See me cnc 3d printer
Downloads – SeeMeCNC
Starting June 2021, new guides are found here
Documents & Instructions
User guides prior to June 2021 are here:
Click here to go to our User Guides
Cura Slicing Software User Guide
The Cura slicing software is our recommended choice. Our slicing profiles have been perfected and perform excellent with the filament we sell.
Click here to go to our User Guides
Artemis
User Guides
Rostock MAX v3.2
User Guides
Hotend & Upgrade Assembly Instructions
User Guides
Delta Calibration Wizard
Use this wizard is for use with RAMBo controlled SeeMeCNC Delta printers. These includee RostockMAX v1, v2, v3, Orion, Eris, and h3 printer models.
Click here to go to the Delta Calibration Wizard page
Rostock MAX v3
Assembly and setup guides for v3 only. See above for v3.2
Rostock MAX v3 DIY Kit Assembly Instruction Manual
Rostock MAX v3 RTP User Manual
Probing GCODE
RostockMAX v3 Firmware
h3 DIY Hacker Delta
h3 Assembly Manual
ERIS Delta
ERIS User Manual
Eris Firmware Update Instructions
ORION DELTA
ORION Users Manual For Current ModelsThis is the complete User Manual for the Orion Delta 3D Printer that came with the firmware version 0.91. To verify this, simply look at the LCD screen when it powers on and it will display the machines firmware information
ORION Users Manual For machines with 0.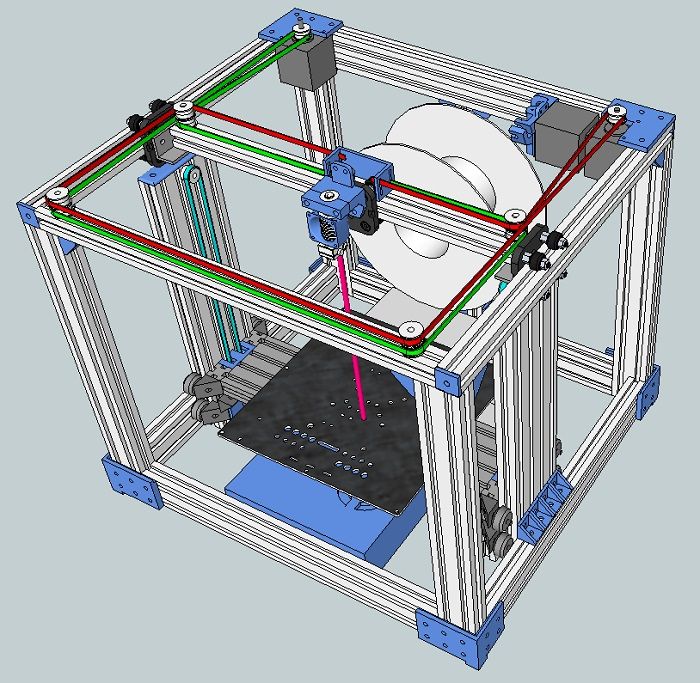
This is the complete User Manual for the Orion Delta 3D Printer that came with the firmware version 0.83. To verify this, simply look at the LCD screen when it powers on and it will display the machines firmware information
ORION Delta Firmware Calibration Gcode FilesThese two files are handy for calibrating your ORION DELTA. The first one named ORIONTOWERS will help you set your three tower endstop screws so you have a level table. The second file named ORIONHRADJUST is for adjusting any delta offset (concave/convex) movement if you modify or adjust your machine. It is specifically written to work best with the newest (091 or newer) firmware for the ORION DELTA. If you are using an older version, you can either update your firmware, or you will have to modify the firmware settings and re-upload for versions previous to 091.
Rostock MAX v2
We recommend the follow deviations from this guide
- Page 5 link error.
Click Here for RAMBO WinDrivers
- Use our recommended latest Cura slicing software setup for SE300 hotends Click Here for the setup guide
Building and Assembling Guide
Rostock MAX v2 Assembly Guide 4th Edition *
* corrections:
- page 139 click here for the new link for v2 original calibration
User Manual for operation and general setup (factory assembled machines start here)
Rostock MAX v2 Users Manual
Older versions for reference can be found below:
Rostock MAX v2 3rd Edition Manual for kits shipped between appx. 06/2015 and 10/2015
Rostock MAX v2 2nd Edition Manual for kits shipped between appx. 02/2015 and 06/2015
Rostock MAX v2 1st Edition Manual for kits shipped between appx. 03/2014 and 02/2015
Rostock MAX v2 Firmware
Rostock MAX v1 (kits shipped
BEFORE appx.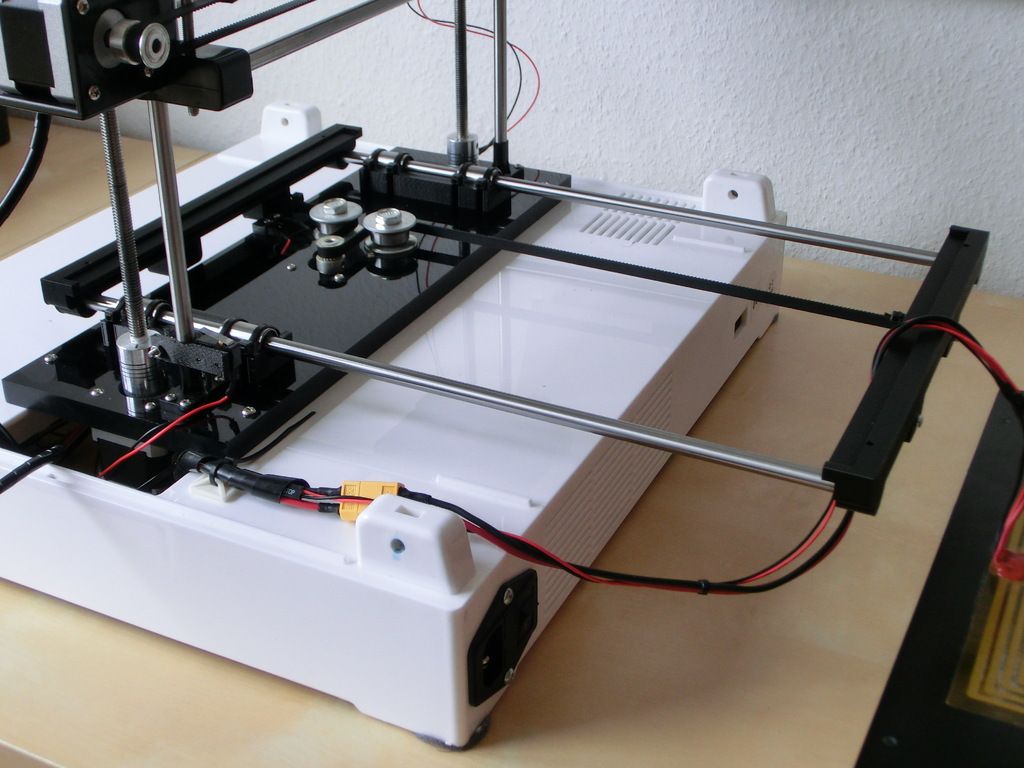
We're often asked for help when someone buys one of these original kits assembled by the original buyer. SeeMeCNC will always provide help, but realize we will only direct you back the these original assembly instructions. We are not able to teach basic wiring, soldering, electrical troubleshooting. These are all basic skills and subject matter you can search on the web. :)
The RostockMAX v1 printer kits would have been assembled by the original purchaser. SeeMeCNC did not manufacture fully assembled printers at the time these printers were sold, we only sold a parts kits. So these machines would have been wired and built by the original buyer. As such, you should carefully review all connections and wiring. Review there are genuine SeeMeCNC factory parts used on the machine (reference the manual) or you could risk fire or damage to personal property or death.
Rostock MAX v1 Assembly/Users Manual
The complete Assembly Manual and users manual for the Rostock MAX DIY 3D Printer Kit
Rostock MAX Firmware
Here's a link to the firmware for the Rostock MAX
SeeMeCNC Open Source Files
Open Source Files
MatterControl User Manual
Here's a guide to get you started with our printers and MatterControl software.
Mattercontrol User Manual
The below links are for our SeeMeCNC specific versions of MatterControl. Use MatterControl to store your stl files, create your gcode and manage your prints all in one software.
GETTING STARTED GUIDE FOR MATTERCONTROL
MatterControl Pre configured Slicing Profiles
These settings are pre-configured for great starting prints with MatterControl software.
MatterControl Orion
MatterControl Rostock MAX
RAMBo USB Driver for Windows, including Windows 8 (Will require manually installing this driver)
Linux and Mac use CDC the interface and have the hardware driver built in already
Slic3r Pre configured Settings
These older profiles were proven to be good starting points for use with slic3r on stock 3D Printers. They were taken directly from our own setups at the shop, the only thing you may need to alter is the machine tab to set it to your machine size.
PLA Profile
ABS Profile
T-GLASE Profile
More... Online User Guides
Other Guides Online
Featured Products
View
View
View
View
SeeMeCNC Rostock MAX v3.2 3D Printer - Complete Kit
Sorry, this product is currently unavailable
Perhaps some of these categories are of interest:
- 3D Printer Accessories
- 3D Printer Filament
- 3D Printer Resins
- 3D Printers
- CNC Machines
- Clearance
- Sale
- Digital Designs
- Education & Curriculum
- Laser Cutters & Engravers
- Sale
- Refurbished Machines
- Software and Add-ons
- Home
- Store
- SeeMeCNC Rostock MAX v3.
2 3D Printer - Complete Kit
The Rostock MAX v3 has been a favorite of our technicians for years because of its laser-like accuracy, and the v3.2 update is even better in every way! The massive Onyx heated bed and extremely flat borosilicate glass build plate allow you to print almost any material (print PLA, ABS, Nylon, and more!). Please note that you will be shipped a black unit.
Remove from wishlist Add to wishlist loading...
Available Add-ons (2)
Show More Addons
Product No. M-H6Q-29AV
List Price: | $999.00 |
---|---|
THE FAVORITE, WITH GOOD REASON
The SeeMeCNC Rostock MAX V3.2 is a favorite of our technicians here at MatterHackers. Why is it a favorite you ask? Because of its incredible accuracy, low layer height, consistent performance, and ability to deliver on every print job. This printer is a Delta style printer so it excels exceptionally well at printing any kind of arch or circular shape (you can't beat a delta for this kind of task). Additionally, this printer has a truly MASSIVE print volume of over 1300 cubic inches (11" Diameter by over 14 1/2" height). This is one of the largest print volumes available in the consumer 3D printing market. The Rostock MAX V3.2 printers are workhorses and can handle any task you put them up to. All SeeMeCNC Machines are proudly made right here in the USA.
This printer can print in strong industrial grade materials like Nylon and is great for industrial projects and prototyping. Enjoy the incredibly simple and efficient EZR Struder extruder as well as SD Card-ready firmware. If you like to tinker and upgrade this is the printer for you. You will find that a strong, tight-knit community of Rostock MAX owners exists online where everyone shares tips and tricks for maximizing their prints. Rostock owners are passionate about 3D printing and about making and tweaking! This is a powerful machine and it is unmatched in its price category.
Automatic Bed Leveling
SO WHAT’S CHANGED WITH THE NEW V3.
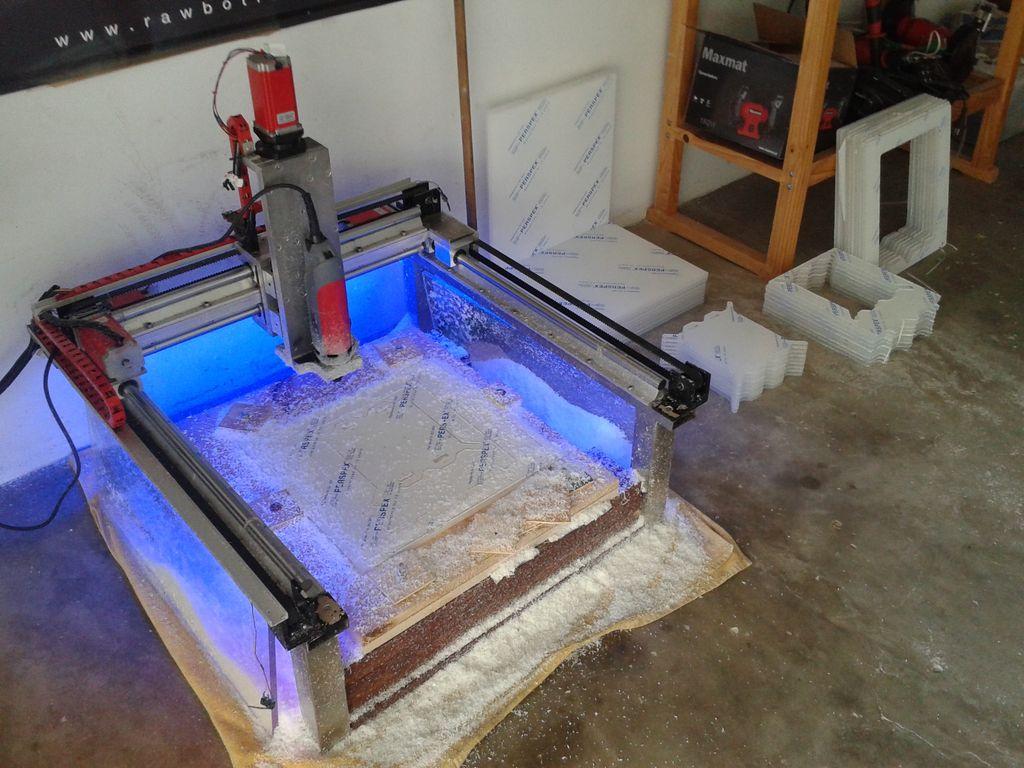
- The V3.2 comes standard with the SeeMeCNC SE300 hotend. This hotend uses a 40w heater cartridge and features thermal runaway protection. The SE300 allows you to print with any material up to 280C. (Jet Kit required for Nylons and other high temperature filaments)
- Features a 32-bit Duet WiFi controller, providing smooth motion, along with the 0.9 degree stepper motors and SeeMeCNC's Cheapskate linear motion design.
- Includes Accel probing feature for easy and accurate automatic bed leveling. This allows you to calibrate your printer with a single click!
- Enjoy the new Onyx heated bed mount which makes the bed float under the glass. This prevents warping while the bed is heated. The bed clips have also been improved to make swapping print surfaces faster than ever.
- The new EZR Struder comes standard on the V3. This new extruder accommodates faster print speeds and works well with flexible filaments.
- 3 part cooling fans keep PLA prints cool from all sides so that your parts come out looking perfect.
The new EZR Struder
DESIGNED FOR ACCURACY AND PRECISION
The advantage of the delta design is that your printed parts never move because the bed never moves. Only the arms delicately and miraculously move around the part until something beautiful and functional is created. Because this machine is so modifiable, you can buy an additional EZRStruder and you can make your Rostock a dual extruder so you can print two materials at once (fair warning it does require some tinkering and is still experimental).
Three Part Cooling Fans
QUICK NUGGETS OF INFO
- 275mm D x 400mm H Print Area
- Minimum Recommended Layer Height w/.5mm nozzle of .1mm
- Maximum Recommended Layer Height w/.5mm nozzle of .4mm
- Power Requirements 110v or 220v (input power selectable) @ 350 watts
- Max Heated Bed Temp 100c
- Max Hotend Temp 280c (hi temp jet-kit recommended above 250c)
- Max Recommended Printing Speed @.
2mm Layer Height 100mm/s
- Max Travel Speed 300mm/s
- US Made - high quality, laser cut, injection molded, and CNC machined parts
- EZRStruder and Hot-End set up for 1.75mm filament
- High torque NEMA 17 stepper motors
- 32-bit Duet WiFi controller by Duet3D, the best available 3D printer controller
- Speed up to 300mm/s in all motion, not just X/Y moves
- Tinker-friendly electronics and hardware. Many extra places to add your own mods
- Filament spool holder incorporated into the machine (for 1lb or 1kg spools only)
- Borosilicate Glass build plate for safety and precision
OVERALL MACHINE DIMENSIONS
- 18" round area on desk
- 42" tall without spool, 48" with spool mounted
- Appx. 20 pounds assembled
Quality and community are the name of the game with SeeMeCNC. The quality of the printer with the gigantic print build you get for less than $2,000 is simply unmatched anywhere else in the 3D printing industry. This pre-assembled Rostock MAX V3.2 will let you become part of the brotherhood (or sisterhood) of Rostock owners across the world immediately. These owners have one of the most active communities online today where they actively share prints, advice, tips and tricks, and loads of step by step guidance for customizing your Rostock MAX. The reason that this community exists is because Rostock owners are passionate makers and builders.
Please note that, due to its size and weight, this product cannot be shipped to a PO Box. If you have any questions or would like help making shipping arrangements, please contact [email protected].
Why the first 3D printer is worth assembling yourself / Sudo Null IT News
- It's faster than waiting from China Anet A8 for $109
- This is better (with non-crooked hands)
And finally, sooner or later you will face the need to repair / modify the printer and you will still have to master the practical skills for these devices.
And at the most inopportune moment.
And given that there were New Year holidays and long quarantine winter evenings ahead,
I bought all the necessary components in two days in three local stores, which cost the same $ 109.
And only thanks to the "Martian rule" the total amount increased by only three evergreens.
But contrary to the well-known tape from the film, I used blue (and how could I do without it) electrical tape and plastic ties.
In general, if you are only thinking of building a 3D printer - welcome under cat,
where will be my thoughts on the design and assembly of some nodes.
For there are so many detailed assembly instructions on the Internet.
So, let's start with the Martian rule - after purchasing all the necessary components, consider that you are on the red planet, and the next rocket from Earth will be in half a year.
Thanks to this, I avoided an increase in the cost of the device by at least one and a half times and still improved the quality of the mechanical part.
The only thing you can afford is to go to the neighboring manufactured goods or unscrew a spare part from your favorite moon rover is great.
Next, we will talk about assembling a Prusa-compatible Graber I3 printer, but it also applies to any device based on the RAMPS 1.4 + Arduino Mega 2560 control board. his hand and began to shake.
Correct! Without proper mechanical strength, you will either have to set the level of the printer table every time, or screw it with screws to the kitchen worktop.
From this point of view, the presence of a high box at the base adds rigidity compared to the original grabber or Annushka.
But the second time from the start I would have already assembled RepRap Mendel
Yes, the body is made of plywood, as I will have to paint, peel and drill during assembly, the main thing is not to loosen the seats giving room for backlash.
It is better to paint with acrylic varnishes - they do not stink, unless their version is sprayed.
And of course, plywood is preferable to metal in terms of acoustic comfort.
The only disadvantage of the selected ATX version of the case is the inconvenient vertical position of the screen compared to the original Graber version:
Pluses - better durability, you don't have to bother with laying wires and fixing the control board, the use of cheap ATX power supplies.
So we come to the second cornerstone issue - NUTRITION.
Our 12 volt unit should provide 20A.
Remember how you chose a PSU for your gaming/school/work PC?
By weight!
I will say right away that if you buy a new power supply from a store, it is no lighter than 1 kilo and the declared power is from 400W.
If used - look at the current and before use you should remove the cover and blow out all the dust with a compressor - at a tire fitting you will blow it out for three rubles along with cockroaches.
Go ahead, computer scientists / 3D-shniks are cool guys, but sometimes they forget Ohm's law by connecting power to the RAMPS with one, Carl wire AWG-20 (section ~ 0. 5mm sq.)
I did the right thing and made a mistake!!!
On a hot table with a power of 120W, a current of 10A simply melted the power connector
I had to dismantle it and solder the wires.
Yes, about soldering irons - the power of 60W is decidedly small: neither the old-fashioned one with a copper (thick) tip, nor the modern one with a thermostat could melt the solder in the process of soldering an acoustic wire with a cross section of 1.5 squares to a hot table.
I had to unearth an ax from the pantry:
But it will not be a crime to use a wire of 1 square and solder not 3, but 2 twisted AWG-20 wires from the power supply, then 60W is enough.
Continuing the topic of Ohm's law - You have already purchased "cheap" NEMA-17 stepper motors, it's time to look at the current consumption of the windings.
Standard model 1.66 (1.7) A, reinforced - 2 (2.1) A, "quiet / cheap" - 1.33 A, I have the last one.
The current produced by a conventional driver 4988 is up to 2Amps (even the dock does not speak to the winding or in general.
Everything seems OK, but there are two motors and RAMPS on the Z axis, and other control boards obviously contain two connectors for their parallel connection.
No, it's not scary if the R100 resistors are charred at the maximum current (there are boards with R50 for half the current).
And not even that the engines do not receive enough power (I have 0.75A everywhere except for the Z axis)
It's just that with this inclusion, the characteristics of the engines must match ABSOLUTELY, otherwise a wedge / skipping steps is possible in certain modes.
The REPETIER firmware did not cope with this at all, MARLIN got lost once at the stage of moving the extruder from the parking position at the beginning of printing.
Neither shuffling the motors nor the drivers helped.
The Z axis with two motors is saved only by their serial connection:
And oh, miracle, everything worked not on 2 amperes, but on the same 0. 75 like the rest of the axes!
Someone may reproach me for the insufficient accuracy of the assembly of the axles, and as a result, the large required force on the Z-shafts.
I will answer - with the printer turned off, turn the right / left shaft by hand - what will happen to the free one?
That's right, for most it will remain motionless, but for me, when connected in parallel due to self-induction, the second shaft also spun.
Yes, about the shafts - usually, the Graber is designed for Hozmag threaded studs m5 with a pitch of 0.8mm.
They should be lubricated with any paste-like grease for bearings - CV joint, "blue" for needle bearings, graphite and hot grease!
In general, you are on your way to your grandfather's garage / car market, or even better, take lubricant from moon rover bike chain.
Of course, you can also buy the glamorous white Molycote-DX, but this is a matter of taste.
Yes, here the "Martian Rule" saved me for the first time - I screwed up the sockets of the nuts of the left carriage of the Z axis Almost ran to buy 3D plastic X/Z carriages and "regular" trapezoidal studs/nuts But no, it turned out that you can throw away the extra / incorrect pads, and nuts on m6 are perfectly clamped between the elements of the plywood carriage: By the way, there were no stainless steel studs in the local hardware store - I took ordinary, galvanized ones. Filed off the threads a bit so they fit into 5mm sockets and bingo! The advantages of such tuning are a normally considered thread pitch of 1mm and the fact that not a threaded part, but a cylindrical part is clamped into the stepper sleeve! Yes, I recommend reaming the mounting holes of the Z-axis motors with a 5-bit drill before assembling - the distance between the guide and the threaded stud varies slightly in mounting and carriages! As a result, this leads to the fact that when moving along the Z axis, the upper ends of the pins move in a circular orbit, and the extruder shakes. In general, you need to select the position of the motors so that the pins remain on the same axis when the axes rotate (via the printer menu). In addition, many mounting holes were reamed, because the sockets in the plywood of my version of the printer are cut out for the M5 nut. Don't forget to press down on the plank when drilling from the back side, otherwise chipping of the plywood can be catastrophic. In a word, the base of the case is assembled on five-millimeter bolts!!! Yeah, and the notorious left carriage is generally assembled on screeds: The fact is that with 6mm studs and 4 fastening screws, a touch was found on their threaded parts. I didn't use 3mm screws and hope for half a millimeter, but used zip ties. This is a truly unique fastener that has replaced the wire used in the past. The only thing that screeds cannot withstand is water hammer in the country water supply. So if you're going to Mars, grab more zip ties! Now let's move on to the control board itself, or rather to the stepper motor drivers and their settings. Let's talk more specifically about the fight against noise. Someone puts expensive TMC2100 drivers in "silent" mode (by the way, you need only two of them - on the X and Y axes) But it's really all about psychoacoustics: And now let's calculate - with a microstep of 1/16, a carriage speed of 60 mm / s and a 20-tooth gear with a 2 mm belt pitch, we get a frequency of 4800 Hz !!! OMG! This is the same peak frequency of perception! Is it possible to double the microstepping (and at the same time the current in order to avoid skipping steps) by installing a DRV8825? thereby shifting the frequency range upwards. And you can show the noise of the middle finger Of course, you can completely remove the microsteps, and stop at the positioning accuracy of the X, Y axes of 0.2 mm. For most tasks, this is enough, the printer will start to "bass" at 300Hz. But it's all about individual preference and sound perception - experiment with a smaller microstep divider and find your comfortable frequency! Where the DRV8825 really comes in handy at 1/32 micro pitch is the standard MK8 extruder! If we calculate that with a 1.75mm filament and an 11mm toothed roller, on a standard 0.4mm nozzle and a 16 divider, we get a 0.2mm column of plastic per step!!! This replacement is justified only after adjusting the pressing force, extruder temperature, plastic type and stepper motor current! If you cannot ensure that the feed system operates normally without clicking and with less than half the nominal current on the stepper, this path is not suitable. Then you should either print a gear feed system or buy a "Titan", which will contradict the "Martian Rule". Has the quality improved from such tuning? At least the supports began to separate without excessive effort, which is already an indicator. To print gears and other parts of the RepRap system (partially self-reproducing printer), a certain print quality is required. But having reached it, the need for the above paragraph disappears. OK, the second most important part after assembly/setting the X/Z axis is the print table!!! Here I am not against plywood, but not for it either! Maybe the proximity of the heating element, albeit covered with thermal insulation, may have influenced, maybe the fact that I did not paint the plywood base with silver, or maybe three bearings instead of four. In general, the level of the table walked constantly, unpredictably and by 0.2 mm! And if it weren't for the "Martian Rule", an auto level would have been bought. In a word, armed with a grinder, I built a table for 4 bearings from an aluminum-polyethylene-aluminum sandwich: Now the table walks no more than 0.05 mm (I checked it with probes to adjust the valves) and I don’t even correct it for the layer 0.20/0.30 mm. Yes, the springs are mega-rigid, I took brass adjusting screws from the same table as the upper support / spring guides. And the glass of the table, it is 4 mm, because this is its main rigid element (the 1.5 mm textolite of the heater "walks" and bends as it wants). Clamps should preferably be placed as close as possible to the corners, but this interferes with the control/adjustment of the gap! And yes, my axles turned out to be longer, I didn’t cut them, but fixed them with ties - it’s more reliable! Print area is 190x180x180 (XYZ). Of course, you can radically redo everything (make the table lower, change the fastening of the belt on it, otherwise position the extruder), but for now it suits me. And a few words about firmware - I counted 8 different names, but I tried only three: At first I grabbed the second version of Marlin, hoping to switch from the Arduino Mega to the Due, which has been gathering dust in the box for a long time, but the firmware is heavy both during compilation and for the 8-bit Atmega2560. Then stuck with engines in Repetir. Teacup considered between glasses of tea - not ours how to quickly launch the 2004 screen - gave up this idea. Well, I returned to Marlin version 1.1.9, downloading separately examples of firmware from github. I came up with a fresh version from Aliexpress's Prusa_i3_MKS_Gen_2Z_V1. That's basically all my notes/remarks. Yes, the choice of filament should also be taken responsibly. Don't print out of shit Liberator! Of course, you've probably already bought a roll of ABS along with the rest of the accessories, but it's better to save it for later, and take PETj, coPET or PLA first. I bought coPET right away. The fact is that these plastics are not as demanding in terms of parameters and printing conditions as ABS. Someone even prints with them on printers without heated bed! ABS is good only for the price, but if you print in a living room not under an exhaust hood, the aroma will still be the same. Yes, and they talk about the dangers to health from its fumes, and heating the table to the desired 100-110 degrees Celsius requires titanic patience. By the way, I got the "Zaporozhets" right, up to a hundred So, having printed a skein of filament, I almost ordered a second one, but I found ABS + half the price! On it, the part behaves differently (compared to conventional ABS), the temperature of the table is 90-100 degrees Celsius, and even the first model was still printed, albeit with a tear off of the edges. After that, a hood with a carbon filter was built, a new coil holder and blowing the RAMPS power transistors. And even the edges of the parts began to stick better. It would seem that ABS + is an absolute plus, but no! On the third model, the edges of the part rose along with the 4mm glass, which predictably burst in the middle!!! Maybe the fault was a glass defect, but somehow I didn’t want to check it. Therefore, my choice is PET-plastics (PETj, coPET and others like them) - the table can not be heated at all (when using a regular PVP-based glue stick). I heat it for the first layer to 75 degrees Celsius, then - 70 in order to avoid peeling high parts. Extruder temperature - 240 degrees always, full blown from the second layer, speed - 60mm / s. If I print in the evening, I set the speed to 40mm/s, because at 60, the spirit of a black 3D printer enters the bedside table and starts slamming the doors ;-) Yes, PET is food grade — you can safely print mugs, children's toys. How long did it take? Before the first print (top) - a week, before an adequate XYZ cube that suits me in all respects - three. Would I do all this a second time? Is that RepRap Mendel V2, but under the table with a print area of 300x300 mm. For every Padawan must assemble his first May Before you start converting the CNC machine into a 3D printer, you first need to stock up on the necessary tools and materials. To print in 3D format on a desktop CNC machine, it is recommended to use a 3D printer extruder. The temperature sensor must first be replaced with a 3K thermocouple. There is a myth that it is almost impossible to convert a CNC machine into a 3D printer without professional technical knowledge. However, if you use the ready-made instructions, select the necessary materials and tools, then everyone will be able to cope with the task. To obtain a proper result, the following procedure is recommended: • Remove the spindle holder. In the holes that have become free, it is necessary to fix the adapter-corner. It is necessary in order to install and fix the print head of the 3D printer; • To fix the filament spool for 3D printing, you need to assemble a stand made of aluminum profile. It is a resistant metal that is tolerated by almost any mechanical impact; • on an existing CNC machine, you need to fix a special stand with a spool and thread for 3D printing; • install additional software; • download the Mach4 program from the official website of the developer. It is worth noting that the program does not require heavy-duty hardware for normal operation. The package contains Skeinforge software, which enables the normal conversion of 3d files to G-code; • In addition, you need to install the Russian-language interface. In this case, management becomes much easier; • Mach4mill must be selected to run the Mach4 program. • double click on the button and select "Open STL File"print addon""; • click on the file and find Open in English. It is necessary to wait until the program completes the creation of the 3D file, then the settings with printing in 3D format should open; • Next, you need to return to the Mach4 window, you must click on the Post Gcode to Mach4 button. The resulting code is easy to save. After you manage to bring the print head to the starting print location, you need to erase or reset the coordinates of the tools. Printing is started by simultaneously holding the combination ALT + R. To make your own 3D printer, you can alternatively purchase the following devices and materials: • Arduino Mega 2560. This is the main element that will be responsible for the future control of the printer in 3D format.
jumper by moving to a 1/4 microstep.
2, set only my table sizes, steps and inverted the Y direction.
accelerates heats for 10 minutes, up to 120 - nothing.
lightsaber 3D printer himself! Force be with you 3Dtoday! How to convert a CNC machine into a 3D printer?
This is the most important and preparatory stage, where you can buy cheap used devices at a lower price. When planning to turn a CNC machine into a 3D printer, anyone can significantly expand the functionality of the equipment. In order to manage the transformed machine-printer in the future, it is recommended to use the Mach4 program. To print in 3D, you need to create a file in STL resolution. It is supported by most 3D printers. If you need to convert the file format, then you can use one of the following programs: Soildworks, google Sketchup and other programs.
What to do
After the download comes to an end, you need to go to the menu and find "Wizards" select "Pick Wizard";
What materials can I buy
Learn more