Watch 3d printer
Watch best 3D printing files・Cults
Wednesday - Thing,hand apple watch charger Diorama
€18 -80% €3.60
THING ADDAMS PACK
€4.87
Buckle for Swatch Watch
Free
Undulated iced diamond rectangular top signet US size 7 8 9 3D print model
€5.70
Manila cathedral tower 3d model
€1.50
Aloha Tower in Oahu Hawaii
€1.50
WATCH SUPPORT
Free
quietly watch your cat
Free
Time & Tide Pocket Watch
Free
Natural Apple Watch Stand
Free
Mi Band 6 Charger
Free
Samsung Watch Wall Mounted Charging Dock Stand
€2. 91
Chamber's Watch
€11.39
3135 Rolex movement holder
€0.62
The Watcher
€5.76
Undulated diamond open rectangular top ring US sizes 6to9 3D print model
€5.70
Nozzle Fiat Uno Fire
€1.67
The Thing - Charger Stand for Airpod and Apple Watch
€14.24
Diamond undulated fluted rectangular top signet Us sizes 6to9 3D print model
€7.59
Support Game & Watch
Free
Game & Watch stand for IKEA MÅLERÅS shelves
Free
Game & Watch Mario stand for IKEA MÅLERÅS shelves
Free
Model of a pendulum clock from the 1350s
€9. -5% €8.97 44
Undulated fluted rectangular top signet ring US sizes 6to9 3D print model
€5.70
iPhone Stand Cupholder BMW F30 F31
Free
Overwatch - Zenyatta
€5.82 -20% €4.65
Mjolnir phone / smart watch charging station viking style
€4.10
Uhr Schlaufe Fossil Hybrid Watch
€0.50
Undulated diamond rectangular signet US sizes 6to9 3D print model
€5.70
SOLAR CLOCK
€0.95
Loading Station holder for LG G Watch R
Free
Game & Watch Symbol Coaster
€0. 95
Apple Watch Band Holder
€1.19
Fluted rectangular top signet ring US sizes 6to10 3D print model
€5.70
Apple Watch Stand
Free
Wall Mount for Apple Watch 20W USB-C Charger
€3
Single shaft Tourbillon 3D PRINT 3D print
€28
PebbleTime Dock
Free
PebbleTime Short Dock
Free
Apple Watch Band Holder Organizer "Band Carousel" to store 12 Apple Watch Straps
€8.99 -50% €4.49
Casio F91W Watch Case, high precision model
€12. 80
Apple Watch Stand
Free
SAMSUNG GALAXY WATCH STAND
€1.03
Submariner Date - Rolex
€3.75
Pocketwatch stand
Free
Minimal Apple Watch charging stand
Free
Universal Smartwatch Dock - Apple, Google, Samsung, Amazfit etc.
Free
Zelda Game and Watch Stand
€2.37
Wristwatch best 3D printing models・Cults
Flexible Watch Band Straps with Tang Buckle for Casio or Similar
Free
Strap Adapter for Casio W96H to NATO 20mm
€2.50
Articulated Garmin Fenix 3/5x/6x 26mm wristband/watchband
Free
Watch and Ring stand with built in container
€1. 25
Angel Clockwork Wall Art 2 versions
€17.46
Angel Clockwork Wall Art 2
€13.96
Nato Strap Adapter for Casio DBC32 to Nato 24mm
€1
Mechanical Wrist Watch (2)
Free
SONY SmartWatch 3 SWR50 bracket
€7.30
Wrist watch
€4.99
Wrist watch rolex
€3.99
Bezel for Casio F91W and F94W to Strap 22mm
€4.50
Display for watch
Free
Wristwatch Stand Designed in DSM
Free
Modular watch stand
Free
Enclosure and Wristband for FitBit Force electronics
Free
Kingsman Tactical Wrist Watch.
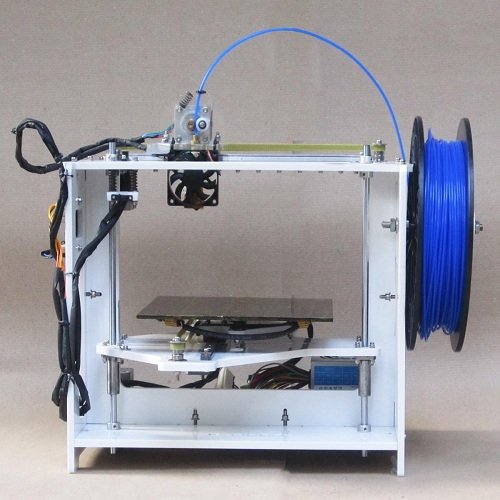
Free
Ultimate Watch Band Holder
Free
3D Printed Wristwatch for Miyota 2415 Movement
Free
22mm Watch Strap with Filament joints
Free
Miniature Watch shaped ring US size 6to13 3D print model
€14.24
It's MakerBot Time - Watch
Free
Simple Sun Dial Wristwatch
Free
V2 - Xiaomi Mi Band 2 replacement wrist band / chain
Free
watch is watching
€25
Tiger Game.Com
Free
Tiger Electronics Sonic Wristwatch
Free
Mini medicine box
€1. 50
Casio W218H gshock strap adapter
€4.18
Xiaomi Mi Band 2 replacement wrist band / chain
Free
Casio F-91W h-link bracelet
€4.35
Casio W218H Combi-style bracelet
€4.35
Better Casio wristwatch band
€5.49
Casio W218H, W800H, and AE1200/AE1300 22mm and 20mm NATO strap tapered adapter
€4.18
President watch bracelet
€9.90
Garmin watch replacement loop
Free
Stand wristwatch - clock holder
Free
Casio A158W 18mm NATO Strap Adapter with Flange
€3. 48
Casio F-91W 18mm, 20mm NATO Strap Adapter
€2.78
Wrist Watch Casing
Free
Watch and Bracelet Stand - Convenient / Adjustable / Space Saving
Free
Wristwatch Base Stand
€1.47
Wristwatch Stand
€1.89
watch-31
€5.70
Makies Wristwatch
Free
Multi-Material and Multi-Color Flexible Watch Band
Free
Modular Wristwatch - 3D Printing Build
Free
Timesquare Wordclock
Free
8 nuances worth paying attention to
Sooner or later, everyone will learn about 3D printing. And only a few lucky people, imbued with the opportunities that 3D printing opens up, catch themselves thinking that they want to purchase a 3D printer. The desire gradually develops into a serious decision and the search for the right option begins. And here the potential buyer is faced with the fact that he does not fully understand what to choose among the whole variety of 3D printers. We will try to answer this question in as much detail as possible. What to look for, and how to make a choice? We want to offer a small checklist of the nuances that you need to pay attention to when choosing a 3D printer. You need to decide for yourself for what tasks you will use this technique? What features should a 3D printer have to solve your problems?
Tip 1 : Decide on 3D printing technology
The first step is to decide on the technology of 3D printing. There are two main paths here. If you are faced with the task of manufacturing high-precision and miniature products, such as jewelry, then 3D printers using SLA or DLP technology are suitable for you. Such printers are specially designed for the manufacture of high-precision models. 3D printing in these printers occurs using a laser beam that illuminates the photopolymer resin. Hence the accuracy of the models. Prominent representatives of this segment: Form 2 3D printer or B9 3D printercreator If you are faced with a wider range of tasks, and functionality, part size, and low manufacturing cost are more important, then an FDM printer will suit you. 3D printing on this equipment involves layer-by-layer melting of plastic. If according to SLA printers everything is clear. The scope of their application is jewelry, dentistry, high-precision prototypes of small parts. Then we will dwell on FDM printers in more detail. There is a lot more variety of different options for implementing printers.
Nuance 2: Evaluate your needs
Of course, you always want to get all the best and with maximum opportunities. Do you need all this to solve your current problems? What can be cited as an example? For example, the size of the working area of the FDM 3D printer. There are printers on the market with a large print area (1m x 1m x 1m), and with a very small one (100mm x 100mm x100mm). But for most tasks, a certain standard has already developed. This is the printable area within 200 x 200 x 200 mm. With slight fluctuations in size in one direction or another. Most 3D printers have exactly this size of the working area. This volume is enough to solve 95% of any tasks. But options are possible ... If you plan to manufacture small parts, then a smaller size will probably be enough for you. But if your work will be related to manufacturing, for example, a master model for casting, or large prototypes, then only then it makes sense to pay attention to a printer with a large print area. In other cases, the size of the print area larger than the standard is nothing more than a nice bonus. But as they say, you have to pay for everything. Therefore, most often it makes sense to focus on the “standard” print area. And even if the part you need to print is larger than the working area of your 3D printer, you can always cut it in a special editor, and then print 2 parts of the model and glue them together.
Nuance 3 : Decide on the complexity of the products
You should decide for yourself how complex models you will print on a 3D printer. If you plan to manufacture complex prototypes, or complex art models, then you need a 3D printer that can print with two materials. This is necessary so that your printer can print supports from soluble material. If the models are not the most complex, then you can get by with one extruder and save the budget. A complex model is a model with a large number of elements suspended in the air, or a model whose elements have angles of more than 30 degrees.
Point 4: Decide on the list of materials to be used.
Another important point. You must immediately determine for yourself a list of possible materials with which you are going to print. This primarily applies to materials with a high degree of shrinkage, such as ABS and Nylon. In order to print with such materials, a heated table is clearly required in a 3D printer. And it is very desirable to have a closed case to provide a thermal circuit around the model. If you plan to print only with PLA plastic. You don't need a heated table. But still it is better that the printer has a heated table. Now the difference in the cost of printers with a heated table is practically the same as the cost without it. But you get a universal solution with which you can perform the full range of tasks facing a 3D printer. One more moment. Ability to print with flexible materials Quite a number of 3D printers face the problem of printing with flexible materials. Of course, printing with various Flexes and Rubbers is very interesting at first glance. But the use of these materials in life is not very common. Usually, for most people, this happens like this: A couple of models are printed, and the understanding comes that this is not a fast and rather complicated process. And this is where the acquaintance with flexible materials ends.
Therefore, it makes sense to demand such an opportunity from the printer if printing with such materials is very necessary.
Nuance 5: Construction and kinematics
Next, you need to pay attention to the design of the 3D printer. Even if you are not a great specialist in technology, you can immediately see that some printers have an open design. And others are closed. As they like to be called in the Russian-speaking community "cubes". What does the appearance say? Printers with an open design, usually have kinematics with a horizontally moving table (based on Prusa 3D printers). This kinematics has some inherent flaws. Such as, not the highest print speed and possible print quality problems associated with the complexity of the settings. First of all, this is the so-called wobble. Also, the lack of a closed case can cause print quality problems with high shrinkage plastics (ABS, Nylon). The main advantage of printers of this design is their price. It is usually lower. But as you know, you have to pay for everything. In this case, the worst performance. The so-called "cubes" today, is the main design, which is represented by leading manufacturers on the market. Such printers are built according to the lifting table scheme. And they lack most of the shortcomings that are inherent in printers from the previous group. “Cubes” usually have a closed body, which allows the highest quality printing with plastics with a high degree of shrinkage. Closed case printers are more rigid. This results in better quality printing. The kinematics of moving the print head is represented by various designs. They have their pros and cons. But most of them have advantages over moving table printer circuits.
Nuance 6: Diameter and changeable nozzle
Most 3D printers on the market come with 0. 3-0.4mm nozzles. This is enough to solve the vast majority of tasks facing a 3D printer. Some of the printers have the ability to install a nozzle of a different diameter, others do not. As we wrote above, the need to print with nozzles with a diameter other than 0.3-0.4 mm arises very infrequently. This mainly concerns, or personal experiments, or some very specific tasks. If you do not plan to do this, then this opportunity is not so necessary. What do we mean by specific tasks? This is especially true for printing large items, where it is very important to reduce the printing time. This can be achieved by using large diameter nozzles. For example, with a diameter of 0.6-0.8 mm, or even a diameter of 1 mm. For printers with a large printable area, the ability to change nozzles is already a vital necessity. Therefore, here, as in the case of a heated table, the ability to change nozzles is a good bonus. It is not mandatory, but very useful if you do not have to pay extra for it.
Nuance 7: Print thickness
It is important to understand that most models on a 3D printer are printed with a layer of 0. 1-0.2 mm. These are the optimal values that allow you to achieve quality and acceptable print speed. There are a certain number of printers that allow you to print with a layer of less than 0.05 mm, and get very high quality prints. But then there is the problem of a sharp increase in print time. And if such print quality is important to you, then it probably makes sense to turn your attention to 3D printers, which we talked about at the very beginning of the article. These are 3D printers using SLA or DLP technology.
Nuance 8: Extruder type
Today there are two main types of extruder. This is a direct extruder in which the bar feed motor is located in the printhead itself. And the so-called Bowden extruder, where the plastic feed motor is located on the body. And the plastic itself is fed to the extruder through a fluoroplastic tube. What are the advantages and disadvantages of each type of extruder? Bowden extruder, due to the lack of a motor on the print head, has less weight. And therefore, it has greater positioning accuracy, which affects the print quality. And a higher speed of movement, which, accordingly, has a positive effect on the speed of printing. But it has one drawback. It is usually difficult to print with flexible plastics on a Bowden extruder. Such as Rubber or Flex. All its positive features, this extruder reveals when using plastic with a diameter of 2.85-3.00 mm. But this type of plastic is less common than the now standard plastic with a diameter of 1.75 mm. And therefore, users of printers with such plastic are often deprived of the opportunity to use new types of materials. Which are primarily produced in the most common form factor of 1.75mm. The direct extruder usually doesn't have such big problems with flexible plastics. Easier to set up, but due to the greater mass of the print head, it is inferior to the Bowden extruder in terms of speed and positioning accuracy. What to prefer? This is the user's choice. We just wanted to talk about the pros and cons of these extruder types.
Of course, there are many more nuances when choosing a 3D printer. But we think that even our small list will force you to look and study some points that you may not have thought about more closely. And it will save you time and money when choosing a 3D printer. 3Dtool company has extensive experience in the 3D equipment market. We work with leading Russian and foreign manufacturers, offering high-quality equipment for a reasonable price. Our service center is staffed by highly qualified specialists who are able to solve any problem in the shortest possible time, and all offered 3D printers come with a 1-year warranty.
In our assortment you can always find 3D printers for your tasks:
1) Budget 3D printers
2) 3D printers for business
3) Large area 3D printers
4) SLA and DLP 3D printers
Do you have any questions?
Call: +7 (495) 324-07-90 (Moscow) and 8 (800) 775-86-69 (toll-free in the Russian Federation) or write to the mail: sales@3dtool. ru and our employees will be happy to give you a detailed consultation on any topic of interest.
How much does a 3D printer cost?
3D printing is a one-stop solution for a wide range of applications, from high-resolution model production to rapid prototyping, rapid tooling for traditional manufacturing processes, manufacturing of aids and end-use models.
However, when you consider investing in a 3D printer, the viability of a solution usually boils down to a simple question: Is it cost-effective for your business? How much does a 3D printer cost and how much time and money can it save your business?
3D printer prices range from $200 to $500,000 depending on the printing process, materials, and complexity of the solution.
In this guide, we'll break down 3D printing costs by technology, compare outsourcing versus in-house manufacturing, list the factors to consider when calculating the cost of each model, and look at what else to look for when comparing different solutions. for 3D printing and other production methods.
Interactive
This interactive ROI tool will help you find out how much time and money you can save by 3D printing with a Formlabs 3D printer.
Calculate Your Costs
The three most well-known plastic 3D printing technologies today are Fused Deposition Modeling (FDM), Stereolithography (SLA), and Selective Laser Sintering (SLS).
Each technology has its advantages and disadvantages - take a look at the infographic:
Download this high resolution infographic here. Interested in learning more about FDM, SLA and SLS 3D printing technologies? Check out our detailed guide.
Prices for 3D printers have dropped significantly in recent years, and today all three technologies are available in compact, low-cost systems.
FDM generally produces models at a lower cost if you only print relatively simple prototypes in limited numbers. SLA technology offers higher resolution and quality, as well as a wide choice of 3D printing materials at a slightly higher price. But this difference is quickly offset when you print complex designs or larger batches due to the less labor-intensive post-processing process. Finally, SLS technology is the most cost effective for medium to high volume production of high quality functional models.
Comparing the total cost of different 3D printers by price alone will not give you a complete picture of how the cost of a 3D printer and a printed model will compare. The cost of 3D printing materials and labor significantly affects the cost of a model, depending on the application and your production needs.
Let's look at the different factors and costs for each process.
FDM, also known as Fused Filament Manufacturing (FFF), is a printing method in which model parts are made by melting and extruding a thermoplastic filament that a printer nozzle applies layer by layer onto the model being made.
FDM is the most popular form of consumer grade 3D printing, fueled by the rise of hobbyist 3D printers. However, professional and industrial FDM printers are also popular among professionals.
The cheapest 3D printers are FDM printers. DIY kits for FDM 3D printers start at $200. However, most of these models are more like toys or DIY projects that require a significant amount of time to build, set up and calibrate. The quality of the print largely depends on the success of these operations. In addition, machines require repairs and regular maintenance to keep them working, so they are more suitable for people with a higher engineering education who have a lot of time and patience.
Hobbyist FDM 3D printers cost between $500 and $1,500, come pre-assembled or unassembled, require less setup, but suffer from the same disadvantages as the cheapest 3D printers. More expensive models are capable of large print volumes and work with a wide variety of materials besides low temperature ones such as PLA.
Professional 3D FDM printers start at $2,500 and large format professional FDM printers are available from $4,000. The cost of the most modern industrial FDM printers can exceed 10,000 US dollars. Most of these printers come pre-assembled and calibrated in the box, or they can be automatically calibrated. Printers in this category offer better print quality, a wider range of media, higher print volumes, improved reliability, and ease of use and maintenance. In addition, professional 3D printer manufacturers offer customer support services for troubleshooting.
Material costs for FDM 3D printing range from $50 to $150/kg for most standard and engineering filaments, and $100 to $200/kg for auxiliary materials. There are also cheaper alternatives, but they are of lower quality.
In addition, FDM printing can be very labor intensive. Successful printing of complex models requires support structures that must be removed manually or dissolved in water. To obtain a high quality surface and remove layer lines, lengthy manual post-processing of models, such as sanding, is necessary.
SLA 3D printers use the process of photopolymerization, which is the conversion of liquid polymers into hardened plastic using a laser. SLA is one of the most popular processes among professionals due to its high resolution, accuracy and material versatility.
Models printed on SLA printers have the highest precision, finest detail, and smoothest surface possible of any plastic 3D printing technology. But the main advantage of the SLA method is its versatility. SLA polymers have a wide range of optical, mechanical and thermal properties that match those of standard, engineering and industrial thermoplastics.
SLA 3D printers can handle a wide range of resin materials for a wide variety of applications.
SLA used to be used only in large and complex industrial 3D printers costing over $200,000, but the process is now much more affordable. With the Formlabs Form 3+ Printer, businesses can now use industrial quality SLA printing for as little as $3,750. With Form 3L, large format SLA printing starts at just $11,000.
Stereolithographic 3D printers will be shipped in a box assembled and calibrated. These are professional tools that are highly reliable and require virtually no maintenance. Technical support is also always available. It provides troubleshooting in a critical situation (but its probability is extremely small).
Most standard and engineered polymers for SLA technology cost between $149 and $200 per liter.
SLA printers are easy to use and many workflow steps, such as rinsing and final curing, can be automated to reduce labor costs. Printed models have a high quality surface immediately after printing and require only simple post-processing to remove supporting structures.
Selective Laser Sintering (SLS) 3D printers use a high power laser to sinter fine polymer powder particles. The unsprayed powder supports the model during printing and eliminates the need for special support structures. This makes SLS ideal for complex geometries, including internal features, grooves, thin walls, and negative taper.
Models produced using SLS printing have excellent mechanical characteristics - their strength can be compared with the strength of injection molded parts. As a result, SLS technology is the most popular plastic 3D printing process for industrial applications.
SLS printed nylon models are ideal for a range of functional applications, from consumer product design to healthcare applications.
Like SLA, SLS technology was previously only available in large format, complex 3D printing systems costing $200,000 or more. With the Formlabs Fuse 1 stereolithography printer, businesses can now solve industrial-scale tasks with SLS technology starting at $18,500. The complete kit, which includes the post-processing and powder recovery system, costs $31,845.
As with SLA printers, stereolithography printers are shipped assembled and calibrated in the box. They are reliable and can operate 24/7. The package includes in-depth training and fast technical support.
SLS nylon print materials cost about US$100/kg. SLS does not require supporting structures and unused powder can be reused, reducing material costs.
SLS is the least labor-intensive plastic 3D printing process in the production environment, because the printed models are of high quality right away, and to remove excess powder, they simply need to be cleaned.
There are several processes for 3D printing not only plastics but also metals.
Metal FDM printers are similar in design to traditional FDM printers, but use extruded metal rods held together by a resin binder. The finished parts of the model are sintered in an oven to remove the binder.
SLM and DMLS printers are similar to SLS printers, but instead of polymer powders, they fuse metal powder particles layer by layer using a laser. 3D printers based on SLM and DMLS technologies can create strong, precise and complex metal products, making this process ideal for the aerospace, automotive and medical industries.
Prices for metal 3D printers have also begun to decline, ranging from $100,000 to $1 million today. However, these systems are still out of reach for most businesses.
SLA 3D printing is available as an alternative to casting workflows that allow metal models to be produced cheaper and faster than traditional methods and provide greater design freedom.
Technical report
Get design guides for 3D printing samples, see the step-by-step direct investment casting process, and study guides for indirect investment casting and sand casting.
Download white paper
Different plastic and metal 3D printing processes have unique qualities that make them suitable for different applications. Below is a comparison of different printing technologies.
Fused Deposition Modeling (FDM) | Stereolithography (SLA) | Selective Laser Sintering (SLS) | Metal FDM Printing | Selective Laser Melting (SLM) and Direct Metal Sintering (SLM) 9 (180180DM) | |||||
---|---|---|---|---|---|---|---|---|---|
Permission | ★ Look | ★ opa | ★cle | ★cle | 901ETRIAL | ||||
★ opa ★ ution | ★ opa | ★cle | ★cle ★ Look | ||||||
★ opa ★ opa ☆ | ★cle | ★ opa | |||||||
performance | ★ opa | ★ Looking ☆ | ★ opa | ||||||
Simplicity of use | ★ opa | ★ Look | ★cle | ★ opa | ★ ☆☆☆☆ | ||||
PROMISE | to LAR x 300 x 600 mm (Desktop and Workshop 3D printers)Up to ~300 x 335 x 200 mm (Desktop and Workshop 3D printers) | Up to 165 x 165 x 300 mm (3D - workshop printers) | Up to 300 x 200 x 200 mm | Up to 400 x 400 x 400 mm | |||||
Price range | DIY kits for 3D printers start at $200, while hobby printers cost $500-1500.![]() | Professional desktop printers start at $3,750, while high-volume large format desktop printers are available from $11,000. | Workshop industrial printers start at $18,500 and traditional industrial printers start at $100,000. | Metal FDM printers start at $100,000, but complete solutions including an oven are much more expensive. | DMLS/SLM solutions start at around $200,000. These printers require special infrastructure conditions, which can further increase costs. | ||||
Cost of materials | US$50-150/kg for most standard and engineering yarns and US$100-200/kg for auxiliary materials. | US$50-150/L for most standard and engineering polymers. | US$100/kg for nylon. SLS does not require supporting structures and unused powder can be reused, reducing material costs. | Depends on material and technology.![]() | Depends on material and technology. Significantly higher than plastic. | ||||
Labor | Manual removal of support structures (soluble support structures may be used in some cases). Long post-processing is required to obtain a high quality surface. | Washing and final polymerization (both can be automated). Simple post-processing to remove supporting structures. | Easy cleaning to remove excess powder. | Washing and sintering (both can be automated). Machining and other types of surface treatment can be used. | Stress relief, support structure removal, heat treatment, and mechanical and other surface treatments. | ||||
Materials | Standard thermoplastics such as ABS, PLA and their various blends. | Various polymers (thermosetting plastics). Standard, engineering (similar to ABS and PP, similar to silicone, flexible, heat resistant, rigid), injection molding, dental and medical (biocompatible).![]() | Engineering thermoplastics - typically nylon and its composites (nylon 12 biocompatible + sterilizable). | Stainless steel, tool steel, inconel, copper, titanium. | Stainless steel, tool steel, titanium, cobalt-chromium, copper, aluminium, nickel alloys. | ||||
Applications | Basic experimental models, low cost rapid prototyping of simple parts. | Prototypes with a high level of detail requiring tight tolerances and smooth surfaces: molds, tooling, templates, medical models and functional parts. | Complex geometries, functional prototypes, low volume production or limited trial production. | Strong and durable models, tools and production aids. | Strong and durable models with complex geometries; ideal for the aerospace, automotive and medical industries. |
When calculating the cost of one model, the cost of ownership of equipment, material costs and labor costs are usually taken into account. It is important to understand the factors that affect each of these cost components, as well as the questions to ask in order to evaluate alternative production methods and uncover hidden costs.
Hardware ownership costs are fixed costs: 3D printer price, service contracts, installation and maintenance. These amounts must be paid whether your printer is idle or produces dozens of models per week.
Add up all projected fixed costs over the lifetime of the equipment, then divide by the number of models you plan to build. As a rule, the higher the performance and efficiency of your 3D printer, the lower the cost of ownership of equipment per model.
In recent years, desktop 3D printers have shown excellent results in reducing the cost of ownership of equipment. With a price 10 to 100 times lower than traditional industrial 3D printers and the ability to produce thousands of models over a lifetime, the cost of ownership can be negligible.
Questions:
-
Are there installation, training or additional initial costs other than the cost of the machine itself?
-
Do I need to sign a (mandatory) service contract? What does it include?
-
What accessories and tools are needed to make the final models?
-
What kind of maintenance is required for the machine to function properly? What is the expected annual maintenance cost? Will it change with an increase in production volumes?
The 3D printing raw materials and consumables you need to create models at an affordable price. These costs largely depend on the number of models you produce.
When calculating the cost of materials, determine how much material is required to create one model, and multiply this figure by the cost of the material. Count the amount of waste and any other consumables. As production grows, the cost of ownership of equipment decreases, and the cost of 3D printing materials tends to become more balanced.
Be sure to check what materials you need to create specific models, as the cost of 3D printing consumables can vary greatly. Please note that some 3D printers only work with their proprietary materials and thus limit your ability to use third party materials.
Questions:
-
What is the cost of each type of 3D printing material?
-
How much material is required to create one particular model, including waste?
-
What is the shelf life of the materials?
-
Do I need other consumables to create models?
-
Can the machine work with third party materials?
While 3D printing can replace complex traditional manufacturing methods and provide significant time savings, depending on the 3D printing technology, it can still be quite labor intensive.
Professional desktop 3D printers are generally optimized for ease of use. DIY kits for 3D printers and hobby printers often require additional effort to adjust settings, while regular maintenance or material changes on traditional industrial machines can involve time-consuming tasks that require the assistance of a skilled operator.
Post-processing workflows vary depending on the 3D printing process, but in most cases include cleaning models and removing support structures or excess material. However, there are solutions to automate some specific tasks. For example, Formlabs Form Wash and Form Cure simplify the wash and finish process for Formlabs SLA 3D printers, while Fuse Sift offers a turnkey post-processing and powder recovery system for the Fuse 1 SLS printer.
More complex processes such as SLA and SLS do not take long to achieve high quality models, while FDM models require lengthy manual post-processing to improve quality and remove layer lines.
Questions:
-
What is the whole workflow of model production? What specific steps are required to set up printing, change materials, and post-process models?
-
How long does it take to post-process one particular model?
-
Are there any tools or devices available to automate some of these tasks?
Outsource production orders to third-party service bureaus or labs when you use 3D printing only occasionally or to produce large models in non-standard materials. Typically, the bureau has several in-house 3D printing processes such as SLA, SLS, FDM, as well as metal 3D printers. They can also provide advice on a variety of materials and offer additional services such as design or improved finishes.
The main disadvantages of outsourcing are the high cost and duration of production. One of the main advantages of 3D printing is its speed compared to traditional production methods. But it is noticeably reduced if the delivery of the model produced by the involved organization takes several days or even weeks. And as demand and capacity grow, the costs of outsourcing are rising rapidly.
Desktop 3D printers are an excellent solution for rapid model production. Depending on the number of parts needed and the volume of prints, the investment in a professional 3D printer can pay for itself in just a few months.
With desktop and workshop printers, you can pay for the capacity that matches your business needs and scale your production by adding more devices as demand grows, without the heavy investment of a large format 3D printer. Using multiple 3D printers also allows you to print models from different materials at the same time. But if there is a need for the production of large parts or the use of non-standard materials, service bureaus can come to the rescue.
Investment, material and labor costs are relatively easy to calculate. But what about indirect costs and hard-to-calculate factors that affect your business? Let's look at some of the main considerations when comparing a desktop 3D printer to outsourcing or other manufacturing methods.
Save time: What if you could get products to market a few months faster? Or reduce the delivery time of your products by a few days or weeks? 3D printing simplifies traditional prototyping and manufacturing workflows, helping you save time and stay ahead of the competition.
Best results: 3D printing allows you to create more iterations, overcome failures faster and produce better end products. Troubleshooting a design early on also helps avoid costly redesign and the use of additional tools.