3D metal printing australia
Metal 3D Printing in Australia | Metal Print
Well, you can find us right here! We are Amiga Engineering, an SME operating across Australia with over 33 years’ worth of experience in our industry. Since our inception, we have poured our passion and skills into our work, growing rapidly every year and becoming an award-winning and accredited engineering company that our customers rely on to deliver high-quality with reliable customer service. So, if you’re looking for a 3D metal printing company based right here in Australia that you can rely on, look no further than Amiga Engineering! Read More
How Does 3D Metal Printing Work?
Whilst 3D metal printing can be a difficult process to understand if it is your first time with the process, it can be beneficial to know the basics in order to know more about your products and where they come from. Therefore, we have broken down some of the basic things for you to be aware of right here.
You may have heard some common Acronyms for the 3d Metal Printing or Powder Bed Fusion process like SLM (Selective laser Melting) or DMLS (Direct Metal Laser Sintering), but in essence the processes are the same with each technology company making a variety of tweaks to the technology, for different outcomes and improvements. These processes can melt many different types of metal powders together in a laminar way, fully melting the layers of the respective metal material together with a laser temperature and focus and speed that is designed for that specific alloy, this is carried out in an inert build chamber environment to minimize oxygen and therefore inhibit porosity and enhance strength and enable detailed prints.
We use a Powder Bed Fusion or DMLS system called DMP (Direct Metal Printing) a 3D Systems Technology, as it creates a lower chamber oxygen concentration leading to best possible industry leading mechanical characteristics.
The process can be broken down into 4 simple steps.
Firstly, in order to counteract any oxidisation of the metals that may occur, the chamber in which the part will be built is filled with an inert gas. We then spread a thin layer of the metal powder over a platform, which is then melted by a high-power laser moving cross-sectionally, ultimately fusing the particles and creating the first layer. Then, the process repeats, with each layer being built on until the part is fully realised. Finally, the 3D printed metal parts will be encased in the metal powder until they cool to room temperature, at which point the unmelted excess powder is removed and the parts will be sent off for use or further processing. The type of metal used will vary depending on the desired part.
Why Choose 3D Metal Printing From Amiga Engineering
Having worked with businesses and organisations in aerospace, medicine, defence, and many other sectors of the economy, we know exactly what it takes to tailor our products and services to the specific needs and preferences of individual customers. Just as no two clients are exactly the same, so no two solutions are exactly the same – and we work closely with our customers to gain a comprehensive understanding of exactly what it is they’re looking for, before setting to work with the task of coming up with the designs that meet their individual needs.
Then, we use some of the most specialist equipment for metal 3D printing in Australia to turn these designs into realities. Using sophisticated additive manufacturing processes, we’re able to create complex, lightweight designs that nonetheless maintain their strength and integrity, making our products highly versatile and perfect for a wide range of practical applications. Furthermore, because we only ever use the very best materials available, our products are renowned for their superior longevity, meaning our customers can always be sure that they’ll be reaping the rewards of their new investments not only in the short term, but for many years to come also.
Place Your Metal Print Order Today At Amiga Engineering
If you’d like to find out more information about DMP metal pricing or about any of the products we sell or 3D printing services we offer, feel free to get in touch with a member of our professional team. You can either call us, send us an email or use the convenient online form available here on our website, and a member of staff will be more than happy to answer any questions you have about the metal printing in Australia.
Get in touch with us today!
If you have any more questions about the Metal 3D printing process or would like to get started with your project for your Australia-based business, then we would love to hear from you! You can get in touch with us by calling us on 1300 361 989 or by filling out the contact form on our website. We look forward to hearing from you soon. Read Less
About – SPEE3D
Board Chairman
Grant Anderson – FAICD, FAMI - CPM
Grant has had extensive Board experience across multiple industries and countries in both listed and private companies. Currently the Executive Director of the Industry Capability Network Victoria, he is also a Non-Executive Director of Sutton Tools Pty Ltd, Fast Bricks Robotics (ASX:FBR) and SPEE3D. In addition, he has experience on the Boards of Berklee Limited (Deputy Chairman), Techni Waterjet Pty Ltd (Chairman) and a number of joint venture companies in multiple countries.
With over 40 years of experience in the design and manufacturing sectors Grant has driven export growth at the level of executive, CEO and Managing Director for a number of public and private international companies and as the CEO/Managing Director in Australian based global technology businesses. The most recent role was as the CEO of the ANCA Group, a world-leading Australian manufacturer of Machine Tools, Motion Control Systems and metal fabrication. ANCA exported around 99% of its product and under Grant’s leadership the group have tripled their sales since his appointment in 2010. Other companies Grant has led include PBR International, Schefenacker (now SMR), Britax International and MHG Plastics.
Non-Executive Director
Kerri Lee Sinclair
Kerri Lee Sinclair brings more than 20 years of management and investor experience in the high-growth technology sector. She has spent the last 5 years working in family offices building direct private investment assets in technology, and now manages over $100m of invested capital in some of Australia’s most interesting scale ups.
Previous to this, Kerri Lee worked at Aconex, the world’s most widely-used cloud collaboration platform for construction, infrastructure, energy and resources projects. A member of the Aconex leadership team, she was responsible for developing new products that tested emerging market strategies developed internally or through acquisition and integration. Her 8 years at Aconex also included several key operational roles like 5 years as GM of Asia & India where she helped develop key international assets. Before Aconex, she had strategy, market development and growth roles at Telstra Wholesale, Intelematics, Looksmart and her own startup which was sold to Microsoft in 2007. She is Non-Executive Director for three other scale ups, sits on Investment Committee / Advisory Boards for two Government boards and is a founding Board member and Chair of SBE Australia, a NFP which supports women-led companies in building high-growth global expansion in technology and life sciences.
Independent Director
Dr.
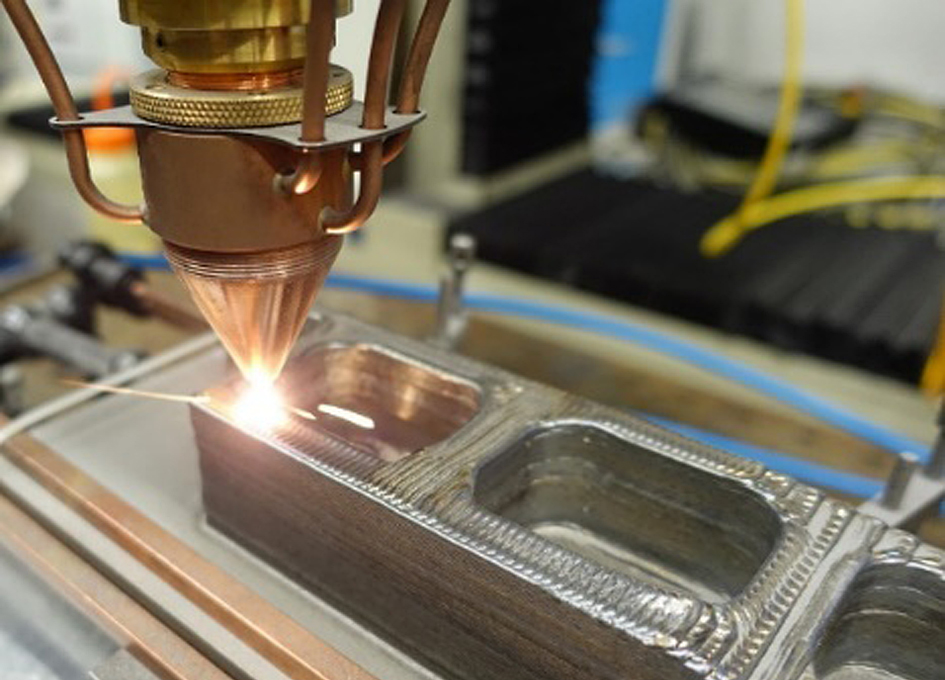
Combining years of experience in finance, sales and technology, Dr. Stephan Beyer today works as serial entrepreneur and founder in the field of innovation and digital manufacturing. Stephan is supporting leading technology companies as a trusted advisor to the C-suite. Additionally, he serves as non-executive board director for high-growth companies.
An entrepreneur at heart, he was in his last role among the founders of BigRep in 2014 and has been a driving force behind the strategic development and global expansion of the company. Prior roles of Stephan include various executive positions in the venture capital and start-up finance business where he realized a total of ten exits from the B2B, software, deep tech and medtech sectors to corporations such as Bosch, Siemens, Panasonic and an IPO. A fully trained engineer, Stephan obtained a doctorate degree in finance from the Technical University of Berlin.
Board Members
Grant Anderson – FAICD, FAMI - CPM
Kerri Lee Sinclair
Dr.
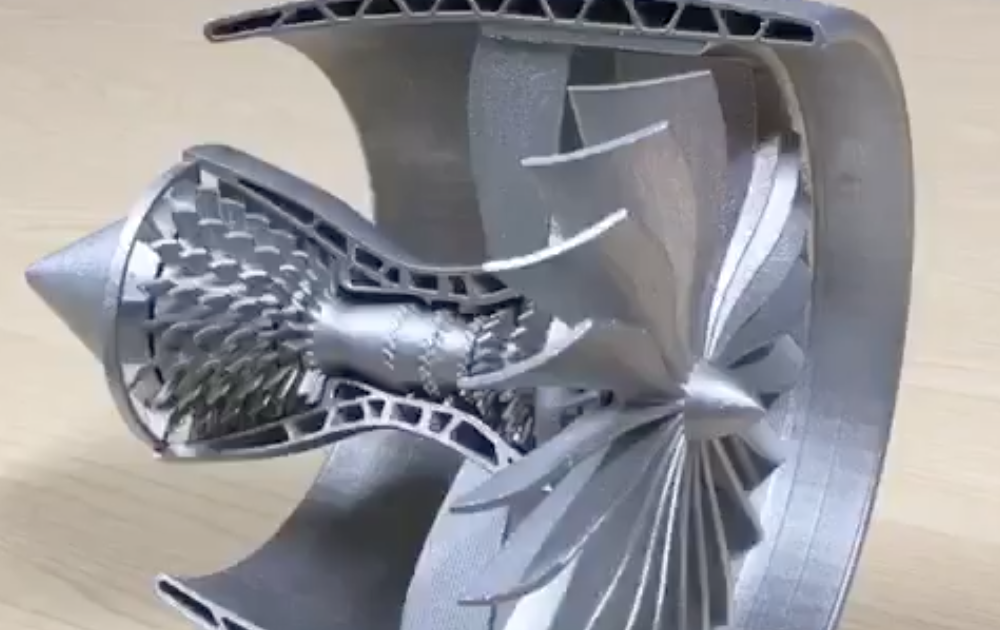
Dan Webster - CSC
Byron Kennedy - CEO, SPEE3D
Steven Camilleri - CTO, SPEE3D
AUSTRALIAN ARMY SUCCESSFULLY FIELD TESTED SPEE3D METAL 3D PRINTER
You are here
Home
A THREE-DAY TEST WAS HELD AT DIFFERENT POINTS IN THE AUSTRALIAN NORTHERN TERRITORIES AND DEMONSTRATED THE EFFICIENCY OF THE SPEE3D WARPSPEE3D 3D PRINTER FOR METAL PRINTING.
Testing has proven that additive systems can be deployed in challenging environments within 30 minutes and provide the capability to repair damaged equipment during missions. nine0005
These tests are the result of a series of investments made by the Australian military in 3D printing technology since 2014. In February 2019, the Royal Australian Navy commissioned a A$1.5 million ($1 million) project in which SPEE3D collaborated with the Advanced Manufacturing Alliance (AMA) and Charles Darwin University (CDU). This two-year government-supported program has effectively become a pilot test of SPEE3D metal 3D printing technology to optimize the maintenance of patrol boats. nine0005
A year later, in February 2020, Melissa Price, the Australian Defense Industries Minister, announced that SPEE3D had received another A$1.5 million project. The 12-month program began with twenty soldiers trained in advanced additive technology at the CDU. Now that the first phase of testing has been deemed a success, the soldiers have tried to use their knowledge to operate the SPEE3D printer in the harsh environment of Australia's Northern Territories. nine0005
In early June, military personnel installed a WARPSPEE3D metal 3D printer at Robertson Barracks in Darwin. A little over a week later, soldiers from the 1st Combat Support Battalion packed and trucked the printer into the bush. Three days of testing at the Mount Bundey field training area, located 120 km southeast of Darwin, involved moving the system to new positions in the bush and deploying it in various types of terrain. Not only has the 3D printer been proven to be able to be transported and installed in difficult environments, but it is also reported to be up and running within 30 minutes. nine0005
The SPEE3D system uses a patented Cold Spray technology to produce metal parts weighing up to 40 kg at a speed of 100 grams per minute. The mobility demonstrated by the additive system during the course of the project allowed soldiers to print the necessary parts and spare parts as needed, rather than carrying them with them during exercises.
Source
nine0002 Other materials:
- Bayer will test new drugs on a 3D model of the heart
- "3Dtoday" online 3D modeling class
- Chevy built an almost completely 3D printed Corvette C8
- Thermwood built a 51-ton metalworking system to produce giant 3D LSAM printers
- Rize offers a desktop 3D printer for printing with composite filaments
Attention! nine0068 We accept news, articles or press releases
with links and images. [email protected]
3D printing research center opens in Australia
Australia's economy is poised to take off, especially in the manufacturing sector. Already, one can observe the active introduction of innovations for a more rational use of natural resources and research potential. nine0005
On November 19, 2014, a new research center opened in Melbourne, which will focus mainly on 3D printing and its applications in various industries. The organization, which cost AU$9 million to set up, was named the Research Center for Reforming Australia's Industry Through Innovative 3D Printing Technologies (under the auspices of ARC, the Australian Research Council). The center brings together specialists in various fields, both academic and industrial, and will be headed by Professor Xinhua Wu. Funding for the center was provided jointly by ARC and its industry partners and will be located at Monash University. nine0005
Professor Wu teaches in the Department of Materials Science at Monash University, where she focuses primarily on aerospace and light metal properties. She came to Australia specifically to lead the open ARC Center for the Development of Light Metals. This organization includes more than a hundred researchers from six universities working on joint projects. Professor Wu's main priority in Australia is natural titanium deposits, which, in her opinion, contain the potential for the development of the country's aerospace industry in the face of international competition. nine0005
“Australia produces the largest amount of titanium ore in the world. It would seem, why, instead of exporting raw materials, we cannot produce something from this ore? To achieve this, local producers and consumers are needed to create demand for this material, explains the professor. – The only factor that can contribute to this is the development of innovative industries or the development of new materials. People do not understand that the aerospace industry is very dependent on technological development. This is not just the production of metal parts, it is always competition and the introduction of lighter, cheaper and better materials.” nine0005
Research at the new center will focus mainly on the creation of parts from powdered metal alloys using selective laser sintering (Selective Laser Sintering, SLS). This is consistent with Professor Wu's statement about the need to use Australian titanium ore for the development of the aerospace industry. 3D printing technologies have already proven their promise for use in this area. In particular, Professor Wu created a small jet engine using a 3D printer. nine0005
Australian MP Tony Smith and ARC Chairman Professor Aidan Byrne attended the opening ceremony of the research centre. In addition to Monash University, the center's partners include Deakin University, the University of Queensland, the Australian Nuclear Research Organization, as well as Safran-Microturbo, Metallica Minerals, A.