Make magazine ultimate guide to 3d printing
The Ultimate Guide to 3D Printing - Stadtbibliothek Bremen
The Ultimate Guide to 3D Printing - Stadtbibliothek Bremen - OverDriveError loading page.
Try refreshing the page. If that doesn't work, there may be a network issue, and you can use our self test page to see what's preventing the page from loading.
Learn more about possible network issues or contact support for more help.
Search Advanced
It’s no exaggeration to say that 3D printing is changing the world. It’s the kind of technology that sounds a little bit like magic when you first hear about it: it allows designs created on a computer to be turned into physical objects by a specialist machine that you might imagine belongs on a spaceship. This guide is designed to tell you everything you need to know about 3D printing. We’ll explain the origins of 3D printing technology, explain how it works and help you take your first steps into designing and making something yourself. You don’t need to have your own printer at home, but if you do fancy buying one, we’ll tell you a bit about all the options available to you. And once you’ve made your first few prints, we’ll show you ways you can improve your skills and make more elaborate objects. We’ll also look at the many ways 3D printing is being used in the world around us – from 3D printed dresses to 3D-printed rocket parts (and you’ll find more over at our website – (www.3d-printing.net.) Ready to jump in?
- Details
Frequency: One time Pages: 148 Publisher:
Dennis Publishing UK
Edition:
The Ultimate Guide to 3D PrintingOverDrive Magazine
Release date: March 18, 2014 - Formats
OverDrive Magazine
- Languages
English
Availability can change throughout the month based on the library's budget. You can still place a hold on the title, and your hold will be automatically filled as soon as the title is available again.
The OverDrive Read format of this ebook has professional narration that plays while you read in your browser. Learn more here.
Your session has expired. Please sign in again so you can continue to borrow titles and access your Loans, Wish list, and Holds pages.
If you're still having trouble, follow these steps to sign in.
Sign in
The library card you previously added can't be used to complete this action. Please add your card again, or add a different card. If you receive an error message, please contact your library for help.
Add a card Contact support
Magazines - The Ultimate Guide to 3D Printing - Bibliothèque et Archives nationales du Québec
Magazines - The Ultimate Guide to 3D Printing - Bibliothèque et Archives nationales du Québec - OverDriveError loading page.
Try refreshing the page. If that doesn't work, there may be a network issue, and you can use our self test page to see what's preventing the page from loading.
Learn more about possible network issues or contact support for more help.
Search Advanced
It’s no exaggeration to say that 3D printing is changing the world. It’s the kind of technology that sounds a little bit like magic when you first hear about it: it allows designs created on a computer to be turned into physical objects by a specialist machine that you might imagine belongs on a spaceship. This guide is designed to tell you everything you need to know about 3D printing. We’ll explain the origins of 3D printing technology, explain how it works and help you take your first steps into designing and making something yourself. You don’t need to have your own printer at home, but if you do fancy buying one, we’ll tell you a bit about all the options available to you. And once you’ve made your first few prints, we’ll show you ways you can improve your skills and make more elaborate objects. We’ll also look at the many ways 3D printing is being used in the world around us – from 3D printed dresses to 3D-printed rocket parts (and you’ll find more over at our website – (www.3d-printing.net.) Ready to jump in?
- Details
Frequency: One time Pages: 148 Publisher:
Dennis Publishing UK
Edition:
The Ultimate Guide to 3D PrintingOverDrive Magazine
Release date: March 18, 2014 - Formats
OverDrive Magazine
- Languages
English
Availability can change throughout the month based on the library's budget. You can still place a hold on the title, and your hold will be automatically filled as soon as the title is available again.
The OverDrive Read format of this ebook has professional narration that plays while you read in your browser. Learn more here.
Your session has expired. Please sign in again so you can continue to borrow titles and access your Loans, Wish list, and Holds pages.
If you're still having trouble, follow these steps to sign in.
Sign in
The library card you previously added can't be used to complete this action. Please add your card again, or add a different card. If you receive an error message, please contact your library for help.
Add a card Contact support
how 3D technologies will lead to a cultural revolution - T&P
3D printing methods are now developing so rapidly that what seemed impossible a few years ago is already being embodied in specific technologies.
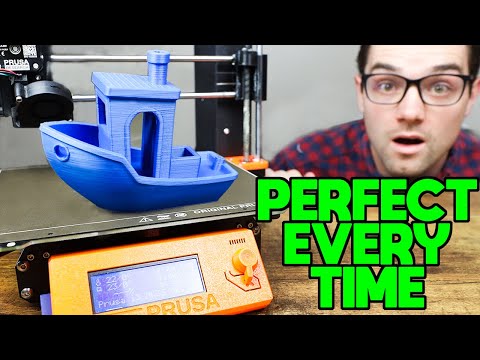
3D printing is a colloquial name for modern digital additive technologies that are part of a new type of production. To better understand the essence of this method, it is necessary to understand that there are two main ways to produce something. The first is with the help of machining, gradually getting rid of everything superfluous: cutting, beating, drilling. The second one is additive, gradually adding material and building up the required shape. nine0005
A year and a half ago, in my predictive study "Elastic City", I tried to imagine how various areas of urban life would change, including manufacturing and the economy with the development of additive technologies. One of the schemes obtained in the work reflects the sequence of changes that occurs and will occur with the transition to 3D printing. It shows how a gradual transition from industrial mass production to individual production in a home or office environment can take place. Approximately the same changes humanity observed when office and home printers appeared. nine0005
The ability to print products directly at home or in a neighboring office changes the very culture of ownership and eliminates the need to accumulate things.
The ability to print products directly at home or in a neighboring office changes the very culture of ownership and eliminates the need to accumulate things. It will be valuable not to own a thing, but its information model and the ability to print it using some materials that are unique in their properties. Possession of digital information will allow you to reproduce the product again and again at any time. Ultimately, an economic and environmental environment can be formed that will act like a natural biosphere - when an outdated object is immediately recycled to meet new requirements. In this case, it is not the number of products that determine the modern understanding of the standard of living that becomes more important, but the number of alterations associated with the energy spent and depreciation of machines. nine0005
To understand what designers and technologists around the world are trying to develop the ideas of 3D printing, it is worth watching the wonderful animation created for the Full Print3d Printingobjects exhibition, held at the Disseny Hub, a hybrid museum and laboratory in Barcelona.
The Economist article The Printed World quotes Terry Wahlers, a 3D printing researcher. He says that at the moment more than 20% of the products produced on 3D printers are the final products, and not the prototypes for which the technology was invented. Wohlers predicts that final product production will rise to 50% by 2020. nine0005
It can be assumed that growth will be much more intense: this will be associated with the introduction of new methods of production from various kinds of materials and the capture of new areas of industry. For 3D printing technology to be available as an attribute of the home or office, it needs to be cheap, easy to use, and provide something that can't be obtained any other way. One of the main advantages of 3D printing is the real-time response to needs.
Recently, HP launched a line of their own 3D printers, reflecting the interest of small firms in these technologies - companies are buying machines, despite the hefty price of $17,500. In contrast to such giants as HP and Z Corporation, there are alternative open-source projects like MakerBot or Fab@Home. They make printer assembly kits that start at just $1225. nine0005 The European Aerospace and Defense Group (EADS) used an additive layering process that combines 3D printing with laser technology to create the Airbike, a ready-to-ride printed nylon bike. The prototype shows a fully functional vehicle - as good as the one you can buy in a store.
Compared to industrial 3D machines, such printers, of course, have a lower quality of product detailing, but they are very versatile in the choice of material. For example, they can be used to print with plastic, silicone, cement, cookie dough, or even cheese. Thus, the field of 3D printing is captured from two sides: global companies and global ideas. nine0005
The next direction that takes us into the printed future is connected with the emergence of a studio like Freedom Of Creation (FOC), which was founded by Janne Kittanen 10 years ago in Amsterdam. They were among the first to create their own design, which could not be produced in any other way than additive. “When we started, everyone thought I was a sleepwalker,” says Janne, who is interviewed at least once a month, now. The method of the studio's work is that it gives a design task, and any designer can offer a solution. After that, an agreement will be drawn up for the use of his project, and the product will be translated into reality. 3D printing technology allows you to get rid of the long process of engineering and manufacturing fine-tuning of the product. nine0005
A huge step in this direction was the emergence of sites like Shapeways and I.materialise, which allow anyone to upload a three-dimensional file to the site, immediately change the scale of the product and select the material from which it will be made, and then order their product and wait, when it arrives in the mail.
The design studio Nervous System works on a similar principle, specializing in the creation of jewelry. The design of jewelry is generated using a computer, and production is carried out using digital technologies, including additive ones. nine0005
In the company's online store, you can choose between ready-made solutions and prototypes that can be customized using simple interactive applications. In fact, the buyer receives a unique piece of jewelry printed exclusively for him.
Interior details and furniture is also one of the main uses of 3D printing. It is impossible not to note the pioneers of a new attitude to the creation of furniture - the FRONT studio and their Sketch Furniture concept, created in 2006. It shows a new way of designing furniture: the user draws it directly in the air with a special pen, the trajectory of which is captured using motion capture technology. Next, the digital information is transmitted to the computer, which instructs the printer to print the received objects based on the generated model. nine0005
The aforementioned FOC also makes a lot of interior products, but the studio's real breakthrough came when Janne Kittanen created 3D fabric prototypes. The concept of fast-produced textiles was developed back in 1999 by Jiří Ivenhuis. 3D printing has allowed the creation of continuous weaving patterns not possible with traditional textiles.
Printers allow anyone to create their own mechanisms and immediately bring them to life, in connection with which there are applications that simplify the design process. Sneak Peek is a small program for simple modeling of any mechanism for subsequent printing of elements on MakerBot. nine0005
But a more interesting property of 3D printing is that it allows
to create mechanisms immediately - without the need to assemble them from separate parts. In
printed movements, all the parts are already in place and ready to work as soon as the excess raw material is removed. This eliminates the need to invent sophisticated assembly procedures and create couplings that have no analogues in traditional mechanisms. This property is used to create movable prosthetic limbs developed by Bespoke. nine0005 Industrial design specialist Scott Summit and orthopedic surgeon Kenneth Trauner of [Bespoke](http://www.bespokeinnovations.com/) have developed a custom prosthetics technology based on rapid prototyping technology using 3D modeling technology.
3D printing has also influenced architecture. For many years architects have been experimenting with scale models using digital manufacturing processes to find form. Fabio Gramazio and Matthias Kohler from the Swiss Federal Institute of Technology examine architectural artifacts built with an industrial robot commonly used to assemble cars and perform various high-precision tasks. Its precision, strength and speed enable them to build architectural forms of unprecedented complexity. nine0005
Dr. Behrokh Khoshnevis of the University of Southern California is developing Contour Crafting technology to print entire buildings.
Gramatio and Kohler's work is currently exploring the potential of mobile digital manufacturing techniques that allow one-to-one production of an object right on the construction site. The place of the classic 3D printer here is occupied by a robot: instead of a print head, we see a manipulator that sequentially adds material to the product. nine0005
Brick, the most common building material, is becoming the raw material for cutting-edge digital building experiments. The New York Pike Loop project is a 22-meter-long structure built on a construction site by an industrial robot mounted on a movable cargo trailer. More than 7,000 bricks form an endless loop that winds along the pedestrian safety island.
The structure is built with an R-O-B robot installed in a movable shipping container. Brought from Switzerland to New York and delivered on a low bed trailer, the R-O-B was transported for on-site production. nine0005
New software allows architects to quickly come up with and design structures, but existing construction methods do not allow the full potential of the new software to be realized. This makes architects and engineers think about finding new production solutions.
Dr. Behrokh Khoshnevis of the University of Southern California is developing a technology that allows entire buildings to be printed. Contour Crafting is a method of layering buildings from ceramic material, which has great potential for automating the construction of entire structures or individual structural elements. Using this technology, you can build each individual house or series of houses according to your own individual project. At the same time, everything can be built automatically in one go - taking into account all the necessary pipelines for electrical wiring, sewerage and ventilation. nine0005
The D-Shape system developed by Enrico Dini can be considered the most innovative in building printing today. This new mechanism makes it possible to create a full-sized sandstone building without human intervention using a stereolithographic printing process that requires only sand and a special inorganic binder. This component transforms sand into a mineral with microcrystalline characteristics, which works in compression and tension much better than Portland cement, which makes it unnecessary to use reinforcement to reinforce structures. Such material is indistinguishable from artificial marble and chemically one hundred percent friendly to the environment. nine0005
Despite the higher binder cost compared to traditional materials, the final cost of a structure printed with D-Shape is 30-50% less than with a manual construction method.
The system is designed to deliver up to four times faster construction time than
traditional building methods. The annual production capacity of the first (small) model machine is 2,500 square meters, equivalent to a 1,220-story building. Despite the higher binder price compared to traditional materials, the final cost of a structure printed with D-Shape is 30-50% less than with a manual construction method. The image shows an element printed by D-Shape that will become part of a villa in Sardinia. nine0005
The world's most innovative universities are developing alternative ways to print buildings. At the Architectural Association in London, a group of students are developing an underwater method. Based on the study of the behavior of materials in the logic of digital manufacturing, the Fluid Cast project explores a technology that can help material transition to a different state of aggregation - using water as a catalyst, causing them to solidify. The goal of the project is to develop a digitally controlled building system that will instantly form structures in water. The project also has the potential to reflect on the sea as a development environment that opens up a wide range of possible applications. nine0005
There are creative groups that are trying to look far ahead and assess how 3D printing technology will develop in the future. Columbia University's GSAPP School of Architecture has been running the (N)certainties lab for several years running under the direction of François Rocher, one of the most futuristic architects of the modern era.
Intermediaries are no longer needed - it will be cheaper to download the file, adjust the parameters, go to a small company near the house and print the desired item. nine0005
The share of energy consumption for transport is one third of the entire structure of the economy. And the share of logistics costs in the price of goods in different countries varies from 10 to 40%. The development of 3D printing technologies is at least a good opportunity to cut costs by removing unnecessary intermediaries. It will be cheaper to download the file, adjust the parameters, go to a small company near the house and print the desired item. And to build a house, you do not need to call workers and construction equipment, just call one construction robot, which will print a house from the material found nearby according to the project that you and your friends created on the Internet. It turns out a kind of globalized locality, which will lead to large and exciting changes in society. nine0005
quick tips for moving from a CAD model to a printed object" from CADmaster #1(92) 2020
At the heart of the 3D printing process - whether it's just a hobby or a source of income - is always the design of the product. For those who are used to traditional
Once the design is complete, there are a number of additional steps that need to be taken to set the orientation of the model and other parameters to ensure that the printing process will run properly. choose the degree of filling of the model with cellular structures.The correct choice of this parameter ensures the protection of the object from deformation and destruction during the printing process, as well as significant savings in material and reduction in production time.0005
Finally, the last factor that influences the success or failure of the 3D printing process is the strength of the connection between the model and the table. If the workpiece separates from the table during printing, then all the work will go down the drain.
Here we will talk about 3D printing processes and provide some simple guidelines for using the possibilities of additive manufacturing at the design stage. In addition, we will dwell on the methods of preparing a finished project for printing, and also consider ways to securely fasten the workpiece to the table. nine0005
These guidelines apply primarily to Fused Deposition Printers (FDM) printers, but may also apply to other types of printers. The process of obtaining a finished part by 3D printing is basically the same regardless of the method used.
Designing an object
Any 3D printing starts with design. If you are developing a product yourself, then you need to build its 3D model in a computer-aided design (CAD) system in order to turn the designer's idea into reality. In this case, the object can be both very simple and very complex. However, models that are too thin and too small should be avoided. nine0005
Saving the file in a special format for printing
To print an object, its model must be saved in a file of a special format - for example, STL, which has become the de facto standard in the world of 3D printing. In this format, model surfaces are represented as a grid of triangles. Simple surfaces are broken down into a small number of triangles. The more complex the surface, the more triangles you will need. Today, 3D printing also uses other formats, in particular, the 3MF format developed by Microsoft. But the most common is still STL. nine0005
CAD systems make it very easy to save the model in the desired format: just execute the command Save as . To improve print quality, it is desirable to set a number of settings for saving to the STL format - for example, the conversion tolerance and the angle of the plane. The smaller the conversion factor and the better the angle, the smoother the printed part will be.
Opening a file in a slicer program
Most, if not all, 3D printers come with their own slicer software. The slicer loads the STL file created in the CAD system and cuts it into layers, and then creates a control program for the printer. nine0005
Correctly placing the model in the print space
After entering the print settings, the model (or several models) needs to be placed on the printer table. You can print many objects on one table at once. At the same time, compared to printing one object, the time slightly increases, but in general it still turns out to be less. Here are some tips for choosing the right model orientation.
Setting parameters
In the slicer software, the user sets parameters such as print speed, material consumption, nozzle and desktop temperatures. Most slicers have simple settings for beginners. However, most often there are also advanced settings so that experienced professionals can achieve optimal results. Advanced settings include infill percentage, amount of support material, and type of support substrate or raft (this is a small, thin base that keeps the printed part stable. The substrate is removed when it is finished). The number of options is truly endless. Specific setting values vary by printer brand. It's easy enough to set them up. nine0005
Sending the control program to the printer
After setting the print parameters, the placement of future objects on the table, their orientation and quality, it's time to finally start the printer. Just press the button Print and find something to do while the production is in progress. Depending on the complexity of the design, the process takes from several minutes to several hours.
Finishing
Finishing includes removing the printed part from the bed and removing the support material by melting, mechanical separation or dissolution (depending on printer design). The part may require light sanding or polishing, but in general a properly printed object looks good from the start. Other types of finishing are placing plastic parts in a container with acetone to smooth out surface roughness, gluing (if the design dimensions exceed the dimensions of the 3D printer or individual elements of the object must have different orientations), drilling holes and painting. nine0005
3D printing process
Considering the capabilities of a 3D printer when designing
Eliminating sharp corners
If the direction of the surfaces changes abruptly (for example, a vertical wall intersects with a horizontal overlap), then such a model is difficult to print. The printer will build excessive inner surfaces, wasting too much material. There are two easy ways to prevent this: add chamfers to smooth out where the surfaces meet, or round the corners so the printer gradually builds a vertical surface. In addition, rounding will increase strength, since destruction most often occurs at sharp corners. nine0005
Eliminate thin walls and small geometries
Layer by layer fusion technology consists in feeding hot plastic through a nozzle to form the printed object layer by layer. The thickness of the extruded plastic layer cannot be made less than a certain limit, depending on the diameter of the nozzle and the speed of the print head. Excessively thin-walled parts are difficult to print - often resulting in a chaotic weave of fibers. If the part can be printed, it turns out to be very fragile and breaks easily. nine0005
Too thick walls - also bad
On the other hand, if the walls are too thick, they become brittle and crack easily. This is especially important when printing from materials other than polymers, as during the manufacturing process, excess thickness leads to the appearance of internal stresses in the part. Even when printing from plastics, too thick walls waste material with a lot of time.
Eliminate large overhangs
3D printers can create amazing shapes and surfaces, but they can't print directly in the air. If the part has a void with material above it, you have to use additional support material. Most slicers add material automatically, but require you to specify the orientation and volume of the support structure. Printers with a single nozzle create an array of thin columns, which then have to be broken off. The result is an insufficiently smooth surface. Therefore, it is recommended to avoid large overhanging elements whenever possible in order to reduce the need for support material. nine0005
If such an element is unavoidable, you can try to flip the object. Most printers are capable of printing overhanging elements with an angle of about 45 degrees. At a certain height, the edge of such an element may sag somewhat. The actual capabilities of a particular printer are determined by trial and error.
Holes shrink
Remember that the part is made of heated plastic. As it cools, it inevitably shrinks. Therefore, holes and other critical structural elements have to be made larger so that after shrinkage their size is as close as possible to the required one. nine0005
However, if you need to make a hole with a tight tolerance, it is better to print it with a smaller diameter and then ream it with a suitable tool. This is especially true for holes whose axis is parallel to the printer table.
Increasing the support area
If the area of contact between the object and the base is small, the part may separate from the table during printing. To prevent this from happening, wide bases are added to the model supports, which are installed on the printer table. In general, the closer to the table, the more material must be added to the support. There are other ways to securely fasten the part to the table, which we will discuss a little later. nine0005
Special Techniques
The right approach to design makes printing easier. In addition, there are special post-processing techniques that are important to be aware of.
Placing round surfaces vertically
The model should be oriented so that the minimum amount of support material is used. Ideally, it should rest on the table with a large flat edge. In addition, circular geometry must be placed so that the circular faces are vertical. If we look at the printer table from above, we should see a round silhouette of the object. In this case, the part comes out as symmetrical as possible with the formation of a solid round structure. nine0005
Placing voids and holes vertically
If there are voids in the model (for example, it is a rectangular pipe), it is desirable to place such voids vertically in order to reduce the amount of support material. If you print a pipe in a horizontal position, then you will have to provide support for the entire internal part. If you put the pipe on the end, then no support is required at all.
The same is true for holes: to get a hole with a straight axis, it is best to print it vertically - in the form of a stack of rings, which avoids warping or deforming a round hole into an oval one. nine0005
Setting print quality parameters
Proper selection of print parameters, such as STL conversion tolerance and slicer program settings, allows you to produce parts with a surface quality that matches that of cutting. However, this entails an increase in print time. When choosing quality parameters, one should proceed from the purpose of the object: is it a finished product or a prototype? Will the part be visible or hidden? nine0005
The quality parameters also affect the shape of the holes in the part. In CAD files, holes are represented as a set of straight lines at an angle to each other. The higher the quality of the model in the saved STL file, the less the circle looks like a polygon.
Reducing the thickness of the layers
To obtain the best quality, especially when using the layer-by-layer technology, it is necessary to reduce the thickness of the layers. This really increases the printing time, but the end result is worth it! nine0005
Optimizing the filling with honeycomb structures
Objects do not have to be solid in terms of strength. Similar to a honeycomb, printers can create a honeycomb filling that allows you to achieve a balance between strength characteristics and savings on expensive polymer material. However, if the printed part serves as a prototype for strength testing, and the serial product will be manufactured by traditional methods, as well as in the case of exposing the part to certain types of mechanical stresses and pressures, a solid design will be preferable. nine0005
Selecting the material
Printing success depends largely on the correct choice of material. Materials have different properties. For example, the melting point of thermoplastic polyurethane (TPU) and polylactic acid (PLA) is lower than that of acrylonitrile butadiene styrene (ABS). In addition, the material is taken into account when choosing the type of support structures. For an object made of polylactic acid, supporting elements can be made from the same polylactic acid, since it will be quite easy to separate them from the finished part. If the part is printed from ABS plastic, then the supporting elements must be made from a different material, and in thermoplastic polyurethane parts it is better not to use such elements at all. nine0005
Cellular infill
Solid body is not always the best choice for 3D printing. Printing solid parts has its advantages, but the internal honeycomb structure saves both expensive material and time.
Creating objects with a specified degree of filling with honeycomb structures is a unique opportunity for 3D printing. Moreover, it is not required to design such a structure: this is done by the slicer program. As a rule, it is enough to set only the percentage of filling (the closer it is to 100, the more solid the object will turn out) and select the type of cells, if the printer has such an opportunity. nine0005
In addition to saving time and material, the internal honeycomb structure has many other advantages.
Cellular infill prevents warpage
Printing large objects in one piece causes warpage hazard. By reducing the infill percentage, the air during printing passes through the part, providing more uniform cooling and eliminating buckling.
Cell filling does not result in strength loss
Cell printing instead of solid material does not reduce part strength. In many cases, a honeycomb part is strong enough for the chosen application, but lighter and less material intensive. nine0005
The functionality determines the choice of cell geometry
Most slicers support a wide variety of cell geometries. The optimal option is determined by the functional purpose of the object. Standard box padding simplifies printing, while hexagonal and triangular boxes add strength. Wave fill allows an object to bend or twist.
How do I choose the right filling percentage?
In general, the strength of an object increases as the infill percentage increases. Most printers have a default infill percentage of 20, which is optimal in some cases but too high or too low in others. Consider mechanical stresses in the printed object and increase the percentage of infill in areas where greater strength is required. If high strength is not required, choose the lowest possible infill. This will save material and increase print speed. Most often, the selection of the optimal filling percentage is made by trial and error. nine0005
Methods for attaching a workpiece to a table
“Rafts”, “brims”, “skirts” - these terms sound funny, but they just refer to three main ways of attaching a 3D printed part to a printer table. Consider each of these methods and their areas of application.
Skirt
The skirt involves creating a few rings around the object at the start of printing to ensure that the plastic is extruded normally. The skirt does not touch the object at all. It surrounds the printable area and helps start the fusing process. When creating a skirt, a large volume of hot thermoplastic polymer passes through the nozzle. This prepares the printer for printing the part itself. This guarantees good adhesion to the table and obtaining smooth surfaces of the object. nine0005
Brim
Brim is a wide flat area connected to the main object as a support base (think of a hat brim). It is very similar to a skirt, but connected to the model. In addition to all the advantages of a skirt, the brim keeps the edges of the object being made on the table.
When printing, the outside of an object often cools faster than the middle, causing the edges to curl. Brim prevents this phenomenon by holding the edges.
Raft
The raft is a detachable base made as a thin mesh platform that is located under the entire object (which lies on the raft). To create a raft, the printer first prints a flat plate in two or three layers, and then begins to produce an object. nine0005
The rafts provide excellent adhesion to the table surface and also provide a strong print base. This is especially useful when making small and unusually shaped parts that do not fit well on the table, as well as thin-walled objects.
After printing is completed, in most cases the raft will separate easily from the part.
If the printer does not have a heated desktop
Rafts are used if the printer does not have a heated desktop. In this case, excessive adhesion becomes a problem. nine0005
An alternative method is to apply adhesive paper tape to the printer bed, wrapping the edges down if possible (this also protects the bed). You can also use packing tape, but it is usually more expensive.
If buckling does occur or the object separates from the table, apply a dissolvable glue stick to the adhesive tape. This will enhance adhesion.
Learn about the features of a specific 3D printer and take them into account when preparing your model
3D printing is not only a science, but also an art. Effective design for subsequent 3D printing requires an understanding of the technological process, taking into account its features and the purpose of the future object. This will greatly improve print performance. nine0005
Using Solid Edge in 3D printing
Not all computer-aided design systems are suitable for 3D printing
The capabilities of the system used should not limit designers. Our Solid Edge system is designed with the latest 3D printing technologies in mind. Various 3D printers and 3D printing services are supported.
Take it to the next level with specific design techniques for 3D printed parts
Generative modeling in Solid Edge opens up new possibilities: the designer selects a specific material, sets the design space, allowable loads, restrictions and target mass of the part, and the system automatically calculates the desired geometry. As a result, 3D printing methods can produce the most complex shapes.
In addition, when building models, the use of the results of three-dimensional scanning is provided. Solid Edge successfully combines the traditional boundary representation of solid models (B-Rep) and the triangle mesh representation of surfaces to avoid time-consuming and error-prone transformations. nine0005
If you've already downloaded an STL file for printing, our unique synchronous technology makes it quick and easy to edit imported models in Solid Edge to prepare them for the process.
Printing on your own printer or submitting an order to a 3D printing service provider
Printing in Solid Edge on a local 3D printer is performed by the command 3D print . Models can be saved in STL and 3MF formats, or sent directly to Microsoft 3D Builder. If you don't have your own 3D printer or want to try out different materials and surface finishes, Solid Edge allows you to directly submit models to cloud-based 3D printing services (such as 3YOURMIND).