Laser lithography 3d printer
High resolution 3d printer | 3D microstereolithography
Home » Products
3D tabletop micro stereolithography system
High resolution 3D lithographic laser system, the Dilase 3D offers the possibility to work in 3 dimensions with a resolution of 5µm standard (until 2µm optional). It allows to write on all type of substrate (semi-conductor, glass, polymer, cristal, thin film…) on a surface expendable up to 100 x 100mm, and a depth of 50mm.
-
A novel technology
-
High resolution 3D printer
-
Great depth of focus
-
Specific softwares for 3D printing
- Performance and features
Request a quote
A novel technology
High resolution objects with a great volume
Kloe has developped a new approach in 3D printing through its knowledge in laser photolithography. Kloe offers a high resolution 3D printing tool (<5µm) currently unique on the market. Dilase 3D enables to conceive high resolution objects with a great volume (100 x 100 x 50mm³).
Partnership LAAS-CNRS / Kloé
This new equipment has been developped in partnership with LAAS-CNRS Renatech lab. LAAS-CNRS particulary developped the process to realise hight quality 3D microfluidics and biotech devices.
High resolution 3D printer
Great depth of focus
The large depth of focus resulting from the specific optical processing developed by Kloe, allows to write as easily in thick layers as thinner layers with the same verticality of edges and minimal roughness.
Therefore, one can save a lot of time in the work process of large object without a quality loss.
Related applications
Microfluidics
3D biotechnology
Surface functionalization
Specific softwares for 3D printing
The software suite Dilasesoft and 3DSlicer equips in standard all 3D equipment.
Perfectly adapted, this software suite brings you concrete answers to current demand in microfabrication, from the prototype phase to the full production.
3DSlicer to visualize and convert your 3D design files to be compatible with our equipment
It enables not only the importation of STL files which is the standard format in 3D industry, but also to recreate a 3D design with the assistance of monochrome images.
DilaseSoft to manage the high resolution 3D printer Dilase 3D
Developed to pilot the lithographic equipment of Dilase range, DilaseSoft is a piloting software that ensures the production of all type of design written by direct laser.
Performances:
- Linear writing speed: up to 100mm/s
- Address grid: 100nm
- Repeatability: 100nm
- Sample holder: 25 x 25mm², 50 x 50mm², 100 x 100mm²
- Planar substrates: up to 100 x 100mm
- Laser beam width combination available: 2µm with 10µm, 5µm with 20µm, 10µm with 60µm
Specifications:
- Dimensions: 544 x 703 x 865mm
- Available laser sources: 375nm or 405nm
- Accepted files format: STL
- Motorized focal length
- Integrated design software: 3D Slicer and Dilasesoft
- Two writing modes: vectorial and scanning
See also:
- Use case of our Dilase 3D by MINT Laboratory - Angers University
- Direct Laser Writers from Dilase range
- Masker and mask aligners from UV-KUB range
Request a quote
Stereolithography (SLA) 3D Printing Guide
Stereolithography (SLA) 3D printing is the most common resin 3D printing process that has become vastly popular for its ability to produce high-accuracy, isotropic, and watertight prototypes and end-use parts in a range of advanced materials with fine features and smooth surface finish.
In this comprehensive guide, learn how SLA 3D printers work, why thousands of professionals use this process today, and how SLA printers can benefit your work.
White Paper
Looking for a 3D printer to realize your 3D models in high resolution? Download our white paper to learn how SLA printing works and why it's the most popular 3D printing process for creating models with incredible details.
Download the White Paper
Stereolithography belongs to a family of additive manufacturing technologies known as vat photopolymerization, commonly known as resin 3D printing. These machines are all built around the same principle, using a light source—a laser or projector—to cure liquid resin into hardened plastic. The main physical differentiation lies in the arrangement of the core components, such as the light source, the build platform, and the resin tank.
Watch how stereolithography (SLA) 3D printing works.
SLA 3D printers use light-reactive thermoset materials called “resin.” When SLA resins are exposed to certain wavelengths of light, short molecular chains join together, polymerizing monomers and oligomers into solidified rigid or flexible geometries.
A graphic representation of the basic mechanics of stereolithography (SLA) 3D printing.
SLA parts have the highest resolution and accuracy, the sharpest details, and the smoothest surface finishes of all 3D printing technologies, but the main benefit of the stereolithography lies in its versatility.
Material manufacturers have created innovative SLA resin formulations with a wide range of optical, mechanical, and thermal properties to match those of standard, engineering, and industrial thermoplastics.
Advancements in 3D printing continue to change the way businesses approach prototyping and production. As the technology becomes more accessible and affordable and hardware and materials advance to match market opportunities and demands, designers, engineers, and beyond are integrating 3D printing into workflows across development cycles. Across industries, 3D printing is helping professionals cut outsourcing costs, iterate faster, optimize production processes, and even unlock entirely new business models.
Stereolithography 3D printing in particular has undergone significant changes. Traditionally, SLA 3D printers have been monolithic and cost-prohibitive, requiring skilled technicians and costly service contracts. Today, small format desktop printers produce industrial-quality output, at substantially more affordable price points and with unmatched versatility.
Compare stereolithography 3D printing to two other common technologies for producing plastic parts: fused deposition modeling (FDM) and selective laser sintering (SLS).
Sample part
See and feel Formlabs quality firsthand. We’ll ship a free sample part to your office.
Request a Free Sample Part
See how to go from design to 3D print with the Form 3+ SLA 3D printer. This 5-minute video covers the basics of how to use the Form 3, from the software and materials to printing and post-processing.
Use any CAD software or 3D scan data to design your model, and export it in a 3D printable file format (STL or OBJ). Each SLA printer includes software to specify printing settings and slice the digital model into layers for printing. Once setup is complete, the print preparation software sends the instructions to the printer via a wireless or cable connection.
More advanced users may consider specifically designing for SLA, or taking steps like hollowing parts to conserve material.
After a quick confirmation of the correct setup, the printing process begins and the machine can run unattended until the print is complete. In printers with a cartridge system, the material is automatically refilled by the machine.
An online Dashboard from Formlabs allows you to remotely manage printers, materials, and teams.
Once the printing is completed, parts require rinsing in isopropyl alcohol (IPA) to remove any uncured resin from their surface. After rinsed parts dry, some materials require post-curing, a process which helps parts to reach their highest possible strength and stability. Finally, remove supports from the parts and sand the remaining support marks for a clean finish. SLA parts can be easily machined, primed, painted, and assembled for specific applications or finishes.
Post-curing is particularly important for functional resins for engineering, and mandatory for some dentistry and jewelry materials and applications.
Webinar
In this webinar, Matt Lewis and Ricky Hopper walk you through an overview of the improved SLA line, and give a hands on demo of the new products.
Watch the Webinar Now
Engineers, designers, manufacturers, and more choose SLA 3D printing for its fine features, smooth surface finish, ultimate part precision and accuracy, and mechanical attributes like isotropy, watertightness, and material versatility.
Because 3D printing creates parts one layer at a time, completed prints may have variations in strength based on orientation of the part relative to the printing process, with different properties in X, Y, and Z axes.
Extrusion-based 3D printing processes like fused deposition modeling (FDM) are known for being anisotropic due to layer-to-layer differences created by the print process. This anisotropy limits the usefulness of FDM for certain applications, or requires more adjustments on the part geometry side to compensate for it.
Read our in-depth guide about FDM vs. SLA 3D printers to learn how they compare in terms of print quality, materials, applications, workflow, speed, costs, and more.
In contrast, SLA resin 3D printers create highly isotropic parts. Achieving part isotropy is based on a number of factors that can be tightly controlled by integrating material chemistry with the print process. During printing, resin components form covalent bonds, but layer to layer, the part remains in a semi-reacted “green state. ”
While in the green state, the resin retains polymerizable groups that can form bonds across layers, imparting isotropy and watertightness to the part upon final cure. On the molecular level, there is no difference between X, Y, or Z planes. This results in parts with predictable mechanical performance critical for applications like jigs and fixtures, end-use parts, and functional prototyping.
SLA printed parts are highly isotropic compared to those produced with fused deposition modeling (FDM).
Because they are isotropic, SLA printed parts like this jig from Pankl Racing Systems can withstand the variety of directional forces they undergo during high stress manufacturing operations.
SLA printed objects are continuous, whether producing geometries with solid features or internal channels. This watertightness is important for engineering and manufacturing applications where air or fluid flow must be controlled and predictable. Engineers and designers use the watertightness of SLA printers to solve air and fluid flow challenges for automotive uses, biomedical research, and to validate part designs for consumer products like kitchen appliances.
OXO relies on the watertightness of SLA printing to create robust functional prototypes for products with air or fluid flow, like this coffee maker.
Industries from dental to manufacturing depend on SLA 3D printing to repeatedly create accurate, precise components. For a print process to produce accurate and precise parts, multiple factors must be tightly controlled.
Compared to machined accuracy, SLA 3D printing is somewhere between standard machining and fine machining. SLA has the highest tolerance of commercially available 3D printing technologies. Learn more about understanding tolerance, accuracy, and precision in 3D printing.
The combination of the heated resin tank and the closed build environment provides almost identical conditions for each print. Better accuracy is also a function of lower printing temperature compared to thermoplastic-based technologies that melt the raw material. Because stereolithography uses light instead of heat, the printing process takes place at close to room temperature, and printed parts don't suffer from thermal expansion and contraction artifacts.
An example from the dental industry comparing a scanned component with the original CAD geometry, demonstrating the ability to maintain tight tolerances across an SLA printed part.
Low Force Stereolithography (LFS) 3D printing houses the optics inside a Light Processing Unit (LPU) that moves in the X direction. One galvanometer positions the laser beam in the Y direction, then directs it along across a fold mirror and parabolic mirror to deliver a beam that is always perpendicular to the build plane, so it is always moving in a straight line to provide even greater precision and accuracy, and allows for uniformity as hardware scales up to larger sizes, like Formlabs larger format SLA printer Form 3L. The LPU also uses a spatial filter to create a crisp, clean laser spot for greater precision.
The characteristics of individual materials are also important for ensuring a reliable, repeatable print process.
Formlabs Rigid Resin has a high green modulus, or modulus before post-curing, which means it’s possible to print very thin parts with precision and a lower chance of failure.
SLA printers are considered the gold standard for smooth surface finish, with appearances comparable to traditional manufacturing methods like machining, injection molding, and extrusion.
This surface quality is ideal for applications that require a flawless finish and also helps reduce post-processing time, since parts can easily be sanded, polished, and painted. For example, leading companies like Gillette use SLA 3D printing to create end-use consumer products, like 3D printed razor handles in their Razor Maker platform.
Leading companies like Gillette use SLA 3D printing to create end-use consumer products, like the 3D printed razor handles in their Razor Maker platform.
Z-axis layer height is commonly used to define the resolution of a 3D printer. This can be adjusted in between 25 and 300 microns on Formlabs SLA 3D printers, with a trade-off between speed and quality.
In comparison, FDM and SLS printers typically print Z-axis layers at 100 to 300 microns. However, a part printed at 100 microns on an FDM or SLS printer looks different from a part printed at 100 microns on an SLA printer. SLA prints have a smoother surface finish right out of the printer, because the outermost perimeter walls are straight, and the newly printed layer interacts with the previous layer, smoothing out the staircase effect. FDM prints tend to have clearly visible layers, whereas SLS has a grainy surface from the sintered powder.
The smallest possible detail is also much finer on SLA, given 85 micron laser spot size on the Form 3+, in comparison with 350 microns on industrial SLS printers, and 250–800 micron nozzles on FDM machines.
While FDM 3D printed parts tend to have visible layer lines and might show inaccuracies around complex features, parts printed on SLA machines have sharp edges, a smooth surface finish, and minimal visible layer lines.
SLA resins have the benefit of a wide range of formulation configurations: materials can be soft or hard, heavily filled with secondary materials like glass and ceramic, or imbued with mechanical properties like high heat deflection temperature or impact resistance. Material range from industry-specific, like dentures, to those that closely match final materials for prototyping, formulated to withstand extensive testing and perform under stress.
Rigid 10K Resin is a highly glass-filled material for industrial parts that need to withstand significant load without bending, including applications like injection molding.
In some cases, its this combination of versatility and functionality that leads to companies to initially bring resin 3D printing in-house. After finding one application solved by a specific functional material, it’s usually not long before more possibilities are uncovered, and the printer becomes a tool for leveraging the diverse capabilities of various materials.
For example, hundreds of engineers in the Design and Prototyping Group at the University of Sheffield Advanced Manufacturing Research Centre (AMRC) rely on open access to a fleet of 12 SLA 3D printers and a variety of engineering materials to support highly diverse research projects with industrial partners like Boeing, Rolls-Royce, BAE Systems, and Airbus. The team used High Temp Resin to 3D print washers, brackets, and a sensor mounting system that needed to withstand the elevated, and leveraged Durable Resin to create intricate custom springy components for a pick and place robot that automates composites manufacturing.
Engineers at the AMRC use a fleet of 12 SLA 3D printers and a variety of engineering materials to print custom parts for diverse research projects, like brackets for a pick and place robot (top), and mounts for sensors in a high-temperature environment (bottom).
Interactive
Need some help figuring out which 3D printing material you should choose? Our new interactive material wizard helps you make the right material decisions based on your application and the properties you care the most about from our growing library of resins.
Recommend Me a Material
SLA 3D printing accelerates innovation and supports businesses across a wide range of industries, including engineering, manufacturing, dentistry, healthcare, education, entertainment, jewelry, audiology, and more.
Rapid prototyping with 3D printing empowers engineers and product designers to turn ideas into realistic proofs of concept, advance these concepts to high-fidelity prototypes that look and work like final products, and guide products through a series of validation stages toward mass production.
Learn More
Manufacturers automate production processes and streamline workflows by prototyping tooling and directly 3D printing custom tools, molds, and manufacturing aids at far lower costs and lead times than with traditional manufacturing. This reduces manufacturing costs and defects, increases quality, speeds up assembly, and maximizes labor effectiveness.
Learn More
Digital dentistry reduces the risks and uncertainties introduced by human factors, providing higher consistency, accuracy, and precision at every stage of the workflow to improve patient care. 3D printers can produce a range of high-quality custom products and appliances at low unit costs with superior fit and repeatable results.
Learn More
Affordable, professional-grade desktop 3D printing helps doctors deliver treatments and devices customized to better serve each unique individual, opening the door to high-impact medical applications while saving organizations significant time and costs from the lab to the operating room.
Learn More
3D printers are multifunctional tools for immersive learning and advanced research. They can encourage creativity and expose students to professional-level technology while supporting STEAM curricula across science, engineering, art, and design.
Learn More
High definition physical models are widely used in sculpting, character modeling, and prop making. 3D printed parts have starred in stop-motion films, video games, bespoke costumes, and even special effects for blockbuster movies.
Learn More
Jewelry professionals use CAD and 3D printing to rapidly prototype designs, fit clients, and produce large batches of ready-to-cast pieces. Digital tools allow for the creation of consistent, sharply detailed pieces without the tediousness and variability of wax carving.
Learn More
Hearing specialists and ear mold labs use digital workflows and 3D printing to manufacture higher quality custom ear products more consistently, and at higher volumes for applications like behind-the-ear hearing aids, hearing protection, and custom earplugs and earbuds.
Learn More
Many companies start using 3D printing via outsourcing to service bureaus or labs. Outsourcing production can be a great solution when teams require 3D printing only occasionally, or for one-offs that require unique material properties or applications. Service bureaus can also provide advice on various materials and offer value-added services such as design or advanced finishing.
The main downsides of outsourcing are cost and lead time. Often, outsourcing is a gateway to bringing production in-house as needs ramp up. One of the greatest benefits of 3D printing is its speed compared to traditional manufacturing methods, which quickly diminishes when an outsourced part takes multiple days or even weeks to arrive. With growing demand and production, outsourcing also rapidly becomes expensive.
Because of the rise of affordable industrial-quality 3D printing, today, more and more companies choose to bring 3D printing in-house right away, vertically integrating into existing shops or labs, or in the workspaces of engineers, designers, and others who could benefit from translating digital designs into physical parts or who are involved in small batch production.
Small format, desktop SLA 3D printers are great when you need parts quickly. Depending on the number of parts and printing volume, investment into a small format 3D printer can break even within months. Plus, with small format machines, it’s possible to pay for just as much capacity as a business needs and scale production by adding extra units as demand grows. Using multiple 3D printers also creates the flexibility to print parts in different materials simultaneously. Service bureaus can still supplement this flexible workflow for larger parts or unconventional materials.
Interactive
Try our interactive ROI tool to see how much time and cost you can save when 3D printing on Formlabs 3D printers.
Calculate Your Savings
Fast turnaround time is a huge advantage to owning a desktop 3D printer. When working with a printing bureau, lead times, communication, and shipping all create delays. With a desktop 3D printer like the Form 3+, parts are in-hand within hours, allowing designers and engineers to print multiple parts in one day, helping to iterate faster and drastically reduce product development time and quickly test mechanisms and assemblies avoid costly tool changes.
Owning a desktop 3D printer results in significant savings over 3D printing service bureaus and traditional machining, as these alternatives rapidly becomes expensive with growing demand and production.
For example, to fulfill tight production deadlines, a process engineer and team at Pankl Racing Systems introduced SLA 3D printing to produce custom jigs and other low-volume parts directly for their manufacturing line. While in-house SLA was initially met with skepticism, it turned out to be an ideal substitute to machining a variety of tools. In one case, it reduced lead time for jigs by 90 percent—from two to three weeks to less than a day—and decreased costs by 80-90 percent.
Cost | Lead Time | |
---|---|---|
In-House SLA 3D Printing | $9–$28 | 5–9 hours |
CNC Machining | $45–$340 | 2–3 weeks |
Outsourced 3D Printing | $51–$137 | 1–3 weeks |
Pankl Racing Systems significantly reduced lead times and costs by 3D printing custom jigs in-house.
With small format machines, it’s possible to pay for just as much capacity as a business needs and scale production by adding extra units as demand grows. Using multiple 3D printers also creates the flexibility to print parts in different materials simultaneously.
The Design and Prototyping Group at the University of Sheffield Advanced Manufacturing Research Centre (AMRC) runs an open-access additive manufacturing station with a fleet of 12 Form 2 stereolithography (SLA) 3D printers for hundreds of engineers working on diverse projects across the site.
Formlabs offers two high precision SLA 3D printing systems, a growing library of specialized materials, intuitive print preparation and management software, and professional services—all in one package.
To continue exploring SLA 3D printing, start with feeling the quality of SLA for yourself: Request a free sample 3D printed part in your choice of material to be mailed straight to your door.
Request a Free Sample Part
LLNL experimental 3D printer prints products in seconds
News
Researchers at the Lawrence Livermore National Laboratory (LLNL) are experimenting with holographic photopolymer 3D printing.
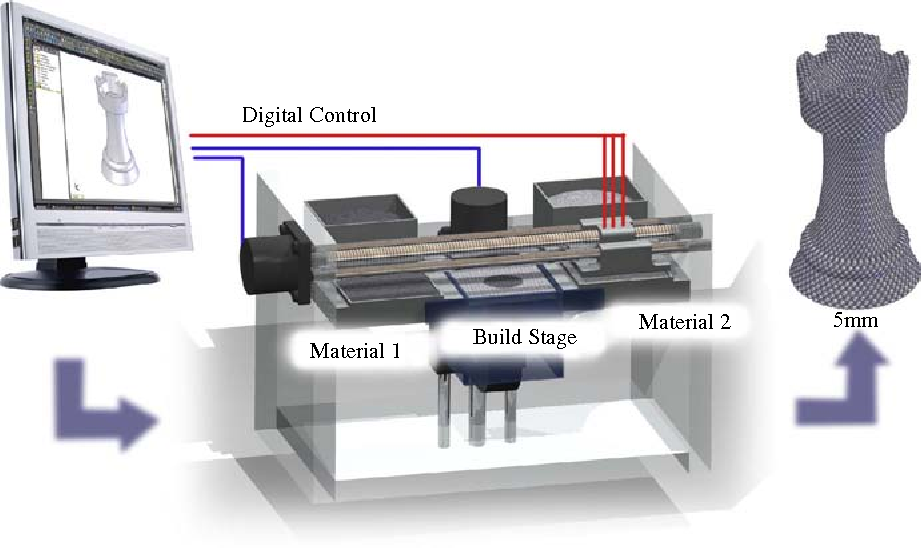
In addition to the engineers at the UC Berkeley laboratory, researchers from the University of Rochester and the Massachusetts Institute of Technology (MIT) are participating in the project. The idea as a whole is based on laser stereolithography (SLA) and two-photon polymerization (aka “two-photon laser lithography”, aka “direct laser writing”), that is, curing photopolymer resins using laser radiation. One of the main problems with SLA printing is the slow speed required by spotlighting each layer. Performance directly depends on the scanning speed and emitter power, but even in the best cases it remains low.
“The ability to create entire 3D objects in one step solves an important problem in additive manufacturing. We are trying to print 3D shapes as a whole. The real question of our research can be formulated as follows: is it possible to print whole three-dimensional objects of a productive form instead of producing them layer by layer? It turns out that this is quite real,” explains Maxim Shusteff, lead author of the report.
The experimental 3D printer developed by LLNL uses the principle of volumetric laser holography: images of models are projected in three planes. Of course, during the passage of lasers through a photopolymer medium, parasitic illumination occurs, but the brightness of the light reaches a maximum at the points of intersection of the laser beams. This is where the most intense curing of the photopolymer takes place. Curing times for small models may well be seconds instead of minutes or even hours ( compared to the most common technologies in the chart below ).
The higher the laser power, the faster the process, however, the speed and size of the products must be balanced against two main factors, namely the same stray light and heat, because photopolymerization is an exothermic process. In addition, the complexity and resolution of the models are still limited by the hardware component: the beams are immobile and intersect at right angles, and therefore, to build more complex structures, it will be necessary to generate more beams, or proceed to plotting, and this will already be a step back to conventional laser stereolithography. However, the benefits are obvious. In addition to increased productivity, you can print objects in a suspended state, because the technique does not require the use of a moving platform. Accordingly, it is possible to print with very vulnerable materials such as soft hydrogels. Finished products are isotropic, that is, homogeneous in all directions, with no distinguishable layers. The research team's report can be downloaded from this link. Recall that similar experiments are being carried out by the Californian company Daqri. How it works, see the video:
Do you have interesting news? Share your developments with us, and we will tell the whole world about them! We are waiting for your ideas at news@3Dtoday. ru.
Follow the author
Follow
Don't want
17
More interesting articles
9
Subscribe to the author
Subscribe
Don't want
The project is experiential and symbolic: the structure was erected by 3D4Art to celebrate...
Read more
7
Subscribe to the author
Subscribe
Don't want
Even the simplest FDM 3D printer can print color products with a smooth gradation of tones...
Read more
82
Subscribe to the author
Subscribe
Don't want
Collaboration 3D
We are pleased to present you our joint development with Speci. ..
Read more
90,000 Axial lithography-the new 3D printing processComputer axial lithography-the new 3D printing process
Researchers from the California University in Berkeley developed a new 3D printer , which used a special photosensitive resin that hardens within minutes. The researchers named their machine "Replicator" after the Star Trek device that materializes any object on demand.
This new 3D printing process creates solid structures by projecting light into a resin that hardens almost instantly. On the other hand, the conventional 3D printing method creates fragments by applying different kinds of material layer by layer.
New production possibilities
This new process provides various production possibilities, such as adding a handle to the metal shaft of a screwdriver by dipping the screwdriver into resin. For example, another traditional The 3D printer will fight for it. In addition, it can also create objects that are sleeker, more flexible, and more complex. The researchers believe this technology could have great potential in medical fields, especially where transparent details are needed.
“I think this is the way to make things even more customizable, whether they're prosthetics or running shoes,” said Hayden Taylor, assistant professor of mechanical engineering at the University of California at Berkeley. He adds, "The fact that you could take a metal component or something from another manufacturing process and add custom geometry, I think that could change the way products are designed."
How does the technology work?
Even other 3D printers using light technology create layer after layer. However, we covered news about a new technique coming from the University of Michigan that promised very fast small-scale production. In fact, they evaluated their technique 100 times faster than other methods. Their method was slightly different from the one that comes from UC Berkeley. He cured liquid resin using two light sources to control where the resin solidified and where it remained liquid.
At the University of California, Berkeley, researchers used a rotating cylinder filled with a photosensitive resin that hardens when exposed to a certain threshold of light. They then projected patterns of light through a projector, which essentially projected the shape of the object they wanted to 3D print.
"Basically you have a ready made video projector that I literally brought from home and then you plug it into a laptop and use it to project a series of computed images while the engine spins a cylinder that has resin for 3D print ,” said Hayden Taylor. "Obviously, there are a lot of subtleties to this - how do you formulate the resin, and most of all, how do you calculate the images that will be projected, but the barrier to making a very simple version of this tool is not that high.