Advanced 3d printing technologies
five innovative 3d printing technologies
The 5 3D Printing Technologies that are taking over the world
3D Printing also known as Additive Manufacturing is increasingly becoming a very important tool in many industries such as education, manufacturing, robotics, automotive, aerospace, construction, architecture, dentistry, jewellery and engineering just to name a few. Compared to outsourcing, fabrication in-house can significantly cut costs and offer more freedom to create more prototypes and design iterations.
To those who are new to 3D printing, distinguishing and understanding the various 3D printing technologies, processes and materials available can be an initial challenge. You may be wondering which 3D printing technology can my business use? To get you more familiar with the different types of 3D printing, we will go through the five 3D printing technologies that are disrupting the industries mentioned above.
SLA (Stereolithography)
Stereolithography short for SLA is a 3D printing process that utilises a UV laser or other light source, to cure liquid resin into solid plastic. The most commonly used SLA-system is inverted Stereolithography and depending on the 3D printer, the resin can either be poured manually by the user or automatically dispensed from a cartridge. The build plate is lowered into the resin at the beginning of the print. A thin layer of liquid is left between the bottom of the tank and the build pate. The UV laser is directed from the Galvanometer or Galvos through a translucent window located at the bottom of the resin tank, selectively solidifying the material. Successive layers are built off a print each having less than 100 microns.
SLA 3D printers are very well suited to print parts that have complex geometries and intricate details. Support structures will need to be used in most cases - the printed parts must be cleaned with isopropyl alcohol followed by UV curing, sometimes in a UV oven, before they can be used.
When the technology was first developed in the 80s, SLA was initially restricted to large industrial machines. The desktop stereolithography 3D printers available today are not only more affordable than ever, they also offer high resolution 3D printing that easily fits in your workspace. SLA makes it possible for you to use an extensive range of materials with limitless physical possibilities, allowing you to take your creativity to the next level.
LFS (Low Force Stereolithography)
Low Force Stereolithography short for LFS is dubbed the next generation of Stereolithography (SLA). In late 2019, Formlabs released two advanced 3D printers using the technology – the Formlabs Form 3 and the Form 3L. This innovative additive manufacturing technology uses a flexible tank and linear illumination to deliver an immaculate surface finish and print accuracy. The lower print forces of the Low Force Stereolithography print process allows printers using the technology such as the Formlabs Form 3 to deliver consistent high-quality results. It allows light-touch support structures to be easily torn away, taking the stress and unnecessary work out of building and cleaning parts. This lets you focus on the more important things such as design and creation.
FFF (Fused Filament Fabrication)
Fused Filament Fabrication short for FFF is the most commonly used additive manufacturing technology. This is because its easy to use and it doesn’t rely on chemicals. FFF utilises roll of filament that is usually thermoplastic delivered on a spool. The Fused Filament Fabrication process extrudes the filament through a heated nozzle that is attached on a motion system. When a part is in the process of 3D printing, the motion system moves around the build area and melted filament is deposited from the nozzle onto the build plate. When the melted filament cools, it hardens to form a layer. The build plate or bed moves less than a millimetre and the process is repeated to start another layer until the part is completely formed.
The Dual Extrusion feature on some FFF 3D printers allow the use of two materials in one print. The use of two different colours of the same material is typically used for aesthetic purposes. The use of two different types of materials are used for variation in mechanical properties. Using a water-soluble PVA support material alongside the build material is also possible. The support material will dissolve away when submerged in water to ensure the final part has a high-quality finish while doing minimal post-processing labour.
FFF 3D printers are perfect to use in office settings because the machines are typically simple to use and maintain. The printing and post processing process doesn’t rely on chemicals, so a well-ventilated area wouldn’t be as necessary to use for FFF 3D printers compared to SLA 3D printers. The consumable options for FFF 3D printers are not only extensive, they are relatively cheaper compared to other methods. The consumables are simple to set up and can be stored for a long period of time.
Composite 3D Printing
The composite and metal 3D printing technology from Markforged (which we will go through in the next section) are the next major revolution of additive manufacturing. 3D printing was changed when Markforged launched their industrial series - with their machines allowing you to reinforce parts with continuous carbon fibre, making the finished part 10x stronger. The features equipped on the Markforged Industrial range printers such as the X7 that makes the composite 3D printing technology very unique and innovative are:
- In Print Scanning/Process Inspection: This feature allows you to ‘in real time’ print your part, scan your part and measure the dimensional accuracy of the part to ensure accuracy.
- Stepper Motor Encoders: Located on the X, Y and extrusion motors, these encoders allow the printer to detect position inaccuracy and correct automatically.
It enables auto correction of the problems and help save more prints, saving you more money in the long run. The encoders also ensure the positional accuracy of the head giving you those stunning part surface finishes.
- Material Detection: Located on both the fibre extruder and plastic extruder, this feature automatically pauses the print and sends you an email notification if the material runs out during the print. It enables you to reload with new material and continue the print.
- Silent Drives: The Markforged industrial 3D printers are equipped with silent drives to ensure noise-free 3D printing day and night.
- Micro Controller: If you replace the print head where the Micro Controller is located at, there is no need for calibrating X Y offsets as these have been done at the factory and saved on the print head. It also includes other sensors allowing you to detect faults before they happen and look for maintenance issues.
Metal 3D Printing
One of the most advanced 3D printing processes today is Metal 3D printing. The Markforged Metal X 3D print system is a manufacturing breakthrough that covers the full production process from beginning to end. The process is a very organised system that let’s you print and post-process ready to use parts in-house. The steps include:
- Software part setup: Once your part is designed in a CAD software, it must be exported to an STL file and imported into Markforged’s software, Eiger. It enables you to choose from a wide range of metals to 3D print and Eiger takes care of the rest. The parts are automatically scaled up to compensate for material shrinkage.
- Print: Metal powder bound in plastic is printed layer by layer until your part is fully formed, using the FFF printing process.
- Wash: After the part has been printed, it goes through what’s called a debinding process. This is where the part is washed in degreaser to remove the wax from the part. This prepares it for the next stage.
- Sinter: The part is then sintered in a furnace which burns away all the plastic bonding material and allows the metal powder to fuse into a part with approximately 96% relative density.
- Final Part: The part is now made from “pure” metal. It is now ready to use and can be post processed and treated like any other metals.
To dive deeper into the process above, you can read our blog ‘3D Model to a Metal 3D Printed Part’ to learn more about this incredible technology.
Conclusion
The 5 3D printing technologies each have their own unique uses. SLA is great for detailed smaller objects that require complex features. LFS is ideal for high-volume production that consistently delivers high-quality results without the need of additional labour. FFF is perfect for those who are budget conscious. This versatile, easy to use and affordable technology can be implemented in the comfort of your own office, without the need of additional space and specialist staff to operate. Composite and Metal 3D printing are ideal for businesses who want to manufacture industrial strength parts in-house.
Click here to see our gallery of FFF, Composite and Metal 3D printed parts.
3D printing technologies: types and advantages
The selection of a technology proper for our project is sometimes one of the most difficult decisions we make. A wide scope of completely different 3D printing methods forces a question: what are the greatest differences between the specific 3D printers and which speciality materials available on the market will be the best. The last but not least question is obviously the one about the price of 3D printing in the technology we have selected.
The most frequently chosen technologies are: Fused Deposition Modeling (FDM), Stereolithography (SLA), Selective Laser Sintering (SLS), PolyJet and Direct Metal Laser Sintering (DMLS). The proper application of those five 3D printing solutions guarantees the achievement of most important advantages related to such printing. Adam Przepolski, 3D Services Manager at 3DGence
1. Fused Filament Fabrication (FFF) lub Fused Deposition Modeling (FDM):
3D printing in FDM/FFF technology is one of the oldest and most widespread additive methods in the world. It consists in depositing the subsequent layers of fused material and letting the adjacent layers cool and merge with each other before another layer is deposited.
The FDM technology may be described as a process reverse to CNC numerical cutting. 3D models are transformed in g-codes being sets of instructions. They serve the positioning of drivers, and thus making precise extrusions for the purpose of creating another layer. The technology mostly uses an exact quantity of material required for the specific part, otherwise than in CNC methods which generate high losses of the material we use.
The resolution of high prototyping is affected by many factors, such as accuracy of drivers positioning, calibration by the user, or quality of material applied in FDM 3D printing. Generally, the FDM printing tolerance is 0.15 mm to 0.25 mm.
Where are FFF or FDM technology applied?The greatest FDM advantages include fast adjustment of the filling of the printed 3D models. This means that it is very easy to print a prototype only for checking the adjustment and finishing. With low internal filling, or even hollow core, we save on the cost of material. With the design phase finished we may carry out final control or launch small or medium-sized production series with the final filling of the respective 3D print.
FFF is the most optimal method of fast prototyping of parts which must keep the standard tolerance. The method has been widely used in creating architectural or model mock-ups. The technology guarantees affordable prices and short lead time.
Request for a 3D printed sample
Contact us
FDM 3D printout
FDM 3D printout
Part 3D printed with the use of FDM technoloy
2. Selective Laser Sintering (SLS):
SLS consists in merging polyamide particles with the use of a high-energy laser beam The process starts with chamber filling with powdered material. Along with the progress of printing the working surface lowers and another layer of powder is added. Sintering of the polyamide powder takes place carefully, layer by layer. The 3D SLS technology does not require any supports to be applied, because models are naturally supported by the excess of powdered material which closely surrounds the printout. The solution enables manufacturing of geometrically complex elements with high dimensional accuracy, compared to other 3D printing methods.
SLS is particularly interesting with regard to the use of materials which are broadly applied in the plastics industry, including polyamides. In that technology we may print, for example from a flame resistant PA 2241 FR material assigned the German certificate of CS 25 / JAR25 / FAR 25 § 25-853 (a) App. F Part I, ABD 0031. For elements which need to be more rigid, the PA 3200 GF (glass fibre) is enhanced with powdered glass. The materials most frequently used in industry includes also PA 12 (PA 2200).
3D printing of large modelsSLS devices mostly used in that 3D printing methods have working chambers of the size 340 x 240 x 600 mm, which enables printing quite large elements or hundreds of smaller pieces in a series, ensuring high level of repeatability offered by Selective Laser Sintering. The SLS technology guarantees 0.15 mm tolerance.
Consult your project with 3D printing experts
Contact us
SLS 3D printed part
SLS 3D printed part
SLS 3D printed part
3.
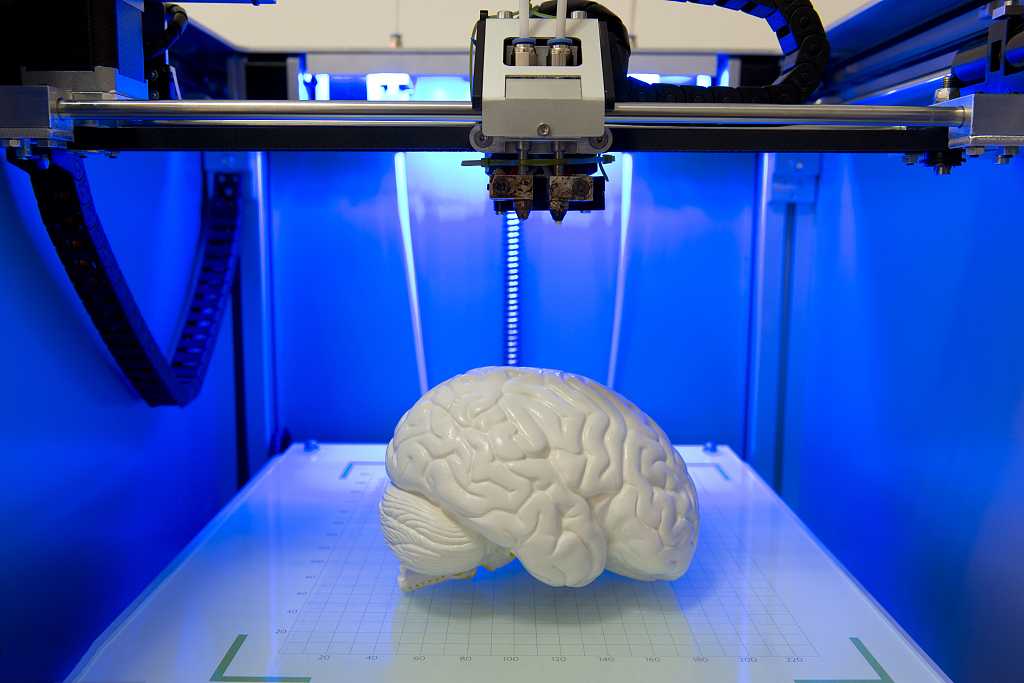
SLA is a 3D printing technology using a liquid photopolymer resin. SLA is a precise 3D printing technology where the model material is cured with an UV laser beam in order to arrive at the final geometry. The material needed for SLA printing – liquid resin – is stored in a tank where the working platform is gradually immersed and then locally illuminated (in the places where the respective model is to be created) by a UV laser. The curing of resin by way of illumination is repeated until the part is ready, and the latter is finally washed with isopropyl alcohol in order to remove the polymer which as not hardened. After cleaning, the printout is placed in a speciality light-setter where the resin models get their final properties.
Wide range of SLA materialsSLS is particularly interesting with regard to the use of materials which are broadly applied in the plastics industry, including polyamides. In that technology we may print, for example from a flame resistant PA 2241 FR material assigned the German certificate of CS 25 / JAR25 / FAR 25 § 25-853 (a) App. F Part I, ABD 0031. For elements which need to be more rigid, the PA 3200 GF (glass fibre) is enhanced with powdered glass. The materials most frequently used in industry includes also PA 12 (PA 2200).
Stereolithography is one of the most precise 3D printing technologies in the world. It enables recreation on the printed models of even the finest details. The accuracy of the SLA printouts ranges from 0.1 mm to 0.2 mm.
Consult your project with 3D printing experts
Contact us
SLA 3D print
SLA 3D print
SLA 3D print
4. Direct Metal Laser Sintering (DMLS)
DMLS one of the most advanced technologies. A powerful laser is used in 3D printing to fuse metals and alloys on a micro scale. The main applications of DMLS include the creation of metal parts of complex geometry. Right after the 3D printing process the parts are fully functional (heat-resistant, strong and durable). In fact, the parts are even better than those cast with regard to density, and that translates into their mechanical properties.
Direct Metal Laser Sintering is highly advantageous compared to the traditional production methods, as even the most complex elements may be manufactured into a unit production cycle, which means a reduction of production costs. The DMLS technology combined with topological analysis enables manufacturing of parts which are lighter than those originating from the conventional manufacturing methods.
The metal parts produced in the DMLS technology are exceptionally durable and their weight to durability ratio is very high. Usually, high-resistance materials are used, such as 316 L tool steel, an aluminium alloy, titanium or Inconel (an alloy of nickel and chromium).
Check how 3D printed metal part may bring savings to your project Know more about 3DServices
5. PolyJet
The 3D PolyJet technology is one of the most precise 3D printing technologies in the world. The operation principle is close to the SLA technology, as it is based on curing liquid resin. However, the photopolymer resins are cured with UV lamps in this case. A single layer printed in the technology is only 0.016 mm thin (less than the thickness of a human hair). The accuracy of the technology of less than 0.099 mm may not be matched by any other additive technology.
The PolyJet technology will prove to be adequate in making precise elements where high accuracy is required, due to the application of resins of varied properties, particularly mechanical properties, and the soluble support material. It is dedicated to fast prototyping and creating high-quality, smooth-surface final prototypes.
Check the possibilites of PolyJet in your project
Contact us
PolyJet 3D print
3DGence responds to the needs of the market, providing their line of as many as fifty-two 3D printers based on five different printing technologies (FDM, SLA, PolyJet, SLS, and DMLS).
All the inquiries about 3D services are forwarded to a specialised team of application engineers who help select the proper materials to the respective needs. Write to use and consult your project: [email protected]
The projects entrusted with us may be created from over 60 available materials. We provide comprehensive support, starting from a design and 3D modelling, through the selection of a proper 3D printing technology, and ending with painting and final finishing of the ready printout. Our experienced team of engineers provides professional support in performing prototype projects, printing speciality tools or making tests for manufacturing lines for small and medium-scale series, or even preparing industrial equipment mock-ups. We offer short lead times and competitive 3D printing prices. Adam Przepolski, 3D Services Manager at 3DGence
What technologies underlie 3D printing?
The plethora of 3D printing techniques currently on the market does not preclude continued ongoing research to develop more innovative technologies. Although the material differs depending on the printing method used, each technology has its own advantages. They are mainly related to the specific applications for which these printers are intended.
3D Printing Technology Overview
The 3D printing technologies available today are grouped into three main families. These include printing by wire deposition or extrusion (FFF, FDM), the use of liquid photosensitive resin (SLA, DLP), and finally the use of powder or sintering (SLS, SLM, DMLS).
Fusion or extrusion printing allows you to create an object layer by layer. It involves the use of plastic thread. Placed on the printhead, the latter melts and deposits superimposed layers on the print bed.
As for the liquid photosensitive resin, it is cured by projector or laser. This operation, also known as polymerization, causes the object to be created to form inside the tray containing the resin. Stereolithography (SLA) is one of the technologies that regularly uses this printing process. ₽
An energy source - for example, a laser - melts metal powder previously placed in a 3D printer tank. The term used for this type of printing is powder sintering or laser sintering. This is a technology with several options: SLS (Selective Laser Sintering) or SLM (Selective Laser Melting).
Molten filament printing
Two expressions are used to characterize this technology. The first, FDM, comes from English (Fused Deposition Modeling).
As for the second one, FFF, it stands for Fused Filament Fabrication. The term extrusion is another name for this 3D printing process. The consumables are plastic filament (PLA or AB).
A 3D printer has a print head, also called a nozzle. It is on this nozzle that the previously heated fiber is melted. The nozzle moves along two axes, x and y, parallel to the print platform, which moves in the vertical direction. Only after the first layer is completed, the print platform lowers along its axis.
Molten thread is applied layer by layer to create a 3D object. The fusion of the various layers is due to the rapid solidification of the molten plastic. As soon as the layers of plastic are stacked on top of each other, we get a designed object, the model of which is visible on the computer screen. Extrusion can also be carried out using an energy source such as a laser and by direct application of energy. This 3D printing mode, better known by its acronym DED (Directed Energy Deposition), can be found on some industrial printers. The material pushed out by the energy source then melts before being fused into an object.
3D printing by polymerization of photosensitive resin
The use of SLA or DLP technology is typical for 3D printers using resin as the printing material. The process of their printing is polymerization. It refers to the curing of the photosensitive resin under the influence of a light source such as a laser or a light projector. The liquid resin in the printer tray hardens as a result of the reaction created by the light beams.
The print tray is located at the bottom of the tray that holds the liquid resin. A DLP projector or SLA laser emits light that hardens the resin from layer to layer. Finishing the layer allows the tray to sink further into the tray and so on until the object is made.
Having parts that require a high level of detail and resolution on the smooth side is a reason to use a 3D printer such as an SLA or DLP printer. Areas such as jewelry and medicine are the most common areas where this printing process is used. The production of molds intended for the manufacture of jewelry or dentures requires both precision and finesse.
Only resin polymerization makes it possible to distinguish between the two categories of SLA and DLP printers. On a DLP printer, the resin hardens layer by layer. In an SLA printer, on the other hand, it solidifies point by point. In addition, a DLP printer uses a projector, while an SLA printer uses a laser to print.
3D powder melt printing
Four technologies use this 3D printing process. These are powder sintering and melting, material grinding, paper lamination and, finally, 3D bioprinting.
The use of metal powder as printing material is common in the industrial sector. Selective laser sintering or selective laser melting are two 3D printing technologies that use powder. In the field of aviation, for example, this technology allows the production of highly complex parts intended for use in aircraft.
Spraying or inkjet printing of material is a printing process in which molten material is deposited on a printing platform. The object is formed by the layer-by-layer solidification of the previously melted material. Multi-Jet Modeling (MJM) is another name for this printing method.
The 3D printing technology known as lamination uses paper or aluminum foil as the material. Objects produced using this technique are distinguished by the perspective of details and colors. The decoration and toy manufacturing sector are those who regularly use this technology.
The creation of living cells or organic tissues is the field of bioprinting experiments. This scientific process represents a real revolution in the field of medicine. Ultimately, bioprinting aims to produce functional organs or living tissues. While this technology is at the experimental stage. 3D bioprinters with this printing ability are not yet a reality. However, if they existed, such machines would make it possible to create organs and treat many pathologies.
Source
Tags:
3D printing technologies, 3D wire deposition or extrusion printing (FFF, FDM), 3D liquid photosensitive resin printing (SLA, DLP), 3D printer, 3D hot melt printing , 3D bioprinting
5 innovative applications of 3D printing in medicine
Personalized and precise solutions in the medical field are becoming increasingly popular. New tools and advanced technologies bring doctors closer to patients by providing treatments and devices that meet the needs of each individual.
The expansion of 3D printing technologies in healthcare has made a huge contribution to improving the quality of medical services. With new tools and treatment approaches developed using 3D printing, patients feel that their treatment becomes more comfortable and personal. For physicians, the new technology available allows them to better analyze complex cases and provides new tools that can ultimately raise standards of care.
Later in this article, you'll learn about five areas, from models for surgical planning to vascular systems and bioreactors, in which 3D printing is used in healthcare, and why many healthcare professionals see great potential in this technology.
In today's medical practice, 3D printed anatomical models based on patient body scans are becoming more indispensable tools, as they provide more personalized and accurate treatment. As cases become more complex and standard case times become more important, visual and tactile anatomical models are helping surgeons to better understand their task, communicate more effectively, and communicate with patients more easily.
Medical professionals, hospitals and research institutions around the world use 3D printed anatomical models as a reference tool for preoperative planning, intraoperative imaging, and for sizing medical instruments or presetting equipment for both standard and very complex procedures, which is reflected in hundreds of scientific publications.
3D printing makes 3D printing affordable and easy to create customized patient anatomical models based on CT and MRI data. The peer-reviewed scientific literature demonstrates that they help clinicians better prepare for surgery, resulting in significant cost and time savings. At the same time, patient satisfaction is also increased through reduced anxiety and reduced recovery time.
Physicians can use individual patient anatomical models to explain the procedure to the patient, making it easier to obtain patient consent and reduce patient anxiety.
Preparation for surgery using preoperative models can also affect the effectiveness of the treatment. The experience of Dr. Michael Ames confirms this. After obtaining bone replications from the young patient's forearm, Dr. Ames realized that the injury was different from what he expected.
Based on this information, Dr. Ames chose a new soft tissue procedure that was much less invasive, reduced downtime, and resulted in much less scarring. Using imprinted bone replication, Dr. Ames explained the procedure to the young patient and his parents and obtained their consent.
Physicians can use patient-specific surgical models to explain the procedure beforehand, improving patient consent and lowering anxiety.
Result? The operation lasted less than 30 minutes instead of the originally planned three hours. With this reduction in operating time, the hospital avoided a cost of about $5,500 and the patient recovered faster.
According to Dr. Alexis Dang, Orthopedic Surgeon at UC San Francisco and Veterans Affairs Medical Center San Francisco: “All of our full-time orthopedic surgeons and nearly all of our full-time surgeons part-time, used 3D printed models to treat patients at a Veterans Medical Center in San Francisco. We could all see that 3D printing improves the efficiency of our work.”
The advent of new biocompatible medical polymers for 3D printing has opened up opportunities for the development of new surgical instruments and techniques to further improve clinical operating procedures. These include sterilizable trays, contoured surgical guides, and implant models that can be used to determine the size of an implant prior to surgery, helping surgeons reduce time and improve accuracy in complex procedures.
Anatomical model of a hand with elastic resin skin for 3D printing.
Todd Goldstein, PhD, lecturer at the Feinstein Institute for Medical Research, is unequivocal about the importance of 3D printing technology to the work of his department. He estimates that if Northwell used 3D-printed models 10-15% of the time, it could save $1,750,000 a year.
“Whether it's prototyping medical devices, complex anatomical models for our children's hospital, designing training systems, or making surgical templates for dental clinics, [3D printing technology] has increased our capabilities and reduced our costs in a variety of areas. In doing so, we were able to produce instruments for treating patients that would be almost impossible to recreate without our sought-after stereolithography 3D printer,” says Goldstein.
3D printing has become virtually synonymous with rapid prototyping. The ease of use and low cost of 3D printing in-house has also revolutionized product development, with many medical instrument manufacturers adapting the technology to produce entirely new medical devices and surgical instruments.
Over 90 percent of the top 50 medical device companies use 3D printing to create accurate medical device prototypes and fixtures and fittings to simplify testing.
According to Alex Drew, Principal Mechanical Engineer at DJO Surgical, an international medical device supplier, “Before DJO Surgical purchased [Formlabs' 3D printer], we printed nearly all of our prototypes outsourced. Today we are working with four Formlabs printers and are very pleased with the results. The speed of 3D printing has doubled, the cost has been reduced by 70%, and the level of detail allows you to effectively coordinate designs with orthopedic surgeons.
Medical companies such as Coalesce are using 3D printing to create accurate medical device prototypes.
3D printing helps speed up the design process by allowing complex designs to be iterated over in days instead of weeks. When Coalesce was tasked with building an inhaler device that could digitally evaluate an asthma patient's inspiratory flow profile, outsourcing would result in a significant increase in production time for each prototype. Before sending the project files to a third party company for the physical implementation of the project, they would have to be carefully developed and carried through various iterations.
Instead, desktop stereolithographic 3D printing allowed Coalesce to handle the entire prototyping process in-house. The prototypes were suitable for use in clinical trials and looked just like the finished product. Moreover, when the company demonstrated the device, its customers mistook the prototype for the final product.
Overall, the introduction of in-house manufacturing resulted in an exceptional reduction in prototyping time by 80–90%. In addition, the models took only eight hours to print and were finished and painted in a matter of days, while outsourcing the same process would take a week or two.
Hundreds of thousands of people lose limbs every year, but only a fraction of them are able to restore limb function with a prosthesis.
Conventional dentures are only available in a few sizes, so patients must adjust to what fits best. On the other hand, custom bionic prostheses that mimic the movements and grips of a real limb based on the impulses of the surviving limb muscles are so expensive that they can only be used by patients living in developed countries with the best medical insurance. In the case of children's prostheses, the situation is aggravated even more. Children grow up and inevitably outgrow their prostheses, which, as a result, require costly modifications.
The difficulty lies in the lack of manufacturing processes that would allow for individual orders at an affordable price. But increasingly, prosthetists are looking to reduce these high financial barriers to rehabilitation with the flexible design capabilities of 3D printing.
Initiatives like e-NABLE allow people around the world to learn about the possibilities of 3D printed prostheses. They are driving an independent movement in the prosthesis industry by offering information and free open source projects so that patients can get a custom-designed prosthesis for as little as $50.
Other inventors, such as Lyman Connor, go even further. With only a small fleet of four desktop 3D printers, Lyman was able to fabricate and customize his first mass-produced prostheses. His ultimate goal? Create a customizable fully bionic arm that will cost incomparably less than similar prostheses that retail for tens of thousands of dollars.
Researchers at the Massachusetts Institute of Technology have also found that 3D printing is the best method for making more comfortable prosthetic sockets.
In addition, the low cost of manufacturing these prostheses, as well as the freedom that comes with being able to design custom designs, speak for themselves. 3D printed prostheses have a lead time of just two weeks, and then they can be tried and serviced at a much lower cost than traditional counterparts.
As costs continue to fall and material properties improve, the role of 3D printing in healthcare will no doubt become more important.
The same high financial barriers that are seen in prosthetics are common in orthoses and insoles. Like many other patient-specific medical devices, custom-made orthoses are often not available due to their high cost and take weeks or months to manufacture. 3D printing solves this problem.
Confirmation is the example of Matej and his son Nick. Nick was born in 2011. Complications during preterm birth led to the fact that he developed cerebral palsy, a pathology that affects nearly twenty million people worldwide. Matei was delighted with how determined his son was to overcome the limitations of his illness, but he was faced with a choice between a standard, off-the-shelf orthosis that would be uncomfortable for his son, or an expensive custom solution that would take weeks or months to manufacture and ship. , and from which the child would quickly grow.
He decided to take matters into his own hands and began to look for new ways to achieve his goal. Thanks to the opportunities provided by digital technologies, in particular 3D scanning and 3D printing, Matei and Nika's physiotherapists were able to develop a completely new innovative workflow for the manufacture of ankle orthoses through experiments.
The resulting 3D-printed, custom-fit orthosis that provides support, comfort, and motion correction helped Nick take his first steps on his own. This non-standard orthopedic device reproduced the functionality of the highest-class orthopedic products, at the same time it cost many times less and did not require any additional settings.
Professionals around the world are using 3D printing as a new method of manufacturing custom insoles and orthoses for patients and clients, as well as a range of other physiotherapy tools. In the past, undergoing a course of physiotherapy with the use of individual physiotherapy instruments carried many difficulties. Often there was a situation when patients had to wait a long time for a finished product, which at the same time did not provide proper comfort. 3D printing is step by step changing this status quo. Data confirms that 3D printed insoles and orthoses offer a more precise fit and lead to better therapeutic outcomes, which means greater comfort and benefit for patients.
The usual treatments for patients with severe organ damage today are autografts, transplantation of tissue from one area of the body to another, or transplantation of a donor organ. Researchers in bioprinting and tissue engineering hope to expand this list soon with on-demand fabrication of tissues, blood vessels, and organs.
3D bioprinting is an additive manufacturing process that uses materials known as bioink (a combination of living cells and a compatible substrate) to create tissue-like structures that can be used in medicine. Tissue engineering combines new technologies, including bioprinting, which make it possible to grow replacement tissues and organs in the laboratory for use in the treatment of injuries and diseases.
Using high-precision 3D printing, researchers such as Dr. Sam Pashne-Tala from the University of Sheffield are opening up new possibilities for tissue engineering.
In order to direct cell growth to form the necessary tissue, Dr. Pashne-Tala grows living cells on a laboratory scaffold that provides a template of the required shape, size and geometry. For example, to create a blood vessel for a patient with cardiovascular disease, a tubular structure is needed. The cells will multiply and cover the scaffold, taking on its shape. Then the scaffold is gradually destroyed, and the living cells take the form of the target tissue, which is cultured in a bioreactor - a chamber that contains the cultured tissue and can reproduce the internal environment of the body so that the cultured tissue acquires the mechanical and biological characteristics of organic tissue.
3D printed bioreactor chamber with tissue engineered aorta miniature inside. The tissue is cultured in a bioreactor to acquire the mechanical and biological characteristics of the organic tissue.
3D printed bioreactor chamber with tissue engineered aorta miniature inside. The tissue is cultured in a bioreactor to acquire the mechanical and biological characteristics of the organic tissue.
This will allow scientists to design patient-specific vascular grafts, expand surgical care, and provide a unique platform for testing new vascular medical devices for people suffering from cardiovascular disease, which is currently the leading cause of death worldwide. The ultimate goal is to create blood vessels that are ready for implantation in patients. Since tissue engineering uses cells taken from a patient in need of treatment, this eliminates the possibility of rejection by the immune system, which is the main problem of modern transplantology.
3D printing has proven its ability to solve the problems that exist in the production of synthetic blood vessels, in particular, the difficulty of recreating the required accuracy of the shape, size and geometry of the vessel. The ability of printed solutions to clearly reflect the specific characteristics of patients was a step forward.
According to Dr. Pashne-Tal: “[Creating blood vessels using 3D printing] makes it possible to expand the possibilities of surgical care and even create designs of blood vessels for a specific patient. Without the existence of high-precision affordable 3D printing, the creation of such forms would not be possible.”
We are witnessing significant advances in the development of biological materials that can be used in 3D printers. Scientists are developing new hydrogel materials that have the same consistency as organ tissues present in the human brain and lungs, which can be used in a range of 3D printing processes. Scientists hope that they will be able to implant them into the body as a "scaffold" for cell growth.
Although bioprinting of fully functional internal organs such as the heart, kidneys and liver still looks futuristic, hybrid 3D printing at very high speed opens up more and more new horizons.
It is expected that sooner or later the creation of biological matter on laboratory printers will lead to the generation of new, fully functional 3D printed organs. In April 2019, scientists at Tel Aviv University 3D-printed the first heart using biological tissue from a patient. A tiny copy was created using the patient's own biological tissues, which made it possible to fully match the immunological, cellular, biochemical and anatomical profile of the patient.
“At this stage, the heart we printed is small, about the size of a rabbit heart, but normal-sized human hearts require the same technology,” says Prof. Tal Dvir.
The first 3D bioprinted heart created at Tel Aviv University.
Precise and affordable 3D printing processes, such as desktop stereolithography, are democratizing access to technology, enabling healthcare professionals to develop new clinical solutions and quickly produce medical devices with individual characteristics, and doctors around the world to offer new types of therapy.