Air force 3d printing
US Air Force 3D prints spare parts to solve maintenance issues
0Shares
The US Air Force (USAF) has invested in a 3D printer capable of producing spare parts for its Strategic Automated Command Control System (SACCS).
When a supplier stopped manufacturing a red fault indicator lens cap to cover the lights on the SACCS system, the USAF purchased a 3D printer to manufacture its own replacement. By leveraging the technology to produce the first cap, the USAF recovered the cost of the printer and scanner and saved more than $4,000.
“This strategy is saving the Department of Defense thousands of dollars each time the part fails,” said Col. Brian Golden, National Airborne Operations Center and 595th Command and Control Group Commander.
A network technician for the 595th SCS constructs a cover for an alert light with a 3D printer at Offut Air Base. Photo via USAF.The Air Force’s use of 3D printing
The USAF has leveraged additive manufacturing for some time across a variety of applications and projects. Back in 2020, engineers from the Air Force Sustainment Center became the first to test a 3D printed metal component inside a USAF aircraft engine.
Since then, the USAF has filed a patent application for a novel 3D printed nose simulator, has enlisted circuit board fabrication specialist BotFactory to develop a fully-automated desktop electronics 3D printer as part of its ‘AFWERX’ program, and has awarded 3D printer manufacturer Optomec with a $500,000 contract to develop optimized 3D printing process parameters to repair its fighter jet engine turbine blades.
More recently, the USAF has awarded aerospace firm Boom Supersonic with a $60 million contract to accelerate the R&D of its upcoming ‘Overture’ supersonic flight-capable aircraft, and has funded the advancement of 3D printing specialist Senvol’s machine learning technology to drive forward the qualification of new aerospace 3D printing materials.
A network technician for the 595th SCS removes a cover for an alert light from a 3D printer slide at Offut Air Base.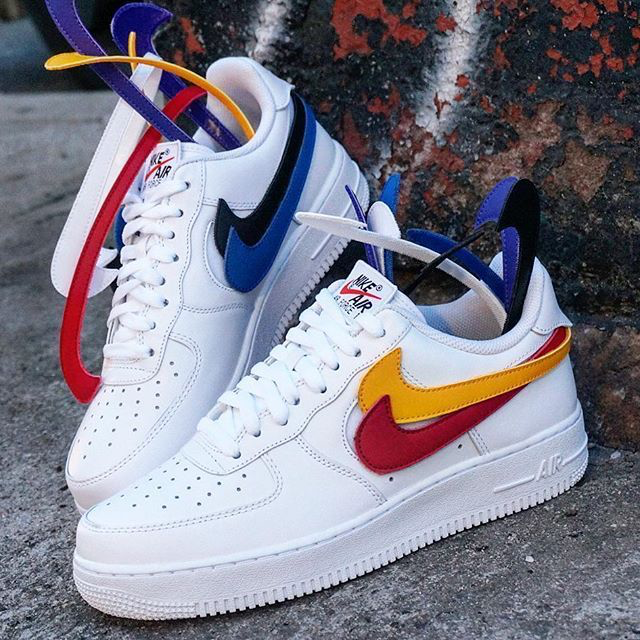
Solving maintenance issues with AM
For its latest 3D printing-focused project, the 595th Strategic Communications Squadron of the USAF, which operates the SACCS, has leveraged the technology to improve its maintenance of the system.
The SACCS provides rapid re-targeting of ICBMs, force distribution and emergency action messaging capabilities, and operates sole depot repair authority across 252 global sites. Operating 24/7, the SACCS processes more than 84 million US Strategic Command messages each year.
The machine itself is 70 years old, and as such some of its parts are becoming obsolete. When the supplier of the SACCS’ red fault indicator lens cap discontinued manufacturing the part, the squadron purchased a 3D printer that would enable it to reverse engineer and produce its own replacement.
Beginning with a trial and error approach, the team worked to configure the necessary design and dimensions of the lens cap via 3D scanning, before achieving the desired part. They then saved the process to allow the easy and quick fabrication of lens caps in the future.
Previously, the only way to repair the fault indicator on a SACCS system blower was to replace the entire component at a hefty cost of $7,187. However, after the first 3D printed cap was produced, the squadron not only recovered the outlay costs of the 3D printer and scanner, but also saved a total of $4,475.
Going forwards, the USAF expects the 3D printer to save “thousands of dollars” in repair and supply chain costs in the future.
“The 3D printer is just another example of how the dedicated and innovative airmen of the 595 SCS continue to find ways to sustain and operate legacy SACCS until the system can be modernized under the phased approach of the SACCS-Replacement program,” said Golden.
U.S. Airman 1st Class Saowalak Wester, a NC3 network technician for the 595th Strategic Communications Squadron, places a cover on an alert light created on a 3D printer at Offutt Air Force Base. Photo via USAF.“We are going to have to come to the realization soon that this type of replacement process is paramount to keep legacy NC3 systems in the game for years to come.
”
Now that the proposal has been approved by the Air Force Global Strike Command, the squadron is working to get a stock number assigned to for the lens cap and enter it into the supply system, eventually enabling other USAF units to request the lens caps directly from the 595th Centralized Repair Facility (CRF).
Going forward, the unit plans to deploy the 3D printer to model and produce similar legacy components that are no longer in the USAF’s supply system. The USAF will also expand the technology’s use to support the repair of other assets within the 595th Command and Control Group.
Subscribe to the 3D Printing Industry newsletter for the latest news in additive manufacturing. You can also stay connected by following us on Twitter and liking us on Facebook.
Looking for a career in additive manufacturing? Visit 3D Printing Jobs for a selection of roles in the industry.
Subscribe to our YouTube channel for the latest 3D printing video shorts, reviews, and webinar replays.
Featured image shows a network technician for the 595th SCS constructs a cover for an alert light with a 3D printer at Offut Air Base. Photo via USAF.
Tags 595th Strategic Communications Squadron AFWERX Air Force Global Strike Command Air Force Sustainment Center Boom Supersonic botfactory Col. Brian Golden optomec Senvol US Air Force USAF
Hayley Everett
Hayley is a Technology Journalist for 3DPI and has a background in B2B publications spanning manufacturing, tools and cycling. Writing news and features, she holds a keen interest in emerging technologies which are impacting the world we live in.
U.S. Air Force Looks to Fly with 3D Printed Parts
Adopting new manufacturing technologies has often proven to be a game changer for companies seeking to enter a new market or retain their leadership in an existing one. For GE, 3D printing is the latest tool for staying ahead of its competitors in the aircraft industry.
Though GE engineers had originally developed the engine for the B-1 supersonic bomber, by 1970 it was no longer seen as a leading supplier. That opinion changed in the 1980s when GE designed a new engine around the B-1 core to provide the U.S. Air Force with propulsion systems for its F-16 and F-15 fighter aircrafts. Decades later, that F110 jet engine still powers most frontline F-16 fighters.
To keep its fleet flying, the U.S. Air Force continually searches for the best ways to procure parts, including crucial spare parts for planes that have been in service for decades. That’s why the Air Force’s Rapid Sustainment Office (RSO) was receptive when representatives from GE Additive approached them last year with the idea of making some parts with 3D printing.
That collaboration is now bearing fruit. GE’s engineers are building a 3D-printed sump cover for the GE F110 engine. The sump is part of the oil lubrication system, and the sump cover is basically a cap, yet still a key part of the engine, says James Bonar, engineering manager at GE Additive. “Compared to other parts on the F110 engine, the sump cover might have lower functionality, but it is incredibly important. It needs to be durable, form a seal, and it needs to work for the entire engine to function. That’s critical, of course, on a single-engine aircraft like the F-16.” F110 engine. Source: GE Aviation
Intricate shapes
GE was able to make its case for 3D printing based on its broad expertise with 3D printing technology. Also known as additive manufacturing, the process works by fusing thin layers of metal powder with a laser or electron beam to make a final product. The technology allows engineers to create shapes that would otherwise be too expensive, or too intricate, to make by casting or stamping.
According to Antroine Townes, site leader for GE Aviation’s Additive Technology Center (ATC), “The beauty and the value of additive manufacturing comes in the flexibility of design and the speed of innovation. ” And it has been a particular boon for GE’s work in aviation.
Engineers at the ATC, for instance, were able to use the technology to combine more than 300 engine parts into just seven 3D-printed components in the new GE9X engine, which GE claims is the most powerful jet engine in the world. Thanks to 3D printing and other technologies, this engine is 10% more fuel-efficient than its predecessor, the GE90.
GE Aviation also relied on 3D printing for its Catalyst, the first “clean-sheet” design of a turboprop engine to make it to the aviation market in more than a half-century, according to GE Aviation. With 3D printing, GE’s engineers distilled about 800 parts down to a dozen or so, while reducing the Catalyst’s weight and improving its fuel consumption.
3D-printed sump cover
GE’s collaboration with the Air Force RSO builds on this experience. “The Air Force wanted to go fast from day one and gain the capability and capacity for metal additive manufacturing as rapidly as possible in order to improve readiness and sustainability,” says Lisa Coroa-Bockley, general manager for advanced materials solutions at GE Aviation. “Speed is additive’s currency.” Additively manufactured cobalt-chrome sump cover for F110 jet engine.
Source: GE Additive
The first print run of the sump covers, which are conventionally cast from aluminum, happened at the ATC, where engineers created the parts from cobalt-chrome powder using GE Additive’s Concept Laser M2 machine.
“Part of that process involved exploring how to quickly eliminate the associated risks with castings, and how metal additive might replace it for those parts that are either no longer in production or where we need smaller production runs to keep our platforms flying,” explains Melanie Jonason, chief engineer for the propulsion sustainment division at Tinker Air Force Base in Oklahoma.
For this collaboration, the Air Force and GE are using a spiral development model common to fields like software. This process begins with lower functionality individual parts, like the sump cover, and then advances to tackle complex components and systems such as heat exchangers. With Phase 1a of the sump cover project underway, the teams are moving on to Phase 1b, which focuses on a sump cover housing—a family of parts on the TF34 engine. This engine powers the Air Force’s Fairchild Republic A-10 Warthog, which has been in service for more than 40 years.
“The program with GE is ahead of schedule and the preliminary work already done on the sump cover has allowed us to move forward quickly,” says Beth Dittmer, division chief of propulsion integration at Tinker Air Force Base. “As we build our metal additive airworthiness plan for the Air Force, the completion of each phase represents a significant milestone as we take a step closer to getting an additive part qualified to fly in one of our aircrafts.”
3D printing in the Israeli Air Force (2): oleggranovsky — LiveJournal
3D printing in the Israeli Air Force (2): oleggranovsky — LiveJournal ?- Aviation
- Technologies
- Army
- CANCEL
2.5 years ago (May 2017) I already wrote about the use of three -dimensional printing technology (3D printing) in the Air Force, at the Air Forces, at the Air Forces, at the Air Force Repair. Air Force plant ("Yekhidat Akhzak Avirit 22", hereinafter YAA-22). Then products were printed only from high-strength polymers, printing from metal (aluminum, titanium and even steel) was in the future. But even then the following was reported: YAA-22, together with specialists from civilian factories and universities (the Technion has a 3D printer for printing from metal), is planning the production of the first metal part on the printer - a beam (“Bark”) for the Yanshuf helicopter (UH- 60 Black Hawk). This beam has a complex geometry and could not be produced using old technologies: the beam requires a certain bend and when trying to bend the workpiece, it breaks. The manufacturer of the original part in the USA refused to supply it in a single quantity. After the beam is manufactured, it will undergo comprehensive tests (strength, resistance to loads under flight conditions, material fatigue tests, etc.) and only after that it will be installed on a helicopter.
I don’t know if we are talking about the same beam, but according to the Air Force website dated 10/02/19, the plan was implemented: shortly before publication, the Yanshuf was first flown with a metal part made using the 3D printing method . And we are not talking about the first flight in general, but about the first operational sortie ("Tisa Mivtsait"). Those. this was preceded by test and training flights with this part.
The Department of Materials ("Thum Homarim"), headed by Lt. Col. Dr. Ofer Levy, and the Department of Materials and Process Engineering ("Gaf handasat Homarim ve Taalihim"), headed by Major Dmitry Fishman, are responsible for the work of YAA-22. The part is called “Fireproof Wall Corner” (“Zavitan Kir Esh”), it is located in the area between the engine and the helicopter body. This wall protects the body of the helicopter from heating, and the corner holds this wall. According to Dmitry, attempts to make the corner using conventional methods were unsuccessful: the material of the corner is titanium, and when trying to bend a thin sheet of titanium at the required angle, it cracked.
The printing of the part was preceded by a deep study of the technology by YAA-22 engineers. It is worth noting that there are differences in the final product obtained using different metal powders and printers from different manufacturers. Moreover, if you take two printers of the same model from the same manufacturer and print from the same type of powder, the final product will be slightly different. Therefore, each printed sample goes through a long series of checks and tests, especially when it is planned to be installed on manned aircraft.
According to Captain Oren Shai, Materials and Process Engineering Officer at YAA-22, the angle was made in two batches. The first did not pass a series of tests and was not approved for installation on a helicopter. After extracting the findings and making changes to the process, the second batch was made and it was tested and approved for flights.
In addition, it was decided that the first 3D printed metal part for an aircraft would not be a safety related part. Those. when it is destroyed, the aircraft will not crash. And this despite all the tests on the ground and the full confidence of the engineers in the success of their work.
The manufactured corner was a relatively simple piece. There are a number of other details in the plans, more complex and more central to the design of the aircraft. YAA-22 continues to develop this area, which is new not only for it, but also for the world's leading aircraft building corporations. A bank of parts desirable for 3D printing has already been created, and careful progress is being made in its embodiment in metal. You need to gain experience. Both manufacturers and operators need to develop confidence in the technology and its results.
Links:
- LA with a part, made by the Trinomatic Press Trinomatic Press, ATC website, 02.19.
- For the first time: a 3D printed part is lifted into the air in operational flight, mako, 02.10.19.
- First time: 3D printed part is lifted into the air by helicopter, israeldefense, 10/10/19.
Tags: Air Force - maintenance
Subscribe
-
Air Force special overalls
06-07.03.23 Israel celebrates Purim. One of the traditions of this holiday is the carnival, the so-called. Purimshpil (in Yiddish - ...
-
Video: 10 samples of Israeli BTT
Caught on the channel "In Search of Facts" on youtube video "ISRAELIAN NEW MOST POWERFUL TANK Surprised the Whole World!".
In fact, ...
-
An attempt to smuggle drugs from Egypt was foiled, 05.03.23
On the night of 04/05.03.23, IDF observers spotted several suspects who were trying to smuggle drugs from Egypt in the territorial…
Photo 9005 /pics.livejournal.com/igrick/pic/000r1edq
- 3 comments
Printing organs: how ears, skin and noses are made with a 3D printer
- Natalka Pisnya
- BBC Russian Service, USA
it will help you sort things out.
image copyrightMasela family archive
Image caption, Luc Masela with his parents one month after his artificial bladder transplant. year 2001.
Luc Masela, now 27, is an athlete with a degree in economics, works for a large exhibition company, travels a lot and recently met, in his words, "the most beautiful girl in the world." Both she and most of his current friends were extremely surprised when they learned that 17 years ago he survived a dozen and a half operations.
Luke was born with spina bifida - and although he was able to walk, his bladder was severely damaged. By the age of 10, he almost did not leave hospitals: due to improper functioning of the bladder, fluid began to return to the boy's kidneys, doctors diagnosed an irreversible pathology of the organ.
You need to enable JavaScript or use a different browser to view this content
Video caption, 3D printed organs are here intestinal segment. This would guarantee Luke several years of medically supervised life and a high risk of developing cancer.
The urologist who was taking care of the boy invited the Masela family to take part in an experimental program: to grow a new bladder from his own cells. Then, in 2001, it sounded like science fiction: only nine people took part in the program before Luke. Despite this, his family agreed.
"The essence of the operation was reduced to two stages: first, a piece of bladder tissue was taken from me, and over the next two months, cells were grown in the laboratory in order to grow a new healthy bladder from them," says Luke.
Image copyright, Masela family archive
Photo caption,Luc Masela, 17 years after the artificial bladder transplant
Then came the transplant, which he said took 16 hours. “I opened my eyes and saw a cut through my entire stomach, tubes of all possible sizes were sticking out of me, except for them - four IVs and a bottle-feeding machine,” he recalls. “I stayed in the hospital for another month, I was prescribed bed rest, after that I stayed at home for another month.
The operation was performed by Dr. Anthony Atala, Pediatric Regenerative Surgeon. In two months, out of a hundred patient cells, scientists created one and a half billion. Further, an engineering structure was created on a collagen frame: the bladder was “sculpted” like a two-layer pie, the core of which dissolved over time, and it started working like an ordinary organ, taking root thanks to Luke’s own cells.
- An animal capable of regrowing its head
- The birth of a chimera: why do scientists need a human-animal hybrid?
- Swedish company 3D prints body parts
Luke and Dr. Atala haven't seen each other for 10 years after being discharged from the hospital. Once a dying child became the champion of the school wrestling team and went to college.
The professor took charge of the Wake Forest Institute of Regenerative Medicine in North Carolina in those 10 years, but he never forgot about Luke: his bladder was one of the most challenging and most successful projects in his early practice.
By 2018, Atala won the Christopher Columbus Award for "work on a discovery that will have a significant impact on society"; The Times and Scientific American magazines at various times named him "Physician of the Year", he was also recognized as "one of the 50 scientists on the planet who in the next 10 years will change the way we live and work."
How to print a new face
Skip the Podcast and continue reading.
Podcast
What was that?
We quickly, simply and clearly explain what happened, why it's important and what's next.
episodes
The End of the Story Podcast
In the mid-2000s, the Atala team turned their attention to an ordinary household 3D printer and wrote special software for it, later specialized machines were created for the laboratory. Now the laboratory "grows" up to 30 different types of cells and organs, as well as cartilage and bones.
One of the team's latest achievements is ears and noses grown outside the human body.
The main customer and sponsor of Atala's developments is the US Department of Defense, and many of the patients are military victims of military operations.
It works like this: first, a CT scan of the ear or nose is done. One of Atala's assistants, Joshua Corpus, jokes that at this stage, people often ask to "improve" the shape of the nose if they thought theirs was too wide or hooked, and the ears if they were too wide.
After that, a special computer code is written, and the printing of the basis of the organs begins.
For this, a bioresorbable polymer, polycaprolactam, is used. At the same time flexible and durable, in the human body it disintegrates within four years.
After printing, the layers of polycaprolactam resemble lace; after transplantation, their place will be taken by a person's own cartilage tissues in a few years.
Polycaprolactam is then saturated with a gel created from the patient's cells, cooled to -18 degrees Celsius - so the cells, according to scientists, are not damaged, they are "alive and happy."
Image caption,Printing a test kidney sample on a bioprinter
In order for the polymer and gel structure to take shape and become something more durable, ultraviolet light is used in the laboratory - it does not damage cells.
The future implant is printed for 4-5 hours, then it is finally formed and inserted under the epidermis.
Skin can also be grown: children affected by fires were the first to participate in the early trials of Atala - after the "printing" of the skin, scientists monitored patients for several more years. The new skin did not crack, did not burst, and grew with the children.
The most difficult job, according to the scientist, is facial wounds: it’s not enough just to stretch the skin, you need to accurately calculate the geometry, align swelling, bone structure, and understand how a person will look after that.
In addition to the skin and ears, Atala can "print" the bones of the jaws, grow blood vessels and cells of some organs - the liver, kidneys, lungs.
This technology is especially appreciated by oncologists: on the basis of patient cells, it is possible to recreate the body's response to various types of chemotherapy and observe the reaction to a particular type of treatment in the laboratory, and not on a living person.
But the liver, kidneys, lungs and heart are still being tested. Atala says he raised them in miniature, but creating organs from various tissues to real size requires a lot of additional research.
But, according to him, cells were grown in the laboratory and a vagina was created for a girl who was born several years ago with a congenital deformity of the genital organs - several years have passed since the transplant.
Image caption,Bioprinted polycaprolactam ear implant base
Atala smiles and adds that his team is also working on a working penis. This research has been going on for several years, and the most troublesome for scientists is the complex structure of tissues and the specific sensitivity of the organ itself.
Among others, Igor Vasyutin, a Russian post-graduate student of the First Moscow State Medical University (MGMU) named after Sechenov, is working on this under laboratory conditions. He is a cell biologist, Atala's right hand.
Vasyutin has been in the USA for about a year - he came on an exchange. He is ready to talk about the behavior of stem cells for hours, but becomes less verbose when it comes to Russian science.
At Vasyutin's alma mater, mass regeneration of human organs has not yet been reached and so far they are training on animals: local scientists have "printed" a mouse thyroid gland on a 3D printer.
However, they are also involved in the study of human organs. According to the head of the Institute of Regenerative Medicine at MSMU Denis Butnar, several years ago the Institute recreated a special engineering design of the buccal mucosa. She functioned perfectly for the first six months, but subsequently had to undergo a second operation.
Test specimen of an ear implant under ultraviolet light
In Russia, however, over the past few years, the Italian transplant surgeon Paolo Macchiarini has been practicing - the man who was the first in history to perform a synthetic organ transplant - a plastic tube that replaced the patient trachea.
- Paolo Macchiarini: the rise and fall of the famous surgeon
However, seven of his nine patients died, and the breathing tubes implanted in the remaining two subsequently had to be replaced with donor ones.
Several criminal cases were opened against him, including on charges of pressure on patients and fraud, and the world's leading doctors called Macchiarini's operations "ethical Chernobyl."
Will printed organs replace donors?
At the zenith of his career, Macchiarini argued that a new perspective is opening up for humanity: you can "print" any human organ on a printer, create an engineering structure from it, enriched with the patient's stem cells, and get the perfect prosthesis.
Be that as it may, complex human organs - the liver, kidneys, heart, lungs - have not yet been able to grow any regenerative surgeon.
Bioprinting of so-called simple organs, however, is already available in the USA, Sweden, Spain and Israel - at the level of clinical trials and special programs.
The American government is actively investing in such programs - in addition to Wake Forest, cooperating with the Pentagon, the Massachusetts Institute of Technology also receives significant amounts to recreate the work of the liver, heart and lungs.
Image caption,Skin application test on a burnt wound
According to Professor Jorge Raquela, a gastroenterologist at the Mayo Clinic Research Center, "Bioprinting is one of the most exciting branches of modern medicine, it has huge potential, and the turning point of the most important discoveries is already close."
Meanwhile, Pete Basillier, head of R&D at analytics firm Gartner, insists technology is advancing much faster than understanding the implications of 3D printing.
Such developments, according to Basilière, even if created with the best of intentions, give rise to a set of questions: what will happen when "improved" organs are created, the basis of which will not only be human cells - will they have "superpowers"? Will a regulatory body be created to monitor their production? Who will check the quality of these organs?
More than 150,000 Americans are on the waiting list for organ transplants each year, according to a report from the US National Library of Medicine. Donor organs will receive only 18% of them; every day in the United States, without waiting for a transplant, 25 people die. Organ transplants and subsequent rehabilitation cost insurance companies and patients $300 billion in 2012 alone.
- A 3D printer helped a cyclist who lost his jaw
- Genetically modified pigs - human organ donors?
- The world's first child to have both hands transplanted plays baseball
And most Americans are potential donors: when they get a driver's license, they voluntarily answer the question of whether they agree to donate their organs in the event of a car accident or other dangerous incident .