Infill in 3d printing
Infill in 3D Printing: Definition, Main Parts, and Different Types
Resources3D Printing DesignInfill in 3D Printing: Definition, Main Parts, and Different Types
Learn about the importance of infill in 3D printing design and the different types of infill patterns.
By Team Xometry
August 23, 2022
9 min read
RECENT STORIES
TPR vs. PVC: Material Differences and Comparisons
December 23, 2022
6 min read
TPR vs. Latex: Material Differences and Comparisons
December 23, 2022
8 min read
Alloy Steel vs. Stainless Steel
December 23, 2022
8 min read
3D printing infill refers to the internal structure of a 3D printed part. This internal structure can be produced using many different shapes. The purpose of infill is to optimize part weight, strength, and printing time. Many different infill patterns exist. These standard designs can be selected in the 3D slicing software menu used to prepare parts for printing.
This article will define 3D printing infill, discuss how to select the correct infill pattern and density, and describe the various infill patterns.
What Is Infill in 3D Printing?
“Infill” in 3D printing refers to the internal patterns found inside most 3D printed parts. Parts made by some manufacturing processes, like injection molding, must be made either completely solid or completely hollow. 3D printed parts, on the other hand, can be made with a variety of structural patterns that partially fill the space inside the outer printed walls. Almost all 3D printing technologies require infill. This is the case because printing objects in a solid material are too costly and time-consuming. For more information, see our guide on Everything You Need to Know About 3D Printing.
Figure 1 below shows the infill of a 3D printed part.
Slide 1 of 1
3D printer manufacturing big question mark.
Image Credit: Shutterstock.com/R_Boe
What Is the Purpose of Infill in 3D Printing?
The purpose of Infill in 3D printing is to save both printing time and material by creating a lattice structure inside of a 3D printed part. Printing fully dense parts is often unnecessary and is just a waste of material. The infill can be strategically placed to provide strength where in-service loads on the part are the highest. The greater the percentage of infill, the higher the density of the part.
What Are the Main Parts of Infill in 3D Printing?
A typical 3D printed part will have an outer shell with a predefined thickness. The infill structure is completely enclosed by this outer shell and is not visible when the part print is complete. The infill will be evenly distributed throughout the part. 3D printing infill is normally printed at higher speeds than the outer shell to save time. The infill print lattice is also not as thick as the shell. The many different infill patterns each have their own advantages and disadvantages.
What Are the Different Types of Infill in 3D Printing?
There are many different types of 3D printer infill. All achieve the same purpose of reducing print time and material usage. Below are some of the 3D printing infill patterns in use today:
1. Line: Line infill consists of multiple parallel lines per layer. Each layer crosses over the previous one at a 90-degree angle. Unlike other patterns, the lines don’t cross over each other on the same layer. This strengthens the part in two dimensions. Line infill is marginally quicker than grid and triangular patterns. Figure 2 is an example of line infill:
Slide 1 of 1
Line infill.
Image Credit: Xometry.com
2. Gyroid: The gyroid 3D printing infill pattern creates alternating wavy lines or curves. This infill pattern takes longer to print than the others. However, the unique gyroid internal structure allows for almost isotropic mechanical properties. Prints are still weaker on the z-axis but this pattern improves the x and y-axis shear strength. The gyroid pattern works well with flexible materials. Figure 3 is an example of a gyroid infill pattern:
Slide 1 of 1
Gyroid infill.
Image Credit: Xometry.com
3. Octet: The octet 3D printing infill pattern creates tetrahedral (pyramid-like) volumes inside the part. It is best for parts with large horizontal surfaces. Smaller gaps between the infill walls are possible due to the tapering nature of the pyramid-like volumes. This allows for shorter span distances between infill walls and a lesser chance for the material to sag. Improved top surfaces can therefore be achieved without having to increase the infill density. Figure 4 is an example of an octet infill pattern:
Slide 1 of 1
Octlet infill.
Image Credit: Xometry.com
4. Concentric: The concentric 3D printing infill is one of the fastest infill patterns to print, and it uses the least material. However, this comes at the cost of reduced part strength. The concentric pattern is not as strong as the other infill types, especially when loaded in the x or y-directions. Figure 5 is an example of a concentric infill pattern:
Slide 1 of 1
Concentric infill.
Image Credit: Xometry.com
5. Lightning: This unique infill type provides the fastest possible print time at the expense of part strength. Supports are added in a lightning bolt structure and only placed where necessary. Parts are shells except where support is needed for horizontal features or internal overhangs. Figure 6 is an example of a lightning infill pattern:
Slide 1 of 1
Lightning infill.
Image Credit: Xometry.com
6. Triangular: The triangular 3D printing infill pattern lays down plastic in a triangular grid that crosses over itself at 60-degree angles. This type of infill pattern is best used on parts with large, flat surfaces, and performs similarly to the grid pattern. The triangular infill can cause the nozzle to clog, as its lines criss-cross each other in the same layer. Figure 7 is an example of a triangular infill pattern:
Slide 1 of 1
Triangular infill.
Image Credit: Xometry. com
7. Tri-Hexagon: The tri-hexagon is the strongest infill pattern. Like the grid and triangular infill types, it will cross over itself to create a hexagonal pattern interspersed with triangles. Due to the crossing of lines in the same layer, this type of infill tends to clog the print nozzle. Figure 8 is an example of a tri-hexagon infill pattern:
Slide 1 of 1
Tri-hexagon infill.
Image Credit: Xometry.com
8. Cubic: The cubic infill type creates cubic volumes inside the part. It does this by producing a layered pattern similar to a triangular infill. However, it offsets each subsequent layer to build enclosed cube-shaped volumes in the part. The cubic volumes are oriented with the cube balanced on one corner. Figure 9 is an example of a cubic infill pattern:
Slide 1 of 1
Cubic infill.
Image Credit: Xometry.com
9. Grid: The grid is one of the most common infill types. The grid pattern lays down plastic in a cubic grid pattern that crosses over itself at 90-degree angles. This infill pattern is ideally used for prints with large, flat surfaces. Gridded infill patterns can cause nozzle clogging since the lines criss-cross over each other in the same layer. Figure 10 is an example of a grid infill pattern:
Slide 1 of 1
Grid infill.
Image Credit: Xometry.com
10. Cross: The cross pattern creates multiple cross shapes as infill. This 3D printing infill pattern is ideal for flexible part shapes as it allows for the part to bend and twist. It is not very useful for more rigid plastics, however. A 3D version of the cross is also available to add additional strength. Figure 11 is an example of a cross-infill pattern:
Slide 1 of 1
Cross infill.
Image Credit: Xometry.com
What Does the Ideal Value of the Infill Percentage Depend Upon?
The main determining factor for infill percentage is the type of application for which the part is destined to be used. Prototypes and hobbyist creations rarely need more than 20% infill. Functional parts that will be exposed to mechanical stress loads will typically require infill percentages of 50% or more.
What Is the Recommended Infill Percentage for Other Simple Exposure Objects?
For objects that will not see any significant mechanical load, a fill percentage of 20% is sufficient. It must be noted that the geometry of the part may require a different infill percentage. For example, a flat, horizontal surface may need a denser infill percentage to ensure that the top layer does not sag due to a lack of support.
How Much Infill Is Required To Achieve Maximum Tensile Strength?
The higher the infill percentage, the higher the tensile strength of the part. It must be noted that infill percentage is not the only factor that determines tensile strength. For example, filament material and print orientation play a major role. FDM parts, in particular, are anisotropic. They are weaker along the z-axis due to interlayer bonding weakness. If an FDM part is loaded in the z-direction, the dominant factor controlling its tensile strength will be the interlayer bonding quality. Infill percentage will have little effect in this case.
How To Choose the Best Type of Infill
The steps in choosing the best type of infill are:
- Check the part requirements. Calculate the infill percentage needed.
- Assess your resources, including the available material and the time you can spend per part.
- Shortlist the infill patterns that match your requirements and resources.
- Select the best infill pattern for your part.
Choosing the best infill pattern is often a trial and error process. It always pays off to do a trial print on a small part to figure out what the best settings are. Sticking with the simplest patterns, like a grid or line pattern, will normally yield good results.
What Is a Good Infill Density?
In most cases, an infill density between 20 and 50% is ideal. Less than 20% results in flimsy parts whereas more than 50% begin to take too much printing time and use too much material.
Is Infill Important for 3D Printing?
Yes, infill is an important consideration in 3D printing. Without infill, some parts may not be printable at all due to unsupported surfaces in the design. Infill adds extra strength where needed to strike a balance between the print time and the material requirements. Some parts can be printed without any infill. However, these are typically hollow shells with open tops (e.g., vases) and cannot be used for structural applications.
Summary
This article discussed the use of infill in 3D printing, the common types of infill patterns that exist, and how to select a pattern for use. To learn more about infill in 3D printing and how you can apply it to your products, contact a Xometry representative to discuss your project needs.
Xometry provides a wide range of manufacturing capabilities, including 3D printing and value-added services for all of your prototyping and production needs. Visit our website to learn more or to request a free, no-obligation quote.
Disclaimer
The content appearing on this webpage is for informational purposes only. Xometry makes no representation or warranty of any kind, be it expressed or implied, as to the accuracy, completeness, or validity of the information. Any performance parameters, geometric tolerances, specific design features, quality and types of materials, or processes should not be inferred to represent what will be delivered by third-party suppliers or manufacturers through Xometry’s network. Buyers seeking quotes for parts are responsible for defining the specific requirements for those parts. Please refer to our terms and conditions for more information.
Team Xometry
This article was written by various Xometry contributors. Xometry is a leading resource on manufacturing with CNC machining, sheet metal fabrication, 3D printing, injection molding, urethane casting, and more.
Choosing Infill Percentage For 3D Printed Parts — 3DPros
3D printed parts are typically not produced with a solid interior. Instead, the printing process uses a crosshatch or other pattern for interior surfaces. This greatly reduces cost due to reduced material usage and print time, while moderately reducing strength. The density of this pattern is referred to as the infill percentage.
The diagram below shows the appearance of various infill settings on a partially completed model. The exposed pattern would not be visible on a completed print.
Use these recommendations to choose the best infill percentage based on the requirements of your project:
0-20%: Non-functional parts: For pieces that are not functional or do not need to withstand force, such as a display model or presentation prototypes, 10-20% infill is sufficient. In some cases, no infill is a viable option if there are no large flat surfaces on the top of the print. If there are large flat surfaces on the top of the print, some infill is needed to support those surfaces.
20-40%: Light-use parts: For functional parts which will undergo some force, a moderate level of infill provides nearly the same strength as a solid part at a reduced cost.
40-100% Heavy-use parts: If your parts must withstand significant forces, or strength is the most important factor above cost, a higher infill percentage is the best choice. However, increasing infill percentage beyond 60% has diminishing returns on strength.
The price difference between higher and lower infill settings can vary greatly depending on the geometry of the model. Models with more interior volume will see a significant impact to the cost from changes in infill percentage, whereas thinner parts may see no impact.
Print speed is another factor to consider when choosing an infill percentage for a 3D print. A higher infill percentage will result in a longer print time, especially on models with a large interior volume.
Also, keep in mind that infill is not the only setting that can impact the strength of a printed part. The thickness of the outer shell and the how the part is oriented when printing are also important factors for the strength of the print. If you print your parts through us, we will help you decide on the best settings based on the requirements of your application.
Want to Learn more about buying your own 3D printer?
Our informational site www.crealityexperts.com is a great place to start! We have used Creality brand 3D printers for years and have been very happy with them
Looking to order 3D printed parts?
You can find a local vendor on Treatstock; a site for small 3D printing businesses to list their services. We have worked with them in the past and had great experiences, and we highly recommend them if you are looking to work with a small business
What is infill in 3D printing and how to properly set it up on a 3D printer.
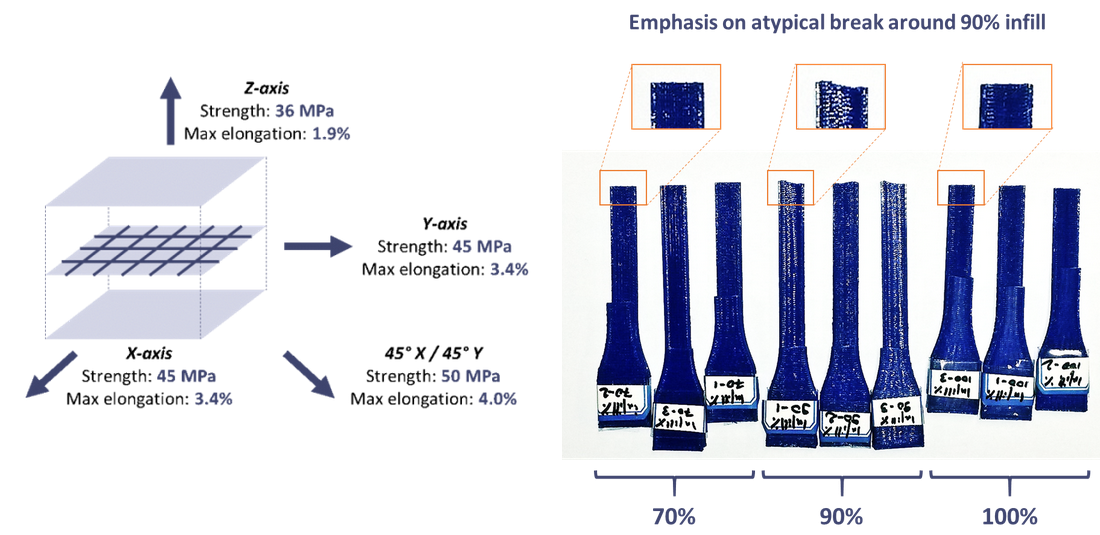
top sellers
-
Bearing 604UU U604ZZ
U-bearing U604ZZ 604UU 4*13*4
35.00 UAH
nine0012 -
Thermal mat for 3D printing 200 x 200 mm
3D printing thermal pad
150.00 UAH
-
Buy epo3d+ 3D printer nine0003
Epo3d+ Ukrainian FDM 3D printer on HIWIN rails. Thanks to reliable...
UAH 35,000.00
-
ABS granules
ABS granules for extrusion
400.
00 UAH nine0009
-
PLA
PLA environmental plastic from Plexiwire. 100% advance payment....
UAH 375.00
-
Buy ABS plastic (ABS) nine0003
ABS plastic from Plexiwire. 100% prepayment. Free shipping...
UAH 220.00
-
Mini motor reducer 12v 100 rpm
high torque mini electric motor. Its size...
150.00 UAH
-
Nozzle for 3D printer 1.
75 mm, for E3D and MK8 hotends
3D printer nozzle 1.75 mm 0.2/0.3/0.4/0.5
35.00 UAH
nine0012 -
PETG plastic for 3D printer
PETG plastic from Plexiwire. 100% prepayment. Free...
UAH 360.00
-
SHF-20 shaft support nine0003
SHF-20 shaft support is used for CNC
60.00 UAH
-
A4988 stepper motor driver
35.00 UAH
nine0005
Buy epo3d 3D printer
Ukrainian epo3d 3D printer built on the basis of modern kinematics. ..
UAH 18,000.00
All best sellers
Information nine0009
What is infill in 3D printing and how to properly set it up on a 3D printer.
In 3D printing, the internal filling is a very important factor for the strength, structure and weight of the finished model. In this article, we will look at the various forms and types of filling to find out why and for what they are needed.
Purpose of
In addition to sealing function, infill also changes weight and allows
3D printers to reliably print flat horizontal edges over empty space. Without it, 3D models would not have robust structure and stability, and would be incredibly fragile. nine0009
Infill is perhaps one of the most significant factors in 3D printing. It comes in a variety of shapes and patterns, densities and styles. Its optimization can be a difficult task. However, with certain knowledge and settings, it will significantly improve the result.
Styles
Each 3D infill pattern has strengths and weaknesses, and each is applicable in its own way. There are several fairly standard patterns.
Because 3D infill takes up space within an object, it should be chosen for quality improvement, not aesthetics. To do this, it is better to use patterns that include grids, lines, honeycombs, as well as rectilinear or concentric patterns. nine0009
If set correctly, they give enough volume for 3D printing between the gaps. This allows the 3D printer to print on voids more accurately and with fewer errors.
Density
Once you have decided on the look of your drawing, the next step is to set the saturation of your 3D print, which is measured as a percentage. 0% is a hollow model and 100% is a solid print. Of course, there are many levels in between, and adjusting this value is incredibly useful. nine0009
One very obvious use is to vary the mass of a 3D product. Higher density makes heavier and harder 3D printing. On the contrary, a lower one will provide a simple and easy result.
Standard 3D infill is 20% to 25%. This strikes a good balance between durability and consumable material. If the composition does not matter, then you can take settings from 10% to 15%.
None of these ranges provide very much support, so don't use them if your subject needs to be rigid. Finally, if design is the main consideration and material consumption is not that important, the best range is 30% to 50%. nine0009
Finally, if you want extra strength, feel free to set it to 100%.
Using the full range of settings and considering all the differences in 3D printers, you need to carefully consider the density to meet your needs.
3D fill examples
"octi" and "archi" in the image are more suitable for circular or rounded objects, while "Hilbert" and "3D honey" are better used for blocky 3D models. nine0009
What is a fill pattern in 3D printing?
3DPrintStory    3D printing process    What is a fill pattern in 3D printing?
Quite often, 3D printing is used to produce parts that can be easily produced using another manufacturing technology. However, while the end results may look the same on the outside, what's on the inside can be drastically different. nine0009
The main advantage (and necessity) of 3D printing is that parts can have different degrees of filling with material. From a production standpoint, this reduces the amount of material needed and the cost as well as the weight of the final product. And in terms of 3D printing, it saves precious time!
What's inside the outer shell of a 3D printed model is called infill. It can be adjusted by the ratio of density (0% - emptiness, 100% - solid) and pattern. nine0009
Next, we'll take a look at the various fill patterns, in particular those available in Cura.
What filling options are available?
In the latest version of Cura (4.5), 13 infill types are available. They are grouped below according to what they are best suited for:
- Models and figures (low strength): Lines, zig-zag ;
- "Standard" 3D models (medium strength): Grid , triangles , tri-hexagon ;
- Functional 3D models (high strength): Cubic , cubic subdivision , octet , quarter cubic , gyroid ;
- Flexible 3D models: Concentric , cross , cross 3D .
Models and figurines
Recommended infill density: 0-15%
3D models that are used as models or figurines usually do not require special strength, as they are not subjected to heavy operating conditions and are not subjected to heavy loads . nine0009
For these 3D printing options, lines or zig-zag fills are best because they provide the fastest 3D printing.
Similar to "rectilinear" in other slicers, both templates create a 2D grid where 3D prints only along one axis on one layer. The difference between the two is that lines create multiple lines per layer, while a zigzag is just one continuous line (unless interrupted by a model).
Models or figurines work well with simple filling patterns. Prototypes of your future parts are also good candidates, given that they do not need to be tested for durability. nine0009
"Standard" 3D models
Recommended infill density: 15-50%
For 3D models subjected to low stress, such as the media guide above, use a medium strength infill pattern. The most appropriate fill options are grid, triangles, or tri-hexagon. However, please note that these patterns can increase print times by up to 25% compared to lines.
- grid: A clear 2D template. The main advantage is the speed of 3D printing, as it is the least complex of the three; nine0012
- triangles: A 2D mesh made up of triangles. This pattern infill option has an inherent strength advantage when a load is applied perpendicular to the object's surface. It makes sense to use for parts with thin rectangular components that might otherwise have very few connections between the walls;
- tri-hexagon: This 2D fill option creates hexagons interspersed with triangles. One of the advantages is that hexagons are a very rigid geometric figure, which ensures high strength of the finished product. In addition to this, the tri-hexagon filling gives shorter lines to connect each side, resulting in fewer bending issues due to poor cooling during 3D printing. nine0012
Functional 3D prints
Recommended infill density: > 50%
Functional 3D prints such as a shelf bracket require high strength in many directions. Excellent candidates for fill patterns include: cubic, cubic subdivision, octet, quarter cubic, gyroid.
- cubic: this is a three-dimensional pattern of stacked and tilted cubes;
- cubic subdivision: this is a variant of the cubic type that uses less material; nine0012
- octet: This pattern variant, also known as tetrahedral infill, combines pyramid shapes;
- quarter cubic: this three-dimensional pattern is similar to the octet, but half of the pyramidal shapes are offset from the other half;
- gyroid: A unique 3D pattern that gives the impression of waves. However, it handles loads equally well in many directions. Thus, this infill pattern will be a good choice for a part that will be subjected to various loads. nine0012
The above 3D model infill options are often used even at lower infill densities due to their aesthetic appeal. Some people just like the effect of the internal pattern, which can be observed directly during 3D printing.
Flexible 3D models
Recommended infill density: 0-100% (depending on how “soft” you want the final product to be).
For flexible materials such as soft PLA MatterHacker, flexible infill patterns must be used to maintain the flexible nature of the print. Fill patterns such as concentric, cross, cross 3D are best for these types of 3D models. nine0009
- concentric: This 2D pattern creates "waves" within the print, mimicking the shapes of exterior walls. This is very similar to how a stone thrown into water leaves concentric circular waves on the surface;
- cross: Another 2D pattern that creates a grid of very fancy crosses. The gaps between the crosses and gratings allow bending and twisting;
- cross 3D: This 3D pattern is similar to a cross, but as the 3D model grows, the lines move at an angle. The end result is an object with a bit more rigidity. nine0012
Helpful Hints
The choice of infill pattern for a 3D model is important, but that's not all. Here are a few things to keep in mind the next time you're configuring Cura's 3D print settings.
Fill Line Direction
One of the often overlooked fill settings is the fill line direction. The default is 45° so that both X and Y motors work together to print infill at maximum speed. However, it may be more useful to orient the infill at a different angle to maximize the strength or flexibility of the part, especially if its walls are aligned diagonally. nine0009
Gradient Fill vs. Gradual Fill
When it comes to fill, we usually think of it as uniform throughout the inside of the part. However, this should not be the case.
Using gradient infill, you can set up 3D printing with a higher infill density around the perimeter. Generally speaking, this should maintain the effective strength and stiffness of the part while using less material. This option is not built into Cura, but it can be implemented relatively easily with a Python script. nine0009
Gradient fill should not be confused with gradual fill, which provides something similar, but along the Z axis rather than the X and Y axes.