Thrimana 3d printer
Thrimana 3D Printers - Electronics Company in Colombo 00600
Thrimana 3D Printers is a Electronics Company located in Colombo 00600. It is one of the 117 Electronics companies in Sri Lanka. Address of Thrimana 3D Printers is No 02 Hamer's Ave, Colombo 00600, Sri Lanka. Website of Thrimana 3D Printers is http://thrimana3dprinters.com/. Thrimana 3D Printers can be contacted at 94112081343. Thrimana 3D Printers is located in a busy area and we are covering at least 601 places around it on Srilanka-Places.com. Thrimana 3D Printers is rated 4.5 (out of 5 stars) by 11 reviewers on the web.
Some of the places around Thrimana 3D Printers are -
BPO Colombo (Pvt) Ltd
(Business administration service) No.16, Harmer's Avenue, Wellawtte, Colombo, Sri Lanka (approx. 198 meters)
Recharge Tours (Taxi service) 118 Galle Rd, Colombo 06000, Sri Lanka (approx. 205 meters)
Mirror Magic by Thanu (Beauty Parlour) 31A, 1/1 St Lawrence Rd, Colombo, Sri Lanka (approx. 372 meters)
S & F CONSULTING FIRM LIMITED (Business management consultant) 57 W. A. Silva Mawatha, Colombo 00600, Sri Lanka (approx. 382 meters)
BASE 1 CONSULTANCY (PVT) LTD. (Corporate office) 142 - 2/4 Galle Rd, Colombo 00600, Sri Lanka (approx. 132 meters)
Ishan Arch and Eng Consultants Lanka (IAEC)
(Engineering consultant) 255 1/1 E, Galle Road, Colombo, Srilanka 06000, Sri Lanka (approx. 175 meters)
lanka hospital (Hospital) 11 Lily Ave, Colombo, Sri Lanka (approx. 239 meters)
D.K FRESH FISH (Seafood market) 57 c W. A. Silva Mawatha, Colombo 00600, Sri Lanka (approx. 382 meters)
Studio RedPix (Wedding photographer) No. 05 1/1 Harmers Avenue, 00600, Sri Lanka (approx. 230 meters)
I WORLD (Stationery store) 159, 06 Galle Rd, Colombo 00600, Sri Lanka (approx. 340 meters)
Within less than half a Kilo meter of Thrimana 3D Printers, you can also find Kamsins, Little Asia Emporium, Fardar Express Logistics, Orient Global Logistics (Pvt) Ltd, R D Partners; Chartered Accountants, Kids Island, Luxmi Flower Shop, Mirbaha Hardware Stores, Wickramarachchi Hearing Care, Wickramarachchi Opticians & Hearing Care, Laugfs Super Market, ChaThak, watsans. com, Ahlukars, Tikiri Fancy Centre, Cloudnine Beauty salon Wellawatte, Priyaashanker - Head Office, Watsans, Sochchy’s Beauty care, Anusha's Finishing Academy and many more.
Distance From Major Landmarks
Distance between Thrimana 3D Printers and Savoy 3D Cinema is approx 745 meters.
Distance between Thrimana 3D Printers and Dinemore - Wellawatte is approx 503 meters.
Distance between Thrimana 3D Printers and Kandy - Nugegoda is approx 2 kilometers.
Distance between Thrimana 3D Printers and Shanmugas is approx 1071 meters.
Distance between Thrimana 3D Printers and Dinemore - Wellawatte is approx 502 meters.
Rating
Contact
94112081343
http://thrimana3dprinters. com/
Address
No 02 Hamer's Ave, Colombo 00600, Sri Lanka
Location
FAQs:
What is the contact Number of Thrimana 3D Printers?
Contact number of Thrimana 3D Printers is 94112081343.
Does Thrimana 3D Printers have website?
Yes, website of Thrimana 3D Printers is http://thrimana3dprinters.com/.
What is rating of Thrimana 3D Printers?
Rating of Thrimana 3D Printers is 4.5 out of 5 stars.
What is the address of Thrimana 3D Printers?
Address of Thrimana 3D Printers is No 02 Hamer's Ave, Colombo 00600, Sri Lanka.
Where is the Thrimana 3D Printers located?
Thrimana 3D Printers is located in Colombo 00600.
What is the Thrimana 3D Printers?
Thrimana 3D Printers is a Electronics Company in Sri Lanka
What is the Pincode of area in which Thrimana 3D Printers is located?
Pincode of Colombo 00600 is 00600
Recent Reviews on Srilanka-Places.com
Darusha Pantry Cupboards
Looking for a pantry cupboard for home in Chilaw. Want to know about the products ,rates and after sales
Tharaka, 26 Nov 2022 11:11 AM
The Academy of National Arts Kundasale
Pencil arts classes
Darani , 26 Nov 2022 11:13 AM
Marvellous Inn
Hi, we already booked 3 nights in your house and we would like to book in advance 2 tickets for the train to Kandy, could you please to help us with that? Thanks a lot
MARTA, 26 Nov 2022 11:13 AM
SIERRA CONSTRUCTION (PVT) LTD
Dear Sir/Madam. I am writing to you from Uganda. We are a consultancy firm in charge of searching for international contractors.
Apparently the office of President in Uganda is seeking eligible contractors who can carry out design and construction of fully furnished hospitals in six districts.
Please let me know if you can extend your services in Uganda .
Frank Adams
Frank Adams, 26 Nov 2022 11:13 AM
Air Trans WWE
Is it possible to bring goods from China to Sri Lanka?
maduranga, 26 Nov 2022 11:23 AM
IOM Migration Health Assessment Centre
I have submitted visa application to Australia. I am asked to undergo medical examinations. How can I arrange that. Pl. let me know.
K.Jayawardane, 26 Nov 2022 11:24 AM
Air Trans WWE
Is it possible to bring goods from China to Sri Lanka?
maduranga, 26 Nov 2022 11:52 AM
Wasana Bakers - Horana Branch 03
I want to apply a new branch how I can do?
shakya kushani, 26 Nov 2022 11:52 AM
Wasana Bakers - Horana Branch 03
I want to apply a new branch how I can do?
shakya kushani, 26 Nov 2022 11:52 AM
Cash On Delivery Courier
Hi, I just wants to know your COD charge for out of Colombo parcel delivery.
Harshini, 26 Nov 2022 12:23 PM
Write a review
☆ ☆ ☆ ☆ ☆
People also search for
Electronics companies in Colombo 00600
Name
Select Reason --This place / business no longer exists.The listing category is wrong. It should be under some other category.There are major mistakes in this listing.Contact details on this listing are incorrect.Other
Explain more about it
3D Printing News Briefs: March 16, 2019 - 3DPrint.
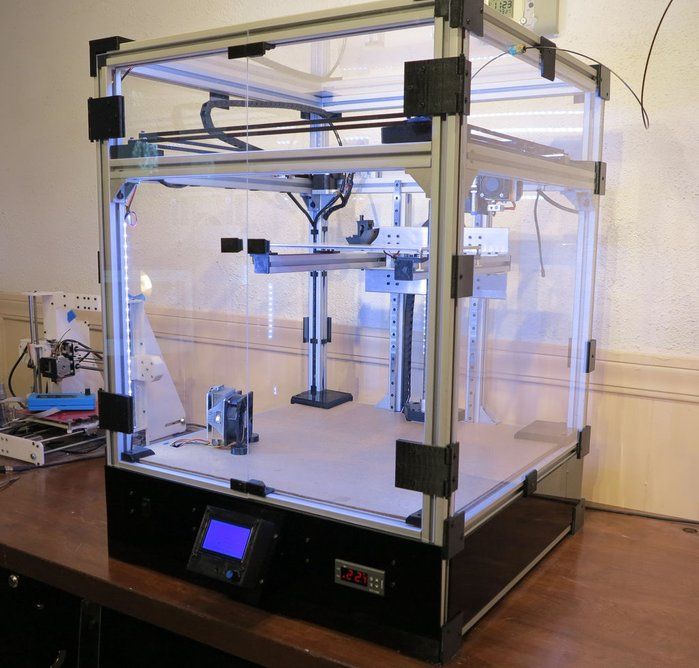
We’re starting with 3D software and medical 3D printing in today’s 3D Printing News Briefs, and then moving on to stories about some cool 3D printed projects. Sinterit has updated the software for its SLS 3D printers, and Deutsche Bahn is increasing efficiency with software solutions by 3YOURMIND. Medical 3D printing is on the rise in Sri Lanka. A designer whose work we’ve previously covered used Carbon technology to 3D print a unique pair of heeled shoes, and an Indian company used 3D printing to reduce the production time for a 6 ft superhero.
Sinterit Releases New Software Update
Desktop SLS 3D printer manufacturer Sinterit just released a new update for its Studio software, which all Lisa and Lisa Pro 3D printer users will now be able to access for a better consumer experience. The update gives these users a lot of positive changes, including more detailed and precise 3D printing with its PA11 Onyx and TPU Flexa materials and optimized slicing, which makes it easier and faster to manipulate models, while also using less RAM.
Sinterit has also made it possible to stream video via WiFi from its 3D printers’ cameras, so users can keep an eye on their prints remotely. In addition, the 3D printers now have an easier step-by-step guide on the screen to make the startup procedure smoother, and a new “About” button on the menu is helpful for optimized model preparation inside Sinterit Studio.
Deutsche Bahn Using 3YOURMIND Software Solutions
German railway company Deutsche Bahn (DB) has been working hard over the last five years to continue developing its 3D printing division. Now, DB has joined industrial 3D printing software solutions provider 3YOURMIND in a strategic partnership in order to increase the efficiency of its 3D printing processes, and also determine possible 3D printing applications from around its company in order to assemble a digital spare parts warehouse. The Berlin-based company’s software platforms allow customers to exploit 3D printing potential with digital workflows, and 3YOURMIND supports DB’s ambition to expand its own additive manufacturing reach.
3YOURMIND’s software will give DB employees access to a simple digital interface so they’re able to quickly submit new ideas for 3D printable parts based on applications they encounter every day. Then, the platform provides an analysis and identifies uses cases with the highest production potential, before DB experts shine a spotlight on the employees and choose the best projects to send into production.
Medical 3D Printing in Sri Lanka
According to Dr. Rajitha Senaratne, the Health Minister for the South Asian island of Sri Lanka, 3D printing for health applications will now be available for the first time in the country beginning this month at the National Hospital of Sri Lanka (NHSL). Minister Senaratne made this announcement in Colombo – the country’s largest city – at the 26th Annual Scientific sessions of the College of Medical Administrators, stating that doctors can provide more personalized care by using modern technology like 3D printing.
In conjunction with this announcement, RCS2 Technologies, the country’s sole 3D printer manufacturer with its Thrimána line, will be working with the country’s Ministry of Health to start up a 3D printed prosthetic manufacturing project.
3D Printed Generative Heels
Talented designer Masaharu Ono, currently working for Japan’s DiGITAL ARTISAN.inc, is well-known for his creative 3D printed projects in both the fashion and technology worlds. Now he’s back in the fashion world with a 3D printed pair of high heels that you’ve got to see to believe. On the artisanal project “Generative Heel – Formless” for DiGITAL ARTISAN, Ono worked with casting company Castem, chemical manufacturer JSR, and 3D printing company Carbon to create the sky-high heels.
“This is concept model for mass customization, but I just getting ready, I will sell it as soon as possible,” Ono told 3DPrint.com.
3D Printed Window Spiderman
An Indian manufacturing company by the name of STPL3D received an unusual order from a traditional fine arts manufacturer: an extremely detailed, 6-foot Spiderman sculpture for the opening of a new entertainment store. Typically, a project like this would take closer to two months, but STPL3D’s given deadline was just one week away. Using 3D printing, the company was able to complete it in just four days, which helped lower the cost and weight of the sculpture as well. Digital sculpting was used to modify an open source file to better fit the client’s needs.
“Our production team wanted to take full advantage of our array of 15 FDM machines so we could finish the project before the timeline, so we divided the 6 ft* 4 ft sculpture into 20 parts, then our post-processing team assembled the spiderman in 6-7 hours with plastic welding and glue to bring it in real shape that was required by the client,” Hardik Prajapati of STPL3D told 3DPrint.com.
“Post processing is always fun and all about teamwork. Our artistic and post-processing team played a major role in finishing the project that had matched our client’s expectation.”
Discuss these stories and other 3D printing topics at 3DPrintBoard. com or share your thoughts in the Facebook comments below.
Stay up-to-date on all the latest news from the 3D printing industry and receive information and offers from third party vendors.
Tagged with: 3D printed high heels • 3d printed prosthetics • 3d printed superheroes • 3D printer software update • 3d printing software solutions • 3YOURMIND • Carbon • concept • Deutsche Bahn • efficiency • fdm 3d printers • generative design and fabrication • high detailed 3d prints • Masaharu Ono • mass customization • post processing • sinterit • Sinterit Lisa • Sinterit Lisa 2 • software updates • spiderman • Sri Lanka • strategic partnership • Thrimana 3D printers
Please enable JavaScript to view the comments powered by Disqus.
Best 3D Printer Candidate 2022 / 3D Printers, Machine Tools & Accessories / iXBT Live
If you want quality printing out of the box as well as a solid build, then Kywoo3D Tycoon Max is the one for you. This printer attracted me with interesting features at a low price. And most importantly, what attracted me is a very reliable design. After all, it is she who affects the quality of the print.
I found the first mentions of this manufacturer and printer on Kickstarter, and then on local sites. Then the model was simply discussed, but there were no real owners. But then the first reviews appeared, and to be honest, the printer was not praised in them. Despite the thoughtful design, the printer had problems with airflow and buggy firmware. Therefore, when I needed a 3D printer, I took myself Anet ET4 Pro. But then there was a need for another printer, so I, again returning to the question of choice, decided to take myself a Tycoon Max. And now, having used the printer for several weeks, I realized that I made the right choice. The printer for its price really gives excellent print quality, and if necessary, also a very fast print speed comparable to deltas.
Characteristics of Kywoo3D Tycoon Max:
Well, in words, I’ll add something that is not in the table:
- Print area: 300 * 300 * 230mm
- Print type: FDM
- Number of extruders: 1
- l.
-0.4mm
- Nozzle: 0.4mm
- Control: USB, MicroSD card, Wi-Fi
- Power: 350W
- Maximum table temperature: 100C
- Maximum extruder temperature: 260C
- Additional design information:
- High rigidity aluminum profile frame.
- X-axis rails, Y-axis shafts.
- Z-axis motor belt synchronization
- 16-point auto-leveling
- 3.5" touch screen for printer and printing process control
- Convenient filament threading with ring on extruder 90 015
-
Now let's talk about the printer itself. It was ordered from a warehouse in the Russian Federation, and the delivery time took 5 days. A huge box weighing 16kg was received in the mail:
Inside the box is a printer disassembled into two parts. Everything lies in layers, which are laid with foam material. So it is unlikely that anything could be damaged along the way.
Opening the box, the first layer I saw was the lower frame of the Y-axis with a heating table and ultra-base:
Below the next layer is the main frame of the Z-axis, a coil of PLA test plastic, a box with accessories:
I’ll tell you right away about the complete plastic. It has a weight of 500g, wound on a plastic reel, sealed in a vacuum bag. I printed part of the coil during the tests, and I liked the plastic.
As for complete accessories, everything is relatively standard. Inside the box are a spatula, a set of hexagons in a convenient case, several spare ties, wire cutters, clamps for the ultrabase, four screws for assembling the printer, a Phillips screwdriver, a piece of heat pipe, a spare 0.4mm nozzle, a needle for cleaning the nozzle, a wrench for unscrewing the nozzle, spare limit switch, USB cable, reel mounting stand. Also included is a card reader and a MicroSD 8Gb flash drive manufactured by Netac ( a good manufacturer, I have several flash drives of this company, and they work well )
The printer is powered through a detachable cord with a European-type plug.
If necessary, it can be replaced without any problems:
Also included with the printer is an assembly and configuration manual. It is made on high-quality printing, but, in fact, there is no great benefit from it:
Now let's consider ultrabase glass. It has dimensions of 305*320mm and a thickness of 4mm. On the edge there is an inscription with the logo of the manufacturer:
Having already printed enough parts, I can say that the quality of the Ultrabase is excellent. It is strong, there are no problems with plastic sticking, it heats up evenly. And at the end of printing and cooling, the parts come off without problems.
The ultrabase is attached to the heating table with 4 stationery clips (they are included). The heating table itself is made of metal, and is attached to the frame on shafts through plain bearings. By the way, in order to reduce weight and inertia during movement, the manufacturer made the table itself with holes that do not affect rigidity.
By the way, the table is connected to the control board via the XT60 connector. This is the first time I see such a solution, but logically, this is a fairly reliable connection.
Another thing I would like to note on the table frame and X-axis is the presence of good legs that can be adjusted in height. This is useful if the printer is not standing on a completely flat surface, and correct adjustment will avoid unnecessary movement of the frame when printing.
Now let's move on to inspecting the frame along the YZ axes. It also contains the control board and power supply. It also has an extruder. This is what it looks like:
The first thing I want to pay attention to is the overall rigidity of the frame. It uses a double frame made of aluminum profile, on which there is a metal box on top. This box serves two purposes: hiding the interior of the printer and adding rigidity to the frame. And it has a very good effect on the quality of the print.
The Z-axis of the printer is fixed on the frame through two shafts rigidly fixed to the frame itself and a closed plain bearing, and for moving there are two studs with stepper motors on both sides.
Additionally, the manufacturer has added a belt that synchronizes the operation of these stepper motors:
Rails are installed on the printer to move the extruder. They are quite high quality, and during the work I personally did not have any problems with them. For better sliding, the rails are immediately lubricated from the factory, and the rails themselves also have holes through which this lubricant enters the rails. Also, through these holes, the rails were fastened along the entire length of the frame.
As for the extruder, the manufacturer did not reinvent the wheel, and equipped the printer with a proven solution. This is MK10, but with some modifications. First, it adds an iron frame that looks good while protecting the user from contact with hot extruder elements. I would like to think that this frame also serves as an additional radiator, but if you look at how it is fixed, it immediately becomes clear that there is not much heat coming to it. And the second addition is a special lamb for scrolling plastic when refueling.
And this is a really handy feature. When refueling, you do not need to press anything, as in other printers. We simply pull the plastic through the plastic sensor, point it into the hole of the extruder and turn the lamb. Plastic itself immediately clings and is pressed through. A simple and elegant solution that is sorely lacking in other printer models.
Also immediately above the extruder is a low filament sensor. This is also a pretty good solution, since the distance between the sensor and the extruder is minimized here. And this means that you don’t have to throw out 20-30cm filament bars that simply cannot be pushed into the printer. The amount of waste here is minimal.
As for blowing, a fan with an impeller is used here, which is mounted near the nozzle. Fan model pb04010ms4. The airflow itself is realized through a wide slot. I personally did not notice any problems with blowing during printing, there is enough blowing, and it blows directly on the model. The blowing speed can naturally be adjusted both during the cutting of the model, and already directly during printing, the fan has speed control.
I also once had to disassemble the extruder to replace the nozzle during printing. What was in the kit, I managed to score on my own stupidity, alternating types of plastics without changing the temperature. Therefore, I will show the extruder in disassembled form:
I also want to draw attention to the fact that the printer has a table auto-calibration function. For this, a BL Touch sensor is installed here. More precisely, there is not the original 3D Touch with a plastic plug.
But by the way, I have no complaints about his work. The table calibrates perfectly, and even if there is a misalignment of fractions of millimeters, everything is taken into account and there are no problems with printing. The table itself is calibrated using 36 points (6*6) and looks like this:
Also, in addition, I can also note the presence of a silicone lining on the hotend, so that the temperature is more stable:
Well, after we have examined both halves of the frame, we can start assembling the printer.
She's very simple. The existing 4 screws are screwed through the grooves, and we stretch harder.
Additionally, you need to connect the connector to the table and connect the motor along the X axis. By the way, in the printer, all the wires are laid right away, and where they can be fixed with ties. Therefore, nothing dangles here, does not hang down and is as neat as possible:
That's it, the assembly is finished. This is what the assembled printer looks like, well, with the exception of the ultrabase and the bracket for installing the filament spool.
The bracket itself, by the way, is standard, like most printers in this price range. Metal profile and plastic tube. The bracket is installed at any point of the aluminum profile, through two spacer nuts:
Well, once the printer is assembled, you can consider the rest of the design elements. If you look at the back of the printer, you can see the power button and the port for connecting the power cord:
On the other hand, there is a sticker on the frame with information about the printer:
Separately, I would like to note one more convenient feature of this particular printer, which I have not seen anywhere else.
These are convenient carrying handles:
They are metal and rigidly fixed to the frame, you can safely lift the entire structure with them and not worry that something will break. For me, this is very important, since my printer can be transferred to different points around the room, and even between rooms. Depending on how long the print is placed.
If you look at the printer from the right end, then you can see a slot for a MicroSD card through which a model for printing is thrown onto the printer. There is also a MicroUSB port for connecting to a computer (does anyone use this method of printing?) and another slot for SD cards, the purpose of this slot remains a mystery to me:
Well, now the most interesting. It is, of course, a touch screen. When you turn on the printer, we first see a splash screen with the manufacturer's logo, and then the main desktop, from which you can get to different settings:0003
All items on the desktop are interactive. Management is implemented by clicking on the desired element.
For example, by clicking on the ruler of XYZ axes, we get to the axis calibration menu:
And if you click on the flash drive icon, the files for printing located on the flash drive are opened:
The printer sees folders and subfolders without problems, but there are Russian file names Problems. In the current firmware, the Cyrillic alphabet looks like unreadable krakozyabry.
If you click on the gear icon, then naturally we get into the settings menu. Here you can select the temperature of the preheating of the table and extruder, change the filament during printing or in idle time. Find out information about the firmware, set up Wi-fi and select the interface language ( there is no Russian language in the photo, but it has already been added in the latest firmware )
By the way, the printer has a built-in Wi-fi module, and it can be run in access point mode or connected to a home wi-fi network.
In the first case, you can connect to the printer and use an additional plug-in in Cura to send files for printing over the air, as well as monitor the status of the printer:
True, the wi-fi module has one minus.
It stands inside a metal case, and it dampens the signal very noticeably. If the printer is in the next room, then I can no longer connect to it because the signal level is too weak. In fact, the range of the access point is about 5-6 meters maximum.
But back to the screen. Despite the modern 32-bit processor, another disadvantage that I want to point out is the lack of model previews. This option is already firmly in use, and I would like to hope that it will also appear in future firmware. But so far the interface looks pretty simple. By the way, this is also visible at print time, when progress is displayed simply as a blue bar with a percentage of completion.
But in general, the management here is really convenient. You can change the Z-axis gap on the fly, change the speed of the blower fan and the temperatures of the table and extruder.
Well, I also want to show the inside of the printer without disassembling it. How could I get the camera. The printer is powered by the built-in Mean Well LRS-350-24 power supply.
Already by the name it is clear that this power supply produces 24v / 350w.
In the future, I plan to crawl up to this PSU and add a backlight tape to the printer frame so that you can see the printing process.
The brains of the printer are located in the upper part of the case, it is already much more difficult to crawl there with the camera:
But since the board is sold separately, I'll just add a photo from the manufacturer here:
True, in this photo it is not clear which processor is used in the board. But let's hope it's good enough.
In general, if we talk about the assembly, then it did not raise any questions for me. The frame here is well thought out and very rigid. All axles run smoothly and there is no backlash. The printer is large, solid and heavy. And gravity, as we know from the words of Boris Razor, is good and reliable.
Now it's time to talk about the printing process and the models I have printed
The first thing I decided to do was check the speed characteristics of the printer.
The specifications indicate that its maximum speed reaches 150mm / s. Therefore, I printed a test cube at this speed:
I shot with a macro lens so that the flaws in the layers were immediately visible. And they are here, since my plastic is not the best, besides, it’s also old, taken from the remnants.
Then I printed the same cube, but at a speed of 180mm/s, and put it next to the first cube:
Try to guess from the photo which of these two cubes was printed at what speed.
I'll give you a hint. On faster printing, at 180 mm/s, the plastic from the nozzle no longer has time to come out and lay down evenly, so the layers appear thinner, and there are gaps between the layers.
And yes, on the left it's a cube printed at 180mm/s and on the right it was 150mm/s.
And by the way, this speed is quite suitable for printing rough parts, when you need to determine the degree of fit and size, without regard to quality. This saves a lot of printing time.
Well, at a speed of 150mm / s, you can already print full-fledged models. Here, for example, I printed a model at this speed:
And this is not a draft part, but a full-fledged one, for a commercial order. Here is what I printed, the size of this medal is 22 centimeters:
If you look at macro photography, you can evaluate both the detail and the level of stacking layers at this print speed:
By the way, as you can see, the medal was printed in two colors of PLA plastic. This type of printing is not difficult, just at a certain moment of printing, you can pause the printer and replace the filament. But I want to add that Cura has a handy plugin that allows you to precisely set the pause on the desired layer. To do this, go to the plugins, and select the “Filament Change” function in the post-processing plugins, in which we simply set the layer on which the pause will occur. The printer will stop printing at the right moment, move its head to the extreme left side in front and squeak loudly, calling for a replacement of the filament:
Through this plug-in, you can set the replacement of the filament at least on each of the layers, which is very convenient and allows you to achieve interesting effects when printing art objects.
I hope my advice will be useful to those who are fond of 3D printing.
I also printed an axolotl toy for children, which consists of closed links:
Printing was done at a speed of 120mm / s, and could have been more successful if I had not forgotten to remove the automatic supports in Cura. But since there were supports, I had to spend time post-processing and separating the supports, as well as cleaning up excess plastic in the links. This is what this axolotl looks like on a macro shot:
Layer height 0.25mm, travel speed 120mm/s, table temperature 60 degrees, extruder temperature 220 degrees.
The next model was among the models on the flash drive provided with the printer, this is a ghost keychain.
By the way, I want to add a macro photo of the substrate that remained after printing, so that you can evaluate the uniformity of laying layers and tracks:
a piece of ordinary sponge to clean the plastic from dust, which is very visible on white parts.
Some print different boxes and cases, but I just took a piece of dish sponge and pierced it with a filament, which I then moved on. After that, the parts became noticeably cleaner.
Another custom-printed detail. Steering shaft bushings for Nissan Qashkai. Designed to eliminate the runout between the shaft and the tube in the steering reach adjustment mechanism:
Another model. Decepticon logo overlay for standard Mazda car logo:
Spinner gear. A toy that I printed to test the possibility of printing gears:
Stand legs for Sony PlayStation 4 Slim:
Well, there were many other models that were printed to order, but I did not have time to take high-quality photos. I mainly use PLA and Petg plastics when printing. Well, a little ABS, which I really dislike because of its capriciousness to ambient temperature and drafts. And as you can see from the photo, there are no problems with printing. The only problem I've encountered is changing different types of plastic during printing and clogging the nozzle as a result.
But it's my own fault, I shouldn't have experimented.
Conclusion:
As you can see from the review, I really liked the Kywoo3D Tycoon Max 3D printer. It is definitely worth the money, here it is clear that the manufacturer did not save on everything and everyone, as is the case with other manufacturers. I will try to indicate the advantages that the buyer receives:
Reliable design and rigid frame . A double profile and a metal frame are assembled into a single design that is reliable and does not give any backlash. This has a positive effect on detail and print quality, as well as on the maximum print speeds. Also, all cables and wires are correctly laid in the printer immediately from the factory. And the heating table is attached through the XT60 connector, which has long proven its reliability.
Shafts along the axes Z and X. The presence of shafts and plain bearings also has a positive effect on the accuracy of printing and the reliability of the design as a whole.
Since they are less subject to wear and play, unlike wheels that drive along a profile.
Axis rail Y . The advantage of rails over conventional wheels, I think, is not even worth discussing. This is a more accurate movement of the extruder, and the absence of backlash, and durability. Of course, it would be better to have rails on all axes, but this will significantly increase the price of the printer, and it will no longer be so interesting.
Convenient filament threading with scroll knob . Here I will attribute this not only to pluses, but directly to huge pluses. Such a trifle like, but very much affects the work with the printer, especially if you print a lot and often change the filament.
Short feed extruder MK10 . Allows you to safely print any type of filament, including flex. In addition, unlike Bowden, plastic is saved here. The retract works more adequately. In general, I personally prefer Direct extruders, although I have a printer with a bowden system.
Availability Wi- fi module. Let it be weak, and not everyone needs it. But for some it will be very useful and necessary.
Axis motor synchronization Z . Another little thing that many manufacturers neglect. Meanwhile, this little thing affects the accuracy of printing. And many people customize their printers by adding a Z-axis belt.
Auto level. The printer builds a table map using 36 points and then takes into account any irregularities during printing. Which is very good for the adhesion of the base layer. Well, of course, there are no dances around the printer with a leaflet for an exact fit. To be honest, this process is what I dislike the most during printing.
Print area 300*300*230mm. With such dimensions of the printed area, you can print a much larger number of details than with the usual 220 * 220mm in most models.
True, as a minus, the dimensions of the printer themselves are already acting here. Under it, you need to prepare a surface with dimensions of 62 * 62 centimeters, and not every table is suitable here.
But to be honest, I did not find any minuses for the printer. Well, except perhaps the dimensions and the weak signal of the Wi-fi module. But I already wrote about this above. Well, perhaps the relatively simple firmware can be attributed to the minuses, although it does not affect the print quality, it's just an interface.
Kywoo3D Tycoon Max is currently my main 3D printer, on which I print most models. For yourself and to order. Print field 300 * 300 * 230mm allows you to print large enough parts or batches of parts, which suits me completely. I also liked the robust, well-thought-out and monolithic design of the printer, as well as the speed of its operation. As for working on wi-fi, this did not take root for me. At first I dabbled in sending and monitoring, and then, out of habit, I returned to the flash drive and card reader again.
In terms of noise, the printer does not raise any complaints, it is the same as most FDM printers. Mostly you can only hear the fans. I also cannot fail to note the most convenient type of filling the filament with the help of a lamb, in my opinion, this bribed me very much.
Well, as it became clear from the review, I can safely recommend this printer for purchase, especially since its price is quite affordable, and frankly, for its price of $280, I cannot find a single competitor for this model. If you like the printer and want to buy it, you can use the promotional code KY3D06 when ordering, which will give an additional discount. And these printers are in stock in the Russian Federation, so delivery will be fast.
Current price for 3D printer Kywoo3D Tycoon Max
Taulman 3D filament for 3D printers
No products were found matching your search criteria.
Taulman 3D is an American manufacturer of 3D printing materials, specializing primarily in high quality nylon products with excellent strength properties.
3D filaments from this brand are of impeccable quality, optimal price and the best solution for all areas of prototyping. Plus, if you're looking for the best nylon or PETG filaments, Taulman 3D is the pros to recommend.
Read more…
Nylon's distinctive characteristics in terms of 3D printing are high strength, elasticity, low shrinkage, a wide range of chemical and thermal resistance - this is an ideal option for industrial prototyping, especially since all products made from it have excellent performance mechanical strength with sufficient surface elasticity.
In our 3DMall online store you can order original consumables manufactured by Taulman 3D with delivery anywhere in the Russian Federation - we, as an accredited partner of the brand, offer you the best prices for products of impeccable quality.
On our website you will find a huge variety of plastic threads of various types and colors. We cooperate with official dealers, therefore we offer our customers goods at the most discounted prices.
Affordable cost of goods, high quality of products, prompt service and delivery throughout Russia are our key advantages. Choose the best for your 3D equipment like Taulman consumables. The range of varieties of plastic threads from this American manufacturer is quite wide, and the quality of products always remains on top.
Taulman Plastic
Consider some of the filaments offered by the Taulman brand. T-Lyne plastic threads are a joint development of Taulman and DuPont. As a result, a unique plastic, characterized by high strength, flexibility and elasticity, went on sale. This product is very popular in the field of golf balls and bowling balls. On our website you can buy T-Lyne plastic threads in spools of various weights. The bar diameter is 2.85 and 1.75 mm.
NinjaFlex plastic threads are among the very flexible materials with high strength properties. Consumables are of excellent quality, they are made using the patented Taulman technology.
NinjaFlex plastic is a thermoplastic elastomer (TPE). Great for 3D equipment with a direct drive extruder.
Separately, I would like to highlight the unique material from the American manufacturer Taulman. Its main advantages are a high level of tensile strength, amazing wear resistance, comparable to nylon, low shrinkage. In addition, the filament is very convenient and comfortable to use during work. Temperature during 3D printing with ALLOY 9 plastic filaments10 is 245 degrees. Coils are available for sale in weights of 0.45 kg and 1 kg, and the diameter of the plastic thread is 1.75 and 2.5 mm.
Nylon 230 is a consumable that allows you to print at low temperatures and without heating the job site. Suitable for almost all models of 3D equipment.
How to place an order?
To purchase the desired product, you can contact the consultants via online chat. A qualified employee will help you make the best choice and suggest the right decision.
Learn more
- Maximum print speed: 0mm/10mm s (personally tested up to 140mm/s and it prints fine)