3D print cells
3D bioprinting of cells, tissues and organs
3D bioprinting of cells, tissues and organs
Download PDF
Download PDF
- Editorial
- Open Access
- Published:
- Madhuri Dey ORCID: orcid.org/0000-0002-9523-80831,2 &
- Ibrahim T. Ozbolat2,3,4,5
Scientific Reports volume 10, Article number: 14023 (2020) Cite this article
-
33k Accesses
-
76 Citations
-
10 Altmetric
-
Metrics details
Subjects
- Experimental models of disease
- Regeneration
- Tissue engineering
3D bioprinting has emerged as a promising new approach for fabricating complex biological constructs in the field of tissue engineering and regenerative medicine. It aims to alleviate the hurdles of conventional tissue engineering methods by precise and controlled layer-by-layer assembly of biomaterials in a desired 3D pattern. The 3D bioprinting of cells, tissues, and organs Collection at Scientific Reports brings together a myriad of studies portraying the capabilities of different bioprinting modalities. This Collection amalgamates research aimed at 3D bioprinting organs for fulfilling demands of organ shortage, cell patterning for better tissue fabrication, and building better disease models.
The discovery of a 3D printer dates back to early 1980s when Charles Hull, an American engineer, built the 1st 3D printer, capable of creating solid objects by following a computer-aided design (CAD). The printer deposited successive layers of an acrylic-based photopolymer which was then simultaneously crosslinked by UV light, thus creating a solid 3D object. This simple technology, called stereolithography (SLA), revolutionized the additive manufacturing industry. Gradually, by the late 1990s, 3D printing made its appearance in healthcare where surgeons began 3D printing dental implants, custom prosthetics, and kidney bladders. Subsequently the term ‘3D bioprinting’ emerged where the material being printed, called ‘bioink’1, consisted of living cells, biomaterials, or active biomolecules. Analogous to additive manufacturing, 3D bioprinting involves layer-by-layer deposition of bioink to create 3D structures, such as tissues and organs2.
3D bioprinting can be broadly categorized as either extrusion3, droplet4, or laser-based bioprinting. Extrusion based bioprinting employs mechanical, pneumatic or solenoid dispenser systems to deposit bioinks in a continuous form of filaments, while droplet based bioprinting relies on the generation of bioink droplets by thermal, acoustic or electrical stimulation. Laser based bioprinting utilizes laser power to 3D print structures such as in SLA by a photopolymerization principle. It can also be used for precise positioning of cells such as in laser direct-write and Laser Induced Forward Transfer (LIFT). The selection of “bioinks” for each of these different bioprinting modalities usually varies based on the ink’s rheology, viscosity, crosslinking chemistry, and biocompatibility. Extrusion based bioprinting primarily requires shear thinning bioinks while droplet or inkjet bioprinting needs materials with low viscosity. Over the past few years, the design and synthesis of bioinks has evolved to meet the increasing needs of new bioprintable materials. Significant advancements have also been made to integrate secondary techniques accompanying the above-mentioned modalities of bioprinting. For example, creating 3D structures with low viscosity bioinks has always been a challenge. To overcome this issue, such bioinks can now be extruded in a granular support bath containing yield stress hydrogels which solidify around the extruded structure and prevent it from collapsing5.
Apart from organ printing, bioprinting is also being used to fabricate in-vitro tissue models for drug screening, disease modelling, and several other in-vitro applications.
The 3D bioprinting of cells, tissues and organs Collection at Scientific Reports is dedicated to this field of research. This collection clearly portrays the diverse applications of different bioprinting modalities and how they could be utilized for improving various aspects of healthcare. Kim et al. 3D printed a novel two-layered polycaprolactone (PCL) -based tubular tracheal graft6. This tracheal graft, seeded with induced pluripotent stem cell (iPSC) -derived mesenchymal (MSCs) and chondrocyte stem cells supported the regeneration of tracheal mucosa and cartilage in a rabbit model of a segmental tracheal defect. Galarraga et al. used a norbornene-modified hyaluronic acid (NorHA) macromer as a representative bioink for cartilage tissue engineering7. Printed structures containing MSCs, on long term culture, not only led to an increase in compressive moduli, but also expressed biochemical content similar to native cartilage tissue. Vidal et al. used 3D printed customized calcium phosphate scaffolds with and without a vascular pedicle to treat large bone defects in sheep8. They used CT angioscan to scan the entire defect site and subsequently 3D print a personalized scaffold to anatomically fit the defect site. A bioink comprising decellularized matrix from mucosal and muscular layers of native esophageal tissues was used by Nam et al. to mimic the microenvironment of native esophagus9. Leucht et al. used gelatin based bioinks to study vasculogenesis in a bone-like microenvironment10. Kilian et al. used a calcium phosphate cement (CPC) and an alginate-methylcellulose based bioink containing primary chondrocytes to mimic the different layers of osteochondral tissue11.
This special issue also contains three notable research articles on the patterning of cells—two utilizing acoustics, and one, magnetism. Even though bioprinting enables the homogenous distribution of cells representing the macro-architectural properties, it lacks control of the tissue micro-architecture such as orientation of cells within the bioprinted constructs. Chansoria and Shirwaiker delved deep into the physics of ultrasound-assisted bioprinting (UAB) that utilizes the acoustophoresis principle to align MG63 cells within single and multi-layered extrusion-bioprinted alginate constructs12. Cells were aligned both orthogonally and in parallel to the printed filaments, thus mimicking cellular anisotropy in tissues such as ligaments, tendons, and cardiac muscle. Similarly, Sriphutkiat et al. used acoustic excitation to align skeletal myoblast cells (C2C12) and human umbilical vein endothelial cells (HUVECs) encapsulated in methacrylated gelatin (GelMA) bioink13. Goranov et al. magnetically labelled MSCs and HUVECs, and aligned them in a magnetic scaffold to mimic vascularization of bone constructs14.
It is important to note that the applications of 3D bioprinting are not limited to organ printing. It also holds great promise in less explored avenues, such as using scaffolds for drug delivery, studying disease mechanisms, or creating personalized medicines. In this Collection, Lee et al. 3D printed a rifampicin loaded PCL scaffold for possible treatment of osteomyelitis15. Xu and coworkers 3D printed paracetamol containing PVA tablets with three different geometries, each demonstrating different release profiles which could be tailored based on the patient's needs16. Further, Foresti et al. applied 5D additive manufacturing techniques to create personalized models of patients’ pathology17. Ding, Illsley and Chang 3D bioprinted GelMA-based models to investigate the trophoblast cell invasion phenomenon, enabling studies of key placental functions18.
Additionally, there are other notable articles in this Collection enumerating different aspects of bioprinting. Afghah et al. used a Pluronic-nanoclay based composite support bath to bioprint representative structures, for complex and hollow tissues, using cell laden alginate hydrogel19. Zhao et al. developed a 3D printed hanging drop dripper system for analyzing tumor spheroids in-situ20. Yumoto et al. performed RNA-seq analysis on inkjet-printed cells to analyze the effect of bioprinting on gene expression21. We would like to extend our utmost gratitude and thank all the authors and reviewers who devoted their time and effort towards this 3D bioprinting collection.
Even though 3D bioprinting is advancing at a commendable rate with researchers trying to develop new printing modalities as well as improve existing modalities, there still remains a multitude of challenges that need to be overcome. Currently, a limited number of bioinks exist which are both bioprintable and which accurately represent the tissue architecture needed to restore organ function post-printing. While bioinks made from naturally derived hydrogels are conducive to cell growth, synthetic hydrogels are mechanically robust. Thus, hybrid bioinks should be designed to amalgamate all these aspects. Moreover, the bioprinting process itself needs to be more cell-friendly. Shear stress applied to the cells during the printing process are detrimental to cell growth and might even alter the gene expression profiles. Stem cells, such as iPSCs, are sensitive to such physical forces and usually do not survive the printing process. As stem cell studies have mostly been performed on 2D environments, there exists a lot of unknowns for a 3D stem cell culture. Effective techniques need to be developed for high throughput generation and bioprinting of organoids22 for personalized drug testing and predictive disease models. Additionally, vascularization of bioprinted constructs for proper nutrient exchange, as well as integration of printed vasculature with host vasculature post organ implantation, is another major obstacle. Overall, 3D bioprinting is a rapidly evolving field of research with immense challenges, but tremendous potential to revolutionize modern medicine and healthcare.
References
Hospodiuk, M., Dey, M., Sosnoski, D. & Ozbolat, I. T. The bioink: a comprehensive review on bioprintable materials. Biotechnol.
Adv. 35, 217–239 (2017).
PubMed CAS Google Scholar
Ozbolat, I. T. 3D Bioprinting: Fundamentals, Principles and Applications (Elsevier Inc., Amsterdam, 2016).
Google Scholar
Ozbolat, I. T. & Hospodiuk, M. Current advances and future perspectives in extrusion-based bioprinting. Biomaterials 76, 321–343 (2016).
PubMed CAS Google Scholar
Gudapati, H., Dey, M. & Ozbolat, I. A comprehensive review on droplet-based bioprinting: past, present and future. Biomaterials 102, 20–42 (2016).
PubMed CAS Google Scholar
Heo, D. N. et al. 3D bioprinting of carbohydrazide-modified gelatin into microparticle-suspended oxidized alginate for the fabrication of complex-shaped tissue constructs.
ACS Appl. Mater. Interfaces 12, 20295–20306 (2020).
PubMed CAS Google Scholar
Kim, I. G. et al. Transplantation of a 3D-printed tracheal graft combined with iPS cell-derived MSCs and chondrocytes. Sci. Rep. 10, 1–14 (2020).
Google Scholar
Galarraga, J. H., Kwon, M. Y. & Burdick, J. A. 3D bioprinting via an in situ crosslinking technique towards engineering cartilage tissue. Sci. Rep. 9, 1–12 (2019).
Google Scholar
Vidal, L. et al. Regeneration of segmental defects in metatarsus of sheep with vascularized and customized 3D-printed calcium phosphate scaffolds. Sci. Rep. 10, 1–11 (2020).
ADS Google Scholar
Nam, H. et al. Multi-layered free-form 3D cell-printed tubular construct with decellularized inner and outer esophageal tissue-derived bioinks. Sci. Rep. 10, 1–14 (2020).
Google Scholar
Leucht, A., Volz, A. C., Rogal, J., Borchers, K. & Kluger, P. J. Advanced gelatin-based vascularization bioinks for extrusion-based bioprinting of vascularized bone equivalents. Sci. Rep. 10, 1–15 (2020).
Google Scholar
Kilian, D. et al. 3D Bioprinting of osteochondral tissue substitutes-in vitro-chondrogenesis in multi-layered mineralized constructs. Sci. Rep. https://doi.org/10.1038/s41598-020-65050-9 (2020).
Article PubMed PubMed Central Google Scholar
Chansoria, P. & Shirwaiker, R. Characterizing the process physics of ultrasound-assisted bioprinting.
Sci. Rep https://doi.org/10.1038/s41598-019-50449-w (2019).
Article PubMed PubMed Central Google Scholar
Sriphutkiat, Y., Kasetsirikul, S., Ketpun, D. & Zhou, Y. Cell alignment and accumulation using acoustic nozzle for bioprinting. Sci. Rep. 9, 1–12 (2019).
ADS CAS Google Scholar
Goranov, V. et al. 3D patterning of cells+in magnetic scaffolds for tissue engineering. Sci. Rep. https://doi.org/10.1038/s41598-020-58738-5 (2020).
Article PubMed PubMed Central Google Scholar
Lee, J. H. et al. Development of a heat labile antibiotic eluting 3D printed scaffold for the treatment of osteomyelitis. Sci. Rep. 10, 1–8 (2020).
ADS CAS Google Scholar
Xu, X., Zhao, J., Wang, M., Wang, L. & Yang, J. 3D printed polyvinyl alcohol tablets with multiple release profiles. Sci. Rep. https://doi.org/10.1038/s41598-019-48921-8 (2019).
Article PubMed PubMed Central Google Scholar
Foresti, R. et al. In-vivo vascular application via ultra-fast bioprinting for future 5D personalised nanomedicine. Sci. Rep. 10, 3205 (2020).
ADS PubMed PubMed Central CAS Google Scholar
Ding, H., Illsley, N. P. & Chang, R. C. 3D bioprinted GelMA based models for the study of trophoblast cell invasion. Sci. Rep. 9, 1–13 (2019).
Google Scholar
Afghah, F., Altunbek, M., Dikyol, C. & Koc, B. Preparation and characterization of nanoclay-hydrogel composite support-bath for bioprinting of complex structures.
Sci. Rep. 10, 1–13 (2020).
Google Scholar
Zhao, L. et al. A 3D printed hanging drop dripper for tumor spheroids analysis without recovery. Sci. Rep. 9, 1–14 (2019).
Google Scholar
Yumoto, M. et al. Evaluation of the effects of cell-dispensing using an inkjet-based bioprinter on cell integrity by RNA-seq analysis. Sci. Rep. 10, 1–10 (2020).
Google Scholar
Ayan, B. et al. Aspiration-assisted bioprinting for precise positioning of biologics. Sci. Adv. 6, eaaw5111 (2020).
ADS PubMed PubMed Central Google Scholar
Download references
Author information
Authors and Affiliations
Department of Chemistry, Penn State University, University Park, PA, 16802, USA
Madhuri Dey
The Huck Institutes of the Life Sciences, Penn State University, University Park, PA, 16802, USA
Madhuri Dey & Ibrahim T.
Ozbolat
Engineering Science and Mechanics Department, Penn State University, University Park, PA, 16802, USA
Ibrahim T. Ozbolat
Biomedical Engineering Department, Penn State University, University Park, PA, 16802, USA
Ibrahim T. Ozbolat
Materials Research Institute, Penn State University, University Park, PA, 16802, USA
Ibrahim T. Ozbolat
Authors
- Madhuri Dey
View author publications
You can also search for this author in PubMed Google Scholar
- Ibrahim T. Ozbolat
View author publications
You can also search for this author in PubMed Google Scholar
Contributions
M.D. wrote the manuscript. I.T.O. reviewed and edited the manuscript.
Corresponding author
Correspondence to Ibrahim T. Ozbolat.
Ethics declarations
Competing interests
The authors declare no competing interests.
Additional information
Publisher's note
Springer Nature remains neutral with regard to jurisdictional claims in published maps and institutional affiliations.
Rights and permissions
Open Access This article is licensed under a Creative Commons Attribution 4.0 International License, which permits use, sharing, adaptation, distribution and reproduction in any medium or format, as long as you give appropriate credit to the original author(s) and the source, provide a link to the Creative Commons license, and indicate if changes were made. The images or other third party material in this article are included in the article’s Creative Commons license, unless indicated otherwise in a credit line to the material. If material is not included in the article’s Creative Commons license and your intended use is not permitted by statutory regulation or exceeds the permitted use, you will need to obtain permission directly from the copyright holder. To view a copy of this license, visit http://creativecommons. org/licenses/by/4.0/.
Reprints and Permissions
About this article
This article is cited by
-
Hydrogel based tissue engineering and its future applications in personalized disease modeling and regenerative therapy
- Shikha Chaudhary
- Eliza Chakraborty
Beni-Suef University Journal of Basic and Applied Sciences (2022)
-
Emerging trends and prospects of electroconductive bioinks for cell-laden and functional 3D bioprinting
- Harish K.
Handral
- Vaishali P. Natu
- Wen F. Lu
Bio-Design and Manufacturing (2022)
- Harish K.
-
Additive manufacturing for biomedical applications: a review on classification, energy consumption, and its appreciable role since COVID-19 pandemic
- Mudassar Rehman
- Wang Yanen
- Jakia Sultana
Progress in Additive Manufacturing (2022)
-
Application of 3D bioprinting in the prevention and the therapy for human diseases
- Hee-Gyeong Yi
- Hyeonji Kim
- Dong-Woo Cho
Signal Transduction and Targeted Therapy (2021)
3D Bioprinting of Living Tissues
Progress in drug testing and regenerative medicine could greatly benefit from laboratory-engineered human tissues built of a variety of cell types with precise 3D architecture. But production of greater than millimeter sized human tissues has been limited by a lack of methods for building tissues with embedded life-sustaining vascular networks.
Play
In this video, the Wyss Institute and Harvard SEAS team uses a customizable 3D bioprinting method to build a thick vascularized tissue structure comprising human stem cells, collective matrix, and blood vessel endothelial cells. Their work sets the stage for advancement of tissue replacement and tissue engineering techniques. Credit: Lewis Lab, Wyss Institute at Harvard UniversityMultidisciplinary research at the Wyss Institute has led to the development of a multi-material 3D bioprinting method that generates vascularized tissues composed of living human cells that are nearly ten-fold thicker than previously engineered tissues and that can sustain their architecture and function for upwards of six weeks. The method uses a customizable, printed silicone mold to house and plumb the printed tissue on a chip. Inside this mold, a grid of larger vascular channels containing living endothelial cells in silicone ink is printed, into which a self-supporting ink containing living mesenchymal stem cells (MSCs) is layered in a separate print job. After printing, a liquid composed of fibroblasts and extracellular matrix is used to fill open regions within the construct, adding a connective tissue component that cross-links and further stabilizes the entire structure.
The resulting soft tissue structure can be immediately perfused with nutrients as well as growth and differentiation factors via a single inlet and outlet on opposite ends of the chip that connect to the vascular channel to ensure survival and maturation of the cells. In a proof-of-principle study, one centimeter thick bioprinted tissue constructs containing human bone marrow MSCs surrounded by connective tissue and supported by an artificial endothelium-lined vasculature, allowed the circulation of bone growth factors and, subsequently, the induction of bone development.
This innovative bioprinting approach can be modified to create various vascularized 3D tissues for regenerative medicine and drug testing endeavors. The Wyss team is also investigating the use of 3D bioprinting to fabricate new versions of the Institute’s organs on chips devices, which makes their manufacturing process more automated and enables development of increasingly complex microphysiological devices. This effort has resulted in the first entirely 3D-printed organ on a chip – a heart on a chip – with integrated soft strain sensors.
- 1/7 Cross section of long-term perfusion of HUVEC-lined (red) vascular network supporting HNDFladen (green) matrix.
- 2/7 Top-down view of long-term perfusion of HUVEC-lined (red) vascular network supporting HNDFladen (green) matrix.
- 3/7 Photograph cross section of printed tissue construct housed within a perfusion chamber.
- 4/7 Photograph cross section of printed tissue construct housed within a perfusion chamber.
- 5/7 Photograph of a printed tissue construct housed within a perfusion chamber.
- 6/7 Photograph of vasculature network and cell inks.
- 7/7 Photograph of 3D printed vasculature network (red) within Red is the
- Next
- Prev
Scientists plan to increase crop yields using 3D printing of plant cells
3D printing of plant cells opens up prospects for studying cellular functions
North Carolina State University study shows how 3D printing of plant cells can be bioprinted as a reproductive method study of cellular communication between different plant cells.
Plant cells are printed using a conventional 3D printer with several important design changes. Lisa Van den Broeck/North Carolina State University
A study published recently in the journal Science Advances shows that understanding how plant cells interact with each other and their environment requires understanding how they function. The knowledge gained will allow scientists to improve the quality of crops grown and create ideal conditions for their cultivation.
In their project, the scientists tried to answer several important questions. Will plant cells survive bioprinting? How long will they live? How will they change and what properties will they acquire? To find out, the researchers printed cells from a model plant, Arabidopsis thaliana, and soybeans. nine0003
"Plant roots have many different cell types with specific functions," says Lisa Van den Broek, NC State postdoctoral fellow and project leader. “In addition, there are different sets of genes that are expressed; some of them are specific to each cell. So we wanted to know what happens after living cells are bioprinted and placed in an environment that we have created: Are they alive and do they do what they are supposed to do? ".
A researcher prepares a 3D bioprinter to 3D print cells on an electrode. Ladanifer/iStock
The mechanics of bioprinting is similar to printing with paints or plastics
3D bioprinting with plant cells is similar in mechanics to printing with inks or polymers, with a few exceptions. "Instead of 3D printing with ink or plastic, "bio-ink" or living plant cells are used. The mechanics of both processes are approximately the same, with a slight difference. In the case of plant cells, an ultraviolet filter is used to maintain the sterility of the environment, as well as several print heads (instead of one) for simultaneous printing with different bio-inks," says Lisa Van den Broek, Project Manager. nine0003
Bioprinting of protoplasts (living plant cells without cell walls) was carried out using nutrients, growth hormones and agarose, a thickening agent derived from seaweed. Agarose gives stability to cells and forms "building scaffolds" much like mortar gives strength to bricks in a building wall.
"We've found it's very important to use the right scaffolds," said Ross Sozzani, professor of plant and microbial biology at NC State and co-author of the paper. "During printing, the bioink must be liquid, but at the exit it must solidify. The imitation of the natural environment helps to maintain cellular processes and mechanisms as they occur in nature. " nine0003
The cells were viable and capable of dividing
According to the study, more than half of the 3D bioprinted cells were alive and eventually split into small cell colonies, the so-called microcalli. "We expected good cell viability within a few hours of printing, but we never had to keep the cells longer, so we had no idea what would happen in a few days," Van den Broek said.
"Similar viability rates are observed after cell pipetting, so the 3D printing process does not seem to do any harm to the cells. But pipetting is a complex manual process, and 3D bioprinting controls the pressure of the droplets and the speed at which they are printed ", Sozzani said. "Bioprinting allows for increased productivity and better control of cell architecture after applying the biomaterial in layers or honeycomb structures." nine0003
The power of Arabidopsis
In addition, the researchers bioprinted individual cells to see if they could divide, grow and regenerate. The results showed that Arabidopsis root and shoot cells require various nutrients and "building scaffolds" for optimal development.
The researchers also studied the cellular composition of the bioprinted colonies. It turned out that soybean embryonic cells and Arabidopsis root cells are characterized by a high proliferation rate and the absence of a stable identity. In other words, such cells can develop into different types of cells, similar to animal or human stem cells. nine0003
recommendations
Sources: Science Advances, North Carolina State University, Eurekalert
1. (https://www.eurekalert.org/news-releases/967268)
2. (https://news.ncsu.edu/ 2022/10/3d-printing-plant-cells-shows-promise-for-studying-cell-function/)
3. (https://interestingengineering.com/science/3d-printing-plant-cells-helps-to -study-cell-function-researchers-suggest)
This content was written by a site visitor and has been rewarded. nine0003
Organ printing: how 3D bioprinting technology has advanced and what is hindering its development In research centers and hospitals around the world, advances in 3D printing and bioprinting are providing new opportunities for human treatment and scientific research.
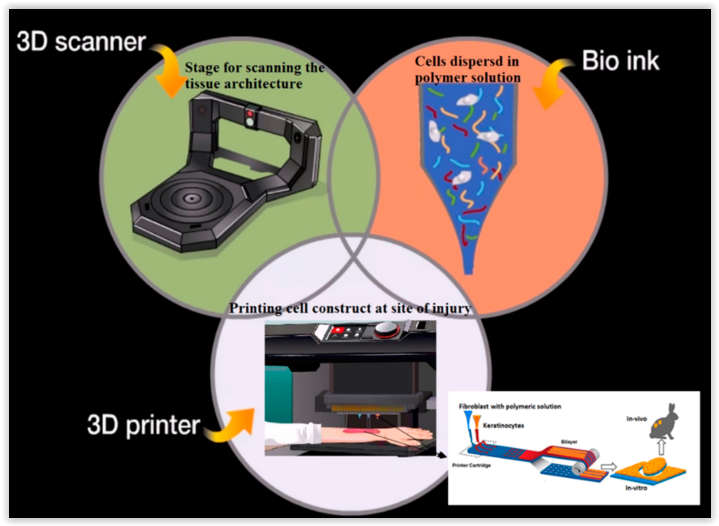
Let's talk about bioprinting technology, the latest advances in the industry and the limitations that professionals face.
How a 3D printer works
Traditional printers, like the one you have at home or office, work in two dimensions. They can print text or images on a flat surface (usually paper) using the x (horizontal) and y (vertical) dimensions. 3D printers add another dimension - depth (z). During the printing process, the printer heads can move up and down, left and right, back and forth, but instead of delivering ink to paper, they distribute various materials - polymers, metal, ceramics and even chocolate - until the "print" of a holistic, voluminous object , layer by layer in a process known as "additive manufacturing". nine0003
To create a 3D object, you need a blueprint for it, a digital file created with modeling software. After its creation, the computer-generated model is sent to the printer. Your chosen material is loaded into the machine and ready to be heated to easily flow out of the printer nozzle. As the printer reads the plan, its head moves, depositing successive layers of the selected material to create the final product.
As each layer is printed, it is solidified either by cooling or by mixing two different solutions delivered by the printer head. The new layers precisely lay down on the previous ones to make a stable, cohesive element. In this way, you can create almost any shape, including a moving one. nine0045
3D printing allows you to create objects with geometric structures that would be difficult or impossible to make in other ways. A wide range of products are already being created using 3D printers, including jewelry, clothing, toys, and high-end industrial products. Even a 10-year-old Moscow schoolboy has learned how to work with a 3D printer: he prints 3D figures to order and sells them through Instagram.
How a bioprinter works
Bioprinters work in much the same way as 3D printers, with one key difference - they deposit layers of biomaterial, which can include living cells, to create complex structures such as blood vessels or skin tissue. nine0003
Living cells? Where do they get them? Every tissue in the body is made up of different types of cells. The required cells (kidney, skin, and so on) are taken from the patient and then cultured until there are enough of them to create "bio-ink" that is loaded into the printer. This is not always possible, therefore, for some tissues, stem cells are taken that are capable of becoming any cell in the body (organism), or, for example, porcine collagen protein, seaweed and others.
Often used in bioprinting is chitosan, a polysaccharide obtained from the external skeleton of mollusks (eg shrimp) or by fermenting fungi. This material has high biocompatibility and antibacterial properties. Its disadvantage is the low rate of gelation. Another popular material is a polysaccharide isolated from seaweed called agarose. Its advantages are high stability and the possibility of non-toxic cross-linking during research. However, this biomaterial does not decompose and has poor cell adhesion (the ability of cells to stick together with each other and with other substrates). nine0003
Collagen, a primary structural protein found in the skin and other connective tissues, has a high biological significance. It is the most abundant protein in mammals and a major component of connective tissue. Its disadvantages for bioprinting include the property of acid solubility. More information about biomaterials can be found here.
Based on computer designs and models, often scans and MRIs taken directly from the patient, the printer heads place the cells exactly where they are needed and within a few hours an organic object is built from a large number of very thin layers. nine0045
Organovo bioprinter creates tissues that mimic the structure and composition of various human organs
Source: Pbs. org
Scaffolding for ear or nose replacement at Wake Forest University in Winston-Salem, North Carolina
Source: CBS News
Computer displays an image of a "scaffold" for the human ear, created in the laboratory of Wake Forest University in Winston-Salem, North Carolina
Source: CBS News
Usually more than just cells are needed, so most bioprinters also supply some kind of organic or synthetic "glue" - a soluble gel or collagen scaffold to which cells can attach and grow. This helps them form and stabilize in the correct shape. Surprisingly, some cells can take the correct position on their own without any "scaffolding". How do they know where to go? How do embryonic cells develop in the uterus, or does adult tissue move to repair damage? Same here. nine0003
Universities, researchers and private companies around the world are involved in the development of bioprinting technologies. Let's take a look at some of the amazing things they are working on.
Bioprinting in Russia
3D Bioprinting Solutions is a biotechnology research laboratory founded by medical company INVITRO. The activity of the laboratory is the development and production of bioprinters and materials in the field of three-dimensional bioprinting and scientific research. August 23, 20193D Bioprinting Solutions laboratory sent a new batch of cuvettes to the ISS to continue experiments on bioprinting in space, which began in 2018. This was reported in the press center of the laboratory. This time it is planned to use organic and inorganic components to assemble bone tissue on the world's first space bioprinter Organ.Aut.
Symposium "Biofabrication in Space"
Source: Zdrav.Expert
Organ.Aut magnetic bioprinter
Source: Zdrav.Expert
The astronauts will also grow protein crystals and experiment with printing biofilms of bacteria to study their behavior in zero gravity. Russian scientists expect to receive unique scientific data that can be applied in the development of new drugs.
Scientific director of 3D Bioprinting Solutions and leading researcher of the Institute of Regenerative Medicine, Candidate of Medical Sciences Vladimir Mironov, in his speech at the Department of Anatomy of Sechenov University on September 2, noted: “Living cells, tissues and human organs will be synthesized already in the current century. To do this, morphological sciences, such as microscopic anatomy and histology, must be digitized or digitalized, that is, digitized and made available for computer programs of robotic bioprinters, since without digital models it is impossible to print human tissues and organs.” nine0045
Bioprinting in the world
Every year, millions of people around the world need a bone transplant. Modern bone grafts often use cement-based synthetic material in combination with the patient's own bone. However, the use of these materials has a number of limitations - some transplants caused rejection and inflammatory processes in patients. Reproduction of the natural bone-cartilage "interface" has also been problematic.
However, a team at Swansea University in 2014 developed a bioprinting technology that allows the creation of an artificial bone prosthesis in the exact shape of the desired bone, using a biocompatible material that is both durable and regenerative. At the same time, scientists from the University of Nottingham in England were working on similar studies. nine0003
It takes about two hours to print a small bone. Therefore, surgeons can do it right in the operating room. This part of the bone is then covered with adult stem cells that can develop into almost any other type of cell. This is combined with bio-ink from the printer, a combination of polylactic acid (which provides mechanical strength to bone) and alginate, a gel-like substance that serves as a shock-absorbing material for cells. The end product is then implanted into the body, where it will completely disappear within about three months and be replaced by new bone. nine0003
Researchers hope that in the future, bioprinted bones can be created with sufficient reliability to support complex spinal reconstruction, and that the bone material will be further improved to increase its compatibility with cartilage cells.
Source: ETH Zurich
Successful 3D printing of human cartilage may soon completely replace artificial implants for people in need of reconstructive surgery. Back in 2015, scientists in Zurich developed technology that would allow hospitals to print a full-size human nose implant in less than 20 minutes. They believe that any cartilage implant can be made using their technique. nine0003
Researcher Matti Kesti described the technology as follows:
“
“A serious car accident can cause the driver or passenger to suffer complex nose injuries. The nose can be restored by creating a 3D model on a computer. At the same time, a biopsy of the patient is performed and cartilage cells are removed from the victim's body, such as from a knee, a finger, an ear, or fragments of a broken nose. The cells are spawned in the laboratory and mixed with the biopolymer. From this suspension, a model of nasal cartilage is created using a bioprinter, which is implanted into the patient during surgery. In the process, the biopolymer is used simply as a mold. It is subsequently broken down by the body's own cartilage cells. And in a couple of months it will be impossible to distinguish between the graft and the person’s own nasal cartilage.” nine0003
Matti Kesti
Since the implant was grown from the body's own cells, the risk of rejection will be much lower than for an implant made of, say, silicone. An additional advantage is that the bioimplant grows with the patient, which is especially important for children and young people.
If a person is severely burned, healthy skin can be taken from another part of the body and used to cover the affected area. Sometimes intact skin is missing. nine0003
Researchers at Wake Forest School of Medicine have successfully designed, built and tested a printer that can print skin cells directly onto a burn wound. The scanner very accurately determines the size and depth of damage. This information is sent to a printer and skin is printed to cover the wound. Unlike traditional skin grafts, it only takes a patch of skin one-tenth the size of a burn to grow enough cells to print. While this technology is still in the experimental stage, the researchers hope that it will be widely available within the next five years. nine0003
As already mentioned, 3D printers print products in layers, and since the skin is a multi-layered organ with different types of cells, it is well suited for this type of technology. However, researchers still have a lot of problems to solve, in particular, how to prevent damage to cells from the heat generated by the printer. And of course, like most parts of the human body, the skin is more complex than it first appears—there are nerve endings, blood vessels, and a host of other aspects to consider. nine0045
Blood vessels
Biomechanical engineer Monica Moya holding a Petri dish with printed alginate-based biotubes. Biotubes can act as temporary blood vessels similar to blood vessels that help create a patch of living tissue.
Source: embodi3D
With tens of thousands of miles of veins, arteries and capillaries in the human body, researchers are working to replace them if they ever wear out. The creation of viable blood vessels is also essential for the proper functioning of all other potential bioprinted body parts. nine0003
Biomechanical Engineer Monica Moya of Livermore National Laboratory. Lawrence uses bioprinting to create blood vessels. The materials created by her bioprinters are engineered to allow small blood vessels to develop on their own.
This development takes time, so vials of cells and other biomaterials are printed to help deliver vital nutrients to the printed environment. After a while, self-assembled capillaries connect with bioprinted tubes and begin to deliver nutrients to cells on their own, mimicking the work of these structures in the human body. nine0045
Internal organs
Many researchers hope that in 20 years the lists of patients waiting for organ transplants will become a thing of the past. They envision a world where any organ can be printed and transplanted in just a few hours, without rejection or complications, because these organs will be created from body cells according to the individual characteristics of each patient. Currently, bioprinting of fully functional complex internal organs is not possible, but research is ongoing (and not without success). nine0045
Bladder
For example, the bladder is already printed. In 2013, at Wake Forest University in the US, researchers successfully took cells from a patient's original, poorly functioning bladder, cultured them, and added additional nutrients. The 3D shape of the patient's bladder was then printed and the cultured cells soaked through it. The form was placed in an incubator and, when it reached the desired condition, it was transplanted into the patient's body. The mold will eventually collapse, leaving only the organic material. The same team successfully created viable urethras. nine0045
Physicians and scientists at the Wake Forest Institute for Regenerative Medicine (WFIRM) were the first in the world to create laboratory-grown organs and tissues that were successfully transplanted into humans. Right now they are working on growing tissues and organs for more than 30 different areas of the body, from the kidneys and trachea to cartilage and lungs. They also aim to accelerate the availability of these treatments to patients.
Scientists in Australia are doing similar research as well. They used human stem cells to grow a kidney organ that contains all the necessary cell types for a kidney. Such cells can serve as a valuable initial source for bioprinting more complex kidney structures. nine0045
MD, Professor of Urology, Professor of the Institute of Regenerative Medicine Anthony Atala shows a kidney created by a bioprinter. A modified desktop inkjet printer sprays cells instead of ink. The cells were cultured from the patient and the structural template for the kidney was obtained from the MRI (so it is the correct size and shape).
Using this technology, back in 2001, Atala printed and successfully transplanted a bladder into a young man, Jake.
Source: TedEd
Heart
Heart cells, laboratory-grown organelles. Source
Surprisingly, it is the human heart that can become one of the easiest organs to print, since, in fact, it is a pump with tubes. Of course, everything is not so simple, but many researchers believe that humanity will learn to print hearts before kidneys or liver.
Researchers at the Wake Forest Institute for Regenerative Medicine in April 2015 created "organoids" - 3D printed fully functional, beating heart cells. nine0045
In April 2019, Israeli scientists printed the world's first 3D heart. It is still very small, the size of a cherry, but it is able to perform its functions. The 3D heart with blood vessels uses personalized "ink" of collagen, a protein that supports cell structures, and other biological molecules.
A Tel Aviv University researcher holds the world's first 3D printed heart on April 15, 2019.
Source: Haaretz
“This is the first time anyone anywhere has successfully designed and printed a whole heart with cells, blood vessels, ventricles and chambers,” said Tel Aviv University scientist Professor Tal Dvir.
So far, scientists have been able to print tissue from cartilage and the aortic valve, for example, but the challenge has been to create tissue with vascularity—the blood vessels, including capillaries, without which organs cannot survive, let alone function. nine0003
The Tel Aviv scientists started with human adipose tissue and separated the cellular and non-cellular components. They then reprogrammed the cells to become undifferentiated stem cells, which could then become cardiac or endothelial. Endothelium - a single layer of flat cells lining the inner surface of the heart cavities, blood and lymphatic vessels. Endothelial cells perform many functions of the vascular system, such as controlling blood pressure, regulating the components of blood clotting, and the formation of new blood vessels. nine0003
Non-cellular materials, including a large amount of proteins, were processed into a "personalized hydrogel" that served as "printing ink".
It will be years before this technology can create organs for efficient transplantation. However, the achievements of scientists in Tel Aviv are a huge milestone along the way.
Medical research and pharmacology
One of the key potential uses for bioprinted living materials is in medical and drug research. Bioprinted tissues have several cell types with different densities and key architectural features. This allows researchers to study the impact of various diseases on the body, the stages of disease progression and possible treatments in the natural microenvironment. nine0003
One of the most impressive developments in recent years is the development of a desktop brain at the ARC Center of Excellence in 2016. The researchers were able to use a 3D printer to create a 3D printed six-layer structure that includes nerve cells that mimic the structure of brain tissue.
This opens up huge potential benefits for researchers, pharmaceuticals and private companies, because it will allow them to test new products and drugs on tissue that accurately reflects the responses of human brain tissue, as opposed to animal samples, which may cause a completely different response. The desktop brain can also be used to further investigate diseases such as schizophrenia or Alzheimer's. nine0003
We are far from printing the brain, but the ability to arrange cells to form neural networks is a significant step forward. By allowing researchers to work with human tissue in real time, testing processes can be greatly accelerated and results can be more realistic and accurate. It will also reduce the need to use laboratory animals for medical tests and potentially dangerous human testing.
Medical simulators and data registries
Source: Simbionix
Around 3,000 medical simulators are currently in use around the world to help doctors practice complex procedures. Virtual blood vessels, 3D printed organs... and no animal suffers!
The American company 3D Systems created an industry segment called VSP (Virtual Surgical Planning). This approach to personalized surgery combines expertise in medical imaging, surgical simulation and 3D printing. Surgeons using the Simbionix medical simulator for the first time often report feeling physical pain while empathizing with their virtual patient - the experience is so realistic. Organs and tissues look completely real. When stitching an organ, the surgeon sees on the screen a needle that enters the tissue, and pulls the thread. If the doctor does something wrong, the virtual blood vessels break and the organ begins to bleed. These simulators were developed by the Israeli company Symbionix, which was acquired by 3D Systems in 2014. nine0003
On September 3, 2019, the Radiology Society of North America (RSNA) and the American College of Radiology (ACR) announced the launch of a new 3D Medical Printing Clinical Data Registry to collect data on treatment outcomes using 3D printing at the point of care. This information will be a powerful tool to assess and improve patient care in real time, drive ongoing research and development, and inform patients and healthcare professionals about the best course of care. nine0045
“
“The establishment of a joint RSNA-ACR 3D printing registry is essential to the advancement of clinical 3D printing. The registry will collect data to support the appropriate use of this technology and its implications for clinical decision making.”
William Widock, Professor of Radiology at the University of Michigan and Chairman of the RSNA 3D Printing Special Interest Group (SIG)
According to RSNA, the information in the registry will allow for the necessary analysis to demonstrate the clinical value of 3D printing. Due to the wide variety of clinical indications, different technologies for creating physical models from medical images, and the complexity of the models, it is problematic to choose the optimal treatment method. The registry will help solve this problem. nine0045
Bioprinting software
Bioprinter and bioprinting software manufacturer Allevi introduced Allevi Bioprint Pro software on September 5, 2019. Built-in model generation and integrated slicing will allow you to focus more on experimenting, rather than setting up the printer. The program runs entirely in the cloud, which means you can create your biostructures, define materials, and track prints right from a web browser on any computer. nine0003
According to the development team, the new bioprinter with the above software is powerful and easy to use and represents another piece of the puzzle on the way to 3D printed organs.
At the same time, the first company in the bio-ink segment, CELLINK, announced the launch of a new product designed to be the most flexible bio-printing platform on the market. The BIO X6 bioprinter, which has no analogues at the moment, has the ability to combine more bioprinting materials, cells and tools. nine0045
Why is this taking so long?
Complex structure of the body
The human body and its various components are much more complex than a plastic toy. The human organ has a complex network of cells, tissues, nerves, and structures that must be arranged in specific ways to function properly. From placing thousands of tiny capillaries in the liver to actually getting a printed heart that "beats" and contracts in the human body, there is still a lot of research and testing. nine0003
Legal regulation
In addition, bioprinting technologies, like all new medical treatments, must pass safety tests and due process of regulation before they become available.
Special software and hardware
It also takes time to develop special software and hardware. These programs can be written only with the appropriate data (medical, clinical, statistical, mathematical, and so on), which someone must first collect, analyze, systematize and digitize. nine0045
Working through all of these steps requires the integration of technologies from various fields, including engineering, biomaterials science, cell biology, physics, mathematics and medicine. So we need to be a little more patient.
The main thing is to know that those who work in the field, doctors and engineers, programmers and scientists are making progress every day both in bioprinting technology itself and in understanding how it can be used and improved. Although we are not quite there yet, there is no doubt that medicine will be very different in 10-20 years, thanks also to bioprinting. nine0045
In brief
Bioprinting is an extension of traditional 3D printing.
Bioprinting can produce living tissue, bones, blood vessels, and possibly entire organs for use in medical procedures, medical training, and testing.
The cellular complexity of a living organism has made 3D bioprinting slower to develop than conventional 3D printing.