Powder bed 3d printer
The Complete Guide to Laser Powder Bed Fusion in 3D Printing
Published on September 3, 2019 by Alexandrea P.
All technologies part of the Powder Bed Fusion (PBF) family use a build platform containing powder material to additively manufacture a part – the powder can be polymers or metals. It was during the 1990s that several companies began exploring Powder Bed Fusion (PBF) for metal: metal powder particles were melted using a heat source such as a laser or electron beam to form a more or less complex part, layer by layer. Today, we will focus on Laser Powder Bed Fusion (LPBF), which, as its name suggests, uses a laser to additively manufacture a metal part.
In 1994, EOS patented its process called Direct Metal Laser Sintering (DMLS), while in 1995 the Fraunhofer Institute introduced the term SLM for Selective Laser Melting. The two techniques are similar, however to avoid any confusion we will use the term Laser Powder Bed Fusion (LPBF). The terms can seem confusing, DMLS uses the word sintering when in fact it works by melting. Similarly, PBF uses the word fusion, when you cannot melt a plastic, you can only sinter it. However, Selective Laser Sintering (SLS) is part of the PBF family.
Image via Fraunhofer ILT, Aachen, Germany
What you should remember is that the difference between sintering and melting is quite simple: melting involves moving from a solid to a liquid state thanks to the high-temperature of the heat source; sintering does not allow the material to reach its liquid state because the temperature of the heat source is not high enough. In the case of sintering metal, the metal particles are agglomerated together, but the result is a fairly weak part. To illustrate this point, let’s take the example of stacking apples: there will always be a gap between two fruits. The 3D printed parts will therefore have a low mechanical strength, unlike fusion (i.e. melting) where the material, because it reaches its liquid form, fills these holes.
How does Laser Powder Bed Fusion work?
Like any 3D printing technique, the design of a part begins with the creation of the 3D model using CAD software. The part is then cut into a multitude of layers by a slicer – in this case, the thickness of a layer generally varies between 20 and 60 microns.
In order to start the printing process, the 3D printer fills its chamber with an inert gas and then heats it to the optimal printing temperature. A thin layer of powder is then applied to the build platform, according to the layer thickness previously defined by the software. The fiber optic laser (200/400 W) then scans the cross-section of the part, melting the metal particles together. When the layer is finished, the platform moves down, allowing another layer of powder to be added. The process is repeated until the final part is obtained.
The 3D printer must then be allowed to cool and the unmelted powder removed from the tray to see the printed part. The part is attached to the build plate thanks to printing supports; Unlike SLS technology, these supports are recommended because they reduce the warping and distortion phenomena observed at high temperatures. They are generally removed by cutting or machining methods or by wire electro-erosion. The parts can be heat treated to reduce residual stresses and improve mechanical properties. Further post-processing can involve CNC machining steps and polishing processes to offer a better surface quality.
Post-processing steps can be more or less important depending on the results you wish to achieve on your final part
Materials and Applications of Laser Powder Bed Fusion technology
As you will have understood, LPBF uses metallic powders to design more or less complex parts. Metallic and alloy materials such as stainless steel, cobalt-chromium, aluminium, titanium and inconel are most often used. Some precious metals (gold, platinum, silver) are sometimes used, but almost exclusively in the jewellery sector. The strength of the parts obtained is comparable to that obtained by casting or machining techniques. LPBF is one of the few additive manufacturing technologies to be used in production.
The aerospace, automotive and medical (especially dental) sectors are very fond of this technology. It offers a geometric complexity that is impossible to achieve using conventional manufacturing methods while reducing their final weight and the number of components to be assembled using techniques such as topology optimisation. This results in shorter production times and very resistant custom parts. However, metal 3D printers and metal powders are very expensive and do not allow the manufacture of very large parts.
A 3D printed metal part | Image via Mercedes-Benz
The Main Market Players
One of the technology pioneers is the German EOS with its EOS M range, which offers a complete production solution for any industrial company. The company was joined by 3D Systems in 2013 following the acquisition of the French company Phenix Systems, which specializes in the development of DMLS machines. Of course, the German company SLM Solutions, but also Trumpf, Renishaw and the Italian company Sisma are some important players. If you are looking for more manufacturers of LPBF 3D printers, have a look at our listing of the main market players of metal AM systems HERE.
Was this guide useful? Let us know in a comment below or on our Facebook and Twitter pages! Sign up for our free weekly Newsletter, all the latest news in 3D printing straight to your inbox!
All About Powder Bed and Inkjet Head (PBIH) 3D Printing
Image credit: asharkyu/Shutterstock.com
Many modern industries benefit from a type of fabrication technique known as additive manufacturing or AM for short. In AM, components are built up from stock material in a selective process and is counter to the traditional subtractive manufacturing methods like cutting, drilling, milling, etc. AM can be done using numerous methods – to see a general overview of these types, read our article about the different types of 3D printing technologies. This article will expand upon powder bed and inkjet head (PBIH) 3D printing, a process that has quickly gained traction since its beginnings. This article will explain what PBIH is, how it works, its pros and cons as an AM technology, how to choose a PBIH machine, and the common applications of this process in modern industry.
What is Powder Bed and Inkjet Head (PBIH) 3D Printing?
PBIH 3D printing was developed and patented by the Massachusetts Institute of Technology in 1993 and is the first trademarked use of the term “3D printing”. PBIH is also known as binder jetting and drop-on-powder 3D printing, which all describe the same underlying process denoted by ISO/ASTM known as binder jetting. In PBIH, a liquid binder adhesive is sprayed onto a powder bed, binding particles together into a part in a layer-by-layer process. An inkjet head (not much different than those used in 2D printers) is used to selectively apply binder onto a variety of powdered materials, such as:
- Silica sand
- Sandstone
- PMMA
- Metal powders
- Gypsum
- Food-safe powders (starch/cellulose/sugar)
- Ceramic powders
- Chromite
and other custom blends.
The binder is applied layer-by-layer until the full part is contained within the powder bed, where it is then removed and post-processing is applied according to its material. PBIH is set apart from other processes, as it uses no energy source to fuse the powder together, unlike the processes found in fused deposition modeling (FDM), stereolithography (SLA), or powder bed fusion (PBF) techniques.
Post-processing is a vital step in PBIH printing, as it will bring the part to full strength and/or visual quality. These post-processing steps can include coating, sintering, infiltrating, painting, and other procedures which will protect the integrity of the print and ensures it reaches final part strength for its application.
How does PBIH Work?
Image credit: Christian Cavallo Consulting, LLC
Figure 1: Functional diagram of PBIH 3D printers. Note that this diagram is a functional representation and may not include all components of real-world PBIH systems.
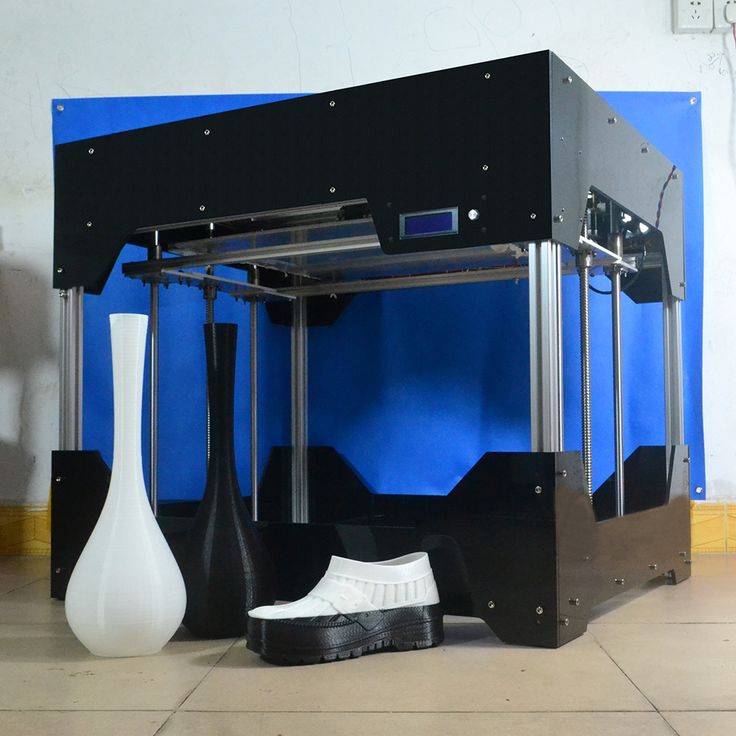
Figure 1 displays the functional components of a PBIH system – this section will use the labels found in Figure 1 to explain how the PBIH process is used to create fully functional 3D parts.
PBIH begins by creating a 3D model and converting it into a printer-friendly format (typically an .STL file) and using a so-called slicing software to cut the model up into discrete layers. This file is then uploaded to the 3D printer, and the printer’s powder supply reservoir is filled with powdered material and the inkjet is connected to a reservoir of liquid adhesive.
Powdered material is elevated from the powder stock and is applied in a thin, even layer over the build platform by the powder roller/re-coater. The inkjet printhead, guided by the 3D model layers in X-Y directions, selectively applies a spray of binder adhesive to the powder. Once this first layer is solidified, the build platform increments down (on the Z-axis), and the powder stock increments up to allow the roller/re-coater to spread the next layer of powder. This process repeats until every layer has been printed, and the part is embedded in powder in the powder bed.
The part is left to fully solidify, and it is then removed from the powder and cleaned of excess material. Any leftover loose powder can be reclaimed for future prints, though some is wasted in the printing process and must be discarded. The part is post-processed according to material specifications, as it is in the so-called “green state” post-printing – meaning very brittle and prone to breaking. Post-processing is the most vital step for PBIH printing, as these procedures imbue the part with its final aesthetic and mechanical properties. The next sub-sections will explore some post-processing procedures for different PBIH materials.
Gypsum/Starch Post-Processing
Powders made of gypsum or starch were one of the first implemented materials in PBIH printing, and it is activated using a water-based adhesive. These prints are very porous and require a process known as infiltration, where material is forced into the negative spaces within the part via capillary action to increase its strength and surface finish. In plaster parts, this infiltrant is usually melted wax, cyanoacrylate glue (super glue), epoxy, or others which fill porous zones and increase the overall rigidity of a part. After infiltration, the part may be sanded to the desired surface finish and is generally ready for use.
Metal HPost-Processing
PBIH printers have recently gained popularity thanks to their use of metal composite powders, which are mixtures of metallic particles and binder material. Parts made from these mixtures are heated in an oven post-print, where the binders disintegrate in the heat and leave behind a fully metal part. The metal particles sinter together – or fuse without reaching their melting temperature – and leave behind a porous metal structure. Parts can be used right after sintering, but most parts undergo a further step and are infiltrated by another, low-melting temperature metal such as bronze. This creates a denser, stronger composite metal part that has an attractive surface finish.
An important note about metal PBIH parts is that they shrink considerably in the heating/consolidation process. Sintered parts shrink about 20% from their initial dimensions and infiltrated parts shrink up to 2%. This shrinkage can be factored in before printing begins, but the non-uniform nature of this deformation can lead to post-print inaccuracies. Also, while these prints are full metal, they are not as strong as those made from other metal 3D printing techniques such as SLM/DMLS, limiting their usage in high-end and rigorous applications (to read more about metal 3D printing, visit our article All About Selective Laser Melting 3D Printing).
Advantages & Limitations of PBIH
PBIH is a process that has some impressive benefits for AM applications, as well as notable issues. Below are brief lists of the pros and cons of using PBIH as an AM tool, and should help buyers determine if PBIH is the right tool for their needs.
Advantages of PBIH:
- PBIH is very efficient and cheap, being over 10x more economical, especially in metal printing
- If using multiple printheads, PBIH can print full-color parts
- Parts in PBIH printing do not need support structures, as the powder bed itself supports overhangs/complex areas, and it does not need to be fused to the build platform
- Because of its lack of heat, PBIH can produce very large parts with no threat of thermal distortions (in printing at least)
- PBIH is can easily handle low to medium batch production runs
Limitations of PBIH:
- Post-processing is time-consuming, difficult, and prone to introducing errors into an otherwise perfect print
- The mechanical properties of PBIH parts (especially metal parts) are much lower than other 3D printing technologies, limiting their uses in high-end applications
- The resolution of PBIH prints is low and the surface finish of parts is rough
- Material choice in PBIH is limited in comparison to other AM technologies
- The price point of PBIH printers to buy upfront may be hard to justify, considering its downsides ($50,000-$2 million)
Selection Criteria and Specifications
This section will explain some selection criteria to look out for when considering a PBIH printer. While not an exhaustive list of specifications, this section should detail the major areas of the printer and help narrow your list of available options based on quantifiable metrics.
Build Volume & Supported Materials
PBIH printers typically have build volumes ranges shown below, based on material:
PBIH printer type | Build volume ranges |
Metal PBIH printers | 400 x 250 x 250mm to 800 x 500 x 400mm |
Full color PBIH printers | 200 x 250 x 200mm to 500 x 380 x 230 mm |
Sand PBIH printer | 800 x 500 x 400 to 2200 x 1200 x 600mm |
The first decisions to make when considering a PBIH printer are what material you will use and how large it needs to be. Ask if a given PBIH machine can handle multiple materials, or if it is dedicated to a limited set of materials. Secondly, determine the largest part you will need to print and see if this printer can accommodate it in its build volume. Note that custom/non-standard build volumes exist which may be larger or smaller than the above-generalized values.
Dimensional Accuracy & Tolerances
Most printer spec sheets will provide the minimum tolerances and dimensional accuracy of printed parts- these values will determine how loyal your printer will be to its 3D print. These values, like build volume, also change with material:
PBIH printer type | Typical dimensional accuracy |
Metal PBIH printers | ±0.2mm |
Full color PBIH printers | ±0. |
Sand PBIH printer | ±0.3mm |
Note that these values are for the printing process and may not account for the shrinkage/deformation caused by post-processing. Understand how much “wiggle” room your part dimensions have and match it to the right printer that will not supersede these maximum boundaries of error.
Resolution & Layer Thickness
Along with dimensional accuracy, the overall resolution and layer thickness of a printer will determine how detailed the print will be. PBIH systems typically have a resolution of 400 x 400 droplets per inch (dpi) to 1200 x 1200 dpi, while their layer thickness varies with the material choice:
PBIH printer type | Typical layer thickness |
Metal PBIH printers | 35 - 50 μm |
Full color PBIH printers | 100 μm |
Sand PBIH printer | 200 - 400 μm |
Physical Dimensions, Price, & Embedded Electronics
PBIH printers can get as large as a cubic meter in size or greater – this may work for a factory setting but would be more challenging for smaller workspaces. Determine the allowable dimensions of the printer to maximize build space, but also consider size restraints on your work area. Also, determine a price point that is justifiable; many PBIH printers come with on-board computer terminals, control displays, and automation features that can quickly add to its cost. Embedded electronics such as these are great quality-of-life features but may not be necessary depending upon the application.
Applications of PBIH 3D Printing
PBIH has found some important applications industry as an AM technology, some that other printers could never accomplish. Below is a brief list of common applications of PBIH:
- Pharmaceutical tablets
- Food/temperature-sensitive substances
- Full-color parts production
- Non-structural metal components
- Large sand-casting cores and molds
- High volume, low-cost components
- Rapid prototyping
and much more.
Summary
This article presented an understanding of what powder bed and inkjet head 3D printing is and how it works. We hope this article has explained what PBIH is, how it works, and how it can benefit your manufacturing capabilities. For more information on related products, consult our other guides or visit the Thomas Supplier Discovery Platform to locate potential sources of supply or view details on specific products.
Sources:
- Powder bed and inkjet head 3D printing – HiSoUR – Hi So You Are
- Additive Manufacturing: Powdered Bed & Inkjet 3D Printing – Tata Technologies PLM Solutions (myigetit.com)
- Powder bed and inkjet head 3D printing - 3D Printing - 3D Printed (partcommunity.com)
- ExOne | Binder Jetting Technology
- Understanding the Seven Types of Additive Manufacturing (firetrace.com)
- What is Binder Jetting and how does binder jetting work (engineeringproductdesign.com)
- How 3D Printing Will Change Composites Manufacturing | Additive Manufacturing
- VX1000 - Multi material 3D printer for small series (voxeljet.
com)
- Metal Binder Jetting | Digital Alloys
Related Articles:
- The Best 3D Printers under $200
- The Best 3D Printing Software
- The Best 3D Printer Under $1000
- The Best 3D Printer Under $500
- All About Material Jetting
- All About Multi Jet Modeling (MJM) 3D Printing
- All About Fused Deposition Modeling
- All About Stereolithography 3D Printing
- All About Photopolymerization
- All About Sheet Lamination/Laminated Object Manufacturing
- All About Electron Beam Additive Manufacturing
- All About Direct Energy Deposition 3D Printing
- All About Binder Jetting 3D Printing
- All About Powder Bed Fusion 3D Printing
- All About Direct Metal Laser Sintering 3D Printing
- All About Selective Laser Sintering 3D Printing
- All About Selective Laser Melting 3D Printing
- All About Selective Heat Sintering 3D Printing
- All About Digital Light Processing 3D Printing
- All About Continuous Liquid Interface Production
More from Custom Manufacturing & Fabricating
3d powder printing | Powder 3D printers
Today, 3D printing has received active development. Many different devices have been created that can create three-dimensional objects. Moreover, various technologies and materials are used for printing, including metal.
What are 3D powder printers?
3D powder printers are devices that, under the action of a laser, bind metal powder particles, creating a product in layers.
Metal 3D printing is a huge investment. The price of printers can reach several hundred thousand dollars. If you add to this the cost of maintenance and service, consumables, training and salaries, you get an impressive amount.
However, the high cost is offset by the economy of the processes. For example, in the aviation industry, up to 90% of raw materials go to waste. In the case of 3D printing, this figure will be no more than 5%. The unused powder is sieved, a new one is added to it and reused for printing.
The advantage of powder 3D printing is the ability to create products from any known alloys. In addition to the generally accepted metal compounds, there is a wide base of special alloys, products from which are made for specific customer tasks.
Purpose
About 20 tested alloys are already used in additive technology. For example, tool, stainless, heat-resistant, aluminum, titanium, etc. Such opportunities bring 3D printing to a new level, expanding its scope.
Powder printing applications:
- aerospace industry;
- large and small machine building;
- oil and gas extraction;
- electrical engineering;
- medicine and dentistry;
- food industry;
- experimental work.
Technologies
All 3D printers are divided into several main categories according to the printing method:
- 3DP - three-dimensional inkjet printing.
- SLM - selective melting of metal powder. In this case, the powder is melted by a laser to a liquid state.
- SLS and DMLS - metal sintering. Here, the temperatures are not so high, so the powder particles simply sinter, sticking together.
Popular 3D powder printers
Today, there are several companies that specialize in the production of 3D powder printers. The most popular models are shown below.
EP-M100T
Industrial 3D printer manufactured by Shining 3D. Works on the basis of SLM technology and is intended for the implementation of individual metal structures. This printer will be relevant for the production of crowns, abutments, bridges and clasp prostheses. It can also be used in jewelry.
The device supports printing with fine powders, such as nickel, cobalt and chromium alloys, copper, titanium.
Model advantages:
- One layer only 0.15-0.05 mm thick. This allows you to create high-precision models.
- Built-in software that allows you to control the parameters and workflow.
- Can be controlled by mobile phone.
- Automatic supply and circulation of inert gas.
- Multifunctional security system.
- Compact size that allows you to install the printer even in a small room.
- Low power consumption - 1 kW of energy.
Up to 110 crowns can be placed on the working platform. During the day, this printer is able to work out 3 cycles, that is, to produce up to 330 products.
Mid2019
Mid2019 is a highly detailed printer with a minimum print layer of just 0.1mm. The height of the manufactured parts is up to 220 mm.
Advantages of the model:
- The operator does not need special training, because there is already a configured program for 3D printing, where the optimal parameters are already set.
- Possibility to install a more powerful laser for higher productivity.
- Individually developed firmware designed to control the operation of components and systems of this particular printer.
- The presence of encoders allows you to stop and resume the printing process at any time.
- Remote monitoring capability.
FS301M
Farsoon FS 301M is a 3D printer based on SLM technology. It is considered one of the best in the world in terms of price and quality. At the request of the customer, it is equipped with two or one laser.
The dual scan and calibration algorithm greatly improves the quality and speed of large part production. The printer has a special inert gas supply and filtration system.
The open platform makes it possible to use all materials available today. The operator can control the operation of the system, including the sintering algorithm, temperature, laser power, layer thickness.
Model advantages:
- High quality and performance. Allows mass production without sacrificing quality.
- Integrated powder loading station. This improves security and processing time.
- Small size. The dimensions of the device help to place it even in small production areas.
- Large printing table. Allows you to create large parts in 1 cycle.
3D Systems ProX DMP 300
This printer is equipped with DMP or DMLS direct printing technology. This machine is equipped with automatic loading and disposal of materials.
This technology also uses a laser, but it melts the powder to create the desired object. The metal powder is spread on the platform by means of a special roller or a coating mechanism.
Direct printed parts have high density: 95-98% versus 70% with SLS technology.
Important! Sealed powder loading and circulation keeps it free from contamination and makes the printing process safer for the operator.
Benefits of 3D Systems ProX DMP 300:
- increased working surface with the ability to adjust the thickness of the deposited layer;
- high performance DMP technology;
- sealed loading and disposal system;
- multifunction software.
Weaknesses:
- large;
- expensive.
Benefits of 3D printing:
- Ability to produce parts with complex geometries that cannot be reproduced with traditional methods.
- Parts have excellent physical properties. Almost all known alloys are available for processing.
Disadvantages:
- The production costs are very high, so powder printing is not suitable for making parts that can be made using traditional methods.
- The list of materials available today is small and limited to the most common alloys (titanium, aluminium, 316L, Inconel 718). Other powders can only be obtained for a huge amount of money.
- Limited area of application, which does not allow the manufacture of large products.
Metal powder 3D printing has significant potential in many industries. More and more companies and research organizations are adopting this technology. For example, such global brands as General Electric, Airbus, Boeing, Michelin. They have already moved from the production of piece products to mass production.
- March 21, 2021
- 2325
Get expert advice
Specifications - Modix Large 3D Printers
Specifications (all models):
Home Info
- Print Technology - FFF (Fused Filament Making)
- Shipping - DIY kit.
The build guide includes easy-to-follow videos and interactive 3D models that can be rotated and scaled.
- Similar core concept All of our printers have the same core design based on Modix BIG-60 V3.0.
- Upgrade - New versions are developed with backwards compatibility in mind. Owners of Modix printers benefit from both configuration and hardware upgrades from time to time.
Detailed specifications
Chassis and housing
- T-Slot Aluminum Solid Profiles 40X40
- Laser Cut Powder Coated Aluminum Brackets and Hinges
- Enclosure - Enclosed enclosure made of 3mm black Aluminum Composite Panels (ACP). The case is an optional add-on for the BIG-60 and BIG-120X and is the default option for all other models.
Duet 3D Printer Controller
Duet 2 WiFi Powerful UK Made 3D Printer Controller
- Powerful 32-bit processor
- Dedicated Wi-Fi module with external antenna
- Quiet TMC2660 stepper motor drivers, up to 256 microsteps.
- High-speed USB memory stick and support for a second external SD card if required.
- Dual extruders controlled on main board, up to 5 additional stepper motor drivers controlled on expansion board.
- High Power: Each stepper driver supports 2.8A motor current, currently software limited to 2.4A.
- Access to the printer via a PC, tablet or smartphone on the local network.
- Web printer setup and management.
Interfaces
touch screen
- 7-inch sensor screen Duet3D, integrated with a controller
Web Interface
Tilt Screen & Emergency Button
Tilt Screen
Tilt Screen is a “convenience” designed for our tallest machines: Modix BIG-Meter and Modix-120Z, but compatible with all our printer models.
Emergency reset button
Along with the upgrade to the tilt screen, the emergency reset (soft reset) button is now located on the front of the machine. This control and safety feature will allow you to immediately stop printing when needed.
* These two features are sold as one combined add-on.
Movement system
- Linear guides HIWIN MGW9H
- Four Z ball screws for movement along the Z axis. Diameter 12 mm, pitch 4 mm.
- Gates GT9 timing belt 2mm wide, glass fiber reinforced
- Axial motors: Motech Nema 17 60mm long MT-1705HS200A.
Holding torque 8.2 kg/cm (114 oz/in). Current/phase: 2.00 A+ - Mechanical positioning accuracy: X-10 micron, Y-10 micron, Z-0.5 micron
- Print speed - normal quality 60 mm/s, draft 100 mm/s, calculated for 0.4 nozzle. Larger nozzles are usually required for slower printing, but parts are made much faster due to fewer layers.
Power supply
- Support both 110V and 230V
- For electronics: Meanwell 24V 280W power supply
- Protection: against short circuit / overload / overvoltage / overheating.
- Power consumption without load <0.5 W
- LED power supply indicator
- Aviation class
- Protection: against short circuit / overload / overvoltage / overheating.
- Heating heating from alternating current
- Controller of the PID heater PID from AUTONIC PID from Autonic connections 208-240V 32A
- North American customers: NEMA L6 30P 30A outlet
- EU / AU / UK customers: IEC 309 32A socket, blue (2P + E)
- Tripp Lite PDU for meter and 180x
- For North American customers: https://www.tripplite.com/ support/PDUh40HV.
- EU/AU/UK customers: https://www.tripplite.com/support/PDUh42HV
Print bed
- Alcoa Mic6.35 cast aluminum plate 6 mm thick, made in USA.
- 1370W AC powered bed heater (1,200W for 110V users). Requires a dedicated independent 15A AC source.
- Dual heating zones. Internal size 200X200mm for small objects and low power consumption.
- Maximum temperature - 110 o in (with housing)
- Print surface - PEI film with 3M high temperature adhesive.
Removable magnetic bed
This add-on will greatly improve the user experience and save you time every day. Modix printers come with PEI sheet by default, which allows sheets to be printed after the table has cooled to room temperature. With the addition of a detachable magnetic platform, users do not have to wait or work hard with a spatula, and they can easily and immediately remove objects after completing a print job by simply bending the spring steel plate.
This add-on includes an adhesive magnetic sheet to be attached to the aluminum base plate and a removable spring steel plate to be placed on top of it.
Flexible spring steel plate can be printed on both sides. One side is PEI powder coated giving a textured underside and the other side is covered with a smooth PEI sheet giving a glossy underside.
Another benefit is that the PEI installed on the baseplate can degrade over time during maintenance. Removing the print with a spatula can cause unwanted scratches that will later appear on the bottom of the printed object. It is much easier to replace the PEI on a removable spring steel or even buy a spare block than to remove it from the bed itself.
Automatic bed leveling
- BLTTouch probe
- Bed shape detection is stored in the controller memory and activated before each print.
- Probing grid: Big60 - 100 points, 120X - 200 points.
* The photo on the right shows the calibration process interface. These results indicate that the rear left bed support needs to be moved up slightly.
Automatic calibration extension
This add-on improves user experience by automating calibration procedures. With this add-on, you now have automatic print bed tilt calibration (Z-axis) and automatic gantry alignment (X-axis).
This upgrade comes as a new controller box that has an additional electronic board called the DUEX-5 expansion board that doubles the total number of stepper drivers from 5 to 10.
By dedicating a dedicated driver to each of the Z and X motors, each of which can be micro-adjusted up and down, allowing the tilt of the bed to be adjusted at the touch of a button.
This type of control box is already included by default in BIG-Meter and BIG-180X and is now available as an optional upgrade for BIG-60, BIG-120X, BIG-120Z and BIG-40.
The update includes a fully wired new electronic box with a Duet 2 WiFi controller, Duex-5 expansion board, wires for all motors and an additional X axis stop. You can leave your default electronic box as a spare/backup.
* Will only work on V3 models.
Georadar software
- Open source Duet RepRap firmware. Leading 3D printing firmware allowing for multiple configurations and easy customization via the macro system.
- Any available slicer and 3D printer controller can be selected, including Slic3r, Cura and Simplify3d (recommended).
Specific printer configurations are shipped in the customer area.
Griffin Printhead
The new Griffin printhead, previously an optional upgrade and now the default printhead on all of our printers, is a significant improvement to our offering. It consists of a custom made Bondtech extruder (based on the BMG model) and a new hot end designed by Modix. The new design comes standard with every Modix printer and includes the following enhancements:
High Flow and High Print Temperature: The Bodtech extruder is equipped with a dual drive system that picks up the filament from both sides. The thermal block is made of nickel-plated copper for improved heat transfer rates and compatibility with higher printing temperatures. The design includes Slice Engineering's advanced bimetal thermal break, which expands the melt zone inside the fuser, as it is also primarily made of copper. In addition, the upgraded PT-1000 temperature sensor allows printing at higher temperatures up to 500°C. The hot end components are rated for 500°C and have so far been tested for printing up to 340°C.
Higher reliability: Large-scale 3D printing typically runs the risk of scratching or hitting the printhead on thicker models, causing thermal breaks to bend or break. The new print head provides a rigid mounting of the fuser, which is naturally more reliable and reduces the number of such situations. The main reason for this is that now the heat block is attached on three sides, and not just on one. With this extra mount, it can withstand a much stronger impact. The longer E3D Super Volcano can also be attached to a hard mount using a dedicated adapter (Late Summer 2022)
Improved user interface: New print head design makes changing nozzles easier. The rigid fastening of the thermoblock allows you to change the nozzle with one hand, which makes it even easier to switch to a nozzle of a different diameter.
Easy Exchange: The design of the mounting bracket and D-rod of the Slice Engineering thermal fuse allows users to easily replace the entire filament melting subsystem. This will allow users to allocate full customization to a specific filament type. those. leave one setup for abrasive carbon filler and another for prototyping with PLA.
Compact design: The new design retains the benefits of a compact design that maintains high Z-axis travel and is compatible with a wide range of E3D Volcano tips in a variety of sizes and materials.
Smart: The new printhead allows automatic calibration of the Z offset between the nozzle and the BL Touch sensor. It is easier and more accurate than the manual procedure. A special sensor allows the BL-Touch and the nozzle to touch the surface. The exact relative distance between probe and nozzle (“Z-offset”) is automatically stored in the printer.
*Brass nozzle must be replaced with a nozzle capable of operating at higher temperatures, as well as at temperatures above 300°C.
Primary extruder Griffin
included:
- Gryffin Hotand
- temperature sensor PT 1000
- heater
- silicone sock - made to order extruder BMG bondtech
- metal um duct and brackets
– Z calibration probe with offset
Secondary extruder Griffin
included:
- Gryffin Hotand
- PT -000
heater - silicone sock
- Mirror Extra brackets
- Fan, duct and brackets
Standard and optional hot end configurations
- Our standard Griffin hot end is compatible with E3D Volcano high flow nozzles.
By default, we offer brass Volcano nozzles with a diameter of 0.4, 0.6 and 0.8 mm.
- E3D offers a wide range of compatible Modix tips, including tips that can handle abrasive fibers such as carbon fiber or metal-filled fibers.
- Our hot end and extruder are suitable for 1.75 mm filament.
- Heater cartridge 24V 50W, default maximum temperature 285°C. Can be converted to higher temperature up to 500°C
- The Griffin extruder is also compatible with two alternatives of the E3D hotend, we sell both as add-ons:
- E3D-V6 with a shorter fuser for detailed printing
- E3D Super Volcano for XL high performance printing.
High-flow E3D Super Volcano add-on
for fast printing of large bulky objects.
E3D V6 with shorter heater block for detailed print jobs.
Dual printhead
The secondary printhead allows you to print complex models that require easy support removal. those. models with internal geometry. For such print jobs, it would be better to use an optional print head that can print with dissolvable filaments that can be removed with water.
Clog Detector
Previously an optional add-on, it is now installed by default on every printer and improves printer reliability. The clogging detector is equipped with a special high sensitivity encoder capable of detecting the following potential faults:
- Hot end clogs
- Filament spools
- Filament outlet
- During extrusion, for example when the nozzle temperature is too low or the nozzle is too close to the bed.
When a failure is detected, the printer is suspended and the print job can be saved. No more discovering a printer that prints in the air!
This add-on is provided as a replacement for the current filament runout sensor. Consider purchasing two units for a dual printhead configuration.
* Requires Duet controller, will not work on models without V2 updates.
Fault Detector
Formerly an optional add-on, now installed by default with every printer, provides an additional layer of security in the rare event that the BL-Touch Platform Leveling Sensor fails and the failure is not detected by the printer controller. In this case, the detector will prevent the print head from colliding with the base.
Active Air Filter
The Modix Active Air Filter (MAAF) is an external air filter. The filter cleans the printer chamber by trapping microparticles and gas vapors that are released from the melted filament during the 3D printing process. MAAF provides constant air purification throughout the entire printing process by circulating air in and out and back into the printer, cleaning it repeatedly.
Multilayer Filtration
A large fan inside the machine draws air out of the printer through a flexible vent tube connected to the top of the machine. The air then passes through a set of three filters before it is returned to the printer.
Triple filter system includes
1. Prefilter - Remove large dust particles from the air.
2. HEPA Filter - High Efficiency Particulate Absorption (HEPA) filter, consisting of a mat of randomly arranged glass fibers designed to trap the smallest particles emitted during printing.
3. Activated carbon filter - Purify the air of toxic fumes released during the 3D printing process.
It's about your health!
Submicron particles and vapors released during the plastic melting process are hazardous to your health. Therefore, every owner of a Modix 3D printer is highly recommended to install an air filter. The air filter is a MUST HAVE add-on if you are going to print with any plastic other than PLA e.g. PETG, ABS... While it is common knowledge that printing PLA in a well ventilated area is fine, there is no clear definition of proper room ventilation in winter and summer times the windows are usually closed.
Air speed control
The front speed switch allows you to control the air flow speed. Running the filter at the lowest speed during the printing process will not affect the temperature inside the chamber while still providing effective filtration. Towards the end of the print, you can set the maximum speed for a few minutes to ensure that the entire chamber is completely clear of any harmful additives that open the doors.
Spare filters
Based on daily use of the printer in a clean room, the HEPA/charcoal combo filters last 6 to 12 months and the prefilter lasts 3 to 6 months. There is a replacement warning indicator on the front panel.
Power Distribution Unit (PDU)
The PDU is included by default with the BIG-Meter and BIG-180X due to their high current requirements. Because we found this to be a very convenient cable management solution, it is now available for all other models*. Replace 3 AC cables with only one cable connected to the wall.