3D printing industry 2023
Manufacturers reveal how industrial 3D printing is helping unlock economic volume production
0Shares
Industrial 3D printer adopters have revealed how HP Multi Jet Fusion (MJF) technology is helping them cost-effectively scale plastic part production.
With the firm’s industrial 3D printers, the Jet Fusion 5200 and Jet Fusion 5420W, it’s now possible for users to manufacture end parts with high-reusability plastics, while optimizing cost and productivity. HP says these industrial 3D printing systems drive efficiency ‘per cubic inch,’ due to the labor and material cost savings gained from their high productivity and automation, as well as predictability, and their materials’ reusability.
Since launch, adopters ranging from robotics and machinery part producers to 3D printing service providers, like DI Labs, Prototal Industries, and Weerg, have each revealed how these manufacturing-ready industrial 3D printers are allowing them to meet their varying production needs.
“Additive manufacturing delivers on today’s most urgent market demands including sustainable innovation, hyper-personalization, and business resiliency,” said Didier Deltort, President of Personalization & 3D Printing at HP. “Together, with our global network of partners and customers, we are scaling additive manufacturing to meet these needs.”
Industrial 3D printers by HP
Since it was first introduced in 2014, MJF has been used to 3D print over 170 million parts, for customers in the aerospace, medical, automotive, education, consumer goods, and manufacturing service sectors. As its offering has begun to meet demand from customers in new industries, HP has expanded its industrial 3D printer portfolio in tandem, launching the Jet Fusion 5200 and 5420W in recent years.
When the former first came out in 2019, it was marketed as a factory-ready system capable of addressing industrial 3D printing needs. Launched alongside a build unit, processing station, and cooling unit, the HP Jet Fusion 5200 is designed to deliver improved economics, performance, and part quality, to those 3D printing in ‘production environments.’
A fleet of industrial 3D printers on the production floor – HP Jet Fusion 5200. Photo via HP.According to HP, the machine itself features a print speed of up to 5058 cm³/hr and a 380 x 284 x 380 mm build volume that enable it to achieve ‘best-in-class economics.’ This claim is justified, the firm says, by the system’s high level of productivity (over 160,000 cm3 per day), its robust ancillary lineup, which automates materials mixing, and integrated software that helps streamline users’ workflows.
On the software side, the HP Jet Fusion 5200 industrial 3D printing solution also features a consolidated dashboard that collates data from multiple management systems. This helps users streamline their workflow, optimize job efficiency, and scale into industrial production.
Similarly geared towards industrial 3D printing, the HP Jet Fusion 5420W launched at Formnext last year. The first in what’s set to be a series of Jet Fusion 5400 products, the machine is designed to bring MJF’s industrial-grade reliability, low cost per part, and enhanced manufacturing predictability to the production of white goods.
At Formnext, it was revealed how the technology has already allowed users like DI Labs, Prototal Industries, and Weerg, to address ‘innovative white applications.’ In fact, Jan Löfving, CEO of Prototal, said it had seen “immediate interest in the new white applications” from customers, thanks largely to the 5420W.
Carl Douglass, Co-Founder of DI Labs, another HP Jet Fusion 5420W industrial 3D printer user, added: “The new HP Jet Fusion 5420W 3D Printing Solution gives us another valuable tool in our toolbox to serve healthcare applications where white parts are an essential aesthetic. After printing over a thousand parts, we could not be more pleased with the surface quality, consistency, and white color. This new addition is a perfect complement to our existing HP Jet Fusion machines and allows us to expand our offerings.”
Where is industrial 3D printing by HP applied?
From molds to end-use spares, HP Jet Fusion industrial 3D printers are being deployed by manufacturers across multiple industries to create parts that feature optimized mechanical properties, without incurring lengthy lead times.
Said to be ideal for automotive, consumer goods, healthcare, and industrial 3D printing applications, the new HP Jet Fusion 5420W Series is already proving a popular means of addressing white applications among early adopters. In fact, HP Digital Manufacturing Network (DMN) member Prototal Industries, has hailed the system for “equipping it to take on bold, innovative” new client projects.
“HP continues to provide us with the advancements we need to push the boundaries of additive manufacturing and produce the final parts our customers need,” added Löfving. “Beyond the industrial grade production HP delivers, we are seeing immediate interest in the new white applications made possible by the latest addition to HP’s Multi Jet Fusion family.”
At Formnext, HP also debuted some of the more innovative applications of its wider MJF portfolio, including GKN Additive-mass produced spoiler seals, designed to provide better fuel efficiency. Smith Optic’s MAG Imprint 3D Goggles were also debuted at the show. Using HP MJF 3D printing, it was said the goggles could be made to fit perfectly to each user’s face, in a way that eliminates light/air leaks.
Any questions? Reach out to an industrial 3D printing expert here:
https://reinvent. hp.com/us-en-3d-prints-plastics-cwu-b?jumpid=af_dfd36af302
HP sponsored this article.
To stay up to date with the latest 3D printing news, don’t forget to subscribe to the 3D Printing Industry newsletter or follow us on Twitter or liking our page on Facebook.
While you’re here, why not subscribe to our Youtube channel? featuring discussion, debriefs, video shorts and webinar replays.
Are you looking for a job in the additive manufacturing industry? Visit 3D Printing Jobs for a selection of roles in the industry.
Featured image shows a fleet of industrial 3D printers on the production floor – HP Jet Fusion 5200. Photo via HP.
Tags DI Labs Didier Deltort Formnext GKN Additive HP HP Jet Fusion 5200 HP Jet Fusion 5420W Jan Löfving Prototal Industries Smith Optics Weerg
Paul Hanaphy
Paul is a history and journalism graduate with a passion for finding the latest scoop in technology news.
3D Printing Webinar & Event Roundup: February 19, 2023 - 3DPrint.com
We’ve got many offerings for you this week, including a few online events, like Mimaki Europe’s Global Innovation Days, and in-person events, such as LMT Lab Day. Markforged will discuss winning metal FFF applications, Stratasys and Materialise will each focus on personalized medical device development, and 3DEO welcomes Jenny Wu for a virtual fireside chat to talk about LACE. Plus, 3DPrint.com and Velo3D are hosting a webinar together about scaling metal additive manufacturing production. For these offerings and more, read on for all the details!
3D Printing News UnpeeledOur Executive Editor Joris Peels, who’s also the Vice President of Consulting at SmarTech Analysis, offers a news livestream one to two times a week called 3D Printing News Unpeeled at 9:30 am EST. For each episode, Peels gets on LinkedIn Live and tells us, in 20 minutes or less, what he considers to be the top news stories from the 3D printing industry that week, and why they’re important. Some of the stories in his roundup are ones we’ve covered at 3DPrint.com, and some are not, but they are all equally interesting and impactful.
For the fourth time, Mimaki Europe will host its online education and networking event for customers and industry peers. Mimaki Innovation Days will be held from February 21-23, and during the information-packed event, will also launch a new product to ensure its customers can run more efficient and productive businesses, enable automated and sustainable production, and meet the demands of their various industries. In addition, the event will feature a full program of webinars on hot industry topics, such as materials, art and technology, and more.
“Innovation Days has been a highly successful initiative for all who attend due to the variety of information shared and the unique chance to gain insights into the worldwide print market.
This year will be another opportunity to see and hear from Mimaki’s team from different corners of the globe, bringing that international industry perspective to individuals in the comfort of their own office or home. On the second day of this eagerly awaited event we’ll not only be launching a brand new Mimaki solution. This printer breaks new ground for Mimaki technology, being the first of its kind to be added to our product portfolio,” said Danna Drion, General Marketing Manager at Mimaki Europe.
You can register for the event here.
February 21: Winning Metal FFF ApplicationsAt 10 am EST on Tuesday, February 21st, Markforged will hold a webinar on “10 Winning Applications in Metal FFF 3D Printing.” Markforged speakers Ross Adams, Product Manager II, and Daniel Leong, Senior Product Marketing Manager will provide a clear, no-hype picture of metal FFF 3D printing today, its advantages and limitations, and what can be done with it. Attendees will get to see metal 3D printed prototypes, tooling, end-use parts, and maintenance parts from the team working every day to innovate metal AM.
“Interested in learning about the capabilities and limitations of the safest, most user-friendly, and accessible metal 3D printing process?
“This session will provide a deep dive into 10 metal FFF applications — the techniques used, why the applications work, and how you can implement them yourself.”
You can register for the webinar here.
February 22 – 23: AM For Aerospace, Defence and SpaceFrom February 22-23, the 9th Additive Manufacturing for Aerospace, Defence and Space show will be taking place in-person at The Hilton Wembley Stadium in London. Establishing itself as a top forum for R&D experts, AM users, and industry partners in the aerospace and space industry, the event welcomes several great guest speakers from the likes of Boeing, Airbus, Boeing, and the Air Force Research Laboratory (AFRL), and there will be multiple roundtables, keynote presentations, and panel discussions as well. Key themes of the show include certification and standardization strategies, commercialization of research, space, air, land, and sea applications for AM processes, developing short-term AM strategies, and more.
“This event will provide a platform to support opportunities in high value manufacturing and help prepare the aerospace industry to tackle the roadblocks of wider AM adoption. It is also a unique opportunity to maintain, strengthen and build connections across the industry following this challenging period.”
You can register for the event here.
February 22: Carbon Fiber 3D Printing BenefitsIf you’re interested in learning more about carbon fiber 3D printing, you’ll want to attend this TriMech webinar at 10 am EST on Wednesday the 22nd for a “Demonstration of the Benefits of Carbon Fiber 3D Printing.” TriMech Hardware Application Engineer Andrew Miller will discuss the major differences between the Stratasys F370 and new F370CR printers, and explain to attendees how they can take advantage of the materials and applications available with the machines.
“With the all new composite ready 3D printer and access to new materials and a wide range of applications, you can supplement your fixture and part fabrication to gain speed, throughput and cost benefits.”
You can register for the webinar here.
February 22: 3D Printing Jigs & Fixtures with FormlabsJigs, fixtures, and other manufacturing aids are used internally by businesses to make assembly and manufacturing more reliable and simple by improving operator safety and reducing cycle times, which in turn can reduce production costs and streamline operations. To hear more, sign up for this Formlabs webinar at 11 am EST on the 22nd to learn how to “3D Print Jigs and Fixtures to Boost Manufacturing Efficiency.” Juliette Combe, Application Engineer, Product Team, will teach attendees how 3D printed jigs and fixtures can lower costs, and guide them through the workflow of quickly 3D printing strong, lasting tools and replacement parts for the factory floor with both SLS and SLA printers. Real-life case studies from each stage of production will also be presented.
“With new advances in additive manufacturing technologies and materials you can now replace the standard expensive machined metal jigs and fixtures with lightweight, ergonomic, and part-specific 3D printed tools, with a wide range of materials to enable functional applications. In-house 3D printing enables you to build manufacturing aids rapidly and at a low cost to improve the speed, quality, and efficiency of production. It increases design freedom to build complex, custom tools and encourages continuous improvement. With 3D printed replacement parts, you can grow operational agility, solve day-to-day production issues and reduce machine downtime.”
You can register for the webinar here.
February 22: Metal 3D Printing for Food ProcessingAlso at 11 am EST on Wednesday, Desktop Metal will be joined by Elliði Hreinsson, founder of Curio, which produces seafood processing machines for heading, filleting, skinning and sharpening. In a webinar on “Metal 3D Printing for Food Processing Industry,” Hreinsson will share his experience using five DM Studio Systems and two ETEC Envision One 3D printers to design and optimize food equipment, all the way from rapid prototyping to batch production in 316L stainless steel with Bound Metal Deposition. His latest filleting machine uses over 100 metal 3D printed parts, and the technology enabled him to reduce time to market by a whole year. Attendees will learn how to combine metal 3D printing with other methods for more efficient production, applications from filleting machines that highlight the challenges of traditional manufacturing and the benefits of additive, and more.
“Designing and manufacturing the complex mechanical assemblies of food processing equipment can be challenging. 3D printing offers value-added solutions to overcome hurdles like long lead times and expensive tooling. Building parts layer-by-layer eliminates many limitations of CNC machining and other traditional manufacturing approaches with benefits like increased design flexibility.
”
You can register for the webinar here.
February 23 – 25: Chicago Dental Society Midwinter MeetingFrom February 23rd through the 25th, the 158th Chicago Dental Society Midwinter Meeting will be taking place at McCormick Place. Featuring an exhibit hall with the latest dental innovations, Student Scientific Research Posters, several special networking events, and over 240 courses, including lectures and hands-on workshops, the scientific dental meeting has been called the best in the country. Some of the courses will touch on the use of 3D printing, and several industry companies will be exhibiting, including Formlabs, Glidewell Dental, Henry Schein Dental, Shining 3D, and SprintRay.
“The Midwinter Meeting is known for providing premiere speakers and exhibitors in dentistry from across the country. At the February 2023 meeting, attendees can access more than 240 CE-accredited courses on the latest practice management solutions and evidence-based clinical knowledge.
”
You can register for the CDS Midwinter Meeting here.
February 23: Scaling Personalized Medical Solutions with AutomationThursday, February 23rd will be especially busy! Materialise kicks things off with a webinar at 10:30 am EST on “How Customized Process Automation Can Help Scale Up Your Personalized Medical Solution.” Materialise Medical experts Karen De Leener, Market Manager, and Simon Lejaegere, Product Manager, will provide an overview of how process automation can help increase efficiency, and decrease lead times, when scaling up personalized medical solutions. Attendees will learn when to consider a customized workflow automation, how to start and the available options, examples of how this has helped other companies, and more.
“Automation plays a significant role in enabling companies to grow personalized medical cases. While the advantages of personalized solutions are now widespread across the healthcare market, the benefits of dedicated workflow automation are still to be adopted.
Many companies are unaware of the easy and accessible possibilities that can decrease lead times and increase efficiency. This webinar aims to give an overview of these possibilities.”
You can register for the webinar here.
February 23: Patient-Specific Medical Device DevelopmentWe stay on the medical track with Stratasys at 11 am EST on the 23rd, as it presents “Patient-Specific Medical Device Development – How to Introduce and Scale Your Personalized Programs” with new partner Axial3D. Stratasys Medical Business Manager Evan Hochstein and Axial3D’s Founder and Chief Strategy Officer Daniel Crawford will have a conversation about patient-specific applications that impact medical device development. They will cover the end-to-end workflow—from getting patient data to producing the device—as well as how AI-driven segmentation can speed up the process, how to cost-effectively implement or begin scaling patient-specific programs, and more. There will also be a Q&A session.
“In the coming years, the medical industry will see increased demand for personalized medical solutions. Stratasys and Axial3D have partnered to take on this growth and enable routine and accessible patient-specific care.”
You can register for the webinar here.
February 23: 3DHEALS Hosts World Community Managers Festival3DHEALS will wrap up things on the medical front, but not in the way you might think. Also on the 23rd, from 9-10 am PST (12-1 pm EST) and 4-5 pm PST (7-8 pm EST), the organization invites its entire healthcare 3D printing and bioprinting ecosystem to meet its global community managers via Zoom during its World Community Managers Festival, as a way to say hello and learn about what the various communities have been up to during the pandemic; 3DHEALS anticipates a “revival of in-person events,” as well as hybrid events, later in 2023. After updates from community managers and local partner organizations, attendees are free to visit community “booths” and connect in small groups. The first session will welcome community managers from New York, Washington, D.C., San Francisco, Detroit, and Eastern Europe / Budapest, while the second welcomes managers from Munich, Chicago, India, Vancouver, Melbourne, Brazil, Singapore, and San Francisco again.
“Since 2018, 3DHEALS has decentralized its community activities from San Francisco, California, USA, to more than twenty cities throughout the world. This growth was mostly organic by motivated and special individuals, 3DHEALS Community Managers, who came from all walks of life ranging from techies, and designers, to entrepreneurs, doctors, and investors. The goal of these local groups and events aims to bridge the knowledge and experience gap between 3D printing, an emerging technology, and the established healthcare and life science innovation ecosystem. It takes a village to make things happen!”
You can register for the virtual events here.
February 23: Scaling Metal AM Production with 3DPrint.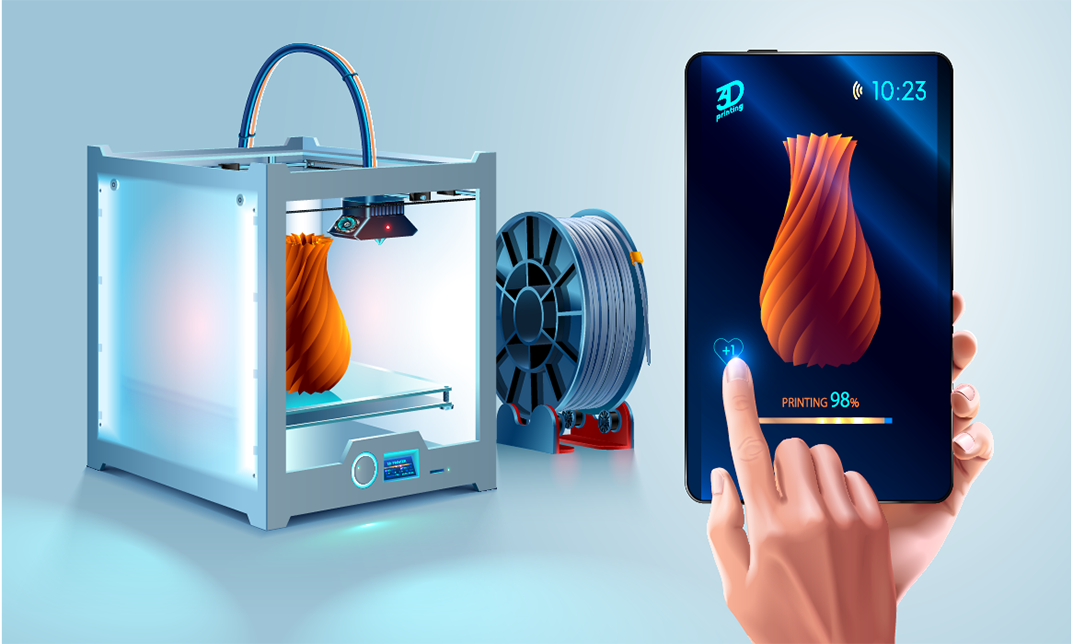
The first of three webinars at 2 pm EST on the 23rd will be co-hosted by 3DPrint.com and Velo3D, about “Unlocking the Potential of Metal AM: Strategies for Scaling Production with Velo3D.” Moderated by Joris Peels, the discussion will focus on the roadblocks to scaling metal AM, and how you can use Velo3D’s fully integrated metal AM solution to overcome these challenges by mitigating variation through standardization. Velo3D’s Technical Sales Engineer Sid Raje and Technical Business Development Account Manager Matt Karesh will discuss the importance of standardized print parameters, the role of fleet-level calibration in combating print variability, how a universal set of instructions allows for consistency across a global network of 3D printers, and more.
“Metal additive manufacturing (3D printing) is quickly becoming a vital technology used in the aerospace, energy, and tooling industries to manufacture complex parts more efficiently than they could using traditional manufacturing methods.
But while conventional metal AM excels at producing one-off and low volume parts, many of the same conventional systems lack the repeatability required to bring parts production to scale.”
You can register for the webinar here.
February 23: 3DEO’s Fireside Chat with Jenny Wu of LACEAlso at 2 pm EST on Thursday, jewelry lovers can join 3DEO‘s intimate fireside chat with award-winning designer, innovator, and 3D printing pioneer Jenny Wu, the Founder and CEO of LACE, her original conception of luxury 3D printed jewelry. 3DEO’s Emily Elpes, Vice President of Marketing, will lead the conversation, looking into Wu’s path from architect to 3D printed jewelry designer and the founding of LACE by Jenny Wu. They will cover Wu’s inspiration and motivation behind her 3D printed luxury jewelry brand, how her successful architecture career plays a role in her consumer brand, success stories behind various LACE collections, advice for entrepreneurs in consumer products, and more.
“Hear the story behind designing and launching her newest piece, Link, in collaboration with 3DEO: the first fully 3D printed chain bracelet.”
You can register for the fireside chat here.
February 23: New Handheld 3D Scanner by ZeissThe final 2 pm EST webinar on the 23rd is TriMech’s second offering this week, and it’s offering a “First Look at Zeiss’ New Handheld 3D Scanner, the T-Scan Hawk 2,” which is the latest addition to the GOM/Zeiss metrology tool lineup. TriMech 3D Scanning Product Sales Specialist Brian Metzger and Juan Uribe from ZEISS, Technical Lead for HandsOnMetrology Americas, will discuss the features of the new T-Scan Hawk 2, and demonstrate the handheld 3D scanner.
“Offering the highest possible standard of accuracy and resolution in a handheld 3D scanner, the T-Scan Hawk 2 will open up new possibilities for Reverse Engineering and Quality Control.”
You can register for the webinar here.
Finally, the largest dental laboratory event in the US, LMT LAB DAY, will be held at the Hyatt Regency Chicago from February 24-26. This is the 37th year for the comprehensive trade show, which got its start with 31 exhibitors and about 400 attendees and has grown to 260 exhibitors and over 4,500 attendees. There will be plenty of educational seminars to choose from, most of which will be approved for CE credits by the NBC, and several of which will focus on 3D printing in the dental industry. Plenty of AM industry companies will be attending or exhibiting as well, including 3D Systems, SprintRay, PostProcess Technologies, and more.
You can register for LMT LAB DAY here.
Do you have news to share about any future webinars or virtual and live events? Please let us know!
Subscribe to Our Email Newsletter
Stay up-to-date on all the latest news from the 3D printing industry and receive information and offers from third party vendors.
Tagged with: 3d print jewelry • 3d print space • 3d printed aerospace applications • 3d printed bracelet • 3d printed medical solutions • 3D printing for tooling applications • 3D printing webinars • 3DEO • 3DHeals • 3dPrint.com • 3DPrint.com webinar • additive mafacturing • additive manufacturing webinars • automation • Axial3D • bound metal deposition • carbon fiber 3D printing • chicago • Chicago Dental Society • community • courses • Curio • Defense 3D printing • dental 3d printing • dental laboratories • dental labs • desktop metal • DM Studio System • envision one 3D printer • ETEC • F370 CR • FFF metal 3D printing • food processing • formlabs • free webinar • GOM T-Scan Hawk • handheld 3d scanner • in-person events • integrated 3D printing solutions • jenny wu • jigs and fixtures • LACE • lace by jenny wu • LMT LAB DAY • London • luxury 3D printed goods • markforged • materialise • medical 3d printing • medical device 3D printing • metal 3d printing • metrology • Mimaki Europe • Mimaki Innovation Days • patient specific medical devices • patient-specific printing • personalized medical devices • product launch • scaling AM • scaling production • sprintray • standardization • stratasys • Stratasys F370 • T-Scan Hawk 2 • TriMech • velo3d • virtual events • webinars • Zeiss
Please enable JavaScript to view the comments powered by Disqus.
4 3D printing trends in 2023
Analytics and business
Experts recommend
Author: Viktor Naumov
Author: Viktor Naumov
Year after year, the adoption of additive manufacturing reaches new heights. What can we expect from 2023? Materialize, a leader in the global 3D printing market, offered its forecast based on four key trends that will drive the industry over the next twelve months:
-
the rise of smart, distributed manufacturing;
-
focus on cost reduction;
-
transition from automation of individual processes to complex automation of the workflow;
-
data security and integrity becomes a priority.
By addressing these issues, companies will be able to bring 3D printing to the level of mass production and accelerate the adoption of additive technologies.
Over the past three decades, 3D printing has established itself as a versatile and flexible tool in the manufacturing arsenal. Being a relatively new technology, it has spent most of this time somewhat isolated from the traditional manufacturing process. But in recent years, the wall between classic manufacturing and 3D printing has begun to disappear. We are starting to see these two separate worlds coming together, and the implications are enormous.
In 2023, the above trends will be the key to overcome the barriers that are still associated with the introduction of technology into industrial production. Addressing these issues will help companies scale up 3D printing to mass production and accelerate the adoption of 3D printing.
Fried Vankran, CEO of Materialize
© Materialise
1. The rise of smart, distributed manufacturing
Traditionally, production has always been concentrated in one place - usually a factory in another country. This system worked well until it stopped working. Over the past few years, we have seen how the COVID-19 crisis has paralyzed production and disrupted supply chains. We have witnessed an increase in geopolitical tensions and environmental concerns. All this taken together forced manufacturing companies to reconsider their model of centralized production. And with the help of smart digital technologies like 3D printing, manufacturers can move to multiple, smaller sites closer to customers.
Find the right 3D printer for you
However, many of the recent implementations owe their success to quick decision making in the face of scarce funds, such as reaching out to local 3D printing service providers to produce essential medical devices during the coronavirus pandemic. It can be said that 3D printing has been used as a temporary replacement. But, fortunately, such decisions have sparked new conversations about the future of production.
Now we see that many companies are ready to take a more strategic approach. These companies need to carefully consider which applications will deliver the most value in terms of supply chain efficiency or environmental sustainability. And this requires a change in thinking, moving from short-term solutions to the use of additive technologies as a stable method for the production of certified final parts.
A good example is CNH, an agricultural machinery company. During the pandemic, CNH was 3D-printing a vital part that could not be obtained due to COVID-related logistical constraints. The experience has proved useful, and the company is now looking at 3D printing as part of its strategy to manage supply chains in a more cost-effective way.
3D printing at CNH © cnhindustrial.com
Thus, the potential is real even in such a highly regulated field as medicine. We are seeing hospitals increasingly turning to 3D printing to create medical models and personalized implants in situ, close to patients.
We can say that this is the medical equivalent of a decentralized model of industrial production. Ultimately, we have smart, distributed manufacturing enabled by 3D printing that, when approached strategically, can be a recipe for success rather than an ad hoc response to problems.
Hanne Gielis, Innovation Manager, Mindware
2. Focus on cost reduction
The history of 3D printing is a history of added value. Additive manufacturing allows for design optimization, delivering performance, weight savings, time savings and supply chain savings that traditional manufacturing methods cannot achieve. In many cases, these benefits create opportunities for cost savings that affect overall manufacturing costs, from design to delivery.
Manufacturers planning to scale additive manufacturing to thousands or even millions of parts must ensure that the 3D printing process is efficient, reliable, and repeatable across multiple manufacturing sites.
Peter Lace, Executive Chairman, Materialize
A recent survey showed that the ability to reduce overall manufacturing costs is cited as the most important benefit of 3D printing. But this does not necessarily mean that the additive process itself is cost effective. Rising material and energy prices have only further increased costs.
The cost of 3D printed parts is determined by several factors, including the materials needed, the lead time per part, and the type of printer. There are two really important ways to reduce these costs. The first is more efficient work to increase production capacity. Software plays a big role in this, allowing you to optimize your designs. We can also customize the printing process to make it more efficient and repeatable. The second way is to use tools and improve quality. And you have to pay for quality.
© Materialise
If we take a certified production in the medical or aviation industry, we will see that up to 70 percent of the cost of production is accounted for by quality control. 3D printing continues to transform factory floors as companies increasingly turn to the technology for large-scale production. But to accelerate this adoption, our industry will have to work harder to bring down the cost of 3D printing.
Brian Crutchfield, Vice President and General Manager, North America
3. Transition from single process automation to integrated workflow automation
3D printing is a digital manufacturing technology, but it still requires a lot of human intervention. And such skilled workers are becoming increasingly difficult to find. According to a recent study by Materialize, finding the right people with the right knowledge and experience is a major challenge for companies that already use or are considering using 3D printers.
At the same time, scaling industrial additive manufacturing to thousands or millions requires repeatability and stability of the printing process. These two issues have increased the need for automation in recent years. The software allowed us to automate various steps in the 3D printing process, from preparing and editing files to creating supports, optimizing object placement in the build chamber, and even post-processing.
But these are all separate processes. In 3D printing, they follow each other, merging into a complex digital manufacturing process. The promise of large-scale industrial 3D printing requires us to automate not only each individual process, but also the workflows between them. And this is what we call end-to-end workflow automation.
© Materialise
We see the same thing in the medical industry, where complex process automation is needed to cope with the surge in custom 3D solutions. The good news is that opportunities to meet this need are growing with the creation of software platforms that allow manufacturers to customize their own unique 3D printing process.
Isabelle Rombaugh, Director of Global Sales and Business Development Medical
4. Data security and integrity becomes a priority
We have already talked about such an important trend as distributed production. Smart digital technologies, including 3D printing, are making it possible to move production to several smaller sites closer to customers. This is a clear sign that the factory of the future will not have a single, central location. This new digital distributed manufacturing environment revolves around one key asset - data, and this data must be protected so that an unscrupulous supplier cannot steal the design and print the product on their own 3D printer.
Of course, data security is important in any kind of manufacturing, be it traditional or smart. In both cases, companies share their unique designs with contractors and suppliers, and they want to know that their design data will remain secure. But in the case of 3D printing, that's not all. Manufacturers planning to scale additive manufacturing to thousands or even millions of parts must optimize and fine-tune their unique printing process to ensure it is efficient, reliable and repeatable across multiple manufacturing sites.
A well-thought-out manufacturing process guarantees the same quality of all 3D printed components, regardless of where they are produced. Creating such a process is a complex and time-consuming task, but it allows companies to stay ahead of the competition. That is why not only the security of data storage, but also their integrity, that is, a close and reliable connection between the project, on the one hand, and production parameters, on the other, becomes a paramount task for companies implementing digital production.
Peter Lace, Executive Chairman
Material provided by Materialize
Article published on 01/20/2023, updated on 01/20/2023
industry3d.ru
CONFERENCE "3D technologies in medicine"
News AT
Worldwide
OTHER
Happy New Year and Merry Christmas!
30.12.2022 Editor-in-chief of the INDUSTRY3D media portal | Reading time: 1 min. Difficulty:
420
Have a magical New Year and Merry Christmas!
An overview of the additive manufacturing of single crystal nickel-based superalloys
09/27/2022 Rekimchuk Viktor Maksimovich
EBAM GLOBAL LASER BASED METAL SLM NEWS REVIEW ARTICLE
HP Announces Commercial Availability of Its Long-Awaited Metal Jet S100 Project for Metal 3D Printing
20. 09.2022 Rekimchuk Viktor Maksimovich
b.j. EURO GLOBAL METAL PRINTING ENGINEERING MEDICINE NEWS ARTICLE
Problems of development of additive manufacturing technologies in space
08/19/2022 Rekimchuk Viktor Maksimovich
COMPOSIT DLP FFF GLOBAL LASER BASED METAL POLYMERS SLA SPACE PROTOTYPES REPAIR ARTICLE TRANSPORT
Laser additive manufacturing of metal structures using biological design
08/10/2022 Rekimchuk Viktor Maksimovich
ASIA DED LASER BASED SLM DESIGN ENGINEERING MEDICINE MODELING ARTICLE TRANSPORT
FORMLABS announces the release of the FUSE 1+ 30W SLS 3D printer
08/05/2022
GLOBAL METAL PRINTING SLS NEWS
Japanese company Shimoda chooses MX3D's WAAM technology for use in wind power
08/01/2022 Rekimchuk Viktor Maksimovich
ARM BASED ASIA DED METAL PRODUCTION WAAM NUCLEAR POWER MULTI-INDUSTRY
All news
Russia and CIS
METAL PRINTING ENG NEWS
Permanent magnets can now be 3D printed
08/10/2022 | Reading time: 6 min. Difficulty:
805
NUST MISIS scientists have proposed a method of 3D printing from hard magnetic materials, which makes it possible to create magnets with controlled properties. In the future, it will simplify and reduce the cost of creating permanent magnets of complex shape for various appliances and devices: from household appliances to high-tech electronics. At the same time, the production time of such magnets is significantly reduced compared to traditional methods.
Additive technologies at INNOPROM 2022. Main results.
08.08.2022
ENG STATE CONFERENCE MULTI-INDUSTRY NEWS DEFENSE INDUSTRY
A 3D-printed shoulder joint implant with a modified surface appeared on the Russian market
07/12/2022
BIOINKS PRINTING ENG BIOPRINTING MEDICINE NEWS
UEC completed the second stage of creating a digital twin of the AI-222-25 aircraft engine
07. 07.2022
PRINTING ENG AVIATION DESIGN DEPARTMENT NEWS
TsAGI has mastered and implemented an additive manufacturing technology for parts of aerodynamic models
07.07.2022
METAL PRINTING ENG SLS AVIATION NEWS
Rosatom presented the concept of a mobile additive complex in container design for the needs of the Ministry of Defense
07.07.2022
PRINTING ENG NEWS DEFENSE INDUSTRY TRANSPORT
Russian aluminum alloys showed a 20% increase in strength
07/01/2022
METAL PRINTING ENG NEWS
All news
3D printing
3D Printing Technologies
METAL PRINTING ENG SLS ARTICLE
The only ones in Russia
09/02/2022 | Reading time: 11 min. Difficulty:
227
The formation of the startup "ONSINT" was rapid. In 2018, we began to develop and design equipment, in 2019 we registered a company, in 2020 sales and participation in status exhibitions on additive technologies began, and the status of a Skolkovo resident was obtained.
Laser stereolithography: state of the art and prospects
10/16/2018 Journal "Additive Technologies"
DLP GLOBAL LP POLYMERS PRINTING SLA ARTICLE
3D printing with low temperature plastic
04.09.2022
FFF GLOBAL POLYMERS POSTPRINT PRINTING WAX ARTICLE
All articles
Materials
GLOBAL METAL PRINTING SLA SLM SLS X-RAY METALLURGY REVIEW ARTICLE
An overview of the additive manufacturing of single crystal nickel-based superalloys
23. 10.2022 | Reading time: 80 min. Difficulty:
169
The traditional manufacturing process for nickel-based single crystal refractory materials is directional solidification, which is classified as casting.
For what simulate microstructure material in 3D printing
06.09.2022
GLOBAL METAL PRINTING SCANNING SLM ARTICLE
The Importance of Choosing an Additive Metal Manufacturing Service Provider
24.02.2022
METAL PRINTING MODELING ARTICLE
All articles
Applications
BIGREP EXTRA FFF GLOBAL LP POLYMERS PRINTING SLA UNIONTECH ARCHITECTURE DESIGN LAYOUTS ARTICLE
Visualization (visual prototyping)
03. 05.2021 Mikhail Rikhirev | Reading time: 8 min. Difficulty:
480
Planning of functional prototyping by 3D printing methods in industrial design and architectural modeling
BigRep 3D printers: from bicycle frame to rocket engine injector
04/28/2021 Mikhail Rikhirev
BIGREP EXTRA FFF GLOBAL POLYMERS PRINTING R&D DESIGN EDUCATION ARTICLE
BigRep ONE and Keter Plastics: 3D Printing Industrial Design Prototypes
04/28/2021 Mikhail Rikhirev
BIGREP EURO EXTRA FFF POLYMERS PRINTING R&D DESIGN DESIGN PROTOTYPES ARTICLE
All articles
Software solutions
DESIGN (CAD) GLOBAL MODELING SIMULATION (CAE) ARTICLE
Computer simulation of metal 3D printing processes based on MSC Software solutions
08/28/2020 | Reading time: 10 min. Difficulty:
512
3D printing technology is a rapidly growing and promising area in many industries. 3D printers make it possible to obtain parts that cannot be made in other ways.
Varieties and tasks geometric optimization of products for additive manufacturing
08/11/2022
CEMENT GLOBAL METAL SLS ARCHITECTURE DESIGN DESIGN ARTICLE CONSTRUCTION
Design Challenges for Additive Technologies
07/14/2020
DESIGN (CAD) GLOBAL MODELING ARTICLE
All articles
3D control
Measuring instruments
GLOBAL LASER BASED RANGE VISION SCANNING SCANTECH STRUCTURED LIGHT THOR3D CASTING OF METALS ARTICLE
The use of handheld 3D scanners in the foundry
04/28/2021 Yakov Bondarev | Reading time: 14 min. Difficulty:
530
Information on the types of handheld scanners and a detailed discussion of their application in the foundry.
Premiere! KSCAN20 universal metrology handheld scanner
04/23/2021
GLOBAL LASER BASED SCANNING SCANTECH ARTICLE
Structured Illumination and New Possibilities for Scanning Small Objects
04/18/2021 Ilya Krupennikov, iQB Technologies
GLOBAL SCANNING STRUCTURED LIGHT ARTICLE
Hardware Overview: Rangevision PRO 2M Stationary 3D Scanner
03.05.2021 Yakov Bondarev
RANGE VISION ENG SCANNING STRUCTURED LIGHT REVIEW
All articles
Applications
DESIGN (CAD) GEOMAGIC LASER BASED PARTS ENG SCANNING SCANTECH ENGINEERING REVERSE ARTICLE
reverse engineering
04. 05.2021 Georgy Kazakevich | Reading time: 22 min. Difficulty:
529
What new and unique opportunities does 3D scanning bring to manufacturers and repairers?
Geomagic Design X
04.05.2021 Yakov Bondarev
DESIGN (CAD) GEOMAGIC GLOBAL METROLOGY MODELING DESIGN CONTROL ENGINEERING ARTICLE
Creating Databases with 3D Scanning
04.05.2021 Yakov Bondarev
DESIGN (CAD) GLOBAL LASER BASED R&D SCANNING SCANTECH ARTICLE TUNING
Control of finished products after machining
03.05.2021 Yakov Bondarev
DESIGN (CAD) GEOMAGIC GLOBAL METROLOGY MODELING CONTROL ENGINEERING REVERSE REPAIR ARTICLE
All articles
Blog
Scientific articles
POSTPRINT PRINTING ENG SLA REVIEW ARTICLE
Post-processing of finished products after SLA printing
Author: Vinogradova Alexandra Ivanovna
02/08/2023 Vinogradova Alexandra Ivanovna | Reading time: 4 min. Difficulty:
60
Read more
SCANNING SCANTECH CONTROL REVERSE
How to Measure Helical Gear Mating with 3D Scanning
Author: Petrova Tatiana
01/26/2023 Petrova Tatiana | Reading time: 5 min. Difficulty:
81
Read more
PCM CASTING OF METALS
3D printer to be used to create wind turbines used offshore
Author: Petrova Tatiana
01/25/2023 Petrova Tatiana | Reading time: 4 min. Difficulty:
53
Read more
AMERICA PRINTING ENG REVIEW ARTICLE CONSTRUCTION
TOP 15 printed structures
Author: Vinogradova Alexandra Ivanovna
01/24/2023 Vinogradova Alexandra Ivanovna | Reading time: 20 min.