Fuji 3d print system
Fujifilm Makes a Unique Entrance into 3D Printing
0Shares
Since HP announced its entrance into the 3D printing space, other print and imaging leaders have looked for their own way into the market, as well. Companies like Canon have begun selling 3D printers, hinting at making their own, while Epson has implied that it’s hoping to develop the ability to 3D print “anything”. Even Kodak has partnered with Carbon to invent new 3D printing materials. The latest is Fujifilm, which has taken what might be considered a unique approach to getting into the 3D printing business. No, they won’t be making a printer or even materials for 3D printing (at least not yet). Fujifilm is going to be offering technical support services.
Just as Fujifilm Service implements inventory management, automated retail, and refurbishment services for photo-imaging and printing systems, and has been since 1983, the Japanese multinational will take on 3D printing services through their North American branch. They will be extending their expertise from these 2D platforms into the third dimensions, providing just about any service that consumers and businesses might need when dealing with 3D printing technology. These services run the gamut from installing a new machine to maintaining it and even training employees in the use of 3D printers. The company states on their website:
Our technicians have significant experience in and knowledge of the mechanics and methods used to control diverse printing processes, including expertise in x, y, and z axis controlled devices, such as 3D printers. And, our in-depth understanding of the importance of printing in many organizations enables us to provide best practices coaching and training for printer operators across a wide range of industries.
Consistently excellent service translates into the best performance and value from your 3D printing systems. Our reputation for service excellence is exemplary. But our customers put it best: “Because of the job you do, we are able to do our job better.
”
The goal with their service is to help customers get the most they can out of their 3D printers. And they plan to do so through their already extensive network of locations in North America. As an established corporation, Fujifilm Service already has two strategically placed parts distribution centers, three depot repair facilities across the US, four help desks, and 500 field service technicians. With these resources, the company has a pretty long list of what they can offer potential clients:
- Initial setup and testing
- Operator training and education
- Telephone technical support
- On-site repair service
- Product exchange/swap service
- Depot repair service
- Routine calibration and quality checks
- Regularly scheduled preventive maintenance
- Replacement parts
And, according to Fujifilm, these services can be applied to a number of different aspects associated with the technology, including CAD and 3D modeling software, computer maintenance, electro-mechanical systems, electronics repair, and more. And they say that they’ll tackle every type of printer out there, including inexpensive 3D printers used in the classroom or home up to the advanced additive manufacturing systems associated with industry.
Given the complexity of most 3D printing systems, as well as the relative unfamiliarity that the general populace has with the technology, this could be a necessary and lucrative business for the imaging giant to initiate. If Apple needs a Genius Bar for its user-friendly products, it’s easy to imagine the genius necessary to install, repair, and train employees around industrial manufacturing equipment. At the same time, Fujifilm won’t find themselves competing with other imaging corporations entering the space. In fact, you might even find yourself calling Fujifilm Services to fix your MultiJet Fusion 3D printer from HP.
Michael Molitch-Hou
Michael Molitch-Hou previously served as Editor-in-Chief of 3D Printing Industry, he is now the Editor of Engineering . com's 3D printing section. He has covered additive manufacturing technology day in and day out since 2012 and has hundreds of article to his credit. He is the founder of The Reality Institute.
3D Printers | FUJIFILM Business Innovation
- Home
- Products
- 3D Printers
Types
Rapid Prototyping Solutions
Small Business Solutions
Large Team Solutions
Production Solutions
Academia Solutions
All Types
Application
Rapid Prototyping
Manufacturing Tools
Production Parts
All Applications
Materials
FDM ThermoPlastics
Polyjet PhotoPolymers
All Materials
Industries
Aerospace and Defence
Architecture
Automotive
Commercial Products
Consumer Products
Digital Dentistry
Education
Entertainment
Medical
All Industries
Comprehensive range of professional 3D Printers utilising FDM and PolyJet additive technology to meet the most demand applications, including primary, secondary and higher education, rapid prototyping, medical modelling and manufacturing. From capable, affordable and user friendly 3D printers to high capacity machines for high end part production and full colour, multi material options for unrivalled and realistic aesthetic performance.
LatestBLI awardBest Seller
Your search criteria has returned 0 results.
Sorry, your search criteria has returned 0 result. Please try again.
Load more
{{? result.buttonlink}}
{{? result.buttontype === 'modalbox'}} {{=result.buttonlabel}} {{??}} {{=result.buttonlabel}} {{?}}
{{?}}
{{? result. recommended}}
Recommended
{{??}}
{{? result.promoted}}
BLI award
{{??}}
{{? result.newitem}}
New
{{??}}
{{? result.bestseller}}
Best Seller
{{?}}
{{?}}
{{?}}
{{?}}
{{~}}
Automation in FDM.

The 24/7 production of parts using FDM technology is hampered by the high labor intensity of each action taken, as well as the need for an operator to be near the printer.
If we compare the most common modern FDM 3D printers on the Russian market with ordinary office printers, then in terms of automation level they are closer to a manual printing press than to an MFP.
The FDM 3D printer will be idle if the operator has not removed an already finished part from the worktable or if he has run out of material. In the event of a technical malfunction, the operator spends more time finding the malfunction itself than fixing it.
If the production is small (up to 10 printers, up to 1000 parts per month), then these problems are not noticeable. Typically, such a pilot plant is run by a single specialist who has a thorough knowledge of the printers entrusted to him, but even an experienced print specialist cannot work 24/7 and produce a large product range with high quality if it changes frequently (for example, in 3D printing service farms).
If an enterprise needs to increase the productivity of its 3D printing department, then this is usually followed by an increase in the staff of operators, an increase in the number of printers, an increase in technical costs (manufacturing defects, technical and technological downtime). When deadlines are pressed, there is a need to work first in two shifts, and then in three.
Over the past three years of running serial orders at our St. Petersburg 3D printing services farm, we have identified the most costly operations in terms of productivity and labor intensity:
requires the presence of an operator.
2. Preparation of the working area, calibration - in case of operator error, it leads to marriage, time is lost for reprinting.
3. Media Inspection - When finished during the printing process, the printer is either idle or the product is rejected.
4. The printer is idle until the operator removes the product from the worktable.
5. The printer is idle while the operator is looking for a problem or waiting for a response from technical support. The problem applies to printers whose manufacturer does not provide detailed technical documentation. A large fleet of printers requires a dedicated service engineer.
6. The increase in the number of orders for production requires the appearance of a technician to solve routine auxiliary tasks (for example, replacement and control of the availability of material), otherwise the workload on operators increases, rejects become more frequent, equipment is idle.
7. Delegation between operator shifts often results in overproduction of parts or loss of order information. To combat this, investments in accounting systems or the hiring of additional administrative staff are required.
It follows from this:
2. An increase in the number of orders is a non-linear increase in the labor intensity of production.
3. Staff expansion - growth of non-production costs.
4. Increasing the labor intensity of production - increasing the terms of product readiness.
5. Lack of automated accounting tools - increased costs for marriage and re-sorting.
6. Shift schedule - increased staff and increased costs for marriage and regrading.
7. Round-the-clock work - increase in staff, decrease in the level of responsibility for quality.
Thus, FDM 3D printing is scaling at a significant cost and is accompanied by an increase in staff, an increase in payroll costs, and a non-linear increase in production and administrative costs. Added to this are the difficulties with organizing in-line printing, the lack of analytics and statistical data on production, material consumption, and data on equipment loading.
The reason is the lack of technical and software automation of routine actions in FDM printing.
To solve the above scaling problems, in the spring of 2020, we began the development of an automated FDM 3D printing complex.
The following development goals were identified:
1. Automate the routine removal of finished products and material replacement, eliminating the need for the constant presence of the operator near the printers.
2. Have complete information about the technical condition of the printer without visual control and operator presence.
3. Ensure the scalability of production without increasing non-production costs.
4. Reduce the labor intensity of production planning, control and accounting of printed products.
5. Reduce the risk of technical failures and downtime for service and recovery.
6. Ensure compatibility with the most common thermoplastics and composites and reduce changeover downtime, reduce downtime between operations.
7. Collect and analyze data on the printing process and equipment status, display analytics not only for production, but also for administrative staff, including material consumption and manufacturing defects.
8. Predict project deadlines as accurately as possible by using real time to print the first samples in a batch.
9. Implement a management system with two-way exchange with third-party CRM (Bitrix24) and accounting systems (1C: UNF) for end-to-end analytics of the effectiveness of investments in the additive unit.
In this article, we present a comprehensive solution to the task of automating FDM 3D printing - the Redfab additive manufacturing hardware and software system.
Redfab 3D printer solves existing problems in the following way:
1. Automatic Selective Feeding and Media Change
The system allows you to selectively feed, remove, cut and rewind media autonomously or at the operator's command. Up to 5 D300 2.25 kg spools or up to 8 D200 1 kg spools are simultaneously connected to each print zone. Main extruder and sub extruder each have 4 slots for 1.75+/-0.15mm bar. Having loaded the coil compartment once, the engineer may not return to the issue of refilling the material for a long time, up to 8 days of continuous printing at a flow rate of ~50 cm3/hour, or 4 days at a flow rate of ~100 cm3/hour. At the end of plastic on the coil, the system automatically switches to the next one. This uses the media specified in the print job.
2. Automatic ejection of finished products
The part is printed on a film pressed against the work table by vacuum. After printing is completed, the film is pulled through the cooling system, the part is separated and dumped into a container. After the finished batch is reset, the printer autonomously starts the next print. Since the parts are ejected from the hot table, reheating is not required.
3. Automatic table plane calibration
Calibration of the print plane by 4 points and the table by 20 points with correction factors entered into the control system (MESH). The milled table has no internal stresses, as it undergoes a heat treatment procedure.
The table is thermally decoupled from the power frame of the printer, due to which it does not warp when heated up to 140°C.
Calibration is performed automatically without the participation of a specialist.
4. Automatic print queue
The user sets the printing parameters, the control system automatically forms a queue of projects and production jobs according to the user-defined parameters. The availability and availability of material, nozzle parameters, production priorities are taken into account.
5. Automatic service operations
The control system detects failures and accidents based on the readings of the sensors, and then attempts to independently maintain and restore the printing process in cases where it is possible. A well-thought-out control system prevents false failures and gives the user flexibility in making decisions. The printing process will not be stopped if a failure occurs in the auxiliary system. Thus, the complex will try to complete the current print, after notifying the user.
6. Easy Maintenance
Modular design, quick-detachable extruders and easy access to all equipment components allow periodic maintenance to be carried out quickly. You can write a request to technical support directly from the control system. When requested and authorized by the user, our technical support service can remotely connect to the control system and both carry out a complete diagnosis of the system settings and track the printing process itself thanks to the built-in video camera. Since we produce most of the components ourselves, we are ready to promptly provide the customer with spare parts.
The Redfab 3D printer is equipped with the advanced control system, which allows real-time analysis of production processes, which is indispensable for assessing the current work and making decisions on the development of FDM printing. 1. Statistics, accounting and analysis carrying out maintenance with the output of reports and comparison of periods.
2. Production time control
The system allows you to visualize the production time on the Gantt chart and calculates the order readiness for delivery based on the actual time of printing the first copy of the print job. This allows you to predict the completion time of the entire project with high accuracy.
3. Remote monitoring of the printing process
The user gets access to the video stream from the camera located in the working area. At the beginning and at the end of printing, a control picture is taken, which allows you to track the readiness of the product and the absence of defects. In the future, we plan to automate this aspect of work, using vision algorithms.
4. Access control and accounting
Authentication system, setting group rights, setting roles (trainee, technician, operator, administrator, technical support), logging user actions in the control system. This functionality allows you to ensure that the system is closed to third parties and restrict access to production and accounting data in accordance with the client's privacy policy.
Parameter name | Value |
---|---|
Print area (X/Y/Z), mm | 250*430*250 |
Number of printing areas in 1 complex, pcs. | 3 |
Number of extruders per print area, pcs. | 2, direct, quick release |
Maximum extrusion temperature, °С | 450 |
Maximum air temperature in the active heat chamber with forced circulation, °C | 80 |
Maximum heating temperature of the working table, °С | 140 |
Parts Cooling Systems | Material cooling at nozzle exit. Cooling of the layer over the entire print area. |
Performance at maximum practical printing speed, cm 3 / hour | up to 150 (for ABS Standard Filamentarno) |
Supported file format | gcode, slicer of user choice |
Data interfaces | LAN Ethernet, USB, Wi-Fi |
Our equipment is running 24/7 on our own 3D printing farm, so we can confidently provide you with a 2 year warranty on your Redfab 3D printer.
To calculate the profitability of purchasing our printer, we suggest using the calculator on our website www.redfab.ru.
The calculator allows you to estimate the rate of return on investment.
For large-scale productions (from 20 units of 3D printers), we recommend considering a one-time purchase of 4 units of Redfab printers at once for leasing at a special price.
![]()
We will be glad to meet you in our showroom in St. Petersburg. You will have the opportunity to check the operation of all systems of the Redfab 3D printer, as well as test the functionality of the latest control system.
If you are unable to visit the showroom in person, we provide remote access to the control system. You can work with its functionality, start printing remotely and monitor the printer via video stream from a camera located in the work area. ■
Find out more on our website
www.redfab.ru.
+7 (812) 425-62-32
9000 9000 9000 9000 9000 9000 9000 9000 9000 9000 9000 Alexander Mikhailenko, CEO of Redfab
Source magazine "Additive Technologies" No. 1-2022
Automation in FDM, 3D printer Redfab, Redfab, FDM 3D printer, FDM 3D-printing, FDM technology, Additative Technologies Magazine No. 1-2022
Comparison of 3D printing technologies: FDM, SLA and SLS
Additive manufacturing or 3D printing reduces costs, saves time and expands the technological possibilities in product development. 3D printing technologies offer versatile solutions for applications ranging from rapid concept and functional prototypes in the field of prototyping to fixtures and clamps or even final parts in manufacturing.
Over the past few years, high resolution 3D printers have become more affordable, more reliable and easier to use. As a result, more companies have been able to use 3D printing technology, but choosing between different competing 3D printing solutions can be difficult.
Which technology is right for your needs? What materials are available for her? What equipment and training is needed to get started? What are the costs and payback?
In this article, we take a closer look at three of today's most well-known plastic 3D printing technologies: Fused Deposition Modeling (FDM), Stereolithography (SLA), and Selective Laser Sintering (SLS).
Choosing between FDM and SLA 3D printer? Check out our detailed comparison of FDM and SLA technologies.
Download this high resolution infographic here.
VIDEO MANUAL
Can't find the 3D printing technology that best suits your needs? In this video tutorial, we compare Fused Deposition Modeling (FDM), Stereolithography (SLA), and Selective Laser Sintering (SLS) technologies in terms of the top factors to consider when purchasing.
Watch Video
Fused Deposition Modeling (FDM), also known as Fused Filament Manufacturing (FFF), is the most widely used form of 3D printing at the consumer level, fueled by the rise of consumer 3D printers. On FDM printers, models are made by melting and extruding a thermoplastic filament, which the printer's nozzle applies layer by layer to the model being built.
The FDM method uses a range of standard plastics such as ABS, PLA and their various blends. It is well suited for making basic experimental models, as well as for quickly and inexpensively prototyping simple parts, such as parts that are usually machined.
FDM models often show layer lines and may have inaccuracies around complex features. This sample was printed on a Stratasys uPrint FDM industrial 3D printer with soluble support structures (price starting at $15,900).
FDM printers have the lowest resolution and accuracy of SLA or SLS and are not the best option for printing complex designs or parts with complex features. Surface quality can be improved by chemical and mechanical polishing processes. To address these issues, industrial FDM 3D printers use soluble support structures and offer a wider range of engineering thermoplastics, but they are also expensive.
FDM printers do not handle complex designs or parts with complex features well (left) compared to SLA printers (right).
Invented in the 1980s, stereolithography is the world's first 3D printing technology and is still one of the most popular technologies among professionals today. SLA printers use a process called photopolymerization, which is the conversion of liquid polymers into hardened plastic using a laser.
See stereolithography in action.
Models printed on SLA printers have the highest resolution and accuracy, the sharpest detail and the smoothest surface of all plastic 3D printing technologies, but the main advantage of the SLA method is its versatility. Materials manufacturers have developed innovative formulas for SLA polymers with a wide range of optical, mechanical and thermal properties that match those of standard, engineering and industrial thermoplastics.
Models created using SLA technology have sharp edges, a smooth surface and almost invisible layer lines. This sample was printed on a Formlabs Form 3 Desktop Stereolithographic 3D Printer (price starting at $3499).
SLA is an excellent option for making highly detailed prototypes that require tight tolerances and smooth surfaces such as molds, templates and functional parts. SLA technology is widely used in industries ranging from engineering and design to manufacturing, dentistry, jewelry, modeling, and education.
White Paper
Download our in-depth white paper to learn how SLA printing works, why thousands of professionals use it today, and how this 3D printing technology can be useful in your work.
Download white paper
free sample
Experience Formlabs print quality first hand. We will send a free 3D printing sample directly to your office.
Request a free sample
Selective laser sintering is the most common additive manufacturing technology used in industry.
Selective Laser Sintering (SLS) 3D printers use a high power laser to sinter fine polymer powder particles. The unsprayed powder supports the model during printing and eliminates the need for special support structures. This makes SLS ideal for complex geometries, including internal features, grooves, thin walls, and negative taper. Models produced using SLS printing have excellent mechanical characteristics: their strength can be compared with the strength of injection molded parts.
Models created with SLS technology have a slightly rough surface, but almost no visible layer lines. This sample was printed on the Formlabs Fuse 1 SLS workshop 3D printer (price starting at $18,500).
The most common selective laser sintering material is nylon, a popular engineering thermoplastic with excellent mechanical properties. Nylon is light, strong and flexible, resistant to impact, heat, chemicals, UV radiation, water and dirt.
The combination of low part cost, high productivity, and widely used materials makes SLS a popular method for engineering functional prototyping and a cost-effective alternative to injection molding in cases where production runs are limited.
White Paper
Looking for a 3D printer to create durable, functional models? Download our white paper to learn how selective laser sintering (SLS) technology works and why it is popular in 3D printing for functional prototypes and end-use products.
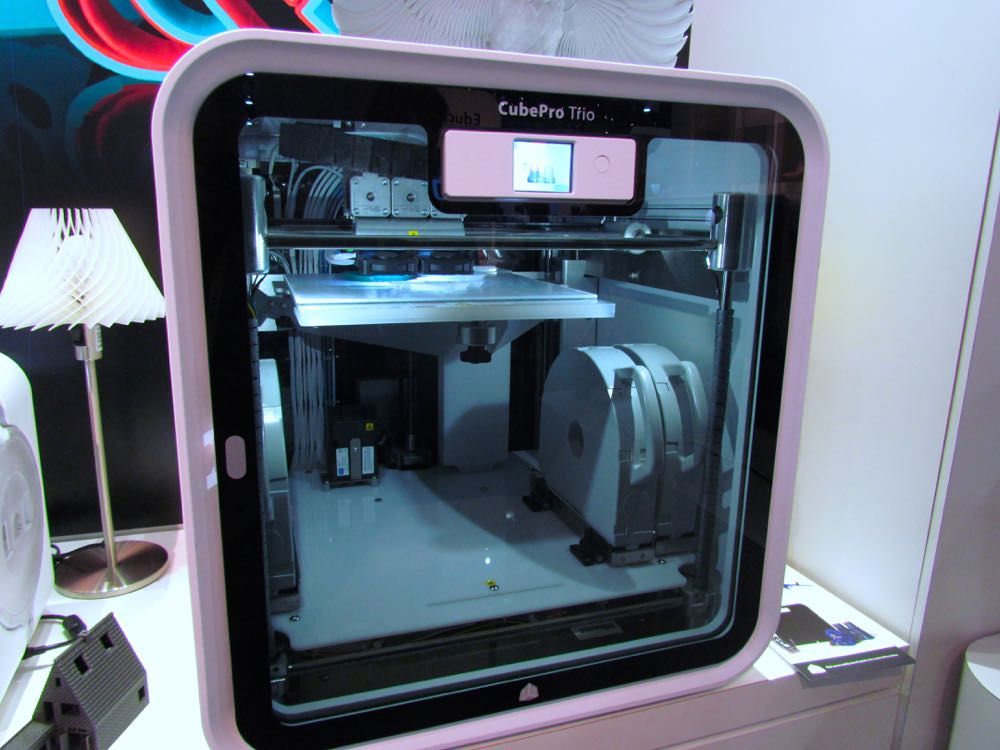

Either way, you should choose the technology that best suits your business. Prices have dropped significantly in recent years, and today all three technologies are offered in compact and affordable systems.
3D printing costing doesn't end with initial equipment costs. Material and labor costs have a significant impact on the cost of each part, depending on the application and production needs.
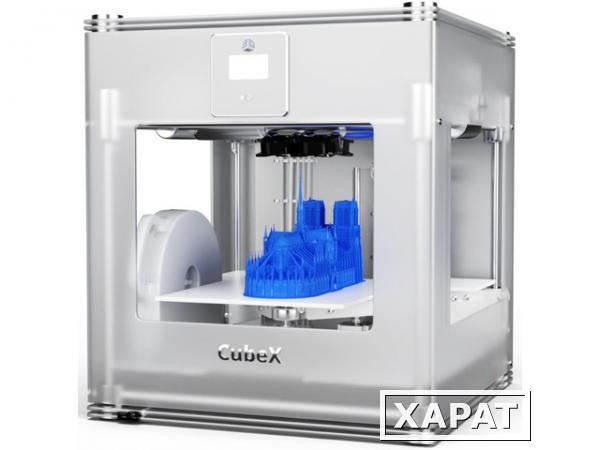
INTERACTIVE MATERIAL
Try our interactive ROI tool to see how much time and money you can save by printing with Formlabs 3D printers.
Calculate savings
FDM, SLA and SLS printed prototype ski goggle frames (left to right).
We hope this article has helped you narrow down your search for the 3D printing technology best suited to your needs.