Instant 3d printer
Metal 3D Printing Service for Custom Parts
Back
-
Materials
Materials by Service
Injection MoldingCNC Machining3D PrintingSheet Metal
Materials by Type
PlasticsMetalsElastomers
Related Links
Customer Supplied ResinsColors
Injection Molding Material Alternatives Guide
Struggling with thermoplastic material shortages? We created a detailed guide to resin substitutes for ABS, PC, PP, and other commonly molded thermoplastics.
Download
-
Resources
Design Tips Guides and Trend Reports Case Studies Design Aids Webinars and Trade Shows
Blog Videos FAQs Educators and Students Glossary
Industries Medical Aerospace Automotive Consumer Electronics Industrial Equipment
-
About Us
Who We Are Why Protolabs? Research and Development Cool Idea Award Partnerships Sustainability and Social Impact
Careers Investors Locations Press Procurement
Contact Us
Proto Labs, Inc.
5540 Pioneer Creek Dr.
Maple Plain, MN 55359
United StatesP: 877.479.3680
F: 763.479.2679
E: [email protected]Best-in-Class Online Quoting
After uploading your part design, you'll receive an online quote that includes manufacturing analysis to help improve part manufacturability. Within your quote, you can also adjust quantity and material and see price changes in real-time.
Learn More
Get a QuoteSign In
Get quality metal 3D-printed prototypes and production parts. Request an online quote today.
GET METAL PARTS
Certifications
ISO 9001:2015 | AS9100D | ITAR Registered
Jump to Section→ Capabilities
→ Available Alloys
→ Compare Material Properties
→ Surface Finishes
→ Post-Processing
→ Why Metal 3D Printing?
Direct metal laser sintering (DMLS) is an industrial metal 3D printing process that builds fully functional metal prototypes and production parts in 7 days or less. A range of metals produce final parts that can be used for end-use applications.
Metal 3D printing technology is commonly used for:
- Prototyping in production-grade materials
- Complex geometries
- Functional, end-use parts
- Reducing metal components in an assembly
We hope you find this guide helpful. If the file did not download, you can find it here.
Metal 3D Printing Guide
Jump start your metal 3D printing with this guide that covers material selection, design, post-processing, and quality inspections.
United States of AmericaAfghanistanÅland IslandsAlbaniaAlgeriaAmerican SamoaAndorraAngolaAnguillaAntarcticaAntigua and BarbudaArgentinaArmeniaArubaAustraliaAustriaAzerbaijanBahamasBahrainBangladeshBarbadosBelarusBelgiumBelizeBeninBermudaBhutanBolivia, Plurinational State ofBonaire, Sint Eustatius and SabaBosnia and HerzegovinaBotswanaBouvet IslandBrazilBritish Indian Ocean TerritoryBrunei DarussalamBulgariaBurkina FasoBurundiCambodiaCameroonCanadaCape VerdeCayman IslandsCentral African RepublicChadChileChinaChristmas IslandCocos (Keeling) IslandsColombiaComorosCongoCongo, the Democratic Republic of theCook IslandsCosta RicaCôte d'IvoireCroatiaCubaCuraçaoCyprusCzech RepublicDenmarkDjiboutiDominicaDominican RepublicEcuadorEgyptEl SalvadorEquatorial GuineaEritreaEstoniaEthiopiaFalkland Islands (Malvinas)Faroe IslandsFijiFinlandFranceFrench GuianaFrench PolynesiaFrench Southern TerritoriesGabonGambiaGeorgiaGermanyGhanaGibraltarGreeceGreenlandGrenadaGuadeloupeGuamGuatemalaGuernseyGuineaGuinea-BissauGuyanaHaitiHeard Island and McDonald IslandsHoly See (Vatican City State)HondurasHong KongHungaryIcelandIndiaIndonesiaIran, Islamic Republic ofIraqIrelandIsle of ManIsraelItalyJamaicaJapanJerseyJordanKazakhstanKenyaKiribatiKorea, Democratic People's Republic ofKorea, Republic ofKuwaitKyrgyzstanLao People's Democratic RepublicLatviaLebanonLesothoLiberiaLibyaLiechtensteinLithuaniaLuxembourgMacaoMacedonia, the Former Yugoslav Republic ofMadagascarMalawiMalaysiaMaldivesMaliMaltaMarshall IslandsMartiniqueMauritaniaMauritiusMayotteMexicoMicronesia, Federated States ofMoldova, Republic ofMonacoMongoliaMontenegroMontserratMoroccoMozambiqueMyanmarNamibiaNauruNepalNetherlandsNew CaledoniaNew ZealandNicaraguaNigerNigeriaNiueNorfolk IslandNorthern Mariana IslandsNorwayOmanPakistanPalauPalestine, State ofPanamaPapua New GuineaParaguayPeruPhilippinesPitcairnPolandPortugalPuerto RicoQatarRéunionRomaniaRussian FederationRwandaSaint BarthélemySaint Helena, Ascension and Tristan da CunhaSaint Kitts and NevisSaint LuciaSaint Martin (French part)Saint Pierre and MiquelonSaint Vincent and the GrenadinesSamoaSan MarinoSao Tome and PrincipeSaudi ArabiaSenegalSerbiaSeychellesSierra LeoneSingaporeSint Maarten (Dutch part)SlovakiaSloveniaSolomon IslandsSomaliaSouth AfricaSouth Georgia and the South Sandwich IslandsSouth SudanSpainSri LankaSudanSuriNameSvalbard and Jan MayenSwazilandSwedenSwitzerlandSyrian Arab RepublicTaiwan, Province of ChinaTajikistanTanzania, United Republic ofThailandTimor-LesteTogoTokelauTongaTrinidad and TobagoTunisiaTurkeyTurkmenistanTurks and Caicos IslandsTuvaluUgandaUkraineUnited Arab EmiratesUnited KingdomUnited States Minor Outlying IslandsUruguayUzbekistanVanuatuVenezuela, Bolivarian Republic ofViet NamVirgin Islands, BritishVirgin Islands, U. S.Wallis and FutunaWestern SaharaYemenZambiaZimbabwe
I agree to receive email messages containing service updates and Design Tips from Protolabs and its affiliates
Metal 3D Printing Capabilities
Our basic guidelines for metal 3D printing include important design considerations to help improve part manufacturability, enhance cosmetic appearance, and reduce overall production time.
Metal 3D Printing Tolerances
For well-designed parts, tolerances of +0.003 in. (0.076mm) plus 0.1% of nominal length can typically be achieved. Note that tolerances may change depending on part geometry.
Max Dimensions
Layer Thickness
Minimum Feature Size
Tolerances
*At this time, Inconel 718 and Aluminum are the only materials available on our large format, X Line machine
Metal 3D Printing Material Options
Below is our available metal alloys for 3D printing. Various heat treatments are available depending on material.
Stainless Steel (17-4 PH)
Stainless Steel 17-4 PH is a precipitation hardened stainless steel that is known for its hardness and corrosion resistance. If needing a stainless steel option, select 17-4 PH for its significantly higher tensile strength and yield strength, but recognize that it has far less elongation at break than 316L. Final parts built 17-4 PH receive vacuum solution heat treatment as well as H900 aging.
Primary Benefits
- Heat treated for full hardness and strength
- Corrosion resistance
LEARN MORE>
Stainless Steel (316L)
Stainless steel 316L is a workhorse material used for manufacturing acid and corrosion resistant parts. Select 316L when stainless steel flexibility is needed; 316L is a more malleable material compared to 17-4 PH. Final parts built in 316L receive stress relief application.
Primary Benefits
- Acid and corrosion resistance
- High ductility
LEARN MORE>
Aluminum (AlSi10Mg)
Aluminum (AlSi10Mg) is comparable to a 3000 series alloy that is used in casting and die casting processes. It has good strength -to-weight ratio, high temperature and corrosion resistance, and good fatigue, creep and rupture strength. AlSi10Mg also exhibits thermal and electrical conductivity properties. Final parts built in AlSi10Mg receive stress relief application.
Primary Benefits
- High stiffness and strength relative to weight
- Thermal and electrical conductivity
LEARN MORE>
Inconel 718
Inconel is a high strength, corrosion resistant nickel chromium superalloy ideal for parts that will experience extreme temperatures and mechanical loading. Final parts built in Inconel 718 receive stress relief application. Solution and aging per AMS 5663 is also available to increase tensile strength and hardness.
Primary Benefits
- Oxidation and corrosion resistance
- High performance tensile, fatigue, creep, and rupture strength
LEARN MORE>
Cobalt Chrome (Co28Cr6Mo)
Cobalt Chrome (Co28Cr6Mo) is a superalloy is known for its high strength-to-weight ratio.
Primary Benefits
- High performance tensile and creep
- Corrosion resistance
LEARN MORE>
Titanium (Ti6Al4V)
Titanium (Ti6Al4V) is a workhorse alloy. Versus Ti grade 23 annealed, the mechanical properties of Ti6Al4V are comparable to wrought titanium for tensile strength, elongation, and hardness. Final parts built in Ti6Al4V receive vacuum stress relief application.
Primary Benefits
- High stiffness and strength relative to weight
- High temperature and corrosion resistance
LEARN MORE>
Compare Material Properties
20 μm = high resolution (HR)
30, 40, and 60 μm = normal resolution (NR)
- US
- Metric
Materials | Resolution | Condition | Ultimate Tensile Strength (ksi) | Yield Stress (ksi) | Elongation (%) | Hardness |
---|---|---|---|---|---|---|
Stainless Steel (17-4 PH) | 20 μm | Solution & Aged (H900) | 199 | 178 | 10 | 42 HRC |
30 μm | Solution & Aged (H900) | 198 | 179 | 13 | 42 HRC | |
Stainless Steel (316L) | 20 μm | Stress Relieved | 82 | 56 | 78 | 90 HRB |
30 μm | Stress Relieved | 85 | 55 | 75 | 88 HRB | |
Aluminum (AlSi10Mg) | 20 μm | Stress Relieved | 39 | 26 | 15 | 42 HRB |
30 μm | Stress Relieved | 50 | 33 | 8 | 59 HRB | |
40 μm | Stress Relieved | 43 | 27 | 10 | 50 HRB | |
Cobalt Chrome (Co28Cr6Mo) | 20 μm | As Built | 182 | 112 | 17 | 39 HRC |
30 μm | As Built | 176 | 119 | 14 | 38 HRC | |
Inconel 718 | 20 μm | Stress Relieved | 143 | 98 | 36 | 33 HRC |
30 μm | Stress Relieved | 144 | 91 | 39 | 30 HRC | |
30 μm | Solution & Aged per AMS 5663 | 208 | 175 | 18 | 46 HRC | |
60 μm | Stress Relieved | 139 | 83 | 40 | 27 HRC | |
60 μm | Solution & Aged per AMS 5663 | 201 | 174 | 19 | 45 HRC | |
Titanium (Ti6Al4V) | 20 μm | Stress Relieved | 153 | 138 | 15 | 35 HRC |
30 μm | Stress Relieved | 144 | 124 | 18 | 33 HRC |
Materials | Resolution | Condition | Ultimate Tensile Strength (MPa) | Yield Stress (MPa) | Elongation (%) | Hardness |
---|---|---|---|---|---|---|
Stainless Steel (17-4 PH) | 20 μm | Solution & Aged (H900) | 1,372 | 1,227 | 10 | 42 HRC |
30 μm | Solution & Aged (H900) | 1,365 | 1,234 | 13 | 42 HRC | |
Stainless Steel (316L) | 20 μm | Stress Relieved | 565 | 386 | 78 | 90 HRB |
30 μm | Stress Relieved | 586 | 379 | 75 | 88 HRB | |
Aluminum (AlSi10Mg) | 20 μm | Stress Relieved | 268 | 180 | 15 | 46 HRB |
30 μm | Stress Relieved | 345 | 228 | 8 | 59 HRB | |
40 μm | Stress Relieved | 296 | 186 | 10 | 50 HRB | |
Cobalt Chrome (Co28Cr6Mo) | 20 μm | As Built | 1255 | 772 | 17 | 39 HRC |
30 μm | As Built | 1213 | 820 | 14 | 38 HRC | |
Copper (CuNi2SiCr) | 20 μm | Precipitation Hardened | 496 | 434 | 23 | 87 HRB |
Inconel 718 | 20 μm | Stress Relieved | 986 | 676 | 36 | 33 HRC |
30 μm | Stress Relieved | 993 | 627 | 39 | 30 HRC | |
30 μm | Solution & Aged per AMS 5663 | 1434 | 1207 | 18 | 46 HRC | |
60 μm | Stress Relieved | 958 | 572 | 40 | 27 HRC | |
60 μm | Solution & Aged per AMS 5663 | 1386 | 1200 | 19 | 45 HRC | |
Titanium (Ti6Al4V) | 20 μm | Stress Relieved | 1055 | 951 | 15 | 35 HRC |
30 μm | Stress Relieved | 993 | 855 | 18 | 33 HRC |
These figures are approximate and dependent on a number of factors, including but not limited to, machine and process parameters. The information provided is therefore not binding and not deemed to be certified. When performance is critical, also consider independent lab testing of additive materials or final parts.
Surface Finish Options
Standard Finish
Expect roughness values of 200 to 400 µin Ra (0.005 to 0.010mm Ra), depending on material and resolution. Support structures are removed and layer lines are visible.
Custom Finish
We offer brushed surfaces in a range of grits and polished mirror finishes. Be sure to indicate if the custom surface finish is for functional or aesthetic purposes so we can best consult you on our custom options.
Post-Processing Capabilities for Metal 3D-Printed Parts
Improve strength, dimensional accuracy, and cosmetic appearance of final metal components with DMLS for production.
Surface Finishing
- 3- and 5-axis milling
- Turning
- Polish (Mirror or Brushed)
- Passivation
- Wire EDM
- Tapping and reaming
Heat Treatments
- Stress relief
- NADCAP heat treatment
- Hot isostatic pressing (HIP)
- Solution annealing
- Aging
Mechanical Testing
- Tensile
- Rockwell Hardness
Powder Analysis & Material
- Traceability
- Chemistry
- Particle size and distribution analysis
Why Use Metal 3D Printing?
See how metal additive manufacturing technology can be used to reduce components within an assembly, fabricate complex geometries, and ultimately save you time and costs.
Click to enlarge
How Does Metal 3D Printing Work?
The DMLS machine begins sintering each layer—first the support structures to the base plate, then the part itself—with a laser aimed onto a bed of metallic powder. After a cross-section layer of powder is micro-welded, the build platform shifts down and a recoater blade moves across the platform to deposit the next layer of powder into an inert build chamber. The process is repeated layer by layer until the build is complete.
When the build finishes, an initial brushing is manually administered to parts to remove a majority of loose powder, followed by the appropriate heat-treat cycle while still fixtured in the support systems to relieve any stresses. Parts are removed from the platform and support structures are removed from the parts, then finished with any needed bead blasting and deburring. Final DMLS parts are near 100 percent dense.
Large Format Metal 3D Printing
We recently added the GE Additive X Line to our fleet of metal 3D printers to build large Inconel 718 and Aluminum (AlSi10Mg) parts. Have a project that might be a good fit? Contact us and we can discuss your requirements.
Learn More >
Metal 3D Printing for Production
Improve strength, dimensional accuracy, and cosmetic appearance for end-use metal components with post-processing options like CNC machining and heat treatments.
Learn More >
Resources
Design Tip
Post-Processing for Metal 3D Printing
Learn how to improve dimensional accuracy, surface roughness, and mechanical properties on metal parts with high-requirement applications.
Read Design Tip
White Paper
Combining Part Assemblies with Additive Manufacturing to Reduce Cost and Increase Performance
How to find the right opportunities to consolidate multi-part assemblies into single components with industrial 3D printing
Read White Paper
Blog
Inconel 718: A Workhorse Material for Additive Manufacturing
Inconel 718 is a go-to material for additive manufacturing of metal parts.
Read Blog
Blog
Large Format 3D Printing for Aluminum and Inconel Parts
When you’re printing really large parts in metal, it’s great to have a choice of materials. Aluminum and Inconel 718 both make a lot of sense, but which one is the best for your application?
Read Blog
Instant quotes on 3D-printed parts
Get A QuoteStereolithography (SLA) 3D Printing Service
Back
-
Materials
Materials by Service
Injection MoldingCNC Machining3D PrintingSheet Metal
Materials by Type
PlasticsMetalsElastomers
Related Links
Customer Supplied ResinsColors
Injection Molding Material Alternatives Guide
Struggling with thermoplastic material shortages? We created a detailed guide to resin substitutes for ABS, PC, PP, and other commonly molded thermoplastics.
Download
-
Resources
Design Tips Guides and Trend Reports Case Studies Design Aids Webinars and Trade Shows
Blog Videos FAQs Educators and Students Glossary
Industries Medical Aerospace Automotive Consumer Electronics Industrial Equipment
-
About Us
Who We Are Why Protolabs? Research and Development Cool Idea Award Partnerships Sustainability and Social Impact
Careers Investors Locations Press Procurement
Contact Us
Proto Labs, Inc.
5540 Pioneer Creek Dr.
Maple Plain, MN 55359
United StatesP: 877.479.3680
F: 763.479.2679
E: [email protected]Best-in-Class Online Quoting
After uploading your part design, you'll receive an online quote that includes manufacturing analysis to help improve part manufacturability. Within your quote, you can also adjust quantity and material and see price changes in real-time.
Learn More
Get a QuoteSign In
SLA 3D printing service for rapid prototyping. Get an instant online quote.
GET SLA PARTS
Jump to Section→ Capabilities
→ SLA Materials
→ Compare SLA Material Properties
→ Surface Finishes
→ Post-Processing
→ Our SLA 3D Printers
→ Why SLA 3D Printing?
Stereolithography (SLA) is an industrial 3D printing process used to create concept models, cosmetic prototypes, and complex parts with intricate geometries in as fast as 1 day. A wide selection of materials, extremely high feature resolutions, and quality surface finishes are possible with SLA.
SLA 3D printing is primarily used for:
- parts requiring high accuracy and features as small as 0.002 in.
- good surface quality for cosmetic prototypes
- form and fit testing
If you have any issues getting your guide, click here to download.
3D Printing Surface Finish Guide
Get this quick reference guide to explore your surface finish options across our six 3D printing technologies.
United States of AmericaAfghanistanÅland IslandsAlbaniaAlgeriaAmerican SamoaAndorraAngolaAnguillaAntarcticaAntigua and BarbudaArgentinaArmeniaArubaAustraliaAustriaAzerbaijanBahamasBahrainBangladeshBarbadosBelarusBelgiumBelizeBeninBermudaBhutanBolivia, Plurinational State ofBonaire, Sint Eustatius and SabaBosnia and HerzegovinaBotswanaBouvet IslandBrazilBritish Indian Ocean TerritoryBrunei DarussalamBulgariaBurkina FasoBurundiCambodiaCameroonCanadaCape VerdeCayman IslandsCentral African RepublicChadChileChinaChristmas IslandCocos (Keeling) IslandsColombiaComorosCongoCongo, the Democratic Republic of theCook IslandsCosta RicaCôte d'IvoireCroatiaCubaCuraçaoCyprusCzech RepublicDenmarkDjiboutiDominicaDominican RepublicEcuadorEgyptEl SalvadorEquatorial GuineaEritreaEstoniaEthiopiaFalkland Islands (Malvinas)Faroe IslandsFijiFinlandFranceFrench GuianaFrench PolynesiaFrench Southern TerritoriesGabonGambiaGeorgiaGermanyGhanaGibraltarGreeceGreenlandGrenadaGuadeloupeGuamGuatemalaGuernseyGuineaGuinea-BissauGuyanaHaitiHeard Island and McDonald IslandsHoly See (Vatican City State)HondurasHong KongHungaryIcelandIndiaIndonesiaIran, Islamic Republic ofIraqIrelandIsle of ManIsraelItalyJamaicaJapanJerseyJordanKazakhstanKenyaKiribatiKorea, Democratic People's Republic ofKorea, Republic ofKuwaitKyrgyzstanLao People's Democratic RepublicLatviaLebanonLesothoLiberiaLibyaLiechtensteinLithuaniaLuxembourgMacaoMacedonia, the Former Yugoslav Republic ofMadagascarMalawiMalaysiaMaldivesMaliMaltaMarshall IslandsMartiniqueMauritaniaMauritiusMayotteMexicoMicronesia, Federated States ofMoldova, Republic ofMonacoMongoliaMontenegroMontserratMoroccoMozambiqueMyanmarNamibiaNauruNepalNetherlandsNew CaledoniaNew ZealandNicaraguaNigerNigeriaNiueNorfolk IslandNorthern Mariana IslandsNorwayOmanPakistanPalauPalestine, State ofPanamaPapua New GuineaParaguayPeruPhilippinesPitcairnPolandPortugalPuerto RicoQatarRéunionRomaniaRussian FederationRwandaSaint BarthélemySaint Helena, Ascension and Tristan da CunhaSaint Kitts and NevisSaint LuciaSaint Martin (French part)Saint Pierre and MiquelonSaint Vincent and the GrenadinesSamoaSan MarinoSao Tome and PrincipeSaudi ArabiaSenegalSerbiaSeychellesSierra LeoneSingaporeSint Maarten (Dutch part)SlovakiaSloveniaSolomon IslandsSomaliaSouth AfricaSouth Georgia and the South Sandwich IslandsSouth SudanSpainSri LankaSudanSuriNameSvalbard and Jan MayenSwazilandSwedenSwitzerlandSyrian Arab RepublicTaiwan, Province of ChinaTajikistanTanzania, United Republic ofThailandTimor-LesteTogoTokelauTongaTrinidad and TobagoTunisiaTurkeyTurkmenistanTurks and Caicos IslandsTuvaluUgandaUkraineUnited Arab EmiratesUnited KingdomUnited States Minor Outlying IslandsUruguayUzbekistanVanuatuVenezuela, Bolivarian Republic ofViet NamVirgin Islands, BritishVirgin Islands, U. S.Wallis and FutunaWestern SaharaYemenZambiaZimbabwe
I agree to receive email messages containing service updates and Design Tips from Protolabs and its affiliates
SLA Design Guidelines and Capabilities
Our basic guidelines for stereolithography include important design considerations to help improve part manufacturability, enhance cosmetic appearance, and reduce overall production time.
SLA Tolerances
For well-designed parts, tolerances in the X/Y dimension of ±0.002 in. (0.05mm) for first inch plus 0.1% of nominal length. (0.001mm/mm), and Z dimension tolerances of ±0.005 in. for first inch plus 0.1% of nominal length, can typically be achieved. Note that tolerances may change depending on part geometry.
Max Part Size
Layer Thickness
Minimum Feature Size
Minimum Wall Thickness
Minimum Hole Size
Tolerances
*Available for the following materials: ABS-Like White and Gray, ABS-Like Translucent/Clear, and PC-Like Translucent/Clear
SLA Material Options
ABS-Like White (Accura Xtreme White 200)
ABS-Like White (Accura Xtreme White 200) is a widely used general purpose SLA material. In terms of flexibility and strength, this material falls between molded polypropylene and molded ABS, which makes it a good choice for functional prototypes. Parts as large as 29 in. x 25 in. x 21 in. can be built with ABS-Like White so consider it a primary option if you require an extensive part size build envelope.
Primary Benefits
- Durable, general purpose resin
- Accommodates extra-large parts
ABS-Like Gray (Accura Xtreme Gray)
ABS-Like Gray (Accura Xtreme Gray) is a widely used general purpose SLA material. In terms of flexibility and strength, this material falls between molded polypropylene and molded ABS, which makes it a good choice for functional prototypes. ABS-Like Gray offers the highest HDT of the ABS-like SLA resins.
Primary Benefits
- Durable, general purpose resin
- Highest HDT of the ABS-like SLA resins
ABS-Like Black (Accura 7820)
ABS-Like Black (Accura 7820) is a widely used general purpose material. Its deep black color and glossy up-facing surfaces in a top profile offer the appearance of a molded part, while layer lines may be visible in a side profile. RenShape 7820 also has low moisture absorption (0.25% per ASTM D570) so that parts are more dimensionally stable. Compared to other SLA materials, it has midrange values for all mechanical properties.
Primary Benefits
- Low moisture absorption
- Glossy cosmetic appearance
ABS-Like Translucent/Clear (WaterShed XC 11122)
ABS-Like Translucent/Clear (WaterShed XC 11122) offers a unique combination of low moisture absorption (0.35% 0.25% per ASTM D570) and near-colorless transparency. Secondary operations are required to achieve functional part clarity, and the part will also retain a very light blue hue afterward. While good for general-purpose applications, WaterShed is the best choice for flow-visualization models, light pipes, and lenses.
Primary Benefits
- Lowest moisture absorption of SLA resins
- Functional transparency
MicroFine™ (Gray and Green)
MicroFine™ is a custom formulated material available in gray and green that is exclusive to Protolabs. This ABS-like thermoset is printed in Protolabs’ customized machinery to achieve high resolution features as small as 0.002 in. MicroFine is ideal for small parts, generally less than 1 in. by 1 in. by 1 in. In terms of mechanical properties, MicroFine falls in the mid-range of SLA materials for tensile strength and modulus and on the low end for impact strength and elongation.
Primary Benefits
- Produces highest resolution parts
- Ideal for extra-small parts
PP-Like Translucent White (Somos 9120)
PP-Like Translucent White (Somos 9120) is the most flexible SLA option outside of Carbon RPU 70 and FPU 50. In direct comparison to the average values of an injection-molded polypropylene, 9120 has similar tensile strength, tensile modulus, flexural modulus, and impact strength. The only departure from molded PP is its elongation value, which is only 25% of the molded thermoplastic.
Primary Benefits
- Semi-flexible
- Translucency
PC-Like Advanced High Temp (Accura 5530)
PC-Like Advanced High Temp (Accura 5530) creates strong, stiff parts with high temperature resistance. A thermal post-cure option can increase HDT as high as 482°F at 0.46 MPa loading. Accura 5530 has the highest E-modulus of all the unfilled SLA materials, and it is known for being resistant to automotive fluids. However, the thermal curing process does make Accura 5530 less durable, resulting in a 50% reduction to elongation.
Primary Benefits
- High elastic modulus
- Higher resistance to heated fluids
PC-Like Translucent/Clear (Accura 60)
PC-Like Translucent/Clear (Accura 60) is an alternative to the general purpose ABS-like materials and WaterShed XC 11122 when stiffness is desired. Like WaterShed, this material can be custom finished to achieve functional transparency with secondary processing. Accura 60 has the highest tensile strength of and elastic modulus compared of all SLA materials outside of the Advanced High Temp options that are most often thermal cured.
Primary Benefits
- High stiffness
- Functional transparency
Ceramic-Like Advanced HighTemp (PerFORM)
Ceramic-Like Advanced HighTemp (PerFORM) exhibits the highest tensile strength and E-modulus making it the stiffest performance material of the SLA materials. When the thermal cure option is applied to parts made from PerFORM, it exhibits the highest HDT (as high as 514°F at 0.46 MPa loading) of the SLA materials.
Primary Benefits
- Stiffest SLA resin
- Highest HDT of SLA resins
Compare SLA Material Properties
- US
- Metric
Material | Color | Tensile Strength | Tensile Modulus | Elongation |
---|---|---|---|---|
ABS-Like White (Accura Xtreme White 200) | White | 7.9 ksi | 479 ksi | 9% |
ABS-Like Gray (Accura Xtreme Gray) | Gray | 5.8 ksi | 290 ksi | 9% |
ABS-Like Black (Accura 7820) | Black | 7.0 ksi | 435 ksi | 5% |
ABS-Like Translucent/Clear (WaterShed XC 11122) | Translucent/Clear | 7. | 421 ksi | 6% |
MicroFine™ (Gray and Green) | Gray or Green | 8.7 ksi | 377 ksi | 8% |
PP-Like Translucent White (Somos 9120) | Translucent/White | 5.0 ksi | 232 ksi | 25% |
PC-Like Translucent/Clear (Accura 60) | Translucent/Clear | 10.8 ksi | 508 ksi | 7% |
PC-Like Advanced High Temp* (Accura 5530) | Translucent/Amber | 6.5 ksi | 566 ksi | 1.5% |
Ceramic-Like Advanced HighTemp* (PerFORM) | White | 10.9 ksi | 1523 ksi | 1% |
*Properties listed are based on thermal cure
Material | Color | Tensile Strength | Tensile Modulus | Elongation |
---|---|---|---|---|
ABS-Like White (Accura Xtreme White 200) | White | 54.47 Mpa | 3300 Mpa | 9% |
ABS-Like Gray (Accura Xtreme Gray) | Gray | 39.![]() | 2000 Mpa | 9% |
ABS-Like Black (RenShape SL7820) | Black | 48.26 Mpa | 3000 Mpa | 5% |
ABS-Like Translucent/Clear (WaterShed XC 11122) | Translucent/Clear | 54.47 Mpa | 2600 Mpa | 6% |
MicroFine™ (Gray and Green) | Gray or Green | 59.98 Mpa | 2600 Mpa | 8% |
PP-Like Translucent White (Somos 9120) | Translucent/White | 34.47 Mpa | 1600 Mpa | 25% |
PC-Like Translucent/Clear (Accura 60) | Translucent/Clear | 74.46 Mpa | 3503 Mpa | 7% |
PC-Like Advanced High Temp* (Accura 5530) | Translucent/Amber | 44.81 Mpa | 3902 Mpa | 1.5% |
Ceramic-Like Advanced HighTemp* (PerFORM) | White | 75.15 Mpa | 10,500 Mpa | 1% |
*Properties listed are based on thermal cure
These figures are approximate and dependent on a number of factors, including but not limited to, machine and process parameters. The information provided is therefore not binding and not deemed to be certified. When performance is critical, also consider independent lab testing of additive materials or final parts.
Surface Finish Options for SLA Parts
Material: ABS-like Translucent/Clear
Finish: Unfinished
Material: MicroFine Gray™
Finish: Unfinished
Material: ABS-like Translucent/Clear
Finish: Standard
Material: MicroFine Gray™
Finish: Standard
Material: ABS-like Translucent/Clear
Finish: Natural
Material: MicroFine Gray™
Finish: Natural
Material: ABS-like Translucent/Clear
Finish: Custom
Material: MicroFine Gray™
Finish: Custom
Additional Finishing Options
Custom finishing is a mix of science, technology, and fine art that can transform a part to your exact specifications. Finishes include:
- Soft-touch paint
- Clear part finishing
- Paint finishes
- Masking
- Color matching
- Decals/graphic
- Texture
Metal Plating
Our metal-plating process for SLA coats a ceramic-filled PC-like material (Somos PerFORM) with a nickel that gives parts the look, feel, and strength of metal, but without the weight. The combination of the material’s strength, rigidity, and temperature resistance with nickel plating, takes strength, stiffness, and impact and temperature resistance to a degree previously unattainable in SLA parts.
Microfluidics
Our microfluidic fabrication process is a modified form of high-resolution SLA that uses a clear ABS-like material (WaterShed XC 11122). Parts are resistance to water and humidity, and work well for lens and flow-visualization models.
Our SLA 3D Printers
Our stereolithography machines consists of Vipers, ProJets, and iPros. In high-resolution mode, Vipers and ProJets can make parts with extremely tiny features and crisp details, while in normal-resolution mode, they can build cost-effective parts very quickly.
iPros have extremely large build volumes at 29 in. by 25 in. by 21 in. (736mm by 635mm by 533mm), yet are still able to image highly detailed parts easily.
Why Use SLA?
Stereolithography (SLA) is an additive manufacturing process that can 3D print parts with small features, tight tolerance requirements, and smooth surface finishes.
How Does SLA 3D Printing Work?
The SLA machine begins drawing the layers of the support structures, followed by the part itself, with an ultraviolet laser aimed onto the surface of a liquid thermoset resin. After a layer is imaged on the resin surface, the build platform shifts down and a recoating bar moves across the platform to apply the next layer of resin. The process is repeated layer by layer until the build is complete.
Newly built parts are taken out of machine and into a lab where solvents are used to remove any additional resins. When the parts are completely clean, the support structures are manually removed. From there, parts undergo a UV-curing cycle to fully solidify the outer surface of the part. The final step in the SLA process is the application of any custom or customer-specified finishing. Parts built in SLA should be used with minimal UV and humidity exposure so they don’t degrade.
SLA Resources
Design Tip
An Introduction to Stereolithography (SLA) 3D Printing
Stereolithography, a staple of 3D printing, can deliver complex prototypes quickly and accurately.
Read Design Tip
Design Tip
Selecting a Material for Stereolithography (SLA) 3D Printing
Compare materials for stereolithography with one another and with injection-molded plastics.
Read Design Tip
Blog
SLA vs. FDM: Comparing Common 3D Printing Technologies
See how these two 3D printing technologies stack up for prototype parts. Understanding the advantages of each will help accelerate design.
Read Blog
Guide
What is 3D Printing?
Gain an understanding of additive manufacturing and how it can be leveraged to improve product development through rapid prototyping and production.
Read Guide
Get an instant online quote for 3D printing.
Get a Quote
Concept Laser (General Electric) metal 3D printers to be equipped with computer vision and machine learning systems
3D printing
Just a few years ago, engineers at General Electric (GE) needed 800 parts to assemble just 30% of a new turboprop.
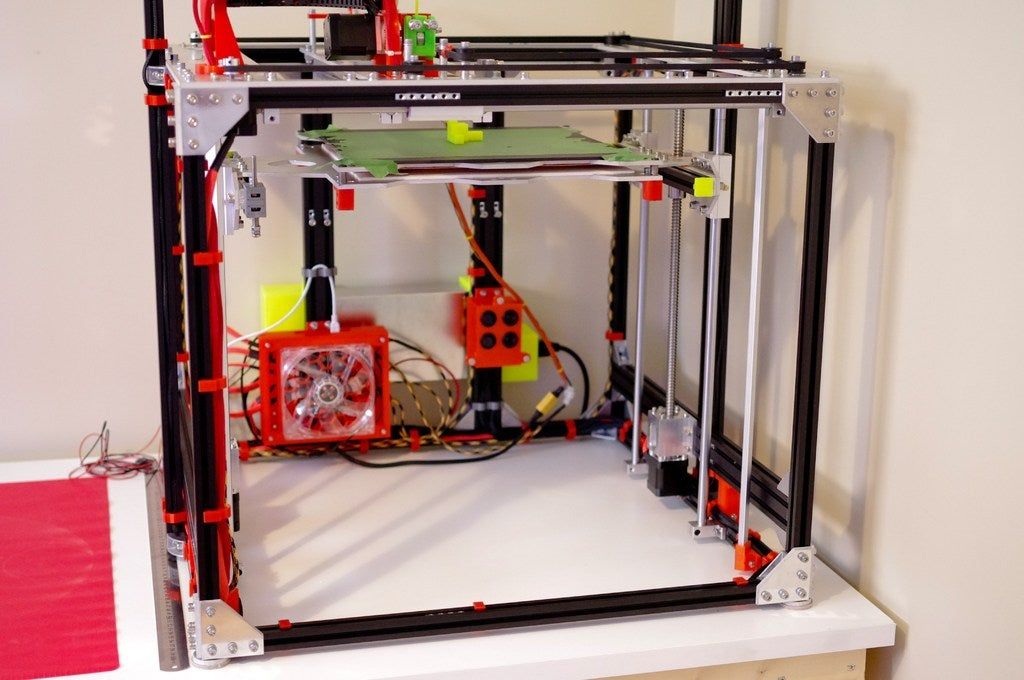
Printing complex parts with 3D printers is possible because they recreate the necessary components step by step right from the computer. Industrial metal 3D printers using laser melting (SLM) or electron beam melting (EBM) technology fuse super-thin layers of fine metal powder into precise final parts that were previously impossible or impractical to produce with traditional methods.
However, printing aircraft engine parts remains an extremely difficult task. To solve this problem, GE Aviation opened a huge additive technology center in Ohio, where engineers prepare 3D printed parts for mass production. At this center, GE Research and colleagues at GE Additive aim to make the 3D manufacturing journey as simple as possible by making printing a one-step process.
Pictured: A GE worker preparing a 3D printer for part
“We want the manufacturer to be able to monitor the quality of printed parts in real time. By integrating edge computing into 3D printers, we have given these machines digital eyes to track every layer applied every time they print,” said Randy Rausch, senior edge computing engineer at GE Research.
Edge computing is the opposite of sending data to the cloud. In edge computing, information is processed directly on 3D printers that directly use this data in order to localize traffic and reduce delays. These computing systems are equipped with machine learning algorithms to perform instant analysis and provide information to printer operators or directly to printers.
Why is this important? Additive manufacturing is a rapidly evolving discipline that requires many steps and iterations to get the right mix of materials, strength, layer thickness, and other build parameters. For example, creating supports for printable parts is currently a difficult and time consuming task.
Engineers at GE Research develop software to help colleagues and customers prototype, print, and test parts faster with fewer resources.
Pictured: GE Catalyst turboprop engine with large 3D printed sections
Working at GE Research additive labs in Niskeynua, NY, Rausch and his team intentionally interfere with the printing process, introducing anomalies, reducing laser power to detect how the sensors on the printer will detect the problem. As a result, the software is increasingly in control of the process with the speed and precision needed to prevent or correct minor defects in the printing process.
The ability to see parts printed in real time could soon completely transform the 3D printing process, making it even faster, better and more affordable.
You can learn more about the models, capabilities and prices of Concept Laser GE industrial metal 3D printers for medicine in the catalog of the exclusive distributor NISSA Digispace.
Subscribe to the author
Subscribe
Don't want
4
More interesting articles
DrProg
Loading
11/08/2022
1548
9
Subscribe to the author
Subscribe
Don't want
We continue to reveal the incredible opportunities of enterprises from the Middle Kingdom, up to...
Read more
261
Follow author
Follow
Don't want
I continue the series of articles started with the part devoted to polymers.
This part will be devoted to...
Read more
198
Subscribe to the author
Subscribe
Don't want
Here I am again :)
With good and joyful news.
But first I want...
Read more
For the first time in Russia, a 3D printer for printing with high-temperature engineering plastics has been created
An innovative breakthrough was made by Total Z, which our magazine met a year and a half ago. Even then, the company was firmly on its feet, producing industrial 3D printers for printing with the most common ABS plastics. In parallel, intensive scientific research was going on. The team worked on prototype printers capable of printing specialized engineering high-temperature plastics. And today, engineering printers for printing with high-temperature plastics have already entered the series. The founding fathers of the company Alexey Dubinin and Andrey Belousov told about this and another equally important columnist of the Additive Technologies magazine.
A long road to the
Series There were several challenges to overcome to move from a regular 3D printer to an engineering one. “Physical and chemical properties of printed products are the only criterion for the quality of engineering printers. The part after printing must be cast, that is, it must have a uniform crystal lattice and the required strength factor, including between printing layers, the developers explain the physics of the process. — To achieve this result, the previous layer at the time of application of the next layer must have a temperature above the glass transition temperature (for engineering plastics, this is 200-300°C). To do this, you need to create an appropriate environment in the chamber, a stable temperature regime - up to 300°C in the chamber and up to 500°C in the extruder. This is what determines the complexity of designing such printers. After all, the operating temperature of any electronics, any mechanical unit, any motor and “further down the list” is a maximum of 80 degrees, therefore it was necessary to separate the printable area from all other elements, not forgetting about fire safety, as well as the safety of the operator, who under no circumstances should get burned during work.
” And only in this way, step by step, bringing together complex design, engineering and technical tasks, "Total Z" came to the third generation of 3D printers for high-temperature printing with engineering plastics.
Today, Total Z is the only company in Russia that mass-produces 3D printers for printing with engineering high-temperature plastics, including materials such as Ultem 9085/1010, polysulfone (PSU), polyphenylene sulfone (PPSU), polyketone, PEEK and other. The real competitor in the Russian market "Total Z" calls only the American company Stratasys with its Fortus 3D printer.
Anyform 450-PRO and Anyform 650-PRO printers
Sometimes customers come to "Total Z" who need high-temperature printing, but at the same time they want the printer to be desktop, "like a Chinese one". First of all, I have to explain that the temperature in the Chinese printer's chamber is 80°C. Some kind of "sticking" of the layers can be achieved even at such a temperature, but there cannot physically be a homogeneous crystal lattice during the transition from one layer to another, and, accordingly, there will be no strength. Unscrupulous suppliers may offer all sorts of modified plastics under well-known names or simply print materials, but with dubious physical properties of the resulting products beyond the specifications. And a 3D printer for printing engineering high-temperature plastics cannot have desktop dimensions either. Let's just count. For example, the Anyform Pro Series work chambers can have a side from 450mm to 1200mm. The working chamber, where it should be 300 ° C, must be packed in 150 mm thick thermal insulation, which adds 300 mm horizontally and vertically. Since the X and Y axes in the printer are not belt drives, but ball screws, the overall size still grows to ensure speed, size and positioning accuracy. And it is the technical solutions embedded in the printer that bring it to "non-desktop" overall dimensions. “Actually, you can, of course, make a desktop printer for a camera with 300 ° C, but then the print area will be small,” Anyform developers ironically.
There is another important point for high-quality industrial printers, which was emphasized by the creators of Anyform. Many industrial plastics, such as nylon, caprolon, polypropylene, have a high shrinkage coefficient, and they definitely need a vacuum table for printing. Some suppliers claim that you can print without it, but only if you use their plastic. “It is quite obvious that this is no longer the nylon that the customer is counting on, and which is incorporated in his methods, specifications with available certificates, test reports, and so on,” warn Total Z.
Everyone needs it
Anyform printers can be used in almost any subject area. In all markets, speed, weight reduction and cheaper products are being updated, but Total Z says that in our country today they are most in demand for the aerospace industry, medicine and the automotive industry. For the aerospace industry, the resulting products are attractive due to their non-combustibility, high strength, cost reduction and significant weight reduction, which leads to an increase in energy efficiency. It is also important that at ULTEM 9085 has European "flight" certificates. For medicine, first of all, it is important that PEEK is biocompatible, ULTEM1010 allows modern sterilization methods and, of course, certificates are required. The automotive industry, according to the observations of my interlocutors, is now in a phase of active experiments with materials, for which it is acquiring printers, while the agricultural engineering industry is demonstrating a growing demand for 3D printers for printing parts and molds. On the Total Z printer, a model for casting a part can be printed in 2-3 days, which cannot be achieved by milling. For agricultural machinery, this is incredibly important. The harvesting season is short, the equipment is working with enormous loads, and it is necessary to repair it almost in a matter of minutes. Military-industrial complex enterprises also have their own reasons.
A helm (black)
Material: ULTEM 9085
Printer: Anyform 450-Pro (Hot+)
Anatomical Skull Implant “Why don't we take a swing at our William Shakespeare? I asked. Tube, media: ULTEM 9085, printer: Anyform 650-PRO(HOT+) “We have our own principles for forming a component base,” my interlocutors state their approach. We do everything responsible ourselves. For less important parts, we try to find reliable domestic suppliers through cooperation. If we don’t find it, then we follow the path of developing our own production. What you can buy ready-made in Russia, we buy here. And if it’s impossible to make or buy in Russia, we buy outside the country from reliable proven manufacturers of industrial equipment.” In practice, it looks like this. The company itself makes metal frame structures, turning, partly milling. The printheads of our own design are manufactured by a Russian partner. Metal and glass are bought from Russian manufacturers, but hex bolts and high-strength bolts, as 3D printer manufacturers said, no one in our country makes. Total Z has its own electronics, but the entire component base in the boards is imported due to the lack of domestic Mechanical part: ball screws, guides - only Bosch. Anyform developers do not tie the consumer to a specific plastic manufacturer, while often US and European 3D printer manufacturers prescribe only their own plastic. “We don’t have serfdom, we don’t restrict the consumer,” they explain in Total Z. - And Russian manufacturers produce very interesting plastics that are used in one area or another. These are the Moscow Institute of Plastics named after G. S. Petrov, where high-quality certified PEEK is produced, Kabardino-Balkarian State University, NIRP and other Russian companies. Our other competitive advantage is the price, which is a multiple of the price of foreign suppliers with comparable quality.
Printer: Anyform 650-PRO 9000 9000 9000 9000 9000 9 Metal printing: intentions and reality
— For printing with metal? Top managers of Total Z really see such an opportunity for their company, but they are aware that today the metal printing market in our country has uncertain prospects due to the high cost of the final part and some technological limitations. “I don’t want to beat my head against the wall,” my interlocutors joke. — But seriously, in plastic printing, not all prospects have been exhausted yet. We continue to develop various 3D printers, including those with ultra-high productivity, machines for laser powder sintering and SLS plastic technology. The step from SLS to SLM is small, and we can say with confidence: by the time the market demand is finalized, we will have something to offer the market.” Business processes in the company are debugged so that when the prototype is ready to go into series, everything will be ready for launch into series: design documentation, assembly drawings, specifications, the purchasing department will know what needs to be purchased, in what quantities, up to the number of bolts.
A company with principles
When asked what is the most expensive thing in the money in the Total Z printer, there was an instant answer with a touch of pride: “The work of designers and assemblers of the highest qualification who are working to make the printer competitive. This is also our principle. High-class work should be adequately paid.
In the role of authority
Plus we're always here. We test their plastics together with customers, because new plastics require not only the appropriate equipment, but also the appropriate printing speeds, temperature conditions, and the number of combinations is very large. It happens that a client has received new material, but they are unable to print, and mutual claims begin, they say, your printer is not the right one, and your material is not the same. In such situations, an expert opinion is required, for which they come to us. We have proven technologies for selecting modes, we can print with different plastics, and we teach customers how to print with plastic. And plastic manufacturers come to us so that we can choose a mode and generally try their plastic. Some people have the ability to print on Stratasys, but they can't put it in there. And if they manage to somehow deceive the machine and somehow put non-standard plastic there, they cannot print in the necessary modes, only in standard ones, which are far from always suitable.
Manufacturers of Russian Anyform say that it is beneficial for them to participate in such work, and this benefit is not always only financial, sometimes they have to go to additional costs. But, firstly, such is the specifics of the Russian market that other opportunities for additive printing equipment consumers are simply not visible. Secondly, this is an additional service, for which the company receives an additional piece of the market. And thirdly, Total Z receives both feedback and experience. And all this together creates the image of an open company for Total Z.
"Total Z" is now actively interacting with the machine tool department of the Ministry of Industry and Trade of the Russian Federation, where a working group on additive technologies has appeared. The created group began to form a list of enterprises involved in additive technologies, and it turned out that in Russia there is only one manufacturer of industrial printers that print plastics using FDM technology.
Learn more