
MixFlow™ Filament Extrusion uses 3x less energy than competitors, while offering superior throughput and performance.
check out ProtoCycler+
Independently Certified. Globally Compliant.
No other filament maker/extruder is fully certified to global standards. From the classroom to the lab, we adhere to safety standards for thermal, electrical, and mechanical safety and are FCC/CE compliant. We really care about the environment, so we manufacture in full compliance with RoHS directives.
ProtoCycler+ is the safest 3D printer filament maker/extruder on the market.
learn more
buy now
Make 3D Print Materials - Desktop Filament Maker and Shredder
Innovate right from your desk
REDEFINING EXTRUSION
Filament Makers
Our Composer and Precision filament makers help you break new ground in the development, production and recycling of 3D printing materials. Find out more..
Learn More
MISSION: ZERO
Upcycling is Off To a Promising Start at Audi.
AUDI is leaping into a new era of sustainability as they create new components from plastic packaging waste. How are they doing this? Through their pilot 3D printing and upcycling project incorporating our solution.
Learn More
NEW PRODUCT LAUNCH
GP20 Shredder Hybrid.
Introducing the most innovative autonomous plastic shredder. A modular dual-part system with an intelligent interactive display, allows you to truly tailor your material settings..
Learn More
EXTREME E
Extreme E is partnering with 3devo.
The first all-electric racing to highlight the climate change challenges has just started, and we just couldn’t miss it!
Learn More
A full recycling ecosystem
From design to development and production, 3devo creates the most complete filament extrusion machines and tools. Using cutting-edge technology, and high-quality European standards, our goal is to make filament extrusion simple for everyone!
Filament Makers
Plastic Shredder
Polymer Dryer
Our Process
Customer Care
Customer care is always the first priority for us. On our online help platform, you will find video tutorials, troubleshooting steps and solutions, and everything else you may need to know about filament extrusion.
Knowledge base
Forums
Videos
Visit Help Center
Quality
3D Printing is a demanding procedure with a focus on detail and we know that. By using the highest quality standards, we make sure that you will be able to recycle your plastics for a long time.
Support
Durable
About Us
Evolution
We are never standstill. Innovation is the reason
3devo was born, thus it is always at the center
of our core values.
Innovation
Production
About Us
Materials Made Simple
Our mission is simple – to streamline the process of material research and development. How do we do this? By providing you with the best accessible features with the highest quality components. Are you ready to join the revolution in material development?
“All-in-All, the extruder is a cost-saving alternative for our 3D printing needs, as it cuts out expensive purchases and deliveries of ready-made filament.”
Svein A. Hjelmtveit
Laboratory Manager
“Navigating the menu was intuitive and the pre-set list is adequate for the first steps of processing.”
Pere Castell
Nanotechnology Manager
“As of this moment, we are extruding a new type of material weekly.”
Martin Olofsson
Laboratory Engineer
“It is a lot more flexible than our big extruder. Quick to use and doesn’t need lots of material. This device allows us to conduct most tests as part of research projects with other companies.”
Kurt van Houtte
Coordinator Fablab
“The machine is perfectly suitable for small batch extrusion in short time-frames, and allows you to immediately proceed with material testing and analysis.”
Mathias Czasny
Materials Scientist
“The Composer 450 is ideal for proceeding with immediate testing and analysis as it requires the minimum amount of input material, unlike the other extruders which require a minimum input of one kilogram.”
Corinne van Noordenne
Researcher and Lecturer
Latest Blog Posts
We're here to help
Contact Sales
Contact Sales
Portable bar extruders.
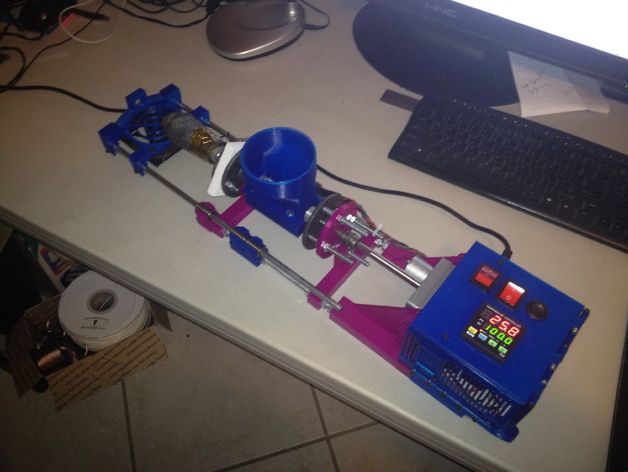
- 1 Description
- 2 Filabot Original
- 3 Filabot Wee
- 4 Filastruder
- 5 Lyman Extruder
- 6 OmniDynamics Struder
- 7 STRUdittle
- 8 Filabot Reclaimer
- 9 FilaMaker
Description
One of the limiting factors in the development of FDM printing is the relatively high cost of consumables. Although most plastics are quite affordable for an ordinary user, the difference between raw materials and finished thread is very significant - often the cost of a rod exceeds the cost of granules of the same weight by dozens of times. Thus, it is not surprising that portable, desktop devices for home production of filament from granules and plastic waste have appeared. nine0026
Extruder device
Such installations can significantly reduce the cost of printing and, of course, improve the environment. In this section, we'll take a look at some of the most well-known home rod making practices, including filament extruders and plastic waste shredders.
Filabot Original
The most well-known development with high performance. The device is designed to work with ABS, PLA and HIPS. Granulated plastic is used as a consumable, but plastic waste can also be used, provided that the particle size does not exceed 5 mm. nine0026
Filabot Original is the world's most famous device for home bar production.
The company offers a choice of seven colors of ABS granular dyes, allowing you to give the finished material the desired shade. Dyes are supplied in packs of 25g. One or two packs are required to paint one kilogram of ABS. For best results, the use of colorants with white ABS granules is recommended.
ABS, PLA and HIPS can also be blended with carbon fiber for stronger and more durable materials. To obtain such a composite, it is only necessary to mix plastic with carbon fiber granules and, if necessary, dye, and then load the finished mixture into a hopper. nine0026
Filabot Original has the highest performance of its kind. It takes about five hours to extrude one kilogram of bar. The temperature range during heating is 40°C-400°C, which allows you to experiment with a wide range of materials, including composites with wood filler, electrically conductive additives, etc.
Bar diameter can be 1.75mm or 3mm depending on nozzle. The extrusion speed is 250-750mm per minute depending on the diameter of the bar to be produced. nine0026
The auger rotates at 35 rpm. The power consumption of the device reaches 300W depending on the extrusion temperature. The extruder is equipped with a filter to remove contaminants just before extrusion.
The device is equipped with a durable metal case and has fairly compact dimensions, comparable to a computer system unit: 431x178x203mm.
Factory selling price: $899.
Filabot Wee
Filabot Wee is a more affordable option, not inferior to the Filabot Original
Version of the original Filabot extruder, equipped with a wooden body. This option is positioned as a budget version and is available both in assembled form and as a kit for self-assembly.
The budget version is slightly inferior to its more expensive counterpart in terms of performance: the extrusion speed varies from 125mm to 500mm per minute. The extrusion temperature varies from 40°C to 350°C. nine0026
The device is primarily intended for the production of HIPS, ABS and PLA rod, although other materials suitable for extrusion temperatures are also possible.
Due to the use of granular dyes, a wide range of colors can be achieved - when using dyes, the use of white ABS plastic or a material with slight color shades is recommended.
The addition of granulated carbon fiber results in a higher strength end product. Carbon fiber can be used in combination with any of the calculated plastics. nine0026
The maximum power consumption is 300W. The device comes with interchangeable nozzles that allow the production of two of the most popular bar diameters: 1. 75mm and 3mm.
Filabot Wee dimensions are similar to Filabot Original: 431x178x203mm.
Filabot has released the Filabot Wee drawings to the public. Those wishing to build an extruder with their own hands can download the necessary files here and here.
Factory selling price: $749for an assembled extruder, or $649 for a self-assembly kit.
Filastruder
A relatively inexpensive extruder designed by two University of Florida students, Tim Elmore and Allen Haynes.
Filastruder - a relatively inexpensive but very efficient extruder
Filastruder allows you to produce one kilogram of filament in 12 hours of operation of the device, or from 150mm to 600mm per minute, depending on the diameter of the nozzle, extrusion temperature and the material used. The developers tested the extruder with ABS plastic, but they allow the use of PLA, HIPS, nylon, polyethylene and other plastics. The maximum extrusion temperature reaches 225°C. nine0026
The extruder is quite economical - the maximum power consumption is 60W with an average of 50W.
Filastruder is available with 1.75 or 3mm nozzles.
Filastruder extruder sells for $300 without hopper or $310 with printed hopper.
Lyman Extruder
Lyman Extruder - a pioneer of desktop filament mills
Named after the inventor, Hugh Lyman. The original development is probably the first homemade bar extruder. It was this design that won the top prize at the Desktop Factory Competition in 2013. nine0026
The design of the extruder was simplified as much as possible, which was the result of the main condition of the competition: the total cost of the components used in the design should not exceed $250.
The Lyman extruder is not commercially available and is not available at retail. The developer posted instructions for creating an extruder in the public domain. The required files can be downloaded here.
OmniDynamics Struder
OmniDynamics Struder is designed for safety and ease of use
A compact device announced on Kickstarter in May 2014. The goal of the developers is to create a portable, convenient and safe device to use.
Delivery of the first batches of the extruder is scheduled for September 2014. The retail price of the device has yet to be announced, but the Kickstarter pre-order price is £149.
Extruder designed to work with any thermoplastic used in 3D printing, including ABS, PLA, PET, HDPE, HIPS, etc. The device is equipped with a full-fledged control module with a color LCD display. nine0026
STRUdittle
STRUdittle is a promising extruder with compact dimensions and high productivity
Another interesting development that received the necessary funding on Kickstarter.
The design of the device is aimed at high compactness and good affordability while maintaining high performance.
According to the developers, the device is capable of producing up to 600mm bars per minute. The extruder is designed to work with ABS plastic. Filament diameter deviations do not exceed 0.03 mm when using a winder or 0.05 mm if the bar is simply extruded onto the floor. Customers can specify the required nozzle diameter: 1.75mm or 3mm. nine0026
Kickstarter pre-order price is $385 for extruder with winder.
Filabot Reclaimer
The Filabot Reclaimer can handle all kinds of plastic waste
The extruders listed are designed to work with granular plastics. At the same time, FDM printers in combination with desktop extruders have great potential for recycling plastic waste into new products. Thus, to use plastic waste as consumables, a device is required that can crush plastic to obtain small particles - usually no more than 5 mm. Filabot has developed a simple yet effective shredder designed for just this purpose. The device was called the Filabot Reclaimer. nine0026
The Filabot Reclaimer is equipped with a strong welded metal frame and hardened steel serrated rollers. The device is not equipped with an electric drive - the rollers are driven manually using a lever.
Almost any thermoplastic used in 3D printing can be used as raw material.
The Filabot Reclaimer lets you recycle bad models, 3D printed waste, and just plain old plastic items. The size of the neck and, accordingly, the processed pieces of plastic reach 50x90mm. Due to the robust metal construction of the fixture, the weight of the Filabot Reclaimer is an impressive 11kg. The installation dimensions are quite modest, reaching 255x255x380mm.
The Filabot Reclaimer retail price is $439. Despite the relatively high cost, the device quickly pays for itself, allowing, together with the extruder, to save up to 90% of the cost of the bar.
FilaMaker
FilaMaker combines crusher and extruder functionality
FilaMaker combines crusher and extruder functions in one device. The machine was demonstrated at the Maker Faire Rome in 2013 and won attention due to its high functionality, neat design and high performance.
The FilaMaker is capable of producing up to one meter of 3mm thread per minute. The deviation of the given diameter does not exceed 0.05 mm. Unfortunately, the selling price of the device is quite high, reaching €1,200.
Go to the main page of the Encyclopedia of 3D Printing nine0026
3D Printer Filament Extruder
USEON offers 3D Printer Filament Extruder.
As 3D printing technology becomes more and more popular, people's demand for 3D printing consumables is also growing.
Our company has more than 15 years of rich experience in the extruder industry. We are professional in 3D printing production line.
Contents
What is 3D printer filament
3D printer filament is a thermoplastic material used in 3D printers.
There are many filaments available in different materials with different characteristics. The filament diameter of a 3D printer is usually 1.75mm and 3mm.
3D Printer Filament Raw Material
There are many raw materials for 3D printing filament. Materials that can be used in our production line: ABS, PLA, PET, HIPS, PVA, etc. mixed with dye. nine0026
Most commonly used materials: ABS, PLA.
ABS is fairly easy to print. No matter which extruder is used, the material will be extruded smoothly without fear of clogging or curing, but the post-extrusion steps are a little tricky.
This material tends to shrink when exposed to cold, partially collapse and hang in the air on the heating plate, which causes problems. In addition, if the height of the printed object is very large, sometimes the entire layer will peel off. nine0026
ABS material is suitable for making items that can be dropped, used in high temperatures or rough handling.
It can withstand the heat of a car and has the strength needed for a mobile phone protective case. But it should be noted that the best environment for ABS is a ventilated room.
PLA is a material that shrinks very little. Even an open printer can print huge objects without worrying about the finished product dangling, skewed or damaged on the board. nine0026
This material is suitable for on-site public 3D printing. PLA can also be used in outdoor projects without any problems.
PLA is a biodegradable plastic that can be recycled and degraded. It is suitable for making boxes, gifts, models and prototype parts. PLA is not suitable for placement in clothes at temperatures above 60°C, as the material deforms at this temperature.
In addition, PLA is brittle and cannot be used to make tool handles or objects subject to impact. Moreover, PLA is not suitable for making thin things, as if it is slightly bent, it will break. nine0026
Features
- Capacity: 15~20kg/h
- Thread diameter: 1.
Learn more