Investment casting 3d printer
Investment Casting with 3D Printing Technology
3D printing technologies and materials produce innovative casting patterns that provide consistency and quality in cast components – both in terms of prototyping and low volume production.
Application OverviewInvestment casting is a manufacturing process (also known as lost wax casting) where a master pattern (traditionally made of wax) is covered with a ceramic slurry. Preheated wax is then melted out of its ceramic shell before molten metal is poured into it. The process generally provides higher accuracy and surface finish compared to other casting processes and is often used in applications that carry low volume production and changing product designs. 3D printed molds offer greater complexity, substantial time and cost savings when creating wax patterns for prototyping and short production runs.
Benefits of Using 3D Printing Technology
for Investment Casting
Freedom of Design
3D printing allows you to create more complex designs than a traditional investment casting process
Cost-Effective
3D printing can be a more cost-effective option than traditional tooling
Time
With 3D printing, you can reduce your time to part versus waiting for tooling to be made
Application
Wax patterns used in traditional investment casting methods are produced using an injection molding process, with costs ranging from $5,000 – $25,000 and lead times estimating at around two months. A major hindrance for companies is that investment casting foundries are unable to produce prototype castings until the injection mold is completed. 3D printing with FDM technology provides an alternate method for producing investment casting patterns that are a lot more efficient and cost-effective.
3D printing with FDM technology provides an alternate method for producing investment casting patterns that are a lot more efficient and cost-effective. A foundry can produce a pattern that also services as a prototype for form and fit evaluation in a single day, providing a perfect match to the casting that would be produced if that exact pattern were to be used. An FDM part’s durability allows it to be put into an assembly for testing while preventing damage that often occurs in transportation and handling. Due to FDM being an additive process, patterns can be as complex or as simple as needed, without any impact on cost.
Process
The wax patterns used in Investment Casting are produced with an injection molding process. FDM patterns are direct replacements for traditional parts that are injection molded but does not melt like wax. It burns, leaving a small amount of ash in the shell cavity which is then later removed in a shell washing operation. To speed the burnout of the FDM pattern, venting is added to ceramic shells. To prevent defects, patterns need to be produced to close tolerances and with excellent surface finish. Using our expert finishing services, hand finishing is not required on FDM parts, making this method a reliable and strong route in the Investment Casting market.
Looking to use 3D printing for Investment Casting?
Speak with one of our advanced manufacturing experts on how you can implement 3D printing technology for your investment casting application.
ASK AN EXPERT
Related Resources
Recommended Products for Investment Casting with 3D Printing
3D Printing & Foundries | Investment Casting Patterns | Stratasys Direct
- March 13, 2018
Industry Highlight: 3D Printing and Foundries
Metal casting at foundries is one of many tried and true manufacturing processes that have been impacted by 3D printing.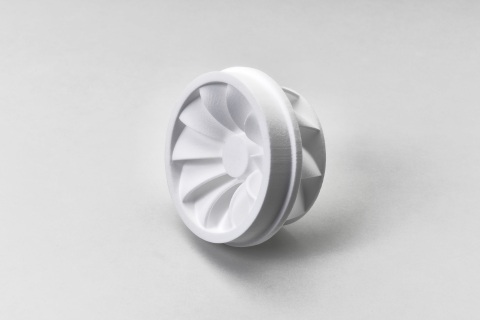
3D Printing Investment Casting Patterns
3D printing offers an effective tool-less solution for investment casting patterns with Stereolithography (SL). As an alternative to wax and wood, SL builds patterns with a UV laser that cures and solidifies thin layers of resin. Stratasys Direct builds SL investment casting patterns in a nearly hollow structure with a sparse internal lattice structure and thin walls. This proprietary build style translates to proportionately less ash and minimized thermal expansion forces during flash firing.
Stratasys Direct utilizes two Stereolithography materials for investment casting patterns. SC 1000P is a custom photopolymer formulation developed for low cost investment casting patterns. SC 1000P has low water absorption, and patterns built with this material are less prone to dimensional distortion. SOMOS® Element is a newer antimony-free formulation for investment casting patterns. This material is specifically used when a project calls for casting with reactive metal alloys where antimony may contaminate the cast metallurgical properties.
Stereolithography offers a new design freedom, unbound to tooling. Designs can be easily altered and gating systems can be proven out prior to tooling. SL delivers excellent pattern accuracy and repeatability, at less expense than conventional methods. These benefits translate to higher yields in the casting process and makes the piece easier to ship and more durable in-transit than a wax pattern.
Expertise in Action
Each foundry is unique, which is why we tailor the process and product for each customer’s distinctive operations. We work to fit into each customer’s unique operations by utilizing a successful process. We start by associating each project with lot sizes, materials, as-cast shrink compensation, surface roughness and dimensional requirements to ensure on-time delivery of quality patterns.
Then, printing parameters are customized to each pattern’s geometry and cast metal alloy. The patterns are optimized with low CTE, print time and material usage. Stratasys Direct has significant experience seamlessly bonding and assembling large SL patterns. Projects more than seven feet in diameter have been assembled with custom assembly fixtures and expertly delivered in large part packaging. We apply specific surface finishes to parts in order to work with foundry-specific face coats. Our sophisticated leak testing device checks each pattern for a perfect seal, and we offer vacuum ports and testing equipment for quality control at the foundry.
Custom Tools for Foundry Functions
Stratasys Direct offers a host of advanced manufacturing solutions for developing manufacturing tools and aids for foundry customers including hybrid wax setters, wax pattern assembly jigs, straightening fixtures, pattern and core inspection gauges, sand casting patterns, match-plates and core-boxes.
Our engineers are experts in examining a customer’s unique operations and identifying areas that custom jigs, fixtures and other manufacturing aids could transform your production floor.
Even with a centuries old manufacturing process, 3D printing can widen foundries customer base by offering a compatible processes and custom tools.
Casting on models printed on a 3D printer / Sudo Null IT News
Jeshua Lacock writes:
This page describes my first and successful attempt to cast aluminum parts directly from 3D printed PLA models. The process is almost identical to wax casting, but instead of burning the wax, I burned the PLA plastic (bio-plastic)
I needed aluminum parts to mount the focus lens for my 150W CO2 cutting laser. These parts had to be adjustable and had to be mounted on a frame assembled from scrap aluminum found.
I get excited when I think about being able to do it all in one day: concept -> design -> 3D printing -> finished metal casting
Step one - detail design.
I used the amazingly powerful OpenSCAD to quickly design the parts I needed. OpenSCAD reads the script in its own language to draw the 3D model. In my case, I just drew a shape in Adobe Illustrator and converted it to OpenSCAD format using the Inkscape plugin.
Here is the design of the second piece. I drew two shapes in Illustrator and gave them depth in OpenSCAD. Very fast and easy. Now I have 3D models, it's time to print them!
The process of printing the first part on my Ultimaker (fast shot).
The resulting part is in hand.
Printing the second part.
Second printed part in hand.
Checking how both parts fit together.
Sprues and air ducts are attached, everything is ready for pouring the molding mass.
Molding mass - 50% fine sand and 50% gypsum.
After adding water and mixing thoroughly, I used a home vacuum food sealer to get rid of air bubbles in the sand.
The second piece is ready to be molded!
The first detail is poured!
The part is completely immersed in the mixture - I hope everything works out.
Both molds are set to dry.
After a couple of hours, I placed the molds in the oven on medium heat.
My new little oven. Heats up quickly for 10 pounds (~4.5kg) or less of molten aluminium. 2 times more when it flares up.
Forms are good and well done. Once heated to about 1200F (650C), the plastic doesn't stand a chance. After removing, I blew out the molds with compressed air to blow out any remaining ash.
The still hot molds are placed in dry sand. It serves several purposes:
- additional support since the molds are quite fragile
- insulates molds and retains heat when cured
- will allow me to install sprue extensions (see below). The expander gives extra pressure to the casting and also acts as a riser that stays molten and provides extra metal while the casting solidifies and contracts
My sprues are just cut aluminum cans. Works great!
After melting aluminum with a small addition of copper in the crucible, removing the slag - it's time to pour!
So cool! It looks like the forms filled out perfectly. Now the hard part is to wait long enough for the metal to cool for me to know if the parts are good or not.
Excellent! The details are straight from the sand, only the sprues and air ducts are cut off.
I cut the center hole with a small 14mm tap. Everything seems to fit together nicely.
I like the details on the casting - you can see all the lines from the 3D printing, their width is only 0.2mm.
The moment of truth - do they fit the frame? YES! I made a plastic part to fit the frame perfectly, then printed it again at 102% size increase. When aluminum cools, it shrinks by exactly 2%.
The center of the black nipple is where the focused CO2 laser beam will come out. Tube - for compressed air to blow off smoke in the path of the laser (the so-called air-assist).
Looks like I can put this to good use!
The black hole in the center is a focusing lens.
I'm so happy that the parts fit the frame perfectly without any additional processing and even without a file!
This is the first test of my laser. Approximately 60% power. Burns wood instantly.
Translator:
Jeshua Lacock has made a wonderful, actually step-by-step guide on how to cast aluminum from 3D printed plastic models. For those interested in the practical aspect, there are many recipes on the site instructables.com on how to make an aluminum casting furnace. Even from a coffee can!
Casting on burnt master models on the example of SLA 3D printers from Kings 3D
News
varieties of precision metal casting, where photopolymer resins or filaments are used as a material for 3D printing. In this article, we will briefly review the technology using examples of products obtained using Kings 3D laser stereolithographic 3D printers.
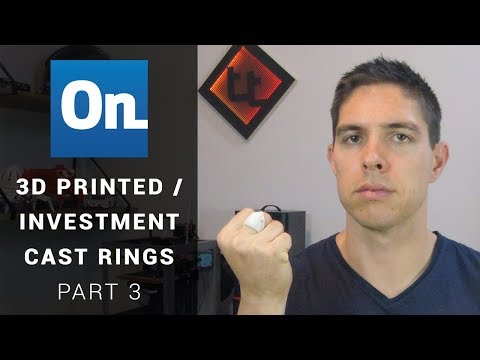
Casting from 3D printed die-cut masters produces castings without cores, tapers, bays and seams, with tighter dimensional tolerances and reduced machining allowances compared to casting from foam and wax blanks.
This technology is already used in some Russian enterprises in the aerospace, automotive, jewelry and other industries, although its implementation in Russia for a number of reasons is much slower than its counterparts in the US, EU, China and other industrialized countries.
In the Chinese city of Xi'an, one of Kings 3D's clients has several dozen SLA 3D printers, including three Kings 600Pro with a working volume of 600x600x400 mm, which print master models around the clock with burn-out photopolymer resin.
The use of burn-out 3D-printed photopolymer master models at foundries allows to optimize production processes and reduce costs, including by reducing the time to receive castings and produce finished products. The advantages of laser stereolithography include the ability to produce complex geometries with very high precision and the increased strength of master models compared to similar parts made from wax and Styrofoam.
3D Lost Wax Casting is more accurate than wax and foam master casting, making it well suited for aerospace, engineering, jewelry, dentistry and other industries with high dimensional accuracy requirements.
When preparing digital models for 3D printing, a cellular internal structure is set using software, which allows:
The main advantages of casting on 3D-printed burnt-out master models:
- no deformation during heat treatment, obtaining a mold;
- high casting accuracy with a significant reduction in post-processing costs;
- possibility of single and small-scale production.
The main stages of the technological process of casting on 3D-burned models:
- 3D printed master model.
- Sprue holder.
- Forming the flask.
- Burn-in of photopolymer.
- Pouring metal into a finished mold.
- Product finishing.
Manufacture of Sanctioned Parts by Reverse Engineering and Casting from 3D Printed Master Models
Today, due to sanctions, there are certain difficulties with the import of a number of spare parts for equipment from the EU countries, Japan, and the USA. However, having an original part in hand, it can be reproduced by casting using burnt master models.
First, you need to get a digital model using reverse engineering, then print a master model on a 3D printer, then make a mold and make a casting. The technology makes it possible to manufacture complex parts such as track shoes, impellers, housings, gears and much more.
Some examples of such products:
Prepared by Z-Axis, the exclusive distributor of additive equipment from Shenzhen Kings 3D Printing Technology Co. on the territory of Russia and the countries of the customs union. Detailed information about Kings 3D 3D printers and consultations on the topic of casting on burnt master models are available through the official website.
Do you have interesting news? Share your developments with us, and we will tell the whole world about them! We are waiting for your ideas at [email protected]
More interesting articles
5
Subscribe to the author
Subscribe
Don't want
Establishment of the center will help improve the quality and reduce the cost of engineering products...
Read more
5
Subscribe to the author
Subscribe
Don't want
Anodizing is a process aimed at creating protective oxide layers on the surfaces of products.