3D scanner for fusion 360
Exploring a Scan-to-CAD Workflow with peel 3d
Jason Evers runs Eversfab, a small custom automotive company located in Lousiana, USA. Evers worked as a firefighter with a passion for racing cars. He then started making parts for his own use. His good work started getting noticed —friends would ask for parts, etc. Eventually, he quit his regular job and dedicated himself to creating race car parts. “I’ve had a lot of jobs, but nothing as enjoyable as creating solutions for problems on dedicated race cars,” he says. “I love seeing a customer’s appreciation when their concept or vision was executed above their expectations.”
For one recent project, a customer asked Eversfab to create a custom roll cage for a Corvette. Using the peel 3d scanning solution combined with Fusion 360, Evers designed the full cage in 3D before any parts were made. Designing custom parts usually requires a lot of manual measuring, trials, and errors, plus many alterations to fit everything in place. However, using this workflow, Eversfab had perfect part fitting on the first try.
I chose Fusion 360 for its intuitive interface and because it was Mac-compatible. There was a learning curve, sure. But Fusion 360 has become my go-to app for in-depth design as well as quick sketches.”
– Jason Evers, Founder of Eversfab
“Even when the roll cage itself is being designed in CAD software, if the measurements for the chassis are being taken by hand, there are too many angles and contours to effectively map out the cage the first time with full confidence,” says Evers. “There are often parts scrapped due to trial and error, with several hours of work and raw materials going into each wasted part. When designing from an actual scan, that waste is eliminated.”
Combined with the tools from Fusion 360, Evers could design the best product without a background in CAD. “I wasn’t familiar with CAD when I started Eversfab. I had programming and design experience, but not CAD related. I chose Fusion 360 for its intuitive interface and because it was Mac-compatible. There was a learning curve, sure. But Fusion 360 has become my go-to app for in-depth design as well as quick sketches.”
Evers uses custom parameters in his designs whenever possible. “Many times, there will be a value that will need to be changed, and basing a measurement on a global variable is very helpful in the parametric design workflow. This can mean roll cage tubing ID, bend locations on sheet metal, the thickness of metal, etc.”
peel 3d scanning technology has become a staple in Evers’ Fusion 360 workflow, as exemplified in the below YouTube video that shows the peel3d team reverse engineer a Mustang ’69 Exhaust Pipe, teaching how to extract geometric entities from mesh files and save time on CAD creation along the way.
When starting the Corvette roll cage project, Evers quickly realized the return on investment of 3D scanning with peel 3d technology would be time-saving. “When the peel 1 scanner came out, I started budgeting toward buying one. I was very excited about the price point and knew that my time spent revising designs would be drastically reduced, so it had to happen.”
But why peel 3d technology specifically? “I initially chose peel 3d because it was a turn-key package. Activate the license, install the software, then begin scanning and creating. I was looking at many other systems, and the amount of issues the customers faced, lack of support, problematic software, and sub-par hardware were all going to waste the time I was hoping to save by using a scanner in the first place. After becoming efficient with the peel, I added more reasons to my list, but my initial scans out the box exceeded my expectations.” When the peel 2 CAD technology came out, Evers knew upgrading from the peel 1 would be beneficial in cutting time and improving his work efficiency in Fusion 360.
For Eversfab’s Corvette roll cage project, the impact of using both the peel 3d scanner and Fusion 360 was undeniable. It is the first roll cage project with zero-waste designed from a scan. “My cage fits so tightly that there is almost no discomfort and maximum head room for my customer,” says Evers. “I credit it completely to the accuracy and design methods available to me thanks to peel 3d and Fusion 360.”
Having the peel 3d scanner at the office had a clear impact on developing broader solutions: “We originally had no plans to go into parts production of any kind, but the Peel has opened those doors for us, and we are working on partnerships for the first runs of parts we plan to release soon.”
The scan-to-CAD workflow may not be for everyone yet, but we fully expect to see advancements made that will make it continue to gain traction across many industries. If you’re interested in trying out a peel 3d and Fusion 360 workflow to save time with measurements and easily extract geometric entities from mesh files, check out peel 3d here and Fusion 360 with the button below.
3D Scanning: From Mesh to Model Online Class
- All topics
- Creative
- Product and Manufacturing
- 3D Scanning
With Nick Kloski Liked by 183 users
Duration: 3h 49m Skill level: Beginner + Intermediate Released: 7/10/2020
Start my 1-month free trial
Course details
Interested in learning the basics of reverse engineering? In this course, instructor Nick Kloski helps you get up to speed, covering the fundamentals of reverse engineering using 3D scan data as a basis. As he details key concepts, Nick steps through how to go from a 3D scan to an optimized model that fits into nearly any product design workflow. He reviews the technologies available for 3D scanning, including photogrammetry and structured light. Using Artec structured light scanners as an example of capture technology, Nick goes into a workflow using inexpensive or free software to perform a complete reverse engineering workflow. See how to convert the scan (a mesh) into an optimized form, and bring it through Fusion 360 to create a solid model that can be flexibly incorporated into product design workflows.
This course was recorded and produced by HoneyPoint3D. We are pleased to host this training in our library.
Skills you’ll gain
- 3D Scanning
Earn a sharable certificate
Share what you’ve learned, and be a standout professional in your desired industry with a certificate showcasing your knowledge gained from the course.
Learning LinkedIn Learning
Certificate of Completion-
Showcase on your LinkedIn profile under “Licenses and Certificate” section
-
Download or print out as PDF to share with others
-
Share as image online to demonstrate your skill
Meet the instructor
-
Nick Kloski
Co-Founder at HoneyPoint3D
Learner reviews
32 ratings
The overall rating is calculated using the average of submitted ratings. Ratings and reviews can only be submitted when non-anonymous learners complete at least 40% of the course. This helps us avoid fake reviews and spam.
- 5 star Current value: 26 81%
- 4 star Current value: 5 15%
- 3 star Current value: 1 3%
Abdalla Mohamed
Metrology Engineer
5/5 July 24, 2022
it was very useful course ,very diverse Software and technics thankx
Helpful · Report
Danish KhanDanish Khan
Master Student at Delhi Technological University(Formerly DCE)
Contents
What’s included
- Practice while you learn 1 exercise file
- Learn on the go Access on tablet and phone
Similar courses
Download courses
Use your iOS or Android LinkedIn Learning app, and watch courses on your mobile device without an internet connection.
EinScan H 3D scanner and Fusion 360 in boat manufacturing
Applications
This area is located in a hilly area in the center of England, far from the sea, but in these parts the Thames begins its journey. The workshop of the hereditary shipbuilder Daniel Lee is also located here. For Daniel, building a boat is the pinnacle of woodworking, as the hulls are almost completely devoid of straight lines. In his own words, this adds difficulty and beauty to his craft.
Daniel has been carpentry, building and repairing boats since he was young. Most of all, he likes racing sailing yachts and boats from the pre-war period, which he considers the golden era - the zenith of the quality and sophistication of wooden shipbuilding. However, Daniel keeps a close eye on the constant development of modern production and design technologies.
From 3D Scanning to Production: Boat Restoration and Reproduction with EinScan H and Fusion 360
Last year, Daniel was involved in the restoration of a boat, apparently built in 1969 or 1970 by a craftsman named Ray Stapley specifically for water skiing. In parallel with the repair, Daniel decided to use the EinScan H 3D scanner and digitize the original in order to have a model in hand for the production of equipment, and then full-fledged replicas of the boat.
1. 3D scan with EinScan H
3D scan of a boat hull with EinScan H
EinScan H is a very efficient, easy-to-use and at the same time inexpensive 3D scanner. The device is easy to learn and well suited for work even in high-tech production: the light weight and dimensions of the 3D scanner make it easier to work with large objects in cramped conditions.
Daniel digitizes a boat hull in his workshop
Digitization with the EinScan H 3D scanner provides accurate digital images of the case in the EXScan software. In this case, scanning was carried out at medium detail settings with an accuracy of one millimeter.
EXScan boat scan data
Digital boat model with EXScan program with textures and color reproduction
2. Reverse engineering in Fusion 360
The next step is to reverse-engineer in Fusion 360 to create a 3D model of the mold tool from the scanned data. At the same time, this information will help to estimate the cost of manufacturing a replica boat from scratch using modern technologies and materials.
Creating cross sections in Fusion 360
Dividing the scan into cross sections of the same length will help with the modeling of a new hull and applying new surfaces.
Sketch of a new housing
Sketch includes outlines of sides, deck and transom. The contours are not yet aligned, but the shape as a whole is close enough to the final one to estimate the consumption of materials for a new hull.
Create mold model
The next step is to sketch the mold tooling. The original body consists of six layers of mahogany veneer laid diagonally across the longitudinal axis on top of the mold. The supporting structure of the mold can be made from fibreboard, by cutting out the transverse and longitudinal sections on a CNC machine to assemble the "skeleton".
Housing design
The "skeleton" of the virtual mold is then covered with wooden planks. The shape of the skin after alignment should exactly repeat the internal contours of the new hull.
Data comparison
The final step is to compare the 3D scan data with the new body model.
It took Daniel only about two hours for the entire modeling process to estimate the cost of the replica. If the price tag is acceptable, it will be possible to start creating a more detailed 3D model directly for production purposes.
Detailed information about the EinScan H 3D scanner and other offers under the Shining 3D brand is available on the official website of our company.
3D scanner EinScan H Dan Lee Boatbuilding
Subscribe author
Subscribe
Don't want
4
More interesting articles
spc
Loading
24. 10.2022
607
four
Subscribe to the author
Subscribe
Don't want
In general, parts of the Baby-Vac aspirator bought a long time ago began to slowly crumble. I think...
Read more
3
Subscribe to the author
Subscribe
Don't want
Microtia is a congenital deformity in which the auricle is underdeveloped. The doctors of the hospital in Guiga...
Read more
153
Subscribe to the author
Subscribe
Don't want
As a maker, I use various tools in my work, including a glue gun. For m...
Read more
Useful articles and examples of 3D scanning
You have disabled JavaScript.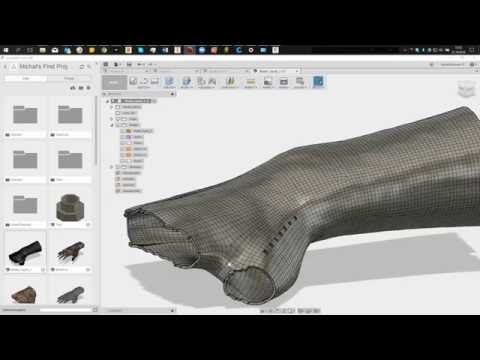
Partners
Category:
- All
- Useful articles
- Production and design
- Reverse engineering and geometry control
- Restoration and preservation of cultural heritage
-
Reverse engineering in Fusion 360: designing the perfect insole from a 3D scan of the foot
We explain step by step how to turn a 3D scan of a foot into a full 3D model in Autodesk Fusion 360, and then design a suitable insole from it...
-
FreeCAD: reverse engineering of mechanical shapes
Explaining for beginners how mechanical shape reverse engineering works in FreeCAD. From importing 3D scans to getting a threaded solid...
... -
Geomagic Design X: Align and edit mesh
We continue to introduce you to lessons on reverse engineering in Geomagic Design X.
In this article, we will look at:
- .
..
- .
-
Geomagic Design X: Reverse engineering of organic shapes. 3D Scan Processing
In our guide, we will introduce you to the reverse engineering of organic shapes in Geomagic Design X.
...
-
SolidWorks: Reverse Engineering of Organic Forms
If you want to start learning reverse engineering, we offer you our free tutorials "Reverse Engineering for Beginners". This r...
-
Maserati Levante transformation into funeral car
Funeral processions can hardly be organized without the use of a funeral car. The level of the event, the status and preferences of relatives rendered...
-
How to Solve Shelby Cobra Body Geometry Problems with RangeVision Spectrum 3D Scanner
We will never know the name of the person who first decided to create in his garage a copy of the desired car, which was not possible to buy .
Learn more